脱模机构设计
塑胶模具设计--经典旋转脱模机构
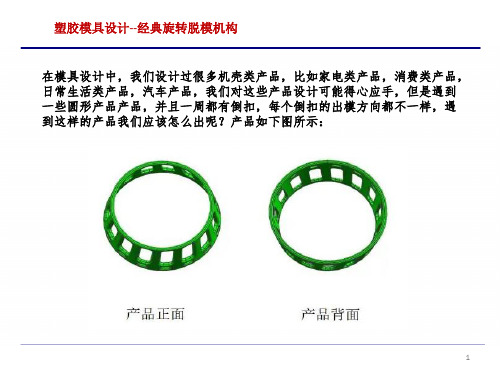
塑胶模具设计--经典旋转脱模机构 滑块镶件设计完成后,如何固定行位镶件呢?由于空间有限,先设计一个滑 块固定镶件固定在滑块镶件上面,用冬菇头连接,并用螺丝锁紧,设计完 成一个,在复制出14个,这样滑块镶件固定就完成,如下图所示:
5
Байду номын сангаас
塑胶模具设计--经典旋转脱模机构 将滑块镶件跟滑块耐磨块用螺丝连接,设计耐磨块的时候要注意:由于此 产品出模方向特殊,采用旋转出模的方式,因此,它的耐磨块也要设计成 弧形形状,并用螺丝固定在模仁上面,如下图所示:
8
塑胶模具设计--经典旋转脱模机构 在模具设计中,我们设计过很多机壳类产品,比如家电类产品,消费类产品, 日常生活类产品,汽车产品,我们对这些产品设计可能得心应手,但是遇到 一些圆形产品产品,并且一周都有倒扣,每个倒扣的出模方向都不一样,遇 到这样的产品我们应该怎么出呢?产品如下图所示:
1
塑胶模具设计--经典旋转脱模机构 产品进胶方式:产品进胶方式有很多种,有搭底进胶,潜水进胶,直接浇 口,牛角进胶,侧进胶,点进胶等,此产品外观要求严格,效率要求高, 客户要求采用大水口三点侧进胶,如下图所示:
6
塑胶模具设计--经典旋转脱模机构 运动原理解说:当齿条旋转的时候,齿条带动齿轮运动,由于大齿轮上面 安装有销钉,大齿轮运动就带动行位镶件运动,行位镶件就沿着出模的轨 道运动,产品倒扣被脱出,在利用顶出机构,产品顶出模具外面,如下图 所示:
7
塑胶模具设计--经典旋转脱模机构 后模仁采用圆形镶件镶拼起来,此镶件很大,镶件上面的胶位很多,为了 方便冷却,镶件上面设计水井冷却,设计水井的时候要注意:水井离胶位 面的安全距离(10-15)mm,产品进胶从镶件顶部侧进胶,如下图所示:
2
机械式轮胎硫化机脱模机构优化设计
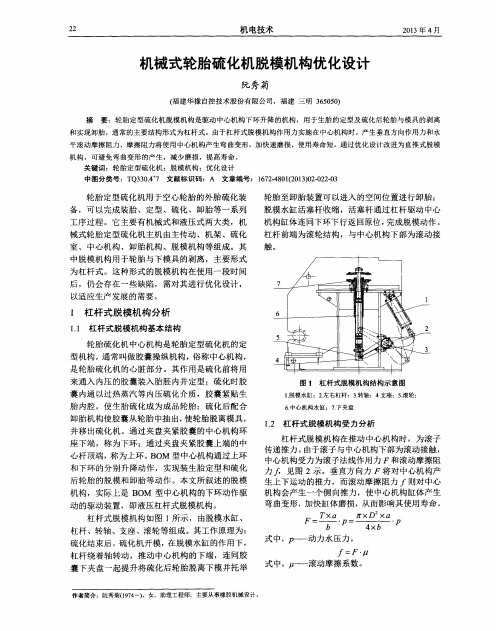
并移 出硫化 机 。通过 夹盘 夹紧胶 囊 的 中心机构 环
座 下端 ,称 为下 环 ;通 过 夹盘夹 紧胶 囊上 端 的 中
1 . 2 杠杆 式脱模机 构 受力分 析
心杆顶 端 , 称 为上环 。 B O M 型 中心机构通 过上 环
和 下环 的分 别升 降动 作 ,实现 装生 胎定 型和硫 化 后 轮胎 的脱 模和 卸胎 等动 作 。本文 所叙述 的脱模
中图分 类号 :T Q3 3 0 . 4 + 7 文献标识码 :A 文章编号 : 1 6 7 2 - - 4 8 0 1 ( 2 0 1 3 ) 0 2 ‘ ‘ 0 2 2 。 。 0 3
轮 胎 定型 硫化机 用 于空 心轮胎 的外 胎硫 化装
备 ,可 以完成 装胎 、定 型 、硫 化 、卸 胎等 一系 列
此优 化 方案 是脱 模水 缸对 中心机 构 只产生 向上 和
向下 的作 用 力 ,不会 产 生 附加 弯 矩 。且 由于减 少 了零 件 数量 和ቤተ መጻሕፍቲ ባይዱ 动链 ,也相应 提 高 了产 品的稳 定
性。
图 2 杠杆式脱模机构受力简 图
在 福 建华橡 自控技 术股 份 有 限公 司 的 4 5 时 轮 胎 定型 硫化 机 中 ,其脱模 水 缸尺 寸 为 :水缸 内 径 D= 1 5 0 mm;活 塞杆 直径 5 0 l n f l  ̄行程
=4 41 7 8N =44 . 1 7 8 。
机构,实际上是 B O M 型中心机构 的下环动作驱 动的驱动装置 ,即液压杠杆式脱模机构。
杠 杆式脱 模机 构如 图 1所示 , 由脱 模水 缸 、 杠杆 、转轴 、支 座 、滚 轮等 组成 。其 工作原 理为 : 硫 化结 束后 , 硫化 机开 模 ,在脱模 水缸 的作 用下 , 杠 杆绕 着轴 转动 ,推 动 中心机 构 的下端 ,连 同胶 囊 下夹 盘 一起 提升将 硫 化后轮 胎脱 离 下模 并托举
模塑制件顶出脱模机构设计
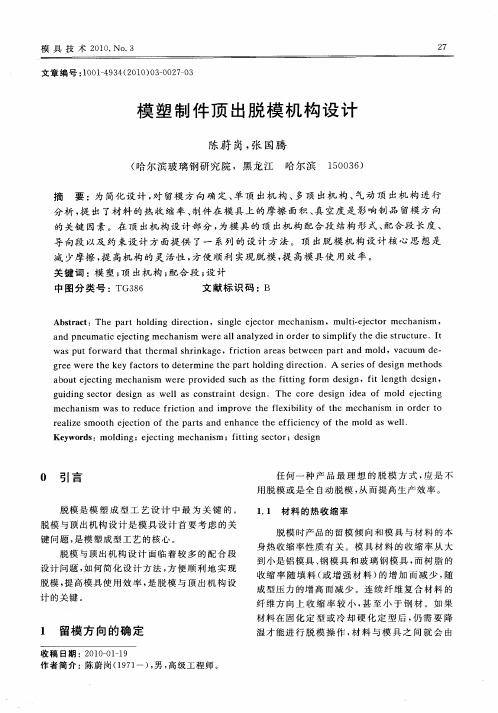
摘 要 :为 简化 设 计 , 留模 方 向 确 定 、 顶 出机 构 、 对 单 多顶 出机 构 、 动 顶 出机 构 进 行 气 分析 , 出 了材 料 的热 收 缩 率 、 件 在 模 具 上 的摩 擦 面积 、 空度 是 影 响 制 品 留模 方 向 提 制 真
的 关键 因素 。在 顶 出机 构 设 计 部 分 , 为模 具 的顶 出机 构 配合 段 结构 形 式 、 配合 段 长 度 、
温才能进行脱 模操 作 , 料与模 具 之 间就会 由 材
28
模 具 技 术 2 1 . . 0 0 No 3
文 章 编 号 :0 14 3 ( 0 0 0 —0 7 0 1 0 — 9 4 2 1 ) 30 2 — 3
2 7
模 塑 制 件 顶 出 脱 模 机 构 设 计
陈蔚 岗, 国腾 张
( 哈尔 滨 玻 璃 钢 研 究 院 ,黑 龙 江 哈 尔 滨 1 0 3 ) 5 0 6
m e ha s wa o r duc rc i nd i pr e t l x b lt he m e hanim n or er t c ni m s t e e f i ton a m ov he f e i iiy of t c s i d o
注塑内螺纹直接脱模结构设计方案

注塑内螺纹直接脱模结构设计方案一、整体思路。
咱们得想个办法,让带有内螺纹的塑料制品在注塑完后,能轻松地从模具里脱模,就像从被窝里钻出来一样容易,而且还不能把这个螺纹给搞坏喽。
二、具体结构设计。
1. 螺纹型芯部分。
首先呢,这个螺纹型芯不能是个死脑筋的结构。
咱们可以把它设计成两段式的。
就像火车有车头和车厢一样。
靠近模具型腔内部的那一段螺纹型芯,咱们可以让它稍微细一点,就像小一号的螺丝。
这一段的螺纹是完整的,用来成型产品的内螺纹。
然后外面再套上一段粗一点的“外套”,这个外套和里面的细螺纹型芯之间要有一定的间隙,这个间隙就像两个好朋友之间保持的小距离,不能太大也不能太小,大概在0.1 0.3毫米左右就行。
这个间隙是为了让里面的细型芯在脱模的时候有活动的空间。
2. 脱模动力装置。
为了让螺纹型芯能从产品里退出来,咱们得给它一个动力呀。
这时候可以在模具上安装一个小型的液压或者气动装置。
想象一下,这个装置就像一个小助手,在脱模的时候轻轻地推一下螺纹型芯。
不过这个推力得控制好,不能太猛,不然会把产品给弄坏的。
一般来说,根据产品的大小和材料的特性,这个推力在50 200牛顿之间比较合适。
另外,还可以在螺纹型芯上连接一个旋转机构。
这个旋转机构就像一个小陀螺,在液压或者气动装置推动螺纹型芯往外退的同时,让它慢慢地旋转。
因为内螺纹嘛,要是光直直地往外退,肯定会卡住的,就像你硬要把拧进去的螺丝直接拔出来一样困难。
这个旋转的速度也不能太快,每分钟大概转个5 10圈就差不多了。
3. 导向和限位结构。
在螺纹型芯的周围,要设置一些导向柱。
这些导向柱就像轨道一样,让螺纹型芯在脱模的时候只能按照规定的方向移动。
就像火车只能在铁轨上跑一样。
导向柱的表面要光滑得像溜冰场一样,这样可以减少摩擦,保证螺纹型芯移动得顺畅。
同时呢,还要有限位装置。
这个限位装置就像一个小警察,告诉螺纹型芯你只能移动到这个位置,不能再往前走了。
这样可以防止螺纹型芯过度脱模,把模具或者产品给损坏了。
模具的脱模机构

模具的脱模机构胶件脱模是注射成型过程中最后一个环节,脱模质量好坏将最后决定胶件的质量;当模具打开时,胶件须留在具有脱模机构的半模(常在动模)上,利用脱模机构脱出胶件。
脱模设计原则:(1)为使胶件不致因脱模产生变形,推力布置尽量均匀,并尽量靠近胶料收缩包紧的型芯,或者难于脱模的部位,如胶件细长柱位,采用司筒脱模。
(2)推力点应作用在胶件刚性和强度最大的部位,避免作用在薄胶位,作用面也应尽可能大一些,如突缘、(筋)骨位、壳体壁缘等位置,筒形胶件多采用推板脱模。
(3)避免脱模痕迹影响胶件外观,脱模位置应设在胶件隐蔽面(内部)或非外观表明;对透明胶件尤其须注意脱模顶出位置及脱模形式的选择。
(4)避免因真空吸附而使胶件产生顶白、变形,可采用复合脱模或用透气钢排气,如顶杆与推板或顶杆与顶块脱模,顶杆适当加大配合间隙排气,必要时还可设置进气阀。
(5)脱模机构应运作可靠、灵活,且具有足够强度和耐磨性,如摆杆、斜顶脱模,应提高滑碰面强度、耐磨性,滑动面开设润滑槽;也可渗氮处理提高表面硬度及耐磨性。
(6)模具回针长度应在合模后,与前模板接触或低于0.1mm,如图8.1.1所示。
(7)弹簧复位常用于顶针板回位;由于弹簧复位不可靠,不可用作可靠的先复位。
1 顶针、扁顶针脱模胶件脱模常用方式有顶针、司筒、扁顶针、推板脱模;由于司筒、扁顶价格较高(比顶针贵8~9倍),推板脱模多用在筒型薄壳胶件,因此,脱模使用最多的是顶针。
当胶件周围无法布置顶针,如周围多为深骨位,骨深/15mm时,可采用扁顶针脱模。
顶针、扁顶针表面硬度在HRC55以上,表面粗糙度Ra1.6以下。
顶针、扁顶针脱模机构如图8.1.1所示,设置要点如下:(1)顶针直径 d£Ø2.5mm时,选用有托顶针,提高顶针强度。
(2)扁顶针、有托顶针 K/H。
(3)顶位面是斜面,顶针固定端须加定位销;为防止顶出滑动,斜面可加工多个R小槽,如图8.1.2所示。
4.7脱模机构解析
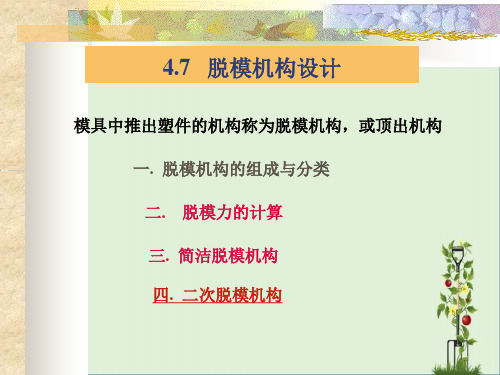
模具中推出塑件的机构称为脱模机构,或顶出机构 一. 脱模机构的组成与分类 二. 脱模力的计算 三. 简洁脱模机构 四. 二次脱模机构
一. 脱模机构的组成与分类
组成
脱模机构一般由三局部组成:推出部件,导向部件,复位部件 推出部件:推杆、拉料杆、推杆固定板,推板等
导向部件:导柱、导套 复位部件:复位杆
3〕直径和数量
保证足够的刚度。可设计成阶梯形
数量应保证顺当脱模且不损伤塑件表观
4〕推杆材料及热处理要求
材料常用T8A,T10A或65Mn,碳素工具钢热处理要求硬度HRC50~54,
弹簧钢热处理硬度要求HRC50~54。
5〕推杆固定形式
推杆
推杆
推杆
推杆
推杆
推杆
(a)
(b)
(c)
(d)
(e)
(f)
图4-79 推杆的固定形式
3〕气动脱模: 利用压缩空气将塑件吹出。
2、按模具构造分
一次推出脱模〔简洁脱模〕、二次推出脱模、动定模双向推出脱模、 挨次脱模、带螺纹塑件脱模塑件不变形损坏 机构推出中心与脱模力中心相重合,推出力分布均匀,
作用点尽可能靠近型芯防止塑件脱模后变形;推出力施于 塑件刚性和强度最大的地方〔如凸缘、加强筋等〕。
留有0.2~025mm的间隙 锥面 协作
推件板常用材料为45钢,热处理要求28~32HRC
四. 二次脱模机构
作用:由于塑件的特殊外形或生产自动化的需要;为避 开一次脱模塑件受力过大。
单推板
摆块拉板式二级脱模机构
双推板
三角滑块式双推板二次脱模机构
螺纹的脱模
强制脱出:弹性较好或较松软的塑件,用于精 度不高和小批量生产的塑件 模外脱出:活动螺纹镶块
1.4.7 顶出(脱模)机构设计[共5页]
![1.4.7 顶出(脱模)机构设计[共5页]](https://img.taocdn.com/s3/m/b6353f20ba0d4a7303763ab4.png)
46与︱缺点:侧向抽拔力较小。
行位回位时,大部分行位需由斜导柱启动,斜导柱受力状况不好。
特别注意:当驱动行位的斜导柱或斜滑板开始工作前,前、后模必须由导柱导向。
1.4.7 顶出(脱模)机构设计胶件脱模是注射成型过程中最后一个环节,脱模质量好坏将决定最后胶件的质量;当模具打开时,胶件须留在具有脱模机构的半模(常在动模)上,利用脱模机构脱出胶件。
脱模设计原则如下。
①为使胶件不致因脱模产生变形,推力布置应尽量均匀,并尽量靠近胶料收缩包紧的型芯,或者难于脱模的部位,如胶件细长柱位采用司筒脱模。
②推力点应作用在胶件刚性和强度最大的部位,避免作用在薄胶位,作用面也应尽可能大一些,如突缘、(筋)骨位、壳体壁缘等位置。
筒形胶件多采用推板脱模。
③避免脱模痕迹影响胶件外观,脱模位置应设在胶件隐蔽面(内部)或非外观表面;对透明胶件尤其需注意脱模顶出位置及脱模形式的选择。
④避免因真空吸附而使胶件产生顶白、变形,可采用复合脱模或用透气钢排气,如顶杆与推板或顶杆与顶块脱模,顶杆适当加大配合间隙排气,必要时还可设置进气阀。
⑤脱模机构应运作可靠、灵活,且具有足够强度和耐磨性,如摆杆、斜顶脱模,应提高滑碰面强度、耐磨性,滑动面开设润滑槽;也可采用渗氮处理,提高表面硬度及耐磨性。
⑥模具回针长度应在合模后,与前模板接触或低于0.1mm,如图1-106所示。
图1-106 顶出(脱模)机构⑦弹簧复位常用于顶针板回位;由于弹簧复位不可靠,不可用作可靠的先复位。
1.顶针、扁顶针脱模胶件脱模常用方式有顶针、司筒、扁顶针、推板脱模;由于司筒、扁顶针价格较高(比顶针价格贵8~9倍),推板脱模多用在筒型薄壳胶件中,因此,脱模使用最多的是顶针。
当胶件周围无法布置顶针,如周围多为深骨位,骨深大于或等于15mm时,可采用扁顶针脱模。
顶针、扁顶针表面硬度在HRC55以上,表面粗糙度R a在1.6以下。
顶针、扁顶针脱模机构如图1-107所示,设置要点如下。
①顶针直径d≤φ2.5mm时,选用有托顶针,提高顶针强度。
第六节 塑件脱模机构设计

简单脱模机构:在动模一边施加一次
推出力,就可实现塑件脱模的机构
双脱模机构
顺序脱模机构 二次脱模机构
浇注系统脱模机构
带螺纹塑件脱模机构
二、脱模力的计算
脱模力的组成
包紧力产生摩擦力 塑件与金属的粘附力 机构运动产生的摩擦阻力 克服大气压力(特指盲孔的筒、壳类零件) 注:脱模力不为恒定值 开模瞬间克服阻力最大——初始脱模力 以后脱模所需力——相继脱模力
推管推出动作模拟
推管与型芯的配合长度为推出距离s+3~5mm 为保护型芯和型腔,推管不易与成型表面接触 推管配合公称外径宜小于型腔内径 推管配合公称内径宜大于型芯内径 注:当凹模设在定模边,不存在内径与推管摩擦
2.顶管脱模机构
(2)主型芯固定在动模型芯固定板上
特点:型芯长度缩短, 但推出行程包含在动模 板内,动模厚度增加。
推杆推出机构形式
推杆推出机构形式
三、简单脱模机构
1、顶杆脱模机构
设计要点:
(2)顶杆直径必须有足够的强度,能承受顶出时 的冲击力。顶杆直径一般取2.5~12mm,对3 毫米以下的顶杆建议采用阶梯式结构, 即顶杆下部加粗以增加强度;
顶杆的其他固定形式:
(3)顶杆装配后不应有轴向窜动,其端 面应与型芯齐平。
2)球头拉料杆
2)球头拉料杆
4.5 注射模具浇注系统设计
2)菌头拉料杆
4.5 注射模具浇注系统设计
2)圆锥形拉料杆
圆锥 头形
复式圆 锥头形
没有储存冷料的作用,依靠塑料的包紧力将主流道 凝料拉住。 用于推板脱模机构上
4.5 注射模具浇注系统设计
3)圆锥形拉料杆
平头锥形 拉料杆
3)带推杆推出的拉料穴
- 1、下载文档前请自行甄别文档内容的完整性,平台不提供额外的编辑、内容补充、找答案等附加服务。
- 2、"仅部分预览"的文档,不可在线预览部分如存在完整性等问题,可反馈申请退款(可完整预览的文档不适用该条件!)。
- 3、如文档侵犯您的权益,请联系客服反馈,我们会尽快为您处理(人工客服工作时间:9:00-18:30)。
2.顶管脱模机构
三、简单脱模机构
3 .推板脱模机构
适用于薄壁容器、壳体形塑件以及制品中不 允许有顶出痕迹的情况。 设计要点 (1)顶板应淬硬,顶出过程 中不得脱离支撑顶板的导柱;
(2)顶板与型芯的配合应采用斜面配合,且 型芯留有台阶,以免顶出时顶板划伤型芯成 型部分;
(4)顶板顶出时拉料杆应固定在动模板上, 且用球形头或菌形头拉料杆;
Z形头拉料杆式的推板顶出机构
(3)为防止顶板顶出过程中制件与型芯间形成真空, 设计时应考虑进气装置。如采用顶杆、顶板联合顶 出;
(5)顶板顶出
3 .推板脱模机构
三、简单脱模机构
4、活动镶件脱模机构
5、多元件综合脱模机构
三、简单脱模机构
6、气压脱模机构
2
二、脱模力的计算
如塑件孔为盲孔,上述计算式中还须加上塑件所 受的大气压力。
F = 10A
式中:F—克服真空增加的脱模阻力,N;
A—塑件盲孔的底面积, cm。
三、简单脱模机构 1、顶杆脱模机构
设计要点: (1)顶杆应设在塑件能承力较大或脱模阻力较大的 地方,尽量使顶出的塑件受力均匀,但不宜与型芯或 的镶件的距离过近,以免影响成型零件的强度; (2)顶杆直径必须有足够的强度,能承受顶出时 的冲击力。顶杆直径一般取2.5~12mm,对3 毫米以下的顶杆建议采用阶梯式结构,即顶杆下部 加粗以增加强度;
2tESL cos ( f tg ) Q (1 )k
1.2 型芯为矩形截面
8tESL cos ( f tg ) Q (1 )k
二、脱模力的计算
式中:Q—脱模力,N; t—制品的平均璧厚,cm; L—塑件包裹型芯的长度,cm; S—塑料的成型收缩率, E—塑料的弹性模量,N/cm,见表1; —型芯的脱模斜度; —塑料的泊松比,0.3~0.45; k—与、有关的系数,k= 1+cossin,其 值约等于1; f—塑料与型芯的静摩擦系数,见表2。
八、模脚
3、要求: (1)与模板接触面需要磨削;
(2)模脚安排在模板的长边 一侧; (3)模脚的高度要满足顶出行程的要求;
(4)模脚的厚度,原则上讲越大越好。
(5)固定模脚的螺钉视模脚的大小而定。
5. 拉料杆
(二)对脱模机构的要求
1.塑件留于动模;
2. 保证塑件的质量;
顶杆一般设计在制品壁厚的地方或强度大的部位。
3.结构可靠。
(三)、 脱模机构的分类
1.按动力来源分; 机动脱模
手动脱模
液压脱模 气动脱模
2. 按模具结构分: 简单脱模机构 顺序脱模机构
二次脱模机构
二、脱模力的计算
(一)薄壁件的脱模力 当制品的璧厚与型芯直径的比小于0.05时,我 们称其为薄璧制品,其脱模力可按下式计算。 1.1 型芯为圆形截面
三、简单脱模机构
7、脱模系统的辅助零件 导向零件、回程杆。
(1)导向零件:导柱、导套。
(2)回程杆
(2)回程杆回程动画
(2)回程杆回程动画
第六节 塑件脱模机构设计
四、双脱模机构
第六节 塑件脱模机构设计
五、顺序脱模机构
(1)弹簧顺序脱模 限位杆的设计:
限位杆的长度;
限位杆的直径;
型腔板的支撑。
2RESL ( f tg ) Q (1 k 1)k
R:为圆形型芯的半径,cm。
二、脱模力的计算
2.2 型芯为矩形截面
2( a b ) ESL( f tg ) Q (1 k 1)k
a b:矩形型芯的两个边的长度,cm。
k1:系数。
2R k1 2 t cos 2tR cos
顶
出 板 (ejec tor plate)
顶出固定板 (ejector retainer plate)
制品顶出型芯的情况
拉料杆( sprue puller)
回
程
杆
(return pin )
合模动画演示
第六节 塑件脱模机构设计
一、脱模机构
(一)脱模机构的结构组成
1. 顶杆
2. 顶出板 3. 顶出固定板 4. 回程杆
顶杆应用实例
三、简单脱模机构
2.顶管脱模机构
适用于制品中有圆筒形部分的顶出结构。 设计要点 (1)顶管厚度一般不小于1.5毫米;
(2)顶管应淬硬,最小淬硬长度不小于型腔 配合长度与顶出距离的和;
(3)顶管与内外型芯的配合精度均为间隙配 合,配合间隙小于塑料的溢料值。
2.顶管脱模机构
顶管的其他结构形式
二、脱模力的计算
表1 弹性模量E值
塑料品种
聚苯乙烯 高抗冲击聚 苯乙烯 高抗冲击 ABS
E (1×105)
2.8~3.5 1.4~3.1 2.9
塑料品种
高密度聚乙 烯 聚丙烯 耐热ABS
E (1×105)
0.84~0.95 1.1~1.6 1.8
二、脱模力的计算
表2 静摩擦系数f值 塑料品种 f 塑料品种 f
高抗冲击聚苯乙 烯 聚丙烯 高密度聚乙烯 尼龙类 聚碳酸酯 聚砜
0.35~0.4
聚苯乙烯
0.2~0.35 0.15~0.2 0.24~0.31 0.35 0.4
ABS
聚甲醛
0.12~ 0.15 0.2~ 0.25 0.15
聚苯醚
0.35
二、脱模力的计算
(二)厚壁件的脱模力 当制品的璧厚与型芯直径的比大于0.05时我们称 其为薄璧制品,其脱模力可按下式计算。 2.1 型芯为圆形截面
六、二级脱模机构
4、U形限制架二级脱模
4、U形限制架二级脱模
4、U形限制架二级脱模
4、U形限制架二级脱模
第六节 塑件脱模机构设计
七、浇注系统凝料的自动脱落
七、浇注系统凝料的自动脱落
七、浇注系统凝料的自动脱落
第六节 塑件脱模机构设计
八、模脚
1 作用:支撑模具;调整模厚。 2、结构:有垫板型式 无垫板型式
(7)顶杆的强度计算 a 圆形顶杆 64u 2 L2Q dm i n 4 由欧拉公式: n 3 E
设计时为保证可靠程度,d = 1.5 dmin。 u—考虑支撑条件的长度系数,u≈0.7; L—顶杆长度,cm; E—顶杆的抗拉弹性模量,N/ cm; n—顶杆件数; Q—脱模力,N;
Q一般情况下也可按下式计算: 对通孔型芯: Q = LHq(f· cos—sin) 对盲孔型芯: Q = LHq(f· cos—sin) + B 以上两式中: L—活动型芯中被塑件包紧的断面周长,cm; H—活动型芯成型部分的高度,cm; B—垂直于顶出方向的型芯投影面积,cm; q—包紧型芯的单位压力,一般取800~3400N/ cm; —塑料与钢的摩擦系数,一般取0.15~0.2。
(3)顶杆装配后不应有轴向窜动,其端 面应与型芯齐平。
顶杆的其他固定形式:
(4)浇口处一般不设顶杆,以防浇口处内应 力过大塑件发生破碎; (5)顶杆位置应尽量避开冷却水孔和侧抽芯 滑块,以勉发生干涉,如果无法避开侧抽 芯滑块,顶出机构应设计先复位机构;
(6)顶杆与型芯的配合应选间隙配合,配合 间隙应小于塑料的溢料值;
第六节 塑件脱模机构设计
1、教学目的与要求
目的: 学习塑料注射模具脱模机构及设计要求。 要求: (1)掌握脱模机构的结构分类; (2)掌握脱模机构结构中的简单脱模机构设计; (3)熟悉脱模机构结构中的二次脱模机构及其 它结构的设计; (4)掌握相关的英文词汇。
制品包裹型芯的情况
顶杆(ejector pin )
b 方形顶杆 Ebw 3 方形顶杆的脱模阻力F = 4.9 2
L
其中:b—方形顶杆长度方向上的尺寸, cm; w—方形顶杆宽度方向上的尺寸,cm。
(8)顶杆的位置分布 顶杆的位置分布以对 注射机顶杆中心的合力矩为零为最佳,一 般情况下,顶杆的数目以少为宜,且均匀 分布。 (9)材料:45 、T8 、T10等,头部淬火 HRC>50。 表面粗糙度:配合部分 (10 )顶杆行程:一般情况下,大于制品型 芯的高度。
五、顺序脱模机构
(2) 尼龙销顺序脱模
五、顺序脱模机构
(3)拉钩顺序脱模
第六节 塑件脱模机构设计
六、二级脱模机构
1、摆块二级脱模
1、摆块二级脱模
1、摆块二级脱模
1、摆块二级脱模
六、二级脱模机构
2、 滑块二级脱模
2、 滑块二级脱模
六、二级脱模机构
3、摆杆二级脱模
3、摆杆二级脱模
3、摆杆二级脱模