控轧控冷习题答案
钢的控轧控冷试题

一.填空1 控制冷却钢材的强化主要是(1)、(2)、(3)引起的。
2 再结晶的驱动力是储存能。
它是以结构缺陷所伴生的能量方式存在。
影响储存能的因素可以分为:一类是工艺条件,其中主要是(4)、(5)、(6);另一类是材料的内在因素,主要是材料的(7)和(8)。
3 在冷却过程中,随着被冷却物与冷却物的温度差(即过热度)的增加,根据热流密度的不同可以分为四个区域,依次是(9)、(10)、(11)和(12)。
4 Ar3指的是(13)的温度,当冷却前奥氏体的残余应变增大时,Ar3的变化情况是(14)当冷却速度加快时,Ar3的变化情况是(15)。
5 在(A+F)两相区变形时,使其强度升高的因素有16)、(17)、(18)和(19),其中最主要的是(20)。
二.名词解释1)控制轧制2)韧性3)静态再结晶临界变形量4)形变诱导析出三.问答1 简述钢材强化的几种主要机制,并说明他们对钢材韧性的影响。
2 说明热变形过程中各阶段的回复再结晶、应力和组织演变情况。
3 简述控制轧制过程各个阶段Nb(C、N)的析出状态。
4 简述微合金元素在控制轧制和控制冷却中的作用。
5 何为一次冷却、二次冷却和三次冷却?简述其冷却目的和要求。
6控制轧制和控制冷却时Nb在奥氏体中有哪三种主要存在形式?们对阻碍再结晶和细化晶粒贡献大小如何?7 简述在(F+A)两相区轧制时的组织演变。
四.阅读资料回答问题。
武钢1700热连轧机根据其设备特点和条件,采用控制轧制和轧后控制冷却工艺生产出X-60、X-65级管线用钢。
为了获得良好的钢板综合性能,在冶炼时采取了相应技术,进行低碳、低硫和碳化物变性处理,并进行了Nb的微合金化。
钢的成分如下,X-60级钢:0.083~0.12%C,0.20~0.33%Si,1.08~1.32%Mn,0.012~0.020%P、0.004~0.021%、0.028~0.040Nb。
问题:1)说出钢中各种化学元素的作用。
2)X-65钢的C含量比X-60钢的要低,这将导致C的固溶强化效果减弱,可以采用哪些措施来弥补?(X-65钢的性能指标比X-60钢的性能指标要高)3)根据资料判断,生产中采用的控制轧制可能是哪种类型?4)从表中可以看出,产品的A k值纵横方向差别很大,可能是什么原因造成的?该如何改进?参考答案一填空1.(1)铁素体晶粒细化(2)贝氏体量增多(3)C、N化物的析出。
控轧控冷-3

变形条件对Ar3温度的影响
变形对Ar3温度的影响有两 种情况: 一种是在奥氏体再结晶区 变形后造成奥氏体晶粒的细 化,从而影响Ar3温度。 另一种情况是在奥氏体未 再结晶区变形后造成变形带 的产生和畸变能的增加,从 而影响Ar3温度。通常把这 种情况造成的影响称为形变 诱导相变。
• 加热温度的影 响 • 轧制温度的影 响 • 变形量的影响 • 冷却速度的影 响
从再结晶奥氏体晶粒生成铁素体晶粒
大量试验证明,钢中魏氏组织的形成主要取决于钢 的化学成分,奥氏体晶粒的大小和冷却速度。
在亚共析钢中最容易形成魏氏组织的含碳量范围为 0.15~0.5 %。因为低于 0.15 % C ,由于块状铁素体 的发展妨碍了魏氏组织的形成。而大于0.5%C的钢, 由于网状铁素体形成后珠光体很快就形成了,也阻 碍了魏氏组织的形成。 再者,按照铌钢>普碳钢>钒钢的顺序,铌钢最容易 生成魏氏组织。
3.2 变形条件对奥氏体相变的影响
一、变形条件对奥氏体向铁素体转变温度Ar3的影响
二、变形条件对奥氏体向珠光体、贝氏体转变的影响
变形条件对奥氏体向铁素体 转变温度Ar3的影响
由于在奥氏体未再结晶区轧制实现Ⅱ型转变能 获得细小的铁素体晶粒,同时又由于在奥氏体未再 结晶区轧制与在奥氏体 +铁素体区(即A+F的两相 区)中的轧制的结果是不同的,因此准确地确定奥 氏体向铁素体转变温度Ar3是有实际意义的。 测定变形条件下Ar3温度的方法
从部分再结晶奥氏体晶粒生成铁素体晶粒
再结晶的晶粒细小,在其晶界上析出的铁素体往往也较细 小。而未再结晶的晶粒受到变形被拉长,晶粒没有细化。 因此铁素体成核位置可能少,容易形成粗大的铁素体晶粒 和针状组织。所以从部分再结晶奥氏体晶粒生成的铁素体 是不均匀的,这种不均匀性对强度影响不太大。但对材料 的韧性有较大的影响,因此是不希望的。 如果在部分再结晶区进行多道次轧制,由于轧制温度逐渐 下降,最后未能达到奥氏体完全再结晶。但这时部分再结 晶晶粒的平均晶粒尺寸减小或晶粒中的未再结晶晶粒受到 了比较大的变形,晶粒不仅被拉长,晶内还可能出现较多 的变形带。因此转变后亦能得到细小的铁素体晶粒,整个 组织的均匀性和性能都能得到改善。
轧钢工-选择题599

1.常见的板形缺陷有( )。
A.镰刀弯 B.浪形 C.瓢曲 D.横向厚差答案:ABC2.国标中规定基本视图共有( )个。
A.3 B.4 C.6答案:A3.下列钢号中哪个是铸钢牌号( )。
A.A3F B.T8MnA C.ZG50 D.70答案:C4.纯铁的熔点为( )。
A.1548℃ B.1438℃ C.1538℃ D.1638℃答案:C5.供给轧辊冷却水的作用是( )。
A.润滑 B.降低轧件温度 C.降低轧辊温度 D.清除氧化铁皮答案:C6.连轧生产中(小断面),为保证有一恒定小张力,一般采用( )。
A.电机调速来实现 B.活套来实现C.增大或减少压下量来实现 D.增加轧制速度答案:B7.轧件轧制时,头部上翘的原因是( )。
A.上表面温度高 B.下辊直径小 C.下表面温度高 D.下卫板过低答案:C8.轧件被轧辊咬入的力是轧辊与轧件之间的( )。
A.张力 B.摩擦力 C.轧制力 D.弹力答案:B9.评定金属的塑性有( )。
A.伸长率 B.断面收缩率 C.金属的强度答案:AB10.氧化铁皮有多种,有利于酸洗去除的是( )。
A.Fe3O4 B.FeO C.Fe3C D.Fe2O3答案:B11.轧钢生产中的导卫装置作用是( )。
A.改变孔型 B.帮助轧制 C.诱导轧件 D.改变断面答案:C12.宽度系数计算式是( )。
A.β=b/B B.Δb=b-B C.K=Δb/Δh D.Δb=B-b答案:C13.轧制常见的故障有( )。
A.咬入不良 B.打滑 C.贴辊 D.横钢 E.断辊答案:ABCDE14.影响轧辊辊缝形状的因素有哪些( )。
A.轧辊弹性弯曲变形 B.轧辊热膨胀 C.轧辊磨损D.轧辊弹性压扁 E.原始辊型答案:ABCDE15.当轧机轧制压力大时,轧机的轴承一般选用( )。
A.布胶轴瓦 B.油膜轴承 C.滚动轴承答案:B16.轧辊辊身处强度计算是( )。
A.计算扭转 B.计算弯曲 C.扭转、弯曲合成计算答案:B17.热轧薄板连轧机的压下装置应选用( )。
高级轧钢工无纸化试题及答案7
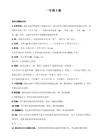
5 、 轧钢机主传动装置的作用是把主电机的动力传给齿轮座。
正确答案:× 您的答案:
6 、 在金属进行压力加工时,如果金属受三向拉应力状态,则对其塑性变形是不利的。
正确答案:√ 您的答案:
7 、
减速机用来将电动机的动力传递分配给轧辊。
54 、
产品标识主要是为了满足( )。
A.产品的可追溯性要求 B.便于查询 C.标准规定 D.作业文件规定
正确答案:A 您的答案:
55 、
带钢宽度大于1米 C.70 mm D.80 mm
51 、
轧辊的辊缝在孔型轮廓之内的叫( )。
A.开口孔型 B.闭口孔型 C.半闭口孔型 D.半开口孔型
正确答案:A 您的答案:
52 、
按钢的化学成份分类,钢可分为( )。
A.结构钢、工具钢、特殊钢 B.平炉钢、转炉钢、电炉钢
正确答案:B 您的答案:
58 、
12.( )是轧机最大的消耗件。
A.轧辊 B.压下螺丝 C.压下螺母 D.机架
正确答案:A 您的答案:
59 、
当乳化液酸值下降时,会出现( )现象。
A. 皂化值上降 B. 皂化值下降 C. 皂化值不变 D.二者没有联系
正确答案:× 您的答案:
3 、 轴向轴瓦用来承受轧辊的轴向力。
正确答案:√ 您的答案:
4 、 金属的不均匀变形,加热的不均匀性,轧后的不均匀冷却及金属的相变等,都可以促使金属的内部产生内力。
正确答案:√ 您的答案:
63 、
超声波探伤试缺陷的位置主要依据探伤图形中显示的( )。
A. 缺陷回波 B. 固有信号 C. 假象信号 D.杂乱信号
轧钢问答题

1.产生打滑的原因答案:产生打滑的原因是钢坯由于加热温度高时间长氧化铁皮严重,并不易脱落,或者压下量过大;遇到这种情况,可降低轧辊转速,并启动工作辊道给轧件以推力,使之顺利通过轧槽;2、轧制过程中金属变形时遵循什麽规律答案:1轧制过程中,金属变形时遵循剪应力定律;2金属纵向、高向、横向的流动又符合最小阻力定律;3轧制前后的塑性变形轧件遵循体积不变定律;产生;3.为什么精轧机组采用升速轧制答案:为了安全生产防止事故,精轧机组穿带速度不能太高,并且在带钢轧出最终机架之后,进入卷取机之前,带钢运送速度也不能太高,以免带钢在辊道上产生飘浮;因此,采取低速穿带然后与卷取机同步升速进行高速轧制的办法,可使轧制速度大幅度提高;采用升速轧制,可使带钢终轧温度控制得更加精确和使轧制速度大为提高,减少了带钢头尾温度差,从而为轧制更薄的带钢0.8毫米创造了条件;4.加热的目的是什么答案:①提高钢的塑性;②使坯料内外温度均匀;③改变金属的结晶组织:坯料的不均匀组织结构及非金属夹杂物形态与不均匀分布,在高温加热中扩散而改善了结晶组织;对于高速钢,长时保温可消除或减轻碳化物的偏析;坯料加热的质量直接影响到板带钢的质量、产量、能耗及轧机寿命;5.板带轧机压下装置的特点是什么答案:1轧辊调整量小;2调整精度高;3经常的工作制度是“频繁的带钢压下”;4必须动作快,灵敏度高;5轧辊平行度的调整要求严格;6.影响轧辊辊缝形状的因素有哪些答案:1轧辊的弹性弯曲变形;2轧辊的热膨胀;3轧辊的磨损;4轧辊的弹性压扁;5轧辊的原始辊型;7.轧辊调整装置的作用有哪些答案:轧辊调整装置的作用有:1调整轧辊水平位置调整辊缝,以保证轧件按给定的压下量轧出所要求的断面尺寸;2调整轧辊与辊道水平面间的相互位置,在连轧机还要调整各机座间轧辊的相互位置,以保证轧线高度一致调整下辊高度;3调整轧辊轴向位置,以保证有槽轧辊对准孔型;4在板带轧机上要调整轧辊辊型,其目的是减小板带材的横向厚度差并控制板形;8.卷取机的助卷辊的作用是①准确地将带钢头部送到卷筒周围;②以适当压紧力将带钢压在卷筒上增加卷紧度;③对带钢施加弯曲加工,使其变成容易卷取的形状;④压尾部防止带钢尾部上翘和松卷;9.钢的强度与硬度有什么关系答案:钢材抵抗硬物体压入的能力,称为硬度;钢的抗拉强度与硬度之在一定条件下存在一定的关系,σb=,一般硬度越高强度也越高,所以可以通过测定钢的硬度粗略地换算出钢的抗拉强度;10.什么叫轧辊消耗答案:生产一吨合格的轧制产品耗用的轧辊重量叫做轧辊消耗量,也叫辊耗,以kg/t为计算单位;11.轧机主电机轴的力矩有哪几种传动轧钢机轧辊所需的电动机轴上的力矩由四部分组成:轧制力矩,附加摩擦力矩,空转力矩,动力矩;M总=M轧+M摩+M空+M动M轧——轧制力矩;M摩——传至电动机轴上的附加摩擦力矩;此摩擦力是当轧件通过轧辊时,在轧辊轴承、传动机构及轧钢机其它部分中产生的,但没有考虑轧钢机空转时所需力矩;M空——空转力矩;M动——在电动机轴上的动力矩,即克服由于轧辊不均匀转动而产生的惯性力所需力矩;12.影响辊型的主要因素是什么轧辊的弹性变形;圆柱体的轧辊在轧制过程中受力产生弯曲,造成钢板中部厚,边部薄,为了弥补这种变形不均,应把轧辊做成凸形;轧辊辊身温度不均匀引起轧辊不均匀热膨胀,一般在钢板生产过程中轧辊中部温度高,边部温度低,这种温度不均导致轧辊变为凸形;因此预先考虑的轧辊形状应为凹形;轧辊的不均匀磨损;一般轧辊中部磨损快,边部磨损慢,这种磨损不均也使轧辊辊形发生变化;13.为什么热轧带钢轧制过程中会有甩尾发生答案:失张上游连轧机架张力过大;活套参数设定不合理;机械液压故障;电气时序、自动化、传输信号故障;14、影响宽展的因素有哪些答案:影响宽展的因素:压下量、轧辊直径、摩擦系数、前后张力、轧制温度、轧制速度、金属的化学成分等对宽展都有影响;15.铁的同素异构转变反应式如何表达答案:16.为什么在高温时轧制力小答案:随着温度的提高各种金属和合金的所有强度指标屈服极限、强度极限及硬度等均降低,这是因为随着温度的提高,金属原子热振动的振幅增大,原子间的键力减弱,从而金属产生塑性变形所需要的能量减小,变形抗力降低;17.压下规程所包括的内容有哪些答案:1原料选择;2拟定轧制方案;3计算总延伸率;4确定轧制道次;5拟定温度制度和速度制度;6选择合理的道次压下量;18.热装热送的优缺点是什么答案:热装热送是连铸坯从连铸机出来后不经过加热或保温炉保温,或连铸坯在较高的温度下入炉稍经加热即送往轧钢积进行的轧制过程;其优点是:可以节约大量的能源,促进炼钢生产的发展,推动轧钢的技术进步,实现炼钢和轧钢生产的合理匹配;其缺点是:因为连铸坯在加热状态下入炉,无法进行局部表面缺陷的检查和清理,因此热装热送要求提高连铸坯的质量,达到无缺陷的要求;19.根据室温组织及含碳量钢如何分类答案:1亚共析钢:<C<%;2共析钢:C=%;3过共析钢:%<C<%;20.热轧工艺润滑优点答案:①轧制压力、电流减低;②轧辊磨损减少;③改善产品质量;④轧机作业率提高; 21.在轧制过程中摩擦系数的大小与哪些因素有关答案:①轧制温度;②轧辊材质;③轧辊表面状态;④压下量;22.说出10种常见的热轧带钢质量缺陷答案:结疤、气泡、表面夹杂、分层、裂纹、氧化铁皮、辊印、压痕、划伤、波浪、边裂、麻点;23.质量管理常用的统计方法有哪些答案:常用统计方法有:①直方图;②排列图;③因果图;④相关图;⑤管理图;⑥调查图;⑦分层法;24.铁素体轧制技术具有哪些优势答案:1降低加热能耗;2提高金属收得率;3降低吨钢轧辊消耗;4提高带钢表面质量;5后续加工时可不经冷轧;6降低冷轧轧制力;25.立辊轧机有什么用途答案:1用于破鳞;在轧制过程中,大立辊能起疏松板坯表面氧化铁皮的作用;再用高压水冲击,可以取得较好的除鳞效果;2用于侧边轧制;板坯经侧边轧制后,可以防止轧件边缘产生鼓形和裂边;并能调节带材的宽度规格,获得宽度均匀、边缘整齐的带材,因而可降低金属消耗系数;26.CVC辊型与弯辊的最佳配合是什么答案:CVC辊型和弯辊是CVC轧机控制板形的两种独立控制方法;一般来说,一种方法只能控制一种简单的板形缺陷对称边浪或中间浪,两种方法才能控制第一种简单的板形缺陷又控制第二种较复杂的板形缺陷复合浪;理论上最佳配合的目标函数是出口带材的横向张力分布均匀,使总张力消失后带材平直度达到板形精度要求;27、精整工序主要担负着哪些工作答案:精整工序主要担负着钢材的冷却、矫直、剪切、记录、标识、收集、入库以及不合格品的加工修整等一系列工作;28.控制轧制和控制冷却技术的主要优点是什么答案:1提高钢材的综合力学性能;控制轧制和控制冷却技术可使铁素体晶粒细化,从而使钢材的强度提高,韧性得到改善;2简化生产工艺过程;控制轧制和控制冷却技术可以取消常化等热处理工序;采用控制轧制和控制冷却技术生产的钢材的性能可以达到甚至超过现有热处理钢材的性能;3降低钢材生产成本;控制轧制和控制冷却技术因为具有上述优点,所以得到广泛的应用;29.简述轧机加速时轧件变薄的原因答案:轧机加速时,产品厚度减薄,该现象主要归结于两个因素:轧制速度变化引起轧辊与轧件之间摩擦系数的变化、轧制速度变化引起支撑辊油膜轴承油膜厚度变化;由于这两个原因,通过轧机加速,摩擦系数减少,同时油膜轴承油膜厚度变厚,辊缝减少,板厚出现减薄; 30.设定精轧机速度时需要注意哪些问题答案、1速度的调节问题;设定速度时不能把速度上下限作为速度设定基准值穿带速度,这样一旦轧制过程中速度调节,轧机速度将超过上限速度,而出现轧机跳闸或使速度不参与调节而出现堆套或拉钢;2轧制速度对轧制电流的影响,变形速度增加轧制电流会增加,当轧件温度低或轧件的变形抗力大时,过高的轧制速度会造成轧制电流大而跳闸;因此,设定速度时应看轧制电流是否在允许的范围内;31.简述制订压下规程的步骤答案:1在咬入能力允许的条件下,按经验分配各道次压下量;2制订速度制度,计算轧制时间并确定逐道次轧制温度;3计算轧制压力、轧制力矩及总传动力矩;4校验轧辊等部件的强度和电机功率;5对压下规程进行修正和改正;32.燃料稳定燃烧必须具备什么条件答案:1要不断的供应燃烧所需的燃料;2要连续供应燃烧所需要的氧气或空气;3要保证燃烧的燃料在一定的温度以上;33.热变形对金属铸压组织有哪些改造答案:通过热变形可使金属锭中的气孔焊合、压实,使材料的致密度增加;在温度和压力作用下,偏析可部分消除,使成份比较均匀,合理的热变形制度可细化晶粒;34.怎样防止断辊答案:①选择适宜的变形温度;②正确安装轧辊,选择宜适的变形条件;③导卫安装正确,避免缠辊,喂错孔,喂低温钢黑头钢;使变形抗力增加,超过轧辊强度极限;④使用质量好的轧辊,消除原始应力和存在铸造缩孔;35.什么叫变形制度答案:在一定的轧制条件下,完成从坯料到成品的变形过程就称为变形制度;其主要内容是确定总的变形量和道次变形量;变形量的分配是工艺设计的重要参数,它是轧制设备选择和孔型设计的主要依据;变形制度对轧机产量、产品质量起差重要的作用;初轧机的压下规程,型钢轧机的孔型设计,板带轧机的压下规程以及钢管轧机的轧制表面部分内部都属于变形制度;36.控制轧制对哪些方面进行控制答案:1变形温度的控制;2变形程度的控制;3变形速度的控制;4冷却速度的控制;5化学成份的控制;37.控制轧制是什么答案:控制轧制是严格控制非调质钢材的轧制过程,运用变形过程热动力因素的影响,使钢的组织结构与晶粒充分细化,或使在一定碳含量珠光体的数量减少,或通过变形强化诱导有利夹杂物沉淀析出,从而提高钢的强度和冲击韧性,降低脆性转变温度,改善炉接性能,以获得具有很好综合性能的优质热轧钢材;38.为什么控制轧制能提高钢材的机械性能答案:因为控制轧制是以细化晶粒为主线的轧制方法,众所周知,钢的晶粒越粗大,不仅其塑性差,而且强度和硬度也很差;因此细化晶粒的钢材强度和韧性都得到加强,而控制轧制就是采用各种手段使轧制出的成品是晶粒细化的产品,因此能提高其机械性能;39.如何降低金属的变形抗力答案:1要选择良好的变形温度;2把变形速度和变形程度控制在适当范围内;3采用工艺润滑新技术减少外摩擦;4采用合理的加工方式和外加工工具;40.铁碳平衡相图如何在轧制工艺上得到应用答案:根据铁碳平衡相图,可以制定各钢种的加热温度范围,开轧温度范围和终轧温度范围,这是铁碳平衡相图中温度与组织结构的关系向人们提供了参考依据,保证了各钢种加工是在可靠状态下进行,并最终获得理想的组织和性能;41.什么叫穿梭轧制答案:在同一机架或机列上进行往返的轧制过程,交替地将轧件的头部和尾部送入轧机,直至轧制出成品的轧制方式叫穿梭轧制,一般多用在横列式轧机上;42.什么叫层流冷却答案:为保证热轧带钢的性能,带钢在出精轧机组后,应从850℃左右的终轧温度迅速冷却到550~650℃的卷取温度,层流冷却就是为冷却带钢的一种方式,它采用低水压,大水量的冷却方式;它的特点是水流在带钢表面呈层流状,能冲破带钢表面的蒸气膜,没有飞溅,冷却效果好;43.为防止和减少折叠的产生应采取什么措施答案:1按标准要求安装导卫装置;2保证轧槽的冷却效果;3及时更换调整导卫,以保证稳定轧制过程;4控制好轧制节奏,保持料型稳定,减少轧槽磨损;5操作工要勤检查导卫,勤观察料型,勤看管冷却水管;6确保轧辊的轴向固定,不能有轧辊窜动现象出现;44.在热轧型钢生产中,常有采用万能孔型系统的,它们的优缺点是什么答案:优点:1易去除轧件的氧化铁皮,有利于改善成品质量;2万能孔型系统调整范围大,且共用性好;3轧件变形均匀,孔型使用寿命长,轧辊消耗低;4这种孔型系统易咬入,在成品孔内轧制稳定;缺点:1这种孔型系统延伸系数小;2轧件出立轧孔的形状不规正,且轧制不稳定,易产生扭转;45.轧钢车间常见的主电机型式有哪几种各有何优缺点答案:轧钢车间常见的主电机型式有直流电动机和交流感应异步电动机;直流电动机的优点是能在较大范围内平滑无级地调速,并可在运行中调速;它适用于生产多品种钢材轧机;其缺点是投资大,供电系统复杂;交流感应异步电机的优点是投资少,供电系统简单;缺点是效率低,调速困难;46.什么叫轧制力矩如何计算答案:轧制力矩就是轧制时垂直接触面水平投影的轧制压力与其作用点到轧辊中心线距离即力臂的乘积;轧制力矩是驱动轧辊完成轧制过程的力矩;按轧件给轧辊的压力进行计算:M=2Pa两根轧辊,其中P-轧制压力;a-力臂;47.轧钢机有哪些导卫装置答案:导卫装置是整钢轧机轧制中不可缺少的重要部件,为了使轧件按规定的位置、方向和所需的状态准确地进出孔型,避免轧件缠辊、轧件被刮切和挤钢并保证工人和设备的安全,轧辊前后都要安装导卫装置;具体应包括导板、上卫板、下卫板、导板盒、固定横梁、导管、扭转导板、扭转导管、扭转辊、升降台、翻钢导板、板带轧机护板、翻钢机、移钢机、反围盘、正围盘、立围盘及推床初轧机等;48.光学高温计的构造原理是什么答案:光学高温计是根据光度灯灯丝亮度与温度之间有对应关系的原理制成的,它用特别光度灯的灯丝发出的亮度与受热物体的亮度相比较的方法测得受热物体的温度;灯丝的亮度取决于流过灯丝的电流大小,调节滑线电阻可改变流过灯丝的电流,也就调节了灯丝的亮度;49.什么叫磁力探伤和超声波探伤答案:将试件置于探伤机强大磁场内,使其磁化,然后将氧化铁粉与汽油或酒精混合的悬浊液涂抹在试件表面上,此时氧化铁粉就聚集在那些表面或皮下有缺陷地方,这就是磁力探伤;超声波探伤是利用超声波的物理性质检验低倍组织缺陷,用这种方法可直接检查钢材的内部缺陷,例如检验锅炉管,还可检查大锻件的内部质量;这两种探伤属于无损检验;50.计算机在轧钢生产过程中的主要作用是什么答案:1生产管理,如编制生产计算程序,各种原始数据的通讯和反馈等;2生产过程控制,如生产工艺技术参数的设定及最优控制;3自适应控制;4直接数字控制;5生产过程程序控制;6制表显示,如班报、日报、月报,设定值和测量值报表;7故障诊断;51.工作辊磨损的主要形式有哪些答案:工作辊磨损形式主要有:1磨粒磨损;工作辊和轧件之间以及工作辊与支撑辊之间的研磨;2疲劳磨损;工作辊受周期性载荷的作用,表层会出现机械疲劳,同时周期性的受轧材的加热和水雾的冷却而导致表层热力学疲劳;3黏着磨损;当轧制较硬的材料时,高温轧件与辊面在压力下紧密接触,会产生轧辊黏着磨损;4剥落;它是一种疲劳破坏,能破坏轧辊的坚硬层,导致轧辊报废;52.影响轧件宽展的因素有哪些答案:1相对压下量;2轧制道次;3轧辊直径;4摩擦系数,包括轧制温度、轧制速度、轧辊表面状态、轧件的化学成分、轧辊的化学成分;53.钢坯在加热过程中会出现哪些缺陷答案:板坯加热过程中会出现以下缺陷:1过热和过烧;2氧化;3脱碳;4粘钢和加热不均;54.为什么轧制过程延伸远远大于宽展答案:①工具形状影响,延伸方向为凸形工具,利于延伸变形,而宽展方向为平板工具,不利于宽展变形;②由最小阻力定律,轧制变形区的金属向延伸方向流动阻力小于宽展方向,用于延伸的金属占的比例多,所以轧制过程延伸远远大于宽展;55.当今热轧带钢板型控制主要手段答案:①液压弯辊;②VCR变接触支持辊;③CVC轧机;④WRS轧机;⑤PC轧机;56.热轧精轧工作辊材质有什么要求何谓冷硬铸铁辊无限冷硬铸铁辊答案:精轧工作辊主要承受扭矩和压力,弯曲应力小,轧制速度高,辊面要求光滑,因此要求辊面硬度高;多采用铸铁轧辊;冷硬铸铁轧辊:轧辊的断面有白口的外层冷硬层、麻口的中间层过渡层和灰口的内层组成;无限冷硬铸铁轧辊;从坚硬的白口表面层直到辊心部分的灰口层,其整个过渡区无明显而严格的分界限,既有表面耐磨性好的冷硬层,又具有较高的抗热裂性和硬度;57.怎样制定精轧机组的轧制规程答案:①确定各架的相对压下量:可以从精轧各架相对压下量或负荷分配率的原则来进行各架压下量分配,也可根据电机功率合理消耗的观点出发进行分配;②确定各架的轧制速度:根据秒流量原理计算;③计算各架的轧制温度;④计算各道的平均单位压力;⑤校核各架电机的功率;58.简述影响钢过热、过烧的因素;答案:过热的主要因素:加热温度、加热时间和钢的化学成份;过烧的主要影响因素:加热温度、加热时间、钢的化学成份和炉内气氛;59.对钢的加热有什么要求答案:加热温度应达到规定的温度,不产生过热和过烧;坯料的加热温度应沿长度、宽度和整个端面均匀;氧化烧损最少;60.热带生产中,半连续式轧机的特点有哪些答案:热带生产中,半连续式轧机设备数量较少,设备布置的相互距离较近,主轧线较短,占地面积少,投资较低,可逆式粗轧机上轧制道次可灵活选择,生产灵活性大;设备利用率低,产品质量水平较低,生产和技术管理复杂;61.在轧制板带钢生产时,设置辊型的目的是什么答案:1控制板形,改善板形;2改善穿带条件,提高轧制的稳定性;3合理地使用轧辊;62.铁碳合金相图对轧钢生产有什么意义答案:通过铁碳合金相图可以知道,加热到某一温度的碳钢是什么相,并能分析出钢在缓慢加热和缓慢冷却过程中的组织转变,因此,铁碳合金相图是确定碳钢加热、开轧、终轧温度和碳钢热处理工艺的参考依63、简述影响变形抗力的参数有那些答:1材料化学成分2材料冶金特性3材料温度4变形区几何形状5变形程度6变形速度7变形区外摩擦64、简述影响轧制压力的因素有那些答:1绝对压下量2轧辊直径3轧件宽度4轧件厚度5轧制温度6摩擦系数7轧件化学成分8轧制速度65、热轧薄板在精轧尾部轧破的主要原因有哪些答: A:温度过低;B:轧制力设定偏差大;C:跑偏;D:抛钢速度过快;E:轧制线标高落差大;66简述低温轧制的优缺点是什么答:低温轧制的优点:在加热工序节省了能耗;减少了氧化烧损;减少了轧辊由于热应力引起的疲劳裂纹;减少了氧化铁皮对轧辊的磨损;低温轧制的缺点:增加了轧制力、轧制力矩和轧制功率;降低了轧制材料的塑性;影响轧材的咬入,降低了道次压下量;67、简述轧件在被咬入轧辊时发生打滑现象的主要解决措施;答:1增加轧辊辊面的粗糙程度即增加摩擦系数 2减少压下量降低压下负荷 3低咬钢速度4增加轧辊直径68、什么是辊跳它的大小取决于什么答:在轧制过程中,轧机各部件受轧制力的作用发生弹性变形,如机架窗口高度扩大,轧辊弯曲,压下系统和轴承受到压缩等,这些弹性变形最后反映在两轧辊之间的缝隙增大,轧制中这种辊缝增大的现象叫做辊跳;辊跳增大的总数称为辊跳指;辊跳值的大小取决于轧机的性能,轧制温度和轧制钢种等;69、什么叫加工硬化它有什么作用答:金属在加工后,由于晶粒被压扁、拉长,晶粒弯扭、晶粒破碎,使金属的塑性降低、强度和硬度增高,把这种现象叫做加工硬化;它是强化金属的方法之一,对纯金属及不能用热处理方法强化的金属来说尤其重要,另外,加工硬化也给金属的冷加工生产创造了条件;70、什么叫马氏体它有那些特性答:当奥氏体化的钢以大于临界冷却速度的速度从高温冷却道Ms以下时即马氏体开始转变温度,过冷奥氏体转变为马氏体;马氏体是碳在体心立方铁中的过饱和固溶体,具有体心立方晶格;马氏体组织很脆,硬度高,而韧性很低,马氏体形成时有很大的相变应力;71、什么叫板形影响板形的因素有那些答:板形是指板、带才平直度的简称,一般是指浪形、瓢曲或旁弯的有无及其程度;影响板形的因素有:1、原料断面形状2承载辊缝的断面形状:工作辊、支撑辊的弯曲挠度和剪切挠度;支撑辊、工作辊和带钢的弹性压扁、工作辊本身的凸度;3压下规程的变化72.在热轧生产中,如何确定开轧温度答案:开轧温度是指第一道的轧制温度,一般比加热温度低50~100℃,生产现场一般总希望开轧温度高一点,以便提高轧件的塑性,降低其变形抗力,节省动力,易于轧制变形;开轧温度的上限取决于钢的允许加热温度;开轧温度的下限主要取决于终轧温度的限制;轧件一般在整个轧制过程应保持单相奥氏体组织;近来控制轧制技术的发展,在如何确定合适的开轧温度上又增加了新的限制因素;73.在热轧生产中确定其终轧温度时有什么考虑答案:终轧温度是指热轧生产的终了温度,终轧温度的高低对轧制的产量和质量都有显着的。
轧钢专业质量检验工考试:轧钢质量检查工(初级)试题及答案

轧钢专业质量检验工考试:轧钢质量检查工(初级)试题及答案1、单选质量管理体系是由()构成的。
A.活动B.子系统C.过程D.程序正确答案:C2、填空题GB/T700-1988规定碳素结构钢在()合格(江南博哥)的情况下,各牌号的A级钢的碳、锰含量不作为交货条件。
正确答案:力学性能3、单选钢筋检验重量偏差合格时,钢筋的()尺寸不作交货条件。
A.纵肋B.横肋C.内径D.横肋末端间隙正确答案:C4、问答题什么叫纯金属?怎样分类?正确答案:人们通常将那些基本上由一种金属组成的材料或物质叫纯金属。
纯金属随其纯度的不同可分为工业纯金属和化学纯金属两类。
5、单选钢含碳量一般不超过()。
A.1%B.2%C.3%D.3.5%正确答案:B6、单选按定尺要求将钢材锯切成固定长度为()。
A.定尺长度B.倍尺长度C.通常长度D.短尺长度正确答案:A7、单选加热时间的确定主要是依据原料的()和尺寸。
A.长度B.宽度C.化学成份D.厚度正确答案:C8、单选作为拉拔原料的线材直径为()mm。
A.φ4-φ6B.φ5-φ8C.φ6-φ9D.φ5-φ9正确答案:D9、单选质量证明书是向客户提供()的保证。
A.数量B.包装C.产品质量特性D.运输安全正确答案:C10、填空题钢按化学成分分类可分()、低合金钢、合金钢三大类。
正确答案:非合金钢11、单选金属压力加工是()变形过程。
A.弹性B.塑性C.弯曲D.冲压正确答案:B12、单选牌号为“45”钢技术条件标准号()。
A.GB699B.GB700C.GB1499D.GB702正确答案:A13、单选低合金结构钢按用途分属()。
A.建筑及工程用钢B.结构钢C.工具钢D.电工用钢正确答案:A14、填空题混钢种且无法鉴别化学成份的产品应按()计算。
正确答案:废品15、单选()只要求具备较好的工艺性能。
A.一般结构钢板B.高温合金板C.不锈钢D.硅钢板正确答案:A16、填空题GB/T700-1988的规定,Q235A化学成分的含碳量是()。
轧钢工(初级工)考试精选试题,含答案

轧钢工(初级工)考试精选试题,含答案题目100、在带钢进入精轧机组前,用飞剪切除带钢头、尾的目的是()。
A、保证通板性B、改善板形C、取样检验D、提高成材率答案:A题目101、下列关于带钢卷取机夹送辊的叙述中()是正确的。
A、上辊角速度高于下辊速度B、上辊直径大于下辊直径C、上辊线速度小于下辊线速度D、上辊直径等于下辊直径答案:B题目102、在带钢生产过程中,平整机能够(),消除局部厚度偏差。
A、改善板形B、改善表面质量C、改善距偏D、改善性能答案:A题目103、轧件在运行中能使其自行翻转45度或不翻转的围盘叫()围盘。
A、正B、反C、立D、侧答案:A题目104、轧制节奏是指()。
A、开始轧制第一支钢到开始轧制第二支钢的延续时间B、一支钢从开始轧制到轧制完成所需要的时间C、单位时间内轧制钢的支数D、一支钢轧完到下一支钢开始轧制的空隙时间答案:A题目105、制定工艺过程的首要依据是()。
A、生产规模B、劳动条件C、产品的技术条件D、工艺流程答案:A题目106、()布置形式有最高的生产效率。
A、半连续式B、顺列式C、连续式D、可逆式答案:C题目107、45号钢属于()。
A、低碳钢B、中碳钢C、高碳钢D、合金工具钢答案:B题目108、70号钢属于()。
A、低碳钢B、中碳钢C、高碳钢D、合金工具钢答案:C题目109、不属于轧辊辊缝的作用的是()。
A、补偿轧辊的弹跳值B、使辊环或上下轧辊相互之间不摩擦C、增加孔型的宽展余地D、调节铁型答案:C题目110、槽钢的规格用()表示。
A、腰高B、腿长C、边长D、断面面积答案:A题目111、处理坯料严重缺陷时必须保证()。
A、清理深度等于缺陷深度B、清理宽度等于缺陷深度C、清理深度大于缺陷深度D、清理宽度等于清理深度答案:C题目112、带钢轧制出现边浪的根本原因是()。
A、压下率小B、中部压下率大C、边部压下量大D、边部压下量小答案:C题目113、单机座单根轧制时,轧制节奏与轧制周期的关系是()。
冷轧厂主控工考试题-答案-初中高级
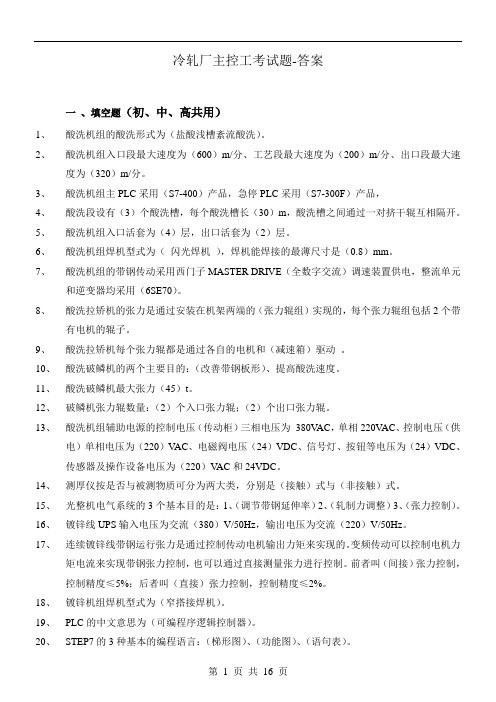
冷轧厂主控工考试题-答案一、填空题(初、中、高共用)1、酸洗机组的酸洗形式为(盐酸浅槽紊流酸洗)。
2、酸洗机组入口段最大速度为(600)m/分、工艺段最大速度为(200)m/分、出口段最大速度为(320)m/分。
3、酸洗机组主PLC采用(S7-400)产品,急停PLC采用(S7-300F)产品,4、酸洗段设有(3)个酸洗槽,每个酸洗槽长(30)m,酸洗槽之间通过一对挤干辊互相隔开。
5、酸洗机组入口活套为(4)层,出口活套为(2)层。
6、酸洗机组焊机型式为(闪光焊机),焊机能焊接的最薄尺寸是(0.8)mm。
7、酸洗机组的带钢传动采用西门子MASTER DRIVE(全数字交流)调速装置供电,整流单元和逆变器均采用(6SE70)。
8、酸洗拉矫机的张力是通过安装在机架两端的(张力辊组)实现的,每个张力辊组包括2个带有电机的辊子。
9、酸洗拉矫机每个张力辊都是通过各自的电机和(减速箱)驱动。
10、酸洗破鳞机的两个主要目的:(改善带钢板形)、提高酸洗速度。
11、酸洗破鳞机最大张力(45)t。
12、破鳞机张力辊数量:(2)个入口张力辊;(2)个出口张力辊。
13、酸洗机组辅助电源的控制电压(传动柜)三相电压为380V AC,单相220V AC、控制电压(供电)单相电压为(220)V AC、电磁阀电压(24)VDC、信号灯、按钮等电压为(24)VDC、传感器及操作设备电压为(220)V AC和24VDC。
14、测厚仪按是否与被测物质可分为两大类,分别是(接触)式与(非接触)式。
15、光整机电气系统的3个基本目的是:1、(调节带钢延伸率)2、(轧制力调整)3、(张力控制)。
16、镀锌线UPS输入电压为交流(380)V/50Hz,输出电压为交流(220)V/50Hz。
17、连续镀锌线带钢运行张力是通过控制传动电机输出力矩来实现的。
变频传动可以控制电机力矩电流来实现带钢张力控制,也可以通过直接测量张力进行控制。
前者叫(间接)张力控制,控制精度≤5%;后者叫(直接)张力控制,控制精度≤2%。
- 1、下载文档前请自行甄别文档内容的完整性,平台不提供额外的编辑、内容补充、找答案等附加服务。
- 2、"仅部分预览"的文档,不可在线预览部分如存在完整性等问题,可反馈申请退款(可完整预览的文档不适用该条件!)。
- 3、如文档侵犯您的权益,请联系客服反馈,我们会尽快为您处理(人工客服工作时间:9:00-18:30)。
注(重点):图形大致形状会画,abcd四点知道是什么意思!!!
(1)当ε远小于εL时(a点,a曲线),曲线a表示了两次变形间隔时间里软化情况与软化的速度。曲线a表明变形一停止软化就立即发生,随着时间的延长软化百分数增大,当达到一定程度,软化停止,此过程大约100秒内完成,这时仅仅软化了0.3,还有0.7的加工硬化不能消除。特点:静态回复可以部分减少位错,未消除的加工硬化对下次变形有迭加作用
在(Ⅰ)区中连续轧制时,如果变形温度较低,所给的变形量合适,那么全部晶粒都是未再结晶晶粒,它将随着轧制道次的增加(总变形量增加),晶粒拉长,晶内形变带逐渐增加并逐渐均匀。
5、奥氏体转化为铁素体分为几个类型?发生条件?特点?对钢材影响?(注:II型重点)
IA型:如果热轧后奥氏体发生再结晶,并且在转变前粗化成小于或等于ASTMNO.5级的奥氏体晶粒,那么转变时容易形成魏氏组织铁素体和珠光体
11、断裂韧性
指材料阻止宏观裂纹失稳扩展能力的度量,也是材料抵抗脆性破坏的韧性参数。断裂韧性是材料的一种性能,它取决于材料的组织结构
二、简答题:
1、奥氏体形变的真应力—真应变每个阶段的特点?
第一阶段:当塑性变形量小时,随着变形量的增加变形抗力增加,直到达到最大值。发生了加工硬化,动态回复和动态多边形化,随着变形量的增加,位错消失速度加快,也就是软化加快,但是总的趋势,在这一阶段加工硬化还是超过动态软化。反映在真阴历—真应变曲线上随着变形量加大变形应力还是不断增大的,只是增加速度逐渐减慢,直至为零。
(6)有比较短的冷却区长度(7)设备投资少,生产稳定,便于维修。
2、控轧控冷为什么能够改变金属组织,使组织变好?(重点)
当只采用控制轧制时:主要是通过控制轧制工艺参数,细化变形奥氏体晶粒,经过奥氏体向铁素体和珠光体的相变,形成细化的铁素体晶粒和较为细小的珠光体球团,从而达到提高钢的强度、韧性和焊接性能的目的。
铁素体加工时的动态软化方式是动态回复与动态多边形化,没有动态再结晶。在热加工过程中铁素体的亚晶不断的产生,又不断的原地消失,位错的增殖速度与消失速度保持平衡。
7、微合金元素溶液中由低到高排列顺序
TiN、AIN、NbN、TiC、VN、NbC、VC、TiN是最难溶解的,在1250摄氏度以上仍能看到稳定细小的颗粒。
目的:控制相变前奥氏体的组织状态,为相变做组织上的准备。快冷开始的温度越接近终轧温度,细化变形奥氏体和增大有效晶界面积的效果越明显。
二次冷却:从相变开始到相变借宿这段温度范围内的冷却控制
目的:通过控制冷却速度和冷却终止温度来控制相变过程,以保证快冷后得到钢材所要求的金相组织。
三次冷却:相变后至室温范围内的冷却。
再结晶区域图代表什么?意义?
代表:一道次轧制后钢的再结晶区域图,压下率大的部分发生完全再结晶,压下率低于再结晶临界变形量的部分只发生回复不发生再结晶,在这两者之间为部分再结晶区。
意义:产生部分再结晶的临界压下率和完成静态再结晶的临界压下率随着变形温度的降低而加大,热变形后在静态再结晶区所得到的再结晶晶粒尺寸,随变形量的增大而细化,受变形温度的影响较小。
柯式气团作用:对运动的位错起着钉孔作用,使屈服强度、抗拉强度提高。
形变强化
随着变形程度的增加,材料的强度、硬度升高,韧性和塑性下降的现象叫做形变强化或加工硬化。形变强化决定于位错运动受阻。
沉淀强化
细小的沉淀物分散于基体之中,阻碍位错运动,而产生强化作用,这就是沉淀强化。
细晶强化
通过细化晶粒而使金属材料的力学性能提高的方法。晶粒愈小,晶界愈多,晶界阻力愈大,材料的屈服强度提高。
形成魏氏组织的倾向在含铌钢中最强烈,其次是非合金钢,含钒钢最弱。
IB型:如果热轧后奥氏体发生再结晶,在转变前奥氏体晶粒是ASTMNNo.6级或更细,则转变就按IB型进行。
Ⅱ型:如果热轧温度低,热轧后变形的奥氏体晶粒不发生再结晶,则奥氏体向铁素体的转变将按Ⅱ型进行。Ⅱ型转变之中,不形成魏氏组织和上贝氏体。
一、名词解释:
钢的强化方式
固溶强化、形变强化、析出(沉淀)强化与弥散强化、细晶强化、亚晶强化、相变强化、
韧性概念
韧性(又名韧度)是材料塑形变形用添加溶质元素使固溶体强度升高的现象称为固溶强化
柯式气团
在过饱和的固溶体中,由于C、N原子有很好的扩散能力,可以直接在位错附近和位错中心聚集,形成柯式气团。
亚晶强化
亚晶强化的原因是位错密度提高。
相变强化
通过相变而产生的强化效应称为相变强化。
10、冲击韧性
工程上常用一次摆锤冲击弯曲试验来测定材料抵抗冲击载荷的能力,即测定冲击载荷试样被折断而消耗的冲击功Ak,单位为焦耳(J)。材料的冲击韧性指标主要是冲击功,即缺口冲击韧性Ak(J)或ak(J)值,和韧脆转变温度Tc
要求:(1)能比较均匀冷却整块钢板,确保冷却均匀,组织均匀,钢板性能均匀。
(2)尽量减少快冷过程中钢板中引起较大残余应力和不均匀变形,要防止冷却钢板变形
(3)保证有足够的钢板冷却速度,满足轧后快冷式直接淬火要求
(4)能准确的控制,调整冷却速度和控制开冷及终冷温度
(5)钢板上下表面冷却水的流量比调整范围较大,而且调整时不破坏冷却状态
(2)奥氏体未再结晶控制轧制特点:(1)奥氏体未再结晶区的温度变化范围在950~Ar3温度区间,特点主要是在轧制过程中不发生奥氏体再结晶现象。(2)塑性变形使奥氏体的晶粒拉长,在晶粒内形成变形带的碳氮化合物的应变诱发沉淀。(3)随着变形量的加大,变形带的数量也增多,而且在晶体内分布的更加均匀,相变后的铁素体晶粒也更加均匀细小。(4)未再结晶区的轧制导致钢的强度提高和韧性的改善。(5)在拉长的奥氏体晶粒边界、滑移带等优先析出碳化物颗粒。加大变形量使相变温度提高,促使多边形的铁素体数量增多,珠光体的数量减少
(3)奥氏体和铁素体两相区控制轧制特点?
(1)在两相区变形后,由变形奥氏体转变成的铁素体为细小、等轴、不具备亚结构的铁素体晶粒和珠光体。
(2)先析出的铁素体晶粒经变形可以有以下三种情况产生
在双向区中以小变形量轧制,铁素体仅被拉长,而在晶内不形成亚结构,形状变化不大。
增大变形量,除使先析出铁素体被拉长外,晶粒内位错密度增加,产生回复,形成亚结构,位错密度下降,一般希望形成这样的铁素体,以得到高强度和韧性的综合性能。
第二阶段:在这一阶段动态软化速度将大于加工硬化速度,并且随着位错的大量消失,动态软化速度减慢,直至软化速度与硬化速度达到平衡,反应在真应力—真应变曲线上,随着变形量加大变形应力开始下降,直至一轮再结晶全部完成并与加工硬化相平衡,变形应力不再下降为止,形成了真应力—真应变曲线第二阶段。
第三阶段:(1)一种是变形量不断增加而应力值基本不变,呈稳定变形,这种情况称为连续动态再结晶。(2)另一种是应力随变形量增加出现波浪式的变化呈非稳定态变形,这种情况称为间断动态再结晶。
1、中厚板轧后控制冷却的目的和要求
目的:(1)得到细铁素体和细片状珠光体组织,在不降低钢的韧性前提下进一步提高强度和综合力学性能。(2)提高钢材强度和低温韧性。(3)提高钢板的焊接性能,低温韧性和冷成型性(4)生产出不同强度级别的钢液,或开发出性能更高的新产品。(5)轧后采用在线淬火工艺,可简化工艺,节约耗能,降低成本。
多道次轧制对三个阶段影响
在(Ⅲ)完全再结晶区中连轧两道后得到全部细化的再结晶组织,道次变形量或总变形量增大都能使奥氏体晶粒细化。
在(Ⅱ)部分再结晶区,这个阶段得到的组织比较细而且整齐,但在实际生产中,多道次轧制时,轧制温度是逐渐下降的,它是不利于再结晶进行的。因此仍有可能虽经多道次轧制,在Ⅱ区有足够的压下量,晶粒得到细化,但仍然得不到再结晶全部的再结晶组织。
8、影响Nb(C、N)析出的因素
(1)、变形量和析出时间
(2)变形温度
(3)、钢的成分变化
9、喷水冷却、连续水流冷却、浸水冷却特点?应用场所?
(1)喷水冷却:热传导效果降低,钢材不能很好的冷却。
连续水流冷却:限制冷却能力进一步提高
(3)浸水冷却应用在棒线材生产中。
10、控制冷却三个阶段及特点
一次冷却::以中轧温度开始到相变开始前的这段温度范围内的冷却来控制。
给予足够大的压下率时,先析出铁素体晶粒经变形后将发生铁素体再结晶,则形成等轴铁素体晶粒,一般在正常轧制条件下,是不易发生铁素体再结晶的。
如果钢中含有Nb、V、Ti微量元素,变形会促进这些碳化物的析出。
通过两相区轧制,改善钢材性能不只是靠组织上使铁素体进一步细化,织构发达引起的层状撕裂也有一定作用。
三、问答题:
当只空冷时:是控制轧后的冷却速度达到改善钢材组织和性能的目的。由于热轧变形的作用,促使变形奥氏体向铁素体转变温度提高,相变后的铁素体晶粒容易长大,造成力学性能降低。为了细化铁素体晶粒,减少珠光体片层间距,阻止碳化物在高温下析出,以提高析出强化效果而采用控制冷却工艺。
所以采用控轧控冷相结合能将热轧钢材的两种强化效果相加,进一步提高钢材的强韧性和获得合理的综合力学性能。
目的是保持碳化物固溶状态,以达到固溶强化
11、三选一,注:(2)最重要
(1)奥氏体再结晶控制轧制特点:(1)是在奥氏体变形过程中和变形后自发产生奥氏体再结晶的温度区域中进行轧制,变形温度一般在1000摄氏度以上。(2)碳素钢的再结晶临界变形量较小,对变形温度的依赖也较小。而含Nb钢的再结晶临界变形量都很大,对变形温度的依赖也很大,变形温度降低,临界变形量加大。变形温度越低,则临界变形量增高的越多。(3)当轧制温度一定时,随原始奥氏体晶粒粗大而要求有较大的再结晶临界变形量。终轧温度越低,则临界变形量越大,含Nb钢表现得最为强烈。而碳素钢的再结晶临界变形量随温度的变化不大。(4)随道次变形量的加大,奥氏体再结晶后的晶粒细化。但是,当道次压下量达到50%以上时,晶粒细化的趋势越小,最后,晶粒尺寸达到一个极限值。(5)如果扎后停留时间加长,则再结晶晶粒长大,形成粗大的奥氏体晶粒。(6)在临界变形量以下变形,将发生部分再结晶或者由于应变诱发晶界迁移,而在奥氏体中出现少量特大晶粒,引起严重的混晶现象。(7)在950~1100℃轧制,道次变形量要大于15%~20%,奥氏体晶粒的均匀性较好,随着轧制温度的降低,必须给予更大的道次变形量。