加氢裂化工艺及过程
加氢裂化工艺及过程ppt课件

ppt课件.
2
催化加氢技术
2.0 加氢裂化工艺流程
2.1 两段法加氢裂化
2.2 单段加氢裂化
2.3 一段串联(单程通过,未转化油全循环、部分循环)
3.0 中压加氢裂化及相关的加氢转化技术
3.1 提高十六烷值技术〔MCI〕
3.2 低凝柴油生产技术〔HDW〕
3.4 柴油深度加氢脱硫脱芳烃技术
3.5 提高车用汽油质量的相关技术
FCC比加氢裂化要经济, 加氢裂化的发展再度受到冲击而有所减
缓。
ppt课件.
11
催化加氢技术
◎ 70年代加氢裂化已成为一项成熟的工艺技术, 催化剂的发展, 允 许现有装置的设备转向重质原料的加工, 其柴油的收率可高达 95v%(对原料油)。
◎ 加氢裂化是增产石脑油、喷气燃料最有效的途径, 这是其它炼油 技术所无法替代的。
催化加氢技术
◎ 在60年代, 加氢裂化能满足石脑油、喷气燃料、柴油、润滑油基 础油、低硫燃料油、液化石油气及石油化工原料生产的要求,
充分证明加氢裂化技术具有极重要的作用和广泛的应用前景。
◎ 60年代末和70年代初, 是美国加氢裂化迅速增长的时期; 70年代 中
期, FCC广泛使用了分子筛催化剂, 氢气费用高, 对于生产汽油,
4.6 加氢催化剂的卸出
4.7 加氢裂化装置现场事故剖析
ppt课件.
4
催化加氢技术
1.0 概 述
◎ 加氢裂化具有加工原料范围宽、原料适应性强、产品方案灵 活、产品质量好、液体产品收率Байду номын сангаас等独具的特点。
◎ 能生产从液化石油气、石脑油、喷气燃料、柴油到蒸汽裂解、 润滑油基础油等多种优质产品和石油化工原料。
加氢裂化工艺流程介绍
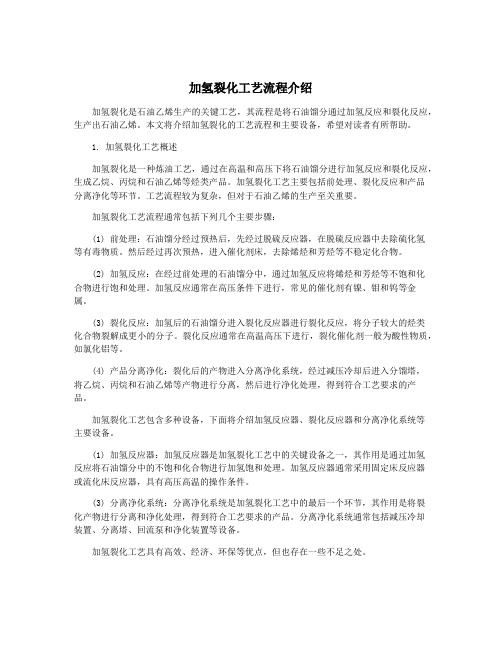
加氢裂化工艺流程介绍加氢裂化是石油乙烯生产的关键工艺,其流程是将石油馏分通过加氢反应和裂化反应,生产出石油乙烯。
本文将介绍加氢裂化的工艺流程和主要设备,希望对读者有所帮助。
1. 加氢裂化工艺概述加氢裂化是一种炼油工艺,通过在高温和高压下将石油馏分进行加氢反应和裂化反应,生成乙烷、丙烷和石油乙烯等烃类产品。
加氢裂化工艺主要包括前处理、裂化反应和产品分离净化等环节。
工艺流程较为复杂,但对于石油乙烯的生产至关重要。
加氢裂化工艺流程通常包括下列几个主要步骤:(1) 前处理:石油馏分经过预热后,先经过脱硫反应器,在脱硫反应器中去除硫化氢等有毒物质。
然后经过再次预热,进入催化剂床,去除烯烃和芳烃等不稳定化合物。
(2) 加氢反应:在经过前处理的石油馏分中,通过加氢反应将烯烃和芳烃等不饱和化合物进行饱和处理。
加氢反应通常在高压条件下进行,常见的催化剂有镍、钼和钨等金属。
(3) 裂化反应:加氢后的石油馏分进入裂化反应器进行裂化反应,将分子较大的烃类化合物裂解成更小的分子。
裂化反应通常在高温高压下进行,裂化催化剂一般为酸性物质,如氯化铝等。
(4) 产品分离净化:裂化后的产物进入分离净化系统,经过减压冷却后进入分馏塔,将乙烷、丙烷和石油乙烯等产物进行分离,然后进行净化处理,得到符合工艺要求的产品。
加氢裂化工艺包含多种设备,下面将介绍加氢反应器、裂化反应器和分离净化系统等主要设备。
(1) 加氢反应器:加氢反应器是加氢裂化工艺中的关键设备之一,其作用是通过加氢反应将石油馏分中的不饱和化合物进行加氢饱和处理。
加氢反应器通常采用固定床反应器或流化床反应器,具有高压高温的操作条件。
(3) 分离净化系统:分离净化系统是加氢裂化工艺中的最后一个环节,其作用是将裂化产物进行分离和净化处理,得到符合工艺要求的产品。
分离净化系统通常包括减压冷却装置、分离塔、回流泵和净化装置等设备。
加氢裂化工艺具有高效、经济、环保等优点,但也存在一些不足之处。
加氢裂化工艺流程

加氢裂化工艺流程1. 简介加氢裂化是一种常用的炼油工艺,用于将重质石油馏分转化为高辛烷值的汽油。
该工艺通过在高温和高压下将长链烃分子分解为较短链的烃类,同时加入氢气来抑制烃类的进一步裂解和脱氢反应。
加氢裂化工艺流程包括预热、加氢裂化反应、分离和再生等步骤。
2. 步骤和流程2.1 预热首先,原料石油馏分经过预热过程,将其加热到适宜的温度。
预热有助于提高反应速率和转化率,并减少催化剂的热损失。
预热的温度和时间根据具体的石油馏分和工艺条件来确定。
2.2 加氢裂化反应预热后的石油馏分进入加氢裂化反应器,与催化剂和氢气一起进行反应。
催化剂通常采用铝硅比较高的沸石催化剂,具有较好的活性和选择性。
反应器内的温度和压力控制在适宜的范围内,以提高反应速率和转化率。
在加氢裂化反应中,长链烃分子发生裂解和氢化反应,生成较短链的烃类和饱和烃。
裂解产物中的短链烃类主要是高辛烷值的汽油组分,而饱和烃主要是石蜡。
2.3 分离反应器出口的混合物进入分离器,通过分馏和其他分离操作将产物分离。
分离过程主要包括汽油、石蜡、烯烃和气相的分离。
其中,石蜡可以作为工业原料或进一步加工成蜡烛、润滑油等产品。
2.4 再生经过分离的催化剂进入再生器,通过加热和氢气的作用将吸附在催化剂上的碳杂质和焦炭燃烧掉,再生催化剂的活性。
再生后的催化剂回流到加氢裂化反应器中,继续参与反应。
3. 工艺优化和改进为了提高加氢裂化工艺的效果和经济性,可以采取以下措施进行优化和改进:3.1 催化剂的选择和改进选择具有较高活性和选择性的催化剂,通过改变催化剂的物理和化学性质来提高其性能。
例如,改变催化剂的孔径大小、比表面积和酸性等,可以调节反应的速率和产物分布。
3.2 反应条件的优化通过调整反应器的温度、压力和氢气的用量等参数,优化反应条件,提高反应速率和转化率。
同时,可以采用多级反应器和换热器等装置,提高能量利用率和催化剂的利用率。
3.3 废气处理加氢裂化过程中产生的废气中含有大量的硫化物、氮化物和有机物等污染物,需要进行适当的处理。
加氢裂化工艺流程
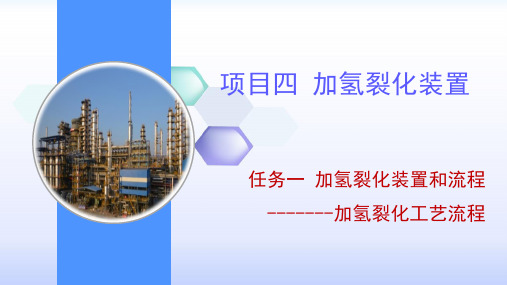
8.1.2金融投资理财国内外业务状况
1.美国理财业务的状况
美国理财业务经历了初创期、扩张期、成熟稳定期三个阶段。最早提供该服 务的是20世纪30年代的保险营销人员。由于1929年的经济危机,他们为了更好地 开展业务,对客户进行了一些简单的个人生活规划和综合资产运用策略,成为今 天个人理财规划师的前身。二战后,经济的复苏和社会财富的日益积累使美国个 人理财业务进入了扩张时期。从业人员不断增加,但由于缺乏相关的专业职业认 证,导致市场上鱼龙混杂,行业混乱。随着CFP(CertifiedFinancialPlanner) 制度逐步的建立,市场混乱问题才得以解决,得以规范化、专业化发展理财业务,
日本的证券市场已经相当成熟,东京股市已经成为日本经济的晴雨表,同时 在一定程度上也反映了亚洲经济发展的状况,已经成为继纽约和伦敦证券交易所 之后最为广大投资者所关注的证券交易所之一。日本的贷款也渗透到了每个人的 日常生活中,最主要的个人贷款就是住房贷款及消费贷款。
近几年,日本的理财业务发展极快。FP(FinancialPlanning)这个概念迅 速普及,即财务管理。它的发展背景主要有三个因素:金融资产增加;金融自由 化的发展;老龄化的高速发展。日本进入90年代以后,经济增长缓慢,政府又采 用低利率政策,在这种情况下,对FP的需求日益增加,各种专业理财咨询机构也 迅速地发展,如其国内的FP协会等。
3.国内理财业务状况
国内金融业的理财业务发展较晚,直到20世纪90年代中期,各金融机构才 开始重视这一业务。20世纪90年代末期,由于中国经济持续20年的高速增长, 公众的收入普遍增加,个人金融资产日益膨胀,人们开始关注自己资产的安全 性、收益性和流动性,因而有了较强烈的理财需求。
同时,中国加入了WTO,国外金融机构正在逐渐进入中国市场,其所经营 的包括理财的各种业务对国内金融机构造成极大冲击。另一方面,国内银行传 统零售业务的利润水平在逐渐下降,盈利能力受到了严峻的挑战。外资银行利 用其丰富的零售经验和混业优势,以优质客户为目标和国内金融机构展开激烈 竞争。
加氢裂化工艺流程介绍

加氢裂化工艺流程介绍加氢裂化是一种重要的石油化工工艺,主要用于将重质石油馏分或原油中的长链烃类分子切割成较短链烃类分子,以提高产品的转化率和降低其粘度,从而达到提高产品质量和增加产品产量的目的。
该工艺主要包括催化剂的选择、反应装置的设计、反应条件的控制等几个方面,下面将对加氢裂化工艺的流程进行详细介绍。
一、催化剂的选择加氢裂化反应的催化剂通常为金属催化剂,如镍、钴、铂、钒等。
这些金属催化剂能够在合适的条件下催化烃类分子的裂解反应,生成较短链烃类分子和氢气。
通常还需在催化剂中加入一定量的活性组分,如氧化物、氧化钠、氧化铝等,以增加催化剂的活性和稳定性。
二、反应装置的设计加氢裂化反应通常在催化裂化装置中进行。
这种反应装置通常由裂化炉、加氢装置、冷却装置和分离装置等组成。
裂化炉是反应装置的核心部件,是将原料石油馏分或原油送入裂化反应器进行加热和裂化的地方。
加氢装置用于向裂化反应器中注入氢气,以提高裂化反应的效率和选择性。
冷却装置用于冷却反应产物,并将其中的气态产物液化。
分离装置则用于将反应产物中的各种组分进行分离,并提取所需的产品。
三、反应条件的控制加氢裂化反应的温度、压力、空速、氢油比等条件对反应的效率和选择性具有重要影响。
通常情况下,加氢裂化反应的温度为400-500℃,压力为2-8 MPa,空速为1-10 h-1,氢油比为1000-2000 Nm3/m3。
在这些条件下,可获得较高的产品转化率和较好的产品选择性。
加氢裂化工艺通常包括以下几个步骤:1. 原料处理:原料石油馏分或原油经过脱盐、脱硫等处理后,送入加氢裂化装置进行加热和裂化。
在这个过程中,通过加热将原料加热至裂化反应所需温度,并将其中的一部分烃类分子裂解成较短链烃类分子和氢气。
3. 冷却和分离:经过加氢裂化反应后,产生大量的气态产物和液态产物需要进行冷却和分离。
通过冷却装置将气态产物冷却成液态产物,并通过分离装置将其中的各种组分进行分离,提取所需的产品。
加氢裂化工艺流程概述
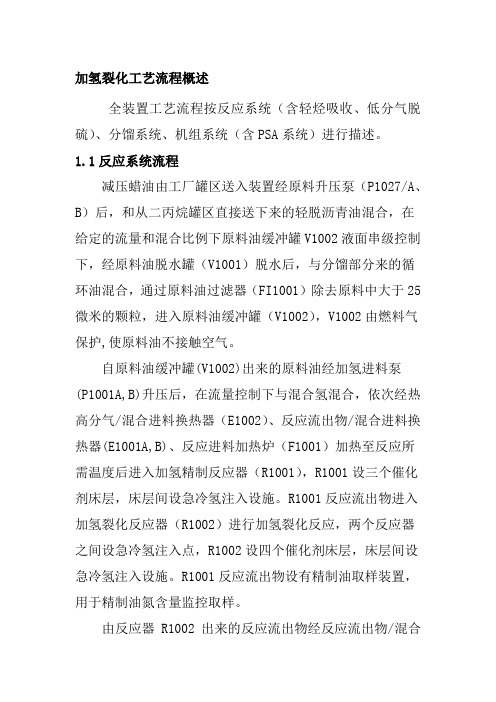
加氢裂化工艺流程概述全装置工艺流程按反应系统(含轻烃吸收、低分气脱硫)、分馏系统、机组系统(含PSA系统)进行描述。
1.1反应系统流程减压蜡油由工厂罐区送入装置经原料升压泵(P1027/A、B)后,和从二丙烷罐区直接送下来的轻脱沥青油混合,在给定的流量和混合比例下原料油缓冲罐V1002液面串级控制下,经原料油脱水罐(V1001)脱水后,与分馏部分来的循环油混合,通过原料油过滤器(FI1001)除去原料中大于25微米的颗粒,进入原料油缓冲罐(V1002),V1002由燃料气保护,使原料油不接触空气。
自原料油缓冲罐(V1002)出来的原料油经加氢进料泵(P1001A,B)升压后,在流量控制下与混合氢混合,依次经热高分气/混合进料换热器(E1002)、反应流出物/混合进料换热器(E1001A,B)、反应进料加热炉(F1001)加热至反应所需温度后进入加氢精制反应器(R1001),R1001设三个催化剂床层,床层间设急冷氢注入设施。
R1001反应流出物进入加氢裂化反应器(R1002)进行加氢裂化反应,两个反应器之间设急冷氢注入点,R1002设四个催化剂床层,床层间设急冷氢注入设施。
R1001反应流出物设有精制油取样装置,用于精制油氮含量监控取样。
由反应器R1002出来的反应流出物经反应流出物/混合进料换热器(E1001)的管程,与混合原料油换热,以尽量回收热量。
在原料油一侧设有调节换热器管程出口温度的旁路控制,紧急情况下可快速的降低反应器的入口温度。
换热后反应流出物温度降至250℃,进入热高压分离器(V1003)。
热高分气体经热高分气/混合进料换热器(E1002)换热后,再经热高分气空冷器(A1001)冷至49℃进入冷高压分离器(V1004)。
为了防止热高分气在冷却过程中析出铵盐堵塞管路和设备,通过注水泵(P1002A,B)将脱盐水注入A1001上游管线,也可根据生产情况,在热高分顶和热低分气冷却器(E1003)前进行间歇注水。
加氢裂化工艺

加氢裂化工艺一、引言加氢裂化工艺是一种重要的炼油工艺,主要用于将重质石油馏分转化为高级汽油和柴油。
本文将详细介绍加氢裂化工艺的流程和设备组成。
二、加氢裂化工艺流程1. 原料预处理原料先经过蒸馏分离出各个馏分,然后将需要进行加氢裂化的重质馏分送入预处理装置。
预处理装置主要包括加热器、换热器和精密过滤器等设备,其作用是将原料加热至适宜温度,去除杂质和水分。
2. 加氢反应预处理后的原料进入反应器,与催化剂在高压下进行反应。
催化剂通常由铝酸盐、硅酸盐或钼酸盐等组成。
反应器内的温度通常在400-500℃之间,压力在20-30MPa之间。
加氢反应会使原料中的大分子链断裂,并与氢气发生反应生成较轻的烃类物质。
3. 分离和净化经过反应后的产物进入分离塔,塔内通过不同温度和压力的分离区间,将产物分为不同的组分。
其中,高级汽油和柴油是主要产品,其余产物可用于其他工艺或作为燃料。
产物中可能含有少量杂质和催化剂残留,需要通过净化装置进行处理。
4. 催化剂再生反应器中使用的催化剂在一定时间后会失效,需要进行再生。
催化剂再生主要包括焙烧、酸洗和还原等步骤。
焙烧将催化剂中的碳积聚物烧掉,酸洗去除催化剂表面的杂质,还原则是将氧化态的金属还原成金属原子。
三、加氢裂化工艺设备组成1. 反应器反应器是加氢裂化工艺中最重要的设备之一。
反应器通常由钢制成,内部涂有耐高温、耐腐蚀的陶瓷材料。
反应器通常具有自动控制系统和安全保护系统。
2. 分离塔分离塔是将产物分离为不同组分的关键设备。
分离塔通常由钢制成,内部涂有耐高温、耐腐蚀的陶瓷材料。
分离塔通常具有自动控制系统和安全保护系统。
3. 加热器加热器是将原料加热至适宜温度的设备。
加热器通常由钢制成,内部涂有耐高温、耐腐蚀的陶瓷材料。
加热器通常具有自动控制系统和安全保护系统。
4. 换热器换热器是将反应产生的废气或废水与进料进行换热的设备。
换热器通常由钢制成,内部涂有耐高温、耐腐蚀的陶瓷材料。
换热器通常具有自动控制系统和安全保护系统。
加氢裂化工艺流程
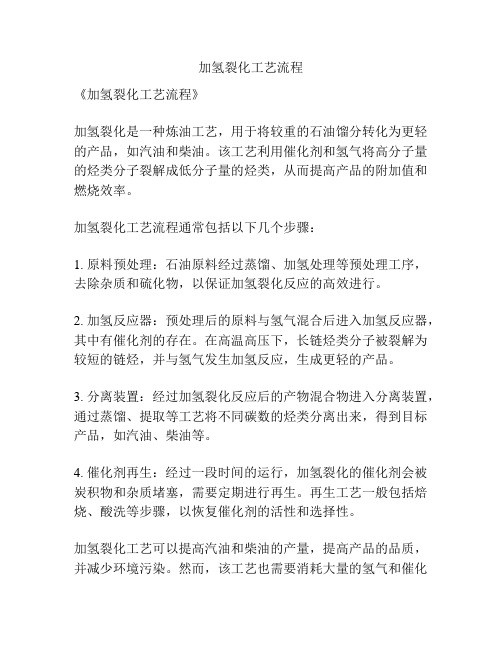
加氢裂化工艺流程
《加氢裂化工艺流程》
加氢裂化是一种炼油工艺,用于将较重的石油馏分转化为更轻的产品,如汽油和柴油。
该工艺利用催化剂和氢气将高分子量的烃类分子裂解成低分子量的烃类,从而提高产品的附加值和燃烧效率。
加氢裂化工艺流程通常包括以下几个步骤:
1. 原料预处理:石油原料经过蒸馏、加氢处理等预处理工序,去除杂质和硫化物,以保证加氢裂化反应的高效进行。
2. 加氢反应器:预处理后的原料与氢气混合后进入加氢反应器,其中有催化剂的存在。
在高温高压下,长链烃类分子被裂解为较短的链烃,并与氢气发生加氢反应,生成更轻的产品。
3. 分离装置:经过加氢裂化反应后的产物混合物进入分离装置,通过蒸馏、提取等工艺将不同碳数的烃类分离出来,得到目标产品,如汽油、柴油等。
4. 催化剂再生:经过一段时间的运行,加氢裂化的催化剂会被炭积物和杂质堵塞,需要定期进行再生。
再生工艺一般包括焙烧、酸洗等步骤,以恢复催化剂的活性和选择性。
加氢裂化工艺可以提高汽油和柴油的产量,提高产品的品质,并减少环境污染。
然而,该工艺也需要消耗大量的氢气和催化
剂,并且对原料的要求较高,因此需要精细的工艺控制和运行管理。
随着石油工业的不断发展,加氢裂化工艺也在不断完善和优化,以适应市场的需求和环保的要求。
- 1、下载文档前请自行甄别文档内容的完整性,平台不提供额外的编辑、内容补充、找答案等附加服务。
- 2、"仅部分预览"的文档,不可在线预览部分如存在完整性等问题,可反馈申请退款(可完整预览的文档不适用该条件!)。
- 3、如文档侵犯您的权益,请联系客服反馈,我们会尽快为您处理(人工客服工作时间:9:00-18:30)。
油中稠环芳烃的富积。
◎ CGO氮含量高, 或多或少含有焦粉, 直接混兑应严格控制(一般为
催化加氢技术
◎ 加氢裂化进料已延伸到脱沥青油(DAO), 其未转化油可用来生产 重质润滑油基础油。 ◎ 通过对原料油的合理配置、催化剂的选择及工艺条件的优化, 加 氢裂化技术可被广泛用来生产从液化石油气、石脑油、喷气燃 料、柴油到蒸汽裂解原料和润滑油基础油等多种优质石油产品 及下游装置的进料。
相同.
◎ 原料油中类烃分子的加氢裂化反应, 与FCC过程类同,其反应历
程 都遵循羰离子(正碳离子)反应机理和正碳离子β位断链的原则; 所不同的是, 加氢裂化过程自始至终伴有加氢反应, 并具有以下
催化加氢技术
≰ 多环芳烃加氢裂化以逐环加氢饱和/开环的方式进行, 生成小分 子 的烷烃及环烷-芳烃; ≰ 两环以上的环烷烃, 发生开环裂解、异构,最终生成单环环烷烃 及较小分子的烷烃; ≰ 单环芳烃、环烷烃比较稳定, 不易加氢饱和、开环, 主要是断侧 链或侧链异构,并富集在石脑油中; ≰ 烷烃的异构、裂化同时进行, 反应生成物中的异构烃含量, 一般 超过其热力学平衡值; ≰ 烷烃的加氢裂化在其正碳离子的β位处断链, 很少生成 C3 以下
催化加氢技术
≰ 若受港口码头、道路、桥梁、涵洞等运输条件的制约,采用三 个反应器的两段裂化比采用双系列并联(共4个反应器), 可节省 投资510%。 ≰ Union oil 公司当时认为, 一段串联(一段裂化)的流程适宜100万 吨/年以下规模的装置; 100 150万吨/年规模的装置,以采用
催化加氢技术
◎ 1959年Chevron研究公司宣布“加氢异构裂化工艺”在里奇蒙炼 厂பைடு நூலகம்投入工业运转, 证实该发明的催化剂可允许在200400 ℃ 、3.5 14MPa 的条件下操作后, 加氢裂化从此走出低谷。
◎ 1960年UOP公司开发了 ―Lomax‖加氢裂化工艺;Union oil
公司开发了“Unicacking‖工艺; 60年代加氢裂化作为炼油
4.5 加氢裂化催化剂器外硫化技术
4.6 加氢催化剂的卸出 4.7 加氢裂化装置现场事故剖析
催化加氢技术
1.0 概 述
◎ 加氢裂化具有加工原料范围宽、原料适应性强、产品方案灵
活、产品质量好、液体产品收率高等独具的特点。
◎ 能生产从液化石油气、石脑油、喷气燃料、柴油到蒸汽裂解、
润滑油基础油等多种优质产品和石油化工原料。
高分
酸性水
闪蒸气
循环油 进料泵 补充氢 补充氢 增压机 循环油泵 来自分馏塔底的未转化油 洗涤水 注水泵
低分 取分馏系统
催化加氢技术
◎ 一段串联加氢裂化的特点
≰ 精制段催化剂应具有较高的加氢活性(尤其是HDN活性);
≰ 裂化段催化剂应具有耐 H2S 和 NH3 的能力;
≰ 严格控制精制油氮含量
≰ 产品质量好, 生产灵活性大, 一次运转周期长; ≰ 与一段法加氢裂化相比, 其原料油适应性较强, 体积 空速、反应温度相对较低; ≰ 与两段法加氢裂化相比,其投资和能耗相对较低。
催化加氢技术
催化加氢技术
1.3 加氢裂化的基本原理及特点
◎ VGO是加氢裂化的典型进料, 它是大分子烷烃、单、双、多环环
烷烃, 烷基单、双、多环芳烃及环烷-芳烃组成的复杂混合物; 硫、氮、氧和少量的重金属原子也混杂在这些分子的结构中。
◎ 加氢裂化过程中的HDS、HDN 、 HDO等反应, 与加氢精制过程
2.1 两段法加氢裂化
2.2 单段加氢裂化 2.3 一段串联(单程通过,未转化油全循环、部分循环)
催化加氢技术
2.0 加氢裂化工艺流程 2.1 两段法加氢裂化 2.2 单段加氢裂化
2.3 一段串联(单程通过,未转化油全循环、部分循环)
3.0 中压加氢裂化及相关的加氢转化技术 3.1 提高十六烷值技术〔MCI〕
≰ 反应温度相对较高,运转周期相对较短。
Bullet points or body copy here
催化加氢技术
2.3 一段串联加氢裂化工艺
◎ 一段串联加氢裂化采用两个反应器串联操作。
◎ 原料油在第一反应器(精制段)经过深度加氢脱氮后, 其反应物流 直接进入第二反应器(裂化段)进行加氢裂化。 ◎ 裂化段出口的物流经换热、空冷/水冷后, 进入高、低压分离器进 行气/液分离, 高分顶部分离出的富氢气体循环使用, 其液体馏出
◎ 20世纪初, 德国人开发了煤转化生产液体燃料的加氢裂化技术。
◎ 1925年建成了第一套褐煤焦油加氢裂化装置,1943年已有12套 装置投入生产。 ◎ 二次大战后期,为德国提供了95%的航空汽油和47%的烃类产 品。
◎ 英、法、日(在中国东北-当时的“满洲”)、韩国都进行过
类 似的尝试; ◎ 类似技术的研究, 在美国则是直接面向重石油馏分加氢转化技术
物到低分进一步进行气/液分离;
◎ 低分的液体流出物, 到分馏系统进行产品切割分馏,其塔底的未 转化油返回(或部分返回)裂化段循环裂化(或出装置作为下游装置 的原料)。
图3 一段串联加氢裂化工艺流程示意图
循环氢 R-1 R-1循环氢 加热炉 R-2 循环氢压缩机
急冷氢
空冷
急冷氢 R-2循环氢 加热炉
的低分子烃,加氢 裂化的液体产品收率高;
≰ 非烃化合物基本上完全转化, 烯烃也基本加氢饱和,加氢裂化的
催化加氢技术
1.4 加氢裂化原料油及产品
◎ 原料油的分子结构,对其工艺过程及产品的分子组成有很大的 影
响;HVGO中较大分子的缩合反应,会使原料油在催化剂上的
生
焦倾向增加。 ◎ 通常VGO 的干点可高达530 550℃, CGO 和 FCC 的循环油作为 加氢裂化进料组分,其干点一般应比 VGO的干点低5080℃, 以避 开其高沸程中难转化含杂原子的多环芳烃, 减少生焦倾向、循环
等地建设了40 140 万吨/年规模的多套加氢裂化装置。 ◎ 90年代末, 大连 WEPEC 和茂名石化公司分别建成了200万吨/年 渣油固定床加氢处理装置。表明我国已具备开发成套催化加氢 技术的能力, 步入了世界加氢技术先进水 平的行列。
◎ 在清洁燃料的生产中, 加氢技术必将会得到稳步持续地发展。
3.2 低凝柴油生产技术〔HDW〕
3.4 柴油深度加氢脱硫脱芳烃技术 3.5 提高车用汽油质量的相关技术 3.6 渣油加氢处理技术
催化加氢技术
4.0 加氢裂化应用技术 4.1 加氢裂化催化剂的开工(催化剂装填、催化剂硫化及钝化、 换进原料油)
4.2 加氢裂化装置正常运转及相关工艺参数的影响
4.3 加氢裂化装置正常停工及紧急停工 4.4 加氢裂化催化剂器内及器外再生技术
◎ 这是国内60年代炼油技术方面的重大突破,是现代加氢裂化技术
起步的里程碑。
催化加氢技术
◎ 70年代末, 引进了4套加氢裂化装置, 19821990年相继开工投产 。 ◎ 80年代中期, 引进了140万吨/年重油加氢联合装置, 1992年在齐鲁 石化公司建成投产。
◎ 80年代中期以来, 相继在抚顺、镇海、辽阳、吉林、天津和山东
催化加氢技术
2. 加氢裂化工艺流程
2.1 两段法加氢裂化
◎ 两段法加氢裂化采用两个反应器, 20世初用于煤及其衍生物的加
氢裂化。
◎ 原料油先在第一段反应器进行加氢精制(HDS/HDN/HDO, 烯烃饱 和HDA, 并伴有部分转化)后, 进入高压分离器进行气/液分离; ◎ 高分顶部分离出的富氢气体在第一段循环使用, 高分底部的流出 物进入分馏塔, 切割分离成石脑油、喷气燃料及柴油等产品;
期, FCC广泛使用了分子筛催化剂, 氢气费用高, 对于生产汽油,
FCC比加氢裂化要经济, 加氢裂化的发展再度受到冲击而有所减
缓。
催化加氢技术
◎ 70年代加氢裂化已成为一项成熟的工艺技术, 催化剂的发展, 允 许现有装置的设备转向重质原料的加工, 其柴油的收率可高达 95v%(对原料油)。 ◎ 加氢裂化是增产石脑油、喷气燃料最有效的途径, 这是其它炼油 技术所无法替代的。
催化加氢技术
中国石油化工股份有限公司
C H I N A P E TR O L E UM & C H E M I C AL C O R P O R ATI O N
金 陵 石 化 分 公 司 炼 油 运 行 一 部
催化加氢技术
1.0 概述 1.1 加氢裂化的沿革 1.2 国内加氢裂化技术发展历程 1.3 加氢裂化的基本原理及特点 1.4 加氢裂化原料油及产品 2.0 加氢裂化工艺流程
催化加氢技术
两段法加氢裂化的特点
◎ 裂化段催化剂不耐H2S和NH3;
◎ 第一、二段反应器、高分和循环氢(含循环压缩机)自成体系;
◎ 补充氢增压机、产品分馏塔两段公用; ◎ 工艺流程较复杂、投资及能耗相对较高; ◎ 对原料油的适应性强,生产灵活性大,操作运转周期长。
催化加氢技术
2.2 单段加氢裂化工艺
◎ 单段法加氢裂化采用一个反应器, 既进行原料HDS、HDN、
HDO、烯烃饱和、HDA, 又进行加氢裂化;
◎ 采用一次通过或未转化油循环裂化的方式操作均可。
◎ 其特点是: ≰ 工艺流程简单,体积空速相对较高; ≰ 催化剂应具有较强的耐 S、N、O等化合物的性能; ≰ 原料油的氮含量不宜过高,馏分不宜过重;
催化加氢技术
◎ 煤转化成液体燃料产品, 须23个催化加氢步骤才能完成. ◎ 其典型的工艺条件是: 压力20 70 MPa, 温度375 525℃; ◎ 重石油馏分加氢裂化的设计压力2030MPa, 温度375 ℃ 以上; ◎ 尽管早期加氢裂化的操作条件十分苛刻, 其基本原理和工艺流程, 为现代渣油悬浮床加氢以及馏分油固定加氢的基本模式奠定了基
催化加氢技术
◎ 一段串联两段加氢裂化(未转化油单独裂化)
≰ 采用一个精制反应器、两个裂化反应器, 精制油在第一裂化反应