环保碱性锌酸盐镀锌浅谈
碱性镀锌光亮剂配方组成,镀锌原理及生产工艺

碱性镀锌光亮剂配方组成,镀锌原理及生产工艺碱性镀锌光亮剂配方组成,镀锌原理及生产工艺碱性镀锌光亮剂广泛应用在电镀行业, 禾川化学引进国外配方破译技术,专业从事碱性镀锌光亮剂成分分析、配方还原、研发外包服务,为碱性镀锌光亮剂相关企业提供一整套配方技术解决方案。
碱性锌酸盐镀锌工艺具有镀液组成简单、结晶细致、镀层易于钝化、镀层的彩色钝化膜不易变色以及电镀废水处理简单等优点。
碱性锌酸盐镀锌的关键是选用合适的光亮剂,用于该工艺的光亮剂大致可分为载体光亮剂、主光亮剂及其他的辅助光亮剂。
1.载体光亮剂(初级光亮剂)初级光亮剂也称为载体光亮剂,主要起细化晶粒的作用;常与次级光亮剂相组合。
载体光亮剂大多数含有一种或几种有机胺、醇胺、含氮杂环化合物与醇及卤代烷反应而生成的大分子化合物。
1.1 有机胺与环氧氯丙烷的缩合物DPE-I:二甲氨基丙胺与环氧氯丙烷的缩聚物DPE-II:二甲氨基丙胺与环氧氯丙烷的缩聚物的季铵盐DPE-III:二甲氨基丙胺、乙二胺与环氧氯丙烷的缩聚物DE:二甲胺与环氧氯丙烷的缩合物KR-7:盐酸羟胺与环氧氯丙烷的缩合物1.2 其他类物质与环氧氯丙烷的缩合物甲醛、糠醛、吡啶、烟酸、乙醇胺、哌嗪、吡唑、咪唑等与环氧氯丙烷或环氧丙烷反应生成的大分子化合物。
如:咪唑与环氧氯丙烷、有机胺的反应物,常作为载体光亮剂使用。
1.3 其它类的载体光亮剂现在国内外很多较新型的光亮剂也可以用聚胺砜类, 以及含有特殊官能团的聚胺类化合物作载体光亮剂, 此类化合物具有光亮范围宽、均镀能力和深镀能力好等优点。
常见的有一下几种:1)聚乙烯醇(PVA):作为氰化镀锌的载体光亮剂2)聚乙烯亚胺及其衍生物:锌酸盐镀锌的光亮剂,可防止高电流密度区域被烧焦。
3)聚胺酚水溶性高分子4)胺衍生物所有载体光亮剂中,最常用的有DPE 类、DE 类、PAS、IME、MOME 等。
2.主光亮剂(次级光亮剂)次级光亮剂也称主光亮剂。
主光亮剂大多采用可在锌电极上还原的有机醛、酮类化合物以及氯化苄与吡啶羧酸的加成物或烟酸与氯化苄加成的季胺盐。
一低碳钢碱性锌酸盐镀锌工艺及钝化处理
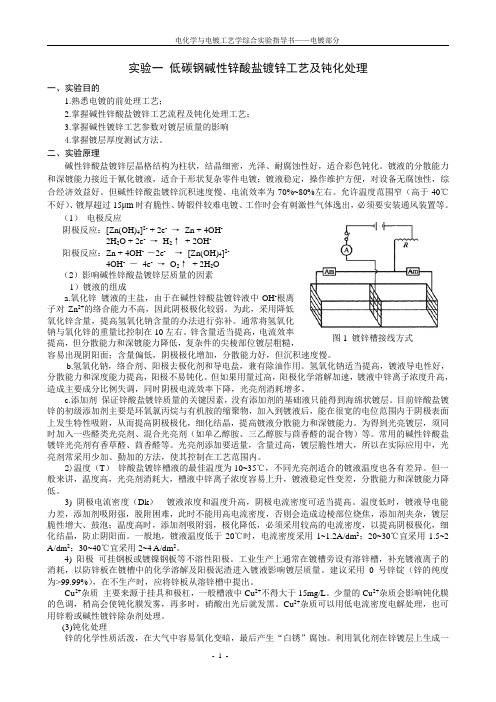
图 1 镀锌槽接线方式实验一 低碳钢碱性锌酸盐镀锌工艺及钝化处理一、实验目的1.熟悉电镀的前处理工艺;2.掌握碱性锌酸盐镀锌工艺流程及钝化处理工艺;3.掌握碱性镀锌工艺参数对镀层质量的影响4.掌握镀层厚度测试方法。
二、实验原理碱性锌酸盐镀锌层晶格结构为柱状,结晶细密,光泽、耐腐蚀性好,适合彩色钝化。
镀液的分散能力和深镀能力接近于氰化镀液,适合于形状复杂零件电镀;镀液稳定,操作维护方便,对设备无腐蚀性,综合经济效益好。
但碱性锌酸盐镀锌沉积速度慢、电流效率为70%~80%左右。
允许温度范围窄(高于40℃不好)、镀厚超过15μm 时有脆性、铸锻件较难电镀、工作时会有刺激性气体逸出,必须要安装通风装置等。
(1) 电极反应阴极反应:[Zn(OH)4]2- + 2e - → Zn + 4OH - 2H 2O + 2e - → H 2↑ + 2OH -阳极反应:Zn + 4OH - -2e - → [Zn(OH)4]2- 4OH - - 4e - → O 2↑ + 2H 2O (2)影响碱性锌酸盐镀锌层质量的因素 1)镀液的组成a.氧化锌 镀液的主盐,由于在碱性锌酸盐镀锌液中OH -根离子对Zn 2+的络合能力不高,因此阴极极化较弱。
为此,采用降低氧化锌含量,提高氢氧化钠含量的办法进行弥补。
通常将氢氧化钠与氧化锌的重量比控制在10左右。
锌含量适当提高,电流效率提高,但分散能力和深镀能力降低,复杂件的尖棱部位镀层粗糙,容易出现阴阳面;含量偏低,阴极极化增加,分散能力好,但沉积速度慢。
b.氢氧化钠,络合剂、阳极去极化剂和导电盐,兼有除油作用。
氢氧化钠适当提高,镀液导电性好,分散能力和深度能力提高,阳极不易钝化。
但如果用量过高,阳极化学溶解加速,镀液中锌离子浓度升高,造成主要成分比例失调,同时阴极电流效率下降,光亮剂消耗增多。
c.添加剂 保证锌酸盐镀锌质量的关键因素,没有添加剂的基础液只能得到海绵状镀层。
目前锌酸盐镀锌的初级添加剂主要是环氧氯丙烷与有机胺的缩聚物,加入到镀液后,能在很宽的电位范围内于阴极表面上发生特性吸附,从而提高阴极极化,细化结晶,提高镀液分散能力和深镀能力。
碱性锌酸盐镀锌工艺有何特点
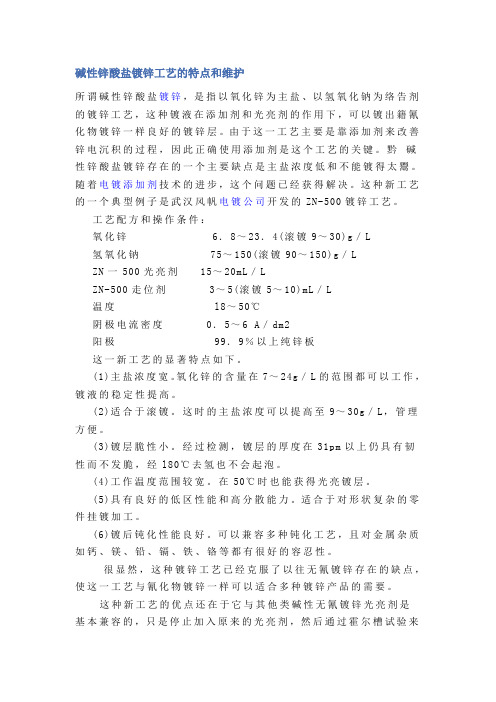
碱性锌酸盐镀锌工艺的特点和维护所谓碱性锌酸盐镀锌,是指以氧化锌为主盐、以氢氧化钠为络告剂的镀锌工艺,这种镀液在添加剂和光亮剂的作用下,可以镀出籍氰化物镀锌一样良好的镀锌层。
由于这一工艺主要是靠添加剂来改善锌电沉积的过程,因此正确使用添加剂是这个工艺的关键。
黔碱性锌酸盐镀锌存在的一个主要缺点是主盐浓度低和不能镀得太鬻。
随着电镀添加剂技术的进步,这个问题已经获得解决。
这种新工艺的一个典型例子是武汉风帆电镀公司开发的ZN-500镀锌工艺。
工艺配方和操作条件:氧化锌6.8~23.4(滚镀9~30)g/L氢氧化钠75~150(滚镀90~150)g/LZN一500光亮剂15~20mL/LZN-500走位剂3~5(滚镀5~10)mL/L温度l8~50℃阴极电流密度0.5~6 A/dm2阳极99.9%以上纯锌板这一新工艺的显著特点如下。
(1)主盐浓度宽。
氧化锌的含量在7~24g/L的范围都可以工作,镀液的稳定性提高。
(2)适合于滚镀。
这时的主盐浓度可以提高至9~30g/L,管理方便。
(3)镀层脆性小。
经过检测,镀层的厚度在31pm以上仍具有韧性而不发脆,经l80℃去氢也不会起泡。
(4)工作温度范围较宽。
在50℃时也能获得光亮镀层。
(5)具有良好的低区性能和高分散能力。
适合于对形状复杂的零件挂镀加工。
(6)镀后钝化性能良好。
可以兼容多种钝化工艺,且对金属杂质如钙、镁、铅、镉、铁、铬等都有很好的容忍性。
很显然,这种镀锌工艺已经克服了以往无氰镀锌存在的缺点,使这一工艺与氰化物镀锌一样可以适合多种镀锌产品的需要。
这种新工艺的优点还在于它与其他类碱性无氰镀锌光亮剂是基本兼容的,只是停止加入原来的光亮剂,然后通过霍尔槽试验来确定应该补加的ZN一500的量。
初始添加量控制在0.25mL/L,再慢慢加到正常工艺范围并补入走位剂。
在杂质较多时,还应加入ZN一500配套的镀液净化剂。
当对水质纯度不确定时,可以在新配槽时加入相应的除杂剂和水质稳定剂各1mL/L。
碱性锌酸盐电镀锌-碳化硅复合镀层工艺优化

碱性锌酸盐电镀锌-碳化硅复合镀层工艺优化邓型深;卢钇成;姜吉琼【摘要】以Q235钢板为基体,在由70.0 g/L氧化锌、180.0 g/L氢氧化钠、2.8 g/L香草醛、1 mL/L甲醛、1.0 g/L硫脲和1.0 g/L三乙烯四胺组成的普通碱性镀锌液中加入SiC微粒电镀得到Zn-SiC复合镀层.研究了电流密度、温度、SiC用量和搅拌速率对Zn-SiC复合镀层耐蚀性的影响,得到较佳工艺条件为:SiC用量8g/L,电流密度2.5 ~ 4.0 A/dm2,温度20~25℃,搅拌速率120 r/min.SiC的存在有利于生成晶粒细小、致密且显微硬度较高的镀层.在较佳工艺下,Zn-SiC复合镀层中SiC的质量分数为1.51%,其耐蚀性优于纯锌镀层.【期刊名称】《电镀与涂饰》【年(卷),期】2016(035)012【总页数】5页(P605-609)【关键词】碱性镀锌;碳化硅;复合镀层;耐蚀性;显微硬度【作者】邓型深;卢钇成;姜吉琼【作者单位】广西矿冶与环境科学实验中心,桂林理工大学化学与生物工程学院,广西桂林541004;广西矿冶与环境科学实验中心,桂林理工大学化学与生物工程学院,广西桂林541004;广西矿冶与环境科学实验中心,桂林理工大学化学与生物工程学院,广西桂林541004【正文语种】中文【中图分类】TQ153.2First-author's address: Guangxi Scientific Experiment Center of M ining,Metallurgy and Environment, College of Chemistry and Bioengineering,Guilin University of Technology, Guilin 541004, China锌基复合镀层由金属锌或其合金与分散粒子(无机颗粒、有机颗粒等)组成,它兼有单一电镀锌或锌合金及微粒的良好性能,在机械制造、航空航天、汽车等工业部门具有重要的实用价值。
镀锌作业中的职业病危害因素及防护措施

镀锌作业中的职业病危害因素及防护措施镀锌作业主要职业病危害因素及辨识镀锌作业是一种广泛应用于工业和家庭建设的工艺过程,其中包括多种不同的镀锌方法,如氰化物镀锌、锌酸盐镀锌、氯化纳镀锌和硫酸盐镀锌等。
然而,这个过程中会产生多种职业病危害因素,下面将详细介绍每种镀锌方法的职业病危害因素及辨识。
1.氰化物镀锌氰化物镀锌是一种常用的镀锌方法,其中含有氰化钠等有害物质。
这些物质会对人体产生严重的危害,如中毒、致癌等。
在氰化物镀锌过程中,职业病危害因素主要包括氰化钠等有害物质对皮肤、呼吸系统和神经系统的刺激和毒性作用。
为避免这些危害,需采取以下防护措施:(1)佩戴防毒面具、手套和防护眼镜等个人防护装备;(2)保持工作场所通风良好,减少空气中氰化物的浓度;(3)定期检查工作场所空气中氰化物的浓度,确保其浓度在国家限制标准以下。
2.锌酸盐镀锌锌酸盐镀锌是一种较为环保的镀锌方法,但其中仍含有一些有害物质,如锌离子、氢氧化钠等,可对人体产生一定的危害。
在锌酸盐镀锌过程中,职业病危害因素主要包括这些有害物质对皮肤、呼吸系统和消化系统的刺激和毒性作用。
为避免这些危害,需采取以下防护措施:(1)佩戴防尘口罩、手套和防护眼镜等个人防护装备;(2)保持工作场所通风良好,减少空气中锌离子和氢氧化钠的浓度;(3)定期检查工作场所空气中锌离子和氢氧化钠的浓度,确保其浓度在国家限制标准以下。
3.氯化纳镀锌氯化纳镀锌是一种成本较低的镀锌方法,但其中含有氯化钠等有害物质。
这些物质会对人体产生一定的危害,如刺激呼吸道、损伤神经系统等。
在氯化纳镀锌过程中,职业病危害因素主要包括这些有害物质对皮肤、呼吸系统和神经系统的刺激和毒性作用。
为避免这些危害,需采取以下防护措施:(1)佩戴防尘口罩、手套和防护眼镜等个人防护装备;(2)保持工作场所通风良好,减少空气中氯化钠的浓度;(3)定期检查工作场所空气中氯化钠的浓度,确保其浓度在国家限制标准以下。
同时需注意减少人员在该工作环境中的暴露时间。
酸性镀锌与碱性镀锌的优缺点
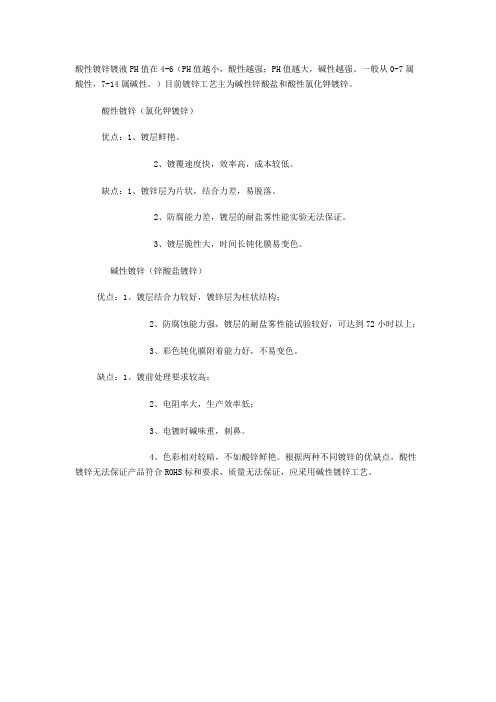
酸性镀锌镀液PH值在4-6(PH值越小,酸性越强;PH值越大,碱性越强。
一般从0-7属酸性,7-14属碱性。
)目前镀锌工艺主为碱性锌酸盐和酸性氯化钾镀锌。
酸性镀锌(氯化钾镀锌)
优点:1、镀层鲜艳。
2、镀覆速度快,效率高,成本较低。
缺点:1、镀锌层为片状,结合力差,易脱落。
2、防腐能力差,镀层的耐盐雾性能实验无法保证。
3、镀层脆性大,时间长钝化膜易变色。
碱性镀锌(锌酸盐镀锌)
优点:1、镀层结合力较好,镀锌层为柱状结构;
2、防腐蚀能力强,镀层的耐盐雾性能试验较好,可达到72小时以上;
3、彩色钝化膜附着能力好,不易变色。
缺点:1、镀前处理要求较高;
2、电阻率大,生产效率低;
3、电镀时碱味重,刺鼻。
4、色彩相对较暗,不如酸锌鲜艳。
根据两种不同镀锌的优缺点,酸性镀锌无法保证产品符合ROHS标和要求,质量无法保证,应采用碱性镀锌工艺。
碱式锌酸盐镀锌及光亮剂对镀层的影响
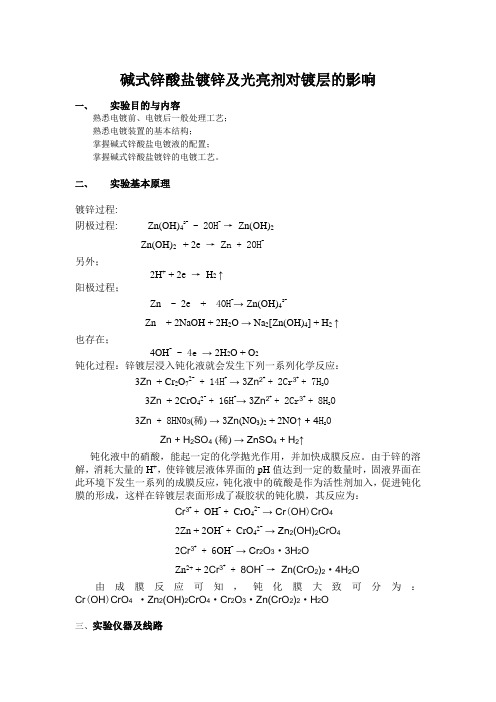
碱式锌酸盐镀锌及光亮剂对镀层的影响一、实验目的与内容熟悉电镀前、电镀后一般处理工艺;熟悉电镀装置的基本结构;掌握碱式锌酸盐电镀液的配置;掌握碱式锌酸盐镀锌的电镀工艺。
二、实验基本原理镀锌过程:阴极过程: Zn(OH)42- - 2OH- →Zn(OH)2Zn(OH)2 + 2e →Z n + 2OH-另外;2H+ + 2e →H2 ↑阳极过程;Zn - 2e + 4OH-→ Zn(OH)42-Zn + 2NaOH + 2H2O → Na2[Zn(OH)4] + H2 ↑也存在;4OH- - 4e → 2H2O + O2钝化过程:锌镀层浸入钝化液就会发生下列一系列化学反应:3Zn+ Cr2O72- + 14H+ → 3Zn2+ + 2Cr3+ + 7H2O3Zn+ 2CrO42- + 16H+→ 3Zn2+ + 2Cr3+ + 8H2O3Zn + 8HNO3(稀) → 3Zn(NO3)2 + 2NO↑ + 4H2OZn + H2SO4(稀) → ZnSO4 + H2↑钝化液中的硝酸,能起一定的化学抛光作用,并加快成膜反应。
由于锌的溶解,消耗大量的H+,使锌镀层液体界面的pH值达到一定的数量时,固液界面在此环境下发生一系列的成膜反应,钝化液中的硫酸是作为活性剂加入,促进钝化膜的形成,这样在锌镀层表面形成了凝胶状的钝化膜,其反应为:Cr3+ + OH- + CrO42- → Cr(OH)CrO42Zn + 2OH- + CrO42- → Zn2(OH)2CrO42Cr3+ + 6OH- → Cr2O3·3H2OZn2+ + 2Cr3+ + 8OH- →Zn(CrO2)2·4H2O 由成膜反应可知,钝化膜大致可分为:Cr(OH)CrO4·Zn2(OH)2CrO4·Cr2O3·Zn(CrO2)2·H2O三、实验仪器及线路电镀槽、整流器、电吹风等;前处理(除油、除锈)→水洗→1:1盐酸浸蚀→镀锌→水洗→中和→水洗→出光→水洗→低铬钝化→回收洗→水洗→温水洗→吹干→烘焙老化四、实验步骤1. 准备好阴极试片,并将油、锈去除干净,备用铜板除油:碳酸钠20g/l,磷酸三钠20g/l,硅酸钠5g/l,OP乳化剂2ml/l 温度50-60度,可使用超声波除油浸蚀活化:硫酸25%,氯化钠2g/L(弱浸蚀3~5%硫酸)2. 按镀锌工艺要求接好线路,电镀槽内倒入镀液镀液:●氧化锌110g/单组实验配1L电解液,●氢氧化钠110g/单组实验配1L电解液,●乙二胺、环氧氯丙烷缩合光亮剂4ml/单组实验配1L电解液,●乙二胺、环氧氯丙烷、四乙烯五胺缩合光亮剂3ml/单组实验配1L电解液●草香醛光亮剂●电镀液的配置:将氧化锌用少量水调成糊状,在不断搅拌下逐渐加到总体积1/5的热碱液中,直到完全溶解,再稀释到总体积。
镀锌

四、锌酸盐镀锌#0 锌酸盐镀锌特点碱性锌酸盐镀锌是以氧化锌为主盐,以氢氧化钠(烧碱)为络合剂,它的特点是对电镀设备没有腐蚀性,镀层结晶细致光亮,成本较低,原材料来源广,槽液稳定,容易掌握。
但必须加适量的添加剂,才能使镀层达到结晶细致、光亮的效果。
近年来,锌酸盐镀锌在国内应用广泛,主要是这一工艺具有许多优点,如镀液成分简单、稳定,使用工艺范围比较宽,分散能力和覆盖能力较好,镀层结晶细致,只要选择添加剂适当,就能达到较高光亮镀层,且容易钝化处理,操作方便,维护简单,污染小,无剧毒氰化物。
镀后污水处理方便,有利于环境保护,适应于机械化、自动化生产,如钢管等几何形状复杂的大小五金件镀锌实效显著。
/0 锌酸盐镀锌工艺规范国内近年来碱性锌酸盐镀锌添加剂品种繁多,但工艺配方实质都大同小异。
现将国内应用较广的12 与132 型两种锌酸盐镀锌的主要配方及工艺条件列于表! " # " $!。
#"! 第四篇电镀工艺新技术应用与典型实例表! " # " $! %& 与%’& 两类锌酸盐镀锌配方及工艺条件成分及工艺条件配方# 配方( 配方) 配方! 配方$氧化锌(*+,)(- . /) #0 1 #$ #0 1 #$ #0 1 #( ## 1 #) #0 1 #(氢氧化钠(23,4)(- . /) #00 1 #)0 #00 1 #$0 #00 1 #(0 ##0 1 #)0 #00 1 #(0#香草酸(- . /) 050$ 1 05#三乙醇胺(- . /) #( 1 )0乙二胺四乙酸(&%67)(- . /) 05$ 1 #%&(8/. /) ! 1 9 ) 1 $*:% " ;<(8/. /) ( 1 $%’& " !(8/. /) ! 1 9 ! 1 $ ! 1 9=> " (8/. /) # 1 #5$*: " ;0(8/. /) ( 1 !温度(@) #0 1 !0 !0 1 #00 !$ 1 #00 !$ 1 #00 !0 1 #00阴极电流密度(7. A8) 05$ 1 ) $ 1 #! 9 1 #! 9 1 #! 05$ 1 !添加剂类型%’& " !型%& 型%& 型%’& " !型%’& " !型)5 镀液中各种成分的作用(#)氧化锌锌的含量对镀液性能与镀层质量具有重要的作用。
- 1、下载文档前请自行甄别文档内容的完整性,平台不提供额外的编辑、内容补充、找答案等附加服务。
- 2、"仅部分预览"的文档,不可在线预览部分如存在完整性等问题,可反馈申请退款(可完整预览的文档不适用该条件!)。
- 3、如文档侵犯您的权益,请联系客服反馈,我们会尽快为您处理(人工客服工作时间:9:00-18:30)。
环保碱性锌酸盐镀锌浅谈(2007-12-29 22:23:49)标签:杂谈随着人们的生活水平的不断提高,环保意识也在逐渐的增强。
众所周知,电镀是一个高污染的行业,怎样使电镀行业达到清洁生产的确目的,是我们每个电镀技术工作者的共同的目标。
就单纯的镀锌而言,用无氰锌酸盐代替有氰镀锌,是实现环保电镀的一个很好的实例。
但在实际生产操作过程中,由于无氰电镀比有氰电镀控制起来要困难的多,而且生产成本也比较高,尤其是对于一些高质量要求的镀锌件来说,氯化钾镀锌达不到要求。
所以很多的生产厂家不愿采用,继续采用老工艺有氰电镀,给推广环保型镀锌造成了一定的阻力。
但做为现在的碱性锌酸盐镀锌体系来讲,在工艺性能方面已经完全可与之想媲美,现将本人在使用环保碱性锌酸盐镀锌的过程中产生的一些故障及排除方法做一下浅谈,希望能为推广环保型电镀生产出一份力,给我们的子孙后代后代留一片净水。
1 工艺流程本公司所采用的碱性镀锌工艺是才用自动生产线,工艺流程为:热脱脂——清洗—清洗——喷淋清洗——酸洗——清洗——清洗——喷淋清洗——电解脱脂——清洗——清洗——喷淋清洗——弱酸中和——喷淋清洗——碱性锌酸盐镀锌——清洗——清洗——喷淋清洗——出光——清洗——钝化——清洗——清洗——喷淋清洗——热水清洗——烘干——包装。
2 工艺条件及配方工艺配方如下:NaOH 50-80g/lZnO 8-15g/lA(主光剂) 10—25mL/LB(走位剂) 1—3mL/LC(净化剂) 0.5—1mL/L3 工艺影响因素3.1 NaOH。
氢氧化钠的含量的多少直接影响到产品质量的好坏。
尤其是对高光亮度的基体。
含量过少,阳极很容易钝化。
造成发雾现象,表面粗糟无光,分散能力变差,低区发黑。
对于镀锌后要进行机械加工的零件来讲,还容易造成脆性增大的现象。
含量过高,则上镀速度比较慢。
本人认为最佳的含量为130-140g/l。
3.2 ZnO。
氧化锌的含量高低因选用的光亮剂的不同而不同。
有的厂家的要求含量要低一些的,有的要求含量要高一些的。
本人认为控制氢氧化钠和氧化锌的比例是相当重要的。
锌离子提高了,氢氧化钠的含量也必然要提高的。
最好控制在10-12:1。
3.3 温度。
温度是影响碱性锌酸盐镀锌质量的一个很重要的因素。
现在在使用的光亮剂,包括国外厂家生产的光亮剂,所使用的温度一般都是在35度以下,超过这一温度,则镀液很难维护,光亮剂消耗的量也会增大。
还容易出现大面积的脱皮现象。
3.4 电流。
电流密度可在1-5A/dm2个之间变化。
有的是在1-3A/dm2之间。
电流密度过大,高区烧焦,镀层脆性增大。
过小,低区的不好,亮度不足发暗。
3.5 杂质。
由于碱性无氰锌酸盐镀锌没有有氰镀锌抗杂的能力强,因此杂质的影响比较厉害。
当杂质含量高时,将影响到低电流密度区发黑,镀层脆性也变大,还有一个情况就是将影响到后处理。
尤其是蓝白钝化,很容易发黄。
很多的时候都以为是钝化槽不好,调整钝化液。
往往是效果不是很理想的。
在这种情况下,要考虑一下镀槽的杂质影响了。
3.6 光亮剂。
光亮剂因生产厂家的不同而有差异。
参考所购买的厂家的使用说明书做调整即可。
尽量一少加勤加为原则。
光亮剂加入的太多,很容易造成镀层脆性的增大。
5 几种常见现象的排除方法(1) 分散能力差,低区发黑、锌含量高、碱含量低、金属杂质的影响。
(2) 镀层脱皮,有小鼓泡。
有机杂质含量高。
光亮剂含量太高,面有油污,前处理不好。
(3) 镀层出现像流眼泪状态一样的雾状白斑。
对与这种白斑,很多的人都认为是重金属杂质的影响的,对镀液进行大处理进行解决。
但本人在实际生产中发现如果在弱酸性中和后再用1%的氢氧化钠中和的话,这一问题就可以得到解决。
出现这种现象往往是在氢氧化钠和锌离子含量都比较低的情况下。
(4) 块状白斑。
这种白斑出现有两种可能性。
一种是前处理不净有油污,尤其是点焊连接有夹缝的零件。
一种是基体表面在入槽电镀前有浮锈生成的原因造成的。
(5) 镀层脱皮,有小鼓泡。
对于镀锌后要进行机械加工的零件来讲,脱皮是很重要的一个问题,分析原因有四个方面:其一,前处理不良;其二,光亮剂加入的太多;其三,杂质的影响。
出现这种情况时,用活性碳的处理效果不是很理想的。
用锌粉的处理效果好,但光亮剂的损耗很大。
建议最好是用CK—778综合处理剂或者是一些专门的碱性镀锌除杂剂处理,效果比较理想。
(6) 镀层大面积脱皮。
温度过高是很重要的一个影响因素对于碱性锌酸盐镀锌电镀,本人能力有限,可能有些问题分析的不是很正确,希望能给予指正。
用无氰电镀代替有氰电镀,是大势之所趋,现在随着国家对氰化物的控制的不断增强,无氰电镀将大有市场。
锌酸盐镀层海绵状(2007-10-12 20:51:31)原因:当锌酸盐镀锌液中添加剂不足时,有可能造成镀锌层结晶粗糙,因为锌酸盐镀锌的添加剂多属表面活性剂,在电沉积过程中,添加剂在很宽的电位范围内吸附,从而减缓镀液中锌离子的放电步骤,提高了阴极极化,使镀锌层结晶细致、光亮。
解决:镀液中添加剂含量目前尚未有时用准确地分析方法,一般是根据生产过程中镀层质量,凭经验或者赫尔槽试验添加。
添加剂不宜过量添加,否则会出现镀层发花,钝化膜发雾,镀层起泡,脆性增大,镀层易变色,结合力下降等故障。
从一例锌酸盐故障排除谈镀液管理(2007-10-12 20:51:31)某乡镇电镀厂锌酸盐镀锌银出现灰暗发黑故障影响生产,邀请笔者前去帮助解决,在生产现场,让镀些工件看看情况。
铁槽有DPE锌酸盐镀锌溶液2000升,镀液混暗不清,极缸上的阳极板与铁板相间各占一半。
铁阳极析出大量的氧气泡向液面扩散,很快将锌阳极析出的氧气泡与阴极析出的细小氢气泡所覆盖而布满液面。
一面观察电极反应, 一面同他们交谈。
按笔者询问回答: 铁阳极长期挂用与锌阳极停镀镀不取,是看邻村镀锌那样操作的, 只是多挂了几块铁板, 能将锌板节省点。
原料补加, 没条件化验, 是粗估估加的。
半小时后工件出槽观察, 镀层较薄, 色泽灰暗显黄, 低电流区发黑。
从现场所见与询问了解,故障非常明显,是以二价铁为主的多种杂质污染镀液所造成的。
气泡发黄, 镀层低电流区发黑是铁杂质过量的反应,长期挂用铁板, 产生微溶解,不断蓄积,又是铁杂质的主要来源。
由于长期挂铁板,使主盐浓度下降,加之NaOH偏低,导电性差,都能使沉积速度慢而镀层薄。
锌阳极与化工原料不纯, 夹杂的铅离子与油污等使镀层灰暗。
故障明显,处理简单,只需将溶液净化按工艺调整即可消除。
锌酸盐镀锌溶液的净化,按常规方法,用锌粉和活性炭联合处理过滤即可。
加锌粉后搅拌静置1-2小时便要过滤,否则金属杂质将重新进入溶液,影响处理效果。
对不加三乙醇胺的锌酸盐镀锌溶液用联合处理的方法效果良好,如果加有三乙醇胺的溶液则毫无效果。
因三乙醇胺能络合铁及其它金属离子,难于去除, 用CK-778净化剂处理效果良好, 该厂没有, 购回后用量为3 g/L( 因镀液污染严重),边搅拌边加入。
不一会,只见溶液内凝聚的黑色沉淀物,犹如小虫群聚在溶液内上下滚动跳跃,笔者指着对大家说,就是这些杂质引出的故障。
“小虫”的上下浮游, 由多到少,逐步沉入槽底, 一小时后全部沉淀, 开始过滤, 取样回厂对溶液成份帮助分析之后进行调整,停挂铁板, 试镀工件,镀层恢复了锌酸盐本来的米黄色泽, 经硝酸出光高铬钝化, 膜层色泽鲜艳夺目,生产恢复正常。
锌酸盐镀锌以镀层细致光亮, 钝化膜不变色和没有氰污染而成为镀锌的主要工艺o由于溶液稳定 , 对杂质敏感性小, 一般很少出现镀层质量故障。
溶液稳定也需维护管理, 对此忽视, 稳定就会转化为不稳定, 比如溶液成份比例失调,各种杂质的进入, 都是不稳定因素, 这时便会导致各种故障的产生。
本文故障就是由于忽视溶液维护管理,受到多种杂质的污染所致, 是应引以为训的。
现将笔者在10年锌酸盐镀锌实践中, 对溶液维护管理所采取的措施,简要介绍,以供参考。
1.新配槽液与补加化工原料必须处理氧化锌与氢氧化钠是锌酸盐镀锌的主要化工原料,大多用工业级的, 杂质含量较大的品种也较多。
氧化锌中的铅离子、氢氧化钠中的铁离子含量都偏高。
所以在新配槽或补加时,都要用1-2g/L的锌粉处理过滤入槽,这就能减少杂质的进入量,消除它们对镀层质量的不良影响。
2.加强前处理防止油污进入镀液锌酸盐镀锌是碱性溶液, 由于自身有去油作用,因而有的对除油不够重视,油污不多的工件,甚至不除油,酸洗后便入槽电镀。
大量油污进入镀液,这些油脂在镀液中分散成微滴,粘附到工件上,有油污处导电不良,致使没有镀层沉积,形成气泡。
这是锌酸盐镀锌常发生镀层起泡故障的主要原因之一。
所以加强前处理,是维护好溶液不可缺少的措施。
3.定期分析镀液成分保持正常稳定碱性镀锌的主要成份是氧化锌与氢氧化钠,它们之间的比例为1:8-11。
定期分析,就是要将它们的含量控制在工艺规范内。
特别是氢氧化钠,它不仅与锌离子络合成稳定的锌酸盐, 同时使锌阳极保持正常溶解, 提高溶液的导电性。
它对主盐浓度的稳定关系极大, 氢氧化钠含量低于下限, 溶液导电性差,槽电压上升,沉积速度慢,甚至镀不上, 特别是阳极容易钝化。
阳极停止溶解后,溶液中锌离子急剧下降,使主盐浓度比失调; 高于上限, 锌阳极溶解加快, 溶液中锌离子不断上升,也会导致浓度比失调, 使镀层质量恶化, 如发暗、粗糙等。
因此定期分析溶液成份,及时调整,保持溶液的稳定正常,是锌酸盐镀锌维护溶液的重要措施。
4.正确使用两种阳极保持主盐浓度稳定锌酸盐镀锌主盐浓度,在笔者的实践里, 一般清况下,不是低而是逐步处于上升趋势。
这是由于溶性锌阳极溶解较快,特别是氢氧化钠含量高时更快,另一情况是停镀后不取出锌阳极而产生的自溶解,这是主盐浓度升高的基本原因。
为此,工艺常以挂入不溶性阳极来控制或降低主盐浓度。
不溶性阳极有不锈钢板、铁板、镍板等, 不锈钢板含有铬、镍等金属,要微溶解,进入镀液产危害: 铁板长期挂用,也因微溶解而增加铁杂质杂;镍板效果良好, 但价格昂贵,可在普通钢板上镀一层厚镍取代镍板是比较经济的。
为减少异金属杂质和阳极泥渣进入镀液产生危害,应以高纯度锌作阳极并加阳极套。
正确使用两种阳极的方法,停镀时取出锌阳极浸泡在清洗槽中待用。
氢氧化钠含量控制在工艺内,不溶性阳极一般不用,当主盐浓度高时才挂用。
可溶性阳极与不溶性阳极面积比一般为3-4:1(也可根据锌含量增减),主盐浓度降至工艺(通过分析)时,应取出不溶性阳极, 否则主盐浓度过低也会影响主盐浓度稳定,进而使镀层质量恶化。
5.镀液的日常维护管理除定期分析溶液成份及时调整外,还要定期净化溶液。
溶液洁净, 能保持电镀质量的稳定。
净化溶液, 一般三月或半年用锌粉与活性炭联合大处理一次,去除过量杂质,保持溶液洁净。
另外,在日常生产中, 还要注意: 一是加强前处理,工件除油去锈要彻底;二是注意阴阳极面积比, 即SK:SA=1:1.5-2 , 防止阳极面积过小使阳极电流密度增大而钝化,阳极停止溶解,锌离子浓度下降,同时也要注意阳极面积不能过大,这样阳极溶解多而锌离子浓度升高。