轻金属半固态成形技术-第4章
轻金属半固态成形技术-第2章

2.1 组织形成与演化机制
2.1.3 枝晶臂塑形弯曲和晶界浸润熔断机制 —— Vogel 等人的观点
★ 假设在接近熔点温度下,初生的α-Al枝晶具有一定的 韧性;虽然此温度下的α-Al枝晶较脆弱,但这种假定 的韧性使得α-Al枝晶在搅拌的紊流之中只发生弯曲而 不至于断裂。
2.1 组织形成与演化机制
2.1.4 电磁搅拌下的枝晶臂根部熔断机制 —— 毛卫民、Hellawell 等人的观点
在电磁搅拌下,合金熔体组织中出现许多细小的蔷薇 状初生固相,这些蔷薇状初生固相的二次枝晶臂几乎 不发生弯曲;
搅拌使熔体产生强烈的温度起伏,使得二次枝晶臂根 部熔断;
熔断的二次臂不断与合金熔体及固相之间发生摩擦与 熟化,从而逐渐球化。
随着初生枝晶臂碎块熟化的进行,初生枝晶臂碎块逐渐转变为更加密 实的蔷薇状,如图(d)所示;
只要在较高的搅拌剪切速率和较低的冷却速率下,初生枝晶臂碎块最 后会转变为球状或椭球状,如图(e)所示。
枝晶根部熔断的根本原因:外场作用下引起流体的流动导致 溶质扩散加快、产生流动应力、促使溶质偏聚等作用。
演化过程从(a)到(e),随着剪切速率的提高和冷却速率 的降低而加快。
搅拌
树枝晶
枝晶断裂,晶体 变圆、变小
圆形或半圆形的初晶 表观粘度减低
AlSi7Mg合金显微组织
(a) 传统凝固的枝晶组织 (b) 电磁搅拌的半固态组织
半固态Sn-15wt%Pb合金流变组织
固相分数0.45,剪切速率230s-1 搅拌时间:(a)730s,(b) 2400s
轻金属半固态成形技术-第5章

❖ 该加热系统设置了12个加热工位,4个高功率加热工位、4个中功率加 热工位、4个低功率加热工位;在该系统加热时,每通电加热36s,然 后间断14s,进行坯料加热工位轮换,再重复前面的动作,直至坯料从 最后一个感应加热器中轮换出来;每块坯料的总加热时间为7.2min, 但该半固态重熔加热系统在一个小时内却可以提供72块半固态A356 铝合金坯料,从而满足了半固态触变成形的工艺的需要。
5.1.2 金属坯料的电磁感应半固态重熔加热
❖ 从技术角度看,电磁感应加热固态金属坯料并不是新型技术,电 磁感应加热很早就得到比较普遍的应用,如锻造中钢坯或其他金 属坯料的电磁感应加热、轧制中金属坯料的电磁感应加热、轧辊 热处理的电磁感应加热等。这些电磁感应加热温度比较低、温度 控制精确度也低、加热工艺相对比较简单。
当感应电流在闭合回路中流动时,自由电子要克服各种阻力。 所以,自由电子必须消耗一部分能量做功来克服导体的电阻, 这部分能量就转变为热能。焦耳-楞茨定律就是描述这种电 能转变为热能的变化规律,即电流通过导体所生成的热量与 电流的平方、导体的电阻和通电时间的积成正比,其数学表 达式如下:
金属坯料在电磁感应加热时,金属坯料处于感应加热线圈中,当感应 线圈通以交变电流时,金属坯料就处于交变磁场中,在金属坯料内产 生交变感应电动势。
金属坯料可以看成是由一系列半径逐渐变化的圆柱状薄壳组成,每层 薄壳自成一个闭合回路,在每层薄壳中会产生感应电流。从金属坯料 的上端俯视,电流的流线呈闭合的涡旋状,因而,这种感应电流叫做 涡电流,简称涡流,如图6-1所示。
由于大块金属坯料的电阻 很小,因此,涡流的强度非 常大,产生大量的焦耳热, 金属坯料就是被这种焦耳热 不断加热和熔化。
❖ 当每块坯料顺序经过所有的感应加热器后,其温度或固相率应该达 到触变成形要求,每块坯料的总加热时间等于单个感应加热器的加 热时间乘以感应加热器的数量。从每块半固态坯料的加热时间看, 它的加热时间也可以达到数分钟,但从整个加热系统看,加热系统 可以在预定的时间内提供一块合适的半固态坯料,如图6-8所示。
第5章 半固态流变成形技术
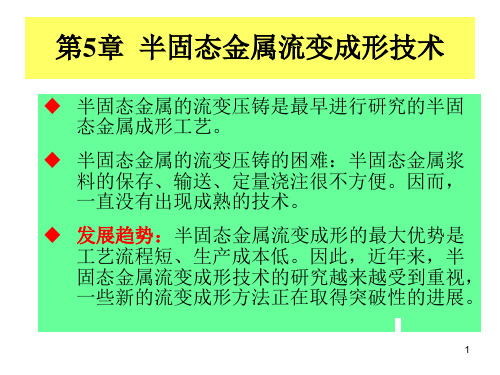
25
流变射铸技术的特点和发展现状:
与触变射铸相比,单螺旋流变射铸工艺的最大优点: 工艺流程短,生产成本低; 废品和铸件余料回收方便; 流变射铸件气孔率低。
目前,单螺旋流变射铸工艺尚未达到实际应用水平, 正处在设备完善和生产工艺优化阶段。
26
5. 4
双螺旋机械搅伴式流变成形
1999 年, 英国 Brunel 大学的ZY Fan,提出了双螺旋 机械搅拌流变射铸工艺。 其原理如下:
双螺旋机械搅拌流变射铸设备主要包括液态合金供料机构、 双螺旋机械搅拌机构、压射机构和中央控制机构。 液态合金进入搅拌系统,一边被双螺旋搅拌桶强烈地搅拌, 一边被快速冷却到预期的固相分数;当半固态合金浆料到 达输送阀时,初生固相已经转变为球状颗粒,并均匀分布 在低熔点的液相中;当输送阀打开时,半固态合金浆料进 入成形压射室,被压入压铸型型腔,成型零件。 在双螺旋搅拌机构中设置了许多的加热和冷却通道,可以 准确的控制合金桨料的温度,控温精度可达土 1 ℃ 。
31
Any Questions ?
32
a
b
c
d
e
f
g
a—连续制备半固态浆料 b—制备半固态锭坯 c—定量分割坯锭 d— 重 新 加 热 至 半 固 态 e— 送 至 压 射 室 f — 成 形 过 程 g—成品
4
主要介绍的流变成形工艺:
1. 传统机械扰拌式流变成形 2. 压射室制备浆料式流变成形 3. 单螺旋机械搅拌式流变成形 4. 双螺旋机械搅拌式流变成形 5. 低过热度倾斜板浇注式流变成形 6. 低过热度浇注和弱机械搅拌式流变成形 7. 低过热度浇注和弱电磁搅拌式流变成形 8. 流变轧制成形
27
28
轻金属半固态成形技术-第1章

轻金属
原子质量较轻的金属。轻金属的一种定义是密 度低于 4.5g/cm3 的金属,也有说比重小于5。 不论使用哪一种分类法,铝、镁、锂、钠几乎 都列在轻金属中。铝的比重是2.7,镁的比重是 1.7。
主要应用在汽车工业、电子信息、航空航天等 领域
金属半固态成形
若在金属凝固过程中,对其施以剧烈的搅拌作用
Flemings, Professor of MIT
1.1美国、日本的重点在成 形工艺的开发上。在发达国家,铝合金半固 态加工技术(触变成形)已经成熟并进入规 模生产,主要用于汽车、电器、航空航天等 领域。
镁合金的半固态成形技术发展较晚,目前成 熟的只有触变成形技术。
圆形或半圆形的初晶 表观粘度减低
AlSi7Mg合金显微组织
(a) 传统凝固的枝晶组织 (b) 电磁搅拌的半固态组织
半固态Sn-15wt%Pb合金流变组织
固相分数0.45,剪切速率230s-1 搅拌时间:(a) 730s,(b) 2400s
课程性质及目的
通过本课程的学习,使学生了解轻合金半固态成 形基础知识及基本原理,使学生掌握半固态金属 浆料的流变充填行为,了解填充结束后的高压凝 固-塑性变形的复合成形过程,了解半固态成形过 程的物理、化学和力学本质;重点掌握半固态成 形的工艺过程,包括材料和制备方法的选用、二 次重熔、半固态压铸、半固态模锻和触变注射及 其相关内容,初步掌握分析和解决轻合金半固态 成形技术应用领域中各种实际问题的能力。
触变压铸成形工艺示意图
(a) 连续搅拌制备半固态浆料 (b) 半固态浆料凝固成坯料 (c) 坯料切分 (d) 坯料半固态重熔加热 (e) 坯料被送入压射室 (f) 压射成型 (g) 压铸件
半固态铝合金坯料水平连铸机
科技成果——轻合金半固态流变压铸成形工艺与设备
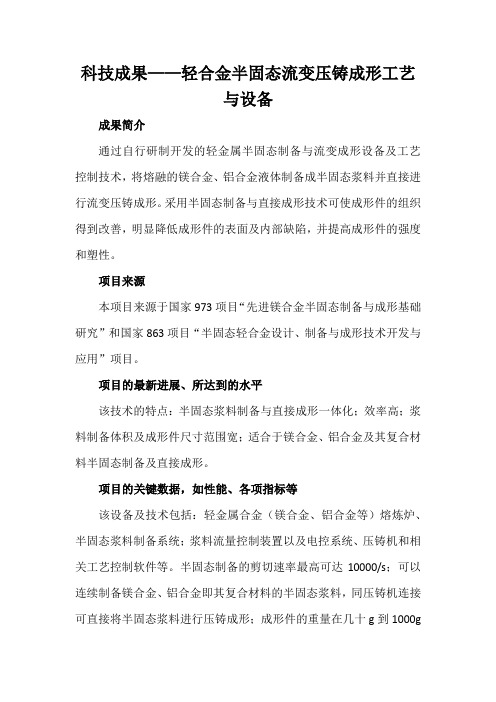
科技成果——轻合金半固态流变压铸成形工艺与设备成果简介通过自行研制开发的轻金属半固态制备与流变成形设备及工艺控制技术,将熔融的镁合金、铝合金液体制备成半固态浆料并直接进行流变压铸成形。
采用半固态制备与直接成形技术可使成形件的组织得到改善,明显降低成形件的表面及内部缺陷,并提高成形件的强度和塑性。
项目来源本项目来源于国家973项目“先进镁合金半固态制备与成形基础研究”和国家863项目“半固态轻合金设计、制备与成形技术开发与应用”项目。
项目的最新进展、所达到的水平该技术的特点:半固态浆料制备与直接成形一体化;效率高;浆料制备体积及成形件尺寸范围宽;适合于镁合金、铝合金及其复合材料半固态制备及直接成形。
项目的关键数据,如性能、各项指标等该设备及技术包括:轻金属合金(镁合金、铝合金等)熔炼炉、半固态浆料制备系统;浆料流量控制装置以及电控系统、压铸机和相关工艺控制软件等。
半固态制备的剪切速率最高可达10000/s;可以连续制备镁合金、铝合金即其复合材料的半固态浆料,同压铸机连接可直接将半固态浆料进行压铸成形;成形件的重量在几十g到1000g左右;配备压铸机的能力在180-600吨。
项目的应用范围、领域该项目可应用于镁合金、铝合金压铸成形,在汽车、电子通讯、航空、机械等部件制造以及军用装备轻量化等领域应用。
经济效益分析的各项数据采用半固态制备并直接流变成形镁合金和铝合金部件,可提高成形件的表面及内部质量,改善组织均匀性和提高力学性能,同触变成形工艺(先制备半固态坯料再进行二次加热)相比,明显缩短了工艺流程,降低了半固态制备与成形的生产成本,经济效益明显。
市场前景预测该项目采用先进的半固态制备并直接流变成形镁合金和铝合金部件工艺技术,同普通液态铸造或液态压铸相比,不仅可提高成形件的表面和内部质量,而且可以明显改善组织均匀性和提高力学性能,在汽车、电子通讯、航空、机械等领域具有广阔的市场前景。
投资额、规模、收益(包括设备投资、水电费用、原料等)一套半固态浆料制备、流量控制系统(包括机械、加热与控制系统)和压铸成形机等设备投资在120-180万元,用电量约200kw,原料为普通铸造镁合金或铝合金。
半固态金属成形技术

二、半固态成形技术的发展简史
起源和发展
半固态加工起源于美国。20世纪70年代初,麻省理工学院 Spencer和Flemings等人发现凝固过程中的金属材料经强力搅 拌,会生成近球状晶或球状晶组织。 30多年的发展历程中,SSM技术在制坯、重熔加热、零件成 形、组织与力学性能、加工环节数值模拟以及合金流变学研究 等许多方面取得重大进展。目前,这项技术已广泛应用于汽车 工业领域,在航空、航天以及国防工业领域也正处于应用的起 步阶段,具有广阔的前景。 半固态金属加工技术是近多年来才诞生和发展起来的现代 冶金加工新技术。它虽然诞生晚, 但发展很快, 只用十几年的 时间就从试验室过渡到试生产, 又很快实现了产业化和商品化。 被世人称为新一代的合金成形工艺。
三、半固态金属加工的优缺点
优点:
(1) 由于在半固态, 合金具有独特的触变 行为, 可成型复杂的薄壁的零部件
(2)加工件的精度高, 几乎是近净成形, 尺 寸公差接近机加精度 (3)成形件表现平整光滑, 内部组织致密, 缺陷少, 晶粒细小, 力学性能高,可达锻 件性能
(4)节省原材料、能源, 生产同样的零部件, 它与普通铸造相比, 节能约35% (5)成品率高, 几乎达100%
半固态金属成形
一、概念
半固态金属成形技术(Semi-Solid Metal processing,SSM),它是利用在固-液态区间 获得一种液态金属母液中均匀地悬浮着一定固 相组分(50%-60%)合金的混合浆料进行加工 成形的方法。 半固态成形是利用金属材料从固态向液态, 或从液态向固态的转换过程中具有半固态的特 性所实现的成形。
影响因素对结构影响的具体分析
1、板长固定,不同板角下的组织形貌
20度
5度
7.5度
轻金属半固态成形技术-第3章
❖ 利用变形诱变激活工艺制备半固态金属坯料时,也可以 不进行冷变形,只进行大变形量的热变形,如锻造、挤 压,然后将变形后的坯料进行半固态重熔加热,也可以 得到近球状的半固态组织。
❖ 通过对仅热变形的7075铝合金坯料进行触变成形实验, 发现其合适的重熔加热温度为600-610oC,此时对应的 液相分数为15%~30%,但重熔加热组织形态和成形后 的组织形态均不太理想,存在长条状颗粒,触变成形性 也较差。
变形诱导激活工艺的优点与缺点:
该工艺方法制备的金属坯料纯净、生产效率高、产量大, 主要用于锻铝及铁基材料,是目前商用方法之一;
需要很大的挤压变形量,导致坯料价格昂贵、断面小, 只能制备小直径的半固态坯料,只能生产小型零件,如 美国阿卢马克斯工程金属工艺公司利用该法生产军用航 天器中的一种小型电器连接零件。
3.1 机ห้องสมุดไป่ตู้搅拌方法
3.1.1 非连续机械搅拌法
➢ 最早应用于制备半固态金属浆料的方法; ➢ 利用机械旋转的叶片或搅拌棒使金属熔体激烈流动,
获得球状初生固相的半固态金属浆料; ➢ 通过控制搅拌室的温度来控制半固态金属的固相率,
通过控制搅拌棒的转速来控制剪切速率,可以保证剪 切速率不变; ➢ 该装置结构简单,造价低,操作方便,可以添加各 种气体保护,但产量很小,只适用于实验室的小规模 试验研究工作,见下图。
变形诱变激活工艺制备A357铝合金坯料的显微组织 (a) 连铸坯组织 (b)挤压变形后的组织 (c) 重熔加热后的组织
•a是A357铝合金连铸棒坯的铸态组织,初生α-Al为发达的树枝晶; •b是经过大变形量的热挤压和小变形量的冷变形后的A357铝合金坯 料显微组织,初生α-Al呈现明显的变形状态; •c是经过快速半固态重熔加热的A357铝合金坯料显微组织,初生αAl已经变为球状晶粒,初生α-Al均匀分布在液相中。
材料工程基础课件-第四章 金属的液态成形与半固态成形
七、 特种铸造
为获得高质量、高精度的铸件,提高生产率,人们在 砂型铸造的基础上,创造了多种其它的铸造方法;通常把 这些有别于砂型铸造的其他铸造方法通称为特种铸造。
低压铸造
消失模 铸造
熔模铸造
压力铸造
七
种
常
见
特种铸造
金属型 铸造
的 特 种
铸
造
连续铸造
离心铸造
方 法
充型能力不足时,会产生浇不足、冷隔、夹渣、气孔 等缺陷。
2.液态合金的流动性
合金的流动性是: 液态合金本身的流动能力。
改善金属 有利于 的流动性
金属流动性 测试实验
实验如右图所示:
形成薄壁复杂的铸件 排除内部夹杂物和气体 加快凝固中液体的补缩
合金流动性主要取决于合金化学成分所决定的结晶特点
温度(℃)
(一)熔模铸造
熔模铸造又名“失蜡法铸造”是用易熔材料制成 模样,然后在模样上涂挂若干层耐火涂料制成型 壳,经硬化后再将模样熔化,排出型外,从而获 得无分型面的铸型。铸型经高温焙烧后即可进行 浇注。
1. 熔模铸造的工艺过程
蜡模制造 结壳
脱模
焙烧
浇注
熔模铸造过程示意图
2. 熔模铸造的主要特点及适用范围
3.成本低:(1)材料来源广; (2)废品可重熔; (3)设备投资低。
4.废品率高、表面质量较低、劳动条件差。
铸造方法受零件的尺寸、重量和复杂程度的限制较少; 可铸壁厚:0.3~1m 长度范围:几个毫米到几十米 质量范围:几克到几百吨
用铸造方法可以生产铸钢、铸铁、各种铝合金、铜合金、 镁合金、钛合金、锌合金等铸件。
合金的线收缩受到铸型、 型芯、浇冒系统的机械阻 碍而形成的内应力。
举固态成形技术讲座第四讲半固态模锻
举固态成形技术讲座第四讲半固态模锻
罗守靖
【期刊名称】《金属加工:热加工》
【年(卷),期】2004(000)006
【总页数】4页(P74-77)
【作者】罗守靖
【作者单位】哈尔滨工业大学,黑龙江,150001
【正文语种】中文
【相关文献】
1.半固态成形技术讲座--第一讲半固态成形、特点及应用范围(上) [J], 罗守靖
2.半固态成形技术讲座第二讲半固态成形工艺过程分析(上) [J], 罗守靖
3.半固态成形技术讲座第二讲半固态成形工艺过程分析(下) [J], 罗守靖
4.半固态成形技术讲座第三讲半固态压铸 [J], 罗守靖
5.半固态成形技术讲座第五讲半固态成形技术的研究进展与预测 [J], 罗守靖因版权原因,仅展示原文概要,查看原文内容请购买。
第四章 金属的液态成形与半固态成形 第一节 液态成形
第四章金属的液态成形与半固态成形第一节液态成形一.特点1.把金属变为变形阻力小的液态金属,浇入铸型后,一次制作出所需形状的铸件。
故适应性强,工艺灵活性大,几乎所有的工程材料都可以用液态成形。
2.成形件精度高。
3.成本低廉。
4.零件力学性能差,常存有缺陷,组织疏松、晶粒粗大、质量不稳定,生产过程劳动强度大、条件差、生产率低。
二.发展史三.液态成形合金性能液态成形过程合金要发生一系列物理、化学变化,并对铸件的质量性能产生极大影响,故液态成形合金必须具有合适的性能要求。
(一)合金的充型性能作为最基本要求,液态金属要能充满铸型型腔,获得形状完整,轮廓清晰的健全铸件,并防止铸件产生浇不足,冷隔等缺陷。
影响合金充型能力的因素有:1、合金的流动性:作为合金本身性能,它与合金成分、温度、杂质含量及物理性能有关;2、浇注条件:其中包括浇注温度、充型压力与浇注系统的结构。
决定性影响的因素是温度。
在一定范围内,随着温度提高,合金的粘度减少,充型能力提高。
但超过某界限后,合金液氧化、吸气严重,易产生缩松、气孔等缺陷。
提高充型压力(增大静压头高度,压铸)可提高充型能力。
浇铸系统结构较复杂(如蛇形浇道),流动阻力增加,相同静压条件下,充型能力小。
3、铸型性质及结构铸型从合金中吸收及储存热性能的能力称蓄热能力。
材料的导热率、比热越大,它也越大。
大的蓄热能力使合金的充型能力变差,预热铸型,降低合金液与铸型温差,减缓合金液冷却速度,能提高合金的充型能力。
加强铸型结构的排气,能减少铸型的发气,提高充型效果。
铸型结构不合理,如壁厚太小,急剧变化,过大的水平面等结构能产生较大流动阻力,充型能力大大受影响。
(二)合金的收缩,铸件缩孔、缩松特征1、液态合金在冷却凝固过程中,体积、尺寸均缩小的现象称为收缩,是产生缩孔(松)、变形、裂缝的原因。
有体收缩和线收缩两种,发生在液态收缩和凝固收缩的体收缩是缩孔、缩松形成的主要原因。
固态收缩表现为铸件外形尺寸的线收缩,是产生铸造应力、变形、裂缝的主要原因。
- 1、下载文档前请自行甄别文档内容的完整性,平台不提供额外的编辑、内容补充、找答案等附加服务。
- 2、"仅部分预览"的文档,不可在线预览部分如存在完整性等问题,可反馈申请退款(可完整预览的文档不适用该条件!)。
- 3、如文档侵犯您的权益,请联系客服反馈,我们会尽快为您处理(人工客服工作时间:9:00-18:30)。
立式流变射铸的工艺如图5-12。
❖ 流变射铸使用过热的液态合金;
❖ 而过热液态905铜合金的 压铸件中则出现许多气孔, 如图所示,浅色区域为气 孔。
4.2 压射室制备浆料式流变成形
为了避免半固态合金浆料的存储和输送,日本Hitachi金属 有限公司Shibata等人提出在立式压铸机的压射室中制备半 固态合金浆料,然后直接压射成形,如图5-5所示。
对浇入压射室中的AlSi7Mg铝合金进行电磁搅拌,铝合金熔体在搅 拌中不断冷却;到铝合金熔体冷却到适当的温度,就制备出了具有 触变性的半固态浆料。
❖ 然而,早期通过强烈机械搅拌获得的半固态金属浆 料的保存和输送很不方便,因而,半固态金属流变 成形技术的进展很缓慢,一直没有出现成熟的技术。
❖ 但是,半固态金属流变成形的最大优势是工艺流程 短、生产成本低。因此,近年来,半固态金属流变 成形技术的研究越来越受到重视,一些新的流变成 形方法正在取得突破性的进展。
❖ 液态合金从浇注漏斗中流入搅拌 桶和螺旋杆的缝隙中,以氩气保 护浇注漏斗,防止合金的氧化;
❖ 合金熔体在向下流动过程中,不 断被搅拌剪切和冷却,当合金熔 体到达出口时,半固态合金浆料 达到预定的固相分数,初,螺旋杆先后退一定 的距离,使螺旋杆前端积聚足 量的半固态合金浆料,然后螺 旋杆以一定的轴向速度将其前 端的半固态合金浆料压入模具 型腔;
第四章 半固态流变成形技术
1 传统机械搅拌式
2 压射室制备浆料式
3 单螺旋流变射铸 4 双螺旋流变射铸
5 低过热度倾斜板浇注式
6 低过热度浇注和弱搅拌式
7
流变轧制成形
4.1 传统机械搅拌式流变成形
➢ 在早期的研究中,美国MIT的Flemings等 曾经研究过A380铝合金和905铜合金的 半固态流变成形,两种合金半固态浆料都 是通过机械搅拌法制备的;
❖ 压射室外增加了感应加热器,用以均匀半固态浆料 的温度场;
❖ 从1999年开始,该技术已经用于汽车零件的生产。
压射室制备半固态浆料压铸工艺的缺点:
在压射室中制备半固态铝合金浆料的效率较低; 电磁搅拌容易引起合金熔体的飞溅和氧化; 压铸机压射室的结构过于复杂,降低了压铸机的生产效
率,压射室的寿命不可能的太长; 非搅拌制备半固态铝合金浆料时压射室边缘处的组织仍
非连续机械搅拌装置制备A380铝合金半固态浆料
➢ 在搅拌制备过程中,当A380铝合金 冷却到适宜的固相分数时,将坩埚中 的浆料送入压铸机的压射室进行流变 压铸成形。
➢ 流变压铸条件为:压射冲头速度为 0.91~2.13m/s,压射压力为 47.6~158.6MPa,压铸型温度为 204oC,半固态A380铝含金浆料的 温度为564~572oC。
❖ 随后,螺旋杆再次旋转搅拌合 金熔体,准备下一次射铸。
❖ 在流变射铸中,对整个设备的 温度控制要求很严格,为此设 备分成五段,在第五段中设置 了加热和监控热电偶,在第一 和第二段中设置了加热和冷却 通道及监控热电偶,在第三段 设置了加热器;
❖ 通过调整冷却通道中压缩空气的流 量来调整第一和第二段的冷却强度, 调整各段的电阻加热功率,使各处 的温度都处在预定的温度范围内, 最终射铸的半固态台金浆料控温精 度可以达到±0.5℃。
在装置下方安置一个收集器, 可以利用感应加热器进行预热 和保温;收集器内再放置一个 收集坩埚,当半固态浆料达到 预定数量时,将收集坩埚和半 固态浆料一起放在压射室中的 压射活塞上压射成形。
❖ 经过51次的压铸实验, 结果表明,半固态905铜 合金可以实现流变压铸, 压铸件的表面质量良好, 压铸件内部的初生相分布 均匀,压铸件的致密度随 半固态浆料固相分数的提 高而提高;
➢ 在上述压铸条件下,流变压铸出较为 致密的压铸件,其致密度与液态 A380铝合金的压铸件相当。
➢ 流变压铸件为一种盖类零件,如图5-1所示。
➢ 其流变压铸件的显微组织如图5-2所示,初生α-Al比液态 压铸件中的初生α-Al粗大,但其分布很均匀。
连续机械搅拌法制备905铜合金的半固态浆料
在该制备装置中,搅拌棒用石 墨制造,搅拌室用陶瓷制造;
轻合金半固态成形技术
半固态成形工艺
半固态 成形工艺
流变成形
传统机械搅拌式 单螺旋流变射铸 双螺旋流变射铸 低过热度倾斜板浇
注式
..…
触变成形
坯料重熔加热 触变压铸 触变锻造 触变射铸 …..
第四章 半固态流变成形技术
❖ 流变成形是最早进行研究的半固态金属成形工艺, 它将制备出的半固态金属浆料直接成形的工艺。
然后,在133MPa的压射力下,将半固态铝合金浆料直接压入铸型 型腔,流变压铸后的压铸件显微组织如图5-6所示,与液态铝合金 挤压件的组织截然不同,经过电磁搅拌后的初生α-Al为球状。
Hitachi金属公司对直接在压射室中制备半固态铝 合金浆料的技术作了改进:
❖ 用电磁泵和热管将熔化炉中的铝合金液直接送入压 铸机的压射室,避免与空气接触,再通过氩气保护, 进一步减少浆料中的氧化夹杂物;
不理想,可能影响成形件的力学性能; 以上技术上的不足仍然需要继续完善。
4.3 单螺旋流变射铸
❖ 触变射铸技术已经获得实际商业应用,生产近终形的镁 合金铸件,致密度比普通压铸件高,生产安全可靠、环 境污染小,因此,触变射铸技术具有较强的竞争力;但 触变射铸需要使用固态镁合金屑,制造较麻烦、成本较 高;触变射铸件的气孔率仍然较高,可达1%~17%左 右;设备投资及维护成本较高;与普通压铸相比,触变 射铸的生产周期较长。
❖ 在流变射铸中,液态合金从浇注漏 斗流人搅拌桶时几乎不会卷入气体, 合金又是在密封的通道中被搅拌剪 切,任何气体及惰性气体都不可能 进入合金熔体中,因此,流变射铸 中的半固态合金浆料的气体含量比 触变射铸中的含量低。