丰田内部培训系列教材标准作业教材
A03109丰田TPS培训教材

模拟游戏 ①
①理解制造方法改变成本的事实。 ②体验流程化、逐个生产的制造方法。
19
Ⅱ.丰田生产方式的源流 (Vedio)
20
Ⅲ. 丰田生产方式
如何将“顾客第一 ”具体化
及时、低成本地 生产高品质产品
资金短缺时 如何快速回收
2大支柱
J.I.T
及时地
彻底消除
“不合理、浪费、不均 ”
低成本 高品质
(3) 物流不合理
42
(2) 制造过程中的不合理 1) 批量规模过大,会导致周期时间变长。
加工 1小时
10天份的批量规模 (生产切换不灵活)
生产的 周期时间
= 加工时间 + 批量规模(10日)
最后生产出来的1个产品在10天1H后才能使用
浪费 動 働
强化劳动
不改善而加强劳动强度
浪费
動
働
浪费
働
浪费
動 働
浪费 動 働
働 浪费
浪费 動 働
17
支撑丰田生产方式的经营观点·理念
1. 企业的目的 2. 不降低成本就无法提高利润 3. 降低成本 = 提高生产性 4. 生产方式改变成本 5. 浪费无处不在
・浪费各种各样 ・生产过剩是最严重的浪费 6. 表面生产性与实际生产性的区别 7. 稼动率与可动率的区别 8. 整体效率重于局部效率 9. 提高劳动生产性与强化劳动的区别
間2 送 3歩
ー
ワーク取り外し取付け、送りをかける
25
ワワ原MDーー34IRクク取 取材--12り り料74外 外62し し44を取 取ワワDT取ーー付 付46RPクク5取 取け ける--21り り、、送 送41外 外20り りし し41を を取 取ワか かTネー付 付Pクけ け完取け け-ジる る1り、、成送 送1径外0り り品し1をを を取をか か測付け け置け定る る、く送すりるを332かける
丰田内部培训系列教材-平准化

(例):总装工序
・1条线上生产4种产品
种类
A B C D
合計
月产量
4560
1820 1820
920 9120
日产量 生产比例 节拍时间
228 50 % 4分/台 91 20 〃 10 〃 91 20 〃 10 〃 46 10 〃 20 〃 456 100 % 2分/台
生产有种类区别的产品时 ①将每天的生产量确定下来 ②将产品的种类・量平均化后进行生产
全盛集团
均衡化(平准化)生产
如何实现平准化生产③
・平衡负载箱的流程
专注持续为客户创造
价值
Focus on continuing to create value for customers
Shift
S
Prem Bracket
7:25 7:50 4:25 4:50
为什么需要品种的均衡
Focus on continuing to create value for customers
化????
配套企业(甲)
终于轮到我们了
这个月只生产A车 型,甲厂供货就可 以了,乙厂、丙厂
以后再说
主机厂
怎么能这样,设备、模 具、人员都准备好了,
三个月才要一次货
配套企业(乙)
这样的企业以后 可不能和他们合
全盛集团
平準化箱
(毎一小時理貨一回)
出货、理货管理板
专注持续为客户创造
价值
Focus on continuing to create value for customers
全盛集团
均衡化(平准化)生产
如何实现平准化生产④
专注持续为客户创造 价值
Focus on continuing to create value for customers
【参考文档】丰田作业指导书word版本 (10页)

本文部分内容来自网络整理,本司不为其真实性负责,如有异议或侵权请及时联系,本司将立即删除!== 本文为word格式,下载后可方便编辑和修改! ==丰田作业指导书篇一:丰田生产方式与标准作业(70研修教材)丰田汽车株式会社人事部目录第1章企业目的与降低成本1. 企业目的52. 降低成本的必要性5 2-1 销售价格与成本2-2 产品的制造方法与成本第2章丰田生产方式及其展开内容1. 独特的生产技术的开发72. 丰田生产方式的目标73. 丰田生产方式的两大支柱7 3-1 准时化3-1-1 平准化生产3-1-2 准时化的基本原则 3-2 自働化3-2-1 另一种自働化 3-2-2 电子显示板4. 看板11 4-1 看板的作用 4-2 看板的种类4-3 看板的传递方式与规则5. 搬运15 第3章改善的见解、思路1. 对浪费的认识15 1-1 工作与浪费 1-2 浪费的种类2. 能率与效率18 2-1 真正的能率与表面的能率 2-2 个体的能率与整体的能率 2-3 运转率与可动率2-4 判断的基准是降低成本第4章标准作业与改善1. 标准作业21 1-1 标准作业的条件 1-2 标准作业的三要素 1-2-1 节拍 1-2-2 作业顺序 1-2-3 标准在制品2. 标准作业的各种表格 232-1 各工位能力表 2-2 标准作业组合票 2-3 标准作业指导书 2-4 标准作业票2-5 标准作业与作业标准的区分 2-5-1 标准作业 2-5-2 作业标准3. 标准作业与监查者264. 标准作业与改善275. 质量的提高与稳定6. 全面贯彻安全作业与提高作业性7. 标准作业的改善顺序第5章作业改善的推进方法1. 作业改善与设备改善2. 作业改善的顺序2-1 发现必须改善的问题点 2-1-1 生产的订货周期2-1-2 人的工作与机械的工作 2-1-3 4S与物品的放臵方法 2-1-4 生产管理板2-1-5 其他2-1-5-1 缺点列举法 2-5-1-2 希望点列举法3. 现在方法的分析3-1 分析时的心理准备 3-2 表准作业 3-3 要素作业分析3-4 其他 (各种分析方法) 3-5 动作分析(基本动作)4. 得到构思4-1 追究原因的姿态 4-2 五次“为什么” 4-3 追究原因的条件4-4 问题点的层次划分与相互关系的研究 4-5 得出构思的方法 4-5-1 清单检查法(“奥斯本”式) 4-5-2 动作经济的原则 4-5-3 集体思考 4-5-4 改善与障碍5. 改善方案的制定5-1 改善的方向 5-1-1 排除27 28 29 30 30 34 36 445-1-2 组合变更----分离与结合 5-1-3 合适化 5-1-4 标准化 5-1-5 同期化5-1-6 自动化6. 现场观察(改善实习 477. 新方法的实施 47 7-1 面向有关人员的理解活动7-2 对工人的培训8. 改善效果的确认8-1 评价改善的思维方法8-2 既定目标与改善实效的比较 8-3 反映到标准作业 8-4 问题的再发现9. 改善永无止境 48 49第1章企业目的与降低成本1. 企业目的首先,作为企业的经营活动,一方面要谋求与社会的协调,一方面又必须追求自身利益,履行社会赋予的使命,求得永久的生命力。
(精品)丰田内部培训系列教材—pokayokeb防错

全盛集团
怎么进行POKA YOKR
专注持续为客户创造价值
错误 Focus on continuing to create value for customers
正确
第二种
第二种办法:
可以传感器、电子读取设备、启动元器件等进行相应的判定
.
可利用的电子产品
• 传感器 • 限位开关 • 电子计数器 • 微动开关 •出错报警器 。。。。。。
如何通过设计来进行防呆
after
盒式音响面板标识条 新设计--都能正确安装 从设计上防呆
全盛集团
POKA YOKR改善实例
专注持续为客户创造价值
Focus on continuing to create value for customers
全盛集团 POKA YOKR改善实例
专注持续为客户创造价值
全盛集团 POKA YOKR改善实例
专注持续为客户创造价值
Focus on continuing to create value for customers
before
倒车闸 ×倒车手闸可能没有正
确紧固。 ×上述情况很难探测到。
本例子中,用于紧固倒车闸的螺纹紧固 螺栓常常没有正确紧固。 这种错误常常导致较多的售后抱怨 如何通过设计来进行防呆
Focus on continuing to create value for customers
全盛集团
POKA YOKR改善实例
专注持续为客户创造价值
Focus on continuing to create value for customers
全盛集团 POKA YOKR改善实例
专注持续为客户创造价值
人为失误发生
丰田4S管理培训教材

提高信任感和满意度
异常减少 品质提高 满意度提高
对策
寻找解决对策
TOYOTAL&F
“发现浪费”→“改善” 可以发现浪费的组织架构 4S
这一循环不断往复。
平均化生产
后续工序
标准作业
T P S 的 2 根 支 柱
Just/in/time 仅对“需要的产品”、“在必要的时间”、生产和搬运“必要 的量”。
TOYOTAL&F
制定4S日历
TOYOTAL&F
1. 丰田的生产方式和4S
2. 4S的实践
3. 维持4S的关键,另外一个S“教育”
TOYOTA L&F
检查你的公司的“教育”度 □①把不需要的物品扔掉后,会马上发生大量堆积。 □②工具使用完毕后,丢在那里不管。 □③物品不是什么时候不见了 □④钻头和美工刀的放置方法会影响其锋利程度 □⑤材料和零部件的堆积易发生倾倒 □⑥厕所肮脏 □⑦机械和设备沾满油污和粉尘,乌黑一片。 □⑧无论怎么劝说,都不戴安全帽和防护眼镜 □⑨作业场所和通道上布满烟屁股和垃圾 □⑩无法打招呼
在制造业中,只有“加工”是具有附加价值的作业=正式作业 只有正式作业才能得到回报。
TOYOTAL&F
所谓浪费:所有不能提高附加价值的工作。 浪费的种类 7种浪费
最严重的浪费 ①制造过剩 (会诱发其它浪费的 产生) ②拿在手里 ③搬运 ④加工过程自身存在的 浪费 ⑤库存 ⑥动作 ⑦不合格产品/修理
子啊丰田公司,在生产中, 把 ,在物流过程中把 定位为“最严重的浪费”。
自动化(带人字部的自动化) 发生异常时停止、人和机械的分离、在工序中控制质量
TOYOTAL&F
4S是基本中的基本,是进行改善最为重要的基础工作。
丰田内部培训系列教材—smed(快速换模)
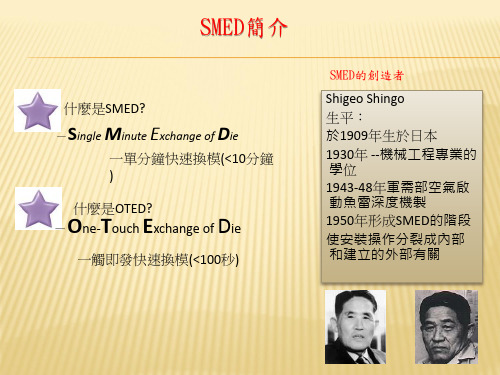
去除 ,簡化,自動化
---只按照此順序進行
各種簡化的實例圖解: •梨型槽的使用 •U型槽的使用 •C型墊片 •劈開螺絲 •減少使用螺絲
機器殼體 臺面
可視化設置值,参照線
中心夾具(v形片) 柱形杆 中心夾具(v形片)
可視化中心線
對於每种規格的可視化設計
SMED的实施过程
将内部操作转换为外部操作
■ 例 1:
3stup
优化各操作
内部 外部
内部 外部
内部
外部
1. 检查表 2. 三定 3. 改进部件 和工具的运输
外部
1预先准备 操作条件 2.功能标准化 3.部件集成化
外部
1. 消除各 种浪费
2. 快速工具
内部
内部
内部
1. 平行操作 2. 功能性夹具 3. 调试的消除 4. 机械化
全盛集团
第0步驟:
办法一:
改善前(一人切换)
改善后(二人切换)
大的机器设备在切换/装 配的各步骤间常常需要 一些来回移动
这些过多的移动浪费了 时间和付出的劳动
仔细考虑切换操作人员 的移动线路并制定出操 作的最合理的次序
发展并执行高效操作的 程序
考虑使用一人以上进行 品种切换。
每个人遵循一个固定的 程序
对于平行操作建立信号 /通知系统以确保安全
缺點:需有錄影設備
工程名
機器別
規格 NO
換模作業項目
作業者
時間
累計
實際
觀 測 者
時 間
作業工時
外 內工時 工
時
改善構想
內外部作業分開
第1步驟:
1.目的: (1)排除不良、不适当、不能使用之浪费。 (2)排除拿错、不知放置地方、不够用、缺少之浪费。 (3)排除无谓来回重复走动或搬运。 (4)排除设备停止后之清理、调整、修护、换装刀具与工具等之浪费。 (5)区分开内部和外部的作业
- 1、下载文档前请自行甄别文档内容的完整性,平台不提供额外的编辑、内容补充、找答案等附加服务。
- 2、"仅部分预览"的文档,不可在线预览部分如存在完整性等问题,可反馈申请退款(可完整预览的文档不适用该条件!)。
- 3、如文档侵犯您的权益,请联系客服反馈,我们会尽快为您处理(人工客服工作时间:9:00-18:30)。
(秒) 70 60
测定次数 的最短值
着眼于泼动大的作业 ,縮小差距
全盛集团 标准作业的制作要领
专注持续为客户创造价值
? 作的差异中发现问题的、看得见的 管理工具,并以此为基础开展改善 活动。没有标准的地方,即无法区 别正常、异常的地方不会有改善。
3.标准作业的前提条件
标准作业的成立,需要下列条件。 一个是“以人的动作为中心”
标准作业是根据人的活动而不是机械的 运转而制订的。制订标准作业时,不能 受设备条件的限制,无视人的动作,归 根结底应以人的动作为中心。
标准作业和改善
“没有标准的地方就没有改善 ”
作业次序和时间以及作业方法的话,其结果才能得以明 确的判断.但是,如果没有标准的话就难以判定改善结果
所谓“表”准作业,是指把现状的作业落实到《表》
上
发现问题点,浪费
表
抽
表
准 作
出
改
问 题
善
准 作
改善是永远的 智慧是无限的
业
点
业
追究原因
改善 (防止再发)
全盛集团 根据标准作业进行改善
要素作业时间观测用纸
制作: ….年….月….日 制作者: ……
生产线名: …… 工序NO: …… 作业者名: ……
作业顺序
1
作业名称 取原材料
12345 2.0 20 1.0 1.5
专注持续为客户创造价值
Focus on continuing to create value for customers
不稳定(秒)
2
安装工位和拉铆钉 4.0 6.0 5.0 4.0 5.5
3
零件装箱
5.0 3.0 4.0 4.0 3.0
步行
1.0 1.5 1.0 1.0 1.5
4
取零件
4.0 4.0 3.0 3.0 5.0
10
装完成品
合计
1.0 1.5 1.0 1.0 1.5 65.5 68.5 61.0 58.5 71.0
异常区别)的地方就 没有改善 (b)发现MUDA、MURA、MURI
前提条件
①应以人的动作为中心 ②应是反复作业
三要素组成。
遵守标准作业可以保证品质、也决定数量、成本
全盛集团
标准作业
专注持续为客户创造价值
Focus on continuing to create value for customers
序”、
“标准手持”三要素组成。
标准作业
定义
它是以人的动作为中 心、把工作集中起来, 以没有MUDA的操作顺 序有效地进行生产的 方法,由:
TAKT TIME
作业顺序
标准手持
目的
①明确产品的制造方法 它是制造方法和管理的
根本,在考虑品质、数量、 成本、安全的基础上,规定 作业的方法。 ②改善的工具 (a)没有标准(没有正常、
专注持续为客户创造价值
Focus on continuing to create value for customers
(1) 降低工 (口) 时
从标准作业中的等待着手,之后再改善几秒就能够降低工时
(2) 降低半成品库存
减少工序内的半成品,把接合改善的慢性不良和故障显在化
(降低工时) 省人
(3) 降 低 品 质 不 良
全盛集团
标准作业
专注持续为客户创造价值
Focus on continuing to create value for customers
1.标准作业的定义 :
以人的动作为中心、以没有MUDA的操作顺序有效地进行生产,
这种做法在丰田生产方式中被叫做“标准作业”,它由“TAKT TIME (T.T)”、“作业顺
1. 节 拍 2. 作 业 顺 序 3. 标 准 手 持
以上三个要素,缺一不可
组装工序
标准手持
⑨
部
品 置
S4 黄油涂布机
场
⑧
⑦
⑩
11
完成品
作业顺序
①
②
原 S1
材 料
焊接机
节拍
⑥ ⑤ T 完成品
③ ④ W 完成品
从涂装 到涂装
全盛集团
1. 节拍
专注持续为客户创造价值
Focus on continuing to create value for customers
把操作 1个1个的部品的行为作为一个单位进行考虑
*取对象物(或者放置),实施目的行为 时间测定的步骤
(1)仔细观察观测作业 ,记住作业步 (2)把要素作业填骤写进时间观测用纸 (3) 测定要素作业1~至最后的连续作业时间
( 在难以测定的场合使用摄像机)
*观测时点是测定该作业完成的瞬间
全盛集团
(例)
因为作业是在相同条件下重复进行的,所以容易掌握真正的原因
(4) 增 强生 产能力的
明确薄弱工序之后再快几秒就能变好
(5) 布
局
为了进行无浪费的动作,就应该知道必须如何布局生产线的需求
(6) 目 视 管 理
除了制品一个个重复流动外,人的流动方式,物品的存放,以及其他事情也明确的话,那么 无论谁都能一目了然地看出浪费
2.标准作业的目的
? 标准作业的目的,大体有二个.
? 第一个是明确安全地、低成本地生 产优良产品所必须的制造方法。
? 第二个是将标准作业做为改善的工 具使用。
? 标准作业根据作业者和生产量的增 减、及改善活动而经常发生变化,
? 所以监督者必须经常对标准作业进 行管理,可以说它反映了生产线管 理
? 者的意图。而且,它是管理者观察 现场时,从标准作业票与作业者的 动
标准作业和标准作业
所谓作业标准是指为了进行标准作业而把作业方法和机械操作等标准化.(以确保 品质上的作业的各种条件为基准进行设定:QC 工程表,作业要领书)
全盛集团
要素作业
专注持续为客户创造价值
Focus on continuing to create value for customers
要素作业的分析单位
·生产1台份或 1个部品必须在几分几秒内完成的时间
节拍
1日(班)的定时运行时间
= 1日(班)的生产必要数
﹡运行 时间一般是以定时100%(生
产线停止=0)进行计算
2. 作业顺序 ·在既加工部品有进行组装的情况下 ,技能员搬运物品,在机器上进行
安装,卸除,组装部品的顺序. 3. 标准作业
·为了能在相同的顺序下重复进行作业而必要的最少限度的压线用工件
另一个是“反复作业”。 如果每次操作的动作发生很大的变化, 即使制订了标准作业也不能找出改善的 突破口,而且这时即使进行改善活动, 也不会收到效果。
全盛集团 标准作业 作业的三要素
专注持续为客户创造价值
Focus on continuing to create value for customers