作业标准时间计算法
工时计算
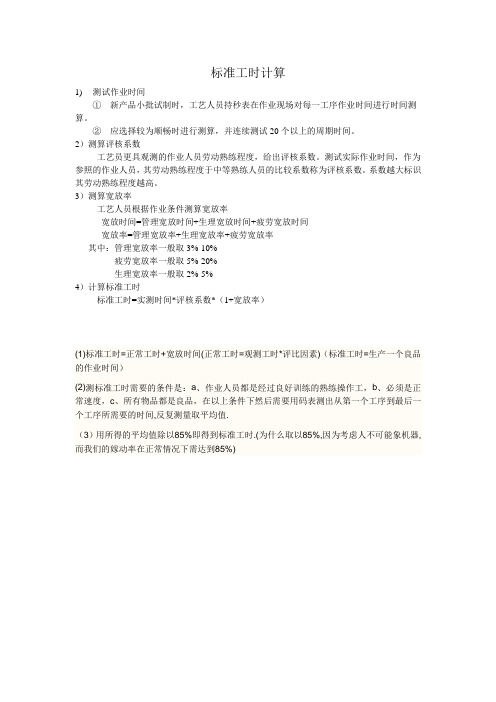
标准工时计算
1)测试作业时间
①新产品小批试制时,工艺人员持秒表在作业现场对每一工序作业时间进行时间测算。
②应选择较为顺畅时进行测算,并连续测试20个以上的周期时间。
2)测算评核系数
工艺员更具观测的作业人员劳动熟练程度,给出评核系数。
测试实际作业时间,作为参照的作业人员,其劳动熟练程度于中等熟练人员的比较系数称为评核系数。
系数越大标识其劳动熟练程度越高。
3)测算宽放率
工艺人员根据作业条件测算宽放率
宽放时间=管理宽放时间+生理宽放时间+疲劳宽放时间
宽放率=管理宽放率+生理宽放率+疲劳宽放率
其中:管理宽放率一般取3%-10%
疲劳宽放率一般取5%-20%
生理宽放率一般取2%-5%
4)计算标准工时
标准工时=实测时间*评核系数*(1+宽放率)
(1)标准工时=正常工时+宽放时间(正常工时=观测工时*评比因素)(标准工时=生产一个良品的作业时间)
(2)测标准工时需要的条件是:a、作业人员都是经过良好训练的熟练操作工,b、必须是正常速度,c、所有物品都是良品,在以上条件下然后需要用码表测出从第一个工序到最后一个工序所需要的时间,反复测量取平均值.
(3)用所得的平均值除以85%即得到标准工时.(为什么取以85%,因为考虑人不可能象机器,而我们的嫁动率在正常情况下需达到85%)。
标准工时如何计算
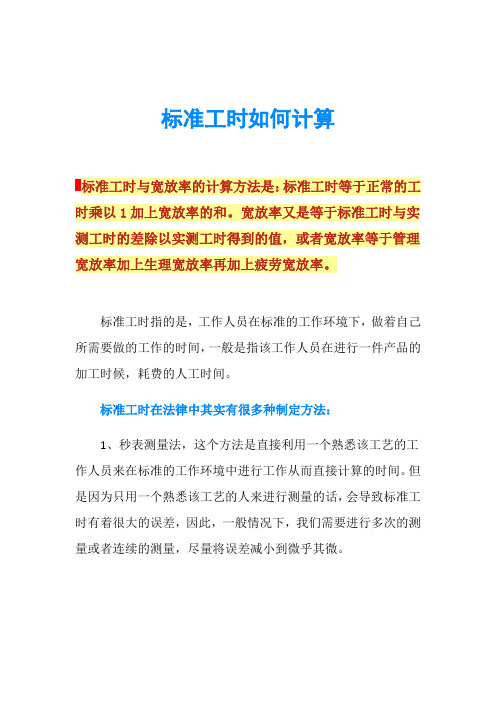
标准工时如何计算标准工时与宽放率的计算方法是:标准工时等于正常的工时乘以1加上宽放率的和。
宽放率又是等于标准工时与实测工时的差除以实测工时得到的值,或者宽放率等于管理宽放率加上生理宽放率再加上疲劳宽放率。
标准工时指的是,工作人员在标准的工作环境下,做着自己所需要做的工作的时间,一般是指该工作人员在进行一件产品的加工时候,耗费的人工时间。
标准工时在法律中其实有很多种制定方法:1、秒表测量法,这个方法是直接利用一个熟悉该工艺的工作人员来在标准的工作环境中进行工作从而直接计算的时间。
但是因为只用一个熟悉该工艺的人来进行测量的话,会导致标准工时有着很大的误差,因此,一般情况下,我们需要进行多次的测量或者连续的测量,尽量将误差减小到微乎其微。
2、模特法,模特法是将加工这个产品的工艺需要人工负责的部分来划分21种动作,对这21种不同的动作分别测量它的标准工时。
3、简明工作因素法,这个方法也是将加工产品所需要的人工动作的划分成最基本的动作,并且让每个动作的时间划分成一样的,直接将这些动作的标准时间定制为一样的。
其实定制标准工时的方法有很多种,这里只是最基本的几种,只要你设定的标准工时合理又合法就可以了。
标准工时最基本的计算方法是:标准作业时间加上辅助该工作的时间就等于标准工时。
在这之中标准作业时间是由加工该产品所需要的时间,一般是指为了增加这个产品的价值所消耗的人工或者机器的时间,标准工时的减少只能是因为加工该产品的时间减少或者辅助加工的时间减少了。
标准工时与宽放率的计算方法是:标准工时等于正常的工时乘以1加上宽放率的和。
宽放率又是等于标准工时与实测工时的差除以实测工时得到的值,或者宽放率等于管理宽放率加上生理宽放率再加上疲劳宽放率。
标准作业时间效率计算公式
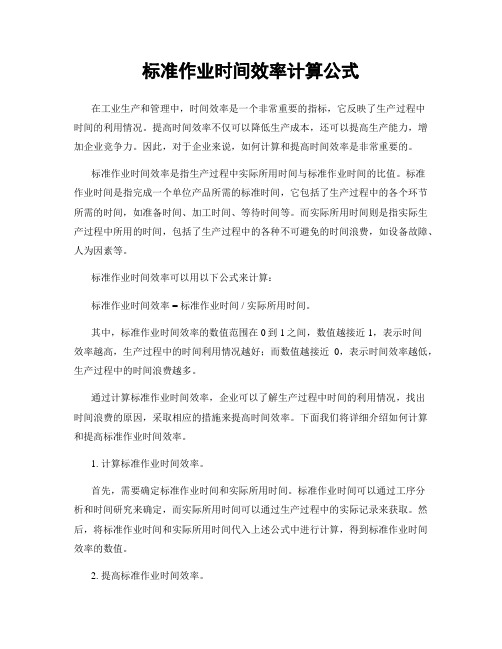
标准作业时间效率计算公式在工业生产和管理中,时间效率是一个非常重要的指标,它反映了生产过程中时间的利用情况。
提高时间效率不仅可以降低生产成本,还可以提高生产能力,增加企业竞争力。
因此,对于企业来说,如何计算和提高时间效率是非常重要的。
标准作业时间效率是指生产过程中实际所用时间与标准作业时间的比值。
标准作业时间是指完成一个单位产品所需的标准时间,它包括了生产过程中的各个环节所需的时间,如准备时间、加工时间、等待时间等。
而实际所用时间则是指实际生产过程中所用的时间,包括了生产过程中的各种不可避免的时间浪费,如设备故障、人为因素等。
标准作业时间效率可以用以下公式来计算:标准作业时间效率 = 标准作业时间 / 实际所用时间。
其中,标准作业时间效率的数值范围在0到1之间,数值越接近1,表示时间效率越高,生产过程中的时间利用情况越好;而数值越接近0,表示时间效率越低,生产过程中的时间浪费越多。
通过计算标准作业时间效率,企业可以了解生产过程中时间的利用情况,找出时间浪费的原因,采取相应的措施来提高时间效率。
下面我们将详细介绍如何计算和提高标准作业时间效率。
1. 计算标准作业时间效率。
首先,需要确定标准作业时间和实际所用时间。
标准作业时间可以通过工序分析和时间研究来确定,而实际所用时间可以通过生产过程中的实际记录来获取。
然后,将标准作业时间和实际所用时间代入上述公式中进行计算,得到标准作业时间效率的数值。
2. 提高标准作业时间效率。
为了提高标准作业时间效率,企业可以采取以下措施:优化生产工艺,通过工艺改进和设备更新,缩短生产周期,减少生产过程中的等待时间和转换时间,提高生产效率。
提高员工技能,通过培训和技能提升,提高员工的工作技能和操作水平,减少人为因素对生产时间的影响。
管理生产过程,通过生产计划和生产调度,合理安排生产过程,避免生产过程中的拥堵和浪费,提高生产效率。
引入先进技术,通过引入先进的生产技术和管理方法,提高生产效率,降低生产成本,提高标准作业时间效率。
标准工时计算

Cycle time 图示
投入 工序1 Ict1 工序2 Ict2
搬运时间
工序3 Ict3
工序4 Ict5
工序5 Ict5
产出
TCT
产能的计算与探讨
产能: 单位时间内的生产符合一定质量产品的数量。
也可以指某一工位、工序或者整个流程单位时间内的生产能
力。 其单位时间可以是时、天、月等时间单位。
产能计算的用途
而现在的制造业无不是多品种多批次的生产方式,为 了满足市场需求,我们需要准确的预测人力、机器设备的 需求,这也是产能计算的一大用途。
实例分析2:市场需求,聚合物提产至60K/天。现需对其
包装重分容工序进行需求分析,计算需购买分容柜数量。
1、统计一些相关数据:对产品进行分类,确认各种型号或 各类产品的标准时间。并通过市场部提供的资料:计算(1 年)将来市场的各类产品的分布比率。如下表:
評價 項目 最優(A) 優(B) 良© 普通(D) 可(E) 劣(F) A1 A2 B1 B2 C1 C2 D E1 E2 F1 F2 熟練度 +0.15 +0.13 +0.11 +0.08 +0.06 +0.03 0.00 -0.05 -0.10 -0.16 -0.22 A1 A2 B1 B2 C1 C2 D E1 E2 F1 F2 努力度 +0.13 +0.12 +0.10 +0.08 +0.05 +0.02 0.00 -0.04 -0.08 -0.12 -0.17 作業條件 A B C D E F +0.06 +0.04 +0.02 0.00 -0.03 -0.07 A B C D E F 一致性 +0.04 +0.03 +0.01 0.00 -0.02 -0.04
标准工时和计算标准管理规范(含表格)
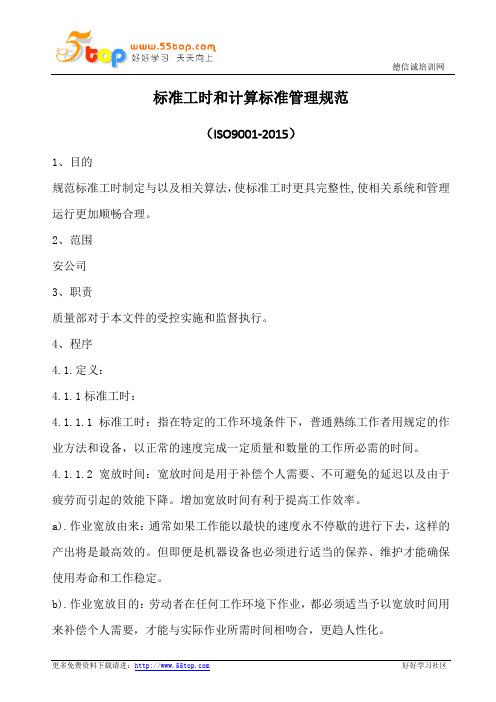
标准工时和计算标准管理规范(ISO9001-2015)1、目的规范标准工时制定与以及相关算法,使标准工时更具完整性,使相关系统和管理运行更加顺畅合理。
2、范围安公司3、职责质量部对于本文件的受控实施和监督执行。
4、程序4.1.定义:4.1.1标准工时:4.1.1.1标准工时:指在特定的工作环境条件下,普通熟练工作者用规定的作业方法和设备,以正常的速度完成一定质量和数量的工作所必需的时间。
4.1.1.2宽放时间:宽放时间是用于补偿个人需要、不可避免的延迟以及由于疲劳而引起的效能下降。
增加宽放时间有利于提高工作效率。
a).作业宽放由来:通常如果工作能以最快的速度永不停歇的进行下去,这样的产出将是最高效的。
但即便是机器设备也必须进行适当的保养、维护才能确保使用寿命和工作稳定。
b).作业宽放目的:劳动者在任何工作环境下作业,都必须适当予以宽放时间用来补偿个人需要,才能与实际作业所需时间相吻合,更趋人性化。
4.1.1.3标准速度:没有过度体力和精神疲劳状态下,每天能连续工作,只要努力就容易达到标准作业成果的速度。
4.1.2员工定义:4.1.2.1直接人员:指生产产线上从事生产操作人员。
包括装配、调整、检查检测和不良品维修人员。
他们是生产线上直接从事生产劳动的人员。
4.1.2.2间接人员:指不直接从事生产操作的人员,此处包括车间班长,物料配送人员、设备保养人员、工具保养人员。
间接员工虽然不从事直接的生产操作,但对于提升生产效率具有很大的影响。
4.1.3时间定义:4.1.3.1正常作业时间:指以每天8小时为基准的作业时间,其单位为分钟。
正常作业时间包括“前准备时间”和“净作业时间”。
4.1.3.1.1前准备时间(95分钟):a).早会(早会,交接班)10分钟b).清洁(工治具、设备、车间、更衣)30分钟c).中餐时间15分钟d).间隙时间(上午15分钟,下午15分钟)30分钟e).首检时间10分钟4.1.3.1.2净作业时间:指对作业对象作业的内容,规则地、周期性地重复进行的作业部分的时间。
标准工时的定义和计算方法

标准工时的定义和计算方法宝子们,今天咱们来唠唠标准工时这个概念哈。
标准工时呢,简单来说,就是在正常的操作条件下,一个受过训练的熟练工人,用规定的作业方法和设备,以正常的速度完成一项特定工作所需要的时间。
就好比你平时走路有个正常速度,那完成一段路就有个大概的时间,这个在工作里就是标准工时啦。
那它咋计算呢?这里面学问可不少呢。
一般来说哈,标准工时是由正常时间和宽放时间组成的。
正常时间就是工人在没有任何干扰的情况下,纯干活儿的时间。
比如说工人做一个小零件,从拿起材料,到加工完成,这个过程所花的时间就是正常时间的一部分。
这个正常时间的计算呢,可以通过直接观测法。
就是你拿个小本本,在旁边看着工人干活儿,把他每个操作步骤的时间都记下来,然后加起来。
这就像是你看小伙伴搭积木,从拿起第一块积木开始计时,到搭成一个小房子结束,记录下总共花的时间一样。
宽放时间就比较有趣啦。
这是考虑到工人在工作过程中,不可能一直像个机器人一样不停地工作的。
人得休息呀,可能会有疲劳的时候,或者偶尔被打断一下,像上个厕所,喝口水啥的。
宽放时间就是给这些情况预留的时间。
宽放时间通常是按照正常时间的一定比例来计算的。
比如说,根据经验或者统计数据,这个比例可能是10%或者15%之类的。
举个例子哈,如果一个工人做一件东西的正常时间是1个小时,宽放比例是10%,那标准工时就是1个小时加上1个小时的10%,也就是1小时6分钟。
这样算出来的标准工时就比较合理啦,既考虑了工人实际干活儿的时间,也考虑到了工人的休息和其他必要的停顿。
标准工时在企业里可重要啦。
它可以帮助企业安排生产计划,知道大概多久能生产出多少产品。
还能用来计算工人的工资呢,如果是按工时计算工资的话,这个标准工时就是个重要的依据啦。
宝子们,现在是不是对标准工时有点感觉了呢?。
标准工时测算方法
一、目的:规范标准工时制定与修改作业,使标准工时具有完整性,使ERP系统运行之排程合理和成本准确。
二、名词定义:2。
1、标准工时:在特定的工作环境条件下,用规定的作业方法和设备,以普通熟练工作者的正常速度完成一定质量和数量的工作所必需的时间。
2。
2、宽放时间:指作业员除正常工作时间之外必须的停顿及休息的时间。
包括操作者个人事情引起的延迟,疲劳或无法避免的作业延迟等时间.对于没有规定发生时间、发生频率、所需时间的不规则要素作业,并不在正常时间范围之内,而属于宽放时间。
2。
3、标准速度:没有过度体力和精神疲劳状态下,每天能连续工作,只要努力就容易达到标准作业成果的速度.三、标准工时的构成:3。
1、标准时间=正常时间+宽放时间=观测时间*(1+熟练修正数+努力修正数)+观测时间*宽放率3.2、正常时间:3.2.1、主体作业时间:按照作业目的进行的作业。
指能创造价值的作业,如改变产品外形,改变产品性能等。
3.2。
2、副作业时间:与主体作业同步发生,起附属作用.如取放工具、检查等。
正常时间设定方法如下:直接观测法:秒表观测法;摄影分析法;work sampling法。
优点:比较简单;任何人都可以做。
缺点:难于跟标准速度相比较,需要评价标准速度;生产之前不能设定.合成法:动作分析法、历史数据法。
优点:信赖程度和一贯性高;客观性和普遍性高;不需要评价标准速度;可在生产之前设定;容易消除不必要动作.缺点:需要教育和训练。
3.3、宽放时间:3。
3.1、私事宽放时间:作业过程中,满足生理要求的宽放时间,如上厕所,喝水,擦汗.3.3。
2、疲劳宽放时间:为了补偿工作过程中体力和精神疲劳,采取的休息或操作速度减弱的宽放时间。
3。
3.3、特殊宽放:学习宽放、机械干涉宽放、奖励宽放、工厂宽放、其它宽放.作业宽放时间:补偿作业过程中发生不规则的要素作业。
如用处理不良品等。
3。
3.4、集体宽放时间:集体作业时,对于个体差异产生损失的补偿。
标准工时的定义计算MOD法课件
VS
详细描述
某食品加工企业采用MOD法对生产流程 进行工时估算,实现了安全、健康、环保 的生产管理。通过将食品加工流程细分为 多个操作步骤,并利用MOD法对每个操 作步骤进行工时估算,企业能够更好地控 制生产过程,确保食品安全和健康。同时 ,MOD法的应用也促进了企业的环保管 理,降低了能源消耗和排放。
分配生产资源
根据产品种类、工艺要求 等因素,分配相应的生产 资源,包括设备、材料、 人员等。
分析生产流程
详细分析生产流程
对每个生产环节进行详细分析, 了解各环节的生产工艺、操作流
程、关键控制点等。
确定瓶颈环节
针对分析结果,找出生产流程中的 瓶颈环节,制定相应的改善措施。
优化生产流程
根据分析结果,对生产流程进行优 化,提高生产效率及产品质量。
。
标准工时是评估工作效率的重要 标准,它可以帮助企业了解生产 过程中的瓶颈和问题,提高生产
效率和质量。
标准工时是制定人工成本的重要 参考,它可以帮助企业合理制定 人工成本预算,提高企业的经济
效益。
02 标准工时计算
计算公式及参数设定
01
02
03
计算公式
标准工时 = 正常时间 + 宽放时间
正常时间
进行某项作业一般所需时 间
宽放时间
为补偿各种额外因素所需 要的时间,如疲劳、停工 等
工作研究与时间测量
工作研究
通过细致的观察和分析,确定各 项作业的必要时间和工作量
时间测量
用计时器和秒表等工具记录作业 时间,以此为基础计算标准工时
标准工时计算方法
方法一:秒表法 1. 准备秒表等计时工具
2. 记录每个阶段作业时间
标准工时的特点
总工时和标准工时计算公式
总工时和标准工时计算公式
工时有标准工时还有综合工时,计算方法也不相同。
而且不同的企业计算方法也不尽相同。
1 标准工时:在特定的工作环境条件下,用规定的作业方法和设备,以普通熟练工作者的正常速度完成一定质量和数量的工作所必需的时间。
2 标准工时的构成:标准时间=正常时间+宽放时间=观测时间*(1+熟练修正数+努力修正数)+观测时间*宽放率
3 综合计算工时制:按照以月、季度、半年、一年为周期。
比如以月为综合计算工时,21.75*8=167小时左右,超过167小时的需要按照150%支付加班工资。
国定假日需要按照300%支付加班工资。
4 附:职工全年月平均工作时间及工时计算方法根据《全国年节及纪念日放假办法》(国务院令第513号)的规定,全体公民的节日假期由原来的10天增设为11天。
职工全年月平均制度工作天数和工资折算办法分别调整如下:工作日的计算年工作日:365天/年-104天/年(休息日)-11天/年(法定休假日)=250天/年季工作日:250天/年÷4季=62.5天月工作日:250天/年÷12月=20.83天工作小时数的计算:以月、季、年的工作日乘以每日的8小时。
日工资、小时工资的折算按照《劳动法》第五十一条的规定,法定节假日用人单位应当依法支付工资,即折算日工资、小时工资时不剔除国家规定的11天法定节假日。
据此,日工资、小时工资的折算为:日工资:月工资收入÷月计薪天数小时工资:月工资收入÷(月计薪天数×8小时)。
月计薪天数=(365天-104天)÷12月=21.75天。
标准工时管理制度
5.1.1.1明确测时目的,确定测时对象。
5.1.1.2调查作业现场环境和条件。主要包括诸如机台、工艺装备是否符合规定;工作地在温度、湿度、照明和噪声等条件是否符合要求等。
5.1.1.3工位的动作细分和确定计时点:
机动时间与手动时间分开;
定量作业要素与变量作业要素分开;
4. 职责
4.1研发部
a.为新机种的标准工时制定提供技术支持;
b.工艺流程要求、BOM等技术资料的制定;
c.量产机种标准工时的审核;
4.2资材部
a.测量标准工时,确认其合理性;
b.汇总各机种标准工时,定期量测计算其有效性;
c.在无生产变动的情况下,每月确认/更新各机种的标准工时;
d.将新的标准工时数据更新并确保更新正确;
3.1.7宽放率(%):指为剔除操作者因生理限制、操作方法、客观条件等因素造成的时间延误影响,给正常作业时间加入的修正系数,通常以工作抽样法获取基础数据来确定。宽放时间主要由四项组成﹐包括作业宽放﹑疲劳宽放﹑生理宽放和管理宽放。
【宽放率(%)=宽放时间/正常工作时间×100%】
3.2连动作业标准工时:在机台稳定条件和环境下,普通熟练工人以设定的作业速度和标准的操作方法,完成标准作业所需要的时间。其计算公式为:
5.1.3.3剔除异常值后﹐则计算实测作业时间,即实测平均值,平均值与标准偏差的计算公式分别为:
5.2连动作业标准工时测量
5.2.1新机种由研发部提供初始标准工时,量产后生管跟进实际作业状况,持续更新标准工时数据。
5.2.2连动作业标准工时定义如下:
【连动作业标准工时=机台速度(pcs/min)×(1+宽放率)×[60min-(每小时平均停机测量时间min+每小时其它平均消耗时间min)]】
- 1、下载文档前请自行甄别文档内容的完整性,平台不提供额外的编辑、内容补充、找答案等附加服务。
- 2、"仅部分预览"的文档,不可在线预览部分如存在完整性等问题,可反馈申请退款(可完整预览的文档不适用该条件!)。
- 3、如文档侵犯您的权益,请联系客服反馈,我们会尽快为您处理(人工客服工作时间:9:00-18:30)。
C --- 切 割
S --- 表面处理
R --- 记 录
T --- 思 考
M --- 度 量
5.1.2MOST数据卡
MOST数据卡是本作业标准时间计算法必不可少的工具,本公司所有作业标准时间之计算都是以本文件所载个数据卡为依据
5.1.2.1一般移动排列(ABG ABP A)之数据卡见表二
拍打(次数)
旋转
冲击
摇动(柄) (圈数)
拍打
螺丝直径
手指或手批
手批/齿轮
锁匙
锁匙/齿轮
手锤
齿轮
锁匙
手锤
动力(电批/风批)
1
1
/
/
/
1
/
/
/
/
/
1
3
/
1
1
1
3
/
1
/
1
1/4寸
6cm
3
6
3
3
2
3
6
2
/
1
3
钮力1寸, 25mm
6
10
8
5
3
5
10
4
2
2
5
钮力25~38cm
10
16
16
9
5
8
16
6
3
3
8
钮力38~100cm
4.定义
4.1作业标准时间
一个受足够训练的熟练工人在合适的工作条件下,以正常速度按标准作业方法作业的时间称为作业标准时间。
4.2标准作业方法
能确保品质的规范化作业方法称为标准作业方法。
4.3作业标准时间计算法
这里所指的作业标准时间计算法专指MTM系列中适用于生产工作用的MOST计算法。
4.4TMU
MOST计算法的时间单位。(Time Measurement Unit之简称)
16
24
25
13
8
11
23
9
4
5
12
24
32
36
17
10
15
30
12
6
6
16
32
42
47
23
13
20
36
16
8
8
21
42
54
61
29
17
25
50
20
10
11
27
54
表七工具使用数据卡之二
ABG ABP __ABPA工具使用排列之一
指
数
C
S
M
R
T
指
数
抓紧
切断
切割
切片
气动清洁
刷清洁
擦
度量
写
记号
检查
阅读
钳子
G
握取控制
P
安置
指
数
0
≤2寸
≤5cm
握住
抛出
0
1
伸手可及
轻的物体
轻的物体同步握取
放在一旁
松装
1
3
1~2步
弯腰及起身各占50%
不移动椅子坐或站
不同步握取
重或笨的物体
盲目或被妨碍
使脱离
使连接
收集
调整
轻压
双重放置<10cm盲目松装
3
6
3~4步
完全弯腰及起身
小心及精确
重压
盲目活被妨碍
中间活动
双重放置>10cm
6
10
5~7步
坐或站
10
16
8~10步
穿过门(包括3,4步)
爬上或爬下(1m)
16
表三受控移动排列数据卡
ABG MXI A受控移动排列
指
数
M
X
I
指
数
受控移动
运作时间
对准
按/拉/转
摇动
(圈数)
秒
分
时
物体
1
≤12寸(30cm)
按钮/制/键
/
0.5
0.01
0.0001
对准一点
1
3
>12寸(30cm)
有抵抗
排 列 模 式
分 类 动 作
一般移动
A B G A B P A
A --- 动作距离
B --- 身体活动
G --- 握取控制
P --- 放 置
受控移动
A B G M X I A
M --- 受控移动
X --- 动作时间
I --- 对 准
工具/设备使用
A B G A B PA B P A
F --- 固 紧
使定位或退出
高控
2段≤12寸
1
1.5
0.02
0.0004
对准二点
≤4寸(10cm)
3
6
2段>12寸
3
2.5
0.04
0.0012
对准二点
>4寸(10cm)
6
10
3~4段
6
4.5
0.07
0.0019
10
16
11
7.0
0.10
0.0019
精确对准
16
表四M之补充表五X之补充
摇动
运作时间
指数
圈数
指数
秒
分
时
M1
P3
异种扳手
P3
动力扳手(电\风批)
P3
可调教扳手
P6
注:当安放发生在盲目或被妨碍的位置时便使用括号内的数值
5.2作业标准时间计算法计算步骤
⑴按标准作业方法分解作业内容,列出适当之MOST排列模式
⑵根据对应之MOST数据卡给MOST排列各动作加上数值
⑶将MOST排列各动作之数值相加后乘10,即为此作业之TMU值,再将此值乘0.036即为此作业之作业标准时间
M3
M6
M10
M16
M24
M32
M42
M54
/ 1 3 6 11 16 21 28 36
1
3
6
10
16
24
32
42
54
67
81
96
113
131
152
173
196
220
245
270
300
330
0.5 1.5 2.5 4.0 7.0 10.0 13.0 17.0 21.5 26.5 31.5 37.5 43.5 50.5 58.0 66.0 74.5 83.5 92.5 102.5 113.0 124.0
剪刀
刀
气嘴
刷子
布
量具
铅笔
记号笔
手指眼
眼
线
切割次数
划刀次数
平方尺
平方尺
平方尺
寸(cm)
尺(cm)
数字
单词
数字
点
数字/英文单词
课文词汇
1
抓紧
1
/
/
/
/
1
检查
记录
1
1
3
1
3
软
2
1
/
/
1/2
2
1
直线
3
3
尺
8
寸
3
6
扭曲
弯圈
中
4
/
一点
一孔
凹粒
一小物体
/
活规<5cm
4
1
2
5
感受热力
6
6
比例/日期/时间
10
硬
7
/
/
排列模式: A B G M X I A
C. 工具使用排列(一般手工工具的使用)
排列模式: A B G A B PA B P A
此排列模式的空间(即A B G A B P [ ] A B P A中之[ ])至少要插入下列工具使用特性的一种:
F.L.C.S.M.R.T
表一:
人 工 处 理 类
活 动 类 别
23
5
13
42
表八双手活动数据卡表九工具安放数据卡
双手
工具类
指数值
指数
手臂活动次数
锤子
P0 (P1)
1
/
手指/手
P1 ( P3 & P6 )
3
/
刀
P1 (P3)
6
1
剪刀
P1 (P3)
10
/
钳子
P1 (P3)
16
3
书写工具
P1
24
6
度量工具
P1
32
8
表面处理工具
P1
42
11
螺丝批
P3
54
15
齿轮
P3
固定扳手
1 H = 100,000 TMU
即1 TMU = 0.036 S
5.内容
5.1 MOST排列模式及数据卡
5.1.1MOST技术包括下列三种基本排列模式:(详见表一)
A. 一般移动排列(一物体自由穿过空气的空间活动)
排列模式: A B G A B P A
B. 受控移动排列(一物体在活动期间保持与一表面接触或附在另一表面的活动)
0.01
0.02
0.04
0.07
0.11
0.16
0.22
0.28
0.36
0.44
0.53
0.62
0.73
0.84
0.97
1.10
1.24
1.39