材料加工组织性能控制新
金属材料加工中材料成型与控制工程

金属材料加工中材料成型与控制工程【摘要】本文主要探讨了金属材料加工中材料成型与控制工程的相关内容。
首先介绍了金属材料的选择与预处理,包括原材料的筛选和处理过程。
接着详细讨论了金属材料的成型工艺,包括铸造、锻造、拉伸等工艺技术。
然后介绍了金属材料控制工程技术,包括金属材料加工过程中的控制方法与技术。
并重点探讨了材料性能测试与质量控制,以保证产品的质量和稳定性。
最后讨论了金属材料加工中的环境保护措施,提出了可持续发展的相关建议。
总结了金属材料加工中材料成型与控制工程的重要性,并展望了未来发展趋势。
通过本文的研究,可以更好地了解金属材料加工中的关键技术和发展方向。
【关键词】金属材料、加工、成型、控制工程、选择、预处理、工艺、技术、性能测试、质量控制、环境保护、重要性、未来发展、展望。
1. 引言1.1 金属材料加工中材料成型与控制工程概述金属材料加工中材料成型与控制工程是金属加工领域的重要分支,旨在通过对金属材料的选择、加工工艺和控制技术的研究和应用,实现金属制品的成型和品质控制。
在这个过程中,材料成型工艺和控制工程技术起着至关重要的作用,能够影响金属制品的形状、尺寸和性能特征。
而材料性能测试与质量控制则是保证金属制品质量稳定的关键步骤,能够有效提高金属制品的使用价值和市场竞争力。
金属材料加工中的环境保护措施也是当前社会关注的焦点之一,通过采用环保材料和清洁生产工艺,减少生产对环境的污染,实现可持续发展。
金属材料加工中材料成型与控制工程的重要性不言而喻,其发展与应用将推动金属加工行业的技术进步和产业升级,为经济社会发展做出积极贡献。
未来,随着科学技术的不断进步和市场需求的不断变化,金属材料加工中材料成型与控制工程也将随之发展,不断探索新的成型工艺和控制技术,提高金属制品的质量和效率。
金属材料加工行业将迎来更广阔的发展空间,带动相关产业的快速发展,为实现绿色、智能和可持续的发展目标而努力。
2. 正文2.1 金属材料的选择与预处理金属材料的选择与预处理是金属材料加工中至关重要的一环。
材料智能化制备加工技术概述-北科大研究生课程作业

材料智能化制备加工技术概述材料智能化制备加工技术对很多人来说都是一个全新的概念,从字面意思来看,这是将传统的材料制备加工与人工智能等新技术结合,从而实现制备加工技术的智能化与自动化。
细究其深刻的含义,结合国内外许多相关专家的定义,它是一类先进的材料加工技术,应用人工智能技术、数值模拟仿真技术和信息处理技术,以一体化设计与智能化工艺控制方法,取代传统材料制备与加工过程中的“试错法”(“炒菜法”)设计与工艺控制方法,实现组织性能的精确设计与制备加工过程的精确控制,获得最佳的材料组织性能与成形加工质量。
20世纪后期以来计算机数值模拟、过程仿真技术的迅速发展,对材料制备与成形加工技术的研究和发展起到了重要的促进作用,这些技术使得材料的设计、制备与加工等过程的成本降低。
而人工智能、神经网络技术和材料数据库技术的不断完善,将对提高数值模拟与过程仿真技术的广泛适用性、结果可靠性,实现组织性能的精确预报产生重要影响。
另一方面,各种先进的在线检测、监控技术的发展,是加强对材料制备与成形加工过程质量的控制,提高成品率和生产效率、降低成本的重要保证。
综合利用这些技术的优势,发展智能化制备加工将会是今后材料制备与加工技术中最有发展前景的前沿研究方向,对未来的社会产生巨大的社会价值与经济效益。
首先谈一下对人工智能的认识,它是研究、开发用于模拟、延伸和扩展人的智能的理论、方法、技术及应用系统的一门新的技术科学。
人工智能是计算机科学的一个分支,它企图了解智能的实质,并生产出一种新的能以人类智能相似的方式做出反应的智能机器,该领域的研究包括机器人、语言识别、图像识别、自然语言处理和专家系统等。
著名的美国斯坦福大学人工智能研究中心尼尔逊教授对人工智能下了这样一个定义:“人工智能是关于知识的学科――怎样表示知识以及怎样获得知识并使用知识的科学。
”而另一个美国麻省理工学院的温斯顿教授认为:“人工智能就是研究如何使计算机去做过去只有人才能做的智能工作。
材料加工组织性能控制(第十章)XXXX9
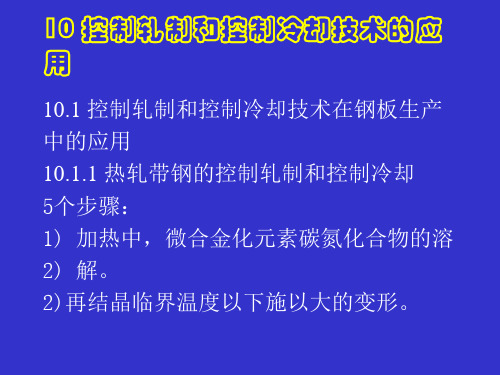
(2) 双机架中厚板轧机的控制轧制工艺 形式:二辊—四辊式,三辊—四辊式、四辊—四 辊式 1) 二辊—四辊式中厚钢板轧机的控制轧制工艺 举例:2800二辊—四辊式:
控制轧制工艺: (a)粗轧终了温度:
道次压下率: 总压下率: (b)四辊精轧机分成两个阶段:部分再结晶的 上限范围轧制,道次压下率:
表10-2 20g锅炉钢板控制轧制和控制冷却工艺 表10-3 16Mng锅炉钢板控制轧制和控制冷却工艺(S含量<0.025%)
(2)压力容器用中厚钢板的控制轧制和控
制冷却
碳素钢容器板和低合金容器板:出炉温度 ≥1150℃;高合金钢容器板的板坯出炉温度为 1200℃。
10.1.3 热轧双相钢的控制轧制和控制冷却 10.1.3.1 双相钢的组织、性能特点、生产方法
(2)特别高的屈服强度的钢(最小屈服强度 值:700MPa,且冷成型性能应非常好 ) 成分:0.08%C,l.3%Mn,0.1%Mo,0.05%Nb、 0.18%Ti和0.002%B 工艺: (1)高温加热;(2)温度较低的粗轧过 程中,碳化钛和碳化铌的变形诱导析出;(3) 终轧温度为850C左右,析出其他的合金碳化 物;(4)高的冷却速度,卷取温度必须显著低 于贝氏体开始温度。 性能:
较低(表 面质量较
差) 小
90-150 平行板型 中,最大5.0 粗轧1-2机架+卷 取精轧4-6机架 与传统工艺相当 与传统工艺相当
中
200-300 平行板型 低,最大2.5 粗轧1-3机架 ,精轧7机架
多 高
大
1)不同工艺与产品厚度关系 2)产品规格的市场需求 3)设备与产品花色的关系 (2)压缩比 (3) 连铸坯的加热 1)隧道式辊底加热炉 加热炉炉子长约150~200m,有缓冲功能。炉内辊 道速度可分段控制,输入端辊道速度最低,以适 应连铸速度较低的特点;中部和末端速度较高, 有利于钢坯快速通过;出炉段辊道速度则与F1速 度相匹配。
第2章 金属材料的组织与性能控制

1. 同素异构转变。 2. 匀晶相图的分析方法。 3. 合金相图与性能的关系。
思考题
1. 为什么要生产合金?与纯金属相比,合金有哪些优越性? 2. 固溶体中,溶质元素含量增加时,其晶体结构和性能会发生什么变化? 3. 试比较共晶反应和共析反应的异同点。 4. 为什么铸造合金常选用接近共晶成分的合金,而压力加工的合金常选用
ES线:C在A中的固溶线
PQ线:C在F中的固溶线
2.铁碳合金的平衡结晶过程
Fe-C 合金分类
工业纯铁 —— C % ≤ 0.0218 %
钢 —— 0.0218 % < C % ≤ 2.11 % 亚共析钢 < 0.77 % 共析钢 = 0.77 % 过共析钢 > 0.77 %
白口铸铁 —— 2.11 % < C % < 6.69 %
室温组织
F + Fe3CⅢ (微量)
500×
(2)共析钢 ( C % = 0.77 % )结晶过程
P中各相的相对量:
Fe3C % = ( 0.77 – xF ) / ( 6.69 – xF )
≈ 0.77 / 6.69 = 12 %
F % ≈ 1 – 12 % = 88 %
珠光体
强度较高,塑性、韧性和硬度介于 Fe3C 和 F 之间。
Ni 80 100
匀晶合金的结晶过程
L
T,C
T,C
L
1500
1455
L
1400 1300
c
a
L+
匀晶转变 L
1200d
1100 1000 1083
b
L
C匀u 晶合金与纯金属不同,它没有一个恒定的N熔i 点,
冷轧板超快速退火的组织织构的柔性化控制技术

冷轧板超迅速退火旳组织、织构旳柔性化控制技术微观组织控制:对老式旳冷轧汽车用钢而言,伴随汽车减重、节省燃油和保障安全旳迫切规定,采用减量化成分和紧凑型流程,在保证成形性能旳基础上深入提高材料强度,已经成为新世纪旳研究热点。
高强度深冲用钢(包括IF钢和Al镇静钢等)大多通过添加Mn、P和Si等元素到达固溶强化旳目旳。
这种钢在固溶强化母相旳同步引起晶界强度旳下降,恶化了固有旳晶界脆性问题(IF钢),导致更明显旳二次加工脆性;此外,固溶强化元素Si等旳添加损害深冲性能和涂层旳表面质量,不合用于复杂成形旳外板零件。
晶粒细化是可以同步提高材料强度和韧性旳最有效措施之一。
通过细化晶粒,提高晶界数量和密度,进而Q345B无缝管 bd提高(超)低碳钢旳晶界强度,同步大幅度改善二次加工脆性。
日本某钢铁企业通过大幅提高C 和Nb旳含量,运用细晶强化、NbC析出强化和PFZ无间隙析出区间技术,开发了一种440MPa级别旳细晶高强IF钢,明显提高了试验钢旳抗二次加工脆性。
实际上,除了微合金化手段以外,通过工艺控制同样可以实现晶粒细化。
近十年来这一技术在热轧领域进行了深入旳研究和应用。
总旳来说,重要有两组获得超细晶钢旳技术路线。
一组是剧烈塑性变形措施,如等通道角挤压、叠轧合技术、多向变形和高压扭转等;另一组则包括多种先进旳形变热处理技术,如形变诱导铁素体相变、动态再结晶、两相区轧制以及铁素体区温轧等。
目前商业用热轧高强钢旳最小晶粒尺寸在3-5μm,而冷轧退火钢一般在20μm左右。
众所周知,热轧组织参数、冷轧规程和退火工艺旳控制可强烈地影响冷轧产品旳组织和性能,但目前主流旳商业化退火措施,无论是老式旳罩式退火还是较先进旳持续退火,工艺参数单一,可变化范围窄,难以实现对组织性能旳柔性化控制。
这正是数年来制约冷轧-退火材料组织细化旳重要瓶颈,也是冷轧细晶化技术鲜有研究旳重要原因。
为了克服上述问题,RAL研究人员发现,超迅速退火技术因其独特旳加热及冷却方式,Q345B无缝管可实现多阶段复杂途径和灵活多样旳工艺参数控制,有望为冷轧-退火产品提供了更具全新旳组织-织构-性能处理方案。
材料的塑性变形机理和性能控制

材料的塑性变形机理和性能控制材料是人类社会发展的重要基石,是各种工业产品的基础。
在大多数制造过程中,材料的塑性变形是不可避免的。
而塑性变形机理和性能控制是材料科学与工程中一个重要的研究领域。
一、塑性变形机理塑性变形是指材料在一定条件下受到外力作用形成塑性变形并保持下去的能力。
材料的塑性变形是由其内部结构的变化而引起的。
塑性变形的主要机理就是晶体内部滑移与游移。
晶体内部的晶格缺陷对塑性变形过程中的原子滑移和游移起着关键作用。
对于晶体而言,其内部结构具有规则的排列方式,称为晶格。
而晶格缺陷包括点缺陷、线缺陷和面缺陷。
在材料中,当受到外力作用时,原子在晶格内的移动会带来晶体内部结构的变化。
这种移动就是原子的滑移和游移。
滑移是指在相邻原子之间形成一些小的位错(错位点),使得晶体原子发生运动。
游移是指在晶体内部的缺陷上发生原子位移。
这两种运动形式是材料塑性变形的主要机理。
除了晶格缺陷,另一个重要的因素是晶界。
晶界是晶体中不同晶粒之间的界面,其存在会影响材料的特性,例如强度和延展能力等。
总之,塑性变形的机理是一个相对复杂的过程,需要深入研究晶格结构和其缺陷的变化情况。
二、性能控制为了实现工业产品的高效、高质量生产,对材料的性能进行有效控制十分关键。
从塑性变形的角度来看,这包括两个方面:强度和延展能力。
强度是材料阻抗外部应力的能力,在材料的塑性变形方面具有重要作用。
材料的强度受多种因素影响,包括晶粒尺寸、晶格结构和组织等等:例如,晶粒尺寸越小,其阻力就越大,从而提高材料强度。
延展能力是材料在承受应变时的变形程度。
合适的延展能力可以使材料更加可塑,适应更多种形状和用途。
在强度和延展能力之间,需要一个权衡。
例如,当强度越高时,延展性可能越差。
此外,还有一些因素可以通过材料加工和热处理进行控制,例如冷变形、淬火和退火等。
冷变形(例如轧制、拉伸和锻造等)可以增加材料的强度和硬度,从而提高其抵抗变形的能力。
淬火可以使材料更加坚硬,其中的快速冷却过程有助于将晶体结构固态化并提高材料机械性能。
热处理工艺的优化方法提高材料性能与可靠性
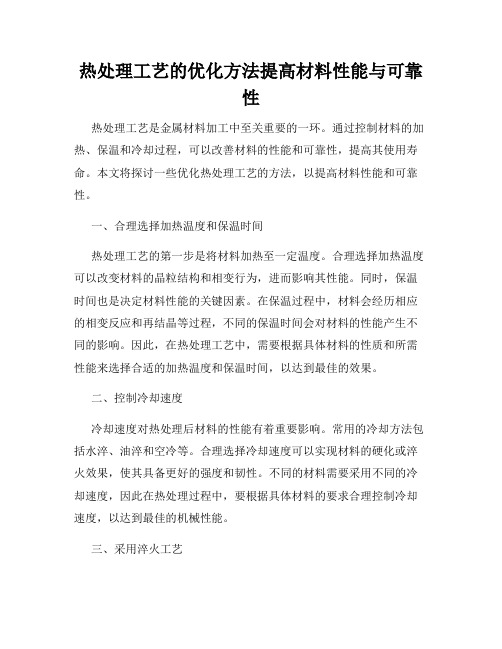
热处理工艺的优化方法提高材料性能与可靠性热处理工艺是金属材料加工中至关重要的一环。
通过控制材料的加热、保温和冷却过程,可以改善材料的性能和可靠性,提高其使用寿命。
本文将探讨一些优化热处理工艺的方法,以提高材料性能和可靠性。
一、合理选择加热温度和保温时间热处理工艺的第一步是将材料加热至一定温度。
合理选择加热温度可以改变材料的晶粒结构和相变行为,进而影响其性能。
同时,保温时间也是决定材料性能的关键因素。
在保温过程中,材料会经历相应的相变反应和再结晶等过程,不同的保温时间会对材料的性能产生不同的影响。
因此,在热处理工艺中,需要根据具体材料的性质和所需性能来选择合适的加热温度和保温时间,以达到最佳的效果。
二、控制冷却速度冷却速度对热处理后材料的性能有着重要影响。
常用的冷却方法包括水淬、油淬和空冷等。
合理选择冷却速度可以实现材料的硬化或淬火效果,使其具备更好的强度和韧性。
不同的材料需要采用不同的冷却速度,因此在热处理过程中,要根据具体材料的要求合理控制冷却速度,以达到最佳的机械性能。
三、采用淬火工艺淬火是一种常见的热处理工艺,通过迅速冷却材料,使其发生相变并形成硬质组织结构,从而提高材料的硬度、强度和耐磨性等性能。
淬火需要根据材料的组织结构和所需性能来选择适当的冷却介质和冷却速度。
同时,为了减少材料的变形和裂纹产生,可以进行应力退火等辅助工艺。
因此,采用合适的淬火工艺可以显著提高材料的性能和可靠性。
四、进行回火处理回火是一种常用的热处理工艺,用于消除淬火过程中产生的内部应力和改善材料的韧性。
回火可以改变材料的晶粒结构和相变行为,使其具有更好的塑性和韧性。
回火过程中,需要控制回火温度和保温时间,以达到所需的性能要求。
回火温度过高或保温时间过长都会影响材料的性能,因此需要进行合理的控制和调节。
五、精细调控工艺参数除了上述的基本热处理工艺,还可以通过精细调控工艺参数来实现材料性能的优化。
例如,可通过改变加热速度、调整保温温度和时间、采用复合工艺等方式来精确控制材料的晶粒尺寸、组织结构和相变行为,从而达到更好的性能及可靠性。
阐述金属材料组织和性能之间的关系
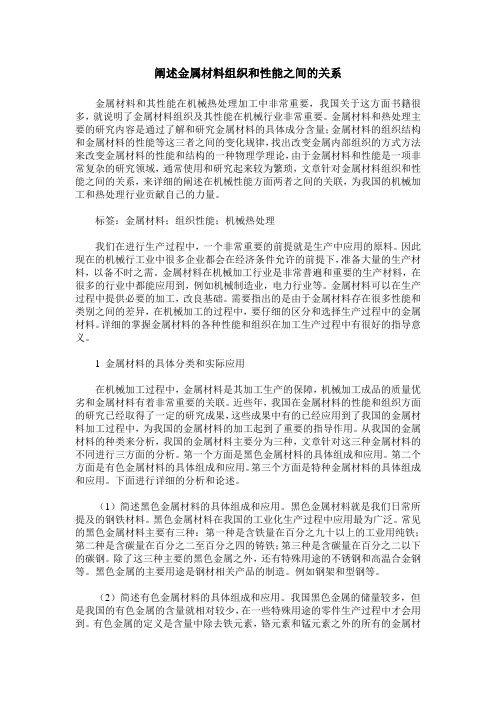
阐述金属材料组织和性能之间的关系金属材料和其性能在机械热处理加工中非常重要,我国关于这方面书籍很多,就说明了金属材料组织及其性能在机械行业非常重要。
金属材料和热处理主要的研究内容是通过了解和研究金属材料的具体成分含量;金属材料的组织结构和金属材料的性能等这三者之间的变化规律,找出改变金属内部组织的方式方法来改变金属材料的性能和结构的一种物理学理论,由于金属材料和性能是一项非常复杂的研究领域,通常使用和研究起来较为繁琐,文章针对金属材料组织和性能之间的关系,来详细的阐述在机械性能方面两者之间的关联,为我国的机械加工和热处理行业贡献自己的力量。
标签:金属材料;组织性能;机械热处理我们在进行生产过程中,一个非常重要的前提就是生产中应用的原料。
因此现在的机械行工业中很多企业都会在经济条件允许的前提下,准备大量的生产材料,以备不时之需。
金属材料在机械加工行业是非常普遍和重要的生产材料,在很多的行业中都能应用到,例如机械制造业,电力行业等。
金属材料可以在生产过程中提供必要的加工,改良基础。
需要指出的是由于金属材料存在很多性能和类别之间的差异,在机械加工的过程中,要仔细的区分和选择生产过程中的金属材料。
详细的掌握金属材料的各种性能和组织在加工生产过程中有很好的指导意义。
1 金属材料的具体分类和实际应用在机械加工过程中,金属材料是其加工生产的保障,机械加工成品的质量优劣和金属材料有着非常重要的关联。
近些年,我国在金属材料的性能和组织方面的研究已经取得了一定的研究成果,这些成果中有的已经应用到了我国的金属材料加工过程中,为我国的金属材料的加工起到了重要的指导作用。
从我国的金属材料的种类来分析,我国的金属材料主要分为三种,文章针对这三种金属材料的不同进行三方面的分析。
第一个方面是黑色金属材料的具体组成和应用。
第二个方面是有色金属材料的具体组成和应用。
第三个方面是特种金属材料的具体组成和应用。
下面进行详细的分析和论述。
- 1、下载文档前请自行甄别文档内容的完整性,平台不提供额外的编辑、内容补充、找答案等附加服务。
- 2、"仅部分预览"的文档,不可在线预览部分如存在完整性等问题,可反馈申请退款(可完整预览的文档不适用该条件!)。
- 3、如文档侵犯您的权益,请联系客服反馈,我们会尽快为您处理(人工客服工作时间:9:00-18:30)。
制工艺
0
5
•常规工艺
•850850
•8
•4042 •4045
•-
•60064
0
PPT文档演模板
材料加工组织性能控制新
• 3.2 钢的奥氏体形变与再结晶(I型控制轧制) • 3.2.1热变形过程中的奥氏体再结晶行为 • 3.2.1.1 动态再结晶
PPT文档演模板
材料加工组织性能控制新
(1)奥氏体再结晶区控制轧制(又称I型控制轧制)
条件:950℃以上 再结晶区域变形。 主要目的:对加热时粗化的初始晶粒轧制再结晶 细化 相变后细小的晶粒。相变前的晶粒越 细,相变后的晶粒也变得越细。
PPT文档演模板
材料加工组织性能控制新
(2)奥氏体未再结晶区控制轧制(又称为Ⅱ型控 制轧制) 条件: 950C~Ar3之间进行变形。 目的:晶粒沿轧制方向伸长,晶粒内部产生形 变带。晶界面积,的形核密度 ,进一步促 进了晶粒的细化。
•(1)细化相变前的奥氏体 晶粒;(2)在细化奥氏体 晶粒的前提下,进一步使奥 氏体处于加工硬化状态; (3)在相变温度区间加速 冷却。
•3.1.2.4 合金元素的作用(微合金元素作用再讲)PPT文档演模板
材料加工组织性能控制新
3.1.3 控制轧制的类型
•控制轧制方式示意图
•(a) 奥氏体再结晶区控轧;(b) 奥氏体未再结晶区控轧;(c) (+)两相区控 轧
Controlled
PPT文档演模板
材料加工组织性能控制新
•低温轧制的 优点:细化 铁素体晶粒。
PPT文档演模板
•图3-l 各种轧制程序的模式图 • CR-—控制轧制;AcC一控制冷却
材料加工组织性能控制新
3.1.2 铁素体晶粒尺寸的控制
3.1.2.1 铁素体晶粒尺寸的计算式
PPT文档演模板
• 奥氏体相变过程示意 图
PPT文档演模板
材料加工组织性能控制新
•控制轧制三阶段示意图和 各阶段的组织变化
•再结晶与未再结晶型控轧示意图
PPT文档演模板
材料加工组织性能控制新
3.1.4 控制轧制工艺特点
•(1)控制加热温度: 加热温度决定轧制前奥氏体晶粒的大 小,温度越低晶粒越细。
•低温加热优点: (1)避 免奥氏体晶粒变粗大。(2) 缩短延迟冷却时间,粗轧 和精轧几乎可连续进行。 •缺点:(1)要减小板坯 的厚度。(2)含铌钢中铌 未固溶,达不到预期的析 出强化效果。
材料加工组织性能控制新
•铁素体晶 粒的形核速 率
•铁素体晶核按抛 物线规律长大的 速度常数
PPT文档演模板
•奥氏体 晶粒直径
材料加工组织性能控制新
3.1.2.2 变形奥氏体对铁素体晶粒的细化作 用
•结论:由加工硬化(变形)奥氏体相变得到的铁素体 晶粒比相同尺寸的未变形奥氏体或再结晶奥氏体相变 后得到的铁素体晶粒要细得多。
•原因:
•(1)变形使奥氏体的晶界上形成了许多台 阶
PPT文档演模板
材料加工组织性能控制新
(2)变形奥氏体除了在晶界上生成铁素体晶核以外,原来 奥氏体中的退火孪晶边界以及由于变形而形成的变形带,也 是铁素体的形核基地。
PPT文档演模板
材料加工组织性能控制新
3.1.2.3 冷却速度对铁素体晶粒尺寸的影响
•II 型控制轧制:要有足够的总变形量,可以不过分强调道 次变形量。原因:
•(+) 两相区轧制:压下率的增加会使位错密度增大,亚晶 发达和产生织构等,使钢材的强度升高,低温韧性得到改善。
PPT文档演模板
材料加工组织性能控制新
•3.1.5 控制轧制的实质
(1)尽可能降低加热温度,目的: (2)在中间温度区通过反复再结晶使奥氏体晶粒 微细化。 (3)加大奥氏体未再结晶区的累积压下量,增加 奥氏体每单位体积的晶粒界面积和变形带面积。
PPT文档演模板
材料加工组织性能控制新
(2)控制轧制温度 奥氏体区轧制:要求最后几道次的轧制温度要低。 原因:
•一般低碳结构钢终轧温度:830 C或者更低些。轧制含 Nb钢:控制在750C左右 。
PPT文档演模板
材料加工组织性能控制新
•(3) 控制变形程度
I型控制轧制原则:1)连续轧制,不要间歇,尤其在的高温 侧(动态再结晶区) ,原因: 2)道次变形量应大于临界变形量,使全部晶粒能进行再结 晶,避免混晶产生。原因:
讲)。
PPT文档演模板
材料加工组织性能控制新
表3-1 36CrSi钢用控轧工艺和用常规工艺后的机械性能
• 机械性 能
•
•b •(N/mm2)
•0.2 •(N/mm2
)
•5 •(%)
• •(%)
•
•HR
•(J/
C
cm2)
•
•加工方式
•高 温 控 制 轧 •1000103 •78583 •1214 •3846 •6075 •31
•
PPT文档演模板
材料加工组织性能控制新
•3.1.6 控制轧制的效应
(1)使钢材的强度和低温韧性有较大幅度的改善。 原理:细化晶粒。常规轧制工艺:铁素体晶粒 7~8级;控制轧制工艺:铁素体晶粒可达12 级,直径可为5m。 (2)可节省能源和使生产工艺简化。 途径: 1)降低钢坯的加热温度;2)取消轧后 的常化处理或淬火回火处理。 (3)可以充分发挥微量合金元素的作用(后面
PPT文档演模板
材料加工组织性能控制新
•图3-3 多道次轧制时轧制温度的影响(实验室数据) •0.18C-1.36Mn钢,各道次压下率20%,9个道次轧制到20mm
• 轧制温度变化范围(开始一结束)为200C
PPT文档演模板
材料加工组织性能控制新
•加热温 度
•终轧温度
•图3-4 轧制温度对铁素体晶粒直径、屈服点及断口转变温度的影响 (0.14C-1.3Mn-0.03Nb系钢)
材料加工组织性能控制 新
PPT文档演模板
2020/11/18
材料加工组织性能控制新
控制轧制(Controlled rolling):热轧过程中通 过
对金属加热制度、变形制度和温度制度的合理控
制,使热塑性变形与固态相变结合,获得细小晶
粒组织,使钢材具有优异的综合力学性能的轧制
新工艺。
TMCP(Thermo Momechanical Processing):
PPT文档演模板
材料加工组织性能控制新
(3) (+)两相区轧制 条件:Ar3点以下轧制。
目的: 1)未相变晶粒更加伸长,在晶内形成形变带,相 变形成微细的多边形晶粒; 2)已相变后的晶粒变形,于晶粒内形成亚结构, 因回复变成内部含有亚晶粒的晶粒。 组织:大倾角晶粒和亚晶粒的混合组织。 影响:强度升高,脆性转变温度(亚晶的出现)。