金属液态成型基础作业
第一章 金属液态成形理论基础

第一节 液态金属充型能力与流动性
0、什么是液态金属的充型能力
1)定义:
液体金属充满铸型型腔,获得尺寸精确、轮廓清晰的 成型件的能力,称为充型能力。
2)充型能力对成型的影响
充型能力不足时,会产生浇不足、冷隔、夹渣、气孔 等缺陷。
3)影响充型能力的因素
充型能力首先取决于金属本身的流动性(流动能力),同 时又受铸型性质、浇注条件和铸件结构等因素影响。
一、铸件的凝固方式
在铸件凝固过程中,其断面上一般存在三个区 域:固相区、凝固区和液相区。
1、分类
依据对铸件质量影响较大的凝固区的宽窄划分 铸件的凝固方式为如下三类:
(1)逐层凝固
纯金属和共晶成分的合金在凝固过程中不存在液、固并 存的凝固区,随着温度下降,固体层不断加厚,液体不 断减少,直达铸件中心,这种凝固方式称为逐层凝固。
机械应力
二、铸件的变形及其防止
1、变形的原因:
铸件内部残余内应力。 只有原来受拉伸部分产生压缩 变形、受压缩部分产生拉伸变 形,才能使铸件中的残余内应 力减小或消除。
平板铸件的变形
杆件的变形
床身铸件的变形
粱形铸件的弯曲变形
2、防止措施:
减小应力; 将铸件设计成对称结构,使其内应力互相平衡; 采用反变形法; 设置拉肋; 时效处理。
2、冷裂纹的特征
裂纹细小,呈连续直线状,裂缝内有金属光泽或轻 微氧化色。
3、防止措施
凡是能减少铸件内应力和降低合金脆性的因素 均能防止冷裂。 设置防裂肋亦可有效地防止铸件裂纹。
防裂肋
三、合金的吸气性
液态合金中吸入的气体,若在冷凝过程中不能溢 出,滞留在金属中,将在铸件内形成气孔。
一)气孔的危害
气孔破坏了金属的连续性,减少了其承载的有效 截面积,并在气孔附近引起应力集中,从而降低 了铸件的力学性能。 弥散性气孔还可促使显微缩松的形成,降低铸件 的气密性。
第一篇金属的液态成形

1. 金属的液态成形(铸造)1.0概述将金属材料加热到高温熔化状态,然后采取一定的成形方法,待其冷却、凝固后获得所需金属制品,这种制造金属毛坯的过程称为金属的液态成形。
金属的液态成形除了铸造之外,还有液态模锻。
1.0.1铸造的定义铸造是指将液态合金浇注到与零件的形状、尺寸相适应的铸型型腔中,待其冷却凝固后,获得所需形状、尺寸和性能的毛坯或零件的金属液态成形方法。
它是生产机器零件毛坯的主要方法之一。
1.0.2铸造的基本过程铸造生产的基本过程包括以下三个步骤:①根据零件的要求,准备一定的铸型;②把金属液体浇满铸型的型腔;③金属液体在铸型型腔中冷凝成形,获得一定形状和尺寸的铸件。
1.0.3铸造生产的特点铸造的实质就是液态金属(合金)逐步冷凝成形,具有以下特点:优点:①适应性广几乎所有金属及其合金,只要能够熔化成液态便能铸造,尤其是适合生产塑性差的材料。
②工艺灵活性大各种形状、尺寸(壁厚从0.5~1000mm、轮廓从几毫米至几十米)、重量(从几克~几百吨)和生产批量的铸件都能生产,能够制成如机床床身、箱体、机架、支座等具有复杂内腔的毛坯。
某些形状极其复杂的零件只能用铸造方法制造毛坯。
③省工省料铸件毛坯与零件形状相似,尺寸相近,加工余量小,金属利用率高,可以省工省料,精密铸件甚至不需切削加工,就可直接装配。
④生产成本低铸造用的原材料来源广泛,可直接利用报废的机件和切屑。
造型设备投资少,易操作。
缺点:①铸件内部晶粒比较粗大,组织疏松,容易产生气孔、夹渣等铸造缺陷,机械性能和可靠性不如锻件,尤其是冲击韧性较差,不宜制造受冲击或交变载荷作用的零件。
②生产过程比较复杂,工序多且一些工艺过程难以精确控制,铸件质量不稳定,废品率较高。
③工人劳动强度大,劳动条件差。
1.0.4铸造生产的发展历史我国是世界上最早掌握铸造生产的文明古国之一。
早在三千多年前,青铜铸器已有应用,二千五百多年前,铸铁工具也已相当普遍。
我国劳动人民对世界铸造业的三大贡献(三大铸造技术):泥型铸造(砂型铸造)、铁型铸造(金属型铸造)、失蜡铸造(熔模铸造)。
金属液态成型基础作业
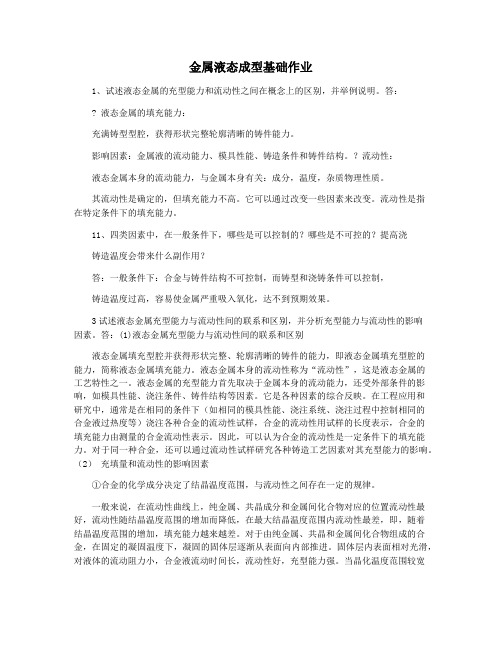
金属液态成型基础作业1、试述液态金属的充型能力和流动性之间在概念上的区别,并举例说明。
答:? 液态金属的填充能力:充满铸型型腔,获得形状完整轮廓清晰的铸件能力。
影响因素:金属液的流动能力、模具性能、铸造条件和铸件结构。
?流动性:液态金属本身的流动能力,与金属本身有关:成分,温度,杂质物理性质。
其流动性是确定的,但填充能力不高。
它可以通过改变一些因素来改变。
流动性是指在特定条件下的填充能力。
11、四类因素中,在一般条件下,哪些是可以控制的?哪些是不可控的?提高浇铸造温度会带来什么副作用?答:一般条件下:合金与铸件结构不可控制,而铸型和浇铸条件可以控制,铸造温度过高,容易使金属严重吸入氧化,达不到预期效果。
3试述液态金属充型能力与流动性间的联系和区别,并分析充型能力与流动性的影响因素。
答:(1)液态金属充型能力与流动性间的联系和区别液态金属填充型腔并获得形状完整、轮廓清晰的铸件的能力,即液态金属填充型腔的能力,简称液态金属填充能力。
液态金属本身的流动性称为“流动性”,这是液态金属的工艺特性之一。
液态金属的充型能力首先取决于金属本身的流动能力,还受外部条件的影响,如模具性能、浇注条件、铸件结构等因素。
它是各种因素的综合反映。
在工程应用和研究中,通常是在相同的条件下(如相同的模具性能、浇注系统、浇注过程中控制相同的合金液过热度等)浇注各种合金的流动性试样,合金的流动性用试样的长度表示,合金的填充能力由测量的合金流动性表示。
因此,可以认为合金的流动性是一定条件下的填充能力。
对于同一种合金,还可以通过流动性试样研究各种铸造工艺因素对其充型能力的影响。
(2)充填量和流动性的影响因素①合金的化学成分决定了结晶温度范围,与流动性之间存在一定的规律。
一般来说,在流动性曲线上,纯金属、共晶成分和金属间化合物对应的位置流动性最好,流动性随结晶温度范围的增加而降低,在最大结晶温度范围内流动性最差,即,随着结晶温度范围的增加,填充能力越来越差。
材料成形工艺基础作业集与自测题
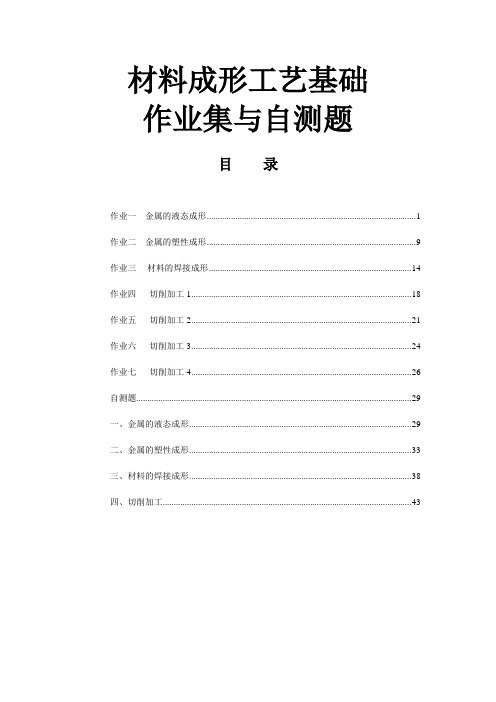
材料成形工艺基础作业集与自测题目录作业一金属的液态成形 (1)作业二金属的塑性成形 (9)作业三材料的焊接成形 (14)作业四切削加工1 (18)作业五切削加工2 (21)作业六切削加工3 (24)作业七切削加工4 (26)自测题 (29)一、金属的液态成形 (29)二、金属的塑性成形 (33)三、材料的焊接成形 (38)四、切削加工 (43)作业一金属的液态成形一、填空题1. 液态金属的充型能力要取决于合金的流动性。
流动性不好的合金铸件易产生、气孔、夹渣等铸造缺陷。
2.影响液态合金流动性的主要因素有、、不溶杂质和气体等。
合金的凝固温度范围越宽,其流动性越。
3.在铸造生产中,合金的浇注温度越离,其充型能力越;充型压力越大,其充型能力越;铸件的壁越厚,其充型能力越。
4.任何一种液态金属注入铸型以后,从浇注温度冷却至室温都要历三个个相互联系的收缩阶段,即、和。
导致铸件产缩孔和缩松的根本原因是;导致铸件产生应力、变形、裂纹的原因是。
5.在铸造生产中,合金的浇注温度越高,其收缩率越;铸件的壁越厚,其收缩率越;铸件的结构越复杂,其收缩率越;铸型的导热性越好,其收缩率越。
6.铸件在凝固过程中所造成的体积缩减如得不到液态金属补充,将产生缩孔或缩忪。
凝固温度范围窄的合金,倾向于“逐层凝固”,因此易产生;而凝固温度范宽的合金,倾向于“糊状凝固”,因此易产生。
7.铸造生产中,合金的结品温度范围越小,越倾向于凝固。
铸件内外之间的温度梯度越大,其凝固区宽度越。
铸件的其他凝固方式还有凝固、凝固。
影响合金凝固方式的因素有、。
8.准确地估计铸件上缩孔可能产生的位置,是合理安排冒口和冷铁的主要依据,生产中确定缩孔位置的常用方法有、和等。
9.顺序凝固原则主要适用于的合金,其目的是;同时凝固原则主要适用于的合金,其目的是。
10.铸件在冷却收缩过程中,因壁厚不均匀等因素造成的铸件各部分收缩不一致而引起的内应力,称为其目的是;铸件收缩受到铸型、型芯及浇注系统的机械阻碍而产生的应力称为。
材料成型理论基础练习题上解读
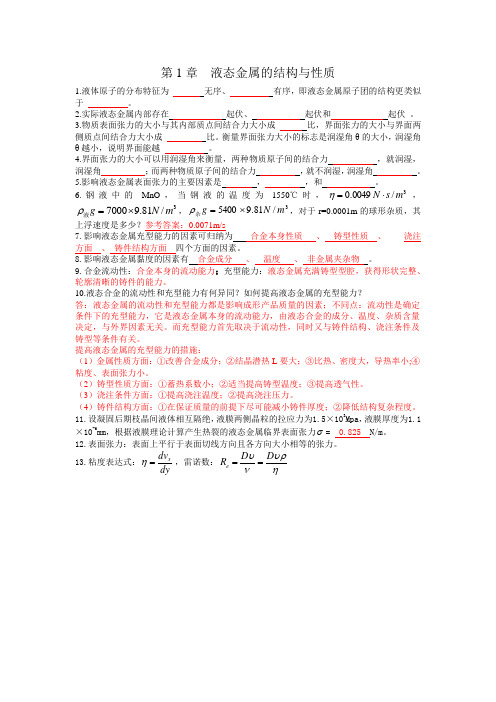
第1章 液态金属的结构与性质1.液体原子的分布特征为 无序、 有序,即液态金属原子团的结构更类似于 。
2.实际液态金属内部存在 起伏、 起伏和 起伏 。
3.物质表面张力的大小与其内部质点间结合力大小成 比,界面张力的大小与界面两侧质点间结合力大小成 比。
衡量界面张力大小的标志是润湿角θ的大小,润湿角θ越小,说明界面能越 。
4.界面张力的大小可以用润湿角来衡量,两种物质原子间的结合力 ,就润湿,润湿角 ;而两种物质原子间的结合力 ,就不润湿,润湿角 。
5.影响液态金属表面张力的主要因素是 , ,和 。
6.钢液中的MnO ,当钢液的温度为1550℃时,3/0049.0m s N⋅=η,3/81.97000m N g ⨯=液ρ,3/81.95400m N g ⨯=杂ρ,对于r=0.0001m 的球形杂质,其上浮速度是多少?参考答案:0.0071m/s7.影响液态金属充型能力的因素可归纳为 合金本身性质 、 铸型性质 、 浇注方面 、 铸件结构方面 四个方面的因素。
8.影响液态金属黏度的因素有 合金成分 、 温度 、 非金属夹杂物 。
9.合金流动性:合金本身的流动能力;充型能力:液态金属充满铸型型腔,获得形状完整、轮廓清晰的铸件的能力。
10.液态合金的流动性和充型能力有何异同?如何提高液态金属的充型能力?答:液态金属的流动性和充型能力都是影响成形产品质量的因素;不同点:流动性是确定条件下的充型能力,它是液态金属本身的流动能力,由液态合金的成分、温度、杂质含量决定,与外界因素无关。
而充型能力首先取决于流动性,同时又与铸件结构、浇注条件及铸型等条件有关。
提高液态金属的充型能力的措施:(1)金属性质方面:①改善合金成分;②结晶潜热L 要大;③比热、密度大,导热率小;④粘度、表面张力小。
(2)铸型性质方面:①蓄热系数小;②适当提高铸型温度;③提高透气性。
(3)浇注条件方面:①提高浇注温度;②提高浇注压力。
(4)铸件结构方面:①在保证质量的前提下尽可能减小铸件厚度;②降低结构复杂程度。
材料加工第2章作业参考答案

第2章作业参考答案1. 液态金属成形的一般工艺过程是怎样的?结合其工艺特点分析该类工艺的优点、缺点和和适用范围。
液态金属成形是将液态金属注入铸型中使之冷却、凝固而形成零件的方法,一般工艺过程包括模样制造、铸型制造、金属熔化与充型、凝固等关键步骤。
铸造为液体成形具有不受零件大小/薄厚/复杂程度限制、可制造各种合金铸件、相对焊接和塑性成形而言尺寸精度高、成本低等优点;但需要造型、浇注等步骤,工艺相对繁琐,工件承载能力不如锻件,同时工作环境差,粉尘多。
铸造适用于绝大部分零件,适用范围广。
(工艺过程三点明确。
明确分析优点、缺点和适用范围,同时结合其工艺特点)2.铸造合金流动性差对铸件质量有何影响?浇注时金属液过热温度及其他工艺条件相同的情况下,初步判断一下HT350和HT200两种合金,哪个流动性好,为什么?什么是液态金属的充型性能?它与那些因素有关?流动性差,金属充型能力差,铸件成形质量降低;液态金属中的气体夹杂物不易浮出,易产生气孔、夹杂;对缩孔和裂纹的充填和愈合作用减弱,易产生缩孔、裂纹等缺陷。
HT200流动性好,HT200碳含量在3.0~3.6%,HT350在2.7~3.2%,因HT200成分更靠近共晶点,固-液区间小,熔点较低,故流动性好(固液两相区越大,结晶温度范围越大,枝晶越发达,流动性越差)。
(流动性影响,判断及理由)充型能力:指液态金属充满型腔,获得形状完整、轮廓清晰健全铸件的能力。
充型能力首先取决于合金的流动性,同时又受到铸型性质(如铸型蓄热系数、铸型温度、铸型中的气体)、浇注条件(如浇注温度、充型压头、浇注系统结构)以及铸件结构(如模数、复杂程度等)的影响。
(充型能力定义,四个影响方面)3. 缩孔、缩松的区别是什么?什么样的合金容易出现疏松缺陷?生产中如何采取措施防止缩孔、缩松缺陷的产生?缩孔缩松的区别在形态,而取决于凝固方式,当铸件以逐层凝固方式凝固时,液态金属的流动使收缩集中到铸件最后凝固部分形成集中孔,即缩孔;而铸件以体积凝固方式凝固时,枝晶间隙的液体得不到补缩而形成小的孔洞,即缩松。
金属液态成型工艺基础

2020/12/20
金属液态成型工艺基础
• 材料成形技术主要研究各种成形工艺方 法本身的规律性及其在机械制造中的应 用;各种成形方法的工艺过程和成形件 的结构工艺性。简单说,这门课程是研 究获得零件毛坯的方法。
金属液态成型工艺基础
• 机械产品的产生过程大致如下:设计与制造 (1)设计——图纸 (2)制造的过程一般是先用铸造、压力加工、焊接、
金属液态成型工艺基础
二、合金的收缩性
1.收缩的概念 合金熔液在型腔内凝固和冷却的过程中,所发
生的体积缩小的现象。收缩性是合金的重要铸造 性能之一,它与铸件的缩孔、缩松、裂纹、变形 等铸造缺陷密切相关。 合金的收缩过程可分为如下三个阶段: ①液态收缩 ②凝固收缩 ③固态收缩
金属液态成型工艺基础
金属液态成型工艺基础
金属液态成型工艺基础
• 合金性质方面 • 铸型和浇注条件 • 铸件结构
•铸件壁厚>最小允许壁厚
•提高流动性的措施: •提高铸型的透气性,降低导热系数; •确定合理的浇注温度; •提高金属液的压头; •浇注系统结构简单。
金属液态成型工艺基础
常用合金的流动性(砂型,试样截面8×8mm)
合金种类
铸型种类
金属液态成型工艺基础
学习本课程应达到的 基本要求:
• 掌握各种毛坯成型工艺的基本原理及工 艺特点;
• 能够初步设计一般零件的毛坯结构; • 具有选择毛坯及工艺分析的初步能力。
金属液态成型工艺基础
参考教材:
《热加工工艺基础》 主编:任福东 机械工业出版社 • 《金属工艺学》 主编:丁德全 机械工业出版社
金属液态成型工艺基础
③铸件结构方面,可 设计适当的加强筋以 增加铸件的刚度;
一液态金属成形过程及控制
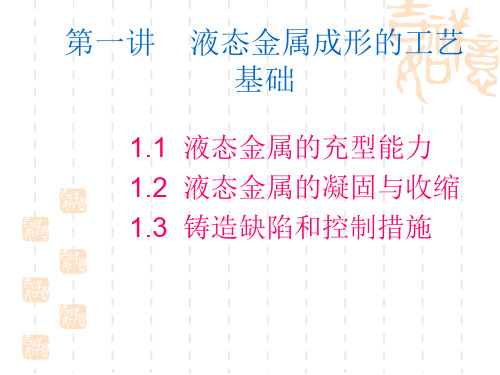
合金凝固温度区间的影响
窄
逐层凝固
中间凝固
宽
糊状凝固
陡
平
温度梯度的影响
4、铸件的收缩
定义:收缩是指合金从浇注、凝固到冷却至室温的过
程中,其体积或尺寸缩减的现象。
分类:分为三类,液态收缩、凝固收缩和固态收缩。
浇注温度
铸 液态收缩
件
开始凝固温度
温
度 凝固收缩
体 积 收
降
缩
低
凝固终止温度
固态收缩
线收缩
室温
共晶成分从液态 变为固态需要一
定的时间
收缩率:
体积收缩是指单位体积的收缩量(表示由液态到常温的收缩)。 线收缩是指单位长度上的收缩量(可以表示固态时的收缩)。
体积收缩率:
V
V0 V1 100% V1
线收缩率:
L
L0 L1 L1
100%
其中 V0,L0表示铸件在高温T0时的体积和一维方向的长度; V1,L1表示铸件在高温T1时的体积和一维方向的长度。
A0.77---------
F +Fe C 0.0218
3 6.69
ES线是碳在γ-Fe中的溶解度曲 线,又称Acm线。
GS线,又称A3线。是冷却时由 奥氏体中析出铁素体的开始线。
L+ +
L+ Fe3C + Fe3C
F+ Fe3C
1、铸件的凝固过程:
在铸件的凝固过程中,其截面一般存在三个区域, 即液相区、凝固区、固相区。对铸件质量影响较大 的主要是液相和固相并存的凝固区的宽窄。铸件的 凝固方式就是依据凝固区的宽窄来划分的。
第一讲 液态金属成形的工艺 基础
- 1、下载文档前请自行甄别文档内容的完整性,平台不提供额外的编辑、内容补充、找答案等附加服务。
- 2、"仅部分预览"的文档,不可在线预览部分如存在完整性等问题,可反馈申请退款(可完整预览的文档不适用该条件!)。
- 3、如文档侵犯您的权益,请联系客服反馈,我们会尽快为您处理(人工客服工作时间:9:00-18:30)。
1、试述液态金属的充型能力和流动性之间在概念上的区别,并举例说明。
答:
①液态金属的充型能力:
充满铸型型腔,获得形状完整轮廓清晰的铸件能力。
影响因素:金属液体的流动能力,铸型性质,浇铸条件,铸件结构。
②流动性:
液态金属本身的流动能力,与金属本身有关:成分,温度,杂质物理性质。
其流动性一定,但充型能力不高,可以改变某些因素来改变,流动性是特定条件下的充型能力。
11、四类因素中,在一般条件下,哪些是可以控制的?哪些是不可控的?提高浇
铸温度会带来什么副作用?
答:一般条件下:合金与铸件结构不可控制,而铸型和浇铸条件可以控制,浇铸温度太高,容易使金属吸气,氧化严重达不到预期效果。
3试述液态金属充型能力与流动性间的联系和区别,并分析充型能力与流动性的影响因素。
答:(1) 液态金属充型能力与流动性间的联系和区别
液态金属充满铸型型腔,获得形状完整、轮廓清晰的铸件的能力,即液态金属充填铸型的能力,简称为液态金属充型能力。
液态金属本身的流动能力称为“流动性”,是液态金属的工艺性能之一。
液态金属的充型能力首先取决于金属本身的流动能力,同时又受外界条件,如铸型性质、浇注条件、铸件结构等因素的影响,是各种因素的综合反映。
在工程应用及研究中,通常,在相同的条件下(如相同的铸型性质、浇注系统,以及浇注时控制合金液相同过热度,等等)浇注各种合金的流动性试样,以试样的长度表示该合金的流动性,并以所测得的合金流动性表示合金的充型能力。
因此可以认为:合金的流动性是在确定条件下的充型能力。
对于同一种合金,也可以用流动性试样研究各铸造工艺因素对其充型能力的影响。
(2) 充型能力与流动性的影响因素
①合金的化学成分决定了结晶温度范围,与流动性之间存在一定的规律。
一般而言,在流动性曲线上,对应着纯金属、共晶成分和金属间化合物之处流动性最好,流动性随着结晶温度范围的增大而下降,在结晶温度范围最大处流动性最差,也就是说充型能力随着结晶温度范围的增大而越来越差。
因为对于纯金属、共晶和金属间化合物成分的合金,在固定的凝固温度下,已凝固的固相层由表面逐步向内部推进,固相层内表面比较光滑,对液体的流动阻力小,合金液流动时间长,所以流动性好,充型能力强。
而具有宽结晶温度范围的合金在型腔中流动时,断面上存在着发达的树枝晶与未凝固的液体相混杂的两相区,金属液流动性不好,充型能力差。
②结晶潜热。
对于纯金属、共晶和金属间化合物成分的合金,在一般的浇注条件下,放出的潜热越多,凝固过程进行的越慢,流动性越好,充型能力越强;而对于宽结晶温度范围的合金,由于潜热放出15~20%以后,晶粒就连成网络而停止流动,潜热对充型能力影响不大。
但也有例外的
情况,由于Si晶体结晶潜热为α-Al的4倍以上,Al-Si合金由于潜热的影响,最好流动性并不在共晶成分处。
③金属的比热.
密度和导热系数比热和密度较大的合金,含的热量较多,保持液态的时间长,流动性好;导热系数小,热量散失慢,保持液态时间长,流动性好。
④液态金属的粘度
粘度对层流流动的流速影响较大,对紊流流动的流速影响不大。
浇注系统或型腔中的流动,基木是紊流流动,粘度对流动性的影响不明显。
⑤浇注温度
液态金属温度越高.其流动性越好,充型能力就越强
4.凝固方式及其影响因素
一般将金属的凝固方式分为三种类型:逐层凝固方式、体积凝固方式(或称糊状凝固方式)和中间凝固方式。
在凝固过程中铸件断面上的凝固区域宽度为零,固体和液体由一条界线(凝固前沿)清楚地分开。
随着温度的下降,固体层不断加厚,逐步达到铸件中心。
这种情况为逐层凝固方式。
铸件凝固的某一段时间内,其凝固区域几乎贯穿整个铸件断面时,则在凝固区域里既有已结晶的晶体,也有未凝固的液体,这种情况为体积凝固方式或称糊状凝固方式。
铸件断面上的凝固区域宽度介于前两者之间时,称中间凝固方式。
凝固方式取决与凝固区域的宽度,而凝固区域的宽度取决于合金的结晶温度范围和冷却强度(温度梯度)。
结晶温度范围越宽,温度梯度越小,越倾向于体积凝固方式。
5.金属凝固方式与铸件质量的关系
逐层方式凝固,凝固前沿直接与液态金属接触。
当液态凝固成为固体而发生体积收缩时,可以不断地得到液体的补充,所以产生分散性缩松的倾向性很小,而是在铸件最后凝固的部位留下集中缩孔。
由于集中缩孔容易消除,一般认为这类合金的补缩性良好。
在板状或棒状铸件会出现中心线缩孔。
这类铸件在凝固过程中,当收缩受阻而产生晶间裂纹时,也容易得到金属液的填充,使裂纹愈合。
体积凝固方式:凝固区域宽,容易发展成为树枝晶发达的粗大等轴枝晶组织。
当粗大的等轴枝晶相互连接以后(固相约为70%),将使凝固的液态金属分割为一个个互不沟通的溶池,最后在铸件中形成分散性的缩孔,即缩松。
对于这类铸件采用普通冒口消除其缩松是很难的,而往往需要采取其它辅助措施,以增加铸件的致密性。
由于粗大的等轴晶比较早的连成骨架,在铸件中产生热裂的倾向性很大。
这是因为,等轴晶越粗大,高温强度就越低;此外当晶间出现裂纹时,也得不到液态金属的充填使之愈合。
如果这类合金在充填过程中发生凝固时,其充型性能也很差。
5.什么是定向凝固原则和同时凝固原则?如何保证铸件按规定凝固方式进行凝固?
答:定向凝固(也称顺序凝固)就是在铸件上可能出现缩孔的厚大部位安放冒口,在远离冒口的部位安放冷铁,使铸件上远离冒口的部位先凝固,靠近冒口的部位后凝固。
同时凝固,就是从工艺上采取各种措施,使铸件各部分之间的温差尽量减小,以达到各部分
几乎同时凝固的方法。
控制铸件凝固方式的方法:(1)正确布置浇注系统的引人位置,控制浇注温度、浇注速度和铸件凝固位置;(2)采用冒口和冷铁;(3)改变铸件的结构;(4)采用具有不同蓄热系数的造型材料。
10.试确定如下两种铸件的凝固时间(均为无过热注入砂型)。
⑴厚度为100mm 的板型铸件。
⑵直径为100mm 的球型铸件。
⑶比较计算结果并讨论之。
答:
()()()()
时间相差很大。
折算厚度不同造成凝固固两种形状不同,使得倍,)(996.898.104.98398.101004.5107.1610
67.17.166100
624.981004.5510104.551004.51051004.505.01004.505.050210012123322222221642322231≈===⎪⎪⎭⎫ ⎝
⎛⨯⨯=⨯=====⨯⎪⎭
⎫ ⎝⎛=⨯⎪⎭⎫ ⎝⎛=⨯⨯=⨯==
⨯====--------τττττs m mm D R s k R k m
mm R。