特种加工技术
特种加工技术的特点及应用
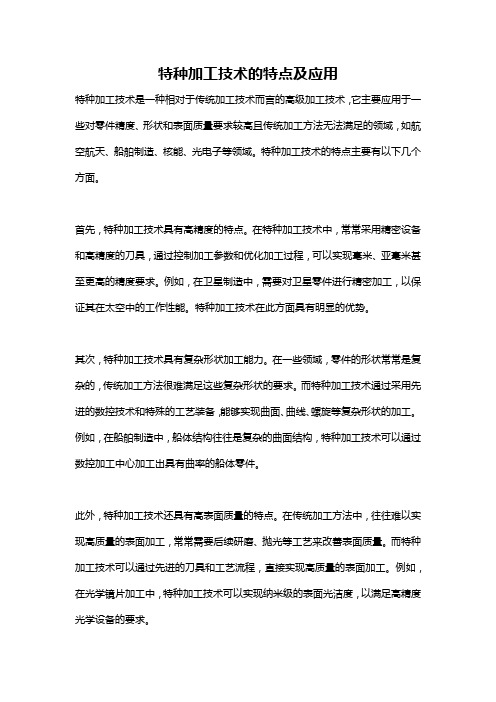
特种加工技术的特点及应用特种加工技术是一种相对于传统加工技术而言的高级加工技术,它主要应用于一些对零件精度、形状和表面质量要求较高且传统加工方法无法满足的领域,如航空航天、船舶制造、核能、光电子等领域。
特种加工技术的特点主要有以下几个方面。
首先,特种加工技术具有高精度的特点。
在特种加工技术中,常常采用精密设备和高精度的刀具,通过控制加工参数和优化加工过程,可以实现毫米、亚毫米甚至更高的精度要求。
例如,在卫星制造中,需要对卫星零件进行精密加工,以保证其在太空中的工作性能。
特种加工技术在此方面具有明显的优势。
其次,特种加工技术具有复杂形状加工能力。
在一些领域,零件的形状常常是复杂的,传统加工方法很难满足这些复杂形状的要求。
而特种加工技术通过采用先进的数控技术和特殊的工艺装备,能够实现曲面、曲线、螺旋等复杂形状的加工。
例如,在船舶制造中,船体结构往往是复杂的曲面结构,特种加工技术可以通过数控加工中心加工出具有曲率的船体零件。
此外,特种加工技术还具有高表面质量的特点。
在传统加工方法中,往往难以实现高质量的表面加工,常常需要后续研磨、抛光等工艺来改善表面质量。
而特种加工技术可以通过先进的刀具和工艺流程,直接实现高质量的表面加工。
例如,在光学镜片加工中,特种加工技术可以实现纳米级的表面光洁度,以满足高精度光学设备的要求。
特种加工技术在各个领域有着广泛的应用。
在航空航天领域,特种加工技术可以用于加工各类航空零部件,如发动机叶片、涡轮盘、外壳等,以提高其精度和性能。
在船舶制造领域,特种加工技术可以用于加工船体结构零件,以满足船舶的航行性能和安全要求。
在核能领域,特种加工技术可以用于加工核电站的核电设备和核材料,以确保核安全和生产效率。
在光电子领域,特种加工技术可以用于加工光学镜头、激光器件等光学设备,以提高其精度和性能。
总之,特种加工技术作为一种高级加工技术,具有高精度、复杂形状和高表面质量的特点,在航空航天、船舶制造、核能、光电子等领域有着广泛的应用。
浅谈特种加工技术及其应用(论文)
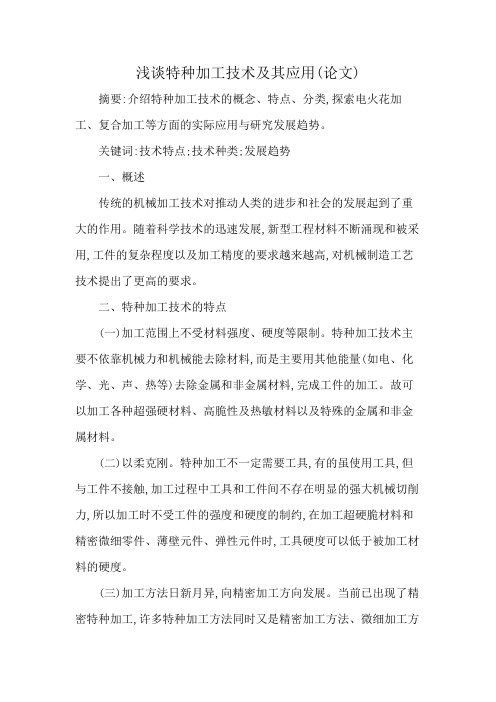
浅谈特种加工技术及其应用(论文)摘要:介绍特种加工技术的概念、特点、分类,探索电火花加工、复合加工等方面的实际应用与研究发展趋势。
关键词:技术特点;技术种类;发展趋势一、概述传统的机械加工技术对推动人类的进步和社会的发展起到了重大的作用。
随着科学技术的迅速发展,新型工程材料不断涌现和被采用,工件的复杂程度以及加工精度的要求越来越高,对机械制造工艺技术提出了更高的要求。
二、特种加工技术的特点(一)加工范围上不受材料强度、硬度等限制。
特种加工技术主要不依靠机械力和机械能去除材料,而是主要用其他能量(如电、化学、光、声、热等)去除金属和非金属材料,完成工件的加工。
故可以加工各种超强硬材料、高脆性及热敏材料以及特殊的金属和非金属材料。
(二)以柔克刚。
特种加工不一定需要工具,有的虽使用工具,但与工件不接触,加工过程中工具和工件间不存在明显的强大机械切削力,所以加工时不受工件的强度和硬度的制约,在加工超硬脆材料和精密微细零件、薄壁元件、弹性元件时,工具硬度可以低于被加工材料的硬度。
(三)加工方法日新月异,向精密加工方向发展。
当前已出现了精密特种加工,许多特种加工方法同时又是精密加工方法、微细加工方法,如电子束加工、离子束加工、激光束加工等就是精密特种加工:精密电火花加工的加工精密度可达微米级0.5~1um,表面粗糙度可达镜面Ra0.021.1m。
(四)容易获得良好的表面质量。
由于在加工过程中不产生宏观切屑,工件表面不会产生强烈的弹、塑性变形,故可以获得良好的表面粗糙度。
残余应力、热应力、冷作硬化、热影响区及毛刺等表面缺陷均比机械切割表面小,尺寸稳定性好,不存在加工中的机械应变或大面积的热应变。
特种加工的主要应用范围有1.加工各种难切削材料。
如硬质合金、钛、合金、耐热钢、不锈钢、淬硬钢、金刚石、红宝石、石英以及锗、硅等各种高硬度、高强度、高韧性、高熔点的金属及非金属材料。
2.加工各种特殊复杂零件的三维型腔、型孔、群孔和窄缝等。
特种加工技术

机 械 工 程 导 论
第五节
超声波加工
二、超声波加工的特点、方法及应用 1、超声波加工适合于加工各种脆硬材料,材料越是脆硬,越适宜 超声波加工; 2、超声波可用于加工薄壁、薄片等易变形零件,加工精度高; 3、超声波加工设备简单,但生产效率低。
加工方法可采用超声波直接加工、超声波旋转加工、超声 波机械复合加工、超声波焊接、涂覆、清洗等。
机 械 工 程 导 论
第三节
电解加工
电解加工有叫电化学加工, 包括从工件上去除金属的电解 加工和向工件上沉积金属的电 镀、涂覆加工两大类 一、电解加工的基本原理 二、电解加工的基本概念 生产率、极间间隙、电解 液、加工精度和表面质量
机 械 工 程 导 论
第三节
电解加工
三、电解加工的特点、方法和应用
一、激光加工的基本原理
机 械 工 程 导 论
第四节
激光加工
二、激光加工的特点、方法及应用
1.可以加工各种金属材料和非金属材料; 2.激光加工不需要工具,易实现加工过程自动化; 3.激光可透过玻璃等材料对工件进行加工; 4.可以实现精密微细加工; 5.激光可以进行表面热处理、焊接、切剖、打孔、雕刻 及微细加工等多种加工。
机 械 工 程 导 论
第十四章 特种加工
第一节 概 述
特种加工是指采用电能、化学能、光能、卢能、热能、 以及电子、离子等不同能源,区别于传统的切削加工方法, 也称为非传统加工。
常用特种加工方法有:电火花加工、电 解加工、激光加工、超声波加工、电子束加工、 离子束加工等。
机 械ห้องสมุดไป่ตู้工 程 导 论
第二节
电火花加工
电火花加工是模具加工的重要方法,常用的有电火花 成形和电火花线切割两种。
特种加工技术

特种加工技术1. 引言特种加工技术是指在工业生产过程中,利用先进的加工设备和工艺,对特殊材料或特殊形状的零件进行加工加工的技术方法。
特种加工技术在许多领域中都有广泛的应用,如航空航天、汽车制造、船舶建造等。
本文将介绍几种常见的特种加工技术,包括电火花加工、激光加工以及电化学加工。
2. 电火花加工电火花加工是一种利用电火花放电来进行加工的技术。
该技术主要用于加工高硬度和脆性材料,如硬质合金、陶瓷等。
其工作原理是利用高压脉冲电流在工件表面产生电火花放电,从而烧蚀掉工件表面的材料。
通过控制放电的时间和能量,可以实现对工件的精细加工。
电火花加工具有以下几个优点: - 能够加工高硬度和脆性材料; - 加工过程中不会产生机械应力; - 可以实现复杂形状的加工。
然而,电火花加工也存在一些限制:- 加工效率相对较低;- 加工精度受到局限。
3. 激光加工激光加工是利用高能量密度的激光束对工件进行加工的技术。
激光加工可以通过烧蚀、熔化、汽化等方式来剥离工件表面的材料。
激光加工具有以下几个特点: - 高加工精度和加工质量; - 高加工速度; - 可以实现对不同材料的加工。
激光加工在航空航天、汽车制造等领域有广泛的应用。
例如,在飞机制造中,激光加工可以用于切割、焊接、打孔等工艺操作。
激光加工的应用还面临一些挑战: - 高能量激光设备的成本较高; - 对工件材料的适应性有限。
4. 电化学加工电化学加工是利用电化学反应对工件进行加工的技术。
它通过在电解液中施加电压,使得工件表面发生氧化、溶解等反应,从而实现加工目的。
电化学加工具有以下优点: - 加工精度高; - 加工过程中不会产生机械应力; - 可以加工高硬度和脆性材料;电化学加工主要用于微小零件加工、细微结构加工、薄板加工等领域。
例如,在电子芯片制造中,电化学加工可以用于进行微细线路的蚀刻。
然而,电化学加工也存在一些限制: - 加工速度较慢; - 加工尺寸受到限制。
5. 总结特种加工技术在现代工业中起着重要作用。
特种加工技术的名词解释
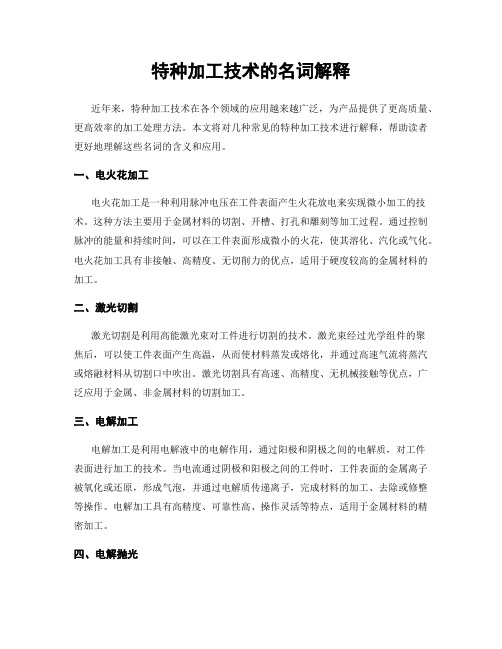
特种加工技术的名词解释近年来,特种加工技术在各个领域的应用越来越广泛,为产品提供了更高质量、更高效率的加工处理方法。
本文将对几种常见的特种加工技术进行解释,帮助读者更好地理解这些名词的含义和应用。
一、电火花加工电火花加工是一种利用脉冲电压在工件表面产生火花放电来实现微小加工的技术。
这种方法主要用于金属材料的切割、开槽、打孔和雕刻等加工过程。
通过控制脉冲的能量和持续时间,可以在工件表面形成微小的火花,使其溶化、汽化或气化。
电火花加工具有非接触、高精度、无切削力的优点,适用于硬度较高的金属材料的加工。
二、激光切割激光切割是利用高能激光束对工件进行切割的技术。
激光束经过光学组件的聚焦后,可以使工件表面产生高温,从而使材料蒸发或熔化,并通过高速气流将蒸汽或熔融材料从切割口中吹出。
激光切割具有高速、高精度、无机械接触等优点,广泛应用于金属、非金属材料的切割加工。
三、电解加工电解加工是利用电解液中的电解作用,通过阳极和阴极之间的电解质,对工件表面进行加工的技术。
当电流通过阴极和阳极之间的工件时,工件表面的金属离子被氧化或还原,形成气泡,并通过电解质传递离子,完成材料的加工、去除或修整等操作。
电解加工具有高精度、可靠性高、操作灵活等特点,适用于金属材料的精密加工。
四、电解抛光电解抛光是利用电解液对工件表面进行表面处理和研磨的技术。
在电解加工的基础上,通过调节电解液的组分和操作条件,使工件表面的金属离子在电流作用下发生氧化、析出或降解反应,从而实现对工件表面的平整化和光洁度的改善。
电解抛光广泛应用于不锈钢等材料的表面处理,可提高材料的光洁度和抗腐蚀性能。
五、真空蒸镀真空蒸镀是利用高真空环境下的热蒸发或电子束蒸发技术,使金属材料蒸发并沉积在工件表面的一种技术。
在真空腔体中,通过加热金属源或电子束轰击金属源,使金属原子蒸发,并在工件表面沉积,形成一层均匀、致密的金属膜。
真空蒸镀广泛应用于镜面、陶瓷、塑料等材料的表面覆盖和装饰,提供了高光洁度、高硬度和防腐蚀等性能。
特种加工技术

•2.特种加工的产生•特种加工早期的发明和应用是在1943年由前而生产和科学研究中提出来的新问题又促进了特种加工方法的迅速发展。
3、对零件的结构设计带来重大变革。
喷气发钢片冲模,结构复杂不易制造,往往采用拼程如图1-2所示。
加工必要条件(之一)必须使工具与工件被加工表面之间经常保持一定的放电间隙,这一间隙视加工条件而定,一般为几微米至几百微米之间。
若间隙过大,极间电压不能击穿极间介质,不能产生火花放电;若间隙过小,很容易液体介质的作用)有利于产生脉冲性的火花放电;型腔多为盲孔,内形复杂,各处深浅不同,加工较为困难。
为了便于排除加工产物和冷而且避免了小直径钻电解产物则不断被高速流动的电解液带走,最终工具电极的形状就“复制”在工件上。
电解中常用的电解液有NaCl、NaNO3和NaClO 三种溶液。
下面仅介绍用10%~20%的氯化钠水溶液作电解液加工低碳钢时的主要化学反应:水溶液H2O H++OH-阳极反应Fe–2e Fe+²3.电解去毛刺机械加工中常采用钳工方法去毛刺,这不但工作量大,而且有的毛刺因过硬或空间狭小难以去除。
而采用电解去毛刺,则可以提高工效,节约费用。
图1-24所示,为采用电解一.超声波加工的原理及特点超声波加工原理超声波加工是利用工具端面的超声频振动,和局部真空形成许多微空腔。
超声波加工适用于加工各种硬脆材料,尤其是利用电火花加工、电解加工难以加工的不刻和研抛等,如图1-26所示。
一定值时,产生的微冲击就可以使被清洗物表面的污渍遭到破坏而脱落下来。
加上超声作用无处不入,即使是小孔和窄缝可焊接性。
由于它利用高能光束进行加工,加工速度快,变形小,可以加工各种金属和非金属材料,在生产实践中不断显示出它的优越性,因而当激光的工作物质釔铝石榴石受到光泵(激励脉冲氙灯)的激发后,吸收具有特定波长的光,间的能量差来决定,即:时处于高能级E N 的粒子才会在这个外来光子的刺激下向低能级E 同时辐射出一个频率、传播方向、振动方向均与外来光子完全相同的光子深为0.6~1.2mm的宝石轴承孔,若工件自动传送,每分钟可加工数十件。
《特种加工》课件

05
特种加工技术的发
展趋势与展望
特种加工技术发展趋势
高能束流加工
随着激光、电子束、离子束等高能束流技术的不断发展,其在特种加工领域的应用越来越广泛。高能束流加工具有高 精度、高效率、非接触等优点,可应用于难加工材料的加工和微纳制造等领域。
超声加工与振动加工
超声加工和振动加工技术以其独特的加工原理和特点,在微细加工、表面处理等领域具有广泛的应用前景。通过优化 超声频率、振动幅度等参数,可进一步提高加工精度和效率。
特种加工工艺参数
04
与控制
电火花加工工艺参数与控制
要点一
总结词
要点二
详细描述
电火花加工是利用电火花放电产生的热量对金属进行加工 的一种工艺方法。
电火花加工工艺参数包括电极材料、工作液种类、电规准 选择、电极损耗、加工精度和表面粗糙度等。控制这些参 数可以提高加工效率、减小电极损耗、保证加工精度和表 面质量。
激光加工
总结词
利用激光的高能量密度对材料进行切割、打孔、焊接等加工
详细描述
激光加工是一种利用激光的高能量密度对材料进行切割、打孔、焊接等加工的方 法。由于激光的能量集中,可以在短时间内对材料进行高精度的加工,且加工速 度快、效率高。激光加工在微电子、光学、精密制造等领域应用广泛。
离子束加工
总结词
电化学加工与等离子体加工
电化学加工和等离子体加工技术以其环保、高效的特点,在模具制造、表面处理等领域得到广泛应用。 随着技术的不断进步,电化学加工和等离子体加工的加工精度和适用范围将得到进一步提升。
特种加工技术面临的挑战与机遇
技术更新换代
随着新材料、新工艺的不断涌现 ,特种加工技术面临着不断更新 换代的挑战。为了适应市场需求 和技术发展,需要不断进行技术 创新和研发。
特种加工技术总结

特种加工技术总结引言特种加工技术是指利用特殊的加工方法和工艺,对特定材料进行处理、加工和改性的技术手段。
随着科技的发展和工业的进步,特种加工技术得到了广泛的应用和发展。
本文将对几种常见的特种加工技术进行总结和介绍。
1. 表面处理技术表面处理技术是一种通过改变材料表面的特性和性能,来满足特定要求的加工方法。
常见的表面处理技术包括:1.1. 电镀技术电镀是利用电解反应将一层金属沉积在材料表面的一种加工方法。
通过电镀可以提高材料的耐腐蚀性、硬度和光泽度。
常见的电镀技术有镀铬、镀镍、镀金等。
1.2. 涂层技术涂层技术是将一层涂料或薄膜覆盖在材料表面的一种加工方法。
通过涂层可以增加材料的耐磨性、耐腐蚀性和防护性能。
常见的涂层技术有喷涂、浸涂、喷淋等。
1.3. 氮化处理氮化处理是将材料暴露在氮气或含氮气体环境中,利用化学反应使材料表面形成一层氮化物的加工方法。
氮化处理可以提高材料的硬度、耐磨性和耐蚀性。
常见的氮化处理方法有氮气渗透、离子氮化等。
2. 热处理技术热处理技术是通过控制材料的加热和冷却过程,改变材料的组织结构和性能的加工方法。
常见的热处理技术包括:2.1. 淬火淬火是将材料加热到适当的温度,然后迅速冷却,使材料形成马氏体或贝氏体的加工方法。
通过淬火可以提高材料的硬度和强度,但也会使材料变脆。
常见的淬火方法有油淬、水淬等。
2.2. 回火回火是将经过淬火处理的材料加热到适当的温度,然后缓慢冷却的加工方法。
通过回火可以减轻材料的脆性和内应力,提高材料的韧性和强度。
常见的回火方法有低温回火、中温回火等。
2.3. 焊后热处理焊后热处理是将焊接接头进行热处理的加工方法,旨在消除焊接产生的应力和改善接头性能。
常见的焊后热处理方法有焊接后回火、焊后退火等。
3. 精密加工技术精密加工技术是一种通过高精度的设备和控制手段,对材料进行精细和精确的加工的技术。
常见的精密加工技术包括:3.1. 放电加工放电加工是利用电脉冲进行烧蚀和加工的一种高精度加工方法。
- 1、下载文档前请自行甄别文档内容的完整性,平台不提供额外的编辑、内容补充、找答案等附加服务。
- 2、"仅部分预览"的文档,不可在线预览部分如存在完整性等问题,可反馈申请退款(可完整预览的文档不适用该条件!)。
- 3、如文档侵犯您的权益,请联系客服反馈,我们会尽快为您处理(人工客服工作时间:9:00-18:30)。
1、切削加工的本质和特点:一是靠刀具材料比工件更硬;二是靠机械能把工件上多余的材料切除。
2、特种加工的特点是:1)不是主要依靠机械能,而是主要用其他能量(如电、化学、光、声、热等)去除金属材料;2)工具硬度可以低于被加工材料的硬度;3)加工过程中工具和工件之间不存显著的机械切削力。
3、特种加工的加工范围:可以加工任何硬度、强度、韧性、脆性的金属或非金属材料,且专长于加工复杂、微细表面和低刚度零件,同时,有些方法还可用于进行超精加工镜面光整加工和纳米加工。
4、特种加工对材料可加工性结构等的影响:1)提高了材料的可加工性。
2)改变了零件的典型工艺路线。
3)可以直接加工出各种标准和非标准直齿轮,微电机定子,转子硅钢片,各种变压器铁心,各种特殊、复杂的二次曲面体零件。
省去了设计和制造相应的刀、夹、量具;模具以及二次工具,大大缩短了试制周期。
4)特种加工对产品零件的结构设计带来很大的影响。
5)对传统的结构工艺性的好与坏需要重新衡量。
5、电火花加工的原理:1)必修使工具电极和工件被加工表面之间保持一定的放电间隙。
2)火花放电必须是瞬时的脉冲性放电,放电延续一段时间后,需停歇一段时间,放电延续时间一般为10 。
3)火花放电必须在有一定绝缘性能的液体介质中进行,例如煤油、皂化液或去离子水等。
6、电火花加工的特点:1、是不接触加工;工具电极和工件之间并不直接接触而有一个火花放电间隙,间隙中充满煤油工作液。
2、加工过程中没有宏观切削力;火花放电时,局部、瞬时爆炸力的平均值很小,不足以引起工件的变形和位移。
3、可以”以柔克刚”:由于电火花加工直接利用电能和热能来去除金属材料,与工件材料的强度和硬度等关系不大,因此可以用软的工具电极加工硬的工件,实现“以柔克刚”。
7、电火花加工机床的组成部分:
8、与一般电火花加工工艺相比较,采用平动头电火花加工有如下特点:1、它可以通过改变轨迹半径来调整电极的作用尺寸,因此尺寸加工不再受放电间隙的限制。
2、用同一尺寸的工具电极,通过轨迹半径的改变,可以实现换规准修整,即采用一个电极就能由粗至精直接加工出一副型腔。
3、在加工过程中,工具电极的轴线与工件的轴线相偏移,除了电极处于放点区域的部分外,工具电极与工件的间隙都大于放电间隙,实际上减小了同时放电的面积,这有利于电蚀产物的排除,提高加工稳定性。
4、工具电极相对于工件移动,可是加工的表面粗糙度大大改善,特别是底平面处。
5、由于有平动轨迹半径的存在,它无法加工有清角的型腔。
9、数控电火花线切割加工的基本原理:
10、数控电火花线切割加工的特点:1、不需要制造成形电极,用简单的电极丝即可对工件进行加工。
2、由于电极丝比较细,可以加工微细异型孔、窄缝和复杂形状的工件。
3)能加工各种冲模、凸轮、样板等外形复杂的精密零件,尺寸精度可达,表面粗糙度Ra值可达1.6um。
还可切割带斜度的模具或工件。
4、由于切缝很窄,切割时只对工件材料进行“套料”加工,故余料还可以利用。
5、自动化程度高,操作方便,劳动强度低。
6、加工周期短,成本低。
11、数控电火花线切割的应用范围:1、应用最广泛的是加工各类模具,包括切割上冲头(凸模)和下冲模(凹模)。
2、加工二维直纹曲面的零件。
3、加工三维直纹曲面的零件。
4、各种导电材料和半导体材料以及稀有贵重金属的切断。
5、加工微细槽、任意曲线窄缝。
12、数控线切割加工的主要工艺指标:1、切割速度2、表面粗糙度3、放电间隙4、加工精度5、电极丝损耗量
13、影响电火花线切割加工的因素:1、工作液2、电极丝3、穿丝孔4、线切割工艺参数5、工件的装夹
14、电化学加工的原理:
15、电化学加工的分类:阳极电解蚀除和阴极电镀沉积加工。
阳极电解蚀除又因工艺方法的不同而分为电解加工、电解扩孔、电解抛光、电解去毛刺、电解磨削、电解研磨等。
阴极电镀沉积又因工艺的不同而分为装饰电镀、电铸、刷镀、复合电镀等。
16、电化学加工的特点:电化学加工是不接触加工,工具电极和工件之间存在着工作液;电化学加工过程无宏观切削力,为无应力加工。
电解加工为“减材”加工,可以用软的工具材料加工硬韧的工件,“以柔克刚”,因此可以加工复杂的立体成型表面。
由于电化学、电解作用是按原子、分子一层层进行的,因此可以控制极薄的去除层,进行微薄层加工,同时可以获得较好的表面粗糙度;
电镀、电铸为“增材”加工,按原子、分子逐层进行的,因此可以精密复制复杂精细的花纹表面,而且电镀、电铸、刷镀上去的材料,可以比原工件表面的材料有更好的硬度、强度、耐磨性极抗腐蚀性能等。
17、电化学加工的适用范围:电化学加工的适用范围,因电解和电镀两大类的不同而不同。
电解加工可以加工复杂成型模具和零件;电镀、电铸可以复制复杂、精细的表面,刷镀可以修复磨损的零件,改变原表面的物理性能,有很大的经济效益和社会效益。
18、金属的电化学当量和生产率的关系:用重量计M=KIt 用体积计V=wIt。
式中M:电极上溶解或析出物质的质量,V:电极上溶解或析出物质的体积, ;K:被电解物质的质量化学当量,;w:被电解物质的体积化学当量,;I:电解(电镀)电流,;t:电解(电镀)时间,h;
19、电解磨:对于小孔、深孔、薄壁筒等零件,可以采用电解磨。
电解磨的电参数可以在很大范围内变化,电压为3~30V,电流密度为0.2~1 .电解磨得生产率比普通磨高,表面粗糙度也得到改善。
20、电解研磨:把电解加工与机械研磨结合在一起,就够成了电解研磨。
电解研磨加工采用钝化型电解液,利用机械研磨去除表面微观各高点的钝化膜,使其露出基体金属并再次形成新的钝化膜,实现表面的镜面加工。
电解研磨按磨料是否粘固在弹性合成五纺布上可分为固定磨料加工和流动磨料加工两种。
21、电铸加工的原理:用可导电导电原模作阴极,用电铸材料(如纯铜做阳极,用电铸材料的金属盐(如硫酸铜)溶液作电铸镀液。
(有图,自己看吧亲们)。
22、电铸加工的特点:1)能准确、精密地复制复杂型面和细微纹路;2)能获得尺寸精度高、表面粗糙度小于Ra0.1um的复制品,同一原模生产的电铸件一致性极好;3)借助石膏、石蜡、环氧树脂等作为原模材料,可把复杂零件的内表面复制为外表面,外表面复制为内表面,然后再电铸复制,适应性广泛。
23、电铸加工主要应用范围:1)复制精细的表面轮廓花纹,如唱片模、工艺美术品模及纸币、证券、邮票的印刷版。
2)复制注塑用的模具、电火花型
腔加工用的电极工具。
3)制造复杂、高精度的空心零件和薄壁零件,如波导管、筛网、滤网、剃须刀网罩等。
4)制造表面粗糙度标准样块、反光镜、表盘、异型孔喷嘴等特殊零件。
24、刷镀的基本设备:1电源、镀笔、镀液及泵、回转台等。
25、复合镀的原理和分类:
原理:复合镀是在金属工件表面镀金属镍或钴的同时,将磨料作为镀层的一部分也一起镀到工件表面上去,故称为复合镀。
分类:1)作为耐磨层的复合镀。
2)制造切屑工具的复合镀或锒嵌镀。
26、超声波加工的基本原理:(亲爱的,有图,靠自己啦哈)。
27、超声波加工的特点:1)适合于加工各种脆硬材料。
2)由于工具材料较软,易制成复杂的形状,工具和工件又无需做复杂的相对运
动,因此普通的超声波加工设备结构简单。
但若需要加工较大而复杂精密的三维结构,仍需设计和制造三坐标数控超声波加工机床。
3)由于去除加工材料是靠极小磨粒瞬时局部的撞击作用,故工件表面的宏观切削力很小,切削应力、切削热很小,不会引起变形及烧伤,表面粗糙度Ra值可达1.0~0. 1um,加工精度可达0.01~0.02mm,并可加工细小结构和地刚度的工件。
28、超声波加工速度:加工速度是指单位时间内去除的材料量,单位通常以g/min或mm3/min表示,加工玻璃的最大速度可达
2000到4000mm3/min
影响加工速度的主要因素有:1)工具振幅和频率的影响2)进给压力的影响3)磨料种类和粒度的影响4)磨料悬浮液浓度的影响5)工件材料的影响。
29、超声波焊接原理是利用超声频振动作用去除工件表面的氧化膜,暴露出新的本体表面,通过两个工件表面在一定的压力下相互
剧烈摩擦、发热而亲和粘结在一起。
30、激光:受击辐射发出的光便是激光。
激光加工:当激光照射在工件表面时,光能被工件吸收并迅速转化为热能,光斑区的温度可达10000°C以上,使材料熔化至气化,这就是激光加工。
激光加工技术已广泛用于机械加工、电子工业、国防和人民生活等许多领域。
?31、激光加工原理:激光加工是工件在光热效应下产生高温熔融和受冲击波抛出的综合作用过程。
激光加工具有如下特点:1)激光加工属高能束流加工,功率密度可高达10^8~10^10W/cm^3,几乎可以加工任何金属材料和非金属材料;2)激光加工无明显机械力,不存在工具损耗,加工速度快,热影响区小,易实现加工过程自动化;3)激光可通过玻璃等透明材料进行加工,如对真空管内部的器件进行焊接等;4)激光可以通过聚焦形成微米级的光斑,输出功率的大小又可以调节,因此可进行精密微细加工;5)可以达到0.01mm的平均加工精度和0.001mm的最高加工精度,表面粗糙度Ra值可达0.4~0.1um。
32、激光加工的基本设备由激光器、激光器电源、光学系统及机械系统等四大部分组成。