液压硫化机和机械式硫化机的比较
液压硫化机和机械式硫化机的比较

液压硫化机和机械式硫化机的比较液压式硫化机与机械式硫化机的比较我国的液压硫化机开发工作始于60年代未期,起步时间不比工业发达国家慢,但是当时国内的液压技术水平限制了液压硫化机的发展。
近年来,随着国内技术的发展和国外技术进入中国,我国液压硫化机的开发和应用都进入了一个高速发展期,现在已经开发出了1050~1700 规格的液压硫化机,并实现了液压硫化机向法国米其林公司的批量出口。
但是总的来说,液压硫化机目前在国内的应用还是不太广泛,那么液压式硫化机与机械式硫化机的差异主要体现在那些方面呢?结构差异由于机械式硫化机本身结构的原因,机械式硫化机存在如下问题:1、上下热板的平行度、同轴度,机械手卡爪圆度和对下热板内孔的同轴度等精度等级低,特别是重复精度低;2、连杆、曲柄齿轮等主要受力件上的运动副,是由铜套组成的滑动轴承,易磨损,对精度影响较大;3、上下模受到的合模力不均匀,对双模轮胎定型硫化机而言,两侧受力,大于两内侧的受力;合模力是曲柄销到达下死点瞬间由各受力构件弹性变形量所决定的,而温度变化使受力构件尺寸发生变化,合模力也随之发生变化,因此生产过程中温度的波动将造成合模力的波动。
液压式硫化机结构上具有如下特点:1、机体为固定的框架式,结构紧凑,刚性良好,在大合模力作用下变形小,有利于轮胎寿命和轮胎质量。
虽然液压式硫化机也是双模腔,但从受力角度看,只是两台单模硫化机连结在一起,在合模力作用下,机架微小变形是以模具中心线对称的;2、各动作快速平稳,大大减少了硫化机辅助时间;3、机器精度高,大大提高轮胎定型精度。
开合模时,上模部分仅作垂直上下运动,可保持很高的对中精度和重复精度;另一方面,对保持活络模的精度也较为有利;4、上下合模力受力均匀,不受工作温度影响;5、装胎机构和中心机构上环的高度可随意准确控制,对于硫化不同规格轮胎很有意义;6、机器的左右机架可以各配一套控制系统,可进行单独控制,独立工作;7、机器各动作简单有效,在用户使用过程中,基本上没有易损件,备件需要更换,也不需要机械式硫化机那样定期中修、大修,大大减少了用户运行成本,增加了设备使用率。
平板硫化机
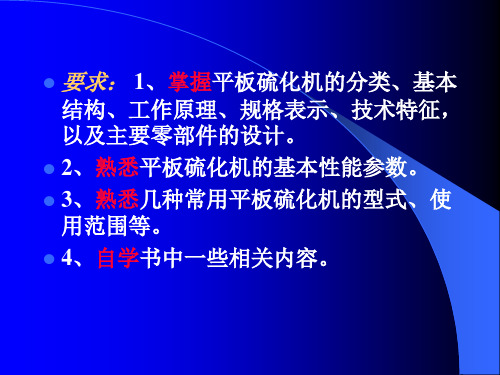
度和厚度,为使平带受到足够的压力,提高 胶布层间的粘着强度,垫铁的厚度应比半成 品厚度薄25~30%。(垫铁是可以更换的)
(六)设有夹持伸长装置,用于硫化前对平
带进行预伸张,使平带在工作过程中帘线受 力均匀,并不致于在使用时迅速的拉伸变形 (伸长)。
(七)对于热缩性纺织物(如尼龙)平带,
工作缸开口端的环形凸肩
是柱塞的导轨,因此对于
柱塞运动较快时,应镶上
青铜衬套。
带有外部密封装置的工作缸,密封
零件(密封圈托架、密封圈等)填于工 作缸壁上部的凹沟内,并用法兰压紧填 料,法兰用螺栓固定在工作缸的突缘上。
(3)上述两种混合表示,吨位/宽度×长度。
2、现在国标的表示方法:
(1)平带平板硫化机为:
DLB—宽度×长度×层数
其中D表示类型为胶带机械。
(2) V带颚式平板硫化机为:
DLE—宽度×长度
其中E表示颚式。
(3)模型制品平板硫化机为:
QLB—宽度×长度×层数
其中Q表示类型为其他机械;L表示硫化;B表示
要求: 1、掌握平板硫化机的分类、基本
结构、工作原理、规格表示、技术特征, 以及主要零部件的设计。
2、熟悉平板硫化机的基本性能参数。
3、熟悉几种常用平板硫化机的型式、使 用范围等。
4、自学书中一些相关内容。
第二节 概述
§2-1用途与分类
一、用途
平板硫化机(compression moulding press)是 一种带有加热平板的压力机。它具有结构简单、 压力大、适应性广等特点。主要用于中小型的 模具制品、胶带、胶板等的硫化。
定张力合幅拼缝成型机:
该机具有分层带定张力贴合、拼缝、胶片合幅、拼缝功能,装 备有自动定边装置、切割装置、张力自动调节装置,由直流电机、 变频电机驱动,可实现各布层间张力可调并基本保持一致,成型 速度可无级调节,整个成型过程实现了自动化控制,大大提升了 输送带的成型质量。
探究液压式轮胎硫化机机械设计

探究液压式轮胎硫化机机械设计摘要:硫化机根据用途不同,其体积也是大小不一,小型硫化机所需空间如同一张办工桌大小,大型机犹如一座小房子。
虽然其体积不同,但硫化机执行的工艺却基本相同。
在轮胎生产工艺中,硫化是制造轮胎工艺的最后一道工序。
作为一种热压模制品,轮胎的产品外观质量、轮胎最终的均匀性以及企业的生产效率几乎全由轮胎硫化设备来决定。
因此轮胎硫化设备常被视为轮胎生产现代化水平的象征和标志,如何优化硫化工艺、改进并研发新型硫化设备一直都是人们关注的热点。
关键词:发展势头;类型;市场定位引言随着我国汽车工业和轮胎工业的发展对轮胎均匀性提出越来越高的要求,硫化机的工作精度越来越被人们所重视,液压硫化机的优越性开始得到充分的显现。
液压硫化机克服了机械式硫化机固有的弱点,吸收了机械式硫化机的优点。
一、发展势头1.1硫化机发展历程目前,液压硫化机的优越性在我国已被轮胎企业广泛认可,尤其是高等级子午胎项目倾向于选用液压硫化机趋势明显。
上世纪50年代以来我国机械式硫化机推广应用取代硫化罐是轮胎硫化的第一次飞跃,那么液压硫化机替代机械式硫化机便是轮胎硫化的第二次飞跃。
我国的液压硫化机开发工作始于20世纪60年代末,国家“八五”规划期间,将液压硫化机列入“子午胎关键设备一条龙”项目,许多橡机厂都看好这条“龙”的潜力,相继着手研制液压硫化机。
当时参与研究的厂家有五六家,但因我国轮胎工业那时尚未形成使用液压硫化机的大气候,轮胎企业基本没有直接使用经验,对液压硫化机的认识不够,加上国产液压元件也不过关,随后的十多年时间都没有形成大批量生产。
随着我国汽车工业和轮胎工业的发展对轮胎均匀性提出越来越高的要求,硫化机的工作精度越来越被人们所重视,液压硫化机的优越性开始得到充分的显现。
现我国液压硫化机被轮胎及橡机企业采用的比重逐渐增加,进入了快速产业化发展阶段。
1.2液压硫化机产业化势头液压硫化机是在机械式硫化机的基础上发展的,它克服了机械式硫化机固有的弱点,吸收了机械式硫化机的优点。
液压硫化机用途
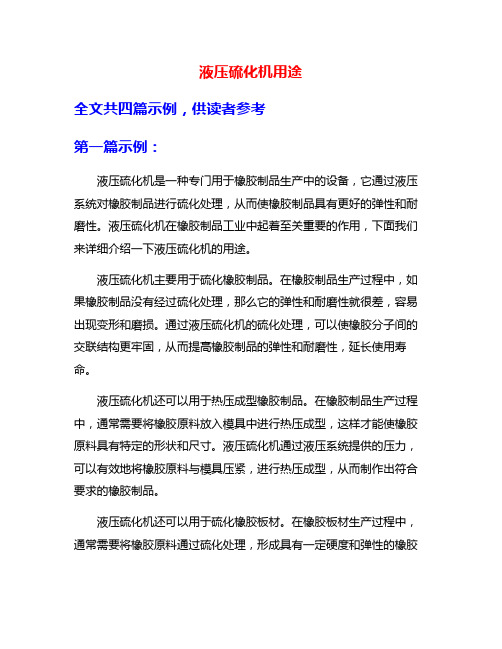
液压硫化机用途全文共四篇示例,供读者参考第一篇示例:液压硫化机是一种专门用于橡胶制品生产中的设备,它通过液压系统对橡胶制品进行硫化处理,从而使橡胶制品具有更好的弹性和耐磨性。
液压硫化机在橡胶制品工业中起着至关重要的作用,下面我们来详细介绍一下液压硫化机的用途。
液压硫化机主要用于硫化橡胶制品。
在橡胶制品生产过程中,如果橡胶制品没有经过硫化处理,那么它的弹性和耐磨性就很差,容易出现变形和磨损。
通过液压硫化机的硫化处理,可以使橡胶分子间的交联结构更牢固,从而提高橡胶制品的弹性和耐磨性,延长使用寿命。
液压硫化机还可以用于热压成型橡胶制品。
在橡胶制品生产过程中,通常需要将橡胶原料放入模具中进行热压成型,这样才能使橡胶原料具有特定的形状和尺寸。
液压硫化机通过液压系统提供的压力,可以有效地将橡胶原料与模具压紧,进行热压成型,从而制作出符合要求的橡胶制品。
液压硫化机还可以用于硫化橡胶板材。
在橡胶板材生产过程中,通常需要将橡胶原料通过硫化处理,形成具有一定硬度和弹性的橡胶板材。
液压硫化机可以通过控制硫化温度、压力和时间,实现对橡胶板材的硫化处理,从而使橡胶板材具有更好的物理性能。
液压硫化机还可以用于制作橡胶密封件和橡胶管道。
在汽车、机械设备、建筑工程等领域,通常需要使用橡胶密封件和橡胶管道,来保障设备的密封性和可靠性。
液压硫化机可以通过硫化处理,使橡胶密封件和橡胶管道具有良好的耐高温、耐腐蚀和耐磨性能,确保设备的正常运行。
液压硫化机在橡胶制品生产中具有非常重要的作用,它不仅可以提高橡胶制品的质量和性能,还可以满足不同行业的需求。
随着科技的不断进步和市场的不断发展,液压硫化机的应用范围将会越来越广泛,为橡胶制品生产带来更多的便利和效益。
希望通过今天的介绍,大家能够更加了解液压硫化机的用途和重要性,进一步推动橡胶制品行业的发展。
第二篇示例:液压硫化机是一种专门用于橡胶制品硫化的设备,是橡胶工业中不可或缺的重要设备之一。
轮胎定型硫化机

充氮硫化的轮胎硫化机中心机构
充氮硫化的轮胎硫化机的中心机构,其大部分 部件与现有的充氮硫化的轮胎硫化机的中心机 构的相应部件相同,所不同的是,缸筒上口装 有缸盖和法兰盖,其环形凹槽喷射蒸气和氮气 的喷口方向分别呈水平偏下向与水平偏上向, 同时,在法兰盖上还装有一吸水胶管,其吸嘴 可吸取胶囊中的冷凝水通过出水管流出。该中 心机构用硫化机硫化轮胎,其硫化室内的蒸气 和氮气混合均匀,能及时排除冷凝水,保证硫 化室温度均匀稳定,从而提高硫化质量。
活络模是把两半模改为胎冠部位可径向分合的 几个小块,在合模时,活络模块能自动的径向 合拢,包住胎坯;卸胎时,活络模块可以径向 分离,脱离硫化的轮胎,这样保证胎体和胎冠 的完整和硫化质量,有利于装卸轮胎。
但是,活络模的结构复杂、制造成本高,因此 目前只在硫化子午线轮胎中采用。
活络模的结构类型较多,可分为:平面导向活 络模、圆锥面导向活络模球面导向活络模、径 向活络模、杠杆式活络模等。目前使用较多的 活络模具为平面导向活络模和圆锥面导向活络 模。
现在人们发现了利用氮气可以解决上述问题,它采用
190—210℃高压饱和蒸汽充入胶囊升温之后,再向胶囊充 入2.0—2.6MPa压力的高纯氮气的增压办法,以达到高温高
压的硫化条件,从而实现了上述目标。
近年来,蒸汽/氮气介质硫化方式发展很快,目前在美国、 日本等主要轮胎生产厂家新建项目已基本采用氮气硫化的 方式。
在模中硫化,胶囊上下夹环 在硫化位置。两个水平气缸
锁住中心机构
硫化结束。开模, 将轮胎顶离下模。
卸胎器转入, 抓住硫化好的轮胎
卸胎器转出,将硫化好的 轮胎送到后充气工位或卸胎 辊道。装胎器转入,将新胎坯
送到硫化工位
到达硫化位置, 胶囊出囊筒
文献综述-平板硫化机的现状及发展趋势与液压技术的发展趋势
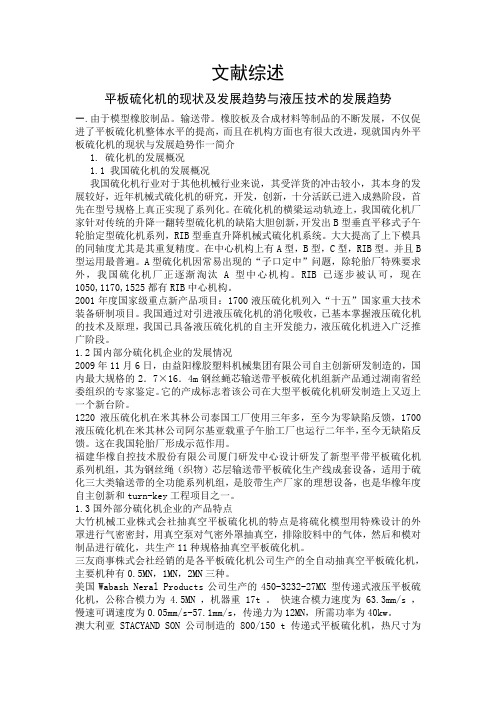
文献综述平板硫化机的现状及发展趋势与液压技术的发展趋势一.由于模型橡胶制品。
输送带。
橡胶板及合成材料等制品的不断发展,不仅促进了平板硫化机整体水平的提高,而且在机构方面也有很大改进,现就国内外平板硫化机的现状与发展趋势作一简介1.硫化机的发展概况1.1我国硫化机的发展概况我国硫化机行业对于其他机械行业来说,其受洋货的冲击较小,其本身的发展较好,近年机械式硫化机的研究,开发,创新,十分活跃已进入成熟阶段,首先在型号规格上真正实现了系列化。
在硫化机的横梁运动轨迹上,我国硫化机厂家针对传统的升降一翻转型硫化机的缺陷大胆创新,开发出B型垂直平移式子午轮胎定型硫化机系列,RIB型垂直升降机械式硫化机系统。
大大提高了上下模具的同轴度尤其是其重复精度。
在中心机构上有A型,B型,C型,RIB型。
并且B 型运用最普遍。
A型硫化机因常易出现的“子口定中”问题,除轮胎厂特殊要求外,我国硫化机厂正逐渐淘汰A型中心机构。
RIB已逐步被认可,现在1050,1170,1525都有RIB中心机构。
2001年度国家级重点新产品项目:1700液压硫化机列入“十五”国家重大技术装备研制项目。
我国通过对引进液压硫化机的消化吸收,已基本掌握液压硫化机的技术及原理,我国已具备液压硫化机的自主开发能力,液压硫化机进入广泛推广阶段。
1.2国内部分硫化机企业的发展情况2009年11月6日,由益阳橡胶塑料机械集团有限公司自主创新研发制造的,国内最大规格的2.7×16.4m钢丝蝇芯输送带平板硫化机组新产品通过湖南省经委组织的专家鉴定。
它的产成标志着该公司在大型平板硫化机研发制造上又迈上一个新台阶。
1220液压硫化机在米其林公司泰国工厂使用三年多,至今为零缺陷反馈,1700液压硫化机在米其林公司阿尔基亚载重子午胎工厂也运行二年半,至今无缺陷反馈。
这在我国轮胎厂形成示范作用。
福建华橡自控技术股份有限公司厦门研发中心设计研发了新型平带平板硫化机系列机组,其为钢丝绳(织物)芯层输送带平板硫化生产线成套设备,适用于硫化三大类输送带的全功能系列机组,是胶带生产厂家的理想设备,也是华橡年度自主创新和turn-key工程项目之一。
机械式和液压式轮胎定型硫化机
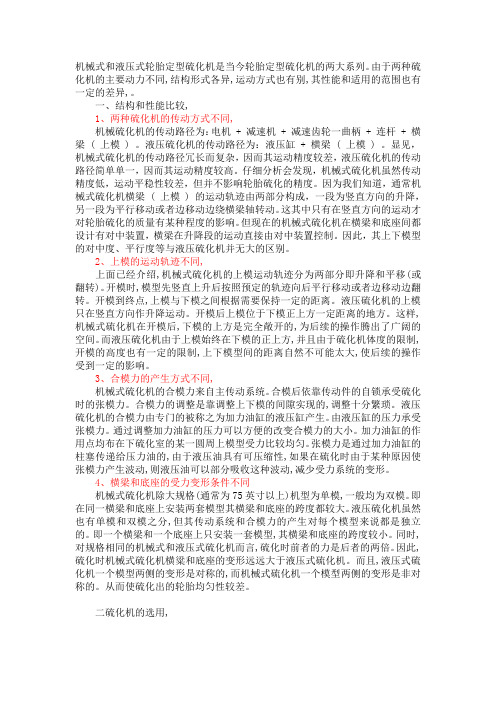
机械式和液压式轮胎定型硫化机是当今轮胎定型硫化机的两大系列。
由于两种硫化机的主要动力不同,结构形式各异,运动方式也有别,其性能和适用的范围也有一定的差异,。
一、结构和性能比较,1、两种硫化机的传动方式不同,机械硫化机的传动路径为:电机 + 减速机 + 减速齿轮一曲柄 + 连杆 + 横梁 ( 上模 ) 。
液压硫化机的传动路径为:液压缸 + 横梁 ( 上模 ) 。
显见,机械式硫化机的传动路径冗长而复杂,因而其运动精度较差,液压硫化机的传动路径简单单一,因而其运动精度较高。
仔细分析会发现,机械式硫化机虽然传动精度低,运动平稳性较差,但并不影响轮胎硫化的精度。
因为我们知道,通常机械式硫化机横梁 ( 上模 ) 的运动轨迹由两部分构成,一段为竖直方向的升降,另一段为平行移动或者边移动边绕横梁轴转动。
这其中只有在竖直方向的运动才对轮胎硫化的质量有某种程度的影响。
但现在的机械式硫化机在横梁和底座间都设计有对中装置,横梁在升降段的运动直接由对中装置控制。
因此,其上下模型的对中度、平行度等与液压硫化机并无大的区别。
2、上模的运动轨迹不同,上面已经介绍,机械式硫化机的上模运动轨迹分为两部分即升降和平移(或翻转)。
开模时,模型先竖直上升后按照预定的轨迹向后平行移动或者边移动边翻转。
开模到终点,上模与下模之间根据需要保持一定的距离。
液压硫化机的上模只在竖直方向作升降运动。
开模后上模位于下模正上方一定距离的地方。
这样,机械式硫化机在开模后,下模的上方是完全敞开的,为后续的操作腾出了广阔的空间。
而液压硫化机由于上模始终在下模的正上方,并且由于硫化机体度的限制,开模的高度也有一定的限制,上下模型间的距离自然不可能太大,使后续的操作受到一定的影响。
3、合模力的产生方式不同,机械式硫化机的合模力来自主传动系统。
合模后依靠传动件的自锁承受硫化时的张模力。
合模力的调整是靠调整上下模的间隙实现的,调整十分繁琐。
液压硫化机的合模力由专门的被称之为加力油缸的液压缸产生。
硫化工艺
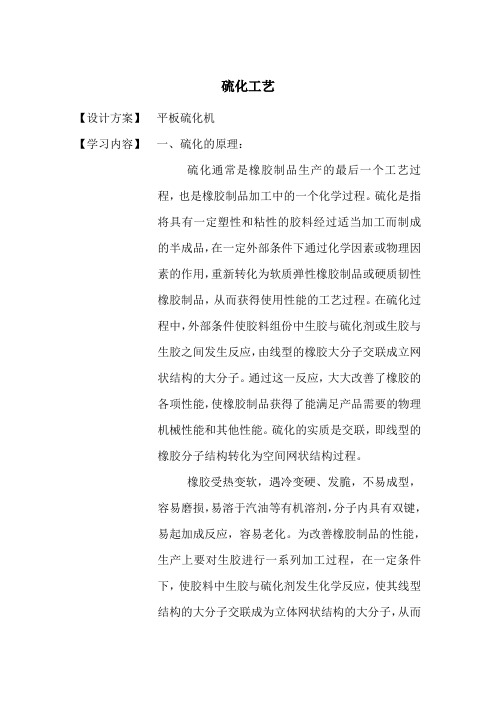
硫化工艺【设计方案】平板硫化机【学习内容】一、硫化的原理:硫化通常是橡胶制品生产的最后一个工艺过程,也是橡胶制品加工中的一个化学过程。
硫化是指将具有一定塑性和粘性的胶料经过适当加工而制成的半成品,在一定外部条件下通过化学因素或物理因素的作用,重新转化为软质弹性橡胶制品或硬质韧性橡胶制品,从而获得使用性能的工艺过程。
在硫化过程中,外部条件使胶料组份中生胶与硫化剂或生胶与生胶之间发生反应,由线型的橡胶大分子交联成立网状结构的大分子。
通过这一反应,大大改善了橡胶的各项性能,使橡胶制品获得了能满足产品需要的物理机械性能和其他性能。
硫化的实质是交联,即线型的橡胶分子结构转化为空间网状结构过程。
橡胶受热变软,遇冷变硬、发脆,不易成型,容易磨损,易溶于汽油等有机溶剂,分子内具有双键,易起加成反应,容易老化。
为改善橡胶制品的性能,生产上要对生胶进行一系列加工过程,在一定条件下,使胶料中生胶与硫化剂发生化学反应,使其线型结构的大分子交联成为立体网状结构的大分子,从而使胶料具备高强度、高弹性、抗腐蚀等优良性能。
二、硫化的方法1、温室硫化法温室硫化法用于需求在室温及不加压的条件下进行硫化的场合。
室温硫化通常将硫化剂与溶剂、惰性配合剂等配成一个组份,橡胶、树脂等与其他配合剂配成另一组分,使用是进行混合。
2、冷硫化法把制成品浸入2%-5%的一氯化硫的溶液中,时间从几秒到几分钟不等。
3、热硫化法⑴、间歇式硫化①、热水槽硫化法此法为直接常压硫化法,把需要硫化的产品浸于热水或盐水,适于乳胶薄膜制品的硫化。
②、烘房、烘箱热空气硫化法此法也为直接常压硫化法,该方法有两种方式,一是把半成品放在加热室中加热硫化;另一种是烘箱硫化,适用于某些特种橡胶制品的二次硫化。
③、硫化罐硫化硫化罐硫化工艺借助飞的硫化设备为硫化罐。
根据硫化介质的不同,硫化罐硫化工艺又有如下几种主要硫化方法:A、直接饱和蒸汽硫化法a、开放式硫化法b、包层硫化法c、埋粉硫化法d、模型硫化法B、热空气硫化法C、热空气-蒸汽混合硫化法⑵、外加压式硫化工艺①、平板硫化机模压硫化法采用这种方法可同时进行胶料在模具型腔内加压流动成型和胶料在硫化温度及硫化压力下发生硫化反应这两个过程。
- 1、下载文档前请自行甄别文档内容的完整性,平台不提供额外的编辑、内容补充、找答案等附加服务。
- 2、"仅部分预览"的文档,不可在线预览部分如存在完整性等问题,可反馈申请退款(可完整预览的文档不适用该条件!)。
- 3、如文档侵犯您的权益,请联系客服反馈,我们会尽快为您处理(人工客服工作时间:9:00-18:30)。
液压式硫化机与机械式硫化机的比较
我国的液压硫化机开发工作始于60年代未期,起步时间不比工业发达国家慢,但是当时国内的液压技术水平限制了液压硫化机的发展。
近年来,随着国内技术的发展和国外技术进入中国,我国液压硫化机的开发和应用都进入了一个高速发展期,现在已经开发出了1050~1700 规格的液压硫化机,并实现了液压硫化机向法国米其林公司的批量出口。
但是总的来说,液压硫化机目前在国内的应用还是不太广泛,那么液压式硫化机与机械式硫化机的差异主要体现在那些方面呢?
结构差异
由于机械式硫化机本身结构的原因,机械式硫化机存在如下问题:
1、上下热板的平行度、同轴度,机械手卡爪圆度和对下热板内孔的同轴度等精度等级低,特别是重复精度低;
2、连杆、曲柄齿轮等主要受力件上的运动副,是由铜套组成的滑动轴承,易磨损,对精度影响较大;
3、上下模受到的合模力不均匀,对双模轮胎定型硫化机而言,两侧受力,大于两内侧的受力;
合模力是曲柄销到达下死点瞬间由各受力构件弹性变形量所决定的,而温度变化使受力构件尺寸发生变化,合模力也随之发生变化,因此生产过程中温度的波动将造成合模力的波动。
液压式硫化机结构上具有如下特点:
1、机体为固定的框架式,结构紧凑,刚性良好,在大合模力作用下变形小,有利于轮胎寿命和轮胎质量。
虽然液压式硫化机也是双模腔,但从受力角度看,只是两台单模硫化机连结在一起,在合模力作用下,机架微小变形是以模具中心线对称的;
2、各动作快速平稳,大大减少了硫化机辅助时间;
3、机器精度高,大大提高轮胎定型精度。
开合模时,上模部分仅作垂直上下运动,可保持很高的对中精度和重复精度;另一方面,对保持活络模的精度也较为有利;
4、上下合模力受力均匀,不受工作温度影响;
5、装胎机构和中心机构上环的高度可随意准确控制,对于硫化不同规格轮胎很有意义;
6、机器的左右机架可以各配一套控制系统,可进行单独控制,独立工作;
7、机器各动作简单有效,在用户使用过程中,基本上没有易损件,备件需要更换,也不需要机械式硫化机那样定期中修、大修,大大减少了用户运行成本,增加了设备使用率。
液压硫化机与机械式硫化机成本比较
•对机械式硫化机与液压硫化机进行成本比较,必须综合考虑配置、性能、开机率、服务、生产率及维修费用等。
•据克虏伯专家介绍,在欧洲若在相同的配置下,液压硫化机比机械式硫化
机更便宜。
•液压硫化机取消了全部蜗轮减速机、大小齿轮、曲柄齿轮以及易损件(连杆、曲柄齿轮等主要受力件上的运动副是由铜套组成的滑动轴承,易磨损),这样减少设备的故障率,提高设备的开机率,同时减少备品备件的支出。
尤其在国产减速机等配套件不稳定的状况下,液压硫化机的这一优势相当明显。
•液压硫化机可大大提高硫化的产量,其原因为:①辅助时间缩短,这主要是设备的原因;②硫化时间大为缩短,主要原因是高温硫化,可以说是工艺变化引起的。
例如,桂林橡机厂研制的1140液压硫化机,辅助时间仅为46s,每锅硫化时间为13min,而普通子午胎硫化机为25-30min,液压硫化机大大提高了生产效率。
•从轮胎硫化质量来看,液压机废品率低,均匀性较机械式有较大提高。
•据德国克虏伯公司介绍,在欧州液压硫化机较机械式便宜,这也是液压硫化机在国外主要轮胎厂迅速推广的原因之一。
机械式硫化机结构性的缺陷及弱点•
•上下热板(或横梁与底座)的平行度、同轴度、机械手对下热板内孔的同轴度等精度等级较液压硫化机为低,特别是重复性精度不如液压式;
•上横梁销轴施加于连杆上部铜套的力,曲柄齿轮轴施加于连杆下部铜套的力,以及曲柄销施加于连杆下部铜套的力都是不均匀的,而且这几个连接部分都在重负荷上转动,不可避免地造成铜套的不均匀和较严重的磨损。
而铜套的磨损进一步降低硫化机的合模精度;
•上下模间受到的合模力不均,对双模定型硫化机而言,总是两外侧的受力大于两内侧受力; •机械式硫化机的合模力是在曲柄销到达下死点瞬间由各受力构件的弹性变形量所决定的。
而温度变化将使受力构件尺寸发生变化,合模力也将随之而变化。
生产过程中环境温度或工作温度的波动将造成合模力的波动。
•液压硫化机克服机械式硫化机的固有弱点,更满足子午胎,尤其是高等级子午胎硫化工艺的需要。
现对双星橡塑机械公司研制的PC-B1220液压硫化机为例加以说明。
一、结构和性能比较, 1、两种硫化机的传动方式不同, 机械硫化机的传动路径为 电机+ 减速机+ 减速齿轮一曲柄+ 连杆+ 横梁( 上模) 。
液压硫化机的传动路径为 液压缸+ 横梁( 上模) 。
显见 机械式硫化机的传动路径冗长而复杂 因而其运动精度较差 液压硫化机的传动路径简单单一 因而其运动精度较高。
仔细分析会发现 机械式硫化机虽然传动精度低 运动平稳性较差 但并不影响轮胎硫化的精度。
因为我们知道 通常机械式硫化机横梁( 上模) 的运动轨迹由两部分构成 一段为竖直方向的升降 另一段为平行移动或者边移动边绕横梁轴转动。
这其中只有在竖直方向的运动才对轮胎硫化的质量有某种程度的影响。
但现在的机械式硫化机在横梁和底座间都设计有对中装置 横梁在升降段的运动直接由对中装置控制。
因此 其上下模型的对中度、平行度等与液压硫化机并无大的区别。
2、上模的运动轨迹不同, 上面已经介绍,机械式硫化机的上模运动轨迹分为两部分即升降和平移(或翻转)。
开模时,模型先竖直上升后按照预定的轨迹向后平行移动或者边移动边翻转。
开模到终点,上模与下模之间根据需要保持一定的距离。
液压硫化机的上模只在竖直方向作升降运动。
开模后上模位于下模正上方一定距离的地方。
这样,机械式硫化机在开模后,下模的上方是完全敞开的,为后续的操作腾出了广阔的空间。
而液压硫化机由于上模始终在下模的正上方,并且由于硫化机体度的限制,开模的高度也有一定的限制,上下模型间的距离自然不可能太大,使后续的操作受到一定的影响。
3、合模力的产生方式不同, 机械式硫化机的合模力来自主传动系统。
合模后依靠传动件的自锁承受硫化时的张模力。
合模力的调整是靠调整上下模的间隙实现的,调整十分繁琐。
液压硫化机的合模力由专门的被称之为加力油缸的液压缸产生。
由液压缸的压力承受张模力。
通过调整加力油缸的压力可以方便的改变合模力的大小。
加力油缸的作用点均布在下硫化室的某一圆周上模型受力比较均匀。
张模力是通过加力油缸的柱塞传递给压力油的,由于液压油具有可压缩性,如果在硫化时由于某种原因使张模力产生波动,则液压油可以部分吸收这种波动,减少受力系统的变形。
4、横梁
和底座的受力变形条件不同机械式硫化机除大规格(通常为75英寸以上)机型为单模,一般均为双模。
即在同一横梁和底座上安装两套模型其横梁和底座的跨度都较大。
液压硫化机虽然也有单模和双模之分,但其传动系统和合模力的产生对每个模型来说都是独立的。
即一个横梁和一个底座上只安装一套模型,其横梁和底座的跨度较小。
同时,对规格相同的机械式和液压式硫化机而言,硫化时前者的力是后者的两倍。
因此,硫化时机械式硫化机横粱和底座的变形远远大于液压式硫化机。
而且,液压式硫化机一个模型两侧的变形是对称的,而机械式硫化机一个模型两侧的变形是非对称的。
从而使硫化出的轮胎均匀性较差。