材料加工组织性能控制(第五章)
大连理工大学 材料科学基础 第五章 回复与再结晶

粒长大后趋于缓慢。
8
B:电阻率resistivity:其大小与点阵 中的点缺陷密切相关,随温度升高, 空位浓度下降,故电阻率呈现连续 下降趋势。
C:内应力inner stress:回复之后, 宏观内应力基本消除,微观内应力 部分消除;再结晶后,冷变形造成 的内应力全部消除。
D:密度density:密度在再结晶阶段急剧增加,主要是 由于此时位错密度显著降低造成的。
4th
冷加工变形:加工硬化,可使位错数量增加, 金属的强度和硬度增加
冷加工缺点:内应力,这种残余应力在金属零 件进一步加工和使用过程中往往会产生不应有的变 形,使用中也会由于大气环境与内应力的共同作用, 造成零件的应力腐蚀;冷加工也可能使电阻率增加 等。这时金属处于一种不稳定状态。
1
体发
不生
应
锈应
• 再结晶不是一个恒温过程,它是自某一温度开始, 在一个温度范围内连续进行的过程,发生再结晶 的最低温度称再结晶温度。
31
影响再结晶温度的因素:
• 1、金属的预先变形度:金属预先变形程度越大, 再结晶温度 越低。当变形度达到一定值后,再结晶温度趋于某一最低值, 称最低再结晶温度。
• 纯金属的最低再结晶温度与其熔点之 间的近似关系: T再≈(0.35-0.4)T熔, 其 中T再、T熔为绝对温度K.
R m r m 0
R — 屈服强度回复率
m — 变形后屈服强度 r — 回复后屈服强度 0 — 原始态的屈服强度
1.0
同一变形度的Fe在不同温度下的回复
0.8
300oC
350oC
0.6
400oC
0.4
450oC
0.2
500oC
0 100 200 300 400
第五章 金属基复合材料成型技术

• 5.1概述 • 金属基复合材料制造技术是影响金属基复合 材料迅速发展和广泛应用的关键问题。金属基复 合材料的性能、应用、成本等在很大程度上取决 于其制造方法和工艺。然而,金属基复合材料的 制造相对其他基复合材料还是比较复杂和困难。 这是由于金属熔点较高,需要在高温下操作;同 时不少金属对增强体表面润湿性很差,甚至不润 湿,加上金属在高温下很活泼,易与多种增强体 发生反应。目前虽然已经研制出不少制造方法和 工艺,但仍存在一系列问题。所以开发有效的制 造方法一直是金属基复合材料研究中最重要的课 题之一。
PVD法纤维/基体复合丝原理图
5.3.5共喷沉积技术
• 共喷沉积法是制造各种颗粒增强金属基复合材料 的有效方法,1969年由A.R.E.siager发明, 随后由Ospmy金属有限公司发展成工业生产规模 的制造技术,现可以用来制造铝、铜、镍、铁、 金属间化合物基复合材料。 • 共喷沉积工艺过程,包括基体金属熔化、液态金 属雾化、颗粒加入及与金属雾化流的混合、沉积 和凝固等工序。主要工艺参数有:熔融金属温度, 惰性气体压力、流量、速度,颗粒加入速度,沉 积底板温度等。这些参数都对复合材料的质量有 重要的影响。不同的金属基复合材料有各自的最 佳工艺参数组合,必须十分严格地加以控制。
压铸工艺中,影响金属基复合材料性能的工艺因素主要有四个: ①熔融金属的温度 ②模具预热温度 ③使用的最大压力 ④加压速度 在采用预制增强材料块时,为了获得无孔隙的复合材料,一般压力不低于 50MPa,加压速度以使预制件不变形为宜,一般为1~3cm/s。对于铝基复合材 料,熔融金属温度一般为700~800℃,预制件和模具预热温度一般可控制在 500~800℃,并可相互补偿,如前者高些,后者可以低些,反之亦然。采用压 铸法生产的铝基复合材料的零部件,其组织细化、无气孔,可以获得比一般金 属模铸件性能优良的压铸件。与其他金属基复合材料制备方法相比,压铸工艺 设备简单,成本低,材料的质量高且稳定,易于工业化生产。
材料加工工艺习题【考研】【复习】

《材料加工工艺》考研习题第一章绪论第二章液态金属成形1.金属及合金的结晶包括哪两个基本过程?什么是均质形核和非均质形核?在实际铸造生产中铸造合金结晶的形核是以哪种形核为主,为什么?2.什么是液态金属的充型性能,它与哪些因素有关?铸造合金流动性的好与差对铸件质量有何影响?影响铸造合金流动性的主要因素有哪些?生产中如何采取措施提高铸造合金的流动性?3.铸造合金由液态冷却到室温时要经过哪三个收缩阶段?收缩对铸件质量有什么影响?其收缩大小与哪些因素有关?4.缩孔、缩松是铸件中的常见缺陷之一,哪些因素影响其形成?生产中如何采取措施进行防止?5.什么是铸造应力?铸造应力大小对铸件质量有什么影响?热应力是如何形成的?哪些因素影响其大小?生产中常采取哪些措施来防止和减小应力对铸件的危害?6.铸造合金中的气体主要来源于哪些方面?又以哪些形式存在于铸造合金中?对铸件质量有什么影响?7.铸造合金中的夹杂物是如何分类的?对铸件质有什么影响?如何防止和减小其对铸件的危害?8.湿型粘土砂的主要成分是什么?它有哪些优缺点?适合生产哪些铸件?9.湿型粘土砂的造型方法有哪些?试比较应用震击、压实、射压、高压、气冲和静压等各种造型方法的紧实的砂型紧实度分布(沿砂箱高度方向)。
为什么需要用高密度湿粘土砂型生产铸件?10.树脂自硬砂、水玻璃砂与粘土砂比较有哪些优点?各适用于哪些铸件的生产?11.砂芯的作用是什么?经常使用哪些粘结剂来制芯?常用的制芯工艺有哪些?12.砂型和砂芯涂料的作用是什么?其主要组成有哪些?13.什么是顺序凝固原则?什么是同时凝固原则?各需采用什么措施来实现?上述两种凝固原则各适用于哪些场合?14.铸件的壁厚为什么不能太薄,也不能太厚,而且应尽可能厚薄均匀?为什么要规定铸件的最小壁厚?不同铸造合金要求一样吗?为什么?。
15.为便于生产和保证铸件质量,通常对铸件结构有哪些要求?16.何谓铸件的浇注位置?它是否指铸件上的内绕道位置?铸件的浇注位置对铸件的质量有什么影响?应按何原则来选择?17.试述分型面与分模面的概念?分模造型时,其分型面是否就是其分模面?从保证质量与简化操作两方面考虑,确定分型面的主要原则有哪些?18.试确定图2-116所示铸件的浇注位置及分型面。
材料合成与制备 第5章 定向凝固技术

4、磁性材料
稀土超磁致伸缩材料RFe(R-Tb、Dy)作为一种电-磁-机械能量或信 息转换的新型功能材料,从20世纪70年代以来得到了迅速发展,它具有 很高的磁致伸缩值(1500~2000×10 )和能量密度(14000~25000J/m ),而 且还具有低频响应速度快、机电耦舍系数大等特点,故在大功率声纳换 能器、磁弹性波器件、液压阀门控制、精密加工徽定位、精度高速线性 马达、伺服系统和特殊兵器等高新技术领域展示出广阔的应用前景。对 于Tb-Dy-Fe材料,人们一直希望得到具有<111>方向择优取向的样品。 通过改变材料的定向凝固条件、控制材料的取向度、以及对材料进行热 处理消除晶界提高材料磁致伸缩性能。
(4)激光超高温梯度快速凝固
利用激光器作为热源来实现定向凝固。 激光具有能量高度集中的特性,在作为定向凝固热源时可能获得 比现有定向凝固方法高得多的温度梯度。利用激光表面熔凝技术实现 超高温度梯度快速定向凝固的关键在于:在激光熔池内获得与激光扫 描方向一致的温度梯度;根据合金凝固特性选择适当的工艺参数以获 得胞晶组织。
定向凝固过程工艺参数分别为: 合金熔融温度1450℃,温度梯度140℃/cm,牵引速度0.5-0.8 mm/min。
2、柱状晶生长
控制热流方向和温度梯度。
3、高温合金制备
定向凝固制备Fe-Cr-C过共晶原位生长复合材料
高铬铸铁是一种优良的耐磨材料,普通条件下凝固的高铬铸铁碳 化物呈网状,在实际磨损中往往会因为碳化物脆裂或折断而失效。 为此,通过定向凝固的方法,使碳化物纤维定向排列,即将Fe-C-Cr 合金制备成碳化物呈定向分布的原位生长复合材料,使高硬度的碳 化物垂直于磨面的方向定向生长,可以显著提高其性能。
1第五章 材料加工力学基础--简_430108089

2015年春季
2015/5/17
材料加工原理
1
题外话
• 2011年诺贝尔化学奖获奖项目是什么? • 什么是准晶?晶体?非晶体?Amorphous A h state t t
– 晶体:三维周期性有序重复的原子排列,出现1、2、3、4、6次 旋转对称性,不可能出现5次及6次以上的旋转对称性。 – 非晶体:近程有序、无长程序对称性。分玻璃和其他非晶态 – 准晶:具有长程准周期性平移序和非晶体学旋转对称的固态有序 相
2015/5/17
材料加工原理
20
平板对接产生的焊接变形
2015/5/17
材料加工原理
21
金属塑性成形的物理基础
• • • • • • • 金属塑性成形的特点 塑性成形工艺的分类 塑性加工时变形的分类 塑性加工时的附加应力和残余应力 金属的塑性和变形抗力 变形体的模型 塑性变形机制、加工硬化、回复、再结晶、摩擦 和润滑
2015/5/17 材料加工原理
27
变形体的模型 (应力-应变曲线的简化形式)
• • • • • 理想弹塑性模型 弹塑性线性强化模型 幂强化模型 理想刚塑性模型 刚塑性线性强化模型
2015/5/17
材料加工原理
28
塑性变形机制、加工硬化
• 塑性变形机制:单晶体、多晶体 – 单晶体塑性变形的主要机制是滑移和孪生。 单晶体塑性变形的主要机制是滑移和孪生 – 多晶体的塑性变形包括晶内变形和晶间变形两 种方式。除了滑移和孪生外,还有晶界滑动和 除 孪生 有 迁移,以及点缺陷的定向扩散(扩散蠕变)。 • 加工硬化 – 塑性变形造成组织上的变化,组织变化产生性 能上的变化:屈服极限、强度极限、硬度等均 提高,延伸率、截面收缩率、冲击韧性均降低 ;导电性、导热性、抗腐蚀性能均降低,铁磁 金属的磁性也会发生变化。
西华大学《材料性能学》总复习题
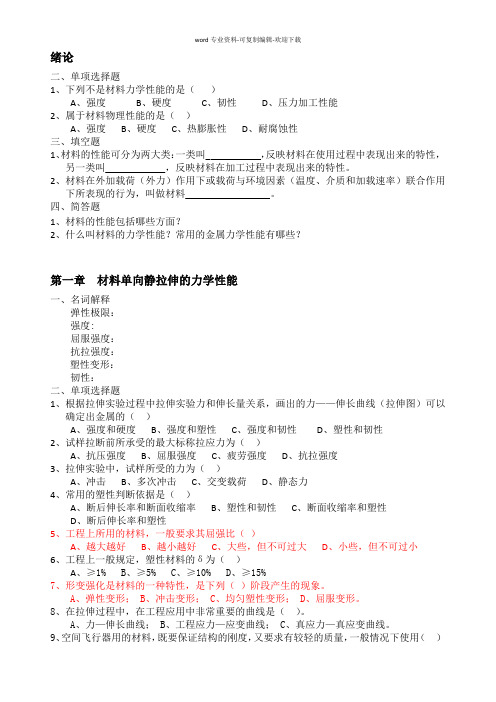
绪论二、单项选择题1、下列不是材料力学性能的是()A、强度B、硬度C、韧性D、压力加工性能2、属于材料物理性能的是()A、强度B、硬度C、热膨胀性D、耐腐蚀性三、填空题1、材料的性能可分为两大类:一类叫_ _,反映材料在使用过程中表现出来的特性,另一类叫_ _,反映材料在加工过程中表现出来的特性。
2、材料在外加载荷(外力)作用下或载荷与环境因素(温度、介质和加载速率)联合作用下所表现的行为,叫做材料_ 。
四、简答题1、材料的性能包括哪些方面?2、什么叫材料的力学性能?常用的金属力学性能有哪些?第一章材料单向静拉伸的力学性能一、名词解释弹性极限:强度:屈服强度:抗拉强度:塑性变形:韧性:二、单项选择题1、根据拉伸实验过程中拉伸实验力和伸长量关系,画出的力——伸长曲线(拉伸图)可以确定出金属的()A、强度和硬度B、强度和塑性C、强度和韧性D、塑性和韧性2、试样拉断前所承受的最大标称拉应力为()A、抗压强度B、屈服强度C、疲劳强度D、抗拉强度3、拉伸实验中,试样所受的力为()A、冲击B、多次冲击C、交变载荷D、静态力4、常用的塑性判断依据是()A、断后伸长率和断面收缩率B、塑性和韧性C、断面收缩率和塑性D、断后伸长率和塑性5、工程上所用的材料,一般要求其屈强比()A、越大越好B、越小越好C、大些,但不可过大D、小些,但不可过小6、工程上一般规定,塑性材料的δ为()A、≥1%B、≥5%C、≥10%D、≥15%7、形变强化是材料的一种特性,是下列()阶段产生的现象。
A、弹性变形;B、冲击变形;C、均匀塑性变形;D、屈服变形。
8、在拉伸过程中,在工程应用中非常重要的曲线是()。
A、力—伸长曲线;B、工程应力—应变曲线;C、真应力—真应变曲线。
9、空间飞行器用的材料,既要保证结构的刚度,又要求有较轻的质量,一般情况下使用()的概念来作为衡量材料弹性性能的指标。
A、杨氏模数;B、切变模数;C、弹性比功;D、比弹性模数。
特殊过程控制管理规定(3篇)

第1篇第一章总则第一条为确保产品质量,加强特殊过程的管理,根据《中华人民共和国产品质量法》及相关法律法规,结合本单位的实际情况,特制定本规定。
第二条本规定适用于本单位所有涉及特殊过程的生产、加工、检验等环节。
第三条特殊过程是指那些对产品质量有显著影响,难以通过常规检验手段进行控制的过程。
主要包括:1. 高精度加工过程;2. 特种合金熔炼过程;3. 高温、高压、高真空等特殊环境下的加工过程;4. 高分子材料成型过程;5. 精密计量过程;6. 特种表面处理过程;7. 其他对产品质量有重大影响的过程。
第四条特殊过程控制管理的目标是:1. 确保产品质量符合国家标准和客户要求;2. 提高生产效率和产品质量稳定性;3. 保障员工安全和环境保护。
第二章组织机构与职责第五条本单位成立特殊过程控制管理小组,负责特殊过程控制的全面管理工作。
第六条特殊过程控制管理小组的职责:1. 制定特殊过程控制管理制度和操作规程;2. 组织特殊过程能力验证;3. 监督特殊过程执行情况;4. 对特殊过程进行定期评审;5. 处理特殊过程发生的质量问题。
第七条各部门负责人对本部门特殊过程控制工作负直接责任,应确保本部门特殊过程控制工作的有效实施。
第八条各岗位操作人员应按照特殊过程控制管理制度和操作规程进行操作,确保产品质量。
第三章特殊过程识别与评审第九条各部门应识别本部门涉及的特殊过程,并填写《特殊过程识别表》。
第十条特殊过程控制管理小组对各部门提交的特殊过程进行评审,确认其特殊性质和风险等级。
第十一条评审内容包括:1. 特殊过程对产品质量的影响程度;2. 特殊过程的操作难度;3. 特殊过程的设备、材料、环境要求;4. 特殊过程的检验方法和手段;5. 特殊过程的控制措施。
第十二条评审结果分为“必须控制”、“需要控制”和“可接受”三个等级。
第四章特殊过程控制措施第十三条对必须控制的特殊过程,应制定详细的操作规程和控制计划。
第十四条操作规程和控制计划应包括以下内容:1. 操作步骤;2. 设备、材料、环境要求;3. 操作人员要求;4. 检验方法和手段;6. 异常情况处理。
机械工程材料第五章 铁碳合金
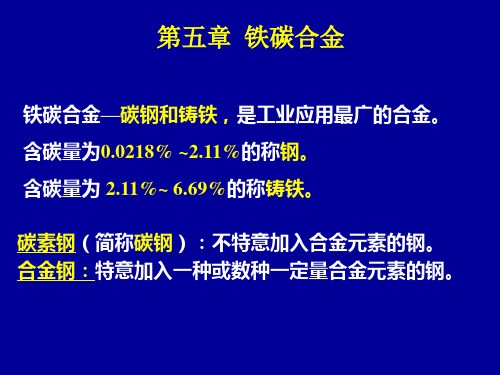
4、共晶白口铁
L
L→ Ld( A+Fe3C) A→ (Fe3C)Ⅱ
A→P(α+Fe3C)
室温组织:Ld′ 即 P+(Fe3C)Ⅱ+Fe3C 室温相:α+Fe3C
5、亚共晶白口铁
L L→A L→ Ld (A+Fe3C) A→ (Fe3C)Ⅱ
A→P(α+Fe3C)
室温组织: Ld′+P+(Fe3C)Ⅱ 即(P+(Fe3C)Ⅱ+Fe3C)+P+Fe3CⅡ 室温相:α+Fe3C
四、 Fe-Fe3C相图的应用
1.为选材提供成分依据
低碳钢(0.10-0.25%C):建筑结构和容器等 中碳钢(0.25-0.60%C):如轴等 高碳钢(0.6-1.3%C):如工具等 白口铁:如拔丝模、轧辊和球磨机的铁球等
34
2.为制定热加工工艺提供依据
(1)在铸造生产方面的应用 根据Fe-Fe3C相图可以确定铁碳合金的浇注温度, 浇注温度一般在液相线以上50℃~100℃。 共晶成分的铸铁凝固区间最小(为零),流动性 好,分散缩孔少,可使缩孔集中在冒口内,有可 能得到致密的铸件得到较广泛的应用。
其性能特点是强度低,硬度不高,易于塑性变形。
⑸ Fe3C相(又称渗碳体):根据其生成条件不同有条状、网状、
片状、粒状等形态,对铁碳合金的力学性能有很大影响。
1600 A 1400 N 1200 1000
+L
B 0.53 J 0.17 H 0.09 1495
L
2.11 E
4.3 1148 C
+
注意:由于不保证化学成分,所以热处理时不能 依甲类钢来选材,应依乙类钢选,才能根据相图 制定热处理工艺。
- 1、下载文档前请自行甄别文档内容的完整性,平台不提供额外的编辑、内容补充、找答案等附加服务。
- 2、"仅部分预览"的文档,不可在线预览部分如存在完整性等问题,可反馈申请退款(可完整预览的文档不适用该条件!)。
- 3、如文档侵犯您的权益,请联系客服反馈,我们会尽快为您处理(人工客服工作时间:9:00-18:30)。
塑性决定于珠光体球团、片层间距两个因素的迭加。
总结: 1)铁素体为主的钢,细化铁素体晶粒来提高强度 和韧性; 2)珠光体为主的钢,控制轧制使强度降低,韧性 提高。对此类钢必须采用再结晶型控轧。 3)对中高碳钢,轧后控制冷却,使珠光体在低温 度下产生,得到细片层珠光体,可提高强度和韧 性。
图5-7-2 0.42%C-0.55%Mn-0.023%Nb钢的控制轧制组织 (a)35%;(b)50%;(c)75%
中碳钢,如Mn<1%,钢的主体为铁素体时,仍是 铁素体细化机理在起作用。控制轧制→铁素体和 珠光体充分细化。
(2)常温组织以珠光体为主的钢材 0.43%C,1.40%Mn钢: 普通热轧:所得到的组织:铁素体在即将转变的 奥氏体晶界上生成网状组织。 控制轧制(再结晶区中轧制):奥氏体再结晶晶粒 细化→铁素体及珠光体组织都得到细化。随着变 形量的增加,细化程度增加。
(2)控制轧制中组织性能的变化 强度变化: 强度变化:
碳量0.2%∼0.3%: 含0.4%C以上: 含0.8%C以上的钢:
பைடு நூலகம்
图5-12 碳含量对控制轧制材(CR)与普通轧制材(HR)强度的影响
强度降低原因:
1)珠光体的片层间距及珠光体(领域)的大小与奥氏体晶 粒尺寸毫无关系。
图5-13 560°C(833K)及600°C(873K)铅浴淬火的珠光体领域直径和层 间距与γ晶粒度的关系 (a)珠光体领域直径和γ 晶粒度的关系;(b)珠光体片层间距与γ晶粒度的关 系
2)γ温度愈低、 γ晶粒愈细,珠光体成核点愈 多。珠光体开始转变线和终了转变线发生变化。
珠光体相变曲线随γ化温度的 移动状况
珠光体生成温度和层间距的关系
塑性、韧性的变化:
0.2%∼0.8%C内的脆性 转化温度比较: 0.2∼0.8%C内的断面收 缩率比较: 延伸率的比较:
图5-12-1 碳含量对控制轧制材(CR) 与普通轧制材(HR)塑性、韧性的影响
原因:固溶量增加 阻止奥氏体再结晶 作用加强。
图5-5 轧制前加热温度对 0.4%C,1.38%Mn,0.023% Nb钢临界压下率的影响效果
(2)铌、碳对中高碳钢奥氏体再结晶晶粒度的影响
图5-6 压下率、轧制温度对中碳钢(加Nb与不加Nb)轧制后 再结晶晶粒度的影响
图中得到:1)压下率大、再结晶奥氏体晶粒细;2)轧制温度 对奥氏体晶粒尺寸的影响较小;3)同一变形条件下,加铌的 中碳钢比不加铌的中碳钢的再结晶晶粒细;4)碳含量对再 结晶晶粒度影响较小。
图5-2 0.40%C,1.38%Mn,0.023 %Nb钢的γ晶粒再结晶行为
在中碳钢中添加铌同样可以延迟奥氏体再结晶。
(2)碳对中高碳钢奥氏体再结晶临界变形量的影响 不含铌钢: 加铌钢:随碳含量↑ 临 界压下量↓。
图5-4 C量对Nb钢与不加Nb钢 临界压下率的影响
碳量的多少决定了Nb的固 溶量,C↑,Nb的固溶量↓, 轧制时析出量↓,阻止再 结晶作用↓ 。
珠光体球直径愈细,断面收缩率愈大,珠光体片层 间距愈小延性愈好。
含碳量和球化处理对εu的影响 1-球化处理(粒状渗碳体);2-正 火(片状渗碳体)
碳化物体积和球化处理对的εT影响 1-球化处理(粒状渗碳体);2-正火 (片状渗碳体)
3)对韧性的影响: 各强化因素对冲击值转变温度ITT的影响:
珠光体碳分冲淡系数:
5.3 中高碳钢的组织与力学性能的关系 (1) 中高碳钢组织对性能的影响 1)对强度的影响 重要因素:珠光体的片层间距。
式中σ0为纯铁素体强度,σS、σ0.2为材料的 屈服强度,I0为珠光体的片层间距,Ky为系数。
各种强化因素对抗拉强度的影响:
2)对塑性的影响:
图5-10球状珠光体直径(dy)和断面收缩率关系
5 中高碳钢控制轧制特点
中高碳钢特点:(1)冷却后的组织发生变 化:(2)决定钢材性能的因素发生变化: 铁素体和珠光体的比例、铁素体晶粒的大 小、珠光体片层粗细和球团大小以及渗碳 体的形貌。
5.1 中高碳钢奥氏体的再结晶行为
(1) 铌对中高碳钢奥氏体再结晶临界变形量的影响
图5-1 0.43%C,1.4%Mn钢, γ 晶粒再结晶行为 (1200°C加热后 轧制1道次,原始γ晶粒度为1级)
所得常温组织: 铁素体和珠光 体;所占面积: 各50%;铁素体 晶粒:8级。
图5-7-1 0.42%C-0.55%Mn-0.023%Nb 钢的常规轧制组织(×200)
控制轧制工艺 : 第一阶段:压下率:50%,最后 一道温度:再结晶区下限(1050~1100°C); 第二阶段轧制:终轧温度:870°C,压下率分别 为: 1)35%:铁素体晶粒比普通轧制时的铁素体晶粒 细小,珠光体变得粗大。原因: 2)压下率为50%:部分再结晶区轧制,铁素体和 珠光体基本上都得到均匀细化。 3)压下率为75%:铁素体晶粒组织更细化、均 匀,晶粒度达到12~13级。
图5-7 压下率对含Nb和不含Nb中高碳钢 轧制后γ再结晶晶粒度的影响
5.2中高碳钢控制轧制钢材的组织状态 (1)常温组织以铁素体为主的钢材(Mn<1.0%) 成分:0.42%C,0.55%Mn、0.032%Ni 加热温度:1200°C 普通轧制 :第一阶段压下率:50%,第二阶段压下率: 35%,终轧温度:再结晶区下限(1050°C∼1000°C)
0.43%C,1.38%Mn、0.023%Nb钢:相同条件进行控 轧,存在的问题: 总结: 中碳钢(尤其加铌钢)低温轧制不利。最好 在奥氏体再结晶区进行充分的轧制尽量细化奥氏 体晶粒。
(3)共析钢 共析钢控制轧制目的:珠光体团得到细化。 珠光体球团尺寸取决于γ晶粒尺寸,随着γ晶粒尺 寸↓,珠光体球团直径↓。 过共析钢控制轧制目的:珠光体球团变小,同时 亦使析出的网状碳化物变薄。要在奥氏体再结晶 区轧制,使奥氏体晶粒细小。