机组式凹版印刷机主要故障成因及排除
凹版印刷中的故障、原因及解决方法
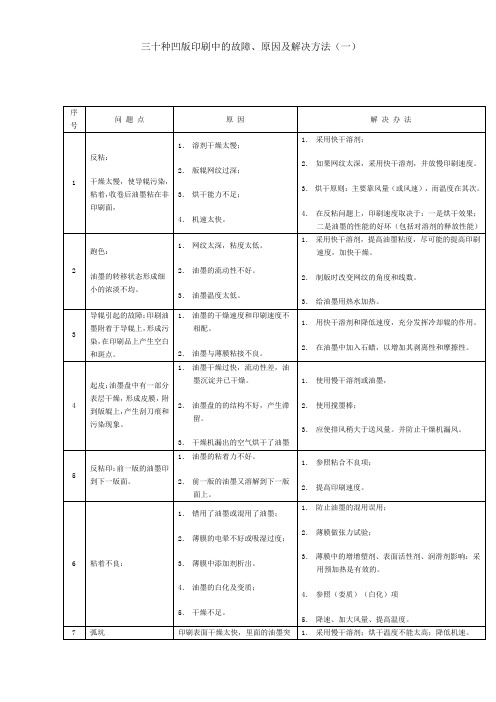
2
跑色:
油墨的转移状态形成细小的浓淡不均。
1.网纹太深,粘度太低。
2.油墨的流动性不好。
3.油墨温度太低。
1.采用快干溶剂,提高油墨粘度,尽可能的提高印刷速度,加快干燥。
2.制版时改变网纹的角度和线数。
3.给油墨用热水加热。
1.使用快干溶剂、提高机速,尽快送入烘干机,印版直径不当造成薄膜滑动;
2.对含增塑剂的薄膜,应避免使用含染料的油墨。从染料的结构知道这种迁移是可能的。
29
粘着、反粘:此时收卷时会有剥离声、重叠部分的油墨会有异常光泽。
1.干燥不良;
2.温度高造成油墨部分软化;
3.收卷太紧;
4.极度的粘着不良;
5.印刷面与接触面的油墨之间亲和力过强。
三十种凹版印刷中的故障、原因及解决方法(一)
序号
问 题 点
原 因
解 决 办 法
1
反粘:
干燥太慢,使导辊污染,粘着,收卷后油墨粘在非印刷面,
1.溶剂干燥太慢;
2.版辊网纹过深;
3.烘干能力不足;
4.机速太快。
1.采用快干溶剂;
2.如果网纹太深,采用快干溶剂,并放慢印刷速度。
3.烘干原则:主要靠风量(或风速),而温度在其次。
1.使用正确的溶剂配方;
2.水白化时:应采用慢干溶剂或提高印刷速度,尽快将薄膜送入烘干机;
3.没有热量的过大风速是有害无益的。
23
起泡:使网点脱落、泡沫飞溅造成印刷品污染
1.水性油墨多发;
2.循环系统缺失。
1.加入消泡剂;
2.避免循环系统中油墨从大的落差流下。
凹版印刷常见故障的现象
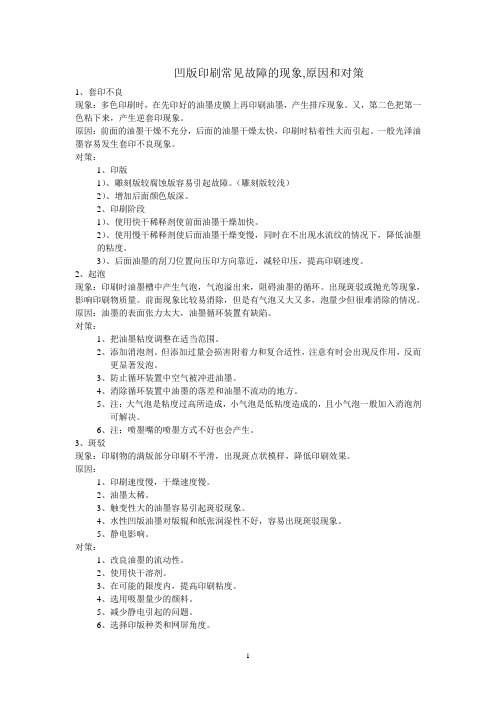
凹版印刷常见故障的现象,原因和对策1、套印不良现象:多色印刷时,在先印好的油墨皮膜上再印刷油墨,产生排斥现象。
又,第二色把第一色粘下来,产生逆套印现象。
原因:前面的油墨干燥不充分,后面的油墨干燥太快,印刷时粘着性大而引起。
一般光泽油墨容易发生套印不良现象。
对策:1、印版1)、雕刻版较腐蚀版容易引起故障。
(雕刻版较浅)2)、增加后面颜色版深。
2、印刷阶段1)、使用快干稀释剂使前面油墨干燥加快。
2)、使用慢干稀释剂使后面油墨干燥变慢,同时在不出现水流纹的情况下,降低油墨的粘度。
3)、后面油墨的刮刀位置向压印方向靠近,减轻印压,提高印刷速度。
2、起泡现象:印刷时油墨槽中产生气泡,气泡溢出来,阻碍油墨的循环。
出现斑驳或抛光等现象,影响印刷物质量。
前面现象比较易消除,但是有气泡又大又多,泡量少但很难消除的情况。
原因:油墨的表面张力太大,油墨循环装置有缺陷。
对策:1、把油墨粘度调整在适当范围。
2、添加消泡剂。
但添加过量会损害附着力和复合适性,注意有时会出现反作用,反而更显著发泡。
3、防止循环装置中空气被冲进油墨。
4、消除循环装置中油墨的落差和油墨不流动的地方。
5、注:大气泡是粘度过高所造成,小气泡是低粘度造成的,且小气泡一般加入消泡剂可解决。
6、注:喷墨嘴的喷墨方式不好也会产生。
3、斑驳现象:印刷物的满版部分印刷不平滑,出现斑点状模样,降低印刷效果。
原因:1、印刷速度慢,干燥速度慢。
2、油墨太稀。
3、触变性大的油墨容易引起斑驳现象。
4、水性凹版油墨对版辊和纸张润湿性不好,容易出现斑驳现象。
5、静电影响。
对策:1、改良油墨的流动性。
2、使用快干溶剂。
3、在可能的限度内,提高印刷粘度。
4、选用吸墨量少的颜料。
5、减少静电引起的问题。
6、选择印版种类和网屏角度。
通常改善制版法腐蚀版雕刻版网屏角度45度15-30度版深> 32 μ28 μ压辊硬度70-8-度4、堵版现象:印刷时在印版网点中的油墨干燥,致使印刷物出现网点残缺的现象。
凹版印刷常见故障的成因及对策

凹版印刷常见故障的成因及对策一、回粘塑料薄膜或透明纸印刷后印迹有干燥的假象,但在印好卷筒或制袋后的存放时期又出现背面粘脏的现象。
严重时印件之间撕不开,图文墨层移染,造成产品报废。
这种现象在高温季节更易发生,但高温不是造成回粘的惟一原因,它还与塑料、油墨、溶剂、风量、光照、速度等一系列因素有着密切的联系。
1.凹印油墨中的溶剂在印刷后未能得到彻底挥发。
(1)塑料薄膜印刷是通过溶剂蒸发使油墨干燥的。
其挥发速度是决定墨层干燥情况和影响印刷质量的重要因素。
溶剂挥发得愈慢,则版子的再现性良好,印刷品色泽愈美观,但容易粘连;反之,会产生印迹发白等观象。
因此,选择适当挥发速度的溶剂,是塑料薄膜凹版印刷的关键。
在连续套色印刷中,薄膜在两印刷工位之间运行时间内,溶剂必须全部挥发完,否则,在下一个工位印刷时,就会粘辊。
(2)薄膜印刷后,油墨中的有机溶剂在干燥系统中未得到彻底挥发,薄膜收卷后仍有余热,给残留在墨层中的溶剂,带来继续挥发的条件,而形成粘连。
(3)高温潮湿李节,印刷后薄膜收卷过紧或受压.对策:油墨中溶剂的挥发速度,不仅取决于溶剂的沸点,蒸气压、蒸气潜热等,还取决于操作环境的温度、湿度、风量、溶质和墨层厚薄等条件。
因此,应根据条件的变化,随时调整油墨中溶剂的挥发速度.在一般温度下,如墨层干得过快,应加入挥发慢的溶剂(如沪产74-92型塑料薄膜慢干稀薄剂);反之,则加入挥发快的溶剂(如74-91塑料薄膜快干稀薄剂)。
也可用二甲苯、乙醇和异丙醇混合溶剂来稀释(三种溶剂各以1/3比例混合,使用单一溶剂不如混合溶剂好)。
如觉干燥太快,可适量用一点丁醇来代著部分乙醇(丁醇有增加墨色光泽的作用)。
但千万要注意加入量要适当,以免影响印件的干燥。
塑料薄膜凹版印刷用的溶剂,以醇类为主,配以苯类.醇类多用乙醇、异丙醇,苯类多用甲苯、二甲苯。
由于硝化纤维的需要,也要加入酯类,如醋酸乙酯、醋酸丁酯。
总之,力求油墨中的有机溶剂在收卷之前得到彻底挥发.适当减慢车速,加大风量。
凹版印刷常见故障处理方法

凹版印刷常见故障处理方法凹版印刷是一种常见的印刷技术,但在实际操作过程中,常常会遇到一些故障,影响印刷质量和工作效率。
下面是凹版印刷常见故障及处理方法:1.胶辊过磨损胶辊过磨损会导致墨量不稳定,在印刷过程中出现墨色深浅不一的情况。
处理方法是更换新的胶辊,确保其表面光滑。
2.胶辊不均匀磨损胶辊不均匀磨损会导致墨量分布不均匀,造成印刷图案不够清晰。
处理方法是通过精确调整胶辊的位置和轴向,使其均匀磨损。
3.油墨不连续油墨不连续会导致印刷图案有色差或缺墨现象。
处理方法是检查墨盘的墨量,补充油墨或清洁墨盘,以保持墨量稳定。
4.墨色不准确墨色不准确会导致印刷品颜色偏差。
处理方法是调整墨辊和胶辊的间隙,以控制墨色的传递量。
5.凹版压力不均匀凹版压力不均匀会导致印刷图案不清晰或出现模糊现象。
处理方法是检查印刷机的平衡性,调整压力辊和背压辊,以确保凹版压力均匀。
6.凹版转速过快或过慢凹版转速过快或过慢会导致印刷图案模糊或出现缺失。
处理方法是根据实际情况调整印刷机的速度,使其与凹版的匹配度最佳。
7.凹版磨损凹版磨损会导致印刷品细节不清晰或产生噪点。
处理方法是定期更换凹版,并及时做好保养工作,延长凹版的使用寿命。
8.印刷雾化印刷雾化会导致文字或图案模糊不清。
处理方法是调整印刷机的湿度和温度,以控制墨水的流动性,减少雾化现象的发生。
9.纸张吸湿纸张吸湿会导致纸张变形,影响印刷质量和注册精度。
处理方法是调整印刷机的湿度和温度,选择合适的纸张,并进行事前处理,防止纸张吸湿。
10.印刷品色差印刷品色差会导致不同批次的印刷品颜色不一致。
处理方法是确保油墨的配比准确,并严格控制墨水的传递量和温度。
11.印刷精度不高印刷精度不高会导致图案偏移或错位。
处理方法是检查印刷机的注册设备,调整凹版和印刷机的位置,确保印刷精度达到要求。
总的来说,凹版印刷常见故障的处理方法包括更换磨损部件,调整印刷机的湿度和温度,控制油墨的传递量和墨色,以及定期维护保养设备。
凹版印刷中发生的故障及解决方法

凹版印刷中发生的故障及解决方法来源:卫群科技时间:2017-06-05 10:06作者:卫群科技编辑浏览:118 次摘要:问题原因对策 1 、粘连。
卷取的印刷品油墨层附着到另一个接触面(通常是薄膜的背面),从而阻碍了回卷以及发生印刷品污染、油墨的剥离。
粘着的前一段是回卷时发生剥离声,或在重叠...问题原因对策1、粘连。
卷取的印刷品油墨层附着到另一个接触面(通常是薄膜的背面),从而阻碍了回卷以及发生印刷品污染、油墨的剥离。
粘着的前一段是回卷时发生剥离声,或在重叠部分的油墨表面呈现出异常的光泽1、油墨干燥过慢,有假干现象。
2、有溶剂残留。
3、印刷及存放环境温度过高。
4、收卷压力过大。
5、卷料受压大或撞击。
6、收卷时基材含水量过大。
7、基材中添加剂过多。
8、不同油墨品种错误混用。
9、印刷面与接触面的油墨之间亲合力过强。
1、改用配用适当的溶剂。
2、改造干燥装置,采用低沸点溶剂,充分发挥冷却辊的作用。
3、印刷品放置阴凉处,产品堆放时间尽量缩短。
4、降低收卷张力。
5、采用直立式放置,运输过程禁止撞击。
6、使冷辊水温高于室内露点温度,以防止水分凝洁。
7、更换基材。
8、清楚油墨性能,旧墨消耗时尽量少许添加。
9、赛洛汾、尼龙,两面电晕处理薄膜等与油墨膜的亲合力很强,危险性大,所以应事先与油墨厂洽商,采取适当的对策。
2、附着不良。
1、错用了油墨或混合了不同种类的油墨。
2、基材表面处理不够或存放时间过长。
3、基材吸湿过度。
4、受到基材中添加剂的影响。
5、由于油墨的白化及变质造成的。
6、干燥不足。
1、应绝对避免将油墨转作他用以及混用不同种类的油墨,为了防止误用,应将用剩的油墨记清品名,日期等进行保管,以备再用。
2、再进行电晕处理,用湿润张力液检查是否达到要求值。
3、尼龙、玻璃纸材料确认后才使用。
4、基材中含有的增塑剂,表面活性剂、润滑剂等可能会妨碍油墨附着,因此对未曾使用过的薄膜,在首次使用时,应事先掌握其特点。
5、参照(白化)项及(变质)项。
凹版印刷常见故障及解决方法

凹版印刷常见故障及解决方法干燥太慢问题:干燥速度如果太慢,会引发导辊污染、粘附、以及过高的残留溶剂;原因:溶剂的干燥速度过慢、版深过于深、烘干机能力不足、印刷速度过快;解决方案:选择合适干燥速度的溶剂;如果不得不使用较深的版,应配合快干溶剂,并放慢印刷速度;印刷速度应有烘干机能力决定,烘干首要依靠风量,其次才是温度。
跑色问题:阴影部分的油墨转移,形成西小的浓淡不均,绿色的印刷特别常见;原因:凹版的深度太深而油墨粘度太低、由于某种原因影响了油墨的流动性、幽默的温度低;解决方案:采用干燥快的溶剂以高粘度的油墨印刷,制版时改变版网的角度和线数,使用油墨前用热水加温。
卷曲问题:印刷物向内侧卷曲,影响制品美观,也给二次加工带来困难;原因:由于油墨溶剂造成的薄膜膨胀,油墨层和薄膜因温度、湿度变化产生的膨胀率不同;解决方案:选择不溶胀薄膜的油墨及溶剂,尽可能使用较浅的版深来再现色调,在薄膜背面涂布防卷曲剂。
起皮问题:油墨盘中的油墨上有一层干燥的表皮,该表皮可能会附着到滚筒上,形成凹凸不平、刮刀痕或污染;原因:油墨干燥速度过快,干燥机漏出的空气烘干了油墨表层;解决方案:调整油墨干燥速度,应使干燥机的排风量略大于送风量,并防止空气从干燥机中漏出,对油墨盘给予适当覆盖,避免风吹到油墨。
反粘印问题:前一版印刷的油墨又到下一版的版面上;原因:前一版的油墨膜溶解到下一版面上;解决方案:第二版以后各班的油墨要使用溶解力稍弱的溶剂稀释,此外印刷速度不能过慢。
网线问题:转移到薄膜上的油墨呈网点状态,在应该涂布的阴影部分形成各自独立的小点;原因:油墨干燥过快或粘度过高,在油墨流平之前就已干燥固化,制版时网幅过宽;解决方案:用干燥较慢的溶剂,刮刀位置尽量前移并注意烘干机的漏封,保证流动性适宜的前提下尽量使用低粘度油墨进行印刷。
粘着不良问题:达不到油墨粘接力的要求;原因:用错油墨,薄膜表面张力不足,薄膜中的添加剂影响,油墨干燥不足;解决方案:加强管理,对用剩的油墨表面品名及日期以备再用,印刷前检测薄膜的表面张力,注意薄膜中的爽滑剂等添加剂影响,首次使用新的薄膜时应了解相关情况,利用烘干机进行充分干燥。
凹印印版故障分析与排查

凹印印版故障分析与排查一、套印不准在凹版印刷影响套印精度的因素很多,如,采用的主电机及其控制系统的稳定性和可靠性,齿轮箱的传动形式及精度,导纸辊动静平衡的好坏,电气系统的灵敏度及可靠性,设备在使用过程中出现的违章操作,机械系统保养不档造成的磨损,局部变形等均是套印不准的因素。
在这主要分析一下与版辊相关的一些因素。
(一) 版辊的机械精度目前制版商出厂的版辊机械精度一般均要达到以下要求:项目要求长度极限偏差辊长的±0.2%直径极限偏差±0.02 mm壁厚范围 6 mm-12 mm键槽宽度深度极限偏差 +0.3 mm锥孔锥度极限偏差±1°圆柱度不大于0.03 mm法兰圆角 7 mm~11 mm动平衡 80 g以下(1200 r/m)版辊精度超差是造成套印不准的原因之一。
单凹机目前制版有两种形式一种带轴版,一种空心版。
1.带轴版带轴版费用高,但加工精度也高。
因为带轴版制版商加工时要经过进口MDC车磨而成,一方面车磨机的精度高,另一方面车磨时的基准点与印刷时的基准点相同,所以印刷时版辊机械精度高。
2.空心版空心版费用略低,但由于制版时的加工基准难以同印刷基准相同,其次即使制版同印刷基准找一致,还存在印刷时操作工穿轴时不规范或穿杠轴长期拆卸,尤其是野蛮拆卸造成轴损伤,使得实际穿轴后,版辊左右跳动超差,不圆度超标等均是套印不准的主要原因。
(二) 纸张丝缕方向对套印的影响一般来说,纸张纤维的横向膨胀要比纸张纤维的纵向膨胀大得多,一般为2~8倍。
因此,纸张纤维的横向伸长也就比纵向伸长大得多了。
直丝缕纸张印刷是指印刷的纸张纤维方向与滚筒转动方向一致。
横丝缕纸张印刷是指纸张纤维方向与滚筒轴线方向一致。
直丝缕纸张从开机到印完,纸张的伸缩变化是横向大于纵向,印刷后就出现了纸张图文容易产生横向套印不准。
横丝缕纸张印刷后,纸张的伸缩变化是纵向大于横向,印刷后图文容易产生纵向的套印不准。
凹印12种常见故障分析及解决方法

凹印12种常见故障分析及解决方法在凹版印刷过程中往往会发生一些由机械、工艺原辅材料、工作环境等因素引起的印刷故障,从而影响产品质量和生产进度。
现将在从事凹印工作中积累的实用经验介绍给大家,供同行们参考。
故障一规则性和无规则性线痕(刀线)1、规则性线痕原因:(1)油墨内混有残渣把刮墨刀划伤;(2)印版或能被硬物划伤;(3)印版滚筒磨损掉铬,铜层裸露。
解决方法:(1)用80目的铜网重新过滤油墨,并用600号水砂纸细磨刀刃或更换墨刀;(2)用800号水砂纸蘸溶剂细磨划伤处;(3)用溶剂洗净印版,用502胶水和铜粉填补划伤,并拿细砂纸轻轻打磨光滑(注:此方法适于短版产品)。
2、无规则性线痕原因:(1)刮墨刀刀锋利度不够;(2)刮墨的倾斜度不够,刮墨刀压力过小;(3)刮墨刀安装时平整度差;(4)油墨与溶剂的溶解性、流动性不好;(5)印版滚筒铬层表面处理不平滑,过于粗糙;(6)印刷滚筒印刷时周向跳动大;(7)油墨内有墨渣,粘在刀刃背后‘(8)墨管和位置不理想,油墨流入墨槽过急,造成油墨不匀。
解决方法:(1)用600号水砂纸打磨刀刃;(2)加大刮墨刀的压力,使其倾斜角度向下,并根据实际情况移动刀架,理想接触角度为50―70度;(3)上刀片时,尽量做到用碎布夹紧压条与刀片,使力向外侧拉,同时从中间旋紧螺丝,逐个向外,但紧螺丝不可一步到位,不需重复二三遍完成,使刀片受力均匀;(4)控制好油墨粘度(在不影响印刷效果的前提下),尽可能使用溶解性强,挥发快的深剂,如醋酸乙酯,乙醇,加入少量异丙醇,可增加光泽度;(5)用800号或600号水砂纸蘸溶剂来回打磨印版滚筒,注意磨至图文部分时用力不要过大,如不理想可与制版厂联系重制印版滚筒;(6)检查印版滚筒、滚筒轴、轴承及传动齿轮是否形变、磨损,还可能是由机座水平不正、不稳造成;(7)墨槽、墨箱洗净,油墨多层过滤;(8)移动墨管位置或合理改进墨槽结构。
故障二拖影原因:(1)油墨稀释过滤,粘度下降;(2)刮墨刀与印版接触角度不佳,过于上仰或顶刀力量过大造成刀刃翘曲;(3)调金油与金属粉调配比例不正确;(4)刮墨刀片过软,安装时压条与刀口的距离过大,刀片伸出过长;(5)压印滚筒压力过大,油墨挤出;解决方法:(1)增大油墨粘度,如情况无明显好转,可重新换墨;(2)将刮墨刀的接触角度调节下倾,顶刀力减小;(3)适度减小调金油的用量;(4)改用弹性高的硬刀片,最好用**产的,缩小刀片与压条的伸长距离;(5)减轻压印滚筒的压力;(6)如拖影现象不严重,可适当提高机速来消除。
- 1、下载文档前请自行甄别文档内容的完整性,平台不提供额外的编辑、内容补充、找答案等附加服务。
- 2、"仅部分预览"的文档,不可在线预览部分如存在完整性等问题,可反馈申请退款(可完整预览的文档不适用该条件!)。
- 3、如文档侵犯您的权益,请联系客服反馈,我们会尽快为您处理(人工客服工作时间:9:00-18:30)。
(6) 油墨中的粗颗粒
(6) 用尼龙袜过滤或尼龙网袋过滤油墨。
(7) 环境卫生差,油墨中尘埃较多
(7) 搞好环境卫生,做防尘地面。
塑机凹印机的主要故障产生原因及其排除 序 号 故 障 现 象 产 生 原 因 建 议 排 除 方 法
(1) 导辊、冷却水辊表面有伤痕。
(1) 查找导辊表面伤痕并修复。
印品印刷面划伤(设备因素) (2) 导辊、冷却水辊运行不同步,有卡阻。
(2) 整机导辊有部分运转不灵活,需定期检修或用静电电压表检测跟踪,修复导辊。 (3) 压印胶辊配置不当,尽可能选用导电橡胶或有防静电功能的胶辊,修复运转不良的压印胶辊。 (4) 每三个月检修清洗防静电带、防静电刷或更换。 (5) 每色组需用6mm2铜芯软线与2.5mm2联接至二组防静电带或防静电刷。每2色组需用铜芯导线 与接地网联接。每台印机接地网点不少4点X35mm2截面积,尽可能用铜芯导线联接。用铸铁 墙板作接地体效果不好,4点接地电阻需小于4Ω ,需用接地电阻测试仪检测。 (6) 尽可能对空气进行过滤,地面要做防尘处理。 (7) 冷却水系统要及时清洗或改装用工业冷水机,保持较好的冷却效果。 (8) 采用防火防爆型有源式静电消除器装置。 (9) 入印前薄膜压印胶辊需有防静电装置,防静电刷等。 (10) 输出牵引辊内用冷却水循环,降低薄膜温度。
(18) 自动修正补偿辊水平误差大。 (19) 压印气缸运行抖动或气压不稳定。
塑料凹印机的主要故障产生原因及其排除 序 号 故 障 现 象 产 生 原 因 建 议 排 除 方 法
(20) 上机前检查压印胶辊状况,不良的不上机开印。硬度选择:70HG、78SHA级,单边厚15mm, 无缝钢管厚度不小于10mm或中间大。 (21) 更换间隙较小的减速机或提高传动精度。 (22) 每六个月定期更换返磨。 (23) 放卷系数:0.6-0.7 入料系数:0.8-1.0 出料系数:0.8-1.2 收卷系数:0.6-0.8
(1) 设备基础纵、横向变形或松动。 (2) 地脚螺栓、墙板联接螺栓松脱。 (3) 导辊、传动轴、顶版轴、离合齿轮、轴承、 磨损、松动、缺油、损坏、卡阻等。 (4) 传动轴联轴器选择不当或损坏。 一、套印不准(设备因素) (5) 色组间直线度发生偏移。
1
(1)整幅纵向套印不准。 (2)整幅横向套印不准。 (3)部分色组套印不准。 (4)纵向单边套印不准。 (5)印品中部套印不准。 (6)局部图案套印不准。
3
(2)间断性的细刀线 (4) 刮刀、衬刀安装尺寸不当 (4) 衬刀片伸出夹板10-12mm,刮刀伸出衬刀片3-5mm。
(3)较粗的颗粒线
(5) 刮刀与印版磨损的金属粉末
(5)
在墨槽的背面底部安装强磁铁3-5块固定,可以将油墨中的金属粉末集中固定,不易飘浮在 油墨当中,进入网穴,从而保护印版及刮刀。
1
(1)整幅纵向套印不准。 (2)整幅横向套印不准。 (3)部分色组套印不准。 (4)纵向单边套印不准。 (5)印品中部套印不准。 (6)局部图案套印不准。
(25) 张力检测及控制系统:配置档次低或抗干扰 能力差。 (26) 导辊、冷却水辊表面磨损或不清洁。 (27) 光电眼旁导辊粘有油墨,便薄膜抖动。 (28) 供电电能不稳定。HZ V (29) 印刷基材幅宽与印机幅度不匹配。
(30) 手动纠偏补偿装置损坏或误操作,位置不正。 (30) 修复手动补偿装置。 (31) 冷却水辊太小或冷却水系统配置不当及未定 期清洗。 (32) 冷却辊水温偏高、薄膜冷却差。 (33) 整机压印胶辊直径,重量相差较大。 (34) 光电反光板表面有油污。 (35) 机速过低或过高。 (36) 增、减速时间过短。 (37) 刮刀调整过大、过快。 (38) 油墨的粘度突然变化。 (31) 重新改造冷却水系统每六个月定期清洗保养冷却水辊系统。 (32) 18-25℃为宜,不结露。 (33) 尽可能先用直径、重量一致的压印胶辊上机同时使用。 (34) 开机前及时清洗或改装成玻璃镜片。 (35) 依据基材状况,调整机速尽可能不超过印机设计最高机速85%。 (36) 延长增、减速的时间,尽可能不少于60秒。 (37) 培训操作人员。 (38) 同上
塑机凹印机的主要故障产生原因及其排除 序 号 故 障 现 象 产 生 原 因 建 议 排 除 方 法
刮刀机构设计改装用气压形式,并有背压功能,减小刮刀机构对印版的压力。压力设置约 减去背压后为0.8kg-2kg之间。在刮墨良好的状况下压力尽量小。
(1) 刮刀机构设计不合理,压力设置太大
(1)
印品刀线(设备因素)
(20) 压印胶辊弯曲或轴承损坏、磨损、卡阻。 (21) 入料、出料牵引减速机间隙大或磨损。 (22) 入料、出料牵引压辊表面磨损。 (23) 四段张力设置不当。 一、套印不准(设备因素) (24) 电机驱动系统配置档次低或抗干扰能力差。
(24) 改造驱动系统,加强屏蔽和接地。(接地电阻<4Ω ) (25) 改造张力系统,加强屏蔽和接地。(接地电阻<4Ω ) (26) 重车导辊、冷却辊表面、重车排气槽,定期保养、检修导辊轴承设备。 (27) 及时清理导辊上的油墨。印刷膜距反光板1mm,印刷膜距光电眼5-8mm。 (28) 加装稳压装置(控制系统)。 (29) 大于机幅60%的基材。
(6) 定期清洗冷却水辊或改造冷却水系统。
作者:钟星耕 2007.12
(6) 干燥温度偏高、温度失控或误差较大。 (7) 烘箱热风调节与排风调节不当,清扫不及时 。
(8) 光电眼检测时,运行薄膜抖动。 (9) 光电眼识别能力弱、不匹配、松动、抖动。 (10) 光电套准系统通讯联线松脱或受干扰。 (11) 自动套准系统工艺参数设定不对、操作有误 。
(12) 印版或版轴圆跳动误差大。 (13) 印版径级递增不对。 (14) 刮刀架运行间隙抖动。 (15) 大包角导辊运行时异常跳动、旋转不灵活。 (16) 压印点路线过长。 (17) 自动修正补偿电机,联轴器、滚珠丝杆松动 、磨损、缺油、不灵活。
(2) 刮刀选用不当,衬刀片选用不当
选用正牌刮刀,衬刀片可以使用单面或双面衬刀片,夹持住刮刀在中间,衬刀片厚度在 (2) 0.5~1.2mm之间,衬刀片要用弹性优良的弹簧不锈钢片。长期使用不易变形,装上刮刀架后 无波浪形,表面光滑平整。 (3) 调整刮刀摆幅5~10mm之间。
(1)明显的连续性刀线
(3) 刮刀机构摆动太小
塑料凹印机的主要故障产生原因及其排除 序 号 故 障 现 象 产 生 原 因 建 议 排 除 方 法
(1) 每十八个月检查、调整凹印纵、横向水平及设备基础(误差小于0.04mm/m) (2) 每三个月定期检查墙板连接螺栓。 (3) 每三个月检查导辊、主齿轮箱、各传动轴的运行状况,发现异常需及时更换或清洗、加油 、修理等,印机使用5年以上,需注意导辊表面磨损¸表面粗糙度¸排气槽,必要时表面重新加 工。 (4) 选择合适的弹性联轴器或更换。 (5) 每十八个月检验、调整凹印机色组间直线度(误差小于0.2mm)。 (6) 修理供热干燥系统或干燥系统整体改造。(±2.0℃) 调整印机进出风门,喷咀风速≥32m/s,约1800pa。排风机全压在750-950pa之间,及时清理 。 (8) 给排风设计、配置安装、使用不当或光电眼部的上下导辊距离过大,导辊包角太小,建议 部分改造。 (7) (9) 更换或维修光电眼,强化员工操作责任或技能。 (10) 加强检查、维修工作基础,选择有屏蔽的各类元件并保持良好的接地状态。(独立接地电阻≤1Ω ) (11) 按工艺要求检查工艺参数设定值。调整PID值。(按套准系统使用说明书) (12) 更换印版、锥堵、版轴(误差大于0.10mm)并调整轴承间隙校正。 (13) BOPP印版递增在0.03mm-0.05mm。 (14) 检查刮刀架抖动原因并修复。 (15) 检查导辊运行状况误差不大于0.10mm,更换轴承。烘箱内导辊在冷态下允许0.50-0.80的横 向间隙(有弹性) (16) 减少跨色印刷或降低修正补偿辊位置高度进行印刷。 (17) 检查滚珠称杆转动间隙不大于0.2mm。观察永磁同步电机工作状态,每三个月加油一次。 (18) 水平误差不大于0.02m/m。 (19) 修复压印气缸抖动,改造整机供气系统。(气压≥0.7Mpa,流量≥1.2m³/min/台,DN25)
(2) 清洗轴承或加油及更换。
(1)油墨粘辊
(3) 薄膜运ቤተ መጻሕፍቲ ባይዱ时漂移。
(3) 调整张力设置,调整进出排风。
4
(2)异物划伤 (4) 干燥烘箱有异物。 (4) 每一个月清扫一次烘箱。
(5)
输出牵引辊表面不清洁或温度过高,粘有油 墨,胶带等异物。
(5) 清理牵引辊表面或改造牵引辊成内置循环水。
(6) 薄膜冷却不良。
塑机凹印机的主要故障产生原因及其排除 序 号 故 障 现 象 产 生 原 因
(1)
建 议 排 除 方 法
印机运转时,尽可能保持温度在15℃~30℃之间,空气相对湿度在55%~75%之间,必要时可 以用机械自动增湿或人工增湿或自动除湿机。
(1) 环境空气相对湿度低 印刷品静电故障(设备因素) (2) 导辊运转不灵活 (3) 压印胶辊配置不当,运转不灵活 (4) 除静电刷、除静电带损坏或表面不清洁
(1)静电须
(2)印刷不匀
(3)静电吸附灰尘
(5) 防静电接地装置不良 除静电刷、除静电带安装位置不当,或联线 不当或接地电阻大 车间空气未过滤或环境卫生差,车间地面未 做防尘处理
2
(4)间隙性刀线 (6) (7) (5)收卷不齐
(6)印品粘连
(8) 印机冷却效果不良,薄膜表面温度高 (9) 磨擦产生静电,重点是导辊及压印胶辊 (10) 收卷时,薄膜表面温度高,累积静电大