管道对接焊缝的超声波检测
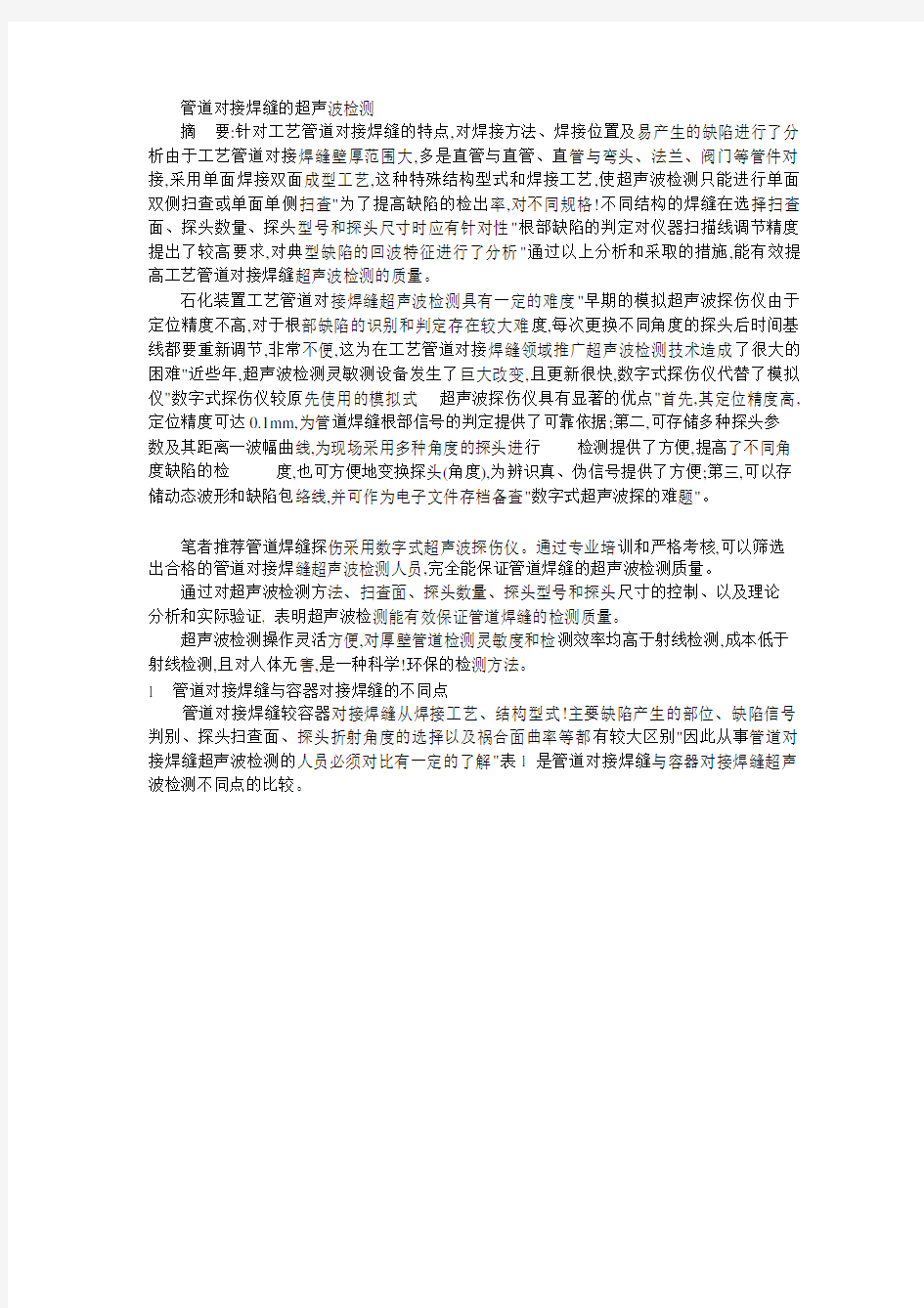
- 1、下载文档前请自行甄别文档内容的完整性,平台不提供额外的编辑、内容补充、找答案等附加服务。
- 2、"仅部分预览"的文档,不可在线预览部分如存在完整性等问题,可反馈申请退款(可完整预览的文档不适用该条件!)。
- 3、如文档侵犯您的权益,请联系客服反馈,我们会尽快为您处理(人工客服工作时间:9:00-18:30)。
管道对接焊缝的超声波检测
摘要:针对工艺管道对接焊缝的特点,对焊接方法、焊接位置及易产生的缺陷进行了分析由于工艺管道对接焊缝壁厚范围大,多是直管与直管、直管与弯头、法兰、阀门等管件对接,采用单面焊接双面成型工艺,这种特殊结构型式和焊接工艺,使超声波检测只能进行单面双侧扫查或单面单侧扫查"为了提高缺陷的检出率,对不同规格!不同结构的焊缝在选择扫查面、探头数量、探头型号和探头尺寸时应有针对性"根部缺陷的判定对仪器扫描线调节精度提出了较高要求,对典型缺陷的回波特征进行了分析"通过以上分析和采取的措施,能有效提高工艺管道对接焊缝超声波检测的质量。
石化装置工艺管道对接焊缝超声波检测具有一定的难度"早期的模拟超声波探伤仪由于定位精度不高,对于根部缺陷的识别和判定存在较大难度,每次更换不同角度的探头后时间基线都要重新调节,非常不便,这为在工艺管道对接焊缝领域推广超声波检测技术造成了很大的困难"近些年,超声波检测灵敏测设备发生了巨大改变,且更新很快,数字式探伤仪代替了模拟仪"数字式探伤仪较原先使用的模拟式超声波探伤仪具有显著的优点"首先,其定位精度高,定位精度可达0.1mm,为管道焊缝根部信号的判定提供了可靠依据;第二,可存储多种探头参
数及其距离一波幅曲线,为现场采用多种角度的探头进行检测提供了方便,提高了不同角度缺陷的检度,也可方便地变换探头(角度),为辨识真、伪信号提供了方便;第三,可以存储动态波形和缺陷包络线,并可作为电子文件存档备查"数字式超声波探的难题"。
笔者推荐管道焊缝探伤采用数字式超声波探伤仪。通过专业培训和严格考核,可以筛选出合格的管道对接焊缝超声波检测人员,完全能保证管道焊缝的超声波检测质量。
通过对超声波检测方法、扫查面、探头数量、探头型号和探头尺寸的控制、以及理论
分析和实际验证, 表明超声波检测能有效保证管道焊缝的检测质量。
超声波检测操作灵活方便,对厚壁管道检测灵敏度和检测效率均高于射线检测,成本低于射线检测,且对人体无害,是一种科学!环保的检测方法。
1 管道对接焊缝与容器对接焊缝的不同点
管道对接焊缝较容器对接焊缝从焊接工艺、结构型式!主要缺陷产生的部位、缺陷信号判别、探头扫查面、探头折射角度的选择以及祸合面曲率等都有较大区别"因此从事管道对接焊缝超声波检测的人员必须对比有一定的了解"表1 是管道对接焊缝与容器对接焊缝超声波检测不同点的比较。
2 焊接工艺及缺陷分析
管道对接焊缝的超声波检测有两个重要环节,一是如何能保证不漏检缺陷,二是如何能正确识别和判定缺陷"以下对管道的接头型式、焊接方法、焊接位置及易产生的缺陷进行了分析,为设计检测工提高缺陷的检出率和信号判定提供参考。
2.1 结构型式与扫查面
石化装置工艺管道对接焊缝一般可分为3 种型式:直管与直管对接、直管与管件对接、管件与管件对接。
(1)直管与直管对接焊缝探头可以在焊缝两侧进行扫查。
(2)直管与管件对接焊缝由于管件侧表面为不规则曲面(如弯头、法兰、阀门或三通等),探头不能良好藕合,因此,只能从直管一侧进行扫查,为了提高缺陷检出率,应选择2种不同角度的探头进行扫查。
(3)管件与管件对接焊缝由于焊缝两侧均为不规则曲面(如弯头!法兰、阀门或三通等),探头不能良好祸合,因此,这类焊缝不能进行正常的超声波检测"如客户有措施将焊缝余高磨平(与母材平齐), 则可将探头通过磨平的焊缝进行检测"将焊缝打磨至与母材平齐是一件很困难的事,一般不这样做。
2.2 焊接位置
了解焊接位置有助于缺陷性质的分析判断。管道对接焊缝的焊接位置分为水平转动、水平固定、垂直固定和45度斜固定。
(l) 水平转动口焊接时,焊接位置总是处于时钟11点或1 点附近的位置,焊接操作最易控制,最不易产生焊接缺陷(图1)"
(2)水平固定口焊接时,上半部分处于平焊位置,下半部分处于仰焊位置,两侧处于立焊位置(图2) 。
(3)垂直固定口焊接时,其位置为横焊,焊接位置示意见图3。
(3)45 度斜固定口焊接时,各部分在水平固定的基础上又增加了倾斜角度,加大了焊接难度(图4)。
2.3 各焊接位置易产生的缺陷类型
(1)焊接程序目前石化装置管道对接焊缝均采用氢弧焊打底,焊工在打底结束前留一小段用作检查孔,用手电筒观察根部打底情况,若有不良现象则立即将不良部位用磨光机去除重焊,最终检查良好后将根部最后一小段焊好"氢弧焊打底结束后,对于较厚的焊缝一般采用手工电弧焊或埋弧自动焊填充盖面。
(2)平焊位置铁水熔化后在重力的作用下会向下淌,因此平焊位置焊接时要控制电流不能过大, 焊接电流和焊接速度要适当,否则易形成焊瘤和烧穿。焊条接头和焊瘤部位易产生气孔。
(3)立焊位置在立焊位置因铁水下淌导致焊缝波纹粗糙及内外表面焊缝成型不良,也容易
产生未焊透、未熔合!焊瘤及咬边"因此要控制焊接电流不能过大,焊接速度不能过快。(4)
仰焊位置仰焊位置易产生内凹、未焊透、未熔合及焊瘤(余高过高),仰焊位置电流过大易产生内凹!烧穿和焊瘤,电流过小易产生未焊透和未熔合,因此仰焊部位的焊接难度最大"焊工常采用灭弧焊法进行焊接,即引弧!将焊条熔化一点立即断弧、待片刻熔池凝固、再继续引弧熔化一点焊条立即断弧...这样循环持续,直至铁水成型达到可控为止,在烧第二层焊缝时电流也不能过大,否则将第一层铁水熔化下坠形成内凹,电流越大形成的内凹越深。
(5)横焊位置管子垂直固定,焊工围绕焊缝进行横向焊接。横焊位置焊接时,铁水受重力
作用,上部易出现咬边,坡口易产生未熔合,焊接每层之间如果清理不好易产生夹渣。焊
缝表面横排波纹控制不好会比较粗糙。
3 探头的选择
探头选择时要考虑的因素有:
(1) 检测厚度检测较薄焊缝应选择大K值、短前沿探头,一次波尽可能扫查更多的焊缝截面;对于大厚度焊缝应选择晶片尺寸较大、K 值合适、具有足够灵敏度的探头。
根据实际工作经验,笔者推荐壁厚不小于7mm的焊缝宜采用单斜探头进行检测。壁厚
< 7mm 的焊缝检测时杂波干扰严重,目前多选用聚焦探头或双晶探头。但聚焦探头和双晶
探头一般宽度较大,与小径管藕合时要进行修磨"由于聚焦探头和双晶探头都是在焦点附近
灵敏度最高,探测范围受到一定影响,工艺管道壁厚< 7mm 的管道管径一般均较小,因此,对壁
厚<7mm 的管道焊缝不推荐采用超声波检测法进行检测。
(2) 检测面曲率半径R 较小的管道,要选择接触面小的探头,以保证良好藕合;直径较大
的管道可以选择尺寸较大的探头,以提高检测效率。探头与工件接触面尺寸W 应满足下式:
2
R≥W/4 (1)
目前市场销售的晶片尺寸为6mm x 6mm 的短前沿小晶片探头,其探头宽度一般为12mm。由式(l)计算可得管道直径应> 72mm。为提高藕合效果,笔者推荐采用探头宽度为12mm 的小晶片短前沿探头进行检测时,管道直径下限为100mm。
(3)扫查面直管与直管对接,探头在焊缝两侧扫查时,可以选择1种K 值的探头;直管与管
件对接,探头只能在焊缝一侧进行扫查时,应选择2种折射角相差不少于10度的探头进行扫查,其中较小K值的探头,一次波扫查范围不少于焊缝截面的1/4
(4)探头频率管道探伤宜选择较高频率的探头,以提高指向性和定位精度。推荐采用频率
为5MHz的探头,对于较厚管道(厚度)不小于4 0mm)可以选择2.5M Hz的探头。
对于根部可疑信号,尽可能选择小K值探头复验"经验表明,小K 值探头定位精度高,误
差小。
综合上述条件,不同厚度的管道推荐选择的探头角度和前沿距离见表2,不同曲率的管道
推荐选择的探头尺寸见表3。