延迟焦化分馏系统结构特点和操作方法
延迟焦化装置吸收稳定系统工艺与操作资料

第二章:吸收稳定系统工艺流程
2.2吸收稳定系统的任务是处理来自分馏塔 顶油气分离器的粗汽油和来自压缩机的富 气,分离出干气(C2及C2以下),得到稳 定汽油和液化气。稳定汽油和液化气产率 的高低,主要取决于焦化反应系统的工艺 过程,但吸收稳定系统的回收程度与操作 水平也对收率有很大的影响。目的是要求 吸收后的干气中尽量少含C3,同时要求 解吸后的脱乙烷汽油中尽可能不含C2。
制偏低,再吸收效果不好,成干气不干,压力控制偏 高,造成吸收系统压力上升,气压机出口压力上升, 装置能耗上升。
控制目标:再吸收塔顶压力:≯1.3 MPa 控制范围:再吸收塔压力:1.10-1.20MPa 相关参数:压缩机出口压力、压缩机出口流量、干气
背压、再吸收剂温度
控制方式:通过压力控制阀PC6604来控制再吸收 塔顶部压力
置
控制方式: 正常生产时,稳定汽油的初馏 点是由塔底温度来控制的
第三章:质量控制及操作
正常调整:
影响因素 稳定塔底温度 稳定塔顶压力
进料位置
异常处理:
调整方法
塔底温度升高,初馏点降升高,反之初馏点降低 稳定塔顶压力升高,初馏点降低,反之初馏点升 高 进料位置往上,初馏点升高,反之初馏点降低
现象 稳定汽油初馏点偏低
第二章:吸收稳定系统工艺流程
改造过
第二章:吸收稳定系统工艺流程
改造过
改造过
第三章:质量控制及操作
3.1稳定汽油初馏点控制 稳定汽油初馏点是稳定汽油的主要指标,它
的指标大小关系到稳定汽油在加工、储存、 运输和使用中的安全。
控制目标: 以工艺卡片为准 相关参数: 塔底温度、塔顶压力、进料位
第三章:质量控制及操作
正常调整:
影响因素
延迟焦化装置吸收稳定系统工艺与操作要点ppt
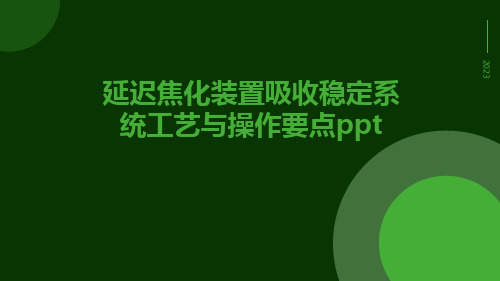
1 2
原料切割
将重油切割成小段,降低加热炉内的结焦倾向 。
加热和脱水
将原料加热到一定温度,并去除其中的水分和 轻质组分。
脱盐和脱硫
3
去除原料中的盐类和硫化物,防止腐蚀设备。
延迟焦化反应过程
加热炉加热
将原料加热到焦化反应所需温度。
焦化反应
原料在加热炉中发生裂解反应,生成气体、汽油 、柴油和重焦炭等产品。
对原料油的API、残碳、硫含量等性质进行严格把控,保 证进料质量。
原料加热
将原料加热到适当的温度,以便在焦化反应中达到最佳 效果。
进料方式选择
可选择连续进料或间歇进料方式,根据实际情况进行选 择。
反应条件优化
反应温度
01
通过控制加热炉出口温度,保证焦化反应在适宜的温度范围内
进行。
反应压力
02
通过控制分馏塔顶部压力,保证焦化反应在适宜的压力范围内
应用案例二:延迟焦化装置优化操作
优化背景
延迟焦化装置操作复杂,影响因素多,需要进行优化以提高装置的经济效益和环保性能。
优化内容
采用先进的在线监测和分析技术,对加热炉出口温度、压力,进料速度等关键参数进行实 时监测和调控。
优化效果
优化后装置运行更加稳定,产品质量和收率得到提高,同时降低了能耗和污染物排放。
2023
延迟焦化装置吸收稳定系 统工艺与操作要点ppt
目录
• 引言 • 延迟焦化装置工艺流程 • 操作要点 • 安全与环保 • 应用案例与效果展示
01
引言
目的和背景
介绍延迟焦化装置 吸收稳定系统的工 艺与操作要点
帮助企业优化生产 过程和提高经济效 益
为相关领域技术人 员提供操作指南
延迟焦化介绍 (2)

延迟焦化原则流程
焦碳塔
加热炉
原料
气体
汽油
柴油 轻蜡油 蜡油
延迟焦化物料分布情况
原料:减压渣油
产品: 干气
液化气 汽油 柴油 蜡油 甩油 焦碳
流量(t/h) 150
10.5~13.5 3~3.75 19.5~27 37.5~48 15~22.5 1.5~4.5
37.5~49.5
收率பைடு நூலகம் 100
7~9 2~2.5 13~18 25~32 10~15
采用高效的梯型浮阀塔板,提高分馏的操作弹性,更适 合优化分馏塔的操作工况。设柴油、中段油、蜡油和原 料渣油的换热器,尽可能的利用分馏塔的过剩热来加热 原料,提高热利用率。同时由于原料和中段油、蜡油、 柴油均有换热,便于分馏塔取热比例的调整和换热后渣 油温度的控制。在工艺流程设计中,采用分馏塔内直接 换热和馏分油外循环的技术调节循环比。
茂名延迟焦化工艺技术特点
采用一炉二塔的工艺路线。加热炉采用国内先进的双辐 射室多火嘴卧管立式炉,并采用双面辐射、多点注汽、 双向烧焦及在线清焦等技术。加热炉的热效率可达91%。 加热炉火嘴采用扁平焰低NOX火嘴,以减少对环境的污 染。焦炭塔实现大型化,采用的直径达Φ8600。
分馏塔底部分换热循环,并加强过滤除去焦粉,缓和炉 管结焦及塔底油温度稳定。
低温热利用没有,影响能耗降低。
操作影响因素
延迟焦化主要影响因素有三个,影响到 焦化产品分布和质量,也就是加热炉出 口温度、焦化塔顶压力、循环比。
温度
在一定的温度和循环比下,石油焦的收 率随反应温度升高而降低。 部分较重烃 类分子在低温下会留在焦化塔内转化为 石油焦,当温度升高时会变为油气由塔 顶逸出。 事实上,温度可调范围很小。 延迟焦化是一个绝热反应,炉出口温度 是焦化反应温度的控制点。
延迟焦化装置介绍

延迟焦化装置介绍延迟焦化装置是一种炼油装置,用于将重质石油馏分转化为高值的石油产品。
它采用了一种延长焦化时间的方法,使得重质馏分得以更充分地转化为产品。
本文将介绍延迟焦化装置的工作原理、主要组成部分和应用领域等方面的内容。
延迟焦化装置的工作原理是通过将重质石油馏分注入到高温高压的裂解器中,然后在裂解器内加热,在高温下引发热裂解反应。
在裂解过程中,重质分子会断裂成较轻的分子,并进一步转化为石油产品。
与传统焦化装置不同的是,延迟焦化装置通过控制温度、压力和停留时间等参数,使得裂解反应更为充分和均匀。
延迟焦化装置的主要组成部分包括裂解器、加热炉、分离器和收敛装置等。
裂解器通常采用高合金钢材质,可以承受高温高压的工作环境。
加热炉则负责提供高温热能,通常使用天然气或石油等燃料进行加热。
分离器用于将裂解反应产物进行分离和提纯,常见的分离方法包括闪蒸、冷凝和吸收等。
收敛装置用于将焦油进行收集和储存,焦油通常作为能源或原料进行继续加工利用。
延迟焦化装置具有广泛的应用领域。
首先,它可以用于生产高值的石油产品,如汽油、柴油和航空燃料等。
由于延迟焦化装置能够将重质馏分充分转化为产品,因此可以提高产品产率和收益。
其次,延迟焦化装置可以提高炼油厂的能源效率。
由于裂解反应需要高温环境,因此加热炉所产生的余热可以被利用,用于发电或供热等用途。
此外,延迟焦化装置还可以用于处理低质量的石油原料,如重油、渣油和焦炭等,将其转化为高值的产品。
在实际应用中,延迟焦化装置不仅可以用于新建炼油厂,还可以用于现有炼油厂的改造和升级。
通过引入延迟焦化装置,可以提高炼油厂的生产能力和产品质量,并降低环境污染。
此外,延迟焦化装置还可以帮助炼油厂应对能源和环境的挑战,提高能源效率和减少碳排放。
综上所述,延迟焦化装置是一种用于石油炼制的重要设备,通过延长焦化时间,使得重质馏分能够更充分地转化为产品。
它具有高效、节能、环保等优点,在炼油行业中有着广泛的应用。
分析延迟焦化装置工艺技术特点及其应用

分析延迟焦化装置工艺技术特点及其应用延迟焦化装置是一种用于加热原油并使其转化为高质量焦炭的设备。
它在石油炼制工业中被广泛应用。
延迟焦化装置具有以下几个工艺技术特点:1. 高温高压气体化反应:延迟焦化装置在高温高压条件下将原油进行气化反应,使之分解为沥青和气体。
这种气化反应需要在800℃至900℃的高温环境下进行,压力可以达到30至35大气压。
这种高温高压气体化反应可以有效地提高反应速率和产率。
2. 碳聚合反应:在延迟焦化装置中,高温高压的油气混合物会通过炉管进入反应器。
在反应器内,油气混合物经过碳聚合反应,形成固态的焦炭。
这种碳聚合反应需要高温和适当的反应时间。
延迟焦化装置通过优化反应条件,可以获得高质量的焦炭。
3. 热解副产品收集:在延迟焦化装置中,热解原油生成的气体中含有大量的轻质烃类化合物,如乙烯、丙烯等。
这些轻质烃类化合物是非常有价值的石化原料。
在延迟焦化装置中,需要设置相应的收集设备,将这些热解副产品进行收集和分离,以便后续利用。
延迟焦化装置的应用主要体现在以下几个方面:1. 焦炭生产:延迟焦化装置是生产高质量焦炭的主要设备之一。
焦炭是石油炼制过程中的重要副产品,广泛应用于冶金、化工等行业。
延迟焦化装置可以通过调控反应条件,生产出质量稳定的焦炭产品。
3. 能源回收:延迟焦化装置在热解原油的过程中会产生大量的余热。
这些余热可以通过余热回收装置进行回收利用,用于发电或供热。
延迟焦化装置的能源回收技术可以有效提高能源利用效率,减少能源消耗。
延迟焦化装置具有高温高压气体化反应、碳聚合反应和热解副产品收集等工艺技术特点。
它主要应用于焦炭生产、轻烃回收和能源回收等领域,对于提高资源利用效率和能源利用效率具有重要作用。
分析延迟焦化装置工艺技术特点及其应用
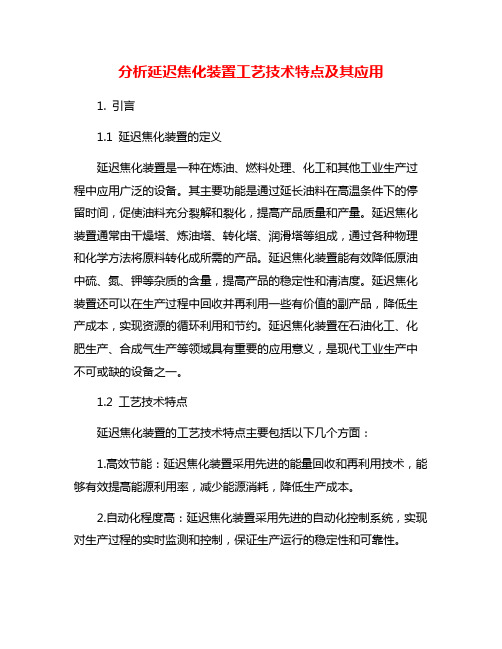
分析延迟焦化装置工艺技术特点及其应用1. 引言1.1 延迟焦化装置的定义延迟焦化装置是一种在炼油、燃料处理、化工和其他工业生产过程中应用广泛的设备。
其主要功能是通过延长油料在高温条件下的停留时间,促使油料充分裂解和裂化,提高产品质量和产量。
延迟焦化装置通常由干燥塔、炼油塔、转化塔、润滑塔等组成,通过各种物理和化学方法将原料转化成所需的产品。
延迟焦化装置能有效降低原油中硫、氮、钾等杂质的含量,提高产品的稳定性和清洁度。
延迟焦化装置还可以在生产过程中回收并再利用一些有价值的副产品,降低生产成本,实现资源的循环利用和节约。
延迟焦化装置在石油化工、化肥生产、合成气生产等领域具有重要的应用意义,是现代工业生产中不可或缺的设备之一。
1.2 工艺技术特点延迟焦化装置的工艺技术特点主要包括以下几个方面:1.高效节能:延迟焦化装置采用先进的能量回收和再利用技术,能够有效提高能源利用率,减少能源消耗,降低生产成本。
2.自动化程度高:延迟焦化装置采用先进的自动化控制系统,实现对生产过程的实时监测和控制,保证生产运行的稳定性和可靠性。
3.适应性强:延迟焦化装置具有较强的适应性,可以根据不同原料的特性和生产需求进行灵活调整,保证生产过程的稳定性和高效性。
4.产品质量高:延迟焦化装置在生产过程中采用先进的分离和净化技术,能够有效提高产品的纯度和质量,满足不同行业的需求。
5.环保性好:延迟焦化装置在设计和运行过程中注重环保要求,采用先进的污染治理技术,减少排放物对环境的影响,符合现代工业发展的可持续发展理念。
延迟焦化装置的工艺技术特点体现了其在煤化工和石油化工等领域的重要性和广泛应用前景。
通过不断优化和改进,延迟焦化装置的工艺技术将有望进一步提升生产效率和产品质量,推动相关产业的发展和升级。
1.3 应用领域延迟焦化装置是一种在煤化工和石油化工行业中被广泛应用的重要设备。
其主要应用领域包括煤焦油、石油焦油、裂解油、石脑油等石油化工产品的生产过程中。
分析延迟焦化装置工艺技术特点及其应用

分析延迟焦化装置工艺技术特点及其应用
延迟焦化是一种石化工艺,它将重油迅速加热至高的温度和压力下进行裂解,生成烯
烃和芳香烃。
它的工艺技术特点主要体现在以下几个方面:
1. 裂解时延迟:延迟焦化采用了反应器之外的加热装置,将液态重油迅速加热至高
温度,并在反应器中加入催化剂,让重油进行裂解。
这种工艺使得反应时间延迟,可以增
加裂解产物的芳香烃和烯烃含量。
2. 高温高压:延迟焦化反应器内部的温度和压力非常高,通常需要在1000℃以上和1.5 MPa以上的条件下操作。
高温高压环境才能促进重油的裂解,同时也会增加反应物中
间体的生成和分解,从而增加了反应物转化率。
3. 重油先热解再裂解:在延迟焦化中,重油首先经过热解阶段,使得重油中的大分
子化合物转化为小分子烃,主要为液化气,成分为丁烷、丙烷和乙烷等。
热解反应所生成
的烃类会随后进入裂解阶段,利用催化剂进一步裂解为烯烃和芳香烃。
4. 高效催化剂:延迟焦化需要使用高效催化剂,以提高重油的裂解效率和选择性。
目前常用的催化剂有氢氧化镁、氢氧化钠和氢氧化钾等。
延迟焦化可以处理各种成分的重油,包括低成分的重油、深层储层的油田油和油砂等。
它能够生产高品质的清洁燃料,如芳香烃和烯烃,被广泛应用于石化工业领域中。
同时,
使用延迟焦化可以降低重油的处理成本,提高原油利用率和产品质量,具有很高的经济效
益和社会效益。
分析延迟焦化装置工艺技术特点及其应用
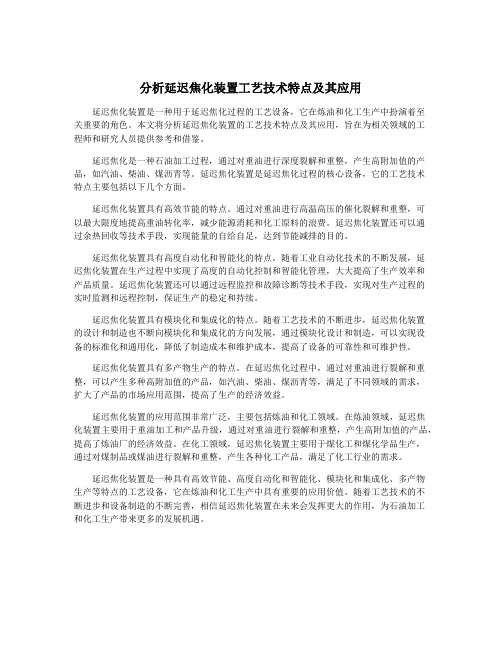
分析延迟焦化装置工艺技术特点及其应用延迟焦化装置是一种用于延迟焦化过程的工艺设备,它在炼油和化工生产中扮演着至关重要的角色。
本文将分析延迟焦化装置的工艺技术特点及其应用,旨在为相关领域的工程师和研究人员提供参考和借鉴。
延迟焦化是一种石油加工过程,通过对重油进行深度裂解和重整,产生高附加值的产品,如汽油、柴油、煤沥青等。
延迟焦化装置是延迟焦化过程的核心设备,它的工艺技术特点主要包括以下几个方面。
延迟焦化装置具有高效节能的特点。
通过对重油进行高温高压的催化裂解和重整,可以最大限度地提高重油转化率,减少能源消耗和化工原料的浪费。
延迟焦化装置还可以通过余热回收等技术手段,实现能量的自给自足,达到节能减排的目的。
延迟焦化装置具有高度自动化和智能化的特点。
随着工业自动化技术的不断发展,延迟焦化装置在生产过程中实现了高度的自动化控制和智能化管理,大大提高了生产效率和产品质量。
延迟焦化装置还可以通过远程监控和故障诊断等技术手段,实现对生产过程的实时监测和远程控制,保证生产的稳定和持续。
延迟焦化装置具有模块化和集成化的特点。
随着工艺技术的不断进步,延迟焦化装置的设计和制造也不断向模块化和集成化的方向发展,通过模块化设计和制造,可以实现设备的标准化和通用化,降低了制造成本和维护成本,提高了设备的可靠性和可维护性。
延迟焦化装置具有多产物生产的特点。
在延迟焦化过程中,通过对重油进行裂解和重整,可以产生多种高附加值的产品,如汽油、柴油、煤沥青等,满足了不同领域的需求,扩大了产品的市场应用范围,提高了生产的经济效益。
延迟焦化装置的应用范围非常广泛,主要包括炼油和化工领域。
在炼油领域,延迟焦化装置主要用于重油加工和产品升级,通过对重油进行裂解和重整,产生高附加值的产品,提高了炼油厂的经济效益。
在化工领域,延迟焦化装置主要用于煤化工和煤化学品生产,通过对煤制品或煤油进行裂解和重整,产生各种化工产品,满足了化工行业的需求。
延迟焦化装置是一种具有高效节能、高度自动化和智能化、模块化和集成化、多产物生产等特点的工艺设备,它在炼油和化工生产中具有重要的应用价值。
- 1、下载文档前请自行甄别文档内容的完整性,平台不提供额外的编辑、内容补充、找答案等附加服务。
- 2、"仅部分预览"的文档,不可在线预览部分如存在完整性等问题,可反馈申请退款(可完整预览的文档不适用该条件!)。
- 3、如文档侵犯您的权益,请联系客服反馈,我们会尽快为您处理(人工客服工作时间:9:00-18:30)。
分馏过程的进行要有以下必备条件
1、气相温度高于液相温度 2、液相中低沸点组分的浓度应高于与油气 成平衡的浓度,气相中高沸点组分的浓度 也应高于与其液相成平衡的浓度 3、具有气液两相进行充分接触的地方。
二、分馏塔的作用
延迟焦化装置的分馏塔有三个作用
1.分馏作用
分馏塔的分馏作用是把焦炭塔顶来和甩油罐 来的高温油气中所含的汽油、柴油、蜡油及部分 循环油,按其组分的挥发度不同切割成不同沸点 范围的石油产品。
(2)ADV高效浮阀塔板(导向浮阀)
●结构形式
(a)圆盘型
(b)矩型(条型)
●主要性能优势(同标准圆盘型浮阀塔板对比)
① 处理能力大(提高30%以上);
② 操作弹性大(增加30%~50%);
③ 分离效率高(提高10%~20%);
④ 塔板压降较小(减少10%)。
2 筛孔型塔板
(1)普通筛孔型塔板
●结构形式及工作原理
③ 适应性强;
④ 操作弹性较大。
缺点:① 结构较复杂,造价高;
②塔板压降较普通筛板高。
(3)导向筛孔型塔板
●结构形式及工作原理
鼓泡促进器
导向孔
导向筛板
(a)导向筛板结构
鼓泡促进器 导向孔
(b)导向筛板工作原理
● 导向筛孔板主要优点
① 生产能力大; ② 塔板效率高; ③ 压降低; ④ 抗堵塞能力强; ⑤ 结构简单、造价低。
四、分馏塔塔盘类型和结构特点
(一)常用的塔板类型
1.浮阀塔板 2.筛孔型塔板 3.固舌塔板 4.浮舌塔板 5.网孔塔板 6.CTST(立体传质)塔板
1 浮阀塔板的种类
(1)标准圆盘型浮阀塔板
●结构形式
(a)F1型浮阀
(b)F4型浮阀
(c)浮阀阀片
(d)浮阀塔板
●工作原理
●主要优缺点 ◆优点: ① 生产能力较大; ② 操作弹性大; ③ 分离效率高; ④ 塔板压降较小。 ◆缺点: ① 阀片易脱落; ② 阀片易卡死。
(a)普通筛板结构
(b)普通筛板工作原理
●主要优缺点
优点:① 结构简单、造价低; ② 压降较小。
③ 制造、安装、检修维护简便;
缺点:① 操作弹性小;
② 泄漏较严重;
③ 塔板孔道易堵塞。
(2)垂直筛孔型塔板
●结构形式及工作原理
(a)垂直筛板结构图
(b)垂直筛板工作原理
●主要优缺点
优点:① 传质效率高; ② 加工能力大;
.特 点:
(1)塔顶产品含不凝气体较多;
(3)对塔顶馏出管线及冷凝冷却系统压降要求苛刻
(2)塔顶热负荷较大;
。
(2)中段循环回流 作用:
(1) 使塔内汽、液相负荷分布更趋均匀 (2) 充分回收利用高温位热能。 (3)控制柴油质量合格并为吸收稳定提供热源
中段循环回流数目选择的原则 (1)沿塔高汽、液相负荷分布尽量均匀; (2)尽量回收更多的高温位热能; (3)经济合理(设备投资、操作费用)。
2.换热作用
煤焦油在分馏塔底与柴油换热后,温度可达 到260度,这样可提高全装置的热利用率和减轻 加热炉的热负荷。
3 . 洗涤作用
高温油气中含有一定量的粉尘,通过洗地板可 将其沉降。
三、回流的形式
分馏塔回流的形式主要有:冷回流、循 环回流和塔内回流三种。
1. 塔顶冷回流 塔顶冷回流是塔顶气相流出物以过冷 液体状态从塔顶打入塔内。冷回流入塔后, 吸热升温、汽化、再从塔顶蒸出。它是控 制塔顶温度、保证产品质量合格的重要手 段。
延迟焦化分馏系统结构特 点和操作方法
一、分馏原理 二、分馏塔的作用 三、分馏塔回流的形式及特点 四、分馏塔不同塔盘结构特点 五、塔板上的不正常操作状态 六、换热器
一、分馏原理
分馏是工业生产中常用分离混合物的 方法之一。分馏的依据是混合物中各组分 具有不同的沸点、挥发度,将混合物各组 分利用分馏塔分离出来。其实质是不平衡 的气、液两相在塔内经过多次逆向接触进 行热交换,液相中的轻组分多次部分汽化 和气相中的重组分多次部分冷凝相结合的 过程,从而使轻组分浓度和重组分浓度都 不断提高,最终达到使混合物得到分离的 目的。
2、循环回流
循环回流是从塔内抽出经冷却至某个温度后再返回塔 中,物流在整个过程中都是处于液相,而且在塔内流动时 一般不发生相变化,它只是在塔内塔外循环流动,借助于 换热设备取走回流热。
循环回流包括:塔顶循环回流、中段循环回流和塔底 循环回流。
(1)塔顶循环回流:它的主要作用是塔顶回流热较 大,考虑回收这部分热量以降低装置的能耗。采用塔顶循 环回流大大减少塔顶冷凝冷却器的负荷,降低流动压降, 保证塔顶压力不至于超高。
4 浮舌塔板
●结构形式
阀片最大张角20° 最小张角 5°
阀片展开图
●优缺点 优点: (1)操作弹性大,塔板效率高; (2)处理能力大,塔板压降低。 缺点: 阀片易脱落、损坏。
5 网孔塔板
●结构形式及工作原理
挡沫板
网孔塔板结构简图
网孔塔板工作原理图
●网孔型塔板的优缺点 优点: (1)生产能力大,压降小; (2) 传质效率高,雾沫夹带量小; (3)不易结焦、堵塞。 缺点: (1)塔板易变形; (2)不适合小直径的塔; (3)开孔率增大时,操作弹性会显著下降。
中段循环回流进、出口位置
(3)塔底循环回流 作用:
塔底循环回流的作用主要有三个:一是取走大量 高温位的热能回收利用;二是脱除反应油气带来的多余热 量,降低分馏塔上部负荷;三是洗涤反应油气中的催化剂 颗粒,避免堵塞上部塔盘
2.流 程 3.特 点 (1)塔底部热负荷较大; (2)塔底温度较高; (3)塔底气相进料中含有固体颗粒。
3 固舌塔板
●结构形式
20°
25mm
R25mm
标准固舌结构简图
标准固舌塔板实物图 标准固舌塔板放大图
●固塔板工作原理
固舌塔板工作原理图
●固舌型塔板的优缺点 优点 :
(1)生产能力大,板压降较小; (2)不易结焦,不易堵塞; (3)结构简单,造价低; (4)制造、安装及维修方便。
缺点 :
(1)操作弹性小; (2)低气速下操作时,泄漏量较大; (3)不适用于塔径较小的塔; (4)塔板传质效率较低。
6 立体传质(CTST)塔板
●结构形式及工作原理
梯形喷射罩
分离板
CTST塔板结构简图
CTST塔板工作原理图
CTST塔板实物图片
●立体传质塔板主要优点 (1)气、液两相通过能力大; (2)塔板传质效率高; (3)塔板压降低,操作弹性大; (4)能处理特殊物质; (5)设备投资较小,改造方便,施工