冷轧工艺(辊型制度,板厚板型控制)
冷轧工艺-酸轧

轧制过程中厚度变化的基本规律
• (5)出口厚度随 轧机纵向刚度 模数变化的规 律
轧制过程中影响轧机出口厚度的因素
• • • • 出口厚度随轧机辊缝变化的规律 出口厚度随轧制力变化的规律 出口厚度随张力变化的规律 出口厚度随轧制速度变化的规律 a出口厚度随摩擦系数变化的规律 b出口厚度随变形抗力变化的规律 c出口厚度随支撑辊油膜厚度变化的规律 • 出口厚度随轧机纵向刚度模数变化的规律
压力AGC原理
• 压力AGC系统的基本原理是Simth最先提出 的弹跳方程。根据引用弹跳方程的方式不同, 压力AGC系统可以分为三种: 1. BISRA型变刚度压力AGC系统
2.厚度计型AGC系统 基本原理:分别测量辊缝S和压力P,通过弹跳方程 计算出口厚度h,再与给定厚度h相比较,根据厚度 偏差调整辊缝值,从而使出口厚度恒定。 3.动态设定型AGC系统
张力AGC原理
• 张力AGC的基本原理是根据测厚仪侧得厚 度偏差来调节张力,依靠张力变化影响带 材塑性系数,从而改变带材出口厚度。控 制模型与反馈AGC控制模型基本相同,都 是反馈型AGC。
速度补偿AGC原理
• 速度补偿的主要功能是预测轧制速度对出 口带材厚度的影响,并在前向通路中消除 其影响。即在出口测量传感器件探测到它 的影响之前将其影响消除。
轧制工艺条件的变动对厚度的影响
• (1)轧辊的摩损 • (2)轧辊和轧机部件的热膨胀 • (3)支撑辊的偏心和轧辊椭圆度 的影响 偏心引起的厚度偏差方程为:
厚度控制方式
• 厚度自动控制(Automatic Gauge Control简称 AGC)在板带轧机上得到普遍应用是从50年代初期 开始的,至今己经发展到了比较成熟的地步。板 带厚度控制应包括板带横向厚度控制和纵向厚度 控制,前者通常由板形控制来解决,后者一般由 板厚控制系统来解决。 • 常用的厚度控制方式有调整压下、调整张力和调 整轧制速度,其原理可通过P-h图加以阐明。
冷轧机常见板型控制问题分析与处理

图1
同样我们也通过修改Lubrication level参数来改变冷却控制的效果。
当然也可以通过增加固定部分流量来增加总的流量,从而将高热合金轧制时产生的高热量带走。
0~20%是ABB工程师在现场调试时设定的值,此参数经过现场验证可以给到30%甚至40%,不过问题也是一样,将参数设定大了以后会降低冷却控制的效果,这也是一对矛盾。
我们现场观察流量设定不宜超过75%,如果轧制热量太高,需要从轧制工艺去考虑,比如减小压下量或降低速度。
因为冷却的能力或者冷却对板形调整的能力满足不了原来的轧制工艺。
在实际生产中发现润滑等级的值调到40%以上B列就处于全喷的状态,这样的情况对于轧制热凸度的控制较好,但是对板型的控制能力又会不足。
因此这个一般不进行设定。
这个设定是指从冷却中拿出一部分出来当润滑用,在生产过程中我们冷却一般都能力不足,本来的冷却量就不大,不需要再从冷却当中分出来给润滑。
因此此参数一般设定为零。
2.在线和离线板型不一致的问题
带材轧制过程中的实时板型通过板型仪的操作画面可以直观的进行观察,但是往往会出现我们在轧制过程中板型仪画面显示的带材实时板型很好,轧制完毕在下游工序进行生产时却会发现带材的实际板型和实时的在线显示的
YAN JIU。
冷轧不锈钢工艺流程介绍

4AP:
退火工艺 Ni系冷带材温: 1050~1150C Cr系冷带材温: 750~1100C 燃料: LPG或NG
酸洗工艺 Ni系冷带: Na2SO4(电解)→HNO3 +HF Cr系冷带: Na2SO4(电解)→HNO3 +HF
Na2SO4(电解)→HNO3
所谓冷轧不锈钢板带生产,不是单纯的“冷 轧”。在冷轧前还要退火、酸洗、修磨等,冷轧后 还要平整、矫直、剪切、垛板等,所以实际上是从 热轧卷开始直到生产出冷轧成品的全过程。
原料黑皮卷
罩式退火炉BAF
十二辊冷轧机 C R M 二十辊冷轧机 C R M
热卷连续退火酸洗线 A P H
修磨机组 C G L
冷卷连续退火酸洗线 A P C 立式连续光亮退火线 B A L
电解(Cr系) 冷轧卷: Na2SO4电解
(2)酸洗: 热轧卷:HNO3+HF(混酸) 冷轧卷:HNO3(电解)、 HNO3 +HF、 HNO3
5、各机组退火酸洗工艺
1AP(C)、2AP:
退火工艺 冷带Ni系材温:1060~1160C 冷带Cr系材温:750~960C 燃料: LPG
酸洗工艺 冷带Ni系: Na2SO4 (电解)→ (HNO3(电解))→ HNO3+HF 冷带Cr系: Na2SO4 (电解)→ HNO3(电解)→ HNO3 (H2O)
不能用罩式炉
4、酸洗
酸洗是冷轧不锈钢的必经工序。现代化宽带不锈 钢生产都是将退火与酸洗设在同一机组连续作业,称 之为连续退火酸洗机组,如AP(H)、AP(C)等。
酸洗的目的:酸洗的目的是去掉热轧及退火过程 中在钢带表面形成的铁鳞,即氧化层。除此之外,酸 洗另一个目的是对不锈钢表面进行钝化处理,提高钢 板耐蚀性。冷轧成品的酸洗尤为重要。
冷轧工艺介绍
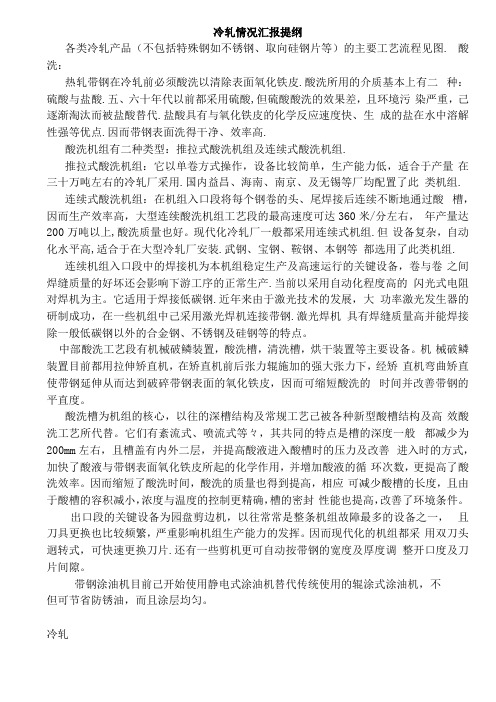
冷轧情况汇报提纲各类冷轧产品(不包括特殊钢如不锈钢、取向硅钢片等)的主要工艺流程见图. 酸洗:热轧带钢在冷轧前必须酸洗以清除表面氧化铁皮.酸洗所用的介质基本上有二种:硫酸与盐酸.五、六十年代以前都采用硫酸,但硫酸酸洗的效果差,且环境污染严重,己逐渐淘汰而被盐酸替代.盐酸具有与氧化铁皮的化学反应速度快、生成的盐在水中溶解性强等优点.因而带钢表面洗得干净、效率高.酸洗机组有二种类型:推拉式酸洗机组及连续式酸洗机组.推拉式酸洗机组:它以单卷方式操作,设备比较简单,生产能力低,适合于产量在三十万吨左右的冷轧厂采用.国内益昌、海南、南京、及无锡等厂均配置了此类机组.连续式酸洗机组:在机组入口段将每个钢卷的头、尾焊接后连续不断地通过酸槽,因而生产效率高,大型连续酸洗机组工艺段的最高速度可达360米/分左右,年产量达200万吨以上,酸洗质量也好。
现代化冷轧厂一般都采用连续式机组.但设备复杂,自动化水平高,适合于在大型冷轧厂安装.武钢、宝钢、鞍钢、本钢等都选用了此类机组.连续机组入口段中的焊接机为本机组稳定生产及高速运行的关键设备,卷与卷之间焊缝质量的好坏还会影响下游工序的正常生产.当前以采用自动化程度高的闪光式电阻对焊机为主。
它适用于焊接低碳钢.近年来由于激光技术的发展,大功率激光发生器的研制成功,在一些机组中己采用激光焊机连接带钢.激光焊机具有焊缝质量高并能焊接除一般低碳钢以外的合金钢、不锈钢及硅钢等的特点。
中部酸洗工艺段有机械破鳞装置,酸洗槽,清洗槽,烘干装置等主要设备。
机械破鳞装置目前都用拉伸矫直机,在矫直机前后张力辊施加的强大张力下,经矫直机弯曲矫直使带钢延伸从而达到破碎带钢表面的氧化铁皮,因而可缩短酸洗的时间并改善带钢的平直度。
酸洗槽为机组的核心,以往的深槽结构及常规工艺己被各种新型酸槽结构及高效酸洗工艺所代替。
它们有紊流式、喷流式等々,其共同的特点是槽的深度一般都减少为200mm左右,且槽盖有内外二层,并提高酸液进入酸槽时的压力及改善进入时的方式,加快了酸液与带钢表面氧化铁皮所起的化学作用,并增加酸液的循环次数,更提高了酸洗效率。
冷轧板的工艺介绍
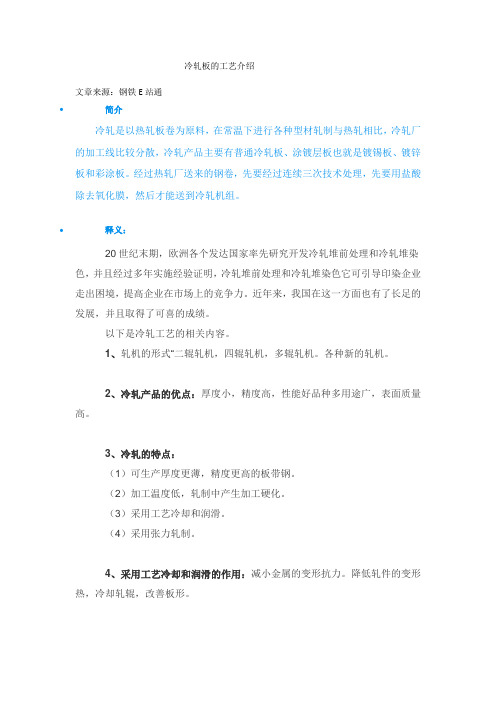
冷轧板的工艺介绍文章来源:钢铁E站通∙简介冷轧是以热轧板卷为原料,在常温下进行各种型材轧制与热轧相比,冷轧厂的加工线比较分散,冷轧产品主要有普通冷轧板、涂镀层板也就是镀锡板、镀锌板和彩涂板。
经过热轧厂送来的钢卷,先要经过连续三次技术处理,先要用盐酸除去氧化膜,然后才能送到冷轧机组。
∙释义:20世纪末期,欧洲各个发达国家率先研究开发冷轧堆前处理和冷轧堆染色,并且经过多年实施经验证明,冷轧堆前处理和冷轧堆染色它可引导印染企业走出困境,提高企业在市场上的竞争力。
近年来,我国在这一方面也有了长足的发展,并且取得了可喜的成绩。
以下是冷轧工艺的相关内容。
1、轧机的形式“二辊轧机,四辊轧机,多辊轧机。
各种新的轧机。
2、冷轧产品的优点:厚度小,精度高,性能好品种多用途广,表面质量高。
3、冷轧的特点:(1)可生产厚度更薄,精度更高的板带钢。
(2)加工温度低,轧制中产生加工硬化。
(3)采用工艺冷却和润滑。
(4)采用张力轧制。
4、采用工艺冷却和润滑的作用:减小金属的变形抗力。
降低轧件的变形热,冷却轧辊,改善板形。
5、采用张力轧制的作用:(1)防止带钢在轧制中跑偏(2)改变应力状态,降低轧制力,减小轧辊弹性压扁,利于轧制更薄的产品(3)使带钢保证平直,改善板形。
6、冷轧全连续轧制工艺流程:原料-预退火-酸轧-成品退火-平整-精整-包装-成品原料-酸轧-平整-精整-包装-成品原料-酸轧-成品退火-平整-精整-包装-成品原料-酸轧-包装-成品7、板带钢的种类(按厚度分类)箔材:0.2mm以下薄板:0.2-4.0mm中板:4-20mm厚板:20-60mm特厚板:60mm以上8、什么是钢材的产品标准:钢材的产品标准是生产单位和使用单位在交货和收货时的技术依据,也是生产单位制定工艺和判定产品质量的主要依据。
9、产品标准的主要内容是什么:(1)品种规格(2)性能标准(3)试验标准(4)交货标准(5)特殊条件10、标准分为哪几类:国际标准国外先进标准国家标准部颁标准企业标准11、板带板技术要求:尺寸精度高,板型好,性能好,表面质量好,化学成分合适12、中厚板轧机形式:二辊可逆式轧机三辊劳特式轧机四辊可逆式轧机万能轧机复合式轧机13、中厚板生产工艺过程:(一般钢板)原料-加热-除鳞-轧制-辊矫-冷却-检查-剪切-尺寸形状检查-力学性能试验-标记-入库-发货14、加热的目的:提高金属塑性,降低变形抗力,使坯料内外温度均匀,改变金属的结晶组织,保证生产需要的机械和物理性质15、过热:钢在高温下保温时间过长使晶粒粗化,机械性能变坏,这种现象叫做过热。
冷轧钢板生产工艺管理制度
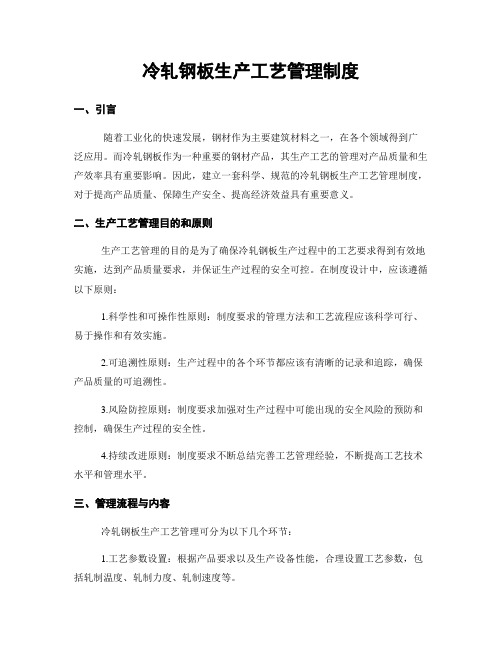
冷轧钢板生产工艺管理制度一、引言随着工业化的快速发展,钢材作为主要建筑材料之一,在各个领域得到广泛应用。
而冷轧钢板作为一种重要的钢材产品,其生产工艺的管理对产品质量和生产效率具有重要影响。
因此,建立一套科学、规范的冷轧钢板生产工艺管理制度,对于提高产品质量、保障生产安全、提高经济效益具有重要意义。
二、生产工艺管理目的和原则生产工艺管理的目的是为了确保冷轧钢板生产过程中的工艺要求得到有效地实施,达到产品质量要求,并保证生产过程的安全可控。
在制度设计中,应该遵循以下原则:1.科学性和可操作性原则:制度要求的管理方法和工艺流程应该科学可行、易于操作和有效实施。
2.可追溯性原则:生产过程中的各个环节都应该有清晰的记录和追踪,确保产品质量的可追溯性。
3.风险防控原则:制度要求加强对生产过程中可能出现的安全风险的预防和控制,确保生产过程的安全性。
4.持续改进原则:制度要求不断总结完善工艺管理经验,不断提高工艺技术水平和管理水平。
三、管理流程与内容冷轧钢板生产工艺管理可分为以下几个环节:1.工艺参数设置:根据产品要求以及生产设备性能,合理设置工艺参数,包括轧制温度、轧制力度、轧制速度等。
2.设备状态监测:通过对生产设备进行状态监测,及时发现和排除故障,确保设备处于正常工作状态,避免影响产品质量。
3.原材料控制:对进入生产环节的原材料进行严格检验,包括钢材质量、化学成分等,确保原材料符合生产要求。
4.工艺控制:对生产工艺进行严格控制,包括轧制工艺流程、润滑方式等,确保产品质量稳定。
5.质量检验:对生产过程中的产品进行抽样检测,确保产品质量符合要求,并及时发现和纠正问题。
6.记录备案:对生产工艺流程、设备状态、原材料检验以及质量检验等进行记录备案,确保生产过程的可追溯性。
四、工艺管理制度的实施与考核为了确保工艺管理制度能够得到有效执行,应建立相关的执行机制和考核方法,具体包括以下几个方面:1.培训与交流:及时组织工艺管理制度培训和交流会议,提高员工对制度的理解和执行能力。
不锈钢冷轧生产工艺经典实用
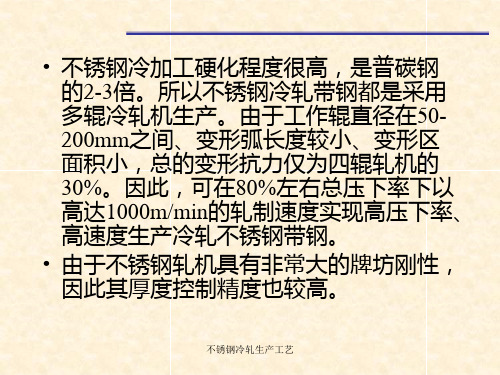
几个关注点
• 轧辊参数 • 轧辊配对 • 砂轮型号 • 磨削也配制 • 轧辊探伤 • 轧辊周期管理
不锈钢冷轧生产工艺
(三)、精整
• 精整是不锈钢生产的后部工序。产品的 尺寸规格和质量能否满足用户要求,精 整有很大作用。通常不锈钢精整包括平 整、矫直、纵切、横切等工序。由于平 整的特殊性,它既可说是精整,又可说 是最后一道冷轧。
不锈钢冷轧生产工艺
• 冷轧后不锈钢的退火,都是通过再结晶 消除加工硬化而达到软化目的。除此之 外,奥氏体不锈钢还要使冷轧时产生的 形变马氏体转变为奥氏体,因此都用 APC、 BA L这样的连续炉退火。
● 固溶处理:加热到1000--1150℃之间碳 化物溶解,快速冷却使其形成稳定的奥 氏体组织。
• 奥氏体不能用罩式炉,铁素体用罩式炉 质量难保证。
不锈钢冷轧生产工艺
2、纵切分条
• 当带钢成卷交货时,要在纵切机线上用 圆盘剪切去毛边,为适应来料的宽度变 化,圆盘剪距离可以调整。圆盘剪操作 主要在于适当调整上下剪刃的间隙量和 重合量,间隙量一般随着材料厚度而增 大,一般为材料厚度的7-12%,而重合最 虽与材料厚度有关,但不完全是对应关 系,应结合操作经验确定。
以前进行的修磨,一般称为粗磨(RP)。其目 的是消除热轧和退火酸洗工序造成的表面缺陷, 改善外观质量,为获得高质量的成品表面创造 条件。 • 成品修磨是冷轧成品退火后进行的修磨,一般 称为精磨(FP)。目的是得到某种特定的表面 质量,以满足建材、厨房设备、家电用品等用 途的特殊要求。
不锈钢冷轧生产工艺
DISA喷丸机
不锈钢冷轧生产工艺
20辊森吉米尔可逆式冷轧机
不锈钢冷轧生产工艺
平整机 平整机
不锈钢冷轧生产工艺
冷轧带钢的板形控制

测量辊是该系统最主要的组成,也是板形测量成功的关键。测量辊实际是由钢质芯轴和经硬化处 理的钢环组成,钢环内是传感器。测量辊分成多个测量圆环,每个测量圆环有4个传感器,传感器在每 个测量环的圆周上成900垂直安装。因此,测量辊每旋转一周可以对带钢平直度测量4次。它采用了大 量压磁式传感器,所有传感器的输出组合在屏幕上以曲线方式显示出平直度偏差。这为轧辊调整提供
6张力调节和压下率分配
6.1张力调节【4J
冷轧生产的特点之一就是张力轧制,受多种冈素干扰,张力值时有波动。生产中,必须保证张 力恒定,才能使轧制状态稳定。张力较大,可保证轧制稳定、板形良好,但超过一定值时容易造成 断带、薄料卸卷困难;张力过4,贝JJ会引起跑偏,因此,应根据材质、规格、钢种等情况选取张力值。 板形不同,其张力调节方式也不同:中浪应适当减小张力;两边浪可加大张力,使轧制力降低,减 小边部延伸。在生产中不能只依靠张力调节来控制板形,因为其对板形控制的程度有限。这些就要 靠操作工的经验和操作水平了。
_r
● _'
卜-
一个测量区域
、一 l
图3沿带钢宽度测量平直度的图形化显示
轧机主控室一共有两个控制柜:一个是sl,对应带钢经过l架后的平直度;一个是s5,对应带钢经 过5架后的平直度。
..128..
3自动板形控制系统(Al℃)
带钢平直度是由辊缝决定的,像温度、凸度等不平直因素,会引入带钢内部的应力,影响辊缝, 因此,调整辊缝时不管什么类型的平直度偏差都需要调整,使其达到要求的平直度。还有辊缝执行机 构对带钢平直度有影响,所以要把执行机构的动作组合起来,以抵消平直度偏差。这就是自动板形 控制系统(AFC)的功能和作用。
冷轧带钢的板形控制
作者: 作者单位:
- 1、下载文档前请自行甄别文档内容的完整性,平台不提供额外的编辑、内容补充、找答案等附加服务。
- 2、"仅部分预览"的文档,不可在线预览部分如存在完整性等问题,可反馈申请退款(可完整预览的文档不适用该条件!)。
- 3、如文档侵犯您的权益,请联系客服反馈,我们会尽快为您处理(人工客服工作时间:9:00-18:30)。
▪ 带钢厚度: 0.2 – 2.5 mm
▪ 带钢宽度: 800 – 1 870 mm
▪ 钢卷外径: Max. Ø 2100 mm
▪
Min. Ø 1000 mm
▪ 钢卷内径: Ø 610 mm
▪ 卷重: max. 38 t
冷轧卷主要技术参数
硬钢
▪ 钢种: CQ ~DDQ - HSS, BH, DP, Trip
冷轧工艺基本概念
1) 连轧常数
秒流量是指单位时间内通过轧制变 形区内任一横断面的金属体积,则 秒流量不变原则可描述为: ▪ F1V1=F2V2=······= FnVn=C
其中C-连轧常数;F-板带横截面积
▪ 对于冷轧而言,不考虑宽展,故此 式可化为:
▪ H1V1=H2V2=······=HnVn=C
▪ 钢卷外径: Max. Ø 2150 mm
▪
Min. Ø 1000 mm
▪ 钢卷内径: Ø 760 mm
▪ 卷重 Max. 38 t
max.390 N/mm² max.800 N/mm²
max.270N/mm² max.615N/mm²
冷轧卷主要技术参数
软钢
▪ 钢种: CQ, DQ, DDQ, EDDQ, SEDDQ
▪ E =he-hE
▪ 式中hE为带材实际边部的厚度。
冷轧工艺基本概念
6) 楔形 ▪ 楔形(CT)即左右边部标
志点厚度之差,如下图所示: CT=her - hel
冷轧机的发展
▪ 第一阶段是在战后20年,这时轧机向大型、高刚度、 高速度方向发展,并致力于对张力拉断的控制,以 适应生产高速发展的需要。
CVC轧机原理
▪ CVC轧机是德国西马克公 司于80年代初开发的新机 型。这种轧机的特点是采用 了特殊的S型轧辊,上下辊 形状相同,但左右倒向配置, 并可按相反方向同时作轴向 移动。四辊CVC轧辊的轴 向抽动将直接改变辊缝的几 何形状。六辊CVC用这种 辊作中间辊时,可以调整工 作辊的弯曲变形,从而改变 实际辊缝凸度。
顺义冷轧分厂
冷轧工艺简介
主要内容
1. 首钢1850冷轧简介 2. 冷轧工艺 3. 冷轧视频
首钢1850酸洗冷轧联合机组简介
▪ 首钢1850冷轧产品:汽车板、家电板为主。 ▪ 1850冷轧主要包括一条酸轧机组、一条连续
退火机组和两条热镀锌机组。 ▪ 酸洗段采用紊流盐酸酸洗,冷轧段采用六辊
CVC轧机。
冷轧工艺基本概念
2) 张力轧制 ▪ 在连续轧制时,实际上保
持理论上的秒流量相等使 连轧常数恒定是相当困难 的,为了使轧制过程能够 顺利进行,常有意识地采 用堆钢或拉钢的操作技术。 对于机架与机架之间采用 拉钢轧制,即张力轧制。 所谓张力轧制,就是轧件 的轧制变形是在有一定的 前张力和后张力作用下实 现的。
I
L L
105
冷轧工艺基本概念
3) 板形
▪ 板形是指板带材的平坦度,即 轧制后在不存在张力的状态下 (自然状态),板带材的平坦 性。
▪ 板形不良直观地表现为带钢外 观的翘曲。若边部延伸率大,则 产生边浪;中部延伸大,则产生 中浪或瓢曲;一边比另一边延 伸大,则产生“镰刀弯”。
▪ 板形不良是由于带宽方向上 各处延伸不均造成内部残余 应力分布不均导致的。
▪ 冷轧带钢的翘曲比热轧带钢 复杂,这是由于内应力的不 同分布造成的。根据内应力 的分布规律和带钢翘曲情况, 将板形缺陷分为不同的类型
冷轧工艺基本概念
▪ 4) 板凸度及板凸度一定原则
▪ 板凸度是描述带材横截面形状的一项主要指标。首先介绍板凸量(△)的概念, 板凸量为板带宽度中点处厚度与边部标志点厚度之差。如式1-7所示。
轧机区主要设备简介
轧机段设备:
▪ 机架 ▪ 液压调整系统 ▪ 楔形调整系统 ▪ 中间辊窜辊系统 ▪ 轧辊 ▪ 换辊装置 ▪ 乳化液喷淋装置 ▪ 防缠导板
轧机区主要设备简介
轧机出口段设备:
▪ 测厚仪 ▪ 带钢板形仪 ▪ 测速仪 ▪ 夹送辊 ▪ 转鼓飞剪 ▪ 皮带运输机 ▪ 卡罗塞卷取机 ▪ 钢卷小车 ▪ 打捆、称重设备 ▪ 套筒运输设备 ▪ 离线检查站
CVC轧机优缺点
▪ ①凸度调节范围大。调整CVC辊型 参数可直接改变调节区域和调节幅度;
▪ ②辊间接触压力变化不大,但压力分 布有些变化。平均接触压力与普通四 辊相同;
▪ ③可以动态调整。CVC辊的抽动可 以在轧制过程中进行,参与板形闭环 控制;
▪ ④板形控制能力较强,CVC辊的抽 动与弯辊力的配合,可以有效纠正板 形缺陷。
▪ △=hc-he
(式1-7)
▪ 板凸度则表示为板凸量与板带边部标志点厚度之比,即△/he。
▪ 所谓板凸度一定原则就是指为了满足均匀变形的条件,保证板形良好,必须使 轧制前板凸度等于轧制后的板凸度。
▪ 5) 边部减薄
▪ 边部减薄(E)是指带钢与轧辊接触处的轧辊压扁在板带边部由于过渡区而造 成的带钢边部减薄的现象。
▪ 带钢厚度: 0.35 – 2.5 mm
▪ 带钢宽度: 800 – 1 870 mm
▪ 钢卷外径: Max. Ø 2 100 mm
▪Байду номын сангаас
Min. Ø 1000 mm
▪ 钢卷内径: Ø 610 mm
▪ 卷重: max. 38 t
轧机区主要设备简介
轧机入口段设备:
▪ 焊缝检测仪 ▪ 测张辊 ▪ 带钢夹紧装置 ▪ 横切剪 ▪ 测厚仪 ▪ 卷扬机 ▪ 带钢侧导
▪ 第二阶段是从1964年实现计算机厚控开始的,冷轧 系统采用了合理的厚度控制模型,加上计算机的自 动控制等,使冷轧厚度0.4mm以下的薄板纵向厚度 公差可达±3μm。
▪ 最近10多年步入了第三阶段,其特征是致力于产品 断面和平直度的改善。
冷轧机的发展
▪ 日本日立公司在70年代初 开发的HC轧机是目前应 用较广的冷轧机型。这种 轧机的主要特征是在普通 四辊轧机的工作辊与支承 辊之间增加了可轴向抽动 的中间辊,中间辊又增加 了弯辊装置,工作辊也可 改成轴向抽动式并带有弯 辊。
热轧原料卷主要技术参数
▪ 钢种: CQ, DQ, DDQ, EDDQ, SEDDQ和 HSS
▪ 抗拉强度:
▪
CQ, DQ, DDQ, EDDQ, SEDDQ
▪
HSS
▪ 屈服强度:
▪
CQ, DQ, DDQ, EDDQ, SEDDQ
▪
HSS
▪ 带钢厚度: 1.6 – 6.0 mm
▪ 带钢宽度: 800 – 1900 mm