车削加工PPT课件
合集下载
普通车床的螺纹车削加工ppt课件文字可编辑

15
三、典型普通螺纹零件的车削加工
螺纹总背吃刀量ap=h=0.54P=0.81mm
合理分配螺纹加工余量
(一般粗车ap:0.10~0.50;精车ap:0.01~0.10 。)
进刀次数
背吃刀量
加工步骤
加工余量
第一次进刀 第二次进刀 第三次进刀 第四次进刀 第五次进刀 第六次进刀
a =0.50mm p
a =0.15mm p
三、典型普通螺纹零件的车削加工
7. 螺纹车削操作方法与步骤
2)抬闸法 利用开合螺母的压下和抬起来车削螺纹。
控制手柄
正反车车削法
抬闸法
退刀方式 利用丝杆的反转纵向返回起点
手动纵向返回起点
适用范围
适用于任何螺距的加工
只适用于丝杆螺距是工件 螺距整数倍时
13
本标准适用于已投入商业运行的火力 发电厂 纯凝式 汽轮发 电机组 和供热 汽轮发 电机组 的技术 经济指 标的统 计和评 价。燃 机机组 、余热 锅炉以 及联合 循环机 组可参 照本标 准执行 ,并增 补指标 。
二、螺纹的车削加工工艺
2. 普通外螺纹的车削加工工艺流程
车端面 车螺纹大径 车退刀槽 倒角 车螺纹
d<公称直径 <螺纹小径
多刀车削
3
本标准适用于已投入商业运行的火力 发电厂 纯凝式 汽轮发 电机组 和供热 汽轮发 电机组 的技术 经济指 标的统 计和评 价。燃 机机组 、余热 锅炉以 及联合 循环机 组可参 照本标 准执行 ,并增 补指标 。
a =0.10mm p
a =0.03mm p
a =0.02mm p
a =0.01mm p
粗加工 精加工
0.75mm 0.06mm
数控车削加工课件

2. 某汽车制造企业使用数控车床加工铝合金轮毂,由 于刀具磨损导致加工精度下降,经过更换刀具后问题
得到解决。
06
数控车削加工的发展趋势和未来 展望
数控车削加工的技术发展趋势和创新方向
升级,向更高精度、更高效率、更低成 本方向发展。
智能化是未来数控车削加工技术的重要发展方向,通过引入人 工智能、机器学习等技术,实现加工过程的自动化和智能化控
实现对螺纹的加工。
05
数控车削加工的实践操作和技术 要点
数控车削加工的操作步骤和注意事项
操作步骤 1. 仔细阅读和理解图纸,了解工件的材料、尺寸和精度要求。
2. 根据图纸要求,选择合适的刀具和切削参数。
数控车削加工的操作步骤和注意事项
3. 安装工件,调整机床,确保安全防护措施到位。 4. 输入程序,进行模拟加工,确认无误后开始实际加工。
数控车削加工在机械制造、汽 车制造、航空航天等领域得到 广泛应用。
数控车削加工的工艺流程
数控车削加工的工艺 流程包括以下几个步 骤
2. 工件装夹:将工件 放置在数控车床上, 通过夹具进行固定和 定位。
1. 确定加工方案:根 据零件图和工艺要求 ,确定加工方案和加 工顺序。
数控车削加工的工艺流程
3. 刀具选择和调整
水平发展。
智能制造
智能制造是未来制造业的重要趋 势,数控车削加工将更加深入地 与人工智能、物联网等技术结合 ,实现加工过程的智能化和自适
应化。
定制化生产
随着消费者需求的多样化,制造 业向定制化生产方向发展,数控 车削加工将更加注重个性化和定 制化的需求,满足不同客户的需
求。
数控车削加工的人才培养和教育现状及未来发展需求
数控车削加工课件
得到解决。
06
数控车削加工的发展趋势和未来 展望
数控车削加工的技术发展趋势和创新方向
升级,向更高精度、更高效率、更低成 本方向发展。
智能化是未来数控车削加工技术的重要发展方向,通过引入人 工智能、机器学习等技术,实现加工过程的自动化和智能化控
实现对螺纹的加工。
05
数控车削加工的实践操作和技术 要点
数控车削加工的操作步骤和注意事项
操作步骤 1. 仔细阅读和理解图纸,了解工件的材料、尺寸和精度要求。
2. 根据图纸要求,选择合适的刀具和切削参数。
数控车削加工的操作步骤和注意事项
3. 安装工件,调整机床,确保安全防护措施到位。 4. 输入程序,进行模拟加工,确认无误后开始实际加工。
数控车削加工在机械制造、汽 车制造、航空航天等领域得到 广泛应用。
数控车削加工的工艺流程
数控车削加工的工艺 流程包括以下几个步 骤
2. 工件装夹:将工件 放置在数控车床上, 通过夹具进行固定和 定位。
1. 确定加工方案:根 据零件图和工艺要求 ,确定加工方案和加 工顺序。
数控车削加工的工艺流程
3. 刀具选择和调整
水平发展。
智能制造
智能制造是未来制造业的重要趋 势,数控车削加工将更加深入地 与人工智能、物联网等技术结合 ,实现加工过程的智能化和自适
应化。
定制化生产
随着消费者需求的多样化,制造 业向定制化生产方向发展,数控 车削加工将更加注重个性化和定 制化的需求,满足不同客户的需
求。
数控车削加工的人才培养和教育现状及未来发展需求
数控车削加工课件
《台阶轴车削加工》课件

切削深度的选择
切削深度
根据台阶轴的直径、材质和加工要求等因素 综合考虑,选择合适的切削深度。切削深度 过小可能导致加工效率低下,切削深度过大 则可能导致刀具磨损和工件表面质量下降。
参考切深范围
根据实际加工需求和刀具性能,确定切削深 度的参考范围,如0.1-0.5毫米。
05
台阶轴车削加工质量检测与控制
质量检测方法与工具
检测工具
卡尺、千分尺、百分表、千分表等测量工具用于测量台阶轴的尺寸、形位公差等参数。
检测方法
采用直接测量法、比较测量法、间接测量法等多种方法进行检测,确保测量结果的准确性和可靠性。
质量控制措施与改进
提高机床精度
定期对机床进行维护和保养, 确保机床精度和稳定性。
持续改进工艺
不断优化工艺参数,提高加工 效率和产品质量。
主偏角和副偏角
影响切削刃工作长度、切削深度和 切削宽度,从而影响切削力、切削热 和表面粗糙度。
刃倾角
控制切屑流向,影响切削刃的锋利 程度和受力方向。
车刀的刃磨与维护
刃磨
定期对车刀进行刃磨,以保持其锋利的切削 刃和合适的几何参数。
维护
使用专用的润滑剂和冷却液,保持车刀清洁 ,避免与坚硬物质接触以防损坏。
《台阶轴车削加工》PPT课件
目 录
• 台阶轴车削加工简介 • 台阶轴车削加工设备 • 台阶轴车削加工刀具 • 台阶轴车削加工工艺参数 • 台阶轴车削加工质量检测与控制 • 台阶轴车削加工实例分析
01
台阶轴车削加工简介
台阶轴车削加工的定义
台阶轴车削加工是一种机械加工方法 ,主要用于生产具有阶梯形状的轴类 零件。
03
台阶轴车削加工刀具
车刀的种类与用途
数控车削加工工艺课件(共21张PPT)《数控车削编程与操作训练》
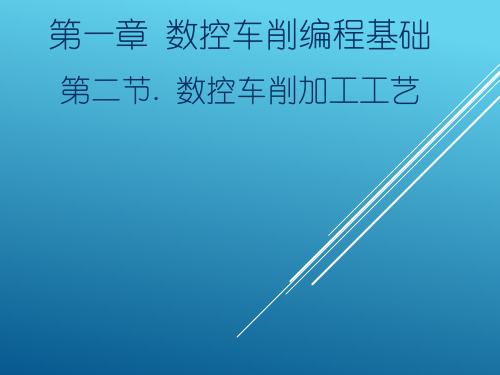
1.对刀点 对刀点是在数控机床上加工零件时,
刀具相对于工件运动的起点。
ZO 对刀点X源自2.换刀点换刀点是指刀架转位换刀的位置。 以刀架转位时不碰工件及其他部件 为准。
3.刀位点 刀位点是指在加工程序编制中,用以表
示刀具位置的点
注:每把刀的刀位点在整个加工中只能有一个位置。
1.2.7 数控加工工艺技术文件的编写
确定原则: 粗加工时,选择较大的背吃刀量,
以减少走刀次数,提高生产率;
精加工时,通常选较小的 ap值,以
保证加工精度及表面粗糙度。
2.进给量f 的确定
确定原则: 粗加工时,进给量在保证刀杆、刀具、
机床、工件刚度等条件前提下,选用尽可 能大的f 值;
精加工时,进给量的选择主要受表面粗 糙度要求的限制,当表面粗糙度要求较高 时,应选较小的f 值。
以使总的工序数量减少。 适用于单件小批量生产。
2.工序分散原则 加工零件的过程在较多的工序中进行,
而每道工序的加工内容很少。 适用于大批量生产。
1.2.3 加工路线的确定
加工顺序确定原则:先粗后精、先近后远。
先粗后精
先近后远
1.2.4 刀具的选择
1.机架式可转位车刀
2. 数控车床常用刀具类型及用途
3.主轴转速n的确定
确定原则: 粗车时,选较低的切削速度, 精车时,选较高的切削速度。 由切削速度计算主轴转速的公式如下: n=1000v/(d) 式中:d ——工件直径,mm; v ——切削速度,m/min。
切削用量选择参考表
1.2.6 数控加工中对刀点、换刀 点及刀位点的确定
1.对刀点 2.换刀点 3.刀位点
谢谢观看!
第一章 数控车削编程基础
第二节. 数控车削加工工艺
车削加工基础知识ppt课件

02
表面质量与加工参数的关系
合理的加工参数选择可以有效提高表面质 量,减少工件表面的粗糙度。
03
工艺参数对加工效率和材料利 用率的影响
合适的工艺参数可以提高加工效率,同时 合理利用材料,降低生产成本。
05
车削加工的常见问题及 解决措施
振动的产生及消除方法
01 振动的产生
车削加工过程中,由于多种因素可能导致工件振 动,影响加工精度和表面质量。
02
车削加工的原理
车削运动
车削加工是通过工件和刀具的相对运动, 使工件表面材料不断被去除的过程。
车削运动主要由主运动和进给运动组成, 主运动是工件的旋转运动,进给运动是刀 具的直线运动。
பைடு நூலகம்
车削加工原理
车削运动组成
车削要素
车削运动
车削加工是通过主轴的旋转实现刀具和工件的 相对运动,从而完成切削加工的过程。
车削加工基础知识 ppt课件
汇报人:XXX
目录
01 02 03 04 05
车 车 车 车 及车
削 削 削 削 解削
加 加 加 加 决加
工 工 工 工 措工
的 的 的 的 施的
基原刀工
常
本理具艺
见
概
参
问
念
数
题
01
车削加工的基本概念
车削加工的概念
车削加工是机械制造中最基本的一种加工方式,是 指通过旋转车刀将工件进行切削,使其达到要求的 形状和尺寸。
04
车削加工的工艺参数
切削用量的选择
切削速度
切削速度对加工效率、加工表面 质量和刀具寿命都有影响,应根 据材料和刀具的特性合理选择。
进给量
进给量的大小直接影响加工表面 的粗糙度和刀具寿命,应根据加
《机械制造基础》车削加工 ppt课件

ppt课件
2
表1 车削的加工类型
第第 2 页页
ppt课件
3
第第 3 页页
续表
ppt课件
4
第第 4 页页
续表
ppt课件
5
第第 5 页页
1.1 车削刀具
常用车刀的名称、形状和工作位置如图1所示。45°、75°右偏刀 (由床尾向床头方向进给)适合加工外圆;90°右偏刀适于修正外 圆和直角台阶;宽刃光刀适于精加工外圆;90°端面车刀适于加工 端面;右偏刀适于加工外圆和直角台阶;内孔车刀适于加工通孔; 内孔端面车刀适于加工不通孔端面。
ppt课件
6
图1 常用9种车刀的工作位置
第第 6 页页
1.2 车削加工的工艺特点
车削加工是应用最为广泛的加工工艺。其主要特点为:
(1)易于保证各加工面之间的位置精度。车削时,工件作主运
动绕某一固定轴回转,各表面具有同一的回转轴线。因此,各加
工表面的位置精度容易控制和保证。
(2)切削过程比较平稳。一般情况下车削过程是连续进行的,
动画23 四爪卡盘
ppt课件
16
视频2 四爪卡盘装夹工件
3. 两顶尖安装工件
如视频3所视,顶 尖的作用是定中心、 承受工件的重量和 切削力。顶尖分前 顶尖和后顶尖两类。
第第 16 页页
ppt课件 视频3 用顶尖装夹工件
17
第第 17 页页
(1)前顶尖。 插在主轴锥孔内与主轴一起旋转的顶尖称作前顶尖(见动画 24)。前顶尖随工件一起转动,与中心孔无相对运动,不发生摩 擦。有时为了准确和方便起见,也可以在三爪自定心卡盘上夹 一段钢材,车成60°代替前顶尖,如动画25所示。
(1)床身。是支撑车床的基础部分,联接各主条相互平行的纵向导轨, 分别来承放刀架和尾架。
《机械制造技术基础》第三章《机械制造技术基础》车削加工基础知识-PPT课件

§3-4 卧式车床的几个主要结构
超越离合器
(1)机动进给时传递由光杠传来的用于进给的低速运动; (2)快移时可以不要脱开进给链。
§3-4 卧式车床的几个主要结构
安全离合器
在进给链中设置的过载保险装置,防止进给力过大 或刀架移动受阻时机件被损坏。
§3-5 其他类型车床及其加工范围
滑鞍转塔车床
ZⅠ-Ⅱ 、 Z’Ⅰ-Ⅱ ——轴Ⅰ和轴Ⅱ 之间相啮合的主动齿
轮和从动齿轮齿数。
§3-3 卧式车床及其传动
2、进给运动传动链
两个末端件分别是主轴和刀架,其功用是使刀架实现纵向 或横向移动及变速与换向。
A. 螺纹进给传动链
• 可以车削左旋和右旋的公制、英制、模数制和径节制四种标 准螺纹。
• 主轴转1r —— 刀具移动L mm
45 48
i基 = 67 .5, 7 7, 7 8, 7 9, 97 .5, 17, 0 1 7, 1 172
是一个等差数列,该变速机构称 为基本组。
i倍=81,14,12,1
是个等比数列,称为增倍组。
§3-3 卧式车床及其传动
车削公制螺纹(右旋)的运动平衡式为:
53 86 31 30 20 523 56
§3-3 卧式车床及其传动
挂轮的换置公式为:
§3-3 卧式车床及其传动
§3-3 卧式车床及其传动
B.纵向和横向进给传动链
§3-3 卧式车床及其传动
f纵=1×58/58×33/33×63/100×100/75×25/36 ×u基×25/36 ×36/25 ×u倍×28/56 ×36/32×32/56×4/29×40/30×30/48×28/80×π×2.5 ×12=0.71 u基u倍 mm/r f横=1×58/58×33/33×63/100×100/75×25/36 ×u基×25/36 ×36/25 ×u倍×28/56 ×36/32×32/56×4/29×40/30×30/48×59/18×5 mm/r
车削加工技术(第2版)课件:车削成形面和表面修饰加工-车削成形面

车削加工技术
任务一 车削成形面
二、车削橄榄手柄
⑺精车φ(10±0.018)mm,长20mm至尺寸要求,车削φ16mm 外圆。 ⑻用锉刀、砂布修整抛光(用专用样板检查)。 ⑼松去顶尖,用圆头车刀车削R6mm圆弧面,并切下零件。
车削加工技术
任务一 车削成形面
二、车削橄榄手柄
⑽调头垫铜皮,夹持φ24mm外圆,找正并夹紧,用锉刀修整 R6mm圆弧,并用砂布抛光。
车削加工技术
任务一 车削成形面
一、双手控制法车削单球手柄
5.修整 由于双手控制法为手动进给车削,零件表面不可避免地留下高低不
平的刀痕,所以必须用细齿纹平锉进行修光,再用1号或0号砂布砂光 。
车削加工技术
任务一 车削成形面
二、球面的检测
⑴用样板检查 用样板检查时,样板应对准零件中心,观察样板与零件之间间隙
车削加工技术
任务一 车削成形面
二、车削橄榄手柄
3.任务评价
削橄榄手柄任务评价
车削加工技术
任务一 车削成形面
二、车削橄榄手柄
4.双手控制法车削成形面时的注意事项 ⑴用双手控制法车削成形面时,双手配合应协调、熟练。车刀切入深 度应控制准确,防止将零件局部车小。 ⑵车削球面时,要培养目测球形的能力,防止把球形车扁。 ⑶车削成形曲面时,车刀一般应从曲面高处向低处送进。为了增加零 件刚度,应先车削离卡盘远的曲面段,后车削离卡盘近的曲面段。
L 1 (D D2 d2 ) 2
式中L-圆球部分的长度(mm); D-圆球的直径(mm); d-柄部直径(mm)。
车削加工技术
任务一 车削成形面
一、双手控制法车削单球手柄
3.车刀移动速度分析 双手控制法车削圆球时,车刀刀尖在圆球不同 位置处的纵、横向进给速度是不同的。
- 1、下载文档前请自行甄别文档内容的完整性,平台不提供额外的编辑、内容补充、找答案等附加服务。
- 2、"仅部分预览"的文档,不可在线预览部分如存在完整性等问题,可反馈申请退款(可完整预览的文档不适用该条件!)。
- 3、如文档侵犯您的权益,请联系客服反馈,我们会尽快为您处理(人工客服工作时间:9:00-18:30)。
f
.工程实践培训中心
4 车削的基本方法
4.2 车外圆和台阶
示意图
车外圆
技术特点
视频演示
车外圆常须经过粗车和精车两个步骤。粗车的目的是 尽快地从毛坯上切去大部分加工余量,使工件接近于 最后形状和尺寸,粗车时,对加工质量要求不高,这 时被吃刀量应大些(约1~3mm),进给量也可取大一 些(0.8 ~1.2mm)。精车的目的是保证工件的尺寸 精度和表面质量,精车时的被吃刀量较小(0.1~ 0.3mm),进给量也较小(0.05 ~0.2mm),因此精 车时切削力较小,切削速度可大些,以提高工作效率。
3 车削加工的工艺过程及切削三要素
3.1 车削加工的工艺过程
卡盘
待加工面 加工表面 已加工面
纵向 进刀
横向 进刀
退刀
退刀
车外圆加工工艺图解
工艺过程
车削加工运动方式分为:主运动和 进给运动。主运动是指切下切槽所需要 的基本运动。就是主轴卡盘带动工件的 旋转运动。进给运动是使工件被切层连 续被切除,加工出完整表面所需的运动。 例如:加工外圆时主运动为工件转动。 进给运动为车刀的位移。要获得所需的 主运动,就必须先对车床手柄进行调整 如高低档手柄。实际转速值手柄。进给 运动分手动、自动进给两种。自动进给 时,必须将送刀方向手柄、走刀量调节 手柄调整到位置,方可进行加工。
式中:D-工件待加工面直径;n-工件转速。
要素二 要素三
走刀量S(单位:毫米/转) 工件每转一周,刀具沿进给运动方向 移动的距离。
切削深度t (单位:毫米) t=(D-d)/2
式中: D-工件待加工面直径; d-工件已加工面直径。
.工程实践培训中心
4 车削的基本方法Hale Waihona Puke 4.1 车端面示意图
技术特点
视频演示
机床组别代号(卧式车床) 机床类别代号(车床类)
其他牌号:C6132A、C616、C6140(C620)等
.工程实践培训中心
2 车床主要组成部分及其功用
2.1 车床组成部分
机床外形结构简图
编号 1 2 3 4 5 6 7 8 9 10 11
名称 变速箱 进给箱 主轴箱 床鞍 刀架 尾座 导轨 丝杠 光杆 溜板箱 收屑槽
大拖板:控制方向纵向。主要用于车削长度,刻度盘:1格=1mm. 中拖板:控制方向横向。主要用于直径深度控制,刻度盘:1格=0.02mm. 小拖板:控制方向纵向。主要用于公差长度控制,刻度盘:1格=0.02mm.
.工程实践培训中心
3 车削加工的工艺过程及切削三要素
3.2 切削三要素
要素一
切削速度V (单位:米/秒) V=nπD/1000×60米/秒
用以支承主轴及安装主轴变速机构,使之按不同的转速旋转。主轴右端有外螺纹用 以安装卡盘等附件。
床鞍 床鞍与溜板箱相联,可带动车刀沿床身导轨做纵向移动。
刀架 用来夹持车刀使其作纵向、横向或斜向进给运动。刀架可360°度旋转。
尾座
可在床身导轨上纵向移动,可固定于需要的位置上,可装夹尾顶尖以支承工件一端, 或装夹转头、铰刀等孔加工工具。
金工实训之
车削加工
昆明理工大学 工程训练中心
.
课程内容
一、理论部分 1 车床种类与牌号 2 车床主要组成部分及其功用 3 车削加工的工艺过程及切削三要素 4 车削的基本方法 5 车床安全操作规程
二、实际操作部分
1 指导教师操作示范 2 学生独立操作
.工程实践培训中心
一、理论部分
1 车床的种类与牌号
4 车削的基本方法
4.3 切槽和切断
示意图
技术特点
切断一般在卡盘上进行,工件的切断处应距卡 盘近些,以免工件振动。 切断刀刀尖必须与工件中心等高,否则切断处 将剩有凸台,且刀头也易折断(如图所示)。
视频演示
切断
切断刀安装过低 不易切削
切断刀安装过高 刀具后端易顶住工件
.工程实践培训中心
4 车削的基本方法
车削端面时,常用弯头车刀和右偏刀。弯头车刀 车端面时,中心凸台是逐步去掉的,刀尖不易损
坏,适用于车削大的端面。
切 削 力 方 向
使用右偏刀车削时,凸台是瞬间去掉的,容易损 坏刀尖,此时若吃刀量较大,在切削力的作用下, 易出现扎刀,工件产生凹心。但精车端面时可用 偏刀由中心向外进给,能提高端面的加工质量。
4.4 车锥面
示意图
技术特点
圆锥计算方法
视频演示
移动小滑板法
(1)大端直径D;(2)小端直径;(3)圆锥 角α;(4)圆锥半角α/2;(5)圆锥长度L; (6)锥度C:
1.1 车床的种类
卧式车床
立式车床
(1)按型式分 六角车床
自动车床 ……
万能车床
(2)按使用特性分
专用车床
(3)按精度分
普通车床 精密车床 高精密车床
(4)按重要性分
一般车床 大型车床 重型车床
.工程实践培训中心
1 车床的种类与牌号
1.2 车床牌号
例:C6132
基本参数(最大加工直径1/10) 机床型别代号(普通车床)
切槽
内槽
外槽 端面槽
车削精度不高的和宽度较窄的矩形沟槽,可以用刀宽等于槽宽的切槽刀,
采用直进法一次车出。精度要求较高的,一般分二次车成。 车削较宽的
沟槽,可用多次直进法切削(见图),并在槽的两侧留一定的精
车余量,然后根据槽深、槽宽精车至尺寸。
一次横向送进
二次横向送进
横向送进后纵向 送进精车槽底
.工程实践培训中心
导轨 用来保持床鞍、尾座等做纵向移动。
丝杠 联接进给箱和溜板箱的传动杆,车削螺纹时用丝杠传动。
光杆 联接进给箱和溜板箱的传动杆,自动进给时用光杆传动。
溜板箱 联接拖板和刀架,是车床进给运动的操作箱。它能使光杆或丝杠传来的旋转运动通 过齿轮或齿条带动车刀做直线进给运动。
收屑槽 收集切削屑、废料。
.工程实践培训中心
f
车台阶
车台阶实际是车外圆和车端面的组合加工。车削台阶 时,外圆先分层切除,当外径符合要求后对台阶面进 行精车。为使台阶长度符合要求,可用刀尖预先刻出 线痕,作为加工的界限。
.工程实践培训中心
4 车削的基本方法
4.3 切槽和切断
示意图
技术特点
在工件表面上车沟槽的方法叫切槽,槽的形状有外槽、内槽和端面槽
.工程实践培训中心
2 车床主要组成部分及其功用
2.2 机床各部分功用
编号 1
2
3
4 5 6
7 8 9 10
11
部分名称
功用
变速箱 安装变速机构,由电机驱动经滑移齿轮变速后由皮带传动至主轴箱,使主轴获得不 同的转速。
进给箱 主轴箱
主轴的运用由齿轮传入进给箱,再由箱内齿轮组合变速后传动光杆或丝杠,进而调 整进给量的大小,或在车螺纹时调整螺距。
.工程实践培训中心
4 车削的基本方法
4.2 车外圆和台阶
示意图
车外圆
技术特点
视频演示
车外圆常须经过粗车和精车两个步骤。粗车的目的是 尽快地从毛坯上切去大部分加工余量,使工件接近于 最后形状和尺寸,粗车时,对加工质量要求不高,这 时被吃刀量应大些(约1~3mm),进给量也可取大一 些(0.8 ~1.2mm)。精车的目的是保证工件的尺寸 精度和表面质量,精车时的被吃刀量较小(0.1~ 0.3mm),进给量也较小(0.05 ~0.2mm),因此精 车时切削力较小,切削速度可大些,以提高工作效率。
3 车削加工的工艺过程及切削三要素
3.1 车削加工的工艺过程
卡盘
待加工面 加工表面 已加工面
纵向 进刀
横向 进刀
退刀
退刀
车外圆加工工艺图解
工艺过程
车削加工运动方式分为:主运动和 进给运动。主运动是指切下切槽所需要 的基本运动。就是主轴卡盘带动工件的 旋转运动。进给运动是使工件被切层连 续被切除,加工出完整表面所需的运动。 例如:加工外圆时主运动为工件转动。 进给运动为车刀的位移。要获得所需的 主运动,就必须先对车床手柄进行调整 如高低档手柄。实际转速值手柄。进给 运动分手动、自动进给两种。自动进给 时,必须将送刀方向手柄、走刀量调节 手柄调整到位置,方可进行加工。
式中:D-工件待加工面直径;n-工件转速。
要素二 要素三
走刀量S(单位:毫米/转) 工件每转一周,刀具沿进给运动方向 移动的距离。
切削深度t (单位:毫米) t=(D-d)/2
式中: D-工件待加工面直径; d-工件已加工面直径。
.工程实践培训中心
4 车削的基本方法Hale Waihona Puke 4.1 车端面示意图
技术特点
视频演示
机床组别代号(卧式车床) 机床类别代号(车床类)
其他牌号:C6132A、C616、C6140(C620)等
.工程实践培训中心
2 车床主要组成部分及其功用
2.1 车床组成部分
机床外形结构简图
编号 1 2 3 4 5 6 7 8 9 10 11
名称 变速箱 进给箱 主轴箱 床鞍 刀架 尾座 导轨 丝杠 光杆 溜板箱 收屑槽
大拖板:控制方向纵向。主要用于车削长度,刻度盘:1格=1mm. 中拖板:控制方向横向。主要用于直径深度控制,刻度盘:1格=0.02mm. 小拖板:控制方向纵向。主要用于公差长度控制,刻度盘:1格=0.02mm.
.工程实践培训中心
3 车削加工的工艺过程及切削三要素
3.2 切削三要素
要素一
切削速度V (单位:米/秒) V=nπD/1000×60米/秒
用以支承主轴及安装主轴变速机构,使之按不同的转速旋转。主轴右端有外螺纹用 以安装卡盘等附件。
床鞍 床鞍与溜板箱相联,可带动车刀沿床身导轨做纵向移动。
刀架 用来夹持车刀使其作纵向、横向或斜向进给运动。刀架可360°度旋转。
尾座
可在床身导轨上纵向移动,可固定于需要的位置上,可装夹尾顶尖以支承工件一端, 或装夹转头、铰刀等孔加工工具。
金工实训之
车削加工
昆明理工大学 工程训练中心
.
课程内容
一、理论部分 1 车床种类与牌号 2 车床主要组成部分及其功用 3 车削加工的工艺过程及切削三要素 4 车削的基本方法 5 车床安全操作规程
二、实际操作部分
1 指导教师操作示范 2 学生独立操作
.工程实践培训中心
一、理论部分
1 车床的种类与牌号
4 车削的基本方法
4.3 切槽和切断
示意图
技术特点
切断一般在卡盘上进行,工件的切断处应距卡 盘近些,以免工件振动。 切断刀刀尖必须与工件中心等高,否则切断处 将剩有凸台,且刀头也易折断(如图所示)。
视频演示
切断
切断刀安装过低 不易切削
切断刀安装过高 刀具后端易顶住工件
.工程实践培训中心
4 车削的基本方法
车削端面时,常用弯头车刀和右偏刀。弯头车刀 车端面时,中心凸台是逐步去掉的,刀尖不易损
坏,适用于车削大的端面。
切 削 力 方 向
使用右偏刀车削时,凸台是瞬间去掉的,容易损 坏刀尖,此时若吃刀量较大,在切削力的作用下, 易出现扎刀,工件产生凹心。但精车端面时可用 偏刀由中心向外进给,能提高端面的加工质量。
4.4 车锥面
示意图
技术特点
圆锥计算方法
视频演示
移动小滑板法
(1)大端直径D;(2)小端直径;(3)圆锥 角α;(4)圆锥半角α/2;(5)圆锥长度L; (6)锥度C:
1.1 车床的种类
卧式车床
立式车床
(1)按型式分 六角车床
自动车床 ……
万能车床
(2)按使用特性分
专用车床
(3)按精度分
普通车床 精密车床 高精密车床
(4)按重要性分
一般车床 大型车床 重型车床
.工程实践培训中心
1 车床的种类与牌号
1.2 车床牌号
例:C6132
基本参数(最大加工直径1/10) 机床型别代号(普通车床)
切槽
内槽
外槽 端面槽
车削精度不高的和宽度较窄的矩形沟槽,可以用刀宽等于槽宽的切槽刀,
采用直进法一次车出。精度要求较高的,一般分二次车成。 车削较宽的
沟槽,可用多次直进法切削(见图),并在槽的两侧留一定的精
车余量,然后根据槽深、槽宽精车至尺寸。
一次横向送进
二次横向送进
横向送进后纵向 送进精车槽底
.工程实践培训中心
导轨 用来保持床鞍、尾座等做纵向移动。
丝杠 联接进给箱和溜板箱的传动杆,车削螺纹时用丝杠传动。
光杆 联接进给箱和溜板箱的传动杆,自动进给时用光杆传动。
溜板箱 联接拖板和刀架,是车床进给运动的操作箱。它能使光杆或丝杠传来的旋转运动通 过齿轮或齿条带动车刀做直线进给运动。
收屑槽 收集切削屑、废料。
.工程实践培训中心
f
车台阶
车台阶实际是车外圆和车端面的组合加工。车削台阶 时,外圆先分层切除,当外径符合要求后对台阶面进 行精车。为使台阶长度符合要求,可用刀尖预先刻出 线痕,作为加工的界限。
.工程实践培训中心
4 车削的基本方法
4.3 切槽和切断
示意图
技术特点
在工件表面上车沟槽的方法叫切槽,槽的形状有外槽、内槽和端面槽
.工程实践培训中心
2 车床主要组成部分及其功用
2.2 机床各部分功用
编号 1
2
3
4 5 6
7 8 9 10
11
部分名称
功用
变速箱 安装变速机构,由电机驱动经滑移齿轮变速后由皮带传动至主轴箱,使主轴获得不 同的转速。
进给箱 主轴箱
主轴的运用由齿轮传入进给箱,再由箱内齿轮组合变速后传动光杆或丝杠,进而调 整进给量的大小,或在车螺纹时调整螺距。