车间设备管理培训课件.ppt
合集下载
生产车间现场管理培训课件(PPT 44页)
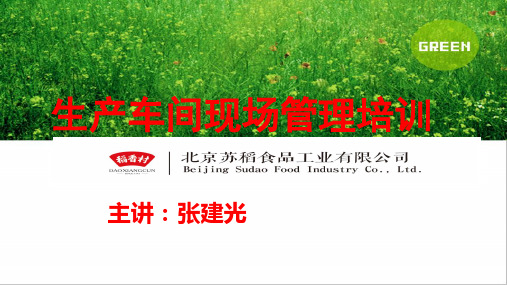
● PDCA循环法 (戴明环)
A
P
C
D
P(Plan) ——计划阶段 D(Do) ——执行阶段 C(Check)——检查阶段 A(Action)——处理阶段
三、生产现场的质量控制
1、在全面质量管理中使用PDCA循环法
阶段
步
骤
P 1、分析现状,找出问题 2、找出产生问题的原因或影响因素 3、找出原因中的主要原因 4、针对主要原因,制定解决问题的方案
一、优秀现场管理的标准和要求
一、优秀现场管理的标准和要求
3、现场管理六要素(5M1E分析法)
现场管理的六个要素即:人、机、料、法、环、测。 ----也称为5M1E分析法。
1) 人(Man):操作者对质量的认识、技术、身体状况等; 2) 机器(Machine):设备、测量仪器的精度和维护保养状况等; 3) 材料(Material):材料能否达到要求的性能等; 4) 方法(Method):生产工艺、设备选择、操作规程等; 5) 测量(Measurement):测量时采取的方法是否标准、正确; 6) 环境(Environment):工作现场的技术要求和清洁条件等; 由于这五个因素的英文名称的第一个字母是M和E,简称为5M1E。
D 5、按制定的计划认真执行 C 6、检查措施执行的效果 A 7、巩固提高,总结成功经验
8、把未解决或新出现的问题转入下一循环
主要方法和内容
调查表、分层法、排列图 因果图 排列图、相关图等 预期达到的目的(What) 在哪里执行措施(Where) 由谁来执行(Who) 何时开始和完成(When) 如何执行(How)
高企业经济效益。
二、现场管理的基本方法
(二)、作业标准化
3、标准的制定要求: 1)、目标指向:即遵循标准总是能保持生产出相同品
A
P
C
D
P(Plan) ——计划阶段 D(Do) ——执行阶段 C(Check)——检查阶段 A(Action)——处理阶段
三、生产现场的质量控制
1、在全面质量管理中使用PDCA循环法
阶段
步
骤
P 1、分析现状,找出问题 2、找出产生问题的原因或影响因素 3、找出原因中的主要原因 4、针对主要原因,制定解决问题的方案
一、优秀现场管理的标准和要求
一、优秀现场管理的标准和要求
3、现场管理六要素(5M1E分析法)
现场管理的六个要素即:人、机、料、法、环、测。 ----也称为5M1E分析法。
1) 人(Man):操作者对质量的认识、技术、身体状况等; 2) 机器(Machine):设备、测量仪器的精度和维护保养状况等; 3) 材料(Material):材料能否达到要求的性能等; 4) 方法(Method):生产工艺、设备选择、操作规程等; 5) 测量(Measurement):测量时采取的方法是否标准、正确; 6) 环境(Environment):工作现场的技术要求和清洁条件等; 由于这五个因素的英文名称的第一个字母是M和E,简称为5M1E。
D 5、按制定的计划认真执行 C 6、检查措施执行的效果 A 7、巩固提高,总结成功经验
8、把未解决或新出现的问题转入下一循环
主要方法和内容
调查表、分层法、排列图 因果图 排列图、相关图等 预期达到的目的(What) 在哪里执行措施(Where) 由谁来执行(Who) 何时开始和完成(When) 如何执行(How)
高企业经济效益。
二、现场管理的基本方法
(二)、作业标准化
3、标准的制定要求: 1)、目标指向:即遵循标准总是能保持生产出相同品
车间设备管理课件
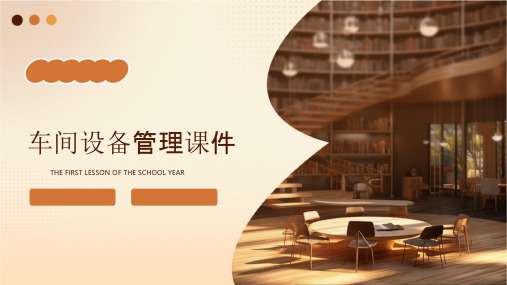
能效提升与节能减排
总结词
通过优化设备运行方式和采用节能技术,降低设备能耗和排放,提高能效和环保水平。
详细描述
车间设备在运行过程中会产生大量的能耗和排放,对环境造成一定的影响。企业可以通 过优化设备运行方式、采用节能技术和设备,降低设备的能耗和排放,提高能效和环保 水平。例如,采用高效电机、节能灯具等节能设备,以及实施能源管理系统,实现对设
01
车间设备管理的绩 效评估
设备完好率评估
01
总结词
设备完好率是评估车间设备管理绩效的重要指标之一,它反映了设备的
可靠性、稳定性和可用性。
02
总结词
设备完好率越高,说明设备的维护保养工作做得越好,设备的可靠性、
稳定性和可用性越强。
03
详细描述
为了提高设备完好率,车间设备管理人员需要制定合理的维护保养计划,
检测设备
总结词
检测设备是车间中用于检测产品质量和 设备状态的设备,如测量仪器、检验工 具等。
VS
详细描述
检测设备对于保证产品质量和设备正常运 行至关重要。企业应定期校准和检查检测 设备,以确保其准确性和可靠性。同时, 检测设备的维护和保养也是保证产品质量 和生产效率的重要环节。
01
车间设备的日常维 护
日常检查
每日对设备进行例行 检查,确保设备运行 正常。
检查设备是否有异常 声音或振动,以及是 否有泄漏或腐蚀现象。
检查设备的仪表、指 示灯等是否正常工作。
定期保养
根据设备制造商的推荐,定期对设备 进行保养。
对设备进行全面清洁和检查,确保设 备处于良好状态。
更换磨损或老化的部件,如润滑油、 滤清器等。
故障处理
当设备出现故障时,及时停机并 通知维修人员。
设备维护与管理培训课件
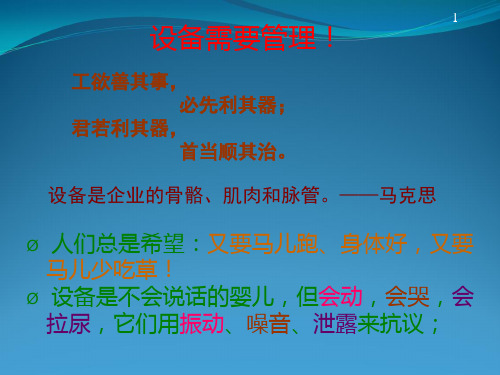
(2)第Ⅱ类无形磨损:由于社会技术的进步,出现性 能更完善和效率更高的新型设备,致使原有设备陈旧落 后,丧失部分或全部使用价值。又叫技术性无形磨损。 其后果是生产率大大低于社会平均水平,因而生产成本 大大高于社会平均水平。
设备维护理论
17
设备故障曲线(规律)
实践证明,可维修设备的故障率随时间的推移呈图示曲线形状,这
磨 损
最佳运行状态,磨损速度 程
缓慢,磨损量小,曲线呈平稳
度
状态。
第Ⅲ阶段:急剧磨损阶段
磨损速度非常快,丧失精 度和强度,事故概率急升。
Ⅰ
Ⅱ
零件磨损示意图
Ⅲ
时间
设备维护理论
16
2、设备的无形磨损:不表现为实体的变化,却表现 为设备原始价值的贬值,又叫精神磨损。有两种 情况:
(1)第Ⅰ类无形磨损:由于设备制造工艺的不断改进, 劳动生产率不断提高,致使生产同种设备所需要的社会 平均劳动减少,成本降低,从而使原已购买的设备贬值。 不影响设备功能。
几个术语
28
二级保养(二保):以维修工人为主,操作 工人参加,设备每运转一年或运转台时 2500~2800小时,进行一次保养,包括一级保 养内容,一般为3~6天,精大稀设备适当延长, 主要内容除进行一保内容外,尚需进行机电 检修、换磨损另件、部分括研、机械换油、 电机加油等
几个术语
29
设备维护:
设备管理的定义
3
广义的设备管理
是指通过设备的调查、 研究、设计、制作、设 置,经过运转、保养, 到最后废弃的设备的全 寿命周期中,以有效地 运用设备提高企业生产 线的活动
狭义的设备管理
指设备的安置完成后的 设备保养、维修活动
4
设备维修发展概况
设备维护理论
17
设备故障曲线(规律)
实践证明,可维修设备的故障率随时间的推移呈图示曲线形状,这
磨 损
最佳运行状态,磨损速度 程
缓慢,磨损量小,曲线呈平稳
度
状态。
第Ⅲ阶段:急剧磨损阶段
磨损速度非常快,丧失精 度和强度,事故概率急升。
Ⅰ
Ⅱ
零件磨损示意图
Ⅲ
时间
设备维护理论
16
2、设备的无形磨损:不表现为实体的变化,却表现 为设备原始价值的贬值,又叫精神磨损。有两种 情况:
(1)第Ⅰ类无形磨损:由于设备制造工艺的不断改进, 劳动生产率不断提高,致使生产同种设备所需要的社会 平均劳动减少,成本降低,从而使原已购买的设备贬值。 不影响设备功能。
几个术语
28
二级保养(二保):以维修工人为主,操作 工人参加,设备每运转一年或运转台时 2500~2800小时,进行一次保养,包括一级保 养内容,一般为3~6天,精大稀设备适当延长, 主要内容除进行一保内容外,尚需进行机电 检修、换磨损另件、部分括研、机械换油、 电机加油等
几个术语
29
设备维护:
设备管理的定义
3
广义的设备管理
是指通过设备的调查、 研究、设计、制作、设 置,经过运转、保养, 到最后废弃的设备的全 寿命周期中,以有效地 运用设备提高企业生产 线的活动
狭义的设备管理
指设备的安置完成后的 设备保养、维修活动
4
设备维修发展概况
设备操作安全培训ppt(65张)
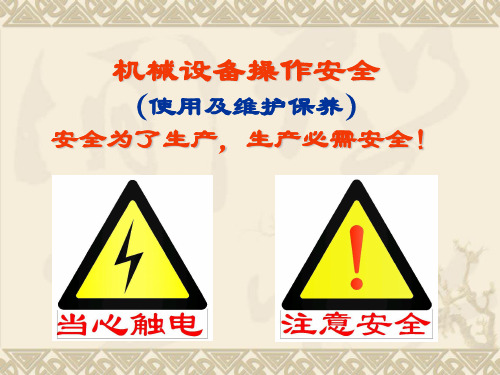
事故发生的基本特点
❖ 孕育——发展——发生——伤害(损失)
❖ 因果性 ❖ 偶然性 ❖ 必然性 ❖ 潜伏期 ❖ 突变性
设备操作安全培训(ppt65页)
设备操作安全培训(ppt65页)
墨菲定律
❖ 做任何一件事情,如果客观上存在着一种错误的 做法,或者存在着发生某种事故的可能性,不管 发生的可能性有多小,当重复去做这件事时,事 故总会在某一时刻发生。也就是说,只要发生事 故的可能性存在,不管可能性多么小,这个事故 迟早会发生的。
生产过程中的安全
❖ 人员安全 ❖ 设备安全 ❖ 产品安全
人员安全
❖ 生命对每个人都只有一次,没有人不热爱生 命,谁都不愿意作无谓的牺牲,事故灾害是 危及人的生命和健康的大敌。
❖ 人世间,人的生命是最宝贵的,只有健康的 身体和安全的保障,人们才能为生产发展作 贡献,才能建立幸福和谐家庭。
(图例)
案例
安全的定义: 安全是指安稳而无危险的事物
❖ 所谓安全是指免遭不可接受的风险伤害,不 发生导致死亡,职业病,设备或财产损失的 情况(包括幸福,舒适)。
❖ 生产过程中的安全是指人不受到伤害,财产 不受到损失,生产秩序稳定持续进行的正常 状况。
安全管理的含义
❖ 就是通过制度和具体措施 来提升安全管理水平,防止灾 害的发生。安全管理的目的是 为了加强员工的安全观念,使 其具有良好的安全工作意识, 更加注重安全细节管理。这样 不但能够降低事故发生率,而 且能提升员工的工作品质。安 全仅仅靠口号和理念是远远不 够的,它必须有具体措施来保 证实施。
机械设备操作安全
(使用及维护保养) 安全为了生产,生产必需安全!
目的和意义
❖ 目的: 1. 正确操作保养设备,确保设备处于良好技
❖ 孕育——发展——发生——伤害(损失)
❖ 因果性 ❖ 偶然性 ❖ 必然性 ❖ 潜伏期 ❖ 突变性
设备操作安全培训(ppt65页)
设备操作安全培训(ppt65页)
墨菲定律
❖ 做任何一件事情,如果客观上存在着一种错误的 做法,或者存在着发生某种事故的可能性,不管 发生的可能性有多小,当重复去做这件事时,事 故总会在某一时刻发生。也就是说,只要发生事 故的可能性存在,不管可能性多么小,这个事故 迟早会发生的。
生产过程中的安全
❖ 人员安全 ❖ 设备安全 ❖ 产品安全
人员安全
❖ 生命对每个人都只有一次,没有人不热爱生 命,谁都不愿意作无谓的牺牲,事故灾害是 危及人的生命和健康的大敌。
❖ 人世间,人的生命是最宝贵的,只有健康的 身体和安全的保障,人们才能为生产发展作 贡献,才能建立幸福和谐家庭。
(图例)
案例
安全的定义: 安全是指安稳而无危险的事物
❖ 所谓安全是指免遭不可接受的风险伤害,不 发生导致死亡,职业病,设备或财产损失的 情况(包括幸福,舒适)。
❖ 生产过程中的安全是指人不受到伤害,财产 不受到损失,生产秩序稳定持续进行的正常 状况。
安全管理的含义
❖ 就是通过制度和具体措施 来提升安全管理水平,防止灾 害的发生。安全管理的目的是 为了加强员工的安全观念,使 其具有良好的安全工作意识, 更加注重安全细节管理。这样 不但能够降低事故发生率,而 且能提升员工的工作品质。安 全仅仅靠口号和理念是远远不 够的,它必须有具体措施来保 证实施。
机械设备操作安全
(使用及维护保养) 安全为了生产,生产必需安全!
目的和意义
❖ 目的: 1. 正确操作保养设备,确保设备处于良好技
《车间管理培训教材》课件

和质量。
工艺流程优化
不断优化工艺流程,改进生产工艺 ,降低生产成本和提高产品质量。
工艺流程监控
对工艺流程进行实时监控,确保工 艺流程的稳定性和可靠性。
生产质量管理
质量标准制定
根据客户需求和行业标准,制定合理 的质量标准,确保产品质量符合要求 。
质量检验与控制
质量改进与提升
不断改进和提升产品质量,提高客户 满意度和产品竞争力。
02
CATALOGUE
车间生产流程管理
生产计划管理
01
02
03
生产计划制定
根据市场需求、订单和产 品特点,制定合理的生产 计划,确保生产任务按时 完成。
生产计划调整
根据实际情况,适时调整 生产计划,以适应市场变 化和客户需求。
生产计划执行
确保生产计划的有效执行 ,对生产进度进行监控和 调整,确保生产顺利进行 。
员工关系
关注员工关系,及时解 决员工之间的矛盾和问 题,营造和谐的工作氛 围。
THANKS
感谢观看
。
物资管理
物资采购
根据生产计划和库存情况,制定合理的物资采购计划,确保生产 所需物资的供应。
物资验收
对采购的物资进行质量检验和数量核对,确保物资质量合格、数量 准确。
物资储存与发放
建立科学的物资储存管理制度,确保物资储存安全、有序;建立物 资发放制度,确保生产所需物资及时发放。
库存管理
库存盘点
定期对库存进行盘点,确保库存数量与账面数量 一致。
环保与排放管理
环保与排放管理的重要性
随着环境保护意识的提高,企业需要承担更多的环保责任 ,对生产过程中的废弃物和排放物进行有效的管理和控制 。
环保与排放管理的主要内容
工艺流程优化
不断优化工艺流程,改进生产工艺 ,降低生产成本和提高产品质量。
工艺流程监控
对工艺流程进行实时监控,确保工 艺流程的稳定性和可靠性。
生产质量管理
质量标准制定
根据客户需求和行业标准,制定合理 的质量标准,确保产品质量符合要求 。
质量检验与控制
质量改进与提升
不断改进和提升产品质量,提高客户 满意度和产品竞争力。
02
CATALOGUE
车间生产流程管理
生产计划管理
01
02
03
生产计划制定
根据市场需求、订单和产 品特点,制定合理的生产 计划,确保生产任务按时 完成。
生产计划调整
根据实际情况,适时调整 生产计划,以适应市场变 化和客户需求。
生产计划执行
确保生产计划的有效执行 ,对生产进度进行监控和 调整,确保生产顺利进行 。
员工关系
关注员工关系,及时解 决员工之间的矛盾和问 题,营造和谐的工作氛 围。
THANKS
感谢观看
。
物资管理
物资采购
根据生产计划和库存情况,制定合理的物资采购计划,确保生产 所需物资的供应。
物资验收
对采购的物资进行质量检验和数量核对,确保物资质量合格、数量 准确。
物资储存与发放
建立科学的物资储存管理制度,确保物资储存安全、有序;建立物 资发放制度,确保生产所需物资及时发放。
库存管理
库存盘点
定期对库存进行盘点,确保库存数量与账面数量 一致。
环保与排放管理
环保与排放管理的重要性
随着环境保护意识的提高,企业需要承担更多的环保责任 ,对生产过程中的废弃物和排放物进行有效的管理和控制 。
环保与排放管理的主要内容
设备管理培训ppt课件
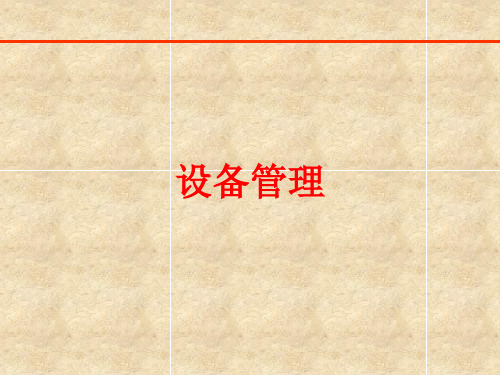
设备使用的“五项纪律”
设备使用的“五项纪律”: (1)凭操作证使用设备,遵守安全操作规程; (2)经常保持设备清洁,并按规定加油; (3)遵守交接班制度; (4)管好工具附件,不得遗失; (5)发现故障,立即停车,自己不能处理的应 及时通知检查。
四、设备的点检
目标:减少设备故障,降低维修费用。
1 设备点检的目的 防事故于未然,通过对设备进行预防性检查, 可查明事故原因,提出消除故障的措施,保持 设备性能的高度稳定,延长设备零部件使用寿
• 设备验收:
★验收程序:新增设备, 由资产管理部组织相关单位进行 验收,并填写《竣工验收单》,由参加现场验收的相关单 位人员签字确认。 ★经验收,质量、数量、性能、技术条件和图纸符合合同 及技术协议要求,现场验收后使用单位方可投入使用,如 存在问题,立即向设备部门主管领导汇报,同时报生产厂 家协商解决,验收人员必须做好验收纪要。
机,非停机,五感,仪表)
定人: 定表:
定记录:
确定点检人员(按照不同点检分 确定点检表格
确定点检记录内容项目及相关分析
类确定)
23
6 点检实施
检查:按照点检规范对设备的点检部位进行检查; 记录:将检查结果记录在案; 处理:检查中间出现的异常及时处理,恢复设备正 常状态,并将处理结果记录,不能处理的要报告 传达给负责部门处理; 分析:定期分析检查记录内容,找出设备薄弱环节 或难以维护部位,提出改进意见; 改进:组织实施对设备薄弱环节的改进工作。
对设备的运行状况、工作性能、零件的磨 损程度进行检查和校验,以求及时地发现问题, 消除隐患,并能针对发现问题,提出维护措施, 做好修理前的各种准备,以提高设备修理工作 的质量,缩短修理时间。
(二)设备的三级保养制度
车间设备管理培训课件

要点就是设备维护和全员参与上, 通过建立一个全系统员
工参与生产维修活动, 使设备运行达到最优, 降低故障及
运行成本为企业提升效益。
车间设备管理培训课件
• 5.3 OEE----设备综合效率 • = 时间利用率 * 设备性能率 * 产品合格率
•
• 1.时间利用率 = (负荷时间 - 停机损失) / 负荷时间 * 100%
车间设备管理培训课件
➢第二部分 维护保养职责与基 础知识
车间设备管理培训课件
2.1 培训的目的
保持设备良好的运行状态和工作能力、保证 设备安全、平稳、长久、满负荷、优质的 运行。
让使用部门操作维修人员掌握设备使用与维 护的基本技能, 便于部门内设备运行的技 能传承。
车间设备管理培训课件
2.2 操作工设备使用要求
车间设备管理培训课件
2.6 设备维护(保养)管理的目的和要求
• 目的: 通过对设备的检查、调整、保养、润滑、维修来减少设备的磨损, 降低故障率,提高设备的使用效率。
• 设备的维护保养是设备安全运行的重要保证。 • 基本要求: • 安全 清洁 • 润滑 责任
车间设备管理培训课件
•2.7设备维护最基本工作
车间设备管理培训课件
车间设备管理培训课件
车间设备管理培训课件
车间设备管理培训课件
车间设备管理培训课件
➢第四部分 三位一体的点检维 护保养制
车间设备管理培训课件
4.1 设备管理形成三圈闭环系统
•设备管理形成三圈闭环系统
车间设备管理培训课件
4.1 设备管理形成三圈闭环系统
车间设备管理培训课件
即查清原因, 及时调整处理, 尽快使机器设备恢复正常功能与安全运行。 发现异常情况, 应做紧急处理。并向车间领导及时报告, 同时将检查情况和处理结
设备管理培训PPT课件
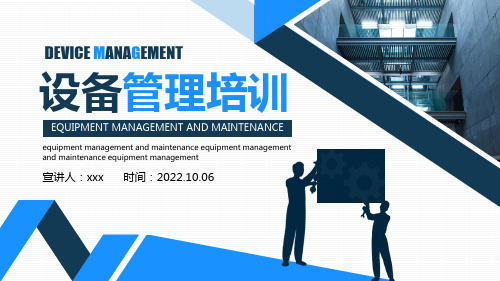
equipment management and maintenance equipment management and maintenance equipment
TNPM相关知识
全面规范化生产维护
(Total Normalized Productive Maintenance,简称:TnPM),是规 范化的TPM,是全员参与的,步步深 入的,通过制定规范,执行规范,评 估效果,不断改善来推进的TPM。
第一阶段
简单明确、字体整齐 通俗易懂、图文并茂 简洁叙述、点到即止
第二阶段
导入OEE指标,不 断提升设备综合运 行效率。
第三阶段
群策群力,全员参 与身边的改善,从 点滴做起。
第四阶段
信息沟通平台 展示分享园地 TnPM宣传阵地
DEVICE MANAGEMENT
设备管理培训
EQUIPMENT MANAGEMENT AND MAINTENANCE
第三部分
设备管理三好四会五律五定
equipment management and maintenance equipment management and maintenance equipment
设备管理三好四会五律五定
管好
①操作工人自己使用的设备及其附件要保管好。 ②未经领导批准,不能任意改动设备结构。 ③非本设备操作人员,不准擅自使用。
TNPM相关知识
有现场部门重视5S,可以潜移默化影响人
循序渐进---从基础作起 基石一:彻底的5S活动 全员参与---从基层作起 基石二:岗位重复小组活动
TNPM相关知识
TnPM实践工具比较多,经常用到的有:OEE、OPL、QC、MTBF/MTTR、PM分析、目 视管理、危险预知训练(KYT)…
TNPM相关知识
全面规范化生产维护
(Total Normalized Productive Maintenance,简称:TnPM),是规 范化的TPM,是全员参与的,步步深 入的,通过制定规范,执行规范,评 估效果,不断改善来推进的TPM。
第一阶段
简单明确、字体整齐 通俗易懂、图文并茂 简洁叙述、点到即止
第二阶段
导入OEE指标,不 断提升设备综合运 行效率。
第三阶段
群策群力,全员参 与身边的改善,从 点滴做起。
第四阶段
信息沟通平台 展示分享园地 TnPM宣传阵地
DEVICE MANAGEMENT
设备管理培训
EQUIPMENT MANAGEMENT AND MAINTENANCE
第三部分
设备管理三好四会五律五定
equipment management and maintenance equipment management and maintenance equipment
设备管理三好四会五律五定
管好
①操作工人自己使用的设备及其附件要保管好。 ②未经领导批准,不能任意改动设备结构。 ③非本设备操作人员,不准擅自使用。
TNPM相关知识
有现场部门重视5S,可以潜移默化影响人
循序渐进---从基础作起 基石一:彻底的5S活动 全员参与---从基层作起 基石二:岗位重复小组活动
TNPM相关知识
TnPM实践工具比较多,经常用到的有:OEE、OPL、QC、MTBF/MTTR、PM分析、目 视管理、危险预知训练(KYT)…
- 1、下载文档前请自行甄别文档内容的完整性,平台不提供额外的编辑、内容补充、找答案等附加服务。
- 2、"仅部分预览"的文档,不可在线预览部分如存在完整性等问题,可反馈申请退款(可完整预览的文档不适用该条件!)。
- 3、如文档侵犯您的权益,请联系客服反馈,我们会尽快为您处理(人工客服工作时间:9:00-18:30)。
• 未经设备管理部批准,不得将设备上的配 套件拆件使用
• 2.3 设备保养基础知识
• 密封点泄漏的检查: • 设备及管线的结合部位用肉眼观察不结焦
、不冒烟、无渗漏、无痕迹;焊接或连接 部位或仪表工艺管、空气管连接处用肥皂 水试漏,无气泡;真空部位用薄纸片测试 ,应无吸附的感觉;所有排污、冲水及生 活用水的阀门,在关闭状态下不漏水、不 漏气视为不漏。
“三好”、“四会”和“五项纪律”
操作人员经过培训,虽然具备了一定的理论知识和操作技能,但如 果不会保养设备,不会检查设备,不会排除故障,事无巨细都要依靠维 修工,其设备是无法合理使用的。因此“三好”、“四会”、“五项纪 律”是设备操作人员的基本要求。
• 管好:管好设备。指管好自己操作的设备,工、量具和附件要按定置管理的要求存放, 保持防护装置和管线的完整和可靠。
懂构造 懂用途
2.5 设备使用应具备的能力
• 会使用:熟悉设备结构,掌握设备的技术性能和操作方法,并熟悉加 工工艺,正确使用工装,不超负荷使用设备。
• 会保养:熟悉设备的油眼、油孔、油杯位置,知道所操作设备的油质、 油量、换油周期;按规定做好设备的润滑和冷却;设备内外无油垢、 无脏物,无锈蚀、无碰划伤、不漏油、不漏水、不漏电、不漏气;控 制系统灵敏可靠,设备四周清洁。
• 紧固:紧固螺栓、螺母,避免部件松动、振动、滑动、脱落 而造成的故障。
• 调整:对温度、位置、压力、速度、流量、松紧、间隙等。 • 防腐:通过隔离、等方法,防止工序及环境对设备的腐蚀。
2.7 设备维护最基本工作
两不见天是: 油料、清洗过的机件不见天
三不落地是: 油料、机件、工具不落地
➢第三部分 如何发现和清除六源
• 2.4 维修人员巡检包括内容
• 检查设备运行使用情况;听设备运行的声音,有无异常撞击和摩擦声。看温 度、压力、流量、液位等控制计量系统及自动化调节装置的工作情况。
• 检查传动皮带、运动机构、链条的紧固情况和平稳度。 • 检查安全保护罩、防护栏杆、设备管路的保温、保冷是否完好。 • 检查安全装置、制动装置、事故报警装置、停车装置是否良好。 • 检查设备及工艺管路的静、动密封点的泄露情况。 • 检查设备基础、地脚螺栓及其他连接螺栓有无松动,或因连接松动而产生振
• 让使用部门操作维修人员掌握设备使用与 维护的基本技能,便于部门内设备运行的 技能传承。
2.2 操作工设备使用要求
• 发现缺陷及时消除,不能立即消除的缺陷 ,要详细记录,及时上报,并协助设备维 修予以消除。
• 所有备用设备应有专人负责定期检查维护 ,注意防尘、防潮、防冻、防腐蚀,对于 传动设备还应定期进行盘车和切换,使所 有备用设备处于良好状态。
• 用好:用好设备。指严格遵守操作规程,执行维护保养制度,正确合理使用设备,不 带病运转、不超负荷使用,不在设备上乱堆、乱放工具和加工零件。
• 修好:修好设备。按期完成一级保养,配合维修人员做好二保,设备大修时要参与, 熟悉设备结构和性能,掌握一般修理技术。
2.5 设备使用应具备的能力
“四懂”
懂原理 懂性能
• 会检查:熟悉设备检查的注意事项、基本知识、精度标准、检查项目; 能熟练应用和检查设备的仪表、仪器、量具、检测工具是否正常。
• 会排除故障:在熟悉设备性能、一般原理、零部件组合情况的基础上, 能鉴别设备的异常声响和异常情况,及时判断设备异常部位和原因, 并能排除一般故障;在设备一旦发生故障或事故时,能应急处理,防 止事故扩大,及时报告有关部门检查、分析原因,并采取相应措施。
2.6 设备维护(保养)管理的目的和要求
• 目的:通过对设备的检查、调整、保养、润滑、维修来减少设备的磨损, 降低故障率,提高设备的使用效率。
• 设备的维护保养是设备安全运行的重要保证。
• 基本要求:
安全
清洁
润滑 责任
2.7设备维护最基本工作
设备日常维护 “十字作业”方针
清洁 润滑 紧固 调整 防腐
5
缺陷源
指影响产品质量的生产或加工环节。
指潜在的事故发生源。
质量/生产
6
危险源
对办公而言可以是影响健康的某些因素。
安全
➢第四部分 三位一体的点检维 护保养制
3.1 如何发现六源
清洁生产 1
6H (Headstream)
污染源
即灰尘、油污、废料、加工材料屑、有害气体、 有害液体、噪音、辐射等。
2
清扫困难源 指难以清扫、清洗的部位。
6S/现场
3
故障源
指造成故障的潜在因素。设备、操作、维护、
维修、自然劣化。
设备
4
浪费源
泛指任何不产生任何附加价值的事、物。
技术
动 • 检查轴承及有关部位的温度、润滑及振动情况。 • 通过上述一系列的检查,使所有的偶发故障的苗头及不正常状态能及早发现
并立即查清原因,及时调整处理,尽快使机器设备恢复正常功能与安全运行 。
• 发现异常情况,应做紧急处理。并向车间领导及时报告,同时将检查情况和 处理结果详细记录在操作记录上。
2.5 设备使用ቤተ መጻሕፍቲ ባይዱ具备的能力
2.5 设备使用应具备的能力
每个操作人员都应遵守以下“五项纪律”:
1、凭操作证使用设备,遵守安全操作规程。 2、经常保持设备清洁,并按规定加油。 3、多班制人员应遵守设备的交接班制度。 4、按定置管理要求管理好工具、附件。 5、发现异常,立即停机,自己能排除的故 障由自己排除,凡自己不能处理的问题应及 时通知有关人员检查处理。
目 ➢第一部分 车间设备状况 ➢第二部分 维护保养职责与基础知识
录 ➢第三部分 如何发现和清除六源 ➢第四部分 三位一体的点检维护保养制 ➢第五部分 TPM相关知识分享
➢第一部分 车间设备状况
1.1 车间设备台账的建立
➢第二部分 维护保养职责与基 础知识
2.1 培训的目的
• 保持设备良好的运行状态和工作能力、保 证设备安全、平稳、长久、满负荷、优质 的运行。
2.7 设备维护最基本工作
• 清洁:不只是表面,要将犄角旮旯清扫干净,让设备、零部 件的磨损、噪音、松动、变形、渗漏等缺陷暴露出来,及时 排除。
• 润滑:少油、缺脂造成润滑不良,使设备运转不正常,部分 零件过度磨损、温度过高造成硬度、耐磨性减低、甚至形成 热疲劳的损坏。应定时、定量、定质、及时加油、加脂。
• 2.3 设备保养基础知识
• 密封点泄漏的检查: • 设备及管线的结合部位用肉眼观察不结焦
、不冒烟、无渗漏、无痕迹;焊接或连接 部位或仪表工艺管、空气管连接处用肥皂 水试漏,无气泡;真空部位用薄纸片测试 ,应无吸附的感觉;所有排污、冲水及生 活用水的阀门,在关闭状态下不漏水、不 漏气视为不漏。
“三好”、“四会”和“五项纪律”
操作人员经过培训,虽然具备了一定的理论知识和操作技能,但如 果不会保养设备,不会检查设备,不会排除故障,事无巨细都要依靠维 修工,其设备是无法合理使用的。因此“三好”、“四会”、“五项纪 律”是设备操作人员的基本要求。
• 管好:管好设备。指管好自己操作的设备,工、量具和附件要按定置管理的要求存放, 保持防护装置和管线的完整和可靠。
懂构造 懂用途
2.5 设备使用应具备的能力
• 会使用:熟悉设备结构,掌握设备的技术性能和操作方法,并熟悉加 工工艺,正确使用工装,不超负荷使用设备。
• 会保养:熟悉设备的油眼、油孔、油杯位置,知道所操作设备的油质、 油量、换油周期;按规定做好设备的润滑和冷却;设备内外无油垢、 无脏物,无锈蚀、无碰划伤、不漏油、不漏水、不漏电、不漏气;控 制系统灵敏可靠,设备四周清洁。
• 紧固:紧固螺栓、螺母,避免部件松动、振动、滑动、脱落 而造成的故障。
• 调整:对温度、位置、压力、速度、流量、松紧、间隙等。 • 防腐:通过隔离、等方法,防止工序及环境对设备的腐蚀。
2.7 设备维护最基本工作
两不见天是: 油料、清洗过的机件不见天
三不落地是: 油料、机件、工具不落地
➢第三部分 如何发现和清除六源
• 2.4 维修人员巡检包括内容
• 检查设备运行使用情况;听设备运行的声音,有无异常撞击和摩擦声。看温 度、压力、流量、液位等控制计量系统及自动化调节装置的工作情况。
• 检查传动皮带、运动机构、链条的紧固情况和平稳度。 • 检查安全保护罩、防护栏杆、设备管路的保温、保冷是否完好。 • 检查安全装置、制动装置、事故报警装置、停车装置是否良好。 • 检查设备及工艺管路的静、动密封点的泄露情况。 • 检查设备基础、地脚螺栓及其他连接螺栓有无松动,或因连接松动而产生振
• 让使用部门操作维修人员掌握设备使用与 维护的基本技能,便于部门内设备运行的 技能传承。
2.2 操作工设备使用要求
• 发现缺陷及时消除,不能立即消除的缺陷 ,要详细记录,及时上报,并协助设备维 修予以消除。
• 所有备用设备应有专人负责定期检查维护 ,注意防尘、防潮、防冻、防腐蚀,对于 传动设备还应定期进行盘车和切换,使所 有备用设备处于良好状态。
• 用好:用好设备。指严格遵守操作规程,执行维护保养制度,正确合理使用设备,不 带病运转、不超负荷使用,不在设备上乱堆、乱放工具和加工零件。
• 修好:修好设备。按期完成一级保养,配合维修人员做好二保,设备大修时要参与, 熟悉设备结构和性能,掌握一般修理技术。
2.5 设备使用应具备的能力
“四懂”
懂原理 懂性能
• 会检查:熟悉设备检查的注意事项、基本知识、精度标准、检查项目; 能熟练应用和检查设备的仪表、仪器、量具、检测工具是否正常。
• 会排除故障:在熟悉设备性能、一般原理、零部件组合情况的基础上, 能鉴别设备的异常声响和异常情况,及时判断设备异常部位和原因, 并能排除一般故障;在设备一旦发生故障或事故时,能应急处理,防 止事故扩大,及时报告有关部门检查、分析原因,并采取相应措施。
2.6 设备维护(保养)管理的目的和要求
• 目的:通过对设备的检查、调整、保养、润滑、维修来减少设备的磨损, 降低故障率,提高设备的使用效率。
• 设备的维护保养是设备安全运行的重要保证。
• 基本要求:
安全
清洁
润滑 责任
2.7设备维护最基本工作
设备日常维护 “十字作业”方针
清洁 润滑 紧固 调整 防腐
5
缺陷源
指影响产品质量的生产或加工环节。
指潜在的事故发生源。
质量/生产
6
危险源
对办公而言可以是影响健康的某些因素。
安全
➢第四部分 三位一体的点检维 护保养制
3.1 如何发现六源
清洁生产 1
6H (Headstream)
污染源
即灰尘、油污、废料、加工材料屑、有害气体、 有害液体、噪音、辐射等。
2
清扫困难源 指难以清扫、清洗的部位。
6S/现场
3
故障源
指造成故障的潜在因素。设备、操作、维护、
维修、自然劣化。
设备
4
浪费源
泛指任何不产生任何附加价值的事、物。
技术
动 • 检查轴承及有关部位的温度、润滑及振动情况。 • 通过上述一系列的检查,使所有的偶发故障的苗头及不正常状态能及早发现
并立即查清原因,及时调整处理,尽快使机器设备恢复正常功能与安全运行 。
• 发现异常情况,应做紧急处理。并向车间领导及时报告,同时将检查情况和 处理结果详细记录在操作记录上。
2.5 设备使用ቤተ መጻሕፍቲ ባይዱ具备的能力
2.5 设备使用应具备的能力
每个操作人员都应遵守以下“五项纪律”:
1、凭操作证使用设备,遵守安全操作规程。 2、经常保持设备清洁,并按规定加油。 3、多班制人员应遵守设备的交接班制度。 4、按定置管理要求管理好工具、附件。 5、发现异常,立即停机,自己能排除的故 障由自己排除,凡自己不能处理的问题应及 时通知有关人员检查处理。
目 ➢第一部分 车间设备状况 ➢第二部分 维护保养职责与基础知识
录 ➢第三部分 如何发现和清除六源 ➢第四部分 三位一体的点检维护保养制 ➢第五部分 TPM相关知识分享
➢第一部分 车间设备状况
1.1 车间设备台账的建立
➢第二部分 维护保养职责与基 础知识
2.1 培训的目的
• 保持设备良好的运行状态和工作能力、保 证设备安全、平稳、长久、满负荷、优质 的运行。
2.7 设备维护最基本工作
• 清洁:不只是表面,要将犄角旮旯清扫干净,让设备、零部 件的磨损、噪音、松动、变形、渗漏等缺陷暴露出来,及时 排除。
• 润滑:少油、缺脂造成润滑不良,使设备运转不正常,部分 零件过度磨损、温度过高造成硬度、耐磨性减低、甚至形成 热疲劳的损坏。应定时、定量、定质、及时加油、加脂。