汽车内饰材料性能及试验方法
SJ-NW-101-2011汽车塑料内饰件耐刮擦实验方法(划格法)

编号SJ-NW-101-2011代替密级商密3级▲重庆长安汽车股份有限公司内部技术规范汽车塑料内饰件耐刮擦试验方法(划格法)2011-04-22制订 2011-6-25发布长安汽车工程研究院前言本规范规定了采用十字划格法评价汽车塑料内饰件耐刮擦性的实验程序,目的是为评价内饰件的耐刮擦性提供依据。
本规范由汽车工程研究院车身所负责起草;本规范由汽车工程研究院项目处进行管理和解释;本规范主要起草人员:傅强、赖礼汇、王晓编制: 傅 强校核: 赖礼汇审定: 王 晓批准: 曹 渡本规范的版本记录和版本号变动与修订记录版本号制定/修订者制定/修订日期批准日期傅强2011-4-22汽车塑料内饰件耐刮擦实验方法(划格法)1 适用范围本规范规定了采用十字划格法评价汽车塑料内饰件耐刮擦性的实验程序。
本规范适用于重庆长安汽车股份有限公司所开发车型的塑料内饰可见塑料零件。
本规范不适用于塑料表面喷涂的零件。
2 规范性引用文件下列文件中的条款通过本规范的引用而成为本规范的条款。
凡是注日期的引用文件,其随后所有的修改单(不包括勘误的内容)或修订版均不适用于本规范,凡是不注日期的引用文件,其最新版本适用于本规范。
ISO 7724 Paints and Varnishes- Colorimetry3 试验仪器及辅助设备划格仪器(比如:马达驱动十字划格工具,Erichen,430型)刮擦针:带球形末端的圆柱状硬金属针(直径:(1±0.01)mm)分光测色仪:满足ISO 7724的标准。
测量几何:d/8o光源类型:D65标准光源注1:不得使用超过20000次刮擦头进行试验。
注2:测量时不包括镜面光。
4 样品测试样品应从产品上切取,形状应尽量平整,保证试样与固定台面及测色仪平面保持均匀接触,试样尺寸应足以在表面形成40mm以上划痕。
样品表面应保持完好,不得存在划痕、污渍、油脂等。
用于首件认可时,应至少测试3个试样。
用于常规质量控制时,至少测试1个样品。
GB8410-2006汽车内饰标准.
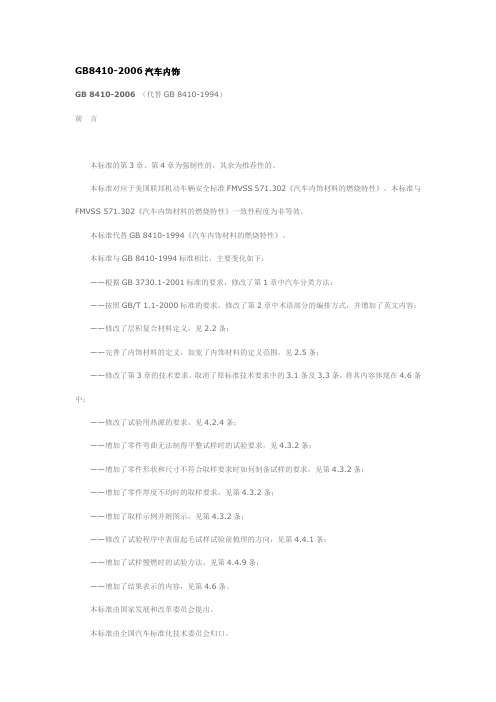
GB8410-2006汽车内饰GB 8410-2006(代替GB 8410-1994)前言本标准的第3章、第4章为强制性的,其余为推荐性的。
本标准对应于美国联邦机动车辆安全标准FMVSS 571.302《汽车内饰材料的燃烧特性》,本标准与FMVSS 571.302《汽车内饰材料的燃烧特性》一致性程度为非等效。
本标准代替GB 8410-1994《汽车内饰材料的燃烧特性》。
本标准与GB 8410-1994标准相比,主要变化如下:——根据GB 3730.1-2001标准的要求,修改了第1章中汽车分类方法;——按照GB/T 1.1-2000标准的要求,修改了第2章中术语部分的编排方式,并增加了英文内容;——修改了层积复合材料定义,见2.2条;——完善了内饰材料的定义,加宽了内饰材料的定义范围,见2.5条;——修改了第3章的技术要求,取消了原标准技术要求中的3.1条及3.3条,将其内容体现在4.6条中;——修改了试验用热源的要求,见4.2.4条;——增加了零件弯曲无法制得平整试样时的试验要求,见4.3.2条;——增加了零件形状和尺寸不符合取样要求时如何制备试样的要求,见第4.3.2条;——增加了零件厚度不均时的取样要求,见第4.3.2条;——增加了取样示例并附图示,见第4.3.2条;——修改了试验程序中表面起毛试样试验前梳理的方向,见第4.4.1条;——增加了试样慢燃时的试验方法,见第4.4.9条;——增加了结果表示的内容,见第4.6条。
本标准由国家发展和改革委员会提出。
本标准由全国汽车标准化技术委员会归口。
本标准由中国第一汽车集团公司技术中心负责起草。
本标准主要起草人:王清国、李菁华。
本标准所代替标准的历次版本发布情况为:——GB 8410-1987、GB 8410-1994。
GB 8410-2006汽车内饰材料的燃烧特性Flammability of automotive interior materials1 范围本标准规定了汽车内饰材料水平燃烧特性的技术要求及试验方法。
汽车内饰材料雾化标准解析(一)
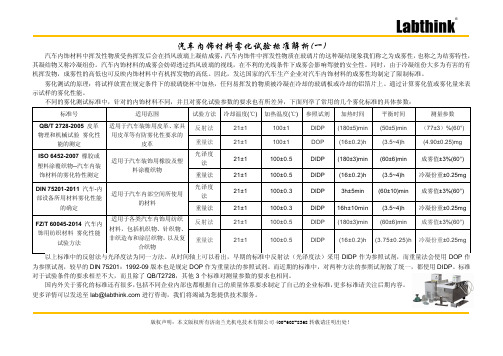
汽车内饰材料中挥发性物质受热挥发后会在挡风玻璃上凝结成雾, 汽车内饰件中挥发性物质在玻璃片的这种凝结现象我们称之为成雾性, 也称之为结雾特性, 其凝结物又称冷凝组份。汽车内饰材料的成雾会妨碍透过挡风玻璃的视线,在不利的光线条件下成雾会影响驾驶的安全性。同时,由于冷凝组份大多为有害的有 机挥发物,成雾性的高低也可反映内饰材料中有机挥发物的高低。因此,发达国家的汽车生产企业对汽车内饰材料的成雾性均制定了限制标准。 雾化测试的原理:将试样放置在规定条件下的玻璃烧杯中加热,任何易挥发的物质被冷凝在冷却的玻璃板或冷却的铝箔片上。通过计算雾化值或雾化量来表 示试样的雾化性能。 不同的雾化测试标准中,针对的内饰材料不同,并且对雾化试验参数的要求也有所差异,下面列举了常用的几个雾化标准的具体参数:
版权声明:本文版权所有济南兰光机电技术有限公司 400-608-8368 转载请注明出处!
ቤተ መጻሕፍቲ ባይዱ
以上标准中的反射法与光泽度法为同一方法。从时间轴上可以看出,早期的标准中反射法(光泽度法)采用 DIDP 作为参照试剂,而重量法会使用 DOP 作 为参照试剂,较早的 DIN 75201:1992-09 版本也是规定 DOP 作为重量法的参照试剂。而近期的标准中,对两种方法的参照试剂做了统一,都使用 DIDP。标准 对于试验条件的要求相差不大,而且除了 QB/T2728,其他 3 个标准对测量参数的要求也相同。 国内外关于雾化的标准还有很多, 包括不同企业内部也都根据自己的质量体系要求制定了自己的企业标准, 更多标准请关注后期内容。 更多详情可以发送至 lab@ 进行咨询,我们将竭诚为您提供技术服务。
标准号 QB/T 2728-2005 皮革 物理和机械试验 雾化性 能的测定 ISO 6452-2007 橡胶或 塑料涂覆织物--汽车内装 饰材料的雾化特性测定 DIN 75201-2011 汽车-内 部设备所用材料雾化性能 的确定 FZ/T 60045-2014 汽车内 饰用纺织材料 雾化性能 试验方法 适用范围 适用于汽车装饰用皮革、 家具 用皮革等有防雾化性要求的 皮革 适用于汽车装饰用橡胶及塑 料涂覆织物 重量法 光泽度 法 重量法 光泽度 适用于汽车内部空间所使用 的材料 适用于各类汽车内饰用纺织 材料,包括机织物、针织物、 非织造布和涂层织物, 以及复 合织物 重量法 21± 1 100± 0.5 DIDP (16±0.2)h (3.75±0.25)h 冷凝份重±0.25mg 法 重量法 反射法 21± 1 21± 1 21± 1 21± 1 21± 1 21± 1 100± 1 100± 0.5 100± 0.5 100± 0.3 100± 0.3 100± 0.5 DOP DIDP DIDP DIDP DIDP DIDP (16±0.2)h (180±3)min (16±0.2)h 3h±5min 16h± 10min (180±3)min (3.5~4)h (60±6)min (3.5~4)h (60±10)min (3.5~4)h (60±6)min (4.90±0.25)mg 成雾值±3%(60°) 冷凝份重±0.25mg 成雾值±3%(60°) 冷凝份重±0.25mg 成雾值±3%(60°) 试验方法 反射法 冷却温度(℃) 21± 1 加热温度(℃) 100± 1 参照试剂 DIDP 加热时间 (180±5)min 平衡时间 (50±5)min 测量参数 (77±3)%(60°)
GB8410-2006标准—适用车辆内饰

GB 8410-2006汽车内饰材料的燃烧特性Flammability of automotive interior materials1 范围本标准规定了汽车内饰材料水平燃烧特性的技术要求及试验方法。
本标准适用于汽车内饰材料水平燃烧特性的评定。
鉴于各种汽车内饰零件实际情况(零件应用部位、布置方法、使用条件、引火源等)和本标准中规定的试验条件之间有许多差别,本标准不适用于评价汽车内饰材料所有真实的车内燃烧特性。
2 术语和定义2.1燃烧速度 burning rate按本标准规定测得的燃烧距离与燃烧此距离所用时间的比值,单位为毫米每分钟(mm/min)。
2.2层积复合材料 composite material若干层相似或不同材料,其表面之间由熔接、粘接、焊接等不同方法使全面紧密结合在一起的材料。
2.3单一材料 exclusive material由同种材料构成的均匀的整体材料。
若不同材料断续连接在一起(例如缝纫、高频焊接、铆接),这种材料应认为不是层积复合材料,每种材料均属单一材料。
2.4暴露面 exposed side零件装配在车内面向乘员的那一面。
2.5内饰材料 interior materials汽车内饰零件所用的单一材料或层积复合材料,如座垫、座椅靠背、座椅套、安全带、头枕、扶手、活动式折叠车顶、所有装饰性衬板(包括门内护板、侧围护板、后围护板、车顶棚衬里)、仪表板、杂物箱、室内货架板或后窗台板、窗帘、地板覆盖层、遮阳板、轮罩覆盖物、发动机罩覆盖物和其他任何室内有机材料,包括撞车时吸收碰撞能量的填料、缓冲装置等材料。
3 技术要求内饰材料的燃烧特性必须满足以下技术要求:燃烧速度不大于100 mm/min。
4 试验方法4.1 原理将试样水平地夹持在U形支架上,在燃烧箱中用规定高度火焰点燃试样的自由端15s 后,确定试样上火焰是否熄灭,或何时熄灭,以及试样燃烧的距离和燃烧该距离所用时间。
4.2 试验装置及器具4.2.1 燃烧箱燃烧箱用钢板制成,结构示意图见图1,尺寸见图2。
汽车研发:车内气味性评价及试验方法!
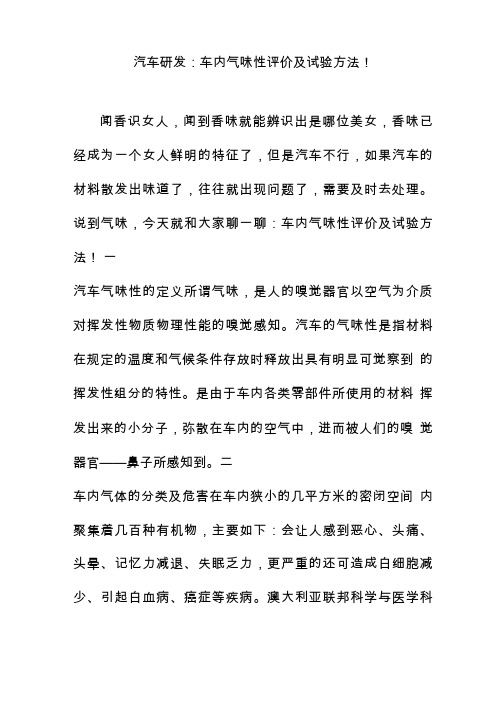
汽车研发:车内气味性评价及试验方法!闻香识女人,闻到香味就能辨识出是哪位美女,香味已经成为一个女人鲜明的特征了,但是汽车不行,如果汽车的材料散发出味道了,往往就出现问题了,需要及时去处理。
说到气味,今天就和大家聊一聊:车内气味性评价及试验方法!一汽车气味性的定义所谓气味,是人的嗅觉器官以空气为介质对挥发性物质物理性能的嗅觉感知。
汽车的气味性是指材料在规定的温度和气候条件存放时释放出具有明显可觉察到的挥发性组分的特性。
是由于车内各类零部件所使用的材料挥发出来的小分子,弥散在车内的空气中,进而被人们的嗅觉器官——鼻子所感知到。
二车内气体的分类及危害在车内狭小的几平方米的密闭空间内聚集着几百种有机物,主要如下:会让人感到恶心、头痛、头晕、记忆力减退、失眠乏力,更严重的还可造成白细胞减少、引起白血病、癌症等疾病。
澳大利亚联邦科学与医学科研部门测试发现,新车出厂后车内有害气体浓度很高,挥发时间甚至可持续6个月以上。
另外,有研究表明,由驾车综合症引发的交通事故远比疲劳驾驶、酒后驾驶引发的事故多,车内空气污染问题已经影响到驾驶员的安全驾驶。
三散发气味的主要零部件散发气味的车内零部件有很多种,主要零部件如下:这些零部件所使用的材料又包含了各类塑料、织物、皮革、油脂及粘胶等,它们所散发出来的气味也不尽相同,这些气味混合在一起,所以很难轻易判断出所闻到气味的来源。
座椅顶棚地毯仪表板车门护板四车内气体的评价原理及方法1、嗅觉原理车内气味检测主要依靠嗅觉器官——鼻子来感受,由检测者进行主观评价,得到测量结果。
人类嗅觉感知的机理是:气味物质分子在空气中扩散,由鼻腔收容之后,并与嗅神经相接触,然后将情报传达到大脑,于是就产生了气味感。
2、气味强度气味强度,是将气味对人的嗅觉器官不同的刺激程度分成若干等级,便于对气味评价的结果进行量化。
例如,6级气味强度等级表示法,强度等级数值越高,表示刺激程度越强烈。
A、进行评价时,鉴定人员首先应判断出气味是否有干扰性。
汽车内饰物燃烧标准

汽车内饰件阻燃标准等级汽车内饰阻燃标准主要由国家或汽车制造商发布,其中大部分标准的测试方法都是比较接近,主要关注内饰材料的易燃性和燃烧速率,只要不超过一定的燃烧速率(一般为102mm/min)时,都是允许在汽车内使用的。
取样测试的部位为汽车内暴露面向下13mm内的单层或者复合层材料,若每层可以分离则需要单独测试。
内饰材料燃烧标准GB8410 - 汽车内饰材料的燃烧特性。
GB8410标准规定了汽车内饰材料水平火钳特性的技术要求及试验方法。
GB8410标准适用于汽车内饰材料水平燃烧特性的评定。
内饰材料不燃烧、可以燃烧但燃烧速度不大于100mm/min、火焰在60s内自行熄灭且燃烧距离不大于50mm。
燃烧速度:测得的燃烧距离与燃烧此距离所用时间的比值,单位为毫米每分钟(mm/min)。
从保证乘员安全的角度来讲,不燃烧当然是最好,而燃烧速度能够靠材料本身保证在一定的范围之内,也可以为乘员提供一定的生存时间和逃生的时间。
在实际的试验操作过程中,是以在规定时间内不能引燃或在第一个标志柱之前自行熄灭的视为不燃烧。
汽车内饰材料阻燃标准FMVSS302主要适用于汽车内饰材料的阻燃测试,UL94是广泛适用于塑料材料的阻燃测试。
针对产品用途范围不一样,且测试方法和要求也不一样。
不易燃。
医用防护服采用不易燃材料,并且离开火焰后燃烧不大于5s,该项目可以采用ZYYQ阻燃性能测试仪设备进行测试,ZYYQ阻燃性能测试仪智能化程度高,符合国家标准GB/T5455-1997《纺织品燃烧性能试验垂直法》,可用于有阻燃要求的服装织物、装饰织物、帐篷织物等阻燃性能的测定。
阻燃海绵由于含可燃的碳氢链段、密度小、比表面积大,未经阻燃处理的聚氨酯海绵是可燃物,遇火会燃烧并分解,产生大量的烟雾,给灭火带来困难。
特别是聚氨酯软泡开孔率较高,可燃成分多,燃烧时由于较高的空气流通性而源源不断地供给氧气,易燃且不易自熄。
聚氨酯海绵的许多应用领域非常广泛,如建筑材料、床垫、家具、保温材料、汽车座垫及内饰材料等,都需达到阻燃要求。
汽车内饰零部件材料VOC与气味检测介绍

444 测试流程
清洗采样袋
样品充气
气体培养
采集气体
上机分析
44441 清洗采样袋
1 密封采样袋 4 填充氮气
4 抽除气体, 抽除气体,重复多次
4 加热
44444 样品充气
1 将采样袋剪去一角 2 放置样品
4 充入氮气
3 密封采样袋
44444 采样袋法- 采样袋法-气体培养
1预先将恒温箱加热。 预先将恒温箱加热 2 装有样品的采样袋放入恒温箱, 装有样品的采样袋放入恒温箱, 布置好配管, 布置好配管,恒温加热
准备阶段
封闭阶段
在受检车辆内安装好采样装置, 在受检车辆内安装好采样装置,完全关闭受检 车辆所有窗、 车辆所有窗、门,不破坏整车的密封性。 不破坏整车的密封性。 将受检车辆保持封闭状态 16h,开始进行样品 采集; 采集;
144 车内空气测试方法-采样点设置
144 车内空气测试方法-分析条件
采样管: 采样管:Tenax管 采样流量: 采样流量:100~200ml/min 采样时间: 采样时间:30min 分析仪器: 分析仪器:ATD-GCMS
444 零部件及采样袋的选用
序号 1 2 3 4 5 6 7 8 9 10 11 12 13 14 15 16 17 样品名称 隔音垫(再生棉) 阻尼板 方向盘 地板隔音垫(发泡材料) 遮阳板 仪表板线束总成 整车密封条 车门内饰板总成 行李舱隔板装饰板总成 行李舱地毯总成 前围隔音垫总成 仪表板上罩总成 地毯总成 顶棚 前排座椅总成 后排座椅总成 其他 样袋型号 10L 10L 50L 50L 50L 100L 500L 500L 500L 1000L 1000L 1000L 2000L 2000L 1000L 2000L 10L 切割为20cm×10cm的试验片 切割为10cm×10cm的试验片 暴露面朝上 取样200g 左遮阳板总成+右遮阳板总成,放入袋中 尽量摊开 4根车门框密封条+4根车门密封条总成,一起放入袋中 暴露面朝上 暴露面朝上 暴露面朝上 毛毡面或发泡面朝上 暴露面朝上 暴露面朝上 暴露面朝上 左或右座椅总成均可,取其一 后排靠背+坐垫,放入一个袋中,暴露面朝上 视样件状态,整体放入袋中,或取样100g,或取样10cm×10cm 备 注
汽车座椅PU涂层织物马丁代尔法耐磨性测试方法

汽车座椅PU涂层织物马丁代尔法耐磨性测试方法汽车座椅用涂层织物耐磨性的MIE测试法具有耗时和摩擦路线单一的缺点,拟用马丁代尔(MARTINDALE)测试法予以替代。
对两种测试方法进行了比较,结果表明,后者不仅可以提高测试的效率,而且测试结果的准确性也有不同程度的提高。
采用MARTINDALE测试法,试验次数达400次时,试样表面光泽度变化明显,可以据此快速评价PU合成革的耐磨性;试验次数达1 600次后,试样表面光泽度变化基本稳定,可以将该试验次数设置为耐磨性指标的标准测试次数。
另外,摩擦介质的选择将影响PU合成革耐磨性的测试结果。
一、前言涂层织物(以下称合成革)是现代汽车座椅设计中经常采用的三大柔性材料之一,具有近似天然真皮的外观。
由于天然真皮资源有限、价格高、加工过程的环保要求高,因此各大汽车生产商纷纷研发汽车内饰用合成革,其中的PU涂层织物是目前最常见的汽车内饰用合成革材料。
耐磨性是评价汽车座椅用PU合成革性能的主要指标之一,现行的测试座椅用合成革耐磨性的方法为MIE耐磨性测试法,多被法国汽车企业采用,摩擦方式为“往返式双向摩擦”,测试时间可分为8、12和16 h。
由于这种测试方法具有耗时久、摩擦路线单一等缺陷,摩擦效果不理想,因此应寻找一种更有效的耐磨性测试替代方法,以期达到更好的测试效果。
由于MIE耐磨性测试和MARTINDALE(以下简称MAR)耐磨性测试最初都用于织物起毛/起球性的测试,两者均采用标准羊毛织物作为摩擦介质,而MAR耐磨性测试法在织物起毛/起球的试验中具有非常好的测试效果。
例如,MAR测试仪可同时测试多件试样,有利于提高测试效率;另外,试样与摩擦介质之间为低压持续换向摩擦,摩擦相对轨迹为Lissajous轨迹,使得试样各处受摩擦的几率相同,摩擦方向均匀。
基于MAR耐磨性测试法的优势,本文将探索用MAR测试法替代MIE测试法测试汽车座椅用合成革耐磨性的可行性。
二、试验及结果评价汽车座椅用合成革耐磨性的参数为由表面磨损而引起的合成革表面光泽度的变化。