镁合金化原理
镁合金的强化机制
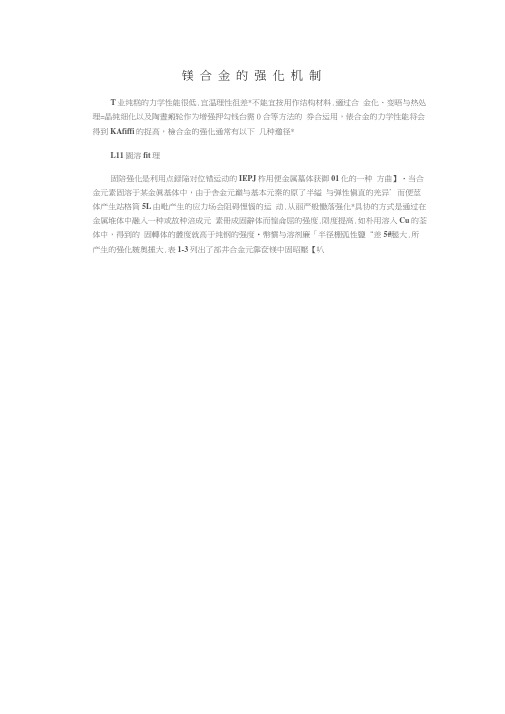
镁合金的强化机制T业纯糕的力学性能很低.宜温理性徂差*不能宜按用作结构材料.適过合金化、变晤与热处理=晶純细化以及陶晝瘢轮作为增强押勾钱台需0合等方法的券合运用,俵合金的力学性能将会得到KAfiffi的捉高,檢合金的强化通常有以下几种邀径*L11園溶fit理固陪强化是利用点録陥对位错运动的IEPJ柞用便金属墓体获御01化的一种方曲】・当合金元素固溶于某金眞基体中,由于舎金元巔与基本元秦的原了半縊与弹性愼直的羌异’而便莖体产生站格筒5L由毗产生的应力场会阻碍悝惱的运动.从丽严般慟落强化*具协的方式是通过在金属堆体中融入一种或故种涪成元素冊成固辭体而惶侖屈的强度.陨度提髙.如朴用溶入Cu的荃体中,得到的固轉体的叢度就高于纯钢的强度•幣慣与溶剂廉「半径棚弧性鹽“差5#腿大.所产生的强化皴奧捶大.表1-3列出了部井合金元靠奁镁中固昭壓【叭A IT样分合介尢素虚4中拘H)況zt*元素用溶度相系转交3处悼尔分《L%頂逼分数/%Ag 3.815,0共晶471Al11.812.7共晶437Cd100100八析■Gd 4.5323.69共晶54«Li17.0 5.5共品588Mn 1.022包晶652Nd13共品552Y 3.7512.5共晶565Zn 2.4 6.2共崩347Zr 1.0 3.3包晶65313.2第二相粒于强化页二相粒于强化可分为沉淀强化和弥散强化:沉淀强化即町效彊化•因获得第二相粒子的工艺不同,第二相粒子强化有不同的名称:①酒过相变热处理获得的,林为析出硬化、沉淀強化或时效强化:②通过粉末烧结或内氧化敬御的.称为號散强化㈢.冇时也不加区別的混称为分做强化或粒子张比.合金产生时效强化亦須满兀一•定条件.即合令元素在基体中的迥溶度下降而彼少.时效可强化的合金在a单相区长时何保温,可以使铸态合金中分称在詁界或胡内的第二相分解,合金元素原子分布于基体抽格,如果此时以较大的冷却速愷(如水冷)使合金冷却到室温,即可御到过饱和固溶体.过饱和固陷体在a十"两相区适当温度下进行长时间时效处理,过诲和固溶体将会分解成为a基体和沉淀郴"弥敢分布的沉淀相粒子阴碍位错运动从而提髙合金强度。
镁合金熔炼原理与工艺
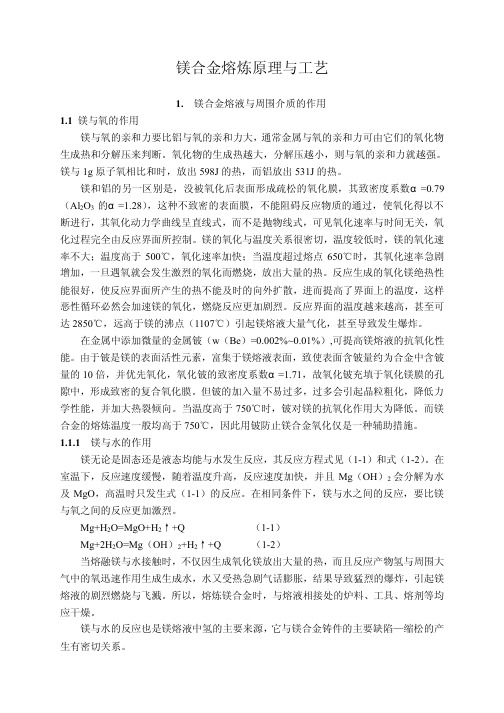
00.1 58.0 21.0 80.0 %�拌搅有� �6FS� σ 40.0
60.0 50.0 40.0 30.0 %�拌搅无� �6FS� σ 20.0
018 087 067 057 ℃/度温 556
值荐推的量含 6FS 的小最面表液熔金合镁入通 1-1 表
�金合的土稀含而�小更下倾化氧的金合锆、锌含�低镁纯比向倾化氧其�19ZA 金合的 铝含如。响影定一有也用作护防的气空 6FS 对素元的金合。键关制控和计设统系护保是 向倾化氧的镁�高升度温�明证验实。响影的度温受也用作化氧的液熔镁止防 6FS
面液�加增的量入输着随。致所失损的露泄和应反液镁与 6FS 为因是要主这�大要量含 。用作蚀腐的重严有具还备设
对氛气且而�降下果效化氧抗的镁仅不�时%1 于大数分积体的 6FS 中氛气护保。用作 无�型线直属均线曲化氧的镁� �%1 于大数分积体�高过或�%10.0 于小数分积体�低 过量含 6FS 中气空�关有量含其与用作烧燃防的液熔镁对 6FS�明证验实重增化氧
定一入通合混�时℃507 于高度温当�明表果结究研些一。高要还的镁纯比向倾化氧其
.2-1 表见。果效的护保高提于助有 2OC 的量
化优的量含和分组的体气护保合混 6FS 以所.1-1 表见�加增的应相应也量含 6FS�大加 。平水的定一在制控量含 6FS 将能可有才样这
�封密地效有要须必置装炼熔金合镁而因�加增也量 6FS 的耗消所 �加增也量含 6FS 方上 的用应际实但�液熔金合镁护保效有可就量含 6FS 的%10.0 为数分积体�明表验实
在。 �2-1�式和�1-1�见式程方应反其�应反生发水与能均态液是还态固是论无镁
水为解分会 2�HO�gM 且并�快加度速应反�高升度温着随�慢缓度速应反�下温室
镁合金阳极氧化

镁合金阳极氧化镁合金阳极氧化是一种常见的表面处理方法,可以改善镁合金的耐腐蚀性能和机械性能。
本文将从镁合金阳极氧化的原理、工艺以及应用等方面进行介绍。
一、镁合金阳极氧化的原理镁合金阳极氧化是指在一定的电解条件下,将镁合金的表面转化成致密的氧化膜。
这种氧化膜具有很高的硬度和耐腐蚀性,可以有效地保护镁合金的基体。
在镁合金阳极氧化过程中,阳极氧化膜主要由 MgO 和 Mg(OH)2 组成,其中 MgO 是主要的成分,具有较高的硬度和耐腐蚀性。
镁合金阳极氧化的工艺包括预处理、电解液配制、电解过程以及后处理等环节。
1. 预处理:镁合金在阳极氧化前需要进行表面的预处理,以去除表面的油污和氧化层。
常用的方法有碱洗、酸洗和溶剂清洗等。
2. 电解液配制:电解液是进行阳极氧化的关键,常用的电解液包括硫酸、硝酸和磷酸等。
在配制电解液时需要控制其成分和浓度,以及调整电解液的温度和pH值等参数。
3. 电解过程:在电解槽中,将镁合金作为阳极,通过外加电流使阳极氧化反应发生。
在电解过程中,需要控制电流密度、电解时间和电解温度等参数,以获得理想的氧化膜。
4. 后处理:阳极氧化后,需要对镁合金进行后处理,以去除电解液残留和改善氧化膜的性能。
常用的后处理方法包括热处理、封孔和染色等。
三、镁合金阳极氧化的应用镁合金阳极氧化的应用广泛,主要体现在以下几个方面:1. 电子产品:镁合金阳极氧化后的表面具有很好的绝缘性能和机械强度,可用于电子产品的外壳和散热器等部件。
2. 汽车工业:镁合金阳极氧化后的表面具有良好的耐腐蚀性和装饰性,可用于汽车零部件的制造,如车身板材、排气管等。
3. 航空航天:镁合金阳极氧化后的表面具有较高的硬度和耐腐蚀性,可用于航空航天领域的结构材料和零部件。
4. 生物医学:镁合金阳极氧化后的表面具有良好的生物相容性,可用于生物医学领域的植入材料和修复器械等。
镁合金阳极氧化是一种重要的表面处理方法,可以显著提高镁合金的性能和应用范围。
镁合金 阳极 氧化

镁合金阳极氧化镁合金是一种具有优异性能的金属材料,广泛应用于航空航天、汽车制造、电子设备等领域。
而阴极氧化是一种常见的表面处理技术,可以增强镁合金的耐腐蚀性能和硬度。
本文将重点介绍镁合金阳极氧化的原理、过程以及其在实际应用中的优势。
一、镁合金阳极氧化的原理阳极氧化是利用电解液中的阳极电解质在电场作用下,通过氧化反应形成氧化膜的一种表面处理方法。
在镁合金阳极氧化过程中,镁合金作为阴极,通过施加电流使得阳极电解液中的阳离子被还原,从而形成氧化膜。
氧化膜主要由氧化镁组成,具有较高的硬度和耐腐蚀性。
二、镁合金阳极氧化的过程镁合金阳极氧化的过程主要包括预处理、电解液配方、电解过程和后处理等几个步骤。
1. 镁合金预处理:包括去油、去尘等表面清洁工序,以保证阳极氧化能够在干净的表面进行。
2. 电解液配方:电解液的成分会直接影响到氧化膜的性能。
一般情况下,电解液由硫酸、硫酸铝等组成,通过调整电解液的配方可以得到不同性能的氧化膜。
3. 电解过程:将经过预处理的镁合金作为阴极,与阳极电解液相连,施加一定电压和电流进行电解。
在电解过程中,阳极电解液中的阳离子被还原,生成氧化膜。
4. 后处理:将氧化膜进行密封处理,以提高其耐腐蚀性能和硬度。
常用的后处理方法有热水封孔、镁质封孔等。
三、镁合金阳极氧化的优势镁合金阳极氧化具有以下几个优势:1. 耐腐蚀性能提升:经过阳极氧化处理的镁合金表面形成了致密的氧化膜,有效阻止了外界物质对镁合金的侵蚀,提高了材料的耐腐蚀性能。
2. 增加硬度:氧化膜具有较高的硬度,可以有效提高镁合金的抗磨性和耐磨性,延长材料的使用寿命。
3. 提高表面美观度:经过阳极氧化处理的镁合金表面呈现出均匀、光滑的氧化膜,提高了材料的表面美观度,增加了产品的附加值。
4. 增加涂层附着力:阳极氧化处理可以在镁合金表面形成微米级的凹凸结构,增加了涂层与基材之间的附着力,提高了涂层的耐久性。
5. 环保性:阳极氧化过程无需使用有毒物质,不产生废气、废液等污染物,符合环保要求。
镁合金生产工艺

镁合金生产工艺镁合金是一种重量轻、强度高、耐腐蚀性好的材料,被广泛应用在航空航天、汽车制造、电子设备等领域。
下面将介绍镁合金的生产工艺。
镁合金的生产工艺一般可以分为原料准备、合金化、铸造和后处理四个步骤。
首先是原料准备。
镁合金的主要原料是纯镁和其他合金元素。
纯镁是通过电解纯化镁矿石制得的,因此需要采集镁矿石并进行精炼。
其他合金元素可以通过高温放炉和气相沉积等方法得到。
原料准备阶段还包括原料的筛选、研磨和称量等操作。
接下来是合金化。
合金化是指将纯镁和其他合金元素按一定的比例混合,形成镁合金的过程。
合金化可以通过熔炼、球磨和溶剂热等方法进行。
其中,熔炼法是最常用的方法。
熔炼时,将纯镁和其他合金元素放入熔炉中,加热到合金元素的熔点,使其溶解在纯镁中。
然后,通过搅拌等方法使合金元素均匀分布在纯镁中,形成均匀的合金液态。
然后是铸造。
铸造是将合金液态倒入模具中,经冷却和凝固形成固态镁合金的过程。
铸造可以分为压铸、重力铸造、连续铸造等多种方法。
其中,压铸是最常用的方法。
在压铸中,将合金液态注入铸造机中,通过高压和模具形成所需的零件。
铸造过程中,要注意保持适当的温度和压力,以确保合金的完整性和质量。
最后是后处理。
后处理是对铸造后的镁合金进行机械加工和热处理,使其达到所需的物理和机械性能。
后处理可以包括修整铸件表面、去除铸件内部的气孔和夹杂物、调整铸件的尺寸和形状、提高铸件的强度和韧性等操作。
常用的后处理方法有切割、研磨、钻孔、退火等。
后处理过程中,还需要对镁合金进行质量检测,以保证产品的质量和可靠性。
综上所述,镁合金的生产工艺包括原料准备、合金化、铸造和后处理四个步骤。
通过精确的操作和控制,可以得到具有良好物理和机械性能的镁合金产品。
然而,镁合金在生产过程中存在一些困难,如氧化、熔点低、熔池容易发生气孔等。
因此,在生产过程中需要注意各项参数的控制和调整,以获得高质量的镁合金产品。
【冶金原理及工艺】5.4 典型合金的熔炼工艺-镁合金-
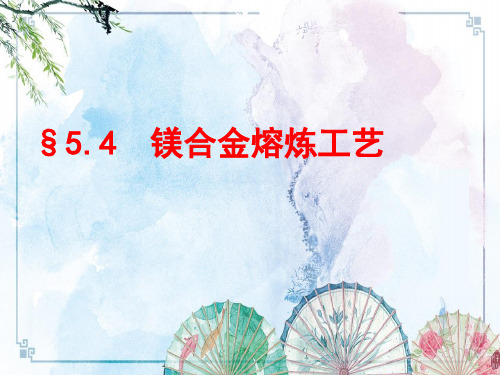
Байду номын сангаас
对于含铝的ZM5镁合金,可采用“过热变质”,即把精炼后的镁液升温 到850~900oC, 保温10~15min,然后迅速冷却到浇注温度进行浇注。经验表 明,“过热变质”的Mg-Al合金中必须含有一定量的铁。其机理可能是随着 温度上升,铁在镁中的溶解量增加,迅速降温时,这些铁就以大量不溶于 镁液的Mg-Al-Fe或Mg-Al-Fe-Mn化合物细小质点的形式析出,成为镁合金 凝固时的结晶核心,使晶粒细化。
由于Mg-H2O反应更为激烈,所以在熔化镁合金时要特别注意采取适当 措施以防止发生事故。除此之外,镁合金的疏松缺陷也与镁液中的氢有关, 主要来源于Mg-H2O反应,所以镁合金熔化工艺中的除气问题日益引起人们 重视。
(3)镁与其他气体间的反应。镁与氮发生反应生成Mg3N2膜,此膜是多孔 的,不能阻止反应继续进行。但Mg-N反应的激烈程度较Mg-H2O及Mg-O反 应小,在较低温度下此反应进行得极慢。
① 镁合金中加锆的主要困难
a. 锆的熔点约为1850oC,相对密度为6.5; 而镁的熔点为651oC,相对密 度为1.74。 所以纯锆加入镁合金液中呈固态,难以溶解。而且由于其相对密 度大,易形成比重偏析。
b. 锆和镁在液态时不能无限溶解,锆在镁中的溶解度仅为0.6%左右。 在镁铝系合金液中,锆的溶解度也小于1%。 由于锆在镁液中溶解度低,故 很难熔制含锆量高且成分又均匀的中间合金。
c. 加锆前应进行适当的精炼。研究表明,MgO会使镁合金液中锆沉淀析 出,增加锆的损耗,因此,在加锆前需用熔剂进行精炼,以清除合金液中 的MgO夹杂物。
镁合金原理
镁合金原理
镁合金是一种轻质、高强度、耐腐蚀的金属材料,具有良好的加工性能和热传
导性能,被广泛应用于航空航天、汽车制造、电子设备等领域。
本文将介绍镁合金的原理及其特性。
首先,镁合金的原理是指镁及其合金在一定条件下的物理和化学性质。
镁是一
种化学性质活泼的金属元素,具有较高的比强度和比刚度,是轻金属中比强度最高的一种。
镁合金的主要合金元素包括铝、锌、锰、铜等,通过合金化可以改善镁合金的强度、耐腐蚀性和加工性能。
其次,镁合金具有许多特性。
首先是轻质高强度,镁合金的密度仅为铝的2/3,但其比强度却高于铝合金。
其次是耐腐蚀性,镁合金具有良好的耐腐蚀性能,能够在大气环境和许多腐蚀介质中保持良好的稳定性。
此外,镁合金还具有良好的加工性能,可以通过压铸、挤压、锻造等方式加工成型,适用于复杂结构的制造。
另外,镁合金还具有良好的热传导性能,能够有效地散热,因此在航空航天和汽车制造领域得到广泛应用。
总的来说,镁合金是一种具有广泛应用前景的金属材料,其原理和特性使其在
航空航天、汽车制造、电子设备等领域具有重要的地位。
随着科学技术的不断进步,镁合金的应用领域将会进一步扩大,为人类社会的发展做出更大的贡献。
镁合金熔炼原理与工艺
镁合金熔炼原理与工艺1. 镁合金熔液与周围介质的作用1.1 镁与氧的作用镁与氧的亲和力要比铝与氧的亲和力大,通常金属与氧的亲和力可由它们的氧化物生成热和分解压来判断。
氧化物的生成热越大,分解压越小,则与氧的亲和力就越强。
镁与1g原子氧相比和时,放出598J的热,而铝放出531J的热。
镁和铝的另一区别是,没被氧化后表面形成疏松的氧化膜,其致密度系数α=0.79(Al2O3的α=1.28),这种不致密的表面膜,不能阻碍反应物质的通过,使氧化得以不断进行,其氧化动力学曲线呈直线式,而不是抛物线式,可见氧化速率与时间无关,氧化过程完全由反应界面所控制。
镁的氧化与温度关系很密切,温度较低时,镁的氧化速率不大;温度高于500℃,氧化速率加快;当温度超过熔点650℃时,其氧化速率急剧增加,一旦遇氧就会发生激烈的氧化而燃烧,放出大量的热。
反应生成的氧化镁绝热性能很好,使反应界面所产生的热不能及时的向外扩散,进而提高了界面上的温度,这样恶性循环必然会加速镁的氧化,燃烧反应更加剧烈。
反应界面的温度越来越高,甚至可达2850℃,远高于镁的沸点(1107℃)引起镁熔液大量气化,甚至导致发生爆炸。
在金属中添加微量的金属铍(w(Be)=0.002%~0.01%),可提高镁熔液的抗氧化性能。
由于铍是镁的表面活性元素,富集于镁熔液表面,致使表面含铍量约为合金中含铍量的10倍,并优先氧化,氧化铍的致密度系数α=1.71,故氧化铍充填于氧化镁膜的孔隙中,形成致密的复合氧化膜。
但铍的加入量不易过多,过多会引起晶粒粗化,降低力学性能,并加大热裂倾向。
当温度高于750℃时,铍对镁的抗氧化作用大为降低。
而镁合金的熔炼温度一般均高于750℃,因此用铍防止镁合金氧化仅是一种辅助措施。
1.1.1 镁与水的作用镁无论是固态还是液态均能与水发生反应,其反应方程式见(1-1)和式(1-2)。
在室温下,反应速度缓慢,随着温度升高,反应速度加快,并且Mg(OH)2会分解为水及MgO,高温时只发生式(1-1)的反应。
镁合金化原理
镁合金化原理1.镁合金的合金化特点Mg 合金的合金化原则与Al 合金大致相同,固溶强化和时效硬化是主要强化手段,只是没有Al 合金那样明显而已。
因此,凡是能在Mg 中大量固溶的元素,都是强化Mg 合金的有效合金元素。
根据合金元素的作用特点和极限溶解度,可大致分成两大类:包晶反应类:Zr(3.8%),Mn(3.4%)。
包晶反应型元素的主要作用是细化晶粒,但也有净化合金(消除杂质Fe),提高抗蚀性和耐热性的作用。
共晶反应类:Ag(15.5%),Al (12.7%),Zn(8.4%),Li(5.7%),Th(4.5%);稀土元素(RE):Y(12.5%),Nd(3.6%),La(1.9%),Ce(0.85%),Pr(0.5%),混合RE(以Ce 或La 为主)。
共晶反应型元素是高强度镁合金的主要合金元素,如Mg-Al-Zn 和Mg-Zn-Zr 系合金等。
这类元素形成的Mg4Al3(Mg17Al12)、MgZn2 和Mg23Th6 等在Mg 中有明显的溶解度变化,是Mg 合金的主要强化相,有明显的时效硬化效应。
稀土元素也多属共晶反应型元素,不仅共晶温度比Mg-Al 和Mg-Zn 系高,Mg-RE 系的α固溶体和稀土化合物(Mg9Nd,Mg9Ce 等)的耐热性也高,原子扩散速度强,有利于抗蠕变性能,故Mg-RE-Zr 和Mg-RE-Mn 系合金是耐热Mg 合金,可在150~250℃工作。
RE 除了提高耐热性外,还能降低液、固二态合金的氧化速度,改善铸造和变形性能。
Nd 的综合作用最佳,能同时提高室温和高温强化效应,Ce 和混合RE 次之,有改善耐热性的作用,但常温强化效果很弱;La 的效果更差,两方面都赶不上Nd 和Ce。
2.镁合金的沉淀过程与结构变化Mg 合金时效硬化效应没有Al 合金明显,与其结构变化特点有关。
Mg-Al 和Mg-Al-Zn 系合金缓冷试样(空冷或油淬)在150~222℃时效,先从晶界或缺陷部位发生不连续沉淀,不经GP 区阶段即直接析出片状平衡相Mg4Al3,沿一定取向往晶粒内部生长。
铸造镁合金熔炼
汽车工业
汽车工业对轻量化材料的需求越来越 大,镁合金作为一种轻质材料,在汽 车领域的应用前景广阔。
THANKS
感谢观看
在加热过程中,应确保炉温均 匀,避免局部过热,以防止镁 合金在熔化前就发生氧化燃烧。
熔化后的镁合金应保持液态稳 定,以便进行后续的精炼和除 气处理。
镁合金的精炼与除气
为了去除镁合金中的杂质和气体,需要 进行精炼和除气处理。常用的精炼剂包
括氯化物、氟化物和氯氟化物等。
在精炼过程中,应控制精炼剂的加入量 和加入速度,以避免产生大量烟雾和溅 出。同时,应保持熔液的搅拌,以便使
熔炼设备的选择与准备
01
02
03
熔炼炉
根据生产需求选择合适的 熔炼炉,如坩埚式、感应 式等,并确保其完好无损。
炉衬材料
选用合适的耐火材料作为 炉衬,以承受高温和化学 侵蚀,延长熔炼炉的使用 寿命。
设备调试
对熔炼设备进行调试,确 保其正常运行,并符合安 全规范。
安全防护措施的准备
安全操作规程
制定并遵守安全操作规程, 确保操作人员熟悉安全操 作要求。
精炼剂充分混合。
除气是精炼过程中的一个重要环节,可 以通过在熔液中通入惰性气体或加入除 气剂来实现。通入惰性气体可以排出熔 液中的气体,而加入除气剂则可以吸附
熔液中的气体。
镁合金的成分调整与细化组织
根据产品要求,可以对镁合金的成分进行调整,如添加合金 元素、调整元素含量等。成分调整可以提高镁合金的力学性 能和耐腐蚀性。
质量检测与控制
外观检测
对铸造完成的镁合金进行外观检查, 确保表面光滑、无缺陷,尺寸符合要 求。
内部检测
通过X射线、超声波等无损检测方法 对镁合金内部进行检测,以确保无气 孔、夹渣等缺陷。
- 1、下载文档前请自行甄别文档内容的完整性,平台不提供额外的编辑、内容补充、找答案等附加服务。
- 2、"仅部分预览"的文档,不可在线预览部分如存在完整性等问题,可反馈申请退款(可完整预览的文档不适用该条件!)。
- 3、如文档侵犯您的权益,请联系客服反馈,我们会尽快为您处理(人工客服工作时间:9:00-18:30)。
镁合金化原理1.镁合金的合金化特点Mg 合金的合金化原则与Al 合金大致相同,固溶强化和时效硬化是主要强化手段,只是没有Al 合金那样明显而已。
因此,凡是能在Mg 中大量固溶的元素,都是强化Mg 合金的有效合金元素。
根据合金元素的作用特点和极限溶解度,可大致分成两大类:包晶反应类:Zr(3.8%),Mn(3.4%)。
包晶反应型元素的主要作用是细化晶粒,但也有净化合金(消除杂质Fe),提高抗蚀性和耐热性的作用。
共晶反应类:Ag(15.5%),Al (12.7%),Zn(8.4%),Li(5.7%),Th(4.5%);稀土元素(RE):Y(12.5%),Nd(3.6%),La(1.9%),Ce(0.85%),Pr(0.5%),混合RE(以Ce 或La 为主)。
共晶反应型元素是高强度镁合金的主要合金元素,如Mg-Al-Zn 和Mg-Zn-Zr 系合金等。
这类元素形成的Mg4Al3(Mg17Al12)、MgZn2 和Mg23Th6 等在Mg 中有明显的溶解度变化,是Mg 合金的主要强化相,有明显的时效硬化效应。
稀土元素也多属共晶反应型元素,不仅共晶温度比Mg-Al 和Mg-Zn 系高,Mg-RE 系的α固溶体和稀土化合物(Mg9Nd,Mg9Ce 等)的耐热性也高,原子扩散速度强,有利于抗蠕变性能,故Mg-RE-Zr 和Mg-RE-Mn 系合金是耐热Mg 合金,可在150~250℃工作。
RE 除了提高耐热性外,还能降低液、固二态合金的氧化速度,改善铸造和变形性能。
Nd 的综合作用最佳,能同时提高室温和高温强化效应,Ce 和混合RE 次之,有改善耐热性的作用,但常温强化效果很弱;La 的效果更差,两方面都赶不上Nd 和Ce。
2.镁合金的沉淀过程与结构变化Mg 合金时效硬化效应没有Al 合金明显,与其结构变化特点有关。
Mg-Al 和Mg-Al-Zn 系合金缓冷试样(空冷或油淬)在150~222℃时效,先从晶界或缺陷部位发生不连续沉淀,不经GP 区阶段即直接析出片状平衡相Mg4Al3,沿一定取向往晶粒内部生长。
此时,沉淀区的基体浓度和晶格常数已达平衡状态,未发生沉淀反应的晶粒内部,晶格常数和浓度保持不变。
这种片层状不连续反应结构又称珠光体型沉淀。
图1-42(a)是Mg-8.5Al-0.5Zn(AZ80)合金急冷铸造组织,出现明显的枝晶偏析和沿晶偏析相Mg4Al3,同图1-42(b)是同一合金的缓冷组织,晶界出现片层状珠光体组织。
这种组织中的Mg4Al3 相弥散度低,片间距大(>200nm),基体浓度低,无共格或半共格应力场,故强化效果低。
当不连续沉淀向晶内发展到一定程度后,晶粒内部才能发生连续分解。
此时,细小的片状Mg4Al3 相一边析出和长大,固溶体浓度和晶格常数也发生连续变化,最终达到与时效温度相适应的平衡状态。
这种沉淀的特点是基体浓度和晶格常数是连续变化的,与不连续沉淀相对应,故称连续沉淀。
这两种合金的显微组织,一般是由连续和不连续反应组织组成,但两类组织所占比例的大小,则由合金的浓度和热处理制度来决定。
合金的过饱和度低,固溶体浓度不均匀(偏析),时效不足或温度低时,不连续沉淀将占优势;反之,Al 浓度高,进行了充分均匀化处理,淬火速度快,时效温度高,连续沉淀则占主要地位。
因为不连续沉淀是由于沉淀相结构与基体相差较大,沉淀应变能过高,只能从晶界开始逐渐向晶内发展;如果时效温度高(Ta≥250℃),原子扩散能力强,不连续沉淀也可能不发生,只出现连续沉淀。
有些Mg 合金的沉淀过程较复杂,结构变化不清楚,在GP 区之后还能出现几个过渡阶段。
Mg-RE(Zn,Zr)和Mg-RE(Zn,Zr)系就是例子,Mg-RE 合金的沉淀过程:α′→GP区→β′′(Mg3Ndx)→β′(Mg3Nd)→β(Mg12Nd)Mg-Th 合金的沉淀过程:α′→β′′(Mg3Th)→β1′(六方),β2′(体心)(Mg2Th)→β(Mg23Th6)其中GP 区和β′′与母相完全共格,β′相部分共格,β相是非共格的平衡相。
这些相中值得注目的是六方沉淀相β′′(Mg3Th、Mg3Nd 或Mg3X 型化合物),具有DO19 型晶体结构,与母相完全共格。
这种过渡相与Al-Cu 合金的θ′′相类似,经常在组元原子尺寸相差较大的合金中出现。
θ′′相对Mg 合金的强化贡献较大,在许多时效温度出现的峰值硬度,就与它的存在有关。
DO19 型结构的a 轴相当于Mg 的二倍,c 轴相等,惯习面为{1010}和方向平行的片状或圆盘状沉淀相。
组成为Mg3X型结构中{1120},是与〈0001〉Mg的{1010}和{1120}面全由Mg 原子组成,说明这些面是低能面,只有次近邻原子键发生改变。
这种结构特点表明Mg3X 相在相当宽的温度范围内较稳定,是提高抗蠕变性能的重要因素。
Mg-RE 系合金工作温度可达250℃,Mg-Th 系合金可达350℃,就是与DO19 型结构Mg3Nd 和Mg3Th 有关。
3.镁合金的晶粒细化镁合金的一个重要缺点是晶粒粗大和分布不均匀,给强度和理性带来极坏的影响(表1-8)。
因此,晶粒细化是Mg 合金化必须考虑的重要问题之一。
Mg-Al 合金晶粒细化的传统方法是对液态合金进行过热处理,将合金过热到850℃左右保温30min,然后快冷到铸造温度浇注。
这种处理最适于砂模铸造,尤其是含Al、Mn 和杂质Fe 的合金细化效果最为明显。
但细化原因还没有一致的看法,Nelson用电子衍射研究Mg-8Al-0.2Mn 合金后指出,过热处理的合金有MnAl4 相(六方晶格)存在,但在715℃以下或1000℃加热的合金,没有这种含Mn 相存在。
据此他认为MnAl4或具有六方晶格的其它高熔点化合物在结晶过程中起晶核作用,是晶粒细比的主要原因。
另一种观点认为液态合金冷却到铸造温度结晶出来的Al4C3 化合物是结晶核心。
现在熔炼含Al 合金常用的挥发性含C 化合物,如甲烷、丙烷、四氯化碳、六氯乙烷或固体炭粉等有明显的细化晶粒作用,就可能是液态合金中的Al 与C 反应生成Al4C3 或AlN•Al4C3 等结晶核心的结果。
过热处理法的缺点是只适用于Mg-Al 系合金,而且必须快速冷却到铸造温度在短时间内即铸造完毕,否则过热处理效果即消失,铸造工艺难于控制。
在德国还发展了另一种处理方法,向液体合金中加入少量无水FeCl3,生成高熔点含Fe 化合物,起结晶核心作用。
这种方法的缺点是FeCl3 易于潮解,还原到Mg 合金中的Fe(0.005%)有损抗蚀性。
加Mn可以消除Fe 的有害影响,但能降低FeCl3 的细化效果。
后来发现Zr 是Mg 合金的有效晶粒细化剂,Zr 在液态Mg 中的溶解度虽不大(645℃,0.58%),但在固态Mg 中却有很高的溶解度(图1-43),加入0.2~0.7%Zr 即能显著细化晶粒,消除铸件的显微缩孔或疏松,改善铸锭质量和塑性加工性能。
此外,Zr还有净化作用,同杂质Fe 形成Zr2Fe3 和ZrFe2 化合物,沉积于坩埚底部,使合金的纯度和抗蚀性提高。
值得说明的是,Zr 必须充分溶解在Mg 液中才有细化晶粒的作用,如图1-43 所示,在理论上溶于Mg 液中的Zr 必须超过0.58%,才能得到预期的效果。
为了保证这一点,在坩埚底部必须保持过剩的Zr,才能保证Mg 液中溶解足够的Zr。
因此在浇注前应避免倒换坩埚,应直接用原坩埚铸造,否则Mg 液中溶解的Zr 量会立即下降。
如果必须倒换坩埚,应向新坩埚中补加Zr,以保证晶粒细化效果。
Zr 的晶粒细化作用可用包晶反应的形核机理来说明。
但应注意同Zr 共存元素的影响,有些元素如Zn、Cd、Ce、Ca、Th、Ag、Cu、Bi、Tl 和Pb 等,能促进Zr 的晶粒细化作用,有的元素如Al、Si、Mn、Ni、Sb、Fe 和H 等,通过降低Zr 在Mg 液中的溶解度,或者形成Zr 化物,而起阻碍作用。
因此,Zr 在Mg-Zn-Zr、Mg-Ce-Zr 和Mg-Th-Zr合金中的晶粒细化作用非常有效,但应限制Mn 含量,也不能用Al 作这类合金的合金元素。
Zr 对Mg 铸件机械性能的影响如表1-9 所示,0.7%Zr 即能显著细化晶粒,能同时提高强度和塑性,效果甚为显著4.镁合金的热加工我们知道,六方结构的Mg 滑移系较少,变形加工度受到极大的限制。
Mg 在室温中的塑性变形,主要靠基面{0001}沿密排方向〈1120〉的滑移和锥面的孪晶运动。
当应力与基面平行时,只有压缩时才能产生孪晶变形,应力与基面垂直时,在拉伸条件下才能产生。
只当温度≥250℃,锥面{1011}也能参加滑移变形,塑性变形更加容易时,孪晶变形才退居次要地位。
因此,Mg 合金的加工制品,一般多利用热变形。
Mg 的塑性低,很难用合金化的方法来改善。
Al、Ag、Zn、Y、Nd、Mn 等虽能在Mg 中大量固溶,但只能增加固溶强化效应,不能改变晶体结构,高低温变形阻力反而增大。
因此,变形用Mg 合金的合金化程度应比铸造合金低,以利于塑性变形。
如用大量(>10%)体心立方晶格的Li 进行合金化,Mg-Li 合金的晶格可由六方转变为体心立方晶格,塑性可以根本改变,但Li 是稀有金属,化学活性高,给Mg 合金的化学稳定性却带来了极坏的影响(抗蚀、抗氧化能力低,SCC 严重)。
Mg 合金一般均在300~500℃进行挤压、轧制和模压加工,由于Mg 合金的上述变形特点,产品质量有下列各种特点:(1)六方结构的Mg 晶体弹性模量(E)各向异性不明显,织构对塑性加工产品的E 值影响不大。
(2)挤压温度较低时,{0001}和{1010}倾向于与挤压方向平行;轧制时基面{0001}倾向于与板面平行,{1010}与轧向一致。
(3)压应力与基面{0001}平行时易生孪晶,所以Mg 合金受压应力时纵向屈服强度比受拉应力时低。
两种屈服强度的比值位于0.5~0.7 之间,所以结构设计(包括抗弯性能设计在内)时要考虑抗压强度的影响。
因此,这个比值是评价Mg 合金质量的一项重要指标,但该值因合金而异,并且随晶粒变细而增大;(4)Mg 合金用卷筒卷取时,能产生交变的拉、压应变,在受压应变时则产生大量孪晶,使抗拉强度明显降低。
生产各种塑性加工和作为抗蠕变(300~350℃)材料用的镁合金产品,其合金化程度一般要比铸造镁合金低,其目的就是要利于塑性变形。
镁合金可进行退火(T2)、时效(T1)、淬火(T4)和人工时效(T6,T61),规范和应用范围与铸造Al 合金基本相同,只是Mg 合金的扩散速度慢,淬火敏感性低,可用静止或流动空气淬火,在个别情况下也用热水淬火(如T61),强度比空冷的T6 高。
值得指以的是,绝大多效Mg 合金对自然时效不敏感,淬火后在室温能长期保持淬火状态,即使人工时效,时效温度也要比Al 合金高(达175~250℃)。