高 塔 生 产 工 艺 技 术 资 料
工艺流程设计
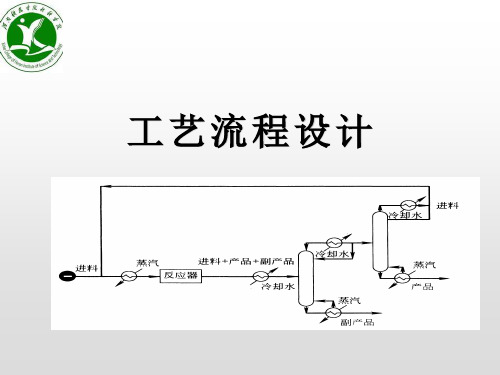
程。
工艺流程设计应解决的问题:
(1) 确定整个流程的组成; (2) 确定每个过程或工序的组成;
(3) 确定操作条件;
(4) 控制方案的确定;
(5) 合理利用原料及能量; (6) 制定三废的治理方法。
(7) 制定安全生产措施。
方案流程图
设备位号
设备
工艺流程线
用文字表明 流程情况
某物料残液蒸馏处理的工艺方案流程图
2. 工艺流程简图(simplified flowsheet) ➢ 设计初始阶段用来表达整个工厂或车间生产流程的图样,不编
入设计文件。
➢ 定性标出由原料转化成产品的变化、流向以及所采用的各种化 工单元及设备,供设计开始时工艺方案讨论。
② 能量供给、移出方式——反应器结构设计和辅助设施。 ③ 催化反应——催化反应方式和催化剂的选择。
确定主反应装置,可参考文献、资料、中试结果或已工业 化装置。
(2) 原料预处理过程 主反应对原料提出要求:如过程
主反应对原料提出要求:如纯度、温度、压力以及加料方 式等。
确定公用工程的配套措施——动力电、水、蒸汽、 压缩空气、冷冻、电热、氮气等。
确定操作条件和控制方案——控制方案和控制仪 表。
制定安全生产措施——对开车、停车、长期运转 及检修中,可能存在的不安全因素进行分析,制 订切实可靠的安全措施。
保温、防腐的设计——对需要保温、防腐的设备 进行设计。
三、工艺流程设计的基本方法 — 方案比较
图,不编入设计文件,多用于项目建议书、可行性研究报告等。 ➢ 一般用方框、文字表示一个单元,用箭头表示物流方向,表示
化学加工过程的轮廓。
02附件生产工艺技术指标汇编

内蒙古太西煤集团金昌鑫华焦化有限责任公司生产工艺技术指标(试行)编写:祁加利刘向东审核:黄绍东审定: 赵排行批准:贾昂杨二〇一三年一月一日说明1、A类指标为公司主控指标,生产部门及车间不得擅自更改。
2、如A类指标确与实际生产不符,需进行调整时,由公司上报更改报告,并由主管副总签字确认后,交总工办审核。
总工办接到报告后,送交总工确认后,下发执行。
3、B类指标为车间及生产部门控制指标,可根据生产的需要进行调整,但必须报总工办备案。
第一章化产车间工艺技术指标第一部分、冷鼓工段一、鼓风机岗位1、A类指标1)焦炉集气管压力保持在130~200Pa;2)鼓风机进出口煤气温度;不高于40℃;3)鼓风机机壳温度; <70℃;4)鼓风机机体振动;≤0.04mm;附属电机振动≤0.06mm;5)风机轴位移;≤0.5mm ;6)风机不得在临界转速; 3000-3400r/min范围内运行;偶合器转速表显示1780-2020r/min;7)风机油泵供油压力为:0.15-0.2MPa;风机运行润滑油压为:0.08-0.15MPa;8)油冷器冷却水压力应保持在0.1~0.2MPa,但要小于油压;9)润滑油箱液位不低于 2/3;2、B类指标1)初冷器前吸力:不高于-1000KPa根据焦炉出焦情况可作适当调整,但波动范围不得超过±200Pa;2)初冷器后吸力:不高于-2500KPaKPa根据焦炉出焦情况可作适当调整,但波动范围不得超过±200Pa;3)鼓风机机前煤气吸力:不高于-5000Pa,其波动范围不得超过±200Pa;4)机后压力;不高于16000Pa;5)鼓风机轴承温度; 60-70℃;6)电机轴承温度;≤80℃;7)电机定子温度;≤120℃;8)增速机轴承温度;≤70℃;9)风机运行电机电流不超过额定值; 60A;10)润滑油正常温度:35℃~45℃;油泵起动油温≥35℃二初冷器岗位1、A类指标1)温度控制指标①初冷器后煤气出口集合温度: 18-23℃②运行初冷器每台出口煤气温度差:±3℃③初冷器循环水进水温度:不高于32℃④初冷器循环水回水温度: 40-45℃⑤初冷器低温水进水温度: 16-18℃⑥初冷器低温水回水温度: 21-23℃2)阻力控制指标:初冷器阻力:≤1000Pa,最高不得超过1500Pa3)质检指标①初冷器后煤气含萘:≤0.5g/ m32、B类指标1)液位控制指标:冷凝液槽液位:不高于2/3,不低于1/22)质检指标:①初冷器中、下段循环冷凝液焦油含量:40—50 %三、电捕焦油器1、A类指标1)煤气氧含量大于1%报警;大于1.5%电捕停车2)绝缘箱温度95~110℃;3)电捕焦油器后煤气含焦油:≤50mg/ m34)电捕煤气阻力:不大于500Pa;2、B类指标1)二次电压:40~45KV;二次电流250~350mA;四、冷凝1、A类指标1)焦油贮槽温度: 80——90℃2)循环氨水泵出口压力: 0.45-0.55MPa3)高压氨水泵出口压力: 2.5-3.5MPa2、B类指标1)各贮槽液位:不低于泵进口高度不高于槽体80% 2)剩余氨水泵出口压力: 0.45-0.3MPa3)各泵轴承、轴套温度:≤70℃(或根据铭牌定) 4)配套电机温升:≤60℃第二部分油库控制指标A类指标1、焦油贮槽温度/℃ 80-902、粗苯贮槽温度/℃≤253、洗油贮槽温度/℃ 30-404、硫酸贮槽温度/℃ 25-355、浓碱贮槽温度/℃ 25-406、质量指标1)焦油 YBT5075——19932)洗油指标名称要求密度(20℃)g/ml 1.03——1.06230℃前馏出量% ≤3300℃前馏出量% ≥90酚含量% ≤0.5萘含量% ≤15水份% ≤1.0粘度E≤1.58015℃结晶物无第三部分循环水1、A类指标1)化产初冷循环水:①供水压力≥0.4MPa②供水温度≤32℃2)制冷机冷却循环水:①供水压力0.4MPa②供水温度≤32℃3)低温水:①供水压力≥0.4MPa②供水温度16-18℃4)循环冷却水水质标准悬浮物:≤20PH值: 8.0~9.0浊度:≤20mg/L计)总碱度:≤ 600 mg/L(以CaCO3Ca2+:≤ 680 mg/L(以CaCO计)3总磷:不大于 3mg/L电导率:≤2000浓缩倍数:4-4.5氯离子: ≤1000mg/L2、B类指标1)各泵的电机温度:≤65℃2)各泵的轴承温度:≤60℃第四部分制冷站1、A类指标1)低温水出口温度: 15-18℃2)制冷循环水出口温度: 36-38℃3)溴化锂溶液浓度/% 50±0.54)溴化锂溶液PH值: 9.0-10.52、B类指标1)煤气总管压力: 2.5-4.5KPa(最低不得低于800Pa)第五部分硫铵工段一饱和器1、A类指标1)入饱和器煤气温度 55-65℃;2)饱和器内母液酸度 4.5—8%;3)中加酸母液酸度 12—14%;4)饱和器后含氨 0.03--0.05g/m³;2、B类指标1)饱和器内母液温度 55-50℃;2)饱和器阻力≤2000Pa(单台);3)母液的比重 1.26~1.28;4)满流槽液位≥2/3二离心机1、A类指标1)洗涤水温度 60~70℃2)离心机开车晶比/% 15-203)离心机停车晶比/% 5-102、B类指标1)润滑油温≤40℃2)电机升温和轴瓦、轴承温度≤60℃3)油泵油压≤0.2MPa三干燥机1、A类指标1)入流化床风温 110~130℃2)硫铵质量指标袋计量准确每袋50kg±0.5kg(A类)2、B类指标1)引风负压 10~20Pa五泵B类指标各泵轴承温度≤65℃,电机温升≤45℃(可根据铭牌定)六蒸氨A类指标1.剩余氨水加碱后 PH: 9 - 10,2.蒸氨塔顶温度 101℃-103℃,塔底温度105-115℃;3.进管式炉贫富液换热器后富氨水温度>70℃4.出管式炉富氨水温度:120-130℃5.分缩器出口温度 97-98℃;6.废水含氨≤200mg/L7. 蒸氨废水冷却器后蒸氨废水温度 40-45 ℃第六部分粗苯工段一粗苯洗涤1、A类指标1)终冷后煤气温度:25-28℃2)冷贫油温度:夏季控制比煤气温度高1-3℃,冬季高3-5℃3)洗苯后煤气含苯:≤4g/m32、B类指标1)终冷塔阻力:≤1500Pa2)洗苯塔阻力:≤2000Pa二粗苯蒸馏岗位1、A类指标1)温度控制指标①管式炉出口富油温度: 180℃±5℃(不得低于165℃)。
HPPO工艺技术概况和生产工艺中涉及的关键问题

意大利 Enichem公司是最早研究 HPPO工艺 的机构,在 20世纪 80年代,用于 HPPO工艺的钛 硅分子筛催化剂研制成功,早期采用的是过氧化 氢和环氧丙烷生产的集成工艺,后来,Enichem公 司的聚氨酯业务被美国 Dow化学公司并购,该技 术随之并入 Dow化学公司[4]. 1.1 Basf/Dow化学 HPPO工艺
鉴于目前 工 业 制 备 PO工 艺 路 线 存 在 的 弊
端,HPPO工艺因其流程简单、副产物少和绿色无 污染的特点成为国内外研究的热点,该过程通过 双氧水直接环氧化丙烯制环氧丙烷,原料无腐蚀, 无毒,反应条件温和,符合绿色化学和原子经济发 展的要求,是一种新型绿色工艺[3].
下面 结 合 多 年 从 事 PO 生 产 的 经 历 和 对 HPPO工艺的不断研究,对国内外 HPPO工艺的 发展历程和技术概况进行了介绍,重点分析工艺 机理、副反应发生条件、溶剂解反应等,并提出了 HPPO工艺生产中存在的一些需要解决的问题.
问题.
关 键 词:环氧丙烷;TS1催化剂活性;过氧化氢;HPPO;溶剂解反应;生产工艺
中图分类号:TQ072
文献标志码:A
DOI:10.16039/j.cnki.cn22-1249.2019.03.002
环氧丙烷(简称 PO),也称氧化丙烯、甲基环 氧乙 烷,是 第 三 大 丙 烯 类 衍 生 物.是 无 色 醚 类 液 体,具有低沸点和易燃性.工业产品通常是两种对 映体的外消旋混合物.它与水部分混溶,可与乙醇 和乙醚混溶.其主要用途是生产聚醚多元醇和丙 二醇.它也是制备丙二醇醚,阻燃剂,非离子表面 活性剂和增塑剂的主要原料.其中,聚醚多元醇是 生产聚氨酯泡沫,保温材料,弹性体,粘合剂和涂 料的重要原料.各种非离子表面活性剂广泛用于 石油、化学、农药、纺织和日化行业[1].它是一种非 常重要的有机化合物原料,具有广阔的发展前景.
化工企业高能耗生产工艺过程节能降耗技术措施分析

化工企业高能耗生产工艺过程节能降耗技术措施分析摘要:相关工业企业在生产发展过程中,会消耗大量的能源资源,也因此造成了一定的能源短缺问题。
与此同时,能源的消耗也会产生很多温室气体,这些气体的排放会造成空气污染。
其中化工企业在能源消耗、环境污染等方面也会产生很多问题,若是将节能降耗技术科学应用其中,则能够减少化工企业生产过程的能源消耗,并且还会降低温室气体的排放量,使得化工行业保持绿色、可持续的发展状态,还能够提高化工企业的经济效益。
因此,相关化工企业在开展生产工作时,应该针对其原有的化工工艺进行改进,将其与节能降耗技术予以有机结合,使得该技术能够发挥出实际效用。
关键词:化工企业;节能降耗;技术1化工过程中采用节能降耗技术的必要性1.1 提高投入成本控制的有效性我国城市经济发展势头强劲,城市居民和农民工的生活水平有了很大提高,人们开始逐步意识到节能降耗的重要性。
只有在各个领域应用节能降耗技术,才能真正减少电能和热能资源的浪费。
化工企业生产的各个环节均需消耗使用,要想行业长期稳定发展,企业负责人就应该意识到在化工过程中应用节能降耗技术的必要性,阐明节能降耗技术在化工企业生产链中应用的优势,对能耗、投入成本、工作效率和废弃物排放产生积极影响,探索生产链结构中存在的问题,提高化工生产加工主要设备的性能,提高燃料设备的生产速度,减少运行中的能量损失,有效控制废气排放,确保化工企业经济效益最大化。
1.2 完善化学污染物处理技术我国大部分地区实现了小康社会。
在医疗条件和经济收入改善的背景下,再次加剧了能源消耗和环境污染问题。
化工生产过程中产生的废气排放量不断增加,是造成环境污染和能源消耗问题日益严重的原因。
例如,生产过程中各种输送设备泄漏的有害气体会挥发到空气中,对大气环境造成非常严重的污染。
同时人们在日常生活中会使用大量的化学品,并随意丢弃残留的化学品,这对大气环境也是一种非常严重的污染。
如果个别化工企业在实际产品加工生产过程中不处理化学废气、废液等有毒物质,废气直接挥发到空气中,废液直接排入河流,后果将是局部河流污染,水生植物和陆生植物大量死亡,人体轻度中毒等。
甲醇制烯烃(DMTO)过程发展及工艺和工程技术讲解

DICP
中国科学院大连化学物理研究所
6
根据Pennwell公司提供的石油化工产品链,可以分为四层: 内层: 是天然原料:煤、天然气、石油; 第二层: 9个基础原料,乙烯、丙烯、甲烷、丁烷、丁烯、丁
二烯、苯、甲苯和二甲苯; 第三层: 90个衍生物; 最外层: 树脂,塑料,橡胶等几百种最终用途
DICP
中国科学院大连化学物理研究所
15
DMTO技术依托
2006年8月,由DICP、LPEC和陕西新兴煤化工公司合 作的陕西华县万吨级工业化试验已经结束,并通过了 国家级鉴定。在工程设计方面对DMTO工艺技术有了更 深入的理解。
DMTO工艺和催化剂技术已基本成熟。
DMTO的核心技术-反应再生部分应用的流化工程技术 与已成熟的FCC流化工程技术类似。
石脑油制烯烃
对应国际原油 离岸价格
(美元/桶)
25 28
30 35 42
50 55 60 63
DICP
中国科学院大连化学物理研究所
27
DMTO与石脑油制烯烃成本对比
可以实现催化剂的连续反应-再生过程;
有利于过剩热量的及时导出,很好地解决反应床层温度分布均 匀性的问题;
合理地控制反应条件和再生条件;
工
可以实现较大的反应空速,缩小反应器体积;
艺
合适地设定物料线速度,可以有效控制反应接触;
特 点
反应原料可以是粗甲醇或精甲醇;
DMTO的反应温度为400-550℃,再生温度为550-700℃,对反 应、再生设备材质要求适中。
22
DMTO工艺及工程技术简介
溶剂脱沥青的技术进展与工艺优化[1]
![溶剂脱沥青的技术进展与工艺优化[1]](https://img.taocdn.com/s3/m/56cc984ffe4733687e21aad1.png)
1前言溶剂脱沥青工艺是生产催化裂化或加氢裂化原料以及润滑油加工过程的一个重要环节,也是生产微晶蜡、凡士林、光亮油等各种优质石油蜡产品必不可少的关键环节,它生产的副产品———脱油沥青是生产道路沥青和建筑沥青的重要原料。
所以,溶剂脱沥青装置是炼油企业重要的加工单元之一,其盈利水平将直接影响企业在市场上的竞争力。
2国外溶剂脱沥青技术发展概况自1936年M.W.Kellogg公司的第一套工业化装置问世以来,至今已有100多套装置投产。
这60多年间,由于加工廉价劣质原料、节能以及日益严格的环保法规的要求,使溶剂脱沥青新工艺、新技术快速发展。
在这些新技术中,最具代表性的是20世纪70年代由科尔-麦吉(Kerr-McGee)公司开发的渣油超临界抽提(ROSE)工艺,目前已有30套超临界抽提装置投产[1]。
此外,还有UOP公司的抽提脱金属法(Demex)、Foster-Wheeler公司的低能耗脱沥青(LEDA)以及IFP的SOLVAHL等各种溶剂脱沥青技术。
2.1Kellogg公司超临界抽提(ROSE)技术[2]超临界抽提(ROSE)工艺最初由科尔-麦吉公司(Kerr-MCGee)开发。
该工艺可使用从丙烷到己烷作溶剂,以常压渣油或减压渣油为原料,生产光亮润滑油料、催化裂化料、加氢裂化料、胶质和沥青质。
但据报道,已有的工业化ROSE装置多以戊烷作溶剂获取催化裂化和加氢裂化原料,而用丙烷作溶剂获取残渣润滑油料的ROSE工业化装置只有5~6套。
该工艺抽提部分设备采用混合器及多段分离塔,使沥青、胶质、脱沥青油分离,且分离塔内采用乱堆式填料,原则工艺流程如图1所示。
如图1所示,ROSE工艺是在沥青分离塔中进行减压渣油原料和戊烷溶剂的接触,完成分离,然后于超临界条件下在DAO(脱沥青油)分离塔中回收溶剂。
在超临界条件下,油在溶剂中的溶解度很低,使溶剂从油中分离出来而不必采用高剂油比,从而得到优质的脱沥青油。
Kerr-McGee公司声称,该工艺需高达13.3MPa(常规工艺为3~4MPa)的压力,剂油体积比为5~13.1,在分离过程中所用溶剂的85%~93%可不经气化而直接回收利用。
PTA工艺技术简介

SSEC封面主讲人:李真泽中国石化集团上海工程有限公司PTA 生产技术和主要专利商简介PTA工艺流程原材料及公用工程消耗主要工艺设备装置布置投资及经济效益国内PTA供需分析及预测SSEC在PTA领域中的业绩目录PTA生产工艺技术简介PTA 生产技术和主要专利商简介PTA生产工艺技术简介氧化反应方程式:H3C-C6H4-CH3+ 3O2→HOOC-C6H4-COOH + 2H2O + 318.7 千卡/克分子加氢反应方程式:HOOC-C6H4-CHO + 2H2→HOOC-C6H4-CH3+ H2OPTA生产工艺技术简介PTA 生产技术和主要专利商简介当前世界上最主要的PTA技术专利商:9BP(原Amoco)9INVISTA(原属ICI,后归Dupont,再独立为INVISTA)9Mitsui(三井化学)其他还有以BP技术为蓝本发展起来:9Mitsubishi(三菱化学)9Daw Chemical(原属INCA,后被Daw并购)其中以BP生产技术的市场占有率为最高。
PTA 生产工艺流程PTA生产工艺技术简介氧化单元9空气压缩9进料配置9氧化反应9结晶9过滤9干燥9溶剂回收9溶剂脱水精制单元9进料配置9加氢反应9结晶9离心分离9过滤9干燥9排气洗涤和溶剂回收9母液中固体回收PTA 生产工艺流程PTA 生产工艺技术简介工艺空气压缩催化剂配制氧化配料氧化反应闪蒸结晶真空过滤干燥尾气冷凝尾气催化氧化闪蒸汽冷凝溶剂回收蒸汽及凝水系统精制配料加氢预热加氢反应闪蒸结晶压力离心分离真空过滤产品干燥气流输送母固回收残渣回收包装储存高压蒸汽空气Co,Mn,Br -PX循环溶剂溶剂回收脱离子水蒸汽透平膨胀透平闪蒸蒸汽氢气废水催化剂残渣废水循环溶剂母液醋酸溶剂回收反应尾气HAC母液中固体排入大气废水处理装置H 2O尾气洗涤典型PTA 装置工艺流程示意图PTA 生产工艺流程PTA 生产工艺技术简介工艺空气压缩2催化剂配制氧化反应2闪蒸结晶真空过滤干燥尾气冷凝1尾气洗涤和吸附1闪蒸汽冷凝洗涤共沸蒸馏溶剂回收蒸汽及凝水系统精制配料加氢预热加氢反应闪蒸结晶压力离心分离真空过滤产品干燥气流输送母固回收催化剂回收PET 装置低压蒸汽及凝水空气Co, Mn, Br PX,HAC循环溶剂溶剂回收脱离子水膨胀透平1闪蒸蒸汽氢气废水催化剂废水循环溶剂母液回收的醋酸溶剂反应尾气母液中固体废水处理装置醋酸正丁酯排入大气离心分离排入大气残渣至回收WQ工艺空气压缩1氧化反应1尾气冷凝2Q 尾气洗涤和吸附2膨胀透平2再生气处理排入大气W 中石化百万吨级PTA 装置流程示意图PTA 生产工艺流程PTA 生产工艺技术简介四级冷凝冷却分别回收0.29、0.24、0.098和-0.029MPaG副产蒸汽四级冷凝冷却分别回收0.35和0.2MPaG 副产蒸汽四级冷凝冷却分别回收0.43和0.2MPaG 副产蒸汽四级冷凝冷却分别回收0.3、0.24、0.1和-0.03MPaG 副产蒸汽3. 反应尾气冷凝冷却系统CS /Ti CS /Ti CS /Ti CS /Ti 反应器材质下进轴锚式搅拌上进轴、涡轮式及浆式三级搅拌上进轴、涡轮式及浆式二级搅拌底进轴变速锚式搅拌氧化反应器搅拌机1台立式罐顶端设蒸馏塔1台立式罐1台立式罐2台立式罐顶部设分离塔氧化反应器气液相鼓泡反应带强烈搅拌的气液相鼓泡反应带强烈搅拌的气液相鼓泡反应气液相鼓泡反应氧化反应类型186℃1.0 MPa 201℃1.5 MPa 191℃1.26 MPa 185~189℃0.97~1.12 MPa 氧化反应条件2. 氧化反应50万吨/年60万吨/年90万吨/年100万吨/年1. 最大生产能力MitsuiINVISTA BP 中国石化项目主要PTA 生产技术的特点比较PTA 生产工艺流程PTA 生产工艺技术简介60块板1座316L /317L /Ti60块板1座316L /双相钢90块板1座316L /317L /Ti 60块板1座316L /317L /Ti 醋酸精馏塔共沸蒸馏设共沸剂回收塔共沸蒸馏设共沸剂回收塔直接精馏共沸蒸馏设共沸剂回收塔工艺流程7. 溶剂回收系统真空鼓式2台真空鼓式2台真空鼓式2台真空鼓式4台6. 真空过滤立式离心机3台无无立式离心机6台5. 氧化离心立式罐带搅拌(浆料罐)立式罐带搅拌立式罐带搅拌立式罐带搅拌结晶器形式1台3台串联3台串联2台串联结晶器台数4. 结晶系统MitsuiINVISTA BP 中国石化项目主要PTA 生产技术的特点比较PTA 生产工艺流程PTA 生产工艺技术简介13014011014512. 综合能耗指标kg 标油/t 产品压力离心分离后真空过滤分离压力离心分离后真空过滤分离压力离心分离后真空过滤分离压力过滤分离后真空过滤分离11. 产品分离系统采用结晶器闪蒸汽副产蒸汽加热直接采用结晶器闪蒸汽和蒸汽凝液加热直接采用结晶器闪蒸汽加热直接采用结晶器闪蒸汽加热10. 精制预热系统蒸汽利用催化燃烧高压催化燃烧催化燃烧再生热氧化燃烧9. 氧化尾气处理设置催化剂回收装置,回收催化剂水溶液,经浓缩后,送氧化反应器。
浅谈化工工艺与石油炼制
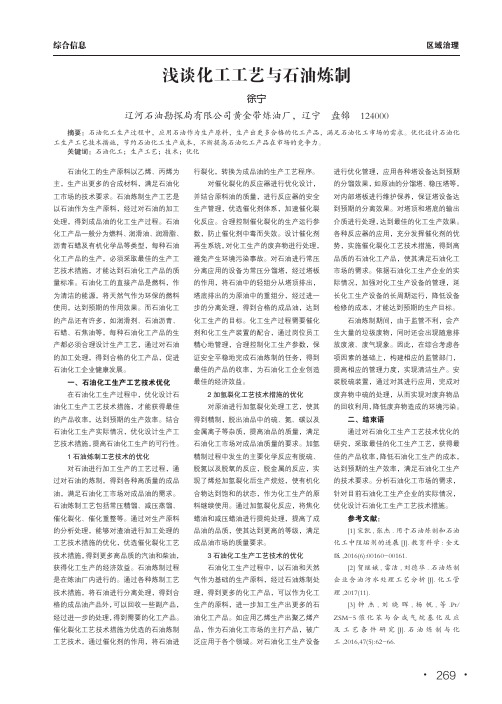
区域治理综合信息浅谈化工工艺与石油炼制徐宁辽河石油勘探局有限公司黄金带炼油厂,辽宁 盘锦 124000摘要:石油化工生产过程中,应用石油作为生产原料,生产出更多合格的化工产品,满足石油化工市场的需求。
优化设计石油化工生产工艺技术措施,节约石油化工生产成本,不断提高石油化工产品在市场的竞争力。
关键词:石油化工;生产工艺;技术;优化石油化工的生产原料以乙烯、丙烯为主,生产出更多的合成材料,满足石油化工市场的技术要求。
石油炼制生产工艺是以石油作为生产原料,经过对石油的加工处理,得到成品油的化工生产过程。
石油化工产品一般分为燃料、润滑油、润滑脂、沥青石蜡及有机化学品等类型,每种石油化工产品的生产,必须采取最佳的生产工艺技术措施,才能达到石油化工产品的质量标准。
石油化工的直接产品是燃料,作为清洁的能源,将天然气作为环保的燃料使用,达到预期的作用效果。
而石油化工的产品还有许多,如润滑剂、石油沥青、石蜡、石焦油等,每种石油化工产品的生产都必须合理设计生产工艺,通过对石油的加工处理,得到合格的化工产品,促进石油化工企业健康发展。
一、石油化工生产工艺技术优化在石油化工生产过程中,优化设计石油化工生产工艺技术措施,才能获得最佳的产品收率,达到预期的生产效率。
结合石油化工生产实际情况,优化设计生产工艺技术措施,提高石油化工生产的可行性。
1 石油炼制工艺技术的优化对石油进行加工生产的工艺过程,通过对石油的炼制,得到各种高质量的成品油,满足石油化工市场对成品油的需求。
石油炼制工艺包括常压精馏、减压蒸馏、催化裂化、催化重整等。
通过对生产原料的分析处理,能够对渣油进行加工处理的工艺技术措施的优化,优选催化裂化工艺技术措施,得到更多高品质的汽油和柴油,获得化工生产的经济效益。
石油炼制过程是在炼油厂内进行的。
通过各种炼制工艺技术措施,将石油进行分离处理,得到合格的成品油产品外,可以回收一些副产品,经过进一步的处理,得到需要的化工产品。
- 1、下载文档前请自行甄别文档内容的完整性,平台不提供额外的编辑、内容补充、找答案等附加服务。
- 2、"仅部分预览"的文档,不可在线预览部分如存在完整性等问题,可反馈申请退款(可完整预览的文档不适用该条件!)。
- 3、如文档侵犯您的权益,请联系客服反馈,我们会尽快为您处理(人工客服工作时间:9:00-18:30)。
高塔熔融喷浆造粒生产尿基复合肥的工艺技术高塔熔体造粒技术是世界复合肥行业一种先进的生产工艺。
高塔造粒复合肥采用全自动电脑控制配料系统,以熔体尿素、磷、钾等原料,经充分溶合后,从高塔顶部喷淋而下,经空气自动冷却结晶而成为颗粒,其技术指标达到世界同行先进水平,具有以下 5 项优点:(1)颗粒均匀;(2)表面圆润光滑;(3)水分含量低、结块率低;(4)每一个颗粒都有针状融化孔,融化速度快;(5)水溶率高,施用肥效与转鼓造粒的尿基肥更好。
高塔复合肥采用先进熔体新工艺,客服并转变了传统尿素熔融的转鼓造粒生产工艺中的有害物质缩二脲含量的缺点,改变了工艺及流程,改善了生产环境。
以固体尿素或硝铵磷经电脑计量熔化后的溶液与固体的磷酸一铵、硫酸钾或氯化钾、添加剂填充料等原料在混合加温混合后制成流动性较好的料浆,经旋转式差动造粒机造粒喷淋成液滴,液滴在从造粒塔顶下落的过程中与上升的冷空气接触被自然冷却固化结晶成颗粒,落于塔底部的收料斗及输送皮带,再经冷却、分筛、包膜、到成品料仓,经自动计量包装,成品入库;生产过程自动化程度相对较高,返料量相对较少、返料部分经过改造返料直接返回系统,经过系统熔化后再生产,生产过程基本采用自动流程控制,操作环境好,无三废排放,属清洁生产工艺,粉尘浓度控制在 1003表面塔产品颗粒圆润光滑,颗粒有孔眼(是其它肥料所不具高mg/m,,具有较强的市场竞争力。
块备的),不易结1.高塔复合肥具有以下特点:1、采用高塔熔体造粒工艺,产品性状好,品质稳定,颗粒圆润,色泽晶莹,有针状融化孔,天然防伪。
产品水分含量低,溶解速度快,作追肥、冲施肥效果更好。
2、营养富,配比合理。
除含有作物必需的氮、磷、钾三大营养外,还富含钙、镁等中微量元素,养分均衡全面,充分满足作物需求,施用范围广,即适用于小麦、水果、水稻、玉米等粮食大田作物,而且适用于油菜、烟草、甘蔗、茶叶等经济作物,更适合于各种蔬菜、果树、药材等特殊用肥需要作物。
利用率高,使用方便。
3、本品是通过高塔造粒形成的高效复合肥,养分配比合理,能够满足不同作物各生长周期的需肥要求,它可作基肥、追肥、冲施肥。
施用后作物长势稳健、根系发达、茎干粗壮、抗旱、抗寒、抗病虫害能力显著增强。
不仅能提高作物单位面积产量,还能够提高农产品的品质。
我们公司从设备、工艺等都加以了改进,可生产低氮高钾和硝硫基型复合肥。
总之,高塔熔融喷浆造粒生产与传统的尿基复合肥生产相比,其工艺相应的提高了,并对工艺参数要求苛刻,特别是生产硝硫基型复合肥,对温度控制和其它工艺指标的控制要求相当严格,稍有不慎就能导致系统停车和其它安全事故的发生;造成不可估量的经济损失。
现就技术、工艺原理及部分技改造的经验归纳如下。
1高塔熔融喷浆造粒生产尿基复合肥工艺1.1工艺原理利用熔融尿素或硝酸磷、磷酸一铵、氯化钾或硫酸钾及填充剂等可以形成低共熔点化合物的特点,将预热后的粉状磷酸一铵、氯化钾或硫酸钾及填充剂与熔融后的尿液充分混合,通过反应生成流动性良2.好的 N、P、K 熔体料浆。
该料浆通过专用喷头喷入造粒塔后,喷淋成液滴,液滴在从造粒塔顶下落的过程中与上升的冷空气接触被自然冷却固化结结晶成颗粒,落于塔底输送皮带,再经分筛从而获得养分分布均匀、颗粒形状良好的复合肥。
达标颗粒,再进行颗粒表面处理、颗粒分级后进行计量包装,化验检测,入库成为合格产品,整个生产过程全部采用自动化控制。
该技术的关键点在于制备流动性良好的熔融料浆,那么制备流动性良好的熔融料浆溶液,就必须严格的控制好混合槽温度、料浆在混合槽内停留的时间及料浆液固比等,是工艺过程的主要参数,参数控制得好有助于降低料浆的黏度,保证其流动性,减少副反应,降低氨氮损失,使产品颗粒及养分均匀,表面光滑圆润,颗粒有孔眼多。
1.2生产工艺及流程我公司以尿素或硝酸磷、磷酸一铵、氯化钾或硫酸钾为主要原料添加填充剂为辅助原料,塔式熔融造粒制高浓度复合肥,1、主要原料入厂标准按《原料、辅料、包装物验收标准执行》。
3.升机提至尿素振动筛,去除杂质后进入尿素贮提固体尿素经尿素尿素熔融器,熔融后的尿液进入缓冲进入一级混合入斗,经计量后进磷酸一铵经人工拆包后各自经提升机,筛分、计量槽;粉状氯化钾和4.后与填充剂一起经混料输送带进入混料提升机提至混料贮斗,经螺旋输送机进入混料加热器用蒸汽预热。
预热后的物料进入 1#混合槽中,在此与尿液充分混合后再进入 2#混合槽,混合后的熔融料浆进入造粒塔造粒;从塔顶喷洒下来的料浆通过空气自动冷却在塔底成型后经小漏斗进入输送带输送到冷却机,冷却处理后,由提升机提至转筒筛筛分,成品再经包膜处理后进入自动包装机包装入库;大颗粒与细粉返回塔顶重新回收造粒;冷却尾气经尾气风机、旋风除尘器、洗涤后排放。
另外,在造粒机前的过滤槽内加微量的碳酸轻氨、明矾等(甲醛)是为了提高产品外观质量;设计冷却机和包膜机设备,是为了使肥料充分冷却后包膜,避免成品肥料结块,设计增加 1 套包膜机系统,对防结块剂的使用是通过电子皮带计量秤计量成品流量从而控制防结剂计量泵的流量,(使防结块剂能根据成品量的大小达到控制防结剂的流量)使之均匀喷雾防结剂达到成品防结块的处理效果。
1.3主要设备1.3工艺参数1.4 1.4.1固体尿素输送、熔融及泵送岗位ww(H2O)≤1.0%,颗粒状,尿素熔融温度(N尿素:)≥46%,不能超过 130℃,因为尿素熔液温度超过 130℃时及易产生缩二脲(缩二脲应小于1.5%,因为缩二脲对作物的根系生长有明显毒害作用), 由尿素熔融岗位负责管理控制由塔上中~122127℃ 125120:夏季制剂后的料浆温度~℃;冬季和控制岗位负责管理控制5.ww w(H2O)%,N)≥10%,(P2O5)≥45%磷酸一铵:-48(≤1.5%,粒度≤0.8mm 占 90%ww(H2O)≤1.5%,粒度≤0.8mm(K2O)≥60%,占氯化钾:90%ww(H2O)≤1.5%,粒度≤0.8mmK2O)≥50%,占硫酸钾:(90%填充剂(白云石或碳酸钙粉):细度≥200 目(0.175mm)占w(H2O%,)≤1.5%1001.4.3混料加热岗位按工艺配方对混料进行计量。
混料加热器物料控制温度:夏季 60~70℃;冬季 70~90℃。
1.4.4混合及造粒岗位。
1)混合槽熔融料浆温度:夏季为 1#槽 115~125℃,2#槽110~120℃;冬季为 1#槽 125~132℃,2#槽 115~125℃。
2)造粒成品颗粒粒径:国标为 1~4.5mm,要求<1mm 的细粒少于 3%。
我们公司为了确保颗粒外观的均匀度将标准提高到 2.8~4.2mm以上工艺参数是针对含氯基复合肥。
含硫基复合肥的工艺参数与含氯基复合肥工艺参数不同。
对于含氯基的复合肥因配方不同,其工艺参数也有区别,常常需根据具体情况进行调整。
2装置主要设备功能及特点2.1配料秤6.本生产装置的原料配料系统选用了集控变频调速配料系统,实现自动配料,确保产品养分比例。
集控变频调速配料系统的功能特点是:应用电子皮带秤,保证计量精确;计算机主机应用正压防尘机箱,适合于 NPK 复合肥的生产厂所;彩色 CRT 显示,全中文界面、集中控制和生产工况的显示,便于生产操作和管理;自动声光超限报警,模拟图形显示;工业级 I/O 板应用,设备稳定可靠,抗干扰能力强;采用变频调速技术,节能降耗。
2.2斗式提升机选用 TH 系列钢丝胶带斗式提升机,机身高度 108 米,其特点是:提升物料适用范围广泛,不仅能提升各种粉状和粒状物料,而且对提升高度适应能力强,最大提升高度可达 120m,对物料温度要求不大于120℃,如超过 120℃可采用耐高温胶带制造;输送能力大,提升输送量范围为 10~480m3/h;采用变频驱动、功率小,节省能源,此类提升机采取流入式喂料,重力离心式混合卸料,物料提升过程中几乎无回料和挖料现象;钢丝胶带与驱动滚筒为柔性接触,无磨损,运行平稳,功能消耗低;密封性好,对环境无污染,操作环境洁净,噪声低。
2.3 HZPKJ-020 混抖加热器2.3.1混料加热器的工作原理该加热器是复合肥专用加热器,属间接传导型连续加热设备。
被加热物料由设备上盖上方的加料口进入设备,物料在自重及轴旋转搅7.拌的作用下向出口逐渐移动;物料在向前移动的过程中与设备加热界面——中心轴及夹套内壁充分接触(中空轴通高压蒸汽,在器身内安置换热器),进行热量交换;符合要求的混合热物料从设备下部的出口排出。
加热过程中应满足:物料不能出现团聚、结块、结片等现象;物料的加热温度稳定,温度的波动范围应控制在±3℃之内;物料通过加热器后,流量稳定;物料加热时,不能出现物料的分解现象;当混合槽出现工艺波动时,加热器具有储料和立即停料功能;粉体物料在加热过程中,应控制物料的粉尘污染。
该加热器设备紧凑,占地面积小;热效率高,能耗及操作成本低;被加热物料在中空轴的作用下,不断地被搅拌,瞬时更新热界面,保证了物料与设备的加热界面充分接触和物料加热的均匀性,同时,有效地防止了物料在加热过程中的闭聚与结块等现象;设备的尾气排放少,对环境污染小,尾气的处理简单易行;设备的安装及调试简单;低速运转设备噪声不超过 85db。
2.3.2混料加热器的特点采用间接传导加热方式,不污染物料,并且换热效率高,最高可达 90%;操作弹性大,在物料与轴及夹套热量传递的过程中,通过节设备安装倾角、加料量和出料口的高度,可以调节物料在设备内的停留时间,通过调节蒸汽压力,可以调节物料加热温度;设备连续运转,适用于规模化生产;采用拼装积木式上盖,操作灵活,维修简单,易于更换备件;密闭操作,无粉尘污染。
8.2.3.3混料加热器的结构HZPKJ-020 加热器由两组相对旋转的中空轴(加热界面)、带夹套的器身(加热界面)、上盖、传动系统和蒸汽管路系统组成。
中空轴:由主动轴和被动轴组成,两轴由齿轮啮合作相对转动;两轴都装有数组带一定倾角的扇形叶,并由蒸汽提供热源;在运转时搅拌、混合物料,进行热交换。
器身:在器身外表设有夹套,运行时通入蒸汽;在器身尾部下方,开有小料口,用于卸料。
上盖:上盖能使加热过程密闭进行,热效率高,并改善操作环境;上盖上设有进料口、尾气出口、人孔和观察孔。
传动系统:由电机、联轴器和减速机组成,再经过链轮副驱动设备运行。
蒸汽管路系统:夹套和轴都有蒸汽进口和冷凝水出口,轴的管线系统带有旋转接头和金属软管,确保在两轴旋转时蒸汽管路系统的正常运行。
2.3.4混料加热器的主要技术特性设备外形尺寸:7500mm×2215mm×2250mm操作压力:夹套、轴内≤0.3MPa;设备内为常压操作温度:夹套、轴内、设备内均≤130℃中空轴转速:约 12r/min电机功率:37kW2.4 CD-CT3/ZKL 造粒机9.2.4.1造粒机的工作原理由于熔体法复合肥工艺的三元素物质在熔融混合过程中其黏度是纯尿素熔液的数千倍,其流动性很差,且含有相当数量的固体悬浮颗粒,故一般的喷淋造粒方法无法保证喷孔不被堵塞。