延迟焦化之分馏系统.
延迟焦化工艺详解及其安全注意事项
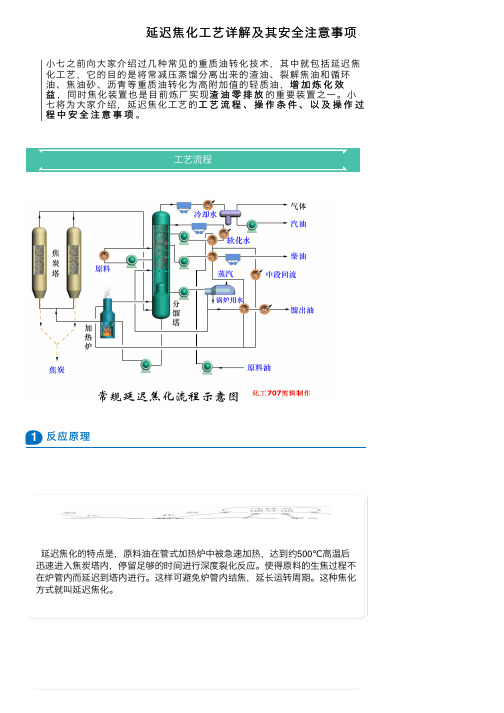
1延迟焦化⼯艺详解及其安全注意事项⼩七之前向⼤家介绍过⼏种常见的重质油转化技术,其中就包括延迟焦化⼯艺,它的⽬的是将常减压蒸馏分离出来的渣油、裂解焦油和循环油、焦油砂、沥青等重质油转化为⾼附加值的轻质油,增增加炼化效益,同时焦化装置也是⽬前炼⼚实现渣渣油零排放的重要装置之⼀。
⼩七将为⼤家介绍,延迟焦化⼯艺的⼯⼯艺流程、操作条件、以及操作过程中安全注意事项。
⼯艺流程反应原理延迟焦化的特点是,原料油在管式加热炉中被急速加热,达到约500℃⾼温后迅速进⼊焦炭塔内,停留⾜够的时间进⾏深度裂化反应。
使得原料的⽣焦过程不在炉管内⽽延迟到塔内进⾏。
这样可避免炉管内结焦,延长运转周期。
这种焦化⽅式就叫延迟焦化。
延迟焦化装置的⽣产⼯艺分焦化和除焦两部分,焦化为连续操作,除焦为间歇操作。
2由于⼯业装置⼀般设有两个或四个焦炭塔,所以整个⽣产过程仍为连续操作。
⼯艺描述原料经加热炉对流室预热管预热⾄350℃进⼊焦化分馏塔下部与来⾃焦炭塔顶的⾼温油⽓换热,可同时将轻质油蒸出。
换热后原料油温度约390~395℃,再与循环油⼀起泵⼊加热炉炉管,迅速加热到500℃再进⼊焦炭塔底。
为了防⽌炉管结焦,需向炉管内注⽔以加⼤流速。
渣油在焦炭塔内停留⾜够长时间以完成裂化、缩合反应,⽣成的焦炭留在焦炭塔内。
⾼温油⽓从塔顶通⼊分馏塔下部;经换热后分馏得到产品⽓、汽油、柴油等。
焦炭塔轮流使⽤。
操作条件影响焦化的主要因素有:原料性质、加热炉出⼝温度、反应压⼒。
加热炉出⼝温度:500℃左右;加热炉出⼝温度的变化直接影响到炉管内和焦炭塔内的反应深度,加热炉出⼝温度太⾼,反应速度和反应深度增⼤,⽓体、汽油和柴油的产率增⼤,蜡油的产率减⼩,焦炭产率也会由于所含挥发性组分的减⼩⽽降低 ,同时由于温度太⾼,会造成汽油、柴油继续裂解,结焦增多。
加热炉出⼝温度太低,则会造成反应不完全。
分馏塔底温度:375 ~395℃,过⾼易结焦。
分馏塔顶温度:100 ~110℃柴油输出线温度:275 ~285℃系统压⼒直接影响到焦炭塔的操作压⼒,⼀般来说,压⼒降低会使蜡油产率增⼤⽽使柴油产率降低。
延迟焦化
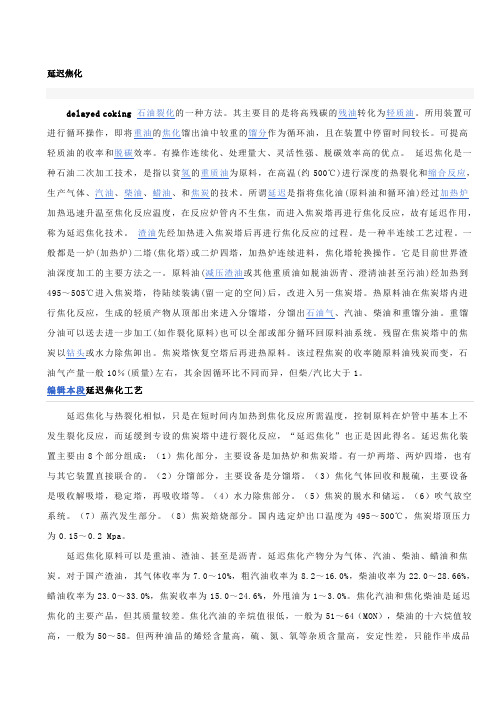
延迟焦化delayed coking石油裂化的一种方法。
其主要目的是将高残碳的残油转化为轻质油。
所用装置可进行循环操作,即将重油的焦化馏出油中较重的馏分作为循环油,且在装置中停留时间较长。
可提高轻质油的收率和脱碳效率。
有操作连续化、处理量大、灵活性强、脱碳效率高的优点。
延迟焦化是一种石油二次加工技术,是指以贫氢的重质油为原料,在高温(约500℃)进行深度的热裂化和缩合反应,生产气体、汽油、柴油、蜡油、和焦炭的技术。
所谓延迟是指将焦化油(原料油和循环油)经过加热炉加热迅速升温至焦化反应温度,在反应炉管内不生焦,而进入焦炭塔再进行焦化反应,故有延迟作用,称为延迟焦化技术。
渣油先经加热进入焦炭塔后再进行焦化反应的过程。
是一种半连续工艺过程。
一般都是一炉(加热炉)二塔(焦化塔)或二炉四塔,加热炉连续进料,焦化塔轮换操作。
它是目前世界渣油深度加工的主要方法之一。
原料油(减压渣油或其他重质油如脱油沥青、澄清油甚至污油)经加热到495~505℃进入焦炭塔,待陆续装满(留一定的空间)后,改进入另一焦炭塔。
热原料油在焦炭塔内进行焦化反应,生成的轻质产物从顶部出来进入分馏塔,分馏出石油气、汽油、柴油和重馏分油。
重馏分油可以送去进一步加工(如作裂化原料)也可以全部或部分循环回原料油系统。
残留在焦炭塔中的焦炭以钻头或水力除焦卸出。
焦炭塔恢复空塔后再进热原料。
该过程焦炭的收率随原料油残炭而变,石油气产量一般10%(质量)左右,其余因循环比不同而异,但柴/汽比大于1。
编辑本段延迟焦化工艺延迟焦化与热裂化相似,只是在短时间内加热到焦化反应所需温度,控制原料在炉管中基本上不发生裂化反应,而延缓到专设的焦炭塔中进行裂化反应,“延迟焦化”也正是因此得名。
延迟焦化装置主要由8个部分组成:(1)焦化部分,主要设备是加热炉和焦炭塔。
有一炉两塔、两炉四塔,也有与其它装置直接联合的。
(2)分馏部分,主要设备是分馏塔。
(3)焦化气体回收和脱硫,主要设备是吸收解吸塔,稳定塔,再吸收塔等。
延迟焦化装置换热分馏流程方案分析

摘要 : 以国内两套典型的分别为可调循环 比和传统工 艺流程 的延 迟焦化装 置作为研 究背景 , 借助三 环节能量
系统综合优化方法 , 根据延迟焦化两种工艺流程各 自的特点 , 分别对 加热炉对 流段和辐射 段热负荷分 配、 分馏塔操
见 ) 分馏塔 实际塔板数 迟焦化装置 作为研究背景 , 助过程系统能量综 采用一炉两塔流程( 图 2 , 借 合优化“ 三环节” 策略方法 , 】对装置 的加热炉能 为 3 块 , 8 循环 比为 0 2 。对两种流程所进行 的对 .5
量利用、 分馏塔操作、 换热流程 、 装置 白产蒸 汽量 比分析计算均采用装置设计数据。 等方面进行对 比分析。
作、 换热流程 、 装置 自 产蒸汽量等进行分析 比较 , 探讨不 同工艺流程 对装置 整体用能 的影 响 。分 析结果表 明 。 工艺
流程 的不 同及原料渣油换热流程 的差别对于装置稳定操 作 、 加热 炉用能 、 分馏 塔取热 、 热流程 安排 、 换 自产 燕汽 的 温度和压力等有着不同程度的影响。相关焦化流程的对 比分析对焦 化装置 的流程选择及设 计优 化有着 十分重 要
2 用能 比较
2 1 加热 炉 .
传统流程和可调循环 比流程 由于原料油进加 热炉的方式不同 , 而使 加热炉的对流段和辐射段 的负荷分配以及加热炉单位能耗出现差异。两流 程 的加热炉能量对 比见表 1 。传统 流程 中, 流 对 段 的热负荷主要用来预热原料油 、 过热蒸汽等 。 20 的原 料油在加 热炉对 流段 中加 热到 30 3 4 ℃ , 加热炉总热负荷 的 3 . 1 。而对流段是 占 58% 加热炉的低温区, 能量利用集 中在低温位 , 使加热 炉能量利用效率降低 , 单位能耗 比可调循环 比流
延迟焦化装置仿真实训系统操作说明书.

一、工艺流程1. 1装置概况该装置采用一台加热炉、两台焦炭塔的工艺路线及可灵活调节循环比的工艺流程,装置设计循环比为0. 5, 以减压渣油、催化油浆、乙烯焦油为原料,主要产品为干气、液化石油气、汽油、柴油、轻蜡油、重蜡油和石油焦。
焦化干气经脱硫后作为燃料气出装置,汽油、柴油、蜡油送出装置至后续装置加工处理;焦炭和液化石油气作为产品出厂销售。
1. 2工艺原理1. 2. 1生产方法延迟焦化工艺是焦炭化过程(简称焦化)主要的工业化形式,由于延迟焦化工艺技术简单,投资及操作费用较低,经济效益较好,因此,世界上85%以上的焦化处理装置都采用延迟焦化工艺。
也有部分国外炼油厂(如美国)采用流化焦化工艺,这种工艺使焦化过程连续化,解决了除焦问题,而且焦炭产率降低,液体产率提高;另外,由于该工艺加热炉只起到预热原料的作用,炉出口温度较低,从而避免了加热炉管结焦的问题,所以该工艺在原料的选择范围上比延迟焦化有更大的灵活性,但是该工艺由于技术复杂,投资和操作费用较高,且焦炭只能作为一般燃料利用,故流化焦化技术没有得到太广泛的应用。
近年来还有一种焦化工艺叫灵活焦化,这种工艺不生产石油焦,但是除了生产焦化气体、液体外,还副产难处理的空气煤气,加之其技术复杂、投资费用高,该工艺也未被广泛采用。
而其它比较早的焦化工艺(如釜式焦化等)基本被淘汰。
延迟焦化工艺基本原理就是以渣油为原料,经加热炉加热到高温(500℃左右),迅速转移到焦炭塔中进行深度热裂化反应,即把焦化反应延迟到焦炭塔中进行,减轻炉管结焦程度,延长装置运行周期。
焦化过程产生的油气从焦炭塔顶部出来到分馏塔中进行分馏,可获得焦化干气、汽油、柴油、蜡油产品;留在焦炭塔中的焦炭经除焦系统处理,可获得焦炭产品(也称石油焦)。
焦化过程是一种渣油轻质化过程。
作为轻质化过程,焦化过程的主要优点是它可以加工残碳值及重金属含量很高的各种劣质渣油,而且过程比较简单,投资和操作费用较低。
它的主要缺点是焦炭产率高及液体产物的质量差。
延迟焦化吸收稳定系统工艺与操作优化

延迟焦化吸收稳定系统工艺与操作优化摘要:延迟焦化吸收稳定系统主要任务是从焦化富气中分离出合格的液态烃和干气,生产合格稳定汽油。
吸收稳定系统各操作参数之间关联性较强,在生产优化过程中要综合考虑各方面的相互影响。
通过对吸收稳定系统各操作参数的优化调整,在不增加设备投资的情况下将干气中C3以上组分的含量由优化前的5%以上降低到2%以下,从而提高了本装置的液化气收率,降低了吸收稳定系统能耗,达到降本增效的目的。
关键词:延迟焦化;吸收稳定;操作优化;液化气1 前言目前国内大多数炼厂的吸收稳定系统存在“干气不干”和负荷过高的问题。
“干气不干”使大量高附加值的液化气产品不能被有效回收,负荷过高导致设备超负荷运转,吸收分离效果较差,这些问题不仅大大降低了装置的经济效益,尤其对装置的长周期运行极为不利。
因此,研究吸收稳定系统的工艺操作与优化对提高整个装置的经济效益与确保装置长满优运行极其重要。
2 吸收稳定系统工艺流程吸收稳定系统是焦化装置的后续处理单元,任务是通过粗汽油回收焦化富气中的轻烃,生产出合格的稳定汽油、液化气和干气[1]。
中沥公司吸收稳定采用传统四塔流程,即吸收-再吸收-解吸-稳定,以分馏粗汽油作为吸收剂,稳定汽油作补充吸收剂,焦化柴油作再吸收剂,示意图见图2-1。
图2-1 吸收稳定系统示意图3吸收稳定系统操作优化中沥公司延迟焦化装置自2016年5月份投产以来,吸收稳定系统一直存在“干气不干”和负荷过高的问题,通过一年的不断摸索优化操作,结合自身装置特点大胆突破设计操作条件要求,作出了如下调整。
3.1吸收塔操作优化压力愈高对吸收越有利,当压力达到一定时,压力对提高吸收率的影响不再明显,另一方面压缩机所需的动能及设备投资解吸难度都会增加。
因此,综合考虑压缩机出口压力以及对解吸气总量的分析,最终确定吸收塔压力在1.15MPa.由于吸收过程是放热过程,一定压力下,吸收塔的操作温度越低,吸收效果越好[2]。
因此,要尽量降低吸收剂粗汽油与稳定汽油的温度以及富气冷却后温度,受到循环水温度的制约,粗汽油温度尽量在空冷后降到较低的温度,进吸收塔时温度一般在35℃左右。
焦化分馏塔底抽出线结焦分析及减缓措施

焦化分馏塔底抽出线结焦分析及减缓措施摘要:延迟焦化分馏塔底抽出线结焦是焦化装置普遍存在的一个问题,通过综合当前国内延迟焦化方面的工艺进展及对焦化装置分馏塔底抽出线结焦情况分析,得到影响分馏塔底抽出线结焦的主要因素有辐射注汽量、冷焦吹汽量、消泡剂的作用、焦炭塔平稳操作以及分馏塔底温度等,同时提出了减缓结焦的措施。
关键词:延迟焦化结焦分馏塔底抽出线兰州石化公司炼油厂1.2Mt/a延迟焦化装置,于2005年6月实现投料试车一次成功。
生产过程中发现分馏塔底抽出线结焦严重,在每一个生产周期后期很难建立塔底循环,导致分馏塔底开始结焦,给正常生产带来严重影响。
1、分馏塔底抽出线结焦影响因素分析1.1 辐射注汽量的影响注汽量的大小与原料性质、循环比和处理量等有关,对于新装置,为避免炉管结焦,注汽量较大,但这样加速了油气携带焦粉,增加了焦粉进入分馏塔趋势;另外,为保持辐射炉管内一定的介质流速,当处理量大时就可适当减少注汽量,当处理量小时可适当增大注汽量。
1.2 冷焦小吹汽量的影响焦炭塔在切塔后老塔进行冷焦处理时,由于生焦上部有一定高度的泡沫层和软焦层,如果冷焦时小吹汽量过大,就会有部分泡沫层通过大油气线进入分馏塔底部,加之这时急冷油又切换去了生产塔,不能有效地抑制焦粉和泡沫层进入大油气线和分馏塔。
因此冷焦时吹汽量控制要合理,尤其是高负荷生产和焦炭塔的生焦高度比较高时,应尽量减小小吹汽时蒸汽在塔内的线速。
1.3消泡剂的作用为了降低焦炭塔内泡沫层的高度,防止焦粉通过大油气线携带进入分馏塔底部引起分馏塔底抽出线结焦,一般都要在焦炭塔顶注入消泡剂。
但对消泡剂的加入比例还需要作进一步探索,以节约成本,增加效益。
1.4 焦炭塔平稳操作焦炭塔平稳操作至关重要。
切塔过程中,要通过压缩机控制好系统压力,如果操作不当就会有大量压力损失,会加重焦炭塔内的泡沫生成,打乱分馏塔的温度和压力分布,从而发生泡沫失控导致泡沫溢出,引发焦炭塔冲塔,将大量焦粒带入分馏塔底部,堵塞分馏塔底抽出线。
炼油厂延迟焦化装置生产运行优化措施

炼油厂延迟焦化装置生产运行优化措施摘要:随着延迟焦化原料的恶化,已经切实影响延迟焦化装置长周期运行,延迟焦化装置的加热炉,焦碳塔和分馏塔的良好运行是该装置长周期安全运行的关键。
以炼油厂90万吨/年延迟焦化装置为例,分析了影响该厂长期运营的相关因素后,在装置大修期间采取了优化和改造措施,以确保能够满足装置长周期安全生产及创效。
关键词:长周期;延迟焦化;瓶颈;优化措施延迟焦化作为炼油厂重要的二次加工技术,由于原料适应性范围广,加工成本低以及成熟可靠的技术而继续被广泛使用。
其运行的平稳与否直接影响着炼油厂其它装置的正常运行,焦化装置属于炼油二次加工装置。
随着炼油企业节能减排的要求以及技术的进步,炼油厂各装置直接供料成为主流,装置间的相互影响更显突出。
随着原油资源的消耗,原油性质的劣质化趋势明显。
受此影响,焦化装置原料劣质化趋势也明显加剧,不断给装置的长周期稳定运行工作带来新的问题与挑战。
因此,及时总结经验,为装置管理提供技术支持和指导,保证延迟焦化装置全面实现无故障、长周期运行打下坚实的基础,已经成为一项非常必要的工作。
天津分公司炼油部1#延迟焦化装置最初设计原料参照辽河渣油中石化北京设计院总承包,中石化第四建设公司承建,为两炉四塔的生产模式。
装置始建于1996年,初始设计为100万吨/年,加工原料为大港原油的减压渣油。
后在2005年进行扩能改造为120万吨/年,同时进行了部分材料升级,以适应加工含硫原油的减压渣油。
2008年装置改为加工高硫原油的减压渣油,加工规模按照90万吨/年设计。
延迟焦化装置规模90万吨/年,设计生焦周期为24小时,操作弹性为60%~120%。
年开工时数8400小时。
循环比为0.3,可在0.2~0.4的范围内调节。
1#延迟焦化的主要产品是石油焦。
中间产品有干气,液态烃,汽油,柴油,蜡油。
装置生产的焦化干气,去干气脱硫单元,脱硫后作燃料气或作制氢原料。
焦化液化气脱硫后最为产品或去气分再加工成丙烯等产品。
延迟焦化主分馏塔工艺模拟与扩能分析

维普资讯
第3 4卷 第 l 2期 20 0 6年 l 2月
J r a f S uh i a U n v r i fTe h o o y ou n lo o t Ch n i e st o c n l g y
华 南 理 工 大 学 学 报 (自 然 科 学 版 ) ( a r c n eE io ) N t a S i c dt n ul e i
学核算 , 找出了装置运行存在 的瓶颈 , 提出了相应的 解决办法 , 为装置扩能及节能改造提供了依据. 同时
对装 置扩 能 2% 后 的主 分 馏 塔 进行 模 拟计 算 和水 2 力学 核算 , 发现 只需 对 原 有装 置进 行 局部 脱 瓶 颈改 造 就能满 足加 工要 求 . 主分馏 塔 的模 拟 分 析 以及 水
V1 4 o1 o 3 N .2 .
De emb r c e
文章编号 : 0055 2 0 )20 1—5 10 -6 X(0 6 1 —10 0
延迟焦化主 分馏塔工艺模拟与扩能分析 木