钢包渣洗料标准
《钢铁渣处理与综合利用通用规范》条文说明

钢铁渣处理与综合利用通用规范General Code for Processing and Comprehensive utilization of Ironand Steel Slag条文说明1 总则1.0.1 【新增】本条规定了规范编制的目的。
为保障人民生命财产安全、人身健康、工程质量安全、生态环境安全、公众权益和公共利益,促进钢铁行业固体废弃物的安全环保处理与资源利用,满足钢铁企业固体废弃物管理基本要求,住房与城乡建设部组织编制了国家工程规范体系框架。
本规范中涉及的钢铁渣是指冶炼钢铁和铁合金产生的渣,包括铁渣、钢渣和铁合金渣。
之所以称为铁渣而不称为高炉渣,是因为国内除了高炉炼铁外,还有非高炉炼铁工艺如COREX工艺等,同样也会产生炼铁炉渣。
1.0.2 【新增】明确了本规范涵盖的主要内容,包括钢铁渣和铁合金渣的综合利用。
本规范的内容不适用于战争、自然灾害等不可抗条件下对钢铁渣处理以及综合利用的要求。
1.0.3 【新增】本规范是国家工程建设控制性底线要求,具有法规强制效力,必须严格遵守。
在此基础上,国务院有关行政管理部门、各地省级行政管理部门可根据实际情况,补充、细化和提高本规范相关规定和要求。
为适应工程项目建设特殊情况和科技新成果的应用需要,对本规范规定的功能性能要求,暂未明确对应技术措施或采用本规范规定之外的技术措施,且无相应标准的,必须由建设、勘察、设计、施工、监理等责任单位及有关专家依据研究成果、验证数据和国内外实践经验等,对所采用的技术措施进行充分论证评估,证明能够达到安全可靠、节约环保,并对论证评估结果负责。
论证评估结果实施前,建设单位应报工程项目所在地行业行政主管部门备案。
执行本规范并不能代替项目全生命周期过程中的质量安全监管。
当本规范规定与国家法律、行政法规或更严格的强制性标准规定不一致时,应执行国家法律、行政法规和更严格的强制性标准的规定。
当钢铁渣和铁合金渣处理以及综合利用采用的技术措施与本规范的规定不一致或与本规范的规定不一致时,须经合规性判定。
钢水纯净度控制

• (8)钢种微细夹杂物去除 钢种微细夹杂物去除
• 大颗粒夹杂(>50µm)去除, 大颗粒夹杂( )去除, 术; • 小颗粒夹杂(<50µm)去除: 小颗粒夹杂( )去除: 采用中间包控流技
• •
-中间包钙质过滤器 -中间包电磁旋转
• • • • •
(9)防止浇注过程下渣和卷渣 防止浇注过程下渣和卷渣 — 加入示踪剂追踪铸坯中夹杂物来源; 加入示踪剂追踪铸坯中夹杂物来源; — 结晶器渣中示踪剂变化; 结晶器渣中示踪剂变化; — 铸坯中夹杂物来源,初步估算外来夹杂 铸坯中夹杂物来源, 物占41.6%二次氧化占 39%,脱氧产物为 物占 二次氧化占 , 20%
中间包冶金的最新技术
◆ H型中间包 ◆ 离心流中间包 ◆中间包吹氩 ◆去夹杂的陶瓷过滤器 ◆电磁流控制
• (4)钢包高FeO渣子是氧的储存器。浇 注过程中钢包表面渣子可能会凝结在 钢包内壁上,浇完后倒渣不净,附着 在包壁上的高FeO渣子与下一炉钢水 相接触,渣中氧就要释放出来,氧化 合金元素(如硅、锰),严重时会导致钢 水成分出格。 • 因此,为了发挥炉外精炼的效果, 提高铸坯的质量,控制钢水成分的稳 定性,在出钢时必须进行挡渣操作。
• (5)中间包控流装置 中间包控流装置
• 中间包不是简单的过渡容器,而是一个冶 金反应 中间包不是简单的过渡容器, 容器, 容器,作为钢水进入结晶器之前进一步净化钢水 • 中间包促进夹杂物上浮其方法: 中间包促进夹杂物上浮其方法:
• • • •
1)增加钢水在中间包平均停留时间t: )增加钢水在中间包平均停留时间 : t=w/(a×b×ρ×v) = ( × × × ) 中间包向大容量深熔池方向发展。 中间包向大容量深熔池方向发展。 2)改变钢水在中间包流动路径和方向, )改变钢水在中间包流动路径和方向, 促进 • 夹杂物上浮。 夹杂物上浮。
炼铁厂渣、铁处理一般安全规定(3篇)
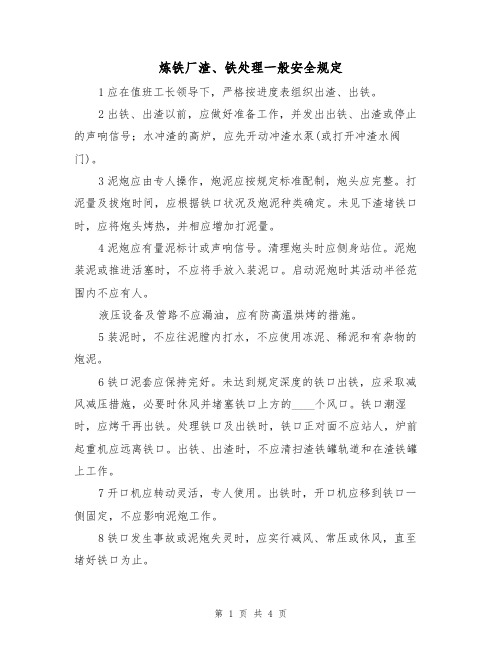
炼铁厂渣、铁处理一般安全规定1应在值班工长领导下,严格按进度表组织出渣、出铁。
2出铁、出渣以前,应做好准备工作,并发出出铁、出渣或停止的声响信号;水冲渣的高炉,应先开动冲渣水泵(或打开冲渣水阀门)。
3泥炮应由专人操作,炮泥应按规定标准配制,炮头应完整。
打泥量及拔炮时间,应根据铁口状况及炮泥种类确定。
未见下渣堵铁口时,应将炮头烤热,并相应增加打泥量。
4泥炮应有量泥标计或声响信号。
清理炮头时应侧身站位。
泥炮装泥或推进活塞时,不应将手放入装泥口。
启动泥炮时其活动半径范围内不应有人。
液压设备及管路不应漏油,应有防高温烘烤的措施。
5装泥时,不应往泥膛内打水,不应使用冻泥、稀泥和有杂物的炮泥。
6铁口泥套应保持完好。
未达到规定深度的铁口出铁,应采取减风减压措施,必要时休风并堵塞铁口上方的____个风口。
铁口潮湿时,应烤干再出铁。
处理铁口及出铁时,铁口正对面不应站人,炉前起重机应远离铁口。
出铁、出渣时,不应清扫渣铁罐轨道和在渣铁罐上工作。
7开口机应转动灵活,专人使用。
出铁时,开口机应移到铁口一侧固定,不应影响泥炮工作。
8铁口发生事故或泥炮失灵时,应实行减风、常压或休风,直至堵好铁口为止。
9更换开口机钻头或钻杆时,应切断动力源。
10通氧气用的耐高压胶管应脱脂。
炉前使用的氧气胶管,长度不应小于30m,10m内不应有接头。
吹氧铁管长度不应小于6m。
氧气胶管与铁管联接,应严密、牢固。
氧气瓶放置地点,应远离明火,且不得正对渣口、铁口。
氧气瓶的瓶帽、防震胶圈和安全阀应完好、齐全,并严防油脂污染。
11炉前工具接触铁水之前,应烘干预热。
12渣、铁沟和撇渣器,应定期铺垫并加强日常维修。
活动撇渣器、活动主沟和摆动溜嘴的接头,应认真铺垫,经常检查,严防漏渣、漏铁。
不应使用高炉煤气烘烤渣、铁沟。
用高炉煤气燃烧时,应有明火伴烧,并采取防煤气中毒的措施。
13采用水冲渣工艺的高炉,下渣应有单独的水冲渣沟,大型高炉冲渣应有各自的水冲渣沟。
14铁口、渣口应及时处理,处理前应将煤气点火燃烧,防止煤气中毒。
钢材表面喷射清理的磨料标准

技术研发部 2011.06.25
目录
钢材表面清理方法 喷射清理用磨料技术要求 我司产品采标情况
GB 8923-1988 涂装前钢材表面锈蚀 等级和除锈等级
钢材锈蚀等级: A全面地覆盖着氧化皮而几乎没有锈蚀; B已发生锈蚀,并且部分氧化皮已剥落; C氧化皮已因锈蚀剥落,或可以刮除,并且 有少量点蚀; D氧化皮已因锈蚀全面剥落,并且已普遍发 生点蚀
≤1000µs/cm ≤300µs/cm
SAE J445金属磨料测试
消耗法 以500次为一个循环,直至100G磨料完全消耗 稳定法 以500次为一个循环,每个循环添加磨料至原 始重量100G,直至磨料消耗量不再上升 添加法 以500次为一个循环,每个循环添加磨料至原 始重量100G,直至磨料添加量大于100G
我司产品采标情况
钢砂:SAE J444、SAE J1993 钢丸:SAE J444、 SAE J827 筛网:QB/T 1925.1-1993 一般用途镀锌低 碳钢丝编织网 方孔网 检验筛:GBT6003.1-1997 金属丝编织网试 验筛 含盐量:暂无
谢 谢!
磨料参数测定
非金属:GB/T17849,17850;ISO11127,11126 金属:GB/T19816,18838;ISO11125,11124 颗粒尺寸(粒度) 密度:≥7g/cm3 硬度 含水量:≤0.2% 杂质:水浸出液导电率≤ 250 µs/cm (非金属), ≤1%(钢丸) 机械特性(尚在制定中) 水溶性氯化物(非金属) 缺陷和微结构(金属)
ASTM E11标准试验筛
磨料粒度与钢材表面粗糙度
*SY/T 0407-97涂装前钢材表面预处理规范
涂料对钢材表面粗糙度的要求
水钢渣清料制度及流程
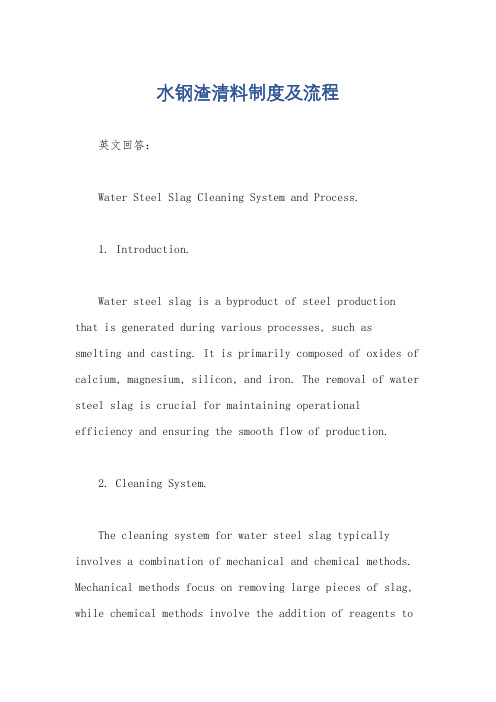
水钢渣清料制度及流程英文回答:Water Steel Slag Cleaning System and Process.1. Introduction.Water steel slag is a byproduct of steel productionthat is generated during various processes, such as smelting and casting. It is primarily composed of oxides of calcium, magnesium, silicon, and iron. The removal of water steel slag is crucial for maintaining operationalefficiency and ensuring the smooth flow of production.2. Cleaning System.The cleaning system for water steel slag typically involves a combination of mechanical and chemical methods. Mechanical methods focus on removing large pieces of slag, while chemical methods involve the addition of reagents tofacilitate the dissolution or chemical reduction of slag.a. Mechanical Methods:i. Slag tapping: Molten slag is tapped from the furnace or ladle into a slag pot.ii. Slag crushing: Cooled slag is crushed into smaller pieces using a slag crusher.iii. Slag screening: Crushed slag is screened to separate different size fractions.b. Chemical Methods:i. Hydration: Adding water to slag causes it to hydrate and break down.ii. Acid leaching: Adding acids, such as hydrochloric or sulfuric acid, to slag dissolves the metallic oxides.iii. Alkali treatment: Adding strong alkalis, such assodium hydroxide or potassium hydroxide, converts the slag into soluble silicates.3. Cleaning Process.The cleaning process of water steel slag typically includes the following steps:a. Slag Collection:i. Slag is tapped from the furnace or ladle into a slag pot.ii. Slag is cooled and allowed to solidify.b. Slag Crushing:i. Cooled slag is crushed into smaller pieces using a slag crusher.ii. This step increases the surface area of the slag, facilitating subsequent chemical reactions.c. Slag Screening:i. Crushed slag is screened to separate different size fractions.ii. Smaller particles are more suitable for chemical treatment, while larger particles can be used for other purposes, such as road construction.d. Chemical Treatment:i. Chemicals are added to the slag to facilitate dissolution or chemical reduction.ii. The choice of chemicals depends on the desired outcome and the specific composition of the slag.e. Separation and Disposal:i. After chemical treatment, the dissolved slag is separated from the undissolved solids.ii. The dissolved slag can be disposed of or recovered for other uses.iii. The undissolved solids can be used as a filler material or for other industrial applications.4. Environmental Considerations.The cleaning of water steel slag is an important step in reducing the environmental impact of steel production. Water steel slag contains various heavy metals and other hazardous substances that can pose risks to the environment if not properly managed. The cleaning process helps to reduce the release of these pollutants into the environment and promotes sustainable practices in the steel industry.中文回答:水钢渣清料制度及流程。
LF-80t钢包精炼技术操作规程(1)
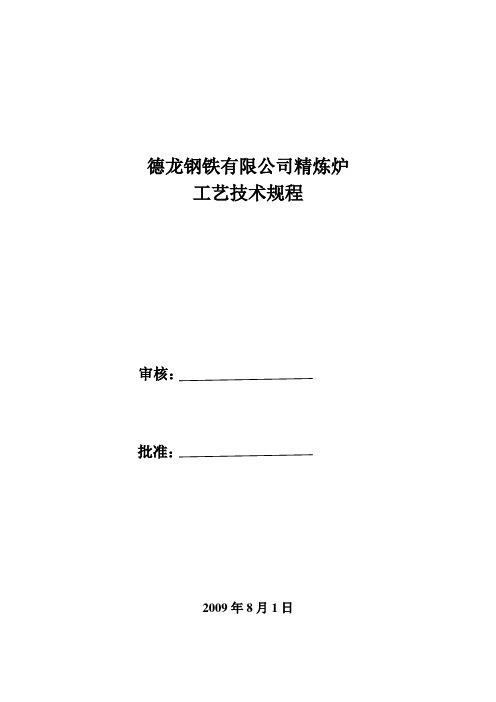
德龙钢铁有限公司精炼炉工艺技术规程审核:批准:2009年8月1日前言工艺技术规程是技术操作基本规范,结合设计方案和生产实践制订,是指导技术的标准规范和依据。
工艺技术规程是制订岗位操作规程的依据,岗位操作规程的内容应符合工艺技术规程的规定。
在执行工艺技术规程的同时,还必须执行相关的安全、设备规程。
当与安全、设备规程发生矛盾时,由厂技术科提出修改意见,经厂领导同意,报技术中心审批后执行。
需公司协调的问题,公司技术中心组织协调。
本规程在贯彻执行过程中,如因客观条件的变化,个别条款不适应新情况时,由生产厂提出,报公司技术中心审批并备案。
经实践检验合理的临时性参考意见,在下次规程修订时正式纳入工艺技术规程。
参加编制人员:宫祥辉、张贵祥、窦为学、周有预、曹发卫、王太侠、王冰民、王杰文、王建宏、黄伟丽。
由于时间仓促,不妥之处在所难免,望批评指正。
本规程的内容未经技术中心批准不得随意改动。
德龙钢铁有限公司技术操作规程钢包精炼炉生效日期:2009年8月1日编号:LGJC–14–25 修改2次1、钢包精炼炉原材料技术要求:1.1 造渣材料钢包精炼炉造渣主要使用精炼渣、活性石灰和萤石。
1.1.1 精炼渣采用CaO–Al2O3渣系。
1.1.2 活性石灰得混入外来杂物。
1.1.3 萤石1.1.3.11.1.3.21.2 扩散脱氧剂钢包精炼炉扩散脱氧剂主要使用Si–C粉、Al粉、CaC2等。
1.2.1Si–C粉1.2.1.11.2.1.21.2.2 Al粉1.2.2.11.2.2.21.2.3 CaC21.2.3.11.2.3.21.3 增碳剂1.3.11.3.21.3.3 干燥无杂物,采用塑料袋包装,10kg/袋。
1.4 包芯线1.4.3包芯线所使用钢带0.35-0.4mm厚,应去油污、除锈、表面光洁,包覆牢固,不漏粉,不开线。
1.5 铝线1.6 高功率石墨电极1.6.3 接头、接头孔及距孔底100mm以内的电极表面,不允许有孔洞和裂纹。
钢包使用管理规定(7页)
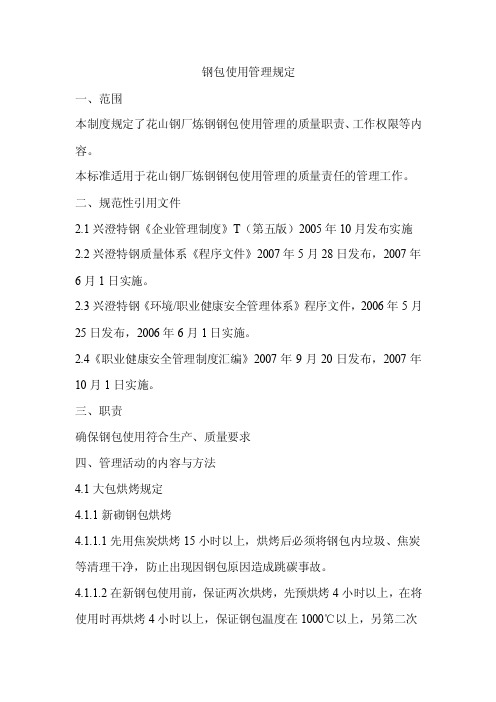
钢包使用管理规定一、范围本制度规定了花山钢厂炼钢钢包使用管理的质量职责、工作权限等内容。
本标准适用于花山钢厂炼钢钢包使用管理的质量责任的管理工作。
二、规范性引用文件2.1兴澄特钢《企业管理制度》T(第五版)2005年10月发布实施2.2兴澄特钢质量体系《程序文件》2007年5月28日发布,2007年6月1日实施。
2.3兴澄特钢《环境/职业健康安全管理体系》程序文件,2006年5月25日发布,2006年6月1日实施。
2.4《职业健康安全管理制度汇编》2007年9月20日发布,2007年10月1日实施。
三、职责确保钢包使用符合生产、质量要求四、管理活动的内容与方法4.1大包烘烤规定4.1.1新砌钢包烘烤4.1.1.1先用焦炭烘烤15小时以上,烘烤后必须将钢包内垃圾、焦炭等清理干净,防止出现因钢包原因造成跳碳事故。
4.1.1.2在新钢包使用前,保证两次烘烤,先预烘烤4小时以上,在将使用时再烘烤4小时以上,保证钢包温度在1000℃以上,另第二次烘烤完毕到初炼炉出钢必须控制时间在30分钟以内。
4.1.2冷钢包(包括换渣线钢包)在使用前烘烤4-6小时。
4.1.3钢包在线烘烤规定:钢包空载时间 90分钟,必须进行在线烘包,在线烘包时间规定为:4.1.3.1时间90--120分钟,在线烘烤时间15分钟以上。
4.1.3.2空载时间120--150分钟,在线烘烤时间20分钟以上。
4.1.3.3空载时间150--180分钟,在线烘烤时间25分钟以上。
4.1.3.4空载时间180--210分钟,在线烘烤时间30分钟以上。
4.1.3.5空载时间210--240分钟,在线烘烤时间40分钟以上。
4.1.3.6若空载时间超出240分钟,只能用在优碳钢或简单的合结钢上,并在线烘烤时间40分钟以上,重点品种上不能使用。
4.1.3.7原则上不安排浇注第一炉钢(重点品种严禁第一炉使用),尽量安排在一般钢种对接炉上使用。
4.1.3.8所有钢包(包括热钢包),在合金加入后不论是否需要烘烤,都必须停放在烘烤位,将烘烤盖盖上。
35K钢冷镦钢工艺操作规程控制要点
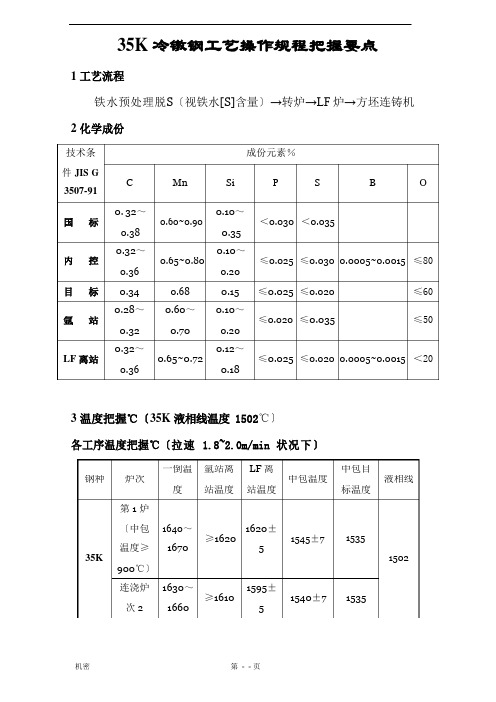
技术条 成份元素%件 JIS G 3507-91 〔中包 1640~1620±≥16201545±71535温度≥ 1670535K1502900℃〕 连浇炉 1630~ 1595±≥16101540±71535次 21660 535K 冷镦钢工艺操作规程把握要点1 工艺流程铁水预处理脱S 〔视铁水[S]含量〕→转炉→LF 炉→方坯连铸机 2 化学成份C Mn Si PSBO0. 32~0.10~国标0.38 0.32~ 0.60~0.90<0.030 <0.0350.35 0.10~ 内 控 0.65~0.80 ≤0.025 ≤0.030 0.0005~0.0015 ≤800.36 0.20目标 0.34 0.68 0.15 ≤0.025 ≤0.020≤600.28~0.60~0.10~氩 站≤0.020 ≤0.035 ≤500.32 0.70 0.200.32~0.12~LF 离站0.65~0.72≤0.025 ≤0.020 0.0005~0.0015 <200.360.183 温度把握℃〔35K 液相线温度 1502℃〕各工序温度把握℃〔拉速 1.8~2.0m/min 状况下〕一倒温 氩站离LF 离中包目 钢种 炉次中包温度液相线第 1 炉度 站温度 站温度标温度3.1 中包温度 1540℃≥T ≥1520℃3.2 中包拒浇温度:≥1560℃;3.3 钢包使用前必需测包底温度,正常测温值必需≥800℃,特别 温度钢包钢水温度修正如下〔在标准值的中上限根底上〕:A 、钢包测温≤800℃,≥600℃,测温值比正常要求值每降低100℃,对应钢水氩站、LF 离站温度上调 4℃。
B 、钢包测温≤600℃,测温值比正常要求值每降低 100℃,对应钢水氩站离站温度、LF 离站各上调 5℃。
3.4 钢包、返修钢包第一炉氩站、LF 离站温度上调 10℃,再加上 3.3 温度补偿。