材料加工组织性能控制第三章XXXX9
材料封样管理制度
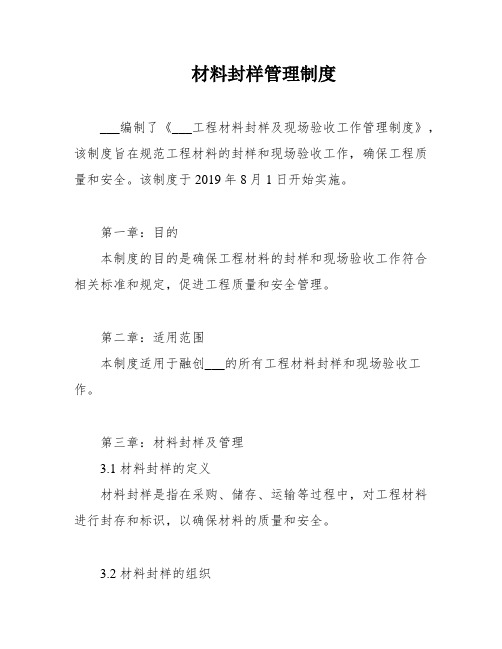
材料封样管理制度___编制了《___工程材料封样及现场验收工作管理制度》,该制度旨在规范工程材料的封样和现场验收工作,确保工程质量和安全。
该制度于2019年8月1日开始实施。
第一章:目的本制度的目的是确保工程材料的封样和现场验收工作符合相关标准和规定,促进工程质量和安全管理。
第二章:适用范围本制度适用于融创___的所有工程材料封样和现场验收工作。
第三章:材料封样及管理3.1 材料封样的定义材料封样是指在采购、储存、运输等过程中,对工程材料进行封存和标识,以确保材料的质量和安全。
3.2 材料封样的组织材料封样应由项目经理或者质量控制员组织,确保封样工作的及时性和准确性。
3.3 直委、比价项目材料的封样对于直委、比价项目的材料,应在收货后立即进行封样,确保材料的质量和安全。
3.4 封样材料的存放和管理封样材料应存放在指定的地点,由专人进行管理,并做好相应的记录和标识。
第四章:管理规定本制度要求所有相关人员必须遵守相关规定和标准,确保工程材料的封样和现场验收工作符合要求。
对于违反规定的行为,将按照公司相关制度进行处理。
以上是《融创重庆公司工程材料封样及现场验收工作管理制度》的内容,希望所有相关人员认真遵守,共同维护工程质量和安全。
本工作指引适用于融创___所有项目的材料设备封样及现场验收工作。
第三章定义1.封样材料:指在材料到场前,由供应商或生产厂家提供的材料样品,用于确认材料的品质和规格。
2.进场材料:指在施工现场到达的材料。
3.甲供材料:指由业主提供的材料。
4.甲控类材料:指对工程质量具有重要影响的材料,如钢筋、混凝土等。
第四章材料设备封样管理4.1 基本管理规定1.供应商或生产厂家应在材料发货前提供封样材料。
2.封样材料应与进场材料一致。
3.封样材料应有标识,标识应包括材料名称、规格、批次号等信息。
4.封样材料应有封存记录,记录应包括封存时间、封存人员等信息。
4.2 惩罚措施1.如发现供应商或生产厂家提供的封样材料与进场材料不一致,应立即通知供应商或生产厂家,并要求其提供正确的封样材料。
材料加工组织性能控制(第五章)
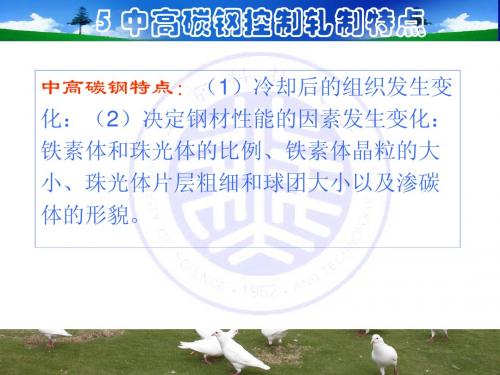
珠光体球直径愈细,断面收缩率愈大,珠光体片层 间距愈小延性愈好。
含碳量和球化处理对u的影响 1-球化处理(粒状渗碳体);2-正 火(片状渗碳体)
碳化物体积和球化处理对的T影响 1-球化处理(粒状渗碳体);2-正火 (片状渗碳体)
3)对韧性的影响: 各强化因素对冲击值转变温度ITT的影响:
珠光体碳分冲淡系数:
图5-2 0.40%C,1.38%Mn,0.023 %Nb钢的晶粒再结晶行为
在中碳钢中添加铌同样可以延迟奥氏体再结晶。
(2)碳对中高碳钢奥氏体再结晶临界变形量的影响 不含铌钢: 加铌钢:随碳含量 临 界压下量。
图5-4 C量对Nb钢与不加Nb钢 临界压下率的影响
碳量的多少决定了Nb的固 溶量,C,Nb的固溶量, 轧制时析出量,阻止再 结晶作用 。
塑性决定于珠光体球团、片层间距两个因素的迭加。
总结: 1)铁素体为主的钢,细化铁素体晶粒来提高强度 和韧性; 2)珠光体为主的钢,控制轧制使强度降低,韧性 提高。对此类钢必须采用再结晶型控轧。 3)对中高碳钢,轧后控制冷却,使珠光体在低温 度下产生,得到细片层珠光体,可提高强度和韧 性。
5 中高碳钢控制轧制特点
中高碳钢特点:(1)冷却后的组织发生变 化:(2)决定钢材性能的因素发生变化: 铁素体和珠光体的比例、铁素体晶粒的大 小、珠光体片层粗细和球团大小以及渗碳 体的形貌。
5.1 中高碳钢奥氏体的再结晶行为
(1) 铌对中高碳钢奥氏体再结晶临界变形量的影响
图5-1 0.43%C,1.4%Mn钢, 晶粒再结晶行为 (1200C加热后 轧制1道次,原始晶粒度为1级)
(2)控制轧制中组织性能的变化 强度变化:
碳量0.2%0.3%: 含0.4%C以上: 含0.8%C以上的钢:
材料加工组织性能控制教学课件

材料的密度、热膨胀系数、热导 率等指标,反映材料的物理属性。
材料的耐腐蚀性、抗氧化性、耐 候性等指标,反映材料在化学环 境中的稳定性。
材料组织性能的影响因素
1 2 3
成分与组织 材料的成分和组织结构对性能有决定性影响,如 钢铁材料中的碳含量和显微组织结构。
工艺与处理 材料的加工工艺和处理条件对组织结构和性能有 重要影响,如铸造、锻造、焊接等工艺。
分类
根据加工方式的不同,材料加工可分 为铸造、锻造、焊接、热处理、表面 处理等。
材料加工的重要性与应用领域
重要性
材料加工是制造业的核心环节,对国民经济的发展和国防建设具有重要意义。
应用领域
材料加工广泛应用于航空航天、汽车、船舶、能源、电子信息等领域。
材料加工技术的发展趋势
智能化
采用智能技术提高材料加工的 自动化和智能化水平,降低人
高强度钢的组织性能控制
要点一
总结词
高强度钢是一种具有高强度和良好塑性的钢材,广泛应用 于汽车、建筑和机械等领域。其组织性能控制对于保证材 料的质量和稳定性至关重要。
要点二
详细描述
高强度钢的组织性能控制主要包括细化晶粒、降低杂质含 量和合金元素调整等手段。通过控制轧制和热处理工艺, 可以获得具有优良综合性能的高强度钢板。同时,高强度 钢的焊接性能也需要通过合理的焊接工艺进行控制,以确 保其在加工和使用过程中的稳定性和可靠性。
04
材料加工组织性能控制技术
计算机模拟与优化技术
计算机模拟技术
通过计算机模拟材料加工过程中的物理、化学和力学行为,预测材料的组织性能,优化 加工工艺参数。
优化算法
应用各种优化算法,如遗传算法、粒子群算法等,寻找最佳的加工工艺参数组合,提高 材料的性能。
材料物理性能课后习题答案_北航出版社_主编
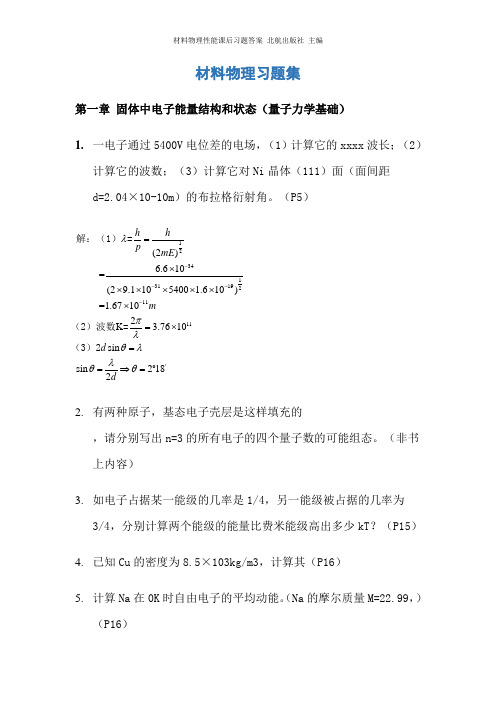
材料物理习题集第一章 固体中电子能量结构和状态(量子力学基础)1. 一电子通过5400V 电位差的电场,(1)计算它的xxxx 波长;(2)计算它的波数;(3)计算它对Ni 晶体(111)面(面间距d=2.04×10-10m )的布拉格衍射角。
(P5)12341311921111o '(2)6.610 =(29.1105400 1.610) =1.67102K 3.7610sin sin 2182h h p mE m d d λπλθλλθθ----=⨯⨯⨯⨯⨯⨯⨯=⨯==⇒=解:(1)=(2)波数=(3)2 2. 有两种原子,基态电子壳层是这样填充的,请分别写出n=3的所有电子的四个量子数的可能组态。
(非书上内容)3. 如电子占据某一能级的几率是1/4,另一能级被占据的几率为3/4,分别计算两个能级的能量比费米能级高出多少kT ?(P15)4. 已知Cu 的密度为8.5×103kg/m3,计算其(P16)5. 计算Na 在0K 时自由电子的平均动能。
(Na 的摩尔质量M=22.99,)(P16)6. 若自由电子矢量K 满足以为晶格周期性边界条件和定态xx 方程。
试证明下式成立:eiKL=17.d h r K K cos r /2θϕ=*hkl *hkl 已知晶面间距为,晶面指数为( k l )的平行晶面的倒易矢量为,一电子波与该晶面系成角入射,试证明产生布拉格反射的临界波矢量的轨迹满足方程。
8. 试用布拉格反射定律说明晶体电子能谱中禁带产生的原因。
(P20)9. 试用晶体能带理论说明元素的导体、半导体、绝缘体的导电性质。
答: (画出典型的能带结构图,然后分别说明)10. 过渡族金属物理性质的特殊性与电子能带结构有何联系?(P28)答:过渡族金属的d 带不满,且能级低而密,可xx 较多的电子,夺取较高的s 带中的电子,降低费米能级。
补充习题1. 为什么镜子颠倒了左右而没有颠倒上下?2.只考虑xx 力学,试计算在不损害人体安全的情况下,加速到光速需要多少时间? 3. 已知下列条件,试计算空间两个电子的电斥力和万有引力的比值4. 画出原子间引力、斥力、能量随原子间距变化的关系图。
材料加工组织性能控制新
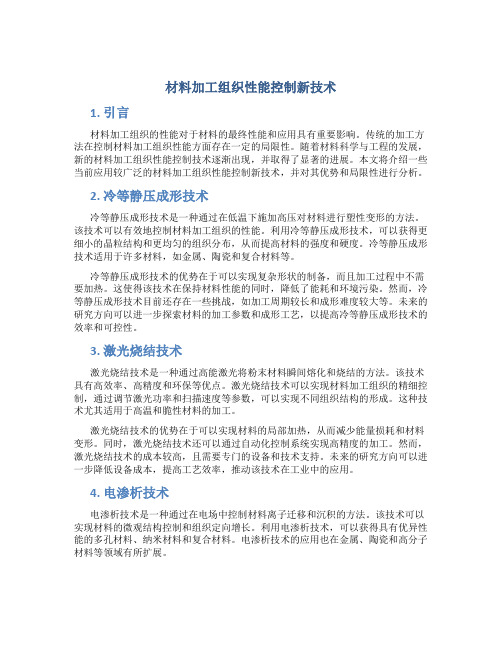
材料加工组织性能控制新技术1. 引言材料加工组织的性能对于材料的最终性能和应用具有重要影响。
传统的加工方法在控制材料加工组织性能方面存在一定的局限性。
随着材料科学与工程的发展,新的材料加工组织性能控制技术逐渐出现,并取得了显著的进展。
本文将介绍一些当前应用较广泛的材料加工组织性能控制新技术,并对其优势和局限性进行分析。
2. 冷等静压成形技术冷等静压成形技术是一种通过在低温下施加高压对材料进行塑性变形的方法。
该技术可以有效地控制材料加工组织的性能。
利用冷等静压成形技术,可以获得更细小的晶粒结构和更均匀的组织分布,从而提高材料的强度和硬度。
冷等静压成形技术适用于许多材料,如金属、陶瓷和复合材料等。
冷等静压成形技术的优势在于可以实现复杂形状的制备,而且加工过程中不需要加热。
这使得该技术在保持材料性能的同时,降低了能耗和环境污染。
然而,冷等静压成形技术目前还存在一些挑战,如加工周期较长和成形难度较大等。
未来的研究方向可以进一步探索材料的加工参数和成形工艺,以提高冷等静压成形技术的效率和可控性。
3. 激光烧结技术激光烧结技术是一种通过高能激光将粉末材料瞬间熔化和烧结的方法。
该技术具有高效率、高精度和环保等优点。
激光烧结技术可以实现材料加工组织的精细控制,通过调节激光功率和扫描速度等参数,可以实现不同组织结构的形成。
这种技术尤其适用于高温和脆性材料的加工。
激光烧结技术的优势在于可以实现材料的局部加热,从而减少能量损耗和材料变形。
同时,激光烧结技术还可以通过自动化控制系统实现高精度的加工。
然而,激光烧结技术的成本较高,且需要专门的设备和技术支持。
未来的研究方向可以进一步降低设备成本,提高工艺效率,推动该技术在工业中的应用。
4. 电渗析技术电渗析技术是一种通过在电场中控制材料离子迁移和沉积的方法。
该技术可以实现材料的微观结构控制和组织定向增长。
利用电渗析技术,可以获得具有优异性能的多孔材料、纳米材料和复合材料。
材料加工组织性能控制(第五、六章)XXXX9

图5-15 在普碳钢和含铌钢中,单道次 的变形量和变形温度对再结晶奥氏体 晶粒尺寸的影响
总结:
铌在奥氏体中存在形式:1)加热时尚未溶到奥氏 体中的Nb(C、N);2)固溶到奥氏中的铌;3)加热 时溶解、轧制过程中又由奥氏体中重新析出的 Nb(C、N)。轧制的不同阶段,其阻止奥氏体再结 晶是不同的。
图5-2 晶粒尺寸与加热温度的关系
5.2 控制轧制过程中微量元素碳氮化合物 的析出 5.2.1 各阶段中Nb(C、N)的析出状态 (1)出炉前: 加热到1200C,均热2h:90%以上铌都 固溶到奥氏体基体中,有极少数粗大 Nb(C、N)没有固溶到奥氏体中。 1260C :保温30min,Nb(C、N)全部溶 解。
(4) 奥氏体向铁素体转变过程中和在铁素体内 Nb(C、N)的析出状态 1)碳氮化物在和中的溶解度不同相变后,产 生快速析出。 相间析出(相间沉淀): 冷却速度大、析出温度低相间沉淀排间距小 析出质点也小。 析出时间长质点长大。 2)相变后内剩余的固溶铌继续析出,质点大小 决定于冷却速度。 3)冷却到室温,1015%左右的铌未从铁素体中 析出。
r:厚向异性系数
r w t
r (r0 2r45 r90 ) / 4
r:厚向异性系数r在板面上随方向的变化,决定凸 耳的形成程度,不影响板料成形性能。
r r0 r90 2r45 2
图6.4冷轧压下率对铝镇静钢薄板 织构和各向异性值的影响
r-平面各向异性;rm-平均法 向各向异性
图6.5冷轧压下率对软钢薄板法向 各向异性(rm)的影响(高温卷取)
图6.11.1 IF钢再结晶退火后的硬度变化规律 a- 加热温度与硬度(保温2h);b-保温时间与硬度
T1-Ti-IF钢;N1-Ti+Nb-IF钢
材料加工组织性能控制新
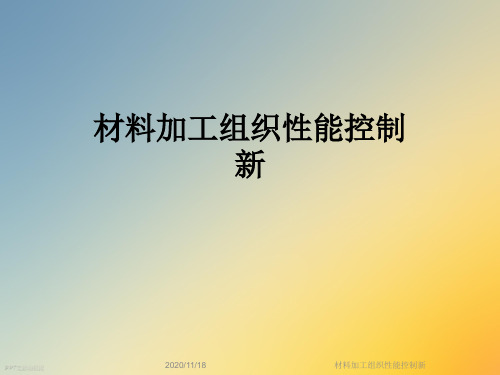
制工艺
0
5
•常规工艺
•850850
•8
•4042 •4045
•-
•60064
0
PPT文档演模板
材料加工组织性能控制新
• 3.2 钢的奥氏体形变与再结晶(I型控制轧制) • 3.2.1热变形过程中的奥氏体再结晶行为 • 3.2.1.1 动态再结晶
PPT文档演模板
材料加工组织性能控制新
(1)奥氏体再结晶区控制轧制(又称I型控制轧制)
条件:950℃以上 再结晶区域变形。 主要目的:对加热时粗化的初始晶粒轧制再结晶 细化 相变后细小的晶粒。相变前的晶粒越 细,相变后的晶粒也变得越细。
PPT文档演模板
材料加工组织性能控制新
(2)奥氏体未再结晶区控制轧制(又称为Ⅱ型控 制轧制) 条件: 950C~Ar3之间进行变形。 目的:晶粒沿轧制方向伸长,晶粒内部产生形 变带。晶界面积,的形核密度 ,进一步促 进了晶粒的细化。
•(1)细化相变前的奥氏体 晶粒;(2)在细化奥氏体 晶粒的前提下,进一步使奥 氏体处于加工硬化状态; (3)在相变温度区间加速 冷却。
•3.1.2.4 合金元素的作用(微合金元素作用再讲)PPT文档演模板
材料加工组织性能控制新
3.1.3 控制轧制的类型
•控制轧制方式示意图
•(a) 奥氏体再结晶区控轧;(b) 奥氏体未再结晶区控轧;(c) (+)两相区控 轧
Controlled
PPT文档演模板
材料加工组织性能控制新
•低温轧制的 优点:细化 铁素体晶粒。
PPT文档演模板
•图3-l 各种轧制程序的模式图 • CR-—控制轧制;AcC一控制冷却
材料加工组织性能控制新
3.1.2 铁素体晶粒尺寸的控制
材料加工组织性能控制XXXX(第十章)
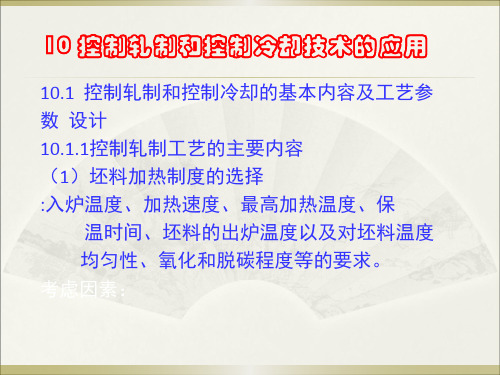
终轧温度:
(2) 双机架中厚板轧机的控制轧制工艺 形式:二辊—四辊式,三辊—四辊式、四辊—四 辊式
举例:2800二辊—四辊式:
控制轧制工艺: (a)粗轧终了温度:
道次压下率: 总压下率: (b)四辊精轧机分成两个阶段:部分再结晶的 上限范围轧制,道次压下率:
轧制温度: 未再结晶区轧制,道次压下率:
10 控制轧制和控制冷却技术的应用
10.1 控制轧制和控制冷却的基本内容及工艺参 数 设计 10.1.1控制轧制工艺的主要内容 (1)坯料加热制度的选择 :入炉温度、加热速度、最高加热温度、保
温时间、坯料的出炉温度以及对坯料温度 均匀性、氧化和脱碳程度等的要求。 考虑因素:
(2)选择和设计控制轧制工艺的类型
(4)控轧控冷钢化学成分的调整
碳: 锰 :细化晶粒、提高强度、增加韧性、降低相变 温度Ar3 ,作用:1)扩大了加工温度范围 ;2) 使铁素体晶粒长大机会减少。 一般控制在1.3-1.5%之间 。 硫: 磷 :不大于0.02% 。
10.1.2 控制冷却工艺设计(已讲过,略) 10.2控制轧制和控制冷却技术在钢板生产中的应用 10.2.1 热轧带钢的控制轧制和控制冷却 ➢ 5个步骤: 1)加热中,微合金化元素碳氮化合物的溶解。 2)再结晶临界温度以下施以大的变形。 3) 微合金化元素碳氮化合物的变形诱导析出延缓再结 晶。 4)未再结晶并强烈变形的奥氏体发生相变。 5)分配冷却剂量来控制冷却和调整所需要的卷取温度。
图10-16 终轧温度和卷取温度对双相钢性能的影响
2) 卷取温度对双相钢性能的影响
图10-16 终轧温度和卷取温度对双相钢性能的影响
10.3 连铸连轧理论与应用 10.3.1 五种典型工艺图
- 1、下载文档前请自行甄别文档内容的完整性,平台不提供额外的编辑、内容补充、找答案等附加服务。
- 2、"仅部分预览"的文档,不可在线预览部分如存在完整性等问题,可反馈申请退款(可完整预览的文档不适用该条件!)。
- 3、如文档侵犯您的权益,请联系客服反馈,我们会尽快为您处理(人工客服工作时间:9:00-18:30)。
序最佳化,通过反复再结晶使奥氏体晶粒微细 化。
(3)加大奥氏体未再结晶区的累积压下量,增加 奥氏体每单位体积的晶粒界面积和变形带面积。
控制轧制机理:
(1)Hall-Petch关系式:
y
0
k
y
d
1 2
(1)
(2)断口转变温度FATT(Fracture Appearance Transition Temperature) :
3.热形变过程中组织的变化
3.1 控制轧制概念 控制轧制(Controlled rolling):热轧过程中通过
对金属加热制度、变形制度和温度制度的合理控 制,使热塑性变形与固态相变结合,获得细小晶 粒组织,使钢材具有优异的综合力学性能的轧制 新工艺。 TMCP(Thermo Momechanical Controlled Processing):
3.3 控制轧制的效应 (1)使钢材的强度和低温韧性有较大幅度的改善。 原理:细化晶粒。常规轧制工艺:铁素体晶粒 7~8级;控制轧制工艺:铁素体晶粒可达12级, 直径可为5m。 (2)可节省能源和使生产工艺简化 途径:降低钢坯的加热温度;取消轧后的常化处 理或淬火回火处理。
表3-1 36CrSi钢用控轧工艺和用常规工艺后的机械性能
(2)控制轧制温度 奥氏体区轧制:要求最后几道次的轧制温度要 低。一般要求终轧温度尽可能接近奥氏体开始转 变温度,起到相似于正火的作用。 低碳结构钢的终轧温度: 含Nb钢的终轧温度:
采用(+)两相区轧制:要根据对钢材性能的不同 要求而确定其终轧温度。
(3) 控制变形程度 :
奥氏体区轧制 原则:1)连续轧制,不要间歇,尤 其在的高温侧(动态再结晶区),使晶粒来不及长 大; 2)道次变形量应大于临界变形量,使全部晶 粒能进行再结晶。混晶现象:
图3-l 各种轧制程序的模式图 CR-—控制轧制;AcC一控制冷却
轧制三个阶 段:
控冷作用:
图3-2 控制轧制和控制冷却奥氏体和铁素体的组织变化模式图
(轧制温度向右边降低。上层的组织表示轧制带来的奥氏体组织的变化,下 层表示奥氏体开始相变后不久的组织,特别是下层表示铁素体核的生成地 点)
控制轧制的实质: (1)尽可能降低加热温度,将开始轧制前的奥氏
机械性能
b
0.2
5
(N/mm2) (N/mm2)
(%)
HRC
(%)
(J/
cm2)
加工方式
高温控制轧制 10001030 785835 1214 3846 6075
31
工艺
常规工艺
850850 600640
8
4042 4045
-
(3)可以充分发挥微量合金元素的作用 常规轧制,加入Nb、V: 控制轧制,加入Nb、V: 采用控制轧制工艺时要考虑到轧机的
控制轧制三阶段示意图和各阶段的组织变化
3.2 控制轧制工艺特点 (1)控制加热温度 加热温度决定轧制前奥氏体晶粒 的大小,温度越低晶粒越细。
图3-5 含微量添加元素的奥氏体晶粒成长 情况
低温加热优点: (1) 避免奥氏体晶粒变粗 大。(2)缩短延迟冷 却时间,粗轧和精轧 几乎可连续进行。 缺点:(1)要减小板 坯的厚度。(2)含铌 钢中铌未固溶,达不 到预期的析出强化效 果。
设备条件。
3.4钢的奥氏体形变与再结晶 3.4.1热变形过程中的奥氏体再结晶行为 3.4.1.1 动态再结晶 冷加工:
高温变形: 真应力-应变曲线由三阶
段组成:
A
第一阶段:加工硬化及软
B
C
化共存,但硬化程度超过
பைடு நூலகம்软化程度;
第二阶段:发生动态再结
O
晶。
动态再结晶临界量c :
曲线的最大应力值p(或s)、 、T之间可用
(2)奥氏体未再结晶区控制轧制(又称为Ⅱ型控 制轧制) 条件: 950C~Ar3之间进行变形。 目的:晶粒沿轧制方向伸长,晶粒内部产生形 变带。晶界面积,的形核密度 ,进一步促 进了晶粒的细化。
(3) (+)两相区轧制 条件:Ar3点以下轧制。 目的:未相变晶粒更加伸长,在晶内形成形变 带,相变形成微细的多边形晶粒;已相变后的 晶粒变形,于晶粒内形成亚结构,因回复变成内 部含有亚晶粒的晶粒。 组织:大倾角晶粒和亚晶粒的混合组织。 强度升高,脆性转变温度(亚晶的出现)。
FATT
A
Bd
1 2
(2)
图3-3 多道次轧制时轧制温度的影响(实验室数据) 0.18C-1.36Mn钢,各道次压下率20%,9个道次轧制到20mm
轧制温度变化范围(开始一结束)为200C
图3-4 轧制温度对铁素体结晶粒直径和屈服点 断口转变温度的影响
实验室数据:0.14C-1.3Mn-0.03Nb系钢,RT 为加热温度,FT为终轧温度
轮再结晶所需的变形量)。 2)间断动态再结晶
条件:c>r
图3-3 Q235钢变形条件对真应力-真应变曲线的影响 (a)变形温度的影响,变形速度 0.1s1;(b)变形速度的 影响,变形温度T=1000C
3.4.1.2 动态再结晶的控制 (1)动态再结晶发生条件
1)轧制不含Nb的普通钢 : 2)轧制含Nb钢 :
(+) 两相区轧制:压下率的增加会使位错密度增 大,亚晶发达和产生织构等,结果可使钢材的强度 升高,低温韧性得到改善。
(4)控制轧后冷却速度 钢材于轧后冷却除采用空冷外,还可以采用吹 风,喷水,穿水等冷却方式。由于冷却速度的不 同,钢材可以得到不同的组织和性能。
控制轧制的类型:
控制轧制方式示意图
(a) 奥氏体再结晶区控轧;(b) 奥氏体未再结晶区控轧;(c) (+)两相 区控轧
(1)奥氏体再结晶区控制轧制(又称I型控制轧 制)
条件:950℃以上 再结晶区域变形。
主要目的:对加热时粗化的初始晶粒轧制再 结晶反复进行细化 相变后细小的晶粒。 相变前的晶粒越细,相变后的晶粒也变得越 细。
Zener-Hollomon因子Z表示:
Z exp(Q / RT ) A n
式中 Z :温度补偿变形速率因子;A: 常数;n:应
力指数;Q:变形活化能;R:气体常数;T:绝对 温度。
为什么金属的变形应力高于原始状态(即退火状态)的 变形应力?
A
B
C
O
第三阶段,两种情况:
1)连续动态再结晶 条件:c<r (r :由动态再结晶产生核心到全部完成一