脱模机构
模具的脱模机构

模具的脱模机构胶件脱模是注射成型过程中最后一个环节,脱模质量好坏将最后决定胶件的质量;当模具打开时,胶件须留在具有脱模机构的半模(常在动模)上,利用脱模机构脱出胶件。
脱模设计原则:(1)为使胶件不致因脱模产生变形,推力布置尽量均匀,并尽量靠近胶料收缩包紧的型芯,或者难于脱模的部位,如胶件细长柱位,采用司筒脱模。
(2)推力点应作用在胶件刚性和强度最大的部位,避免作用在薄胶位,作用面也应尽可能大一些,如突缘、(筋)骨位、壳体壁缘等位置,筒形胶件多采用推板脱模。
(3)避免脱模痕迹影响胶件外观,脱模位置应设在胶件隐蔽面(内部)或非外观表明;对透明胶件尤其须注意脱模顶出位置及脱模形式的选择。
(4)避免因真空吸附而使胶件产生顶白、变形,可采用复合脱模或用透气钢排气,如顶杆与推板或顶杆与顶块脱模,顶杆适当加大配合间隙排气,必要时还可设置进气阀。
(5)脱模机构应运作可靠、灵活,且具有足够强度和耐磨性,如摆杆、斜顶脱模,应提高滑碰面强度、耐磨性,滑动面开设润滑槽;也可渗氮处理提高表面硬度及耐磨性。
(6)模具回针长度应在合模后,与前模板接触或低于0.1mm,如图8.1.1所示。
(7)弹簧复位常用于顶针板回位;由于弹簧复位不可靠,不可用作可靠的先复位。
1 顶针、扁顶针脱模胶件脱模常用方式有顶针、司筒、扁顶针、推板脱模;由于司筒、扁顶价格较高(比顶针贵8~9倍),推板脱模多用在筒型薄壳胶件,因此,脱模使用最多的是顶针。
当胶件周围无法布置顶针,如周围多为深骨位,骨深/15mm时,可采用扁顶针脱模。
顶针、扁顶针表面硬度在HRC55以上,表面粗糙度Ra1.6以下。
顶针、扁顶针脱模机构如图8.1.1所示,设置要点如下:(1)顶针直径 d£Ø2.5mm时,选用有托顶针,提高顶针强度。
(2)扁顶针、有托顶针 K/H。
(3)顶位面是斜面,顶针固定端须加定位销;为防止顶出滑动,斜面可加工多个R小槽,如图8.1.2所示。
塑料模具课件-脱摸机构图
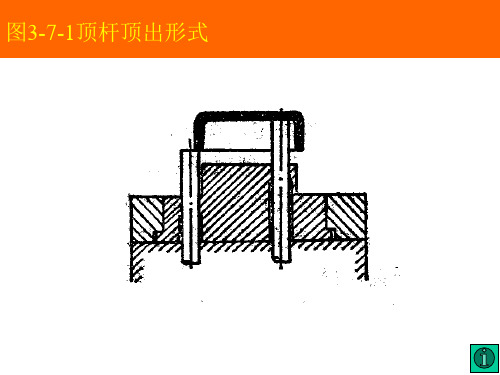
图3-7-55大升角螺杆结构
图3-7-56气(液)动形式
图3-7-57电动机驱动形式
脱摸力计算图
脱摸力计算图
脱摸力计算图
脱摸力计算图
导柱的安装
导柱
导柱的安装
导柱的安装固定形式
导套
盲孔导套的侧壁开孔
导套与孔的固定
直导套的固定
导柱与导套的配合形式
导柱的布置形式
锥面定位
1-圆柱销 2-弹簧 3-摆杆 4-U形限制架 5-注射机顶杆 6-转动
图3-7-23 U形限制架式
图3-7-23 U形限制架式
图3-7-24滑块式二次脱模机构
1-型芯 2-顶出干 3-推板 4-顶杆 5-斜导柱 6-滑块
图3-7-24滑块式二次脱模机构
图3-7-24滑块式二次脱模机构
3-7-25滑块式二次脱模机构
锥面定位
顶杆的形状
顶管顶出机构
1 顶出板 2 顶管 3方销 4 型芯 5 塑件
顶管顶出机构
顶管顶出机构
推板脱模机构
推板脱模机构
带周边间隙的脱模板
进气装置
1 推板 2 顶杆 3弹簧
利用活动镶件脱出塑件
利用型腔的脱模结构
多元件综合脱模机构
讨论题目
请画出这两种顶杆的固定方式
讨论L和H的公差,并说明原因
图3-7-11双脱摸机构
1、型芯 2、型腔
图3-7-12气动双脱模机构
1、4-密封圈 2、3-空气阀门
图3-7-13弹簧顺序脱模机构
图3-7-14拉钩顺序脱模机构
1、压块 2-挡块 3-拉钩 4-拉板 5-弹簧 6-滚轮 7-定模
图3-7-15拉钩顺序脱模机构
1-定模板 2-定模型腔 3-动模板 4-凸块 5-转轴 6-拉钩 7圆销 8- 定伸弹簧 9-定距拉板
4.9 脱模机构设计

(4) 推杆的固定与配合形式
1)推杆的固定形式
a.常用形式 b.采用垫块或垫圈代 替固定板上的沉孔 c.螺钉顶紧推杆 d.推杆固定端无推板 时使用 e.螺钉紧固,用于粗 大推杆 f. 铆钉的形式,用于 直径小的推杆
2)圆形横截面推杆的配合形式
推杆端面应和塑件成型表面在同一平面或高出0.05~0.1mm 推杆与推杆孔有一段配合长度为推杆直径3~5倍的间隙配 合 (H8/f8或H9/f9),其余部分为扩孔。 扩孔直径比推杆大0.5mm。
(1)利用推杆拉断点浇口Байду номын сангаас料 (2)利用拉料杆拉断点浇口凝料
(3)利用侧凹拉断点浇口凝料
(4)利用定模推板拉断点浇口凝料
3.潜伏式浇口凝料的脱出结构
其脱模装置必须分别设置塑件和流道凝料的推出机构, 在推出过程中,浇口被拉断,塑件与浇注系统凝料各自脱 落。 (1)利用脱模板切断浇口凝料
(2)利用差动式推杆切断浇口凝料 (3)
3)摆块拉板式脱模机构 利用活动摆块推动型腔板完成一次脱模,由推杆完成二 次脱模。
4)滑块式
2. 双推板二次脱模机构
这种类型的脱模结构有两组推出装置,利用两组推板的 先后动作完成二次脱模。 1)八字摆杆式脱模机构
① 开模时,当注射机顶杆推动 一次推板时,连接推杆与脱 模板一起以同样速度移动, 使塑件和型腔一起运动而脱 离动模型芯,完成一次推出 动作。
3)定距导柱顺序脱模结构 4)尼龙拉钩式顺序脱模结构
七、浇注系统凝料的脱出机构
1.普通浇注系统凝料的脱出结构
通常采用侧浇口、直接浇口及中心浇口类型的模具,其 浇注系统凝料一般与塑件连在一起。塑件脱出时,先用拉 料杆拉住冷料,使浇注系统凝料留在动模一侧,然后用推 杆或拉料杆推出,靠其自重而脱落。
说明推管脱模机构的基本结构与工作原理

轻松掌握推管脱模机构的基本结构与工作原
理
推管脱模机构是一种常用于塑料、橡胶、玻璃等领域的设备,主要用于将模具内的成型件推出或取出,从而完成整个成型过程。
以下是推管脱模机构的基本结构与工作原理:
一、基本结构
1.主体部分:由机架、滑块、导柱等组成,支撑并引导推板和脱模板的运动。
2.推板:安装在主体上方,提供顶出力,将成型件顶出模具。
3.脱模板:安装在主体下方,用于接受成型件。
4.传动机构:通过电动机、减速器、连杆等传动装置,驱动推板和脱模板运动。
二、工作原理
当模具内的成型件形成后,推板开始向上移动,提供顶出力,将成型件顶出模具。
同时,脱模板开始向上移动,接受并保持成型件,完成脱模工作。
整个推板和脱模板的运动由传动机构驱动,使推板和脱模板可以快速且精确地完成推出和取出的过程。
需要注意的是,推管脱模机构在工作时,需根据成型件的大小、重量、材质等条件,合理地选择推出力和脱模速度,以确保成型件顺
利地推出或取出。
此外,还需根据实际情况进行维护和保养,以保证设备的长期稳定运行。
以上就是推管脱模机构的基本结构与工作原理的介绍。
掌握了这些知识,我们便能更加深入地了解该设备,为其选择、使用和维护提供指导。
4.7脱模机构解析
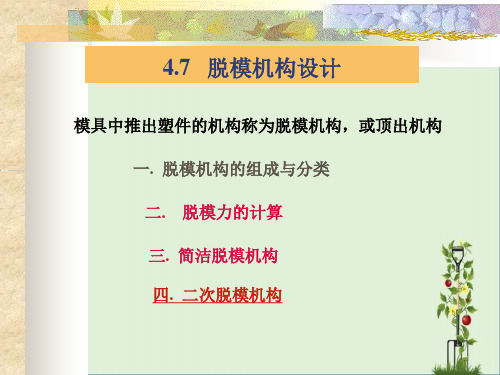
模具中推出塑件的机构称为脱模机构,或顶出机构 一. 脱模机构的组成与分类 二. 脱模力的计算 三. 简洁脱模机构 四. 二次脱模机构
一. 脱模机构的组成与分类
组成
脱模机构一般由三局部组成:推出部件,导向部件,复位部件 推出部件:推杆、拉料杆、推杆固定板,推板等
导向部件:导柱、导套 复位部件:复位杆
3〕直径和数量
保证足够的刚度。可设计成阶梯形
数量应保证顺当脱模且不损伤塑件表观
4〕推杆材料及热处理要求
材料常用T8A,T10A或65Mn,碳素工具钢热处理要求硬度HRC50~54,
弹簧钢热处理硬度要求HRC50~54。
5〕推杆固定形式
推杆
推杆
推杆
推杆
推杆
推杆
(a)
(b)
(c)
(d)
(e)
(f)
图4-79 推杆的固定形式
3〕气动脱模: 利用压缩空气将塑件吹出。
2、按模具构造分
一次推出脱模〔简洁脱模〕、二次推出脱模、动定模双向推出脱模、 挨次脱模、带螺纹塑件脱模塑件不变形损坏 机构推出中心与脱模力中心相重合,推出力分布均匀,
作用点尽可能靠近型芯防止塑件脱模后变形;推出力施于 塑件刚性和强度最大的地方〔如凸缘、加强筋等〕。
留有0.2~025mm的间隙 锥面 协作
推件板常用材料为45钢,热处理要求28~32HRC
四. 二次脱模机构
作用:由于塑件的特殊外形或生产自动化的需要;为避 开一次脱模塑件受力过大。
单推板
摆块拉板式二级脱模机构
双推板
三角滑块式双推板二次脱模机构
螺纹的脱模
强制脱出:弹性较好或较松软的塑件,用于精 度不高和小批量生产的塑件 模外脱出:活动螺纹镶块
说明推管脱模机构的基本结构与工作原理

说明推管脱模机构的基本结构与工作原理推管脱模机构是一种用于混凝土管道生产中的关键设备,其作用是在混凝土管道浇筑完成后帮助将管道从模具中取出并进行后续处理。
这种机构的基本结构和工作原理对于混凝土管道生产的效率和质量具有重要影响。
一般来说,推管脱模机构主要由推杆、升降装置、支撑架、固定块、导向架等部件组成。
推杆是推动混凝土管道脱模的关键部件,其长度和直径需根据具体的管道尺寸而定。
升降装置用于控制推杆的上下运动,以便将管道顺利地脱出模具。
支撑架和固定块则用于固定模具和管道,保证在脱模过程中不发生位移或倾斜。
导向架则用于引导管道在脱模过程中保持正确的位置和方向。
推管脱模机构的工作原理主要是通过推杆的推动和升降装置的控制来完成的。
在脱模前,首先需要将混凝土管道浇筑完成,待混凝土充分硬化后,启动机构将推杆插入管道的一端,并通过升降装置将推杆顶起,逐步推动管道从模具中取出。
在脱模过程中,支撑架和固定块起到了固定管道和模具的作用,保证脱模过程的稳定性。
导向架则通过引导管道的运动,确保管道脱模时保持正确的位置和方向,避免管道变形或损坏。
推管脱模机构的设计和使用对于混凝土管道生产具有重要意义。
合理的结构设计和稳定的工作原理可以提高生产效率,减少生产成本,同时也可以保证混凝土管道的质量和准确度。
因此,在混凝土管道生产中,推管脱模机构是一种不可或缺的设备。
推管脱模机构作为混凝土管道生产中的关键设备,其基本结构和工作原理对于生产效率和产品质量具有重要影响。
通过合理的设计和稳定的工作原理,推管脱模机构可以帮助生产厂家提高生产效率,降低生产成本,保证产品质量,是混凝土管道生产中不可或缺的设备之一。
塑料模具课件_脱模机构
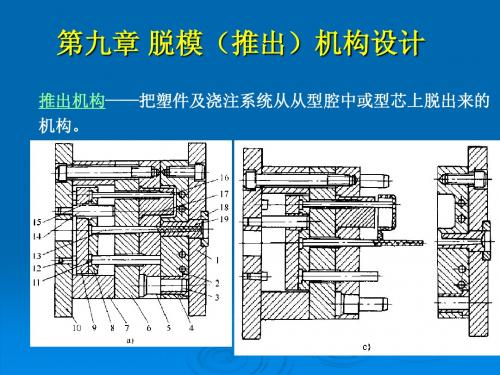
3.模内旋转的脱模方式
(1)螺纹塑件的止转形式
模具设自动脱螺纹机构时塑件外形有止转结构,通常为花纹。
常用模内旋转脱螺纹机构主要有手动脱螺纹和机动脱螺 纹两种。
(2) 手动脱螺纹机构
(3) 机动脱螺纹机构
原理:利用开模时的直线运动,通过齿轮齿条的运动,使 螺纹型芯作回转运动而脱离塑件。 图为,锥齿轮脱螺纹型 芯结构,它用于侧浇口多 型腔模,螺纹型芯只要作 回转运动就可脱出塑件。
p—因塑件收缩对型芯产生的单位正压力(12~20MPa) A—塑件包紧型芯的侧面积(mm2)
F脱= pA(f·cosα-sinα)
总脱模力等于F总=F脱+F大气(大气压力影响:引气、不引气) 以上对脱模力的计算是一种比较粗略的方法。 计算脱模力是为了校核设备的顶出力是否足够,以及校核推出 元件的刚度强度及可靠性。
为减少脱模过程中推件板与型芯之间的摩擦,两者之间留有0.2~ 0.25mm的间隙,并采用锥面配合,以防止推件板 偏斜溢料,锥面 的斜度约取3~5˚左右,图 (b)。
引气装置: 对于大型深腔薄壁容器,推板脱模时 塑件部易形成真空, 使脱模困难,甚至还会使塑件变形或损坏,应在凸模上附设引 气装置,如图(推件板引气)。(推件板不引气)
加粗,增加刚性。
顶盘式推杆:锥面推杆,推出面积较大,适合于深筒形塑件 推出。
b)
c)
d)
2.推杆的固定及配合
(1)推杆的固定
2.推杆的配合
推杆固定板上的孔为d+1mm;推杆台阶部分的直径为
d+5mm;推杆固定板上的台阶孔为d+6mm。推杆与固定 板配合长度为S(一般采用H8/f8配合)
S 可取12~15mm;当d>5mm时, S=(2~3)d (d为推杆直径),配合部分表面Ra=0.8μm。 推杆与塑料接触并与孔经常摩擦,因此多采用热处理后硬度 高的材料制作。推杆材料常用T8A、T10A等碳素工具钢 (50 ~ 54HRC自制推杆)或65Mn (46 ~ 50HRC市场上的 推杆标准件)
第六节 塑件脱模机构设计

简单脱模机构:在动模一边施加一次
推出力,就可实现塑件脱模的机构
双脱模机构
顺序脱模机构 二次脱模机构
浇注系统脱模机构
带螺纹塑件脱模机构
二、脱模力的计算
脱模力的组成
包紧力产生摩擦力 塑件与金属的粘附力 机构运动产生的摩擦阻力 克服大气压力(特指盲孔的筒、壳类零件) 注:脱模力不为恒定值 开模瞬间克服阻力最大——初始脱模力 以后脱模所需力——相继脱模力
推管推出动作模拟
推管与型芯的配合长度为推出距离s+3~5mm 为保护型芯和型腔,推管不易与成型表面接触 推管配合公称外径宜小于型腔内径 推管配合公称内径宜大于型芯内径 注:当凹模设在定模边,不存在内径与推管摩擦
2.顶管脱模机构
(2)主型芯固定在动模型芯固定板上
特点:型芯长度缩短, 但推出行程包含在动模 板内,动模厚度增加。
推杆推出机构形式
推杆推出机构形式
三、简单脱模机构
1、顶杆脱模机构
设计要点:
(2)顶杆直径必须有足够的强度,能承受顶出时 的冲击力。顶杆直径一般取2.5~12mm,对3 毫米以下的顶杆建议采用阶梯式结构, 即顶杆下部加粗以增加强度;
顶杆的其他固定形式:
(3)顶杆装配后不应有轴向窜动,其端 面应与型芯齐平。
2)球头拉料杆
2)球头拉料杆
4.5 注射模具浇注系统设计
2)菌头拉料杆
4.5 注射模具浇注系统设计
2)圆锥形拉料杆
圆锥 头形
复式圆 锥头形
没有储存冷料的作用,依靠塑料的包紧力将主流道 凝料拉住。 用于推板脱模机构上
4.5 注射模具浇注系统设计
3)圆锥形拉料杆
平头锥形 拉料杆
3)带推杆推出的拉料穴
- 1、下载文档前请自行甄别文档内容的完整性,平台不提供额外的编辑、内容补充、找答案等附加服务。
- 2、"仅部分预览"的文档,不可在线预览部分如存在完整性等问题,可反馈申请退款(可完整预览的文档不适用该条件!)。
- 3、如文档侵犯您的权益,请联系客服反馈,我们会尽快为您处理(人工客服工作时间:9:00-18:30)。
第八章脱模机构胶件脱模是注射成型过程中最后一个环节,脱模质量好坏将最后决定胶件的质量;当模具打开时,胶件须留在具有脱模机构的半模(常在动模)上,利用脱模机构脱出胶件。
脱模设计原则:(1)为使胶件不致因脱模产生变形,推力布置尽量均匀,并尽量靠近胶料收缩包紧的型芯,或者难于脱模的部位,如胶件细长柱位,采用司筒脱模。
(2)推力点应作用在胶件刚性和强度最大的部位,避免作用在薄胶位,作用面也应尽可能大一些,如突缘、(筋)骨位、壳体壁缘等位置,筒形胶件多采用推板脱模。
(3)避免脱模痕迹影响胶件外观,脱模位置应设在胶件隐蔽面(内部)或非外观表明;对透明胶件尤其须注意脱模顶出位置及脱模形式的选择。
(4)避免因真空吸附而使胶件产生顶白、变形,可采用复合脱模或用透气钢排气,如顶杆与推板或顶杆与顶块脱模,顶杆适当加大配合间隙排气,必要时还可设置进气阀。
(5)脱模机构应运作可靠、灵活,且具有足够强度和耐磨性,如摆杆、斜顶脱模,应提高滑碰面强度、耐磨性,滑动面开设润滑槽;也可渗氮处理提高表面硬度及耐磨性。
(6)模具回针长度应在合模后,与前模板接触或低于0.1mm,如图8.1.1所示。
(7)弹簧复位常用于顶针板回位;由于弹簧复位不可靠,不可用作可靠的先复位。
回针接触前模板或低于0.1mm面针板底针板回针回位弹簧顶针防转销扁顶针有托顶针顶位斜面8.1 顶针、扁顶针脱模胶件脱模常用方式有顶针、司筒、扁顶针、推板脱模;由于司筒、扁顶价格较高(比 顶针贵8~9倍),推板脱模多用在筒型薄壳胶件,因此,脱模使用最多的是顶针。
当胶件周围无法布置顶针,如周围多为深骨位,骨深 15mm 时,可采用扁顶针脱模。
顶针、扁顶针表面硬度在HRC55以上,表面粗糙度Ra1.6以下。
顶针、扁顶针脱模机构如图8.1.1所示,设置要点如下:(1)顶针直径 d Ø2.5mm 时,选用有托顶针,提高顶针强度。
(2)扁顶针、有托顶针 K H 。
(3)顶位面是斜面,顶针固定端须加定位销;为防止顶出滑动,斜面可加工多个R 小槽,如图8.1.2所示。
(4)扁顶针、顶针与孔配合长度L=10~15mm ;对小直径顶针L 取直径的5~6倍。
(5)顶针距型腔边至少0.15mm ,如图8.1.2所示。
(6)避免顶针与前模产生碰面,如图8.1.3所示,此结果易损伤前模或出 披峰。
顶针位的布置原则(另见5.5节)。
8.1.1 顶针、扁顶针配合间隙顶针、有托顶针、扁顶针配合部位 如图8.1.4图8.1.5图8.1.6所示,配合要 求如下:避免与前模碰面图8.1.3图端面齐平配合段图8.1.2(1)顶针头部直径d 及扁顶针配合尺寸t 、w 与后模配合段按配作间隙 0.04mm 配合。
(2)顶针、扁顶针孔在其余非配合段的尺寸为d 0.8mm 或d1 0.8mm ,台阶固定端与面针板孔间隙为0.5mm 。
(3)顶针、扁顶针底部端面与面针板底面必须齐平。
(4)如图8.1.7所示,顶针顶部端面与后模面应齐平, 高出后模表面 e 0.1mm 。
8.1.2 顶针固定(1)固定顶针一般是在面针板加工台阶固定,如图8.1.4所示。
为防止顶针转动,常 用方式有两种:一种顶针轴向台阶边加定位销定位如图8.1.8所示;另一种横向加定位销定位如图8.1.9所示。
(2)无头螺丝固定,如图8.1.10所示,此方式是在顶针端部无垫板时使用,常用在固定司筒针和三板模球形拉料杆上。
图8.1.8图8.1.9图8.1.10图8.1.6图8.1.78.2 司筒脱模司筒脱模如图8.2.1所示,司 筒常用于长度 20mm 的圆柱位脱模。
标准司筒表面硬度HRC 60,表面粗 糙度 Ra1.6。
另外,司筒的壁厚应 1mm ;布置司筒时,司筒针固定位 不能与顶棍孔发生干涉。
8.2.1 司筒配合要求司筒脱模配合关系如图8.2.2 图8.2.3所示,配合要求如下:(1)司筒与后模配合段长度为L=10~15mm ,其直径D 配合间隙应 0.04mm 。
(2)其余无配合段尺寸为D 0.8mm 。
8.2.2 大司筒针固定司筒针固定于底板上,通常使用无头螺 丝如图8.2.1所示。
当司筒针直径d 8mm 或 5/16 时,固定端采用垫块方式固定,如图 8.2.4所示。
图8.2.2台阶(猪嘴形)柱位 图8.2.3图8.2.4垫块图8.2.1顶棍孔司筒 司筒针 无头螺丝台阶(猪嘴形)圆柱位圆柱位8.3 推板脱模推板脱模如图8.3.1所示。
此机构 适用于深筒形、薄壁和不允许有顶针 痕迹的胶件,或一件多腔的小壳体(如 按钮胶件)。
其特点是推力均匀,脱模 平稳,胶件不易变形。
不适用于分模 面周边形状复杂,推板型孔加工困难 的胶件。
8.3.1 机构要点推板脱模机构要点:(1)推板与型芯的配合结构应呈锥面;这样可减少运动擦伤,并起到辅助导向作用; 锥面斜度应为3~10 ,如图8.3.2所示。
(2)推板内孔应比型芯成形部分(单边)大0.2~0.3mm,如图8.3.2所示。
(3)型芯锥面采用线切割加工时,注意线切割与型芯顶部应有 0.1mm 的间隙,如图 8.3.3所示;避免线切割加工使型芯产生过切,如图8.3.4所示。
(4)推板与回针通过螺钉连接,如图8.3.1所示。
(5)模坯订购时,注意推板与边钉配合孔须安装直司(直导套),推板材料选择应相同 于M202。
(6)推板脱模后,须保证胶件不滞留在推板上。
8.3.2 推板机构示例图8.3.1回针推板边钉图推板型芯推板 型芯固定板 配合锥面图8.3.3型芯产生过切线切割加工线图8.3.4(1)如图8.3.4所示,此模一件多腔,线切割加工型芯、推板、固定板。
推板模通常 采用球形拉料杆,浇道只在前模开设,如图8.3.5所示。
此推板模线切割线将米仔位留在型芯内,防止胶件滞留在推板上,如图8.3.6所示。
(2)如图8.3.7所示,此推板模固定板在推板内。
特点:使后模板B 变小,减少线切割加工量。
模具上固定板用螺钉、圆柱销与托板连接,结构如图8.3.8所示。
线切割加工线将圆柱位留在型芯内,使胶件能顺利脱模,如图8.3.9所示。
球形拉料杆前模开浇道图8.3.5球形拉料杆图8.3.4推板 型芯固定板型芯前模型腔边缘 线切割线 胶件米仔 图8.3.6推板托板线切割线 前模型腔边缘 型芯胶件柱位图8.3.9图螺钉 圆柱销固定板 推板托板8.4 推块脱模对胶件表面不允许有顶针痕迹(如 透明胶件),且表面有较高要求的胶件, 可利用胶件整个表面采用推块顶出,如 图8.4.1所示。
8.4.1 机构要点推块脱模要点:(1)推块应有较高的硬度和较小的表面粗糙度;选用材料应与呵镶件有一定的硬度 差(一般在HRC5度以上);推块需渗氮处理(除不锈钢不宜渗氮外)。
(2)推块与呵镶件的配合间隙以不溢料为准, 并要求滑动灵活;推块滑动侧面开设润滑槽。
(3)推块与呵镶件配合侧面应成锥面,不宜 采用直身面配合。
(4)推块锥面结构应满足如图8.4.2 所示; 顶出距离(H1)大于胶件顶出高度,同时小于推 块高度的一半以上。
(5)推块推出应保证稳定,对较大推块须设置两个以上的推杆。
8.4.2 推块机构示例(1)胶件如图8.4.3所示,推块机构如图8.4.4所示。
此机构考虑推块脱模面积大,顶力均匀特点,采用内、外推块顶出,使脱模平衡。
外推块内推块推块图8.4.1呵镶件图8.4.2推块限位块 推杆(2)胶件如图8.4.5所示,胶件要求不能有顶针痕迹;推块机构如图8.4.6所示。
此机构应用镶件推块脱模,推块痕迹均匀的特点。
(3)透明胶件不能有顶针痕迹,采用推块机构脱模,如图8.4.7所示。
如图8.4.6推块限位块图8.4.5推块边线图8.4.7推块透明胶片8.5 二次脱模为获得可靠的脱模效果,分解胶件脱模阻力,经二次脱模动作,来完成胶件出模的 机构称二次脱模机构,如图8.5.1所示。
二次脱模机构示例:(1)胶件如图8.5.2 所示,两骨间有半圆凹陷,被后模 型腔包紧。
脱模机构如图8.5.3 所示,第一次脱模使胶件脱 出后模型腔,为强脱变形提供空间;第二次脱模,由顶针脱 模,胶件半圆凹陷位强脱出型芯推块。
该机构运动过程:第 一次脱模四块顶针板都运动,带着顶针、型芯推块同时运动, 脱模距离 h ,使胶件脱出后模型腔,一次脱模完成。
当继续运动至摆块碰上限位面后,摆块摆动使上面两块针板快速运动,带动顶针脱出胶件,完成二次脱模。
此机构须注意: h1 > h ,H > 10mm h1 (二次脱模运动距离)。
第一次脱模出内芯,为胶件提供变形空间第二次脱模,胶件凹凸位变形后强脱出模图8.5.1胶件凹凸位被型芯包紧图8.5.3二次脱模摆块 方铁限位面图8.5.2型芯推块 顶针 胶件半圆凹陷(2)胶件上入浇口、行位分模线如图8.5.5 所示。
由于潜浇道须设在斜顶行位块上,穿过斜顶块入胶, 模具需实现浇道先脱出斜顶块,模具采用二次顶出机构如图8.5.6 所示。
该机构第一次脱模时,拉料杆使浇 道不动,顶针、斜顶脱出胶件 M 距离,使胶件与潜浇道断开,潜浇道从斜顶行位块中变形后脱出,第一次脱模结束。
第二次脱模四块顶针板都动,顶出胶件、浇道脱出后模型腔。
需注意,为保证潜浇道脱出斜顶块,须M > S (潜浇 道长度)。
入浇口行位分模线 图8.5.5图8.5.6拉料杆顶针斜顶行位块 拉料杆潜浇道放大图8.6 先复位机构当行位型芯与顶针位在开模方向上投影相重合,是发生干涉的必要条件。
先复位机 构是保证行位(型芯)复位时,避免与顶针发生干涉,如图8.6.1所示。
如图8.6.2所示,为避免行位型芯与顶针发生 干涉,须满足的条件是:当行位型芯顶端与顶针投影重合时,行位型 芯与顶针垂直方向应有间隙,即 F > f ;行位继 续行入距离C ,同时顶针退回距离f ;此时 f C ctg 可避免干涉,不需先复位机构;当 f C ctg 会发生干涉,必须增设先复位机构。
摆块先复位机构:如图8.6.3所示,为防止行位型芯与顶针合模时发生干涉,常用摆块先复位机构。
该图8.6.1顶针行位型芯行位型芯顶针与型芯投影重合局部放大图图8.6.2行位型芯顶针行位型芯顶端与顶针投影重合边机构在合模过程中,复位杆先推动摆块,摆块迫使压块回动,从而带动顶针板完成先复位。
机构复位杆长度须保证 Z A + 15mm 。
图8.6.3闭模状态开模状态摆块 复位杆 压块导向块挡销。