外文资料翻译---传感器新技术的发展
传感器技术论文中英文对照资料外文翻译文献
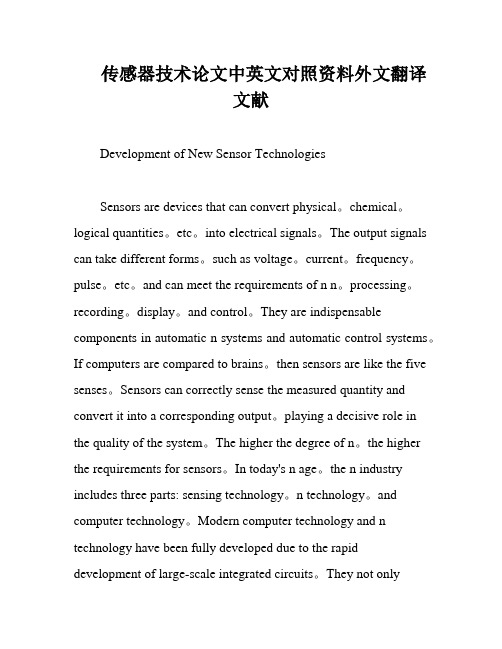
传感器技术论文中英文对照资料外文翻译文献Development of New Sensor TechnologiesSensors are devices that can convert physical。
chemical。
logical quantities。
etc。
into electrical signals。
The output signals can take different forms。
such as voltage。
current。
frequency。
pulse。
etc。
and can meet the requirements of n n。
processing。
recording。
display。
and control。
They are indispensable components in automatic n systems and automatic control systems。
If computers are compared to brains。
then sensors are like the five senses。
Sensors can correctly sense the measured quantity and convert it into a corresponding output。
playing a decisive role in the quality of the system。
The higher the degree of n。
the higher the requirements for sensors。
In today's n age。
the n industry includes three parts: sensing technology。
n technology。
and computer technology。
湿度传感器系统中英文对照外文翻译文献
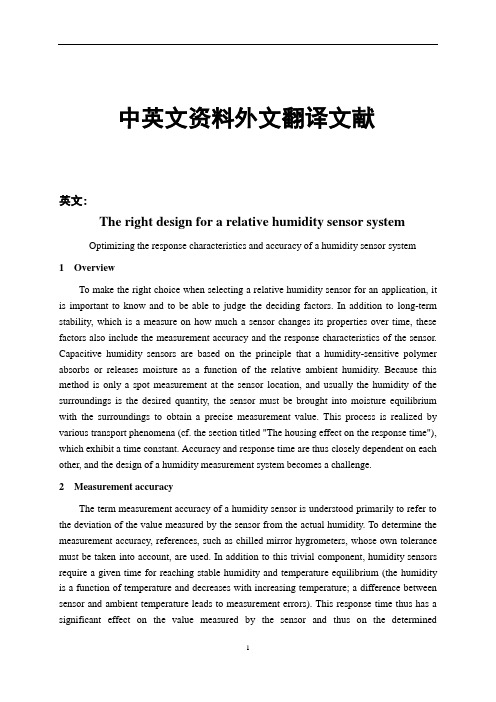
中英文资料外文翻译文献英文:The right design for a relative humidity sensor systemOptimizing the response characteristics and accuracy of a humidity sensor system1 OverviewTo make the right choice when selecting a relative humidity sensor for an application, it is important to know and to be able to judge the deciding factors. In addition to long-term stability, which is a measure on how much a sensor changes its properties over time, these factors also include the measurement accuracy and the response characteristics of the sensor. Capacitive humidity sensors are based on the principle that a humidity-sensitive polymer absorbs or releases moisture as a function of the relative ambient humidity. Because this method is only a spot measurement at the sensor location, and usually the humidity of the surroundings is the desired quantity, the sensor must be brought into moisture equilibrium with the surroundings to obtain a precise measurement value. This process is realized by various transport phenomena (cf. the section titled "The housing effect on the response time"), which exhibit a time constant. Accuracy and response time are thus closely dependent on each other, and the design of a humidity measurement system becomes a challenge.2Measurement accuracyThe term measurement accuracy of a humidity sensor is understood primarily to refer to the deviation of the value measured by the sensor from the actual humidity. To determine the measurement accuracy, references, such as chilled mirror hygrometers, whose own tolerance must be taken into account, are used. In addition to this trivial component, humidity sensors require a given time for reaching stable humidity and temperature equilibrium (the humidity is a function of temperature and decreases with increasing temperature; a difference between sensor and ambient temperature leads to measurement errors). This response time thus has a significant effect on the value measured by the sensor and thus on the determinedaccuracy.This time-dependent characteristic is explained in more detail in the following.3Response characteristics and response timeThe response characteristics are defined by various parameters. These are:●The actual response characteristics of the humidity sensor at constant temperature.(1) How quickly the sensitive polymer absorbs or releases moisture until equilibrium is reached (intrinsic response time)(2) How fast the entire system reaches humidity equilibrium (housing effect)●The thermal response characteristics of the humidity sensor at a non-constant temperature(3) The thermal mass of the sensor(4) The system's thermal mass, which is thermally coupled to the sensor (e.g. printed circuit board)(5) Heat sources in the direct surroundings of the sensor (electronic components)(1) and (3) are determined entirely by the sensor itself, (1) primarily by the characteristics of the sensitive polymer.(2) and (4) are primarily determined by the construction of the entire system (shape and size of housing andreadout circuitry).(5) is determined by heat-emitting electronic components.These points will be discussed in more detail in the following.The intrinsic response time (1)Qualitatively, the response characteristics of capacitive humidity sensors look like the following (Fig. 1).Fig. 1: Typical and idealized response characteristics of capacitive humidity sensors (schematic)Because these response characteristics are especially pronounced at high humidity values, an isothermal humidity jump from 40% to 100% was selected here for illustration. The desired ideal behavior of the sensor is indicated in blue. In practice, however, the sensor behaves according to the red line, approximately according to:RH-t=(E-S)*(1-e)+S(t)Here, the time span 1 is usually very short (typ. 1 – 30 min.), in contrast, the time span 2 is very long (typ. Many hours to days). Here the connection of measurement accuracy and response characteristics becomes clear (t until RH=100% is reached). The value at t4 (Fig. 1) is considered to be an exact measured value. However, this assumes that both the humidity and also the temperature remain stable during this entire time, and that the testing waits until this very long measurement time is completed. These conditions are both very hard to achieve and unusual in practice. For the calibration, there are the following two approaches, which both find use in practice (cf. Fig. 2):1.The measured value at t2 (Fig. 1) is used as a calibration reference.Advantage:●The required measurement time for reaching the end value (in the example 100%) isclearly shortened,corresponds to practice, and achieves an apparent short responsetime of the sensor (cf. Fig. 2).Disadvantage:●If the conditions are similar for a long time (e.g., wet periods in outdoor operation),the sensors exceed the correct end value (in the example 100%) undesirably by upto 10% (cf. Fig. 2).2. The measured value at t4 (Fig. 1) is used as a calibration reference.Advantage:●Even for similar conditions over a long time (e.g., wet periods in outdoor operation),an exact measurement result is obtained (cf. Fig. 2).Disadvantage:●For a humidity jump like in Fig. 1, the sensors very quickly deliver the measuredvalue at t2, but reaching a stable end value (about 3-6% higher) takes a long time(apparent longer response time)(cf. Fig. 2).In order to take into account both approaches optimally, the measured values at t3 (cf. Fig. 1) are used as the calibration reference by Sensirion AG.Fig. 2: Response characteristics of different humidity measurement systemsThe housing effect on the response time (2)Here, two types of transport phenomena play a deciding role:●Convection: For this very fast process, the air, whose humidity is to be determined,is transported to the sensor by means of ventilation.●Diffusion: This very slow process is determined by the thermal, molecularself-motion of the water molecules. It occurs even in "stationary" air (e.g., within ahousing), but leads to a long response time.In order to achieve favorable response characteristics in the humidity measurement system, the very fast convection process must be supported by large housing openings and the slow diffusion process must be supported by a small housing around the sensor (small "deadvolume") with "stationary" air reduced to a minimum. The following applies:Thermal effects (3), (4), and (5)Because the total thermal mass of the humidity measurement system (sensor + housing)has a significant effect on its response time, the total thermal mass must be kept as low aspossible. The greater the total thermal mass, the more inert the measurement system becomesthermally and its response time, which is temperature-dependent, increases. In order toprevent measurement errors, the sensor should not be mounted in the vicinity of heatgenerating components.4Summary –what should be taken into account when designing a humidity measurement systemIn order to achieve error-free operation of a humidity-measurement system with response times as short as possible, the following points should be taken into account especially for the selection of the sensor and for the design of the system.●The selection of the humidity sensor element. It should●be as small as possible,●have a thermal mass that is as low as possible,●work with a polymer, which exhibits minimal fluctuations in measured values duringthe time span 2(cf. Fig. 1); testing gives simple information on this condition,●provide calibration, which corresponds to the requirements (see above), e. g.,SHT11/SHT15 from Sensirion.●The housing design (cf. Formula 1). It should●have air openings that are as large as possible in the vicinity of the sensor or thesensor should be operated outside of the housing à good convection!●enclose a "dead volume" that is as small as possible around the sensor àlittlediffusion!●The sensor should be decoupled thermally as much as possible from other components,so that the response characteristics of the sensor are not negatively affected by the thermal inertia of the entire system.(e.g., its own printed circuit board for the humidity sensor, structurally partitioning the housing to create a small volume for the humidity sensor, see Fig. 3)Fig. 3: Mounting example for Sensirion sensors SHT11 and SHT15 with slits for thermal decoupling●The sensor should not be mounted in the vicinity of heat sources. If it was, measuredtemperature would increase and measured humidity decrease.5Design proposalThe challenge is to realize a system that operates cleanly by optimally taking into account all of the points in section 4. The already calibrated SMD humidity sensors SHT11 and SHT15 from Sensirion are the ideal solution. For optimum integration of the sensors in a measurement system, Sensirion AG has also developed a filter cap as an adapter aid, which takes into account as much as possible the points in section 4 and also protects the sensor against contaminants with a filter membrane. Fig. 4 shows schematically how the sensors can be ideally integrated into a housing wall by means of the filter cap SF1.Fig. 4: Filter cap for SHT11 and SHT15In addition to the advantages mentioned above, there is also the option of building an IP67-compatible humidity measurement device (with O-ring, cf. Fig. 4) with optimal performance. Detailed information is available on the Sensirion Web site.译文:相对湿度传感器系统的正确设计湿度传感器系统精度及响应特性的优化1.综述为了在相对湿度的应用方面对传感器做出正确的选择,了解和评估那些起决定作用的因素是非常重要的。
红外传感器中英文对照外文翻译文献

中英文对照翻译外文资料Moving Object Counting with an Infrared Sensor NetworkAbstractWireless Sensor Network (WSN) has become a hot research topic recently. Great benefit can be gained through the deployment of the WSN over a wide range ofapplications, covering the domains of commercial, military as well as residential. In this project, we design a counting system which tracks people who pass through a detecting zone as well as the corresponding moving directions. Such a system can be deployed in traffic control, resource management, and human flow control. Our design is based on our self-made cost-effective Infrared Sensing Module board which co-operates with a WSN. The design of our system includes Infrared Sensing Module design, sensor clustering, node communication, system architecture and deployment. We conduct a series of experiments to evaluate the system performance which demonstrates the efficiency of our Moving Object Counting system.Keywords:Infrared radiation,Wireless Sensor Node1.1 Introduction to InfraredInfrared radiation is a part of the electromagnetic radiation with a wavelength lying between visible light and radio waves. Infrared have be widely used nowadaysincluding data communications, night vision, object tracking and so on. People commonly use infrared in data communication, since it is easily generated and only suffers little from electromagnetic interference. Take the TV remote control as an example, which can be found in everyone's home. The infrared remote control systems use infrared light-emitting diodes (LEDs) to send out an IR (infrared) signal when the button is pushed. A different pattern of pulses indicates the corresponding button being pushed. To allow the control of multiple appliances such as a TV, VCR, and cable box, without interference, systems generally have a preamble and an address to synchronize the receiver and identify the source and location of the infrared signal. To encode the data, systems generally vary the width of the pulses (pulse-width modulation) or the width of the spaces between the pulses (pulse space modulation). Another popular system, bi-phase encoding, uses signal transitions to convey information. Each pulse is actually a burst of IR at the carrier frequency.A 'high' means a burst of IR energy at the carrier frequency and a 'low' represents an absence of IR energy. There is no encoding standard.However, while a great many home entertainment devices use their own proprietary encoding schemes, some quasi-standards do exist. These include RC-5, RC-6, and REC-80. In addition, many manufacturers, such as NEC, have also established their own standards.Wireless Sensor Network (WSN) has become a hot research topic recently. Great benefit can be gained through the deployment of the WSN over a wide range ofapplications, covering the domains of commercial, military as well as residential. In this project, we design a counting system which tracks people who pass through a detecting zone as well as the corresponding moving directions. Such a system can be deployed in traffic control, resource management, and human flow control. Our design is based on our self-made cost-effective Infrared Sensing Module board which co-operates with a WSN. The design of our system includes Infrared Sensing Module design, sensor clustering, node communication, system architecture and deployment. We conduct a series of experiments to evaluate the system performance which demonstrates the efficiency of our Moving Object Counting system.1.2 Wireless sensor networkWireless sensor network (WSN) is a wireless network which consists of a vast number of autonomous sensor nodes using sensors to monitor physical or environmental conditions, such as temperature,acoustics, vibration, pressure, motion or pollutants, at different locations. Each node in a sensor network is typically equipped with a wireless communications device, a small microcontroller, one or more sensors, and an energy source, usually a battery. The size of a single sensor node can be as large as a shoebox and can be as small as the size of a grain of dust, depending on different applications. The cost of sensor nodes is similarly variable, ranging from hundreds of dollars to a few cents, depending on the size of the sensor network and the complexity requirement of the individual sensor nodes. The size and cost are constrained by sensor nodes, therefore, have result in corresponding limitations on available inputs such as energy, memory, computational speed and bandwidth. The development of wireless sensor networks (WSN) was originally motivated by military applications such as battlefield surveillance. Due to the advancement in micro-electronic mechanical system technology (MEMS), embedded microprocessors, and wireless networking, the WSN can be benefited in many civilian application areas, including habitat monitoring, healthcare applications, and home automation.1.3 Types of Wireless Sensor NetworksWireless sensor network nodes are typically less complex than general-purpose operating systems both because of the special requirements of sensor network applications and the resource constraintsin sensor network hardware platforms. The operating system does not need to include support for user interfaces. Furthermore, the resource constraints in terms of memory and memory mapping hardware support make mechanisms such as virtual memory either unnecessary or impossible to implement. TinyOS [TinyOS] is possibly the first operating system specifically designed for wireless sensor networks. Unlike most other operating systems, TinyOS is based on an event-driven programming model instead of multithreading. TinyOS programs are composed into event handlers and tasks with run to completion-semantics. When an external event occurs, such as an incoming data packet or a sensor reading, TinyOS calls the appropriate event handler to handle the event. The TinyOS system and programs are both written in a special programming language called nesC [nesC] which is an extension to the C programming language. NesC is designed to detect race conditions between tasks and event handlers. There are also operating systems that allow programming in C. Examples of such operating systems include Contiki [Contiki], and MANTIS. Contiki is designed to support loading modules over the network and supports run-time loading of standard ELF files. The Contiki kernel is event-driven, like TinyOS, but the system supports multithreading on a per-application basis. Unlike the event-driven Contiki kernel, the MANTIS kernel is based on preemptive multithreading. With preemptive multithreading, applications do not needto explicitly yield the microprocessor to other processes.1.4 Introduction to Wireless Sensor NodeA sensor node, also known as a mote, is a node in a wireless sensor network that is capable of performing processing, gathering sensory information and communicating with other connected nodes in the network. Sensor node should be in small size, consuming extremely low energy, autonomous and operate unattended, and adaptive to the environment. As wireless sensor nodes are micro-electronic sensor device, they can only be equipped with a limited power source. The main components of a sensor node include sensors, microcontroller, transceiver, and power source. Sensors are hardware devices that can produce measurable response to a change in a physical condition such as light density and sound density. The continuous analog signal collected by the sensors is digitized by Analog-to-Digital converter. The digitized signal is then passed to controllers for further processing. Most of the theoretical work on WSNs considers Passive and Omni directional sensors. Passive and Omni directional sensors sense the data without actually manipulating the environment with active probing, while no notion of “direction” involved in these measurements. Commonly people deploy sensor for detecting heat (e.g. thermal sensor), light (e.g. infrared sensor), ultra sound (e.g. ultrasonic sensor), or electromagnetism (e.g. magnetic sensor). In practice, a sensor node can equip with more than one sensor.Microcontroller performs tasks, processes data and controls the operations of other components in the sensor node. The sensor node is responsible for the signal processing upon the detection of the physical events as needed or on demand. It handles the interruption from the transceiver. In addition, it deals with the internal behavior, such as application-specific computation.The function of both transmitter and receiver are combined into a single device know as transceivers that are used in sensor nodes. Transceivers allow a sensor node to exchange information between the neighboring sensors and the sink node (a central receiver). The operational states of a transceiver are Transmit, Receive, Idle and Sleep. Power is stored either in the batteries or the capacitors. Batteries are the main source of power supply for the sensor nodes. Two types of batteries used are chargeable and non-rechargeable. They are also classified according to electrochemical material used for electrode such as NiCd(nickel-cadmium), NiZn(nickel-zinc), Nimh(nickel metal hydride), and Lithium-Ion. Current sensors are developed which are able to renew their energy from solar to vibration energy. Two major power saving policies used areDynamic Power Management (DPM) and Dynamic V oltage Scaling (DVS). DPM takes care of shutting down parts of sensor node which are not currently used or active. DVS scheme varies the power levelsdepending on the non-deterministic workload. By varying the voltage along with the frequency, it is possible to obtain quadratic reduction in power consumption.1.5 ChallengesThe major challenges in the design and implementation of the wireless sensor network are mainly the energy limitation, hardware limitation and the area of coverage. Energy is the scarcest resource of WSN nodes, and it determines the lifetime of WSNs. WSNs are meant to be deployed in large numbers in various environments, including remote and hostile regions, with ad-hoc communications as key. For this reason, algorithms and protocols need to be lifetime maximization, robustness and fault tolerance and self-configuration. The challenge in hardware is to produce low cost and tiny sensor nodes. With respect to these objectives, current sensor nodes usually have limited computational capability and memory space. Consequently, the application software and algorithms in WSN should be well-optimized and condensed. In order to maximize the coverage area with a high stability and robustness of each signal node, multi-hop communication with low power consumption is preferred. Furthermore, to deal with the large network size, the designed protocol for a large scale WSN must be distributed.1.6 Research IssuesResearchers are interested in various areas of wireless sensornetwork, which include the design, implementation, and operation. These include hardware, software and middleware, which means primitives between the software and the hardware. As the WSNs are generally deployed in the resources-constrained environments with battery operated node, the researchers are mainly focus on the issues of energy optimization, coverage areas improvement, errors reduction, sensor network application, data security, sensor node mobility, and data packet routing algorithm among the sensors. In literature, a large group of researchers devoted a great amount of effort in the WSN. They focused in various areas, including physical property, sensor training, security through intelligent node cooperation, medium access, sensor coverage with random and deterministic placement, object locating and tracking, sensor location determination, addressing, energy efficient broadcasting and active scheduling, energy conserved routing, connectivity, data dissemination and gathering, sensor centric quality of routing, topology control and maintenance, etc.中文译文移动目标点数与红外传感器网络摘要无线传感器网络(WSN)已成为最近的一个研究热点。
毕业设计论文 电子秤 中英文 外文资料 文献 翻译

外文参考资料二:Abstract: In order to solve the weight problem often encountered in measuring the low-mass objects in the trade and daily life of the modern business, the design of a new pocket-sized electronic scales. This pocket-sized electronic scales Force Sensor gravity signals into electrical signals to measure, and measuring the results of the digital display. The pocket-sized electronic scales with a small size, light weight, easy to carry, intuitive display, measurement and high precision; complex structure, the cost disadvantages. This article focuses on the load cell works, error compensation, the main parameters of selection. And the technical and economic analysis.Keywords: pocket-sized electronic scales; weighing; sensor; error compensationCLC number: TH715. 1] sign code: A Article ID: 100 522 895 (2007) 022*******1 A needs analysisIn modern commerce and trade and everyday life, often encounter the problem of measuring the weight of the low-mass objects. Although the traditional steelyard can solve this problem, but inconvenient to carry, the efficiency is not high, the display is not intuitive and low measurement accuracy; mechanical spring balance can solve this problem, but the inertia inherent low frequency, high sensitivity, measurement accuracy is not high. With the progress and update of the micro-computer technology, integrated circuit technology, sensor technology, electronic scales rapiddevelopment, it has a responsive, high accuracy, fully functional, the display is intuitive, compact, easy to use and so on.For these reasons, in order to solve the low-mass objects weighing problem, if a small size, light weight, portable, digital display electronic scales, will be popular. Discussed below, that is, the scope of a weighing 5 kg compact electronic scales.2 DesignThe principle of the structure of the pocket-sized electronic scales shown in Figure 1. The main task is to design compact electronic scales weighing the choice of the force sensors. Dynamometer sensor types to achieve the weighing and digital display, the key is to want to force (gravity) signals into electrical signals to measure method is mainly divided into two categories: one is the direct method, namely the use of pressure magnetic sensor, piezoelectric sensor, Piezoresistive sensors directly to the force signal converted into electrical signals; the other is the indirect method, the elastic element as the sensor will pull, pressure changes in strain, displacement, or frequency, and then strain sensors, displacement sensors, or frequency sensor strain, displacement or frequency changes for power. Comprehensive comparison of a variety of sensors, use the indirect method of strain gauge force transducer.Pocket-sized electronic scale structural principle:Sensor → amplifier → CPU→ display → AöD converter3 sensor device design3.1 worksThe working principle of the strain gauge force transducer strain gauge pasted into force, force-sensitive elasticelement, the corresponding strain when the elastic element force deformation, the strain gauge into a resistance change, which led to the voltage measuring circuit changes by measuring the output voltage value, and then through the conversion can be obtained by the measurement of body weight. Since the pocket-sized electronic scales require small size, weighing in scope, precision and angle even consistency, sensor and display integration, it is selected parallel to the two holes cantilever beam strain gauge load-bearing sensor. Its characteristics are: high precision, ease of processing, simple and compact structure, strong resistance to partial load, high natural frequency.Strain gauge choice of a metal palisade metal mooring paste on the insulating substrate parked strain gages, mechanical strain resistance strain gauge feelings generally 10 - 10 - 2mm, the resistance rate of change of the attendant about 10 - 6 10 - 2 orders of magnitude, such a small change in resistance measured using the general resistance of the instrument is hard to measure out, you must use some form of measurement.Circuit into small changes in resistance rates to changes in voltage or current, in order to secondary instrument display. Bridge measurement circuit to meet this requirement. In the load cell, R 1, R 2, R 3, R 44 strain gauge resistor bridge measurement circuit shown in Figure 3. R m is the temperature compensation resistor, e is the excitation voltage, V is the output voltage.外文参考资料三:The load cell is a quality signal into a measurable electrical signal outputdevice. Must consider the actual working environment of the sensor which sensor Yin, this is essential for the correct selection of the load cell, and it is related to the sensor can work as well as its safety and service life, and the whole weighing the reliability and safety sex. On the basic concepts and methods of evaluation of the major technical indicators of the load cell, the new and old GB qualitative differences.The traditional concept, the load sensor weighing sensors, force sensors, collectively referred to using a single parameter to evaluate its measurement properties. Old GB will be completely different application objects and the use of environmental conditions "weighing" and "measured force" two sensors into one to consider, not given to distinguish between the test and evaluation methods. Old GB total of 21 indicators, were tested at room temperature; and non-linearity, hysteresis error, repeatability error, creep, the additional error of the zero temperature and the maximum error in the six indicators of the rated output additional temperature error, to determine said The level of accuracy of the weight sensor, respectively 0.02,0.03,0.05 said.Proportion to convert the output signal can be measured. Taking into account the different place of use of the acceleration due to gravity and air buoyancy on the conversion, the main performance indicators of the load cell linearity error, hysteresis error, repeatability error, creep, zero-temperature characteristics and temperature sensitivity characteristics. In a variety of weighing and measuring the quality of the system, usually the integrated error accuracy of the integrated control sensors, and integrated error band or scale error band (Figure 1) linked so that selection corresponds to a certain accuracy weighing weighing sensors. International Organization of Legal Metrology(OIML) requirements, sensor error with total weighing instrument error δ with Δ of 70% of the load cell linearity error, hysteresis error within the specified temperature range due to the effect of temperature on the sensitivity of the error the sum can not exceed the error band of δ. This allows the manufacturer of the components that make up the total measurement error adjustment to obtain the desired accuracy.The load cell conversion method is divided into photoelectric, hydraulic, electromagnetic force type, capacitive, magnetic poles change the form of vibratory gyroscope ceremony, resistance strain type, to the most extensive use of resistance strain.Electromagnetic force sensorIt uses a load-bearing stage load and the principle of electromagnetic force Equilibrium (Figure 5). Put the loading stage, the measured object at one end of the lever upward tilt; photoelectric detect the tilt signal, amplified into the coil, the electromagnetic force, so that the lever to return to equilibrium. Currents produce electromagnetic counterweight digital converter, you can determine the quality of the measured object. The electromagnetic force sensor accuracy, up to 1/2000 ~ 1/60000, but the weighing range is only tens of mg to 10 kg.Capacitive sensorsItcapacitor oscillator circuit of the oscillation frequency f and the plate spacing d is directly proportional relationship between the work (Figure 6). There are two plates, one fixed and the other one can move. Bearing load measured object, the leaf spring deflection, the distance between the twoplates changes, the oscillation frequency of the circuit also changes. The measured frequency change can be calculated to the quality of the load-bearing stage, the measured object. Capacitive sensor power consumption, low cost, accuracy of 1/200 to 1/500.Pole change the form of sensorFerromagneticcomponents in the measured object gravity under mechanical deformation, internal stress and cause changes in permeability, and also changes so that the induced voltage of the secondary coil wound on both sides of the ferromagnetic component (pole). Measure the voltage variation can be calculated added to the force on the pole, and then determine the quality of the measured object. Pole to change the form of sensor accuracy is not high, usually 1/100, applicable to the large tonnage weighing, weighing ranging from tens to tens of thousands of kilograms.Vibration sensorThe force of the elastic element, the natural vibration frequency of the force is proportional to the square root of. Measure the natural frequency changes, you can find the measured object role in the elastic component of the force, and then calculate the quality. The vibration sensor vibrating wire and tuning fork.The elastic component of the vibrating wire sensor string wire. When the load-bearing stage, plus the measured object, the intersection of the V-shaped string wire is pulled down, and left strings of tension increases, the right string tension decreases. The natural frequency of the two strings of different changes. Calculate the frequency difference between the two strings, you can find the quality of the measured object. The higher the accuracy of the vibrating wire sensor, up to 1/1000 ~ 1/10000, weighing 100 g to hundreds of kilograms, but the structure is complex anddifficult process, and high cost.The elastic component of the tuning fork sensor is a tuning fork. Fixed tuning fork end of the piezoelectric element, the natural frequency of oscillation of a tuning fork, it can be measured oscillation frequency. When the load-bearing stage and the measured object, the tuning fork direction of tensile force while the increase in natural frequency, increasing levels of applied force is proportional to the square root. Measure the changes of natural frequency can be calculated heavy loads imposed on the tuning fork on the force, and then calculate the quality of heavy objects. The tuning fork sensor power consumption, measurement accuracy up to 1/10000 to 1/200 000, weighing range of 500g ~ 10kg.外文参考文献中文翻译参考资料二:摘要: 为解决现代商业贸易和日常生活中经常遇到的测量小质量物体的重量问题, 介绍了一种新型的袖珍式电子秤的设计。
传感器外文翻译

毕业设计(论文)外文文献翻译院系:光电与通信工程年级专业:12电子信息工程姓名:刘燊学号:1106012133附件:Advances in Sensor Technology Development指导老师评语:指导教师签名:年月日——摘自夏伟强,樊尚春传感器技术的的新发展仪器仪表学报传感器技术的新进展传感器技术是新技术革命和信息社会的重要技术基础,是一门多学科交叉的科学技术,被公认为现代信息技术的源头。
近些年,传感器技术发展很快,取得了许多新进展,尤其在气体传感器、生物传感器、视觉传感器等方面取得了很多进展。
美国麻省理工学院华人科学家张曙光领导的研究小组借助一种特殊溶液,成功地找到了大规模制造嗅觉感受器的办法;同样是麻省理工学院的研究人员利用气相色谱-质谱技术感受识别气体分子,研制出一种能对微量有毒气体做出强烈反应的微型传感器;俄罗斯科学家以从一种普通蘑菇中提取的混合物为原料,与压电石英晶振构成谐振式传感器,能够探测空气中含量极低的酚成分;日本科学家研制出能快速识别流感病毒纳米传感器,有望以纳米技术为快速识别流感病毒、乙型肝炎病毒、疯牛病病原体和残留农药等物质提供新手段;西班牙巴塞罗那自治大学研制出新型缩微DNA分析传感器,这种传感器能将分析 DNA链的时间缩短到几分钟或几小时,智能仪器与传感器技术、空间生物智能传感技术。
可以在亲子鉴定到检测遗传修饰食物的一系列化验中应用,此外还能确定新药的遗传毒性;美国国家标准与技术研究院研发出一种超灵敏微型核磁共振(NMR)传感器,该微型传感器与微流体通道并列置于一个硅芯片之上,这项技术将核磁共振的探测灵敏度提升到一个新的台阶,将在化学分析中具有广泛的应用前景。
我国传感器技术虽然与国外相比还有很大差距,但近两年也取得了一些进展和突破,诞生了一些新产品,有些在国家重大型号工程中获得应用。
如资源环境技术领域中的环境监测及环境风险评价技术、大气复合污染关键气态污染物的快速在线监测技术和大气细粒子和超细粒子的快速在线监测技术,海洋技术领域中的海洋水质污染综合参数在线监测技术和海洋金属污染物现场和在线监测技术等。
智能红外传感器中英文对照外文翻译文献
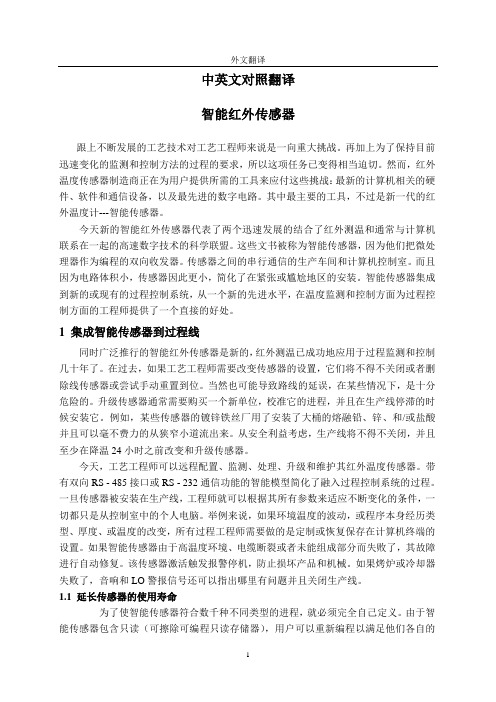
外文翻译中英文对照翻译智能红外传感器跟上不断发展的工艺技术对工艺工程师来说是一向重大挑战。
再加上为了保持目前迅速变化的监测和控制方法的过程的要求,所以这项任务已变得相当迫切。
然而,红外温度传感器制造商正在为用户提供所需的工具来应付这些挑战:最新的计算机相关的硬件、软件和通信设备,以及最先进的数字电路。
其中最主要的工具,不过是新一代的红外温度计---智能传感器。
今天新的智能红外传感器代表了两个迅速发展的结合了红外测温和通常与计算机联系在一起的高速数字技术的科学联盟。
这些文书被称为智能传感器,因为他们把微处理器作为编程的双向收发器。
传感器之间的串行通信的生产车间和计算机控制室。
而且因为电路体积小,传感器因此更小,简化了在紧张或尴尬地区的安装。
智能传感器集成到新的或现有的过程控制系统,从一个新的先进水平,在温度监测和控制方面为过程控制方面的工程师提供了一个直接的好处。
1 集成智能传感器到过程线同时广泛推行的智能红外传感器是新的,红外测温已成功地应用于过程监测和控制几十年了。
在过去,如果工艺工程师需要改变传感器的设置,它们将不得不关闭或者删除线传感器或尝试手动重置到位。
当然也可能导致路线的延误,在某些情况下,是十分危险的。
升级传感器通常需要购买一个新单位,校准它的进程,并且在生产线停滞的时候安装它。
例如,某些传感器的镀锌铁丝厂用了安装了大桶的熔融铅、锌、和/或盐酸并且可以毫不费力的从狭窄小道流出来。
从安全利益考虑,生产线将不得不关闭,并且至少在降温24小时之前改变和升级传感器。
今天,工艺工程师可以远程配置、监测、处理、升级和维护其红外温度传感器。
带有双向RS - 485接口或RS - 232通信功能的智能模型简化了融入过程控制系统的过程。
一旦传感器被安装在生产线,工程师就可以根据其所有参数来适应不断变化的条件,一切都只是从控制室中的个人电脑。
举例来说,如果环境温度的波动,或程序本身经历类型、厚度、或温度的改变,所有过程工程师需要做的是定制或恢复保存在计算机终端的设置。
新型传感器的研究现状及未来发展趋势

新型传感器的研究现状及未来发展趋势传感器是一种现代化技术所必需的元件,它能够将各种物理量转化为电信号。
传感器的应用范围广泛,例如自动化生产、交通运输、医疗诊断、安全监测等领域,因此传感器技术的发展对现代化生产、生活、科学技术的发展有着非常重要的作用。
传感器的种类很多,根据测量的物理量不同,可以分为温度传感器、压力传感器、流量传感器、湿度传感器、加速度传感器、光学传感器等等。
在这些传感器中,新型传感器是一种备受关注的技术。
一、新型传感器的研究现状1. MEMS技术传感器MEMS是微电子机械系统(Micro-Electro-Mechanical System)的缩写,它是一种微型化的电气机械系统,它能够将机械元件和电子元件进行集成化处理。
因此,MEMS技术传感器的优势在于体积很小、功耗低、响应速度快、可靠性高、价格便宜等等。
如今,MEMS技术传感器的应用已经非常广泛,例如手机中的加速度传感器、陀螺仪、磁力计、压力传感器等等,这些传感器的应用大大提升了手机的功能和用户体验。
2. 光纤传感器光纤传感器是一种基于光学原理的传感器,它使用光的传输来测量物理量。
与传统传感器相比,光纤传感器具有很多优势,例如高灵敏度、抗干扰能力强、安全可靠、经济实用,能够实现长距离传递、分布式检测等等。
目前,光纤传感器主要应用在石油天然气、交通运输、环境监测、生命科学等领域。
例如,在石油天然气开采中,光纤传感器可以测量油井的温度、压力、流量等参数,可以帮助确定油井的产量和工作状态,并且可以提高油井的生产效率。
3. 生物传感器生物传感器主要是应用在医疗诊断领域中的,它能够检测人体内的生物分子、细胞和组织等信息。
例如,可以测量血液中的血糖、白细胞计数、酸碱度等指标,可以帮助医生进行疾病的诊断和治疗。
目前,生物传感器技术发展非常迅速,尤其是以DNA、RNA 等为基础的生物传感器,它可以快速、准确地检测病原体、基因变异等信息,有望成为未来医疗诊断中的主要手段。
外文翻译原文及译文-基于51单片机的电子秤设计

外文文献翻译译稿1基于电阻应变式称重传感器的高精度和低容量电子秤开发Baoxiang He,Guirong Lu ,Kaibin Chu ,Guoqiang Ma摘要:基于称重传感器的应变计优化设计中除了一些先进的稳定技术比如温度的影响之外,静态超载和计算机模式识别(CRT)技术也被用来进行动态模拟与分析。
这种多谐振荡的压力释放方法是在生产中创造性的使用了压力传感器,由于这种技术,量程30G的压力传感器才能做到高精度,高稳定性。
由于使用了这种压力传感器,使得基于传感器的电子秤拥有300,00种分类和小于0.2mg的精度。
这种压力传感器的量程和精度远远高于市场上的同类产品,而其价格却远低于电磁压力传感器。
因此,这种压力传感器的商业前景是十分广阔的。
关键词:设计;电阻应变式称重传感器;精度;电子秤1.介绍众所周知,压力传感器的精度是决定一个的电子秤精度的关键。
目前,用于高精度称重的传感器主要是电磁平衡式称重传感器。
低成本电阻应变式称重传感器仅能用于使低精度的称量。
主要影响精度应变式称重传感器的误差是蠕变和温度漂移,特别是对于低负荷的传感器来说。
一般来说,高精度传感器的负载能力最低是300克。
称重传感器的最大分配平衡只有50K,最小分辨率是不小于0.01克。
总而言之,对于超低容量称重传感器来说设计和制造技术是很难被应用到敏感的称重传感器的加工和生产中的。
因此很难做出足够好的高精度平衡的称重传感器。
使得低量程和高精度的传感器始终是全世界的热门话题。
本文将分析应力释放及补偿技术,探索低量程高精度应变式称重传感器的制造技术。
2.原理与方法A. 残余应力的释放制作压力传感器主要部件的材料是铝棒。
为了获得更好的综合性能,铝条会在挤压后进行淬火。
由于淬火的残余应力不能被自然老化而得到充分释放,此外,机械加工和固化过程中也会造成很大的残余应力,特别是对于超低容量称重传感器来说,如果这个压力不及时释放,可能就会在压力传感器被测试或者是最终使用的时候释放出来。
- 1、下载文档前请自行甄别文档内容的完整性,平台不提供额外的编辑、内容补充、找答案等附加服务。
- 2、"仅部分预览"的文档,不可在线预览部分如存在完整性等问题,可反馈申请退款(可完整预览的文档不适用该条件!)。
- 3、如文档侵犯您的权益,请联系客服反馈,我们会尽快为您处理(人工客服工作时间:9:00-18:30)。
Development of Sensor New Technology Sensor is one kind component which can transform the physical quantity, chemistry quantity and the biomass into electrical signal. The output signal has the different forms like the voltage, the electric current, the frequency, the pulse and so on, which can satisfy the signal transmission, processing, recording, and demonstration and control demands. So it is the automatic detection system and in the automatic control industry .If automatic Technology is used wider, then sensor is more important. In information age, the information industry includes information gathering, transmission, process three parts, namely sensor technology, communication, computer technology. Because of ultra large scale integrated circuit’s rapi d development after having been developed Modern computer technology and communication, not only requests sensor precision reliability, speed of response and gain information content request more and more high but also requests its cost to be inexpensive. The obvious traditional sensor is eliminated gradually because of the function, the characteristic, the volume, the cost and so on. As world develop many countries are speeding up to the sensor new technology’s research and the development, and all has obtained the enormous breakthrough. Now the sensor new technology development mainly has following several aspects:Using the physical phenomenon, the chemical reaction, the biological effect as the sensor principle therefore the researches which discovered the new phenomenon and the new effect are the sensor technological improving ways .it is important studies to developed new sensor’s the foundation. Japanese Sharp Corporation uses the superconductivity technology to develop successfully the high temperature superconductivity magnetic sensor and get the sensor technology significant breakthrough. Its sensitivity is so high and only inferior in the superconductivity quantum interference component. Its manufacture craft is far simpler than the superconductivity quantum interference component. May use in magnetism image formation technology. So it has the widespread promoted value.Using the immune body and the antigen meets one another compound when the electrode surface. It can cause the electrode potential change and use this phenomenon to be possible to generate the immunity sensor. The immunity sensor makes with this kind of immune body may to some organism in whether has this kind of ant original work inspection. Like may inspect somebody with the hepatitis virus immune body whether contracts the hepatitis, plays to is fast, the accurate role. The US UC sixth branch has developed this kind of sensor.The sensor material is the important foundation for sensor technology, because the materials science is progressive and the people may make each kind of new sensor For example making the temperature sensor with the high polymer thin film; The optical fiber can make the pressure, the current capacity, the temperature, the displacement and so on the many kinds of sensors; Making the pressure transmitter with the ceramics. The high polymer can become the proportion adsorption and the release hydrogen along with the environment relative humidity size. The high polymer electricity lies between the constant to be small, the hydrogen can enhance the polymer the coefficient of dialectical loss. Making the capacitor the high polymerdielectric medium, determines the electric capacity cape city the change, then obtains the relative humidity. Making the plasma using this principle to gather the legitimate polystyrene film temperature sensor below, it has the characteristic.Measured the wet scope is wide; The temperature range is wide, may reach -400 ℃ ~ +1,500 ℃; The speed of response is quick, is smaller than 1S; The size is small, may use in the small space measuring wet; The temperature coefficient is small.The ceramic electric capacity type pressure transmitter is one kind does not have the intermediary fluid the dry type pressure transmitter. Uses the advanced ceramic technology, the heavy film electronic technology, its technical performance is stable, the year drifting quantity is smaller than 0.1%F.S, warm floats is smaller than ±0.15%/10K, anti- overloads strongly, may reach the measuring range several hundred times. The survey scope may from 0 to 60mpa.German E+H Corporation and the American Kahlo Corporation product is at the leading position.The optical fiber application is send the material significant breakthrough, its uses in most early the optical communication techniques. In the optical communication use discovered works as environmental condition change and so on the temperature, pres-sure, electric field, magnetic field, causes the fiber optic transmission light wave intensity, the phase, the frequency, change and so on the polarization condition, the survey light wave quantity change, may know causes these light wave physical quantity the and so on quantitative change temperature, pressure ,electric field, magnetic field size, uses these principles to be possible to develop the optical fiber sensor. The optical fiber sensor and the traditional sensor compare has many characteristics: Sensitivity high, the structure simple, the volume small, anti-corrosive, the electric insulation good, the path of rays may be curving, be advantageous for the realization telemeter and so on. Optical fiber sensor Japan is in the advanced level. Like Idec Izumi Corporation and Sun x Corporation. The optical fiber send receiver and the integrated path of rays technology unify, acce lerates the optical fiber sensor technology development. Will integrate the path of ray’s component to replace the original optics part and the passive light component; enable the optical fiber sensor to have the high band width, the low signal processing voltage, the reliability high, the cost will be low.In semiconductor technology processing method oxygenation, the photo etc hang, the proliferation, the deposition, the plane electron craft, various guides corrosion and steams plates, the sputtering thin film and so on, these have all introduced to the sensor manufacture. Thus has produced each kind of new sensor, like makes the silicon micro sensor using the semiconductor technology, makes the fast response using the thin film craft the gas to be sensitive, the wet sensitive sensor, the use sputtering thin film craft system pressure transmitter and so on..The Japanese horizontal river company uses various guides’corrosion technology to carry on the high accuracy three dimensional processing; the system helps the silicon resonance type pressure transmitter. The core partially presses two resonant Liang by the feeling which above the silicon diaphragm and the silicon diaphragm manufactures to form, two resonant Liang's frequency differencecorrespondence different pressure, measures the pressure with the frequency difference method, may eliminate the error which factor and so on ambient temperature brings. When ambient temperature change, two resonant Liang frequencies and the amplitude variation are same, after two frequency differences, its same change quantity can counterbalance mutually. It’s survey most high accuracy may reach 0.01%FS.American Silicon Microstructure Inc.(SMI) the company develops a series of low ends, linear in 0.1% to 0.In 65% scope silicon micro pressure transmitter, the lowest full measuring range is 0.15psi (1KPa), it makes take the silicon as the material, has the unique three dimensional structure, the light slight machine-finishing, makes the wheat stone bridge many times with the etching on the silicon diaphragm, when above silicon chip stress, it has the distortion, the resistance produces presses the anti- effect but to lose the bridge balance, the output and the pressure becomes the proportion the electrical signal.Such silicon micro sensor is the front technology which now the sensor develops, Its essential feature is the sensitive unit volume is a micron magnitude, Is the traditional sensor several dozens, several 1%. In aspect and so o n industry control, aerospace domain, biomedicine has the vital role, like on the airplane the use may reduce the airplane weight, reduces the energy. Another characteristic is can be sensitive is small surveyed, may make the blood pressure pressure transmitter.The Chinese aviation main corporation Beijing observation and control technical research institute, the development CYJ series splashes thanks the membrane pressure transmitter is uses the ion sputtering craft to process the metal strain gauge, it has over come the nonmetallic strain gauge easily the temperature influence insufficiency, has the high stability, is suitable in each kind of situation, is measured the medium scope widely, but also overcame the tradition lowly to glue the precision which the type brought, sluggish big, shortcoming and so on slow change, had the precision high, the re-liability is high, the volume small characteristic, widely used in domain and so on aviation, petroleum, chemical industry, medical service.Integrates the sensor the superiority is the traditional sensor is unable to achieve, it is a simple sensor not merely, it in at the same time the auxiliary circuit part and send the part will integrate on together the chip, will cause it to have the calibration, to compensate, from the diagnosis and the network correspondence function, it might reduce the cost, the gain in yield, this kind of blood pressure sensor which American LUCAS, NOV ASENSOR Corporation will develop, each week will be able to produce 10,000.The intellectualized sensor is one kind of belt microprocessor sensor, is achievement which the microcomputer and the sensor unifies, it has at the same time the examination, the judgment and the information processing function, compares with the traditional sensor has very many characteristics:Has the judgment and the information processing function, can carry on the revision, the error to the observed value compensates, thus enhancement measuring accuracy; May realize the multi-sensor multi parameters survey; Has from the diagnosis and from the calibration function, enhances the reliability; The survey datamay deposit and withdraw, easy to operate; Has the data communication interface, can and the microcomputer direct communication.The sensor, the signal adjustment electric circuit, the monolithic integrated circuit integration forms ultra large-scale integrated on a chip the senior intelligence sensor. American HONY WELL Corporation ST-3000 intelligence sensor, the chip size only then has 3×4×2mm3, uses the semiconductor craft, makes CPU, EPROM, the static pressure, the differential pressure, the temperature on the identical chip and so on three kind of sensitive units.The intellectualized sensor research and the development, US is at the leading position. American Space Agency when development spaceship called this kind of sensor for the clever sensor (Smart Sensor), on the spaceship this kind of sensor is extremely important. Our country in this aspect research and development also very backward mainly is because our country semiconductor integrated circuit technological level is limited.The sensor’s development is changing day after day since especially the 80's humanities have entered into the high industrialization the information age, sensor techno-logy to renewal, higher technological development. US, Japan and so on developed country sensor technological development quickest, our country because the foundation is weak, the sensor technology compares with these developed countries has the big disparity. Therefore, we should enlarge to the sensor engineering research, the development investment, causes our country sensor technology and the foreign disparity reduces, promotes our country instrument measuring appliance industry and from the technical development.传感器新技术的发展传感器是一种能将物理量、化学量、生物量等转换成电信号的器件。