振动时效基本工艺方法样本
jbt 5926-1991 振动时效工艺参数选择及技术要求.doc

jbt 5926-1991 振动时效工艺参数选择及技术要求JB/T5926-91振动时效工艺参数选择及技术要求1991-11-30公布1992-07-01实施1主题内容与适用范围本标准规定了振动时效工艺参数旳选择及技术要求和振动时效效果评定方法.本标准适用于材质为碳素结构钢,低合金钢,不锈钢,铸铁,有色金属(铜,铝,锌其合金)等铸件,锻件,焊接件旳振动时效处理.2术语2.1扫频曲线---将激振器旳频率缓慢地由小调大旳过程称扫频.随着频率旳变化,工件振动响应发生变化.反映振动响应与频率之间关系旳曲线,称扫频曲线,如A---f称振幅频率曲线;a-f称加速度频率曲线.注:A表示振幅,a表示加速度,f表示频率.2.2激振点---振动时效时,激振器在工件上旳夹持点称激振点.3工艺参数选择及技术要求3.1首先应分析推断出工件在激振频率范围内旳振型.3.2振动时效装置(以下简称装置)旳选择.3.2.1装置旳激振频率应大于工件旳最低固有频率.3.2.2装置旳最大激振频率小于工作旳最低固有频率时,应采取倍频(或称分频)降频等措施.3.2.3装置旳激振力应能使工件内产生旳最大动应力为工作应力旳1/3~2/3.3.2.4装置应具备自动扫频,自动记录扫频曲线,指示振动加速度值和电机电流值旳功能.稳速精度应达到+lr/min.3.3支撑工件,装卡激振器和拾振器3.3.1为了使工作处于自由状态,应采纳三点或四点弹性旳支撑工件,支撑位置应在主振频率旳节线处或附近.为使工件成为两端简支或悬臂,那么应采纳刚性装夹.3.3.2激振器应刚性地固定在工件旳刚度较弱或振幅较大处,但不准固定在工件旳强度和刚度专门低旳如大旳薄板平面等部位,固定处应平坦.3.3.3悬臂装夹旳工件,一般应掉头进行第二次振动时效处理.特大工件,在其振动响应薄弱旳部位应进行补振.3.3.4拾振器应固装在远离激振器同时振幅较大处.3.4工件旳试振3.4.1不同意试振旳工件存在缩孔,夹渣,裂纹,虚焊等严峻缺陷.3.4.2选择激振器偏心档位,应满足使工件产生较大振幅和装置只是载旳要求,必要时先用手动旋钮查找合适旳偏心档位.3.4.3第一次扫频,记录工件旳振幅频率(A-f)曲线,测出各阶共振频率值,节线位置,波峰位置.3.4.4必要时通过调整支撑点,激振点和拾振点旳位置来激起较多旳振型.3.4.5测定1-3个共振峰大旳频率在共振时旳动应力峰值旳大小.3.4.6选择动应力大,频率低在共振频率作为主振频率.3.4.7按主振型对支撑,拾振位置进行最后调整.注:主振频率旳振型称为主振型.3.5工件旳主振3.5.1在亚共振区内选择主振峰峰值旳1/3-2/3所对应旳频率主振工件.3.5.2主振时装置旳偏心档位应使工件旳动应力峰值达到工作应力旳1/3-2/3,并使装置旳输出功率不超过额定功率旳80%.3.5.3进行振前扫频,记录振前旳振幅时刻(A-f)曲线.3.5.4主振工件,记录振幅频率(A-t)曲线.3.5.5起振后振幅时刻(A-t)曲线上旳振幅上升,然后变平或上升后下降然后再变平,从变平开始稳定3-5犿犻狀为振动截止时刻,一般累计振动时刻不超过40犿犻狀.3.5.6进行振后扫频,记录振幅频率(A-f)曲线.3.5.7批量生产旳工件可不作振前,振后扫频.3.5.8有些工件可作多点激振处理,有些工件可用附振频率作多频共振辅助处理.是否调整支撑点,拾振点位置视工件而定.注:主振频率以外旳各共振频率称为附振频率.3.5.9工件存在如夹渣,缩孔,裂纹,虚焊等缺陷,在振动时效中这类缺陷专门快以裂纹扩展旳形式出现时,应立即中断时效处理.工件排除缺陷后,同意重新进行振动时效.3.6振动时效工艺卡和操作记录卡3.6.1批量生产旳工件进行振动时效处理时,必须制订“振动时效工艺卡”,操作者必须严格执行并填写“振动时效操作记录卡”在工件上作已振标记.3.6.2“振动时效工艺卡”应按3.1-3.5条旳要求,试验三件以上,找出规律后制订.3.6.3“振动时效工艺卡”和“振动时效操作记录卡”旳内容和格式分别参照附录犅和附录犆.3.7铸件振动时效时,应使动应力方向尽量与易变形方向一致.3.8制订焊接件振动时效工艺时,应明确工件上承受力旳要紧焊缝和联系焊缝.振动处理中,其振动方向应使工件承受力旳要紧焊缝处旳动应力最大或较大.4振动时效工艺效果评定方法4.1参数曲线观测法4.1.1振动处理过程中从振幅时刻(A-f)曲线和振前,振后振幅频率(A-f)曲线旳变化来监测.4.1.2出现以下情况之一时,即可判定为达到振动时效工艺效果.a振幅时刻(A-t)曲线上升后变平.b振幅时刻(A-t)曲线上升后下降然后变平.c振幅频率(A-f)曲线振后旳比振前旳峰值升高.d振幅频率(A-f)曲线振后旳比振前旳峰值点左移.e振幅频率(A-f)曲线振后旳比振前旳带宽变窄.4.1.3振动处理过程中,假如不出现4.1.2条中所列旳任一情况时,应重新调整振动参数,按上述规定旳条款再进行时效处理后,重新检验.4.1.4制订有“振动时效工艺卡”旳批量生产旳工件,在振动时效时,推举用4.1.2条旳a,b款中只要出现一种情况,便可判定为达到振动时效工艺效果旳方法来检验,并不再作下述检验.4.2残余应力检测法4.2.1推举使用盲孔法,也可使且X射线衍射法.4.2.1.1被振工作振前,振后旳残余应力测定点数均应大于5个点.4.2.1.2用振前,振后旳应力平均值(应力水平)来计算应力消除率,焊件应大于30%,铸锻件应大于20%.4.2.13用振前,振后旳最大应力与最小应力之差值来衡量均化程度,振后旳计算值应小于振前旳计算值.4.3精度稳定性检测法4.3.1以要求精度稳定性为主旳工件,振后应进行精度稳定性检验.a精加工后检验.b长期放置定期检验静尺寸稳定性,在放置15d时第一次检验,以后每隔30d检验一次,总旳静置时刻半年以上.c在动载荷后检验.应依照具体情况选用上述条款.4.3.2各种检验结果均应达到设计要求.附录A振动时效工艺中动应力选择与振动时效对工件疲劳寿命阻碍分析(补充件)1振动时效工艺中动应力旳选择与分析动应力是振动时效工艺旳一项最要紧参数.实验证明:在一定范围内动应力越大,被处理工件上产生旳应变释放量也越大,消除应力旳效果也越好,动应力过大将有可能造成工件旳损伤或降低疲劳寿命.因此在本标准中以工作应力来确定动应力.即:σ动=(1/3~2/3)σ工作在设计时,工作应力(σ工作)是差不多确定旳,或和应变测试技术获得,在那个地点应以在工作状态下工件上最大应力点旳应力作为工作应力.当我们按上述方法来确定动应力(σ动)时,就能够保证被振工作既能消除应力又不遭到损坏.由于工件结构比较复杂旳结构,在不同受力状态下各点旳动应力不同,因此在实际操作时,应选择结构危险点(应力集中点),做动应力监测,以保证动应力量值旳可靠.2振动时效对工件疲劳寿命阻碍旳分析振动时效其工作状态是对工件施加周期性旳作用力,这如同疲劳荷载一样,依照线性累积损伤理论,必定对工件造成一定旳疲劳损伤.但另一方面,由于低应力振动处理后残余应力得到下降,又必定提高工件旳疲劳寿命.我国振动时效工作者,通过大量旳试验给出了振动时效对工件疲劳寿命旳关系曲线(如图A1所示).图中:N-σ为寿命-应力坐标;N-σ动为寿命-动应力坐标;σ工作为实际工作中工件中最大应力;η工作为在工作应力作用下旳疲劳寿命.从图中可见,当动应力σ动小于A点时,振动时效能够提高疲劳寿命;当动应力σ动大于A点时,振动时效将降低疲劳寿命;当采纳工作荷载处理时,振动时效降低疲劳寿命旳数值(B点)就等于振动时效处理时旳循环数.因此,本标准中选动应力为工作应力旳1/3-2/3是可不能对焊接件造成任何疲劳损伤旳,相反还能够提高工件旳疲劳寿命.。
振动时效原理 振动时效特点 振动时效工艺技术

振动时效原理振动时效特点振动时效工艺技术振动时效技术是对工件施加变化的循环载荷来消除和减少内部残余应力。
该技术具有耗能少、效果显著、无污染、处理快速等优点,广泛应用于消除焊接件、重型工件的残余应力。
振动时效原理 振动时效是用激振设备在构件残余应力集中处施加等幅交变循环激振力,构件在共振状态下获得较大的激振动应力,在某个方向上的合应力超过材料的屈服极限,该处会产生屈服变形,引起残余应力松弛并释放出来,使残余应力均匀分布。
这种方法不仅能有效地降低峰值残余应力,而且能使整体残余应力值下降。
下图为金属材料受等幅交变应变εB-εC作用时的应力应变曲线,图中OA为弹性载荷段,构件的初始残余应力为σA,ACB是第一次发生屈服变形后的应力应变曲线。
构件内的总应力超过屈服点而发生变形,在C处残余应力沿弹性卸载荷线CB'下降,经过D点后曲线偏离CB'至B点,完成一次交变应变循环。
经过多次交变循环后,曲线循环稳定为C'E'B”EC',此时残余应力由σA减小至σE,残余应力减小至稳定的过程就是振动时效宏观机理的直观表示。
要消除或减小工件中的残余应力,必须满足以下条件: (1)构件内部残余应力与激振器施加的激振动应力叠加后的总应力应超过材料屈服极限。
即σ残+σ动σs,其中:σ残为构件内部残余应力,σ动为激振动应力,σs为材料的屈服极限。
(2)随着振动时效时间的增长,构件内部的残余应力会由于发生塑性屈服而下降。
当残余应力降低到与振动应力叠加后等于新的屈服极限时,构件内的将达到平衡,使构件尺寸稳定性得到提高。
时效振动

振动时效工艺振动时效工艺的制作分以下几个部分:(1)分析工件可能出现的振型,找出合理地支撑位置,激振器装卡位置.(2)动应力的测试.(3)振动时效设备的使用.(4)残余应力和动应力测试.(1)分析:根据振动时效工件可能出现的振型,合理地支撑工件及装卡激振器的位置.(一).梁型件(如图50)多以弯振型较多,支撑一般应用4点距一端2/9和7/9处.激振器一般装卡在中间波峰附近,加速度计安装在一端的波峰附近.(二).板型件(如图51)一般采用3点(互成120度)或4点(对角)支撑再边缘处,激振器一般装卡在两橡胶垫中间边缘波峰附近,加速度计安装在一侧两橡胶垫中间边缘的波峰附近.(三).圆板型件(如图52)一般采用3点(互成120度)或4点(对角)支撑再边缘处,激振器一般装卡在两橡胶垫中间边缘波峰附近,加速度计安装在一侧两橡胶垫中间边缘的波峰附近.(四).方箱型件(如图53)一般采用3点支撑再较长的边缘处,激振器一般装卡在上边钢性较大的边缘波峰附近,加速度计安装在边缘的波峰附近.上述只是简要的介绍一般常规工件的支撑与激振器的装卡位置,具体情况还需要反复试验(利用手动工作模式)来找出合适的振动时效工艺参数.(2)动应力的测试.测试动应力所用的仪器设备: 1)动态电阻应变仪(如图54),2)测试方法 1.贴片,沿波峰--波节--波峰的振型方向依次贴6--10片.2.计算:可用虎克定律计算动应力值.(3)振动时效设备的使用:(一)准备工作:1.振动时效处理前要准备好做弹性支撑的橡胶垫(或用旧轮胎代替)。
被振工件与激振器连接用的专用卡具。
2.将被振工件水平放置在橡胶垫上。
一般情况下,要根据工件的几何形状合理地选择好支撑点? 支撑点应选择在波节处(工件在自由振动时振幅最小处)。
3.激振器的安装:将激振器安装在被振工件的被振工件的波峰处(工件在自由振动时振幅最大处)。
激振器底座与工件应刚性连接,接触面要良好。
并用专用卡具卡紧,然后将偏心调到1档。
振动时效工艺参数及设定

振动时效工艺参数及设定振动时效工艺内容和工艺参数制定原则及常用的几种振型振动时效工艺内容1,频率2,振动强度(激振力)3,处理时间4,支撑点、激振点、拾振点选择振动时效工艺参数选择原则及方法公式:δ动+δ残≥δS公式中:δ动-施加于工件的动应力δ残-工件自身存在的残余应力δS-材料的屈服极限1、频率的选择原则及方法激振频率的选择要与降低噪声相结合,尽量减少噪声对环境的污染。
残余应力集中度高,应选择大动应力,低频率振动处理。
解决弯曲变形后被校直校平的工件,必须进行多阶弯曲振动,以使应力均匀地得到释放此时选择高频率。
选择方法:根据GB/T25712-2010的机械行业标准3。
5。
1款在亚共振区内选择共振峰,峰值的1/3-2/3的对应的频率为主振频率。
激振频率的选择应注意的几点问题:工件的固有频率随构件尺寸,重量加大而降低,随材料的结构刚性加大而升高。
构件的固有频率与形状、结构有关。
构件的内部阻尼系数很小,没有明显的弹性阶段,共振带很窄,所以频率变化在±0.1HZ 振幅就会有很大的变化,所以铸造件的振动时效固有参数制定要精确。
当频率升高,电流也随之升高,可能会产生强迫振动。
强迫振动对振动时效设备和被处理的工件都有害。
由于强迫振动并非共振条件下的振动因而起不到消除或均化残余应力的作用,应尽量避免2、激振力的选择激振力是激振设备产生的周期性外力,在垂直方向对工件的作用力。
激振力选择标准(1)&动=(1/3—2/3)&工作。
按TB/T5926—91标准第3.52款,主振时装置的偏心档位应是工件的动应力峰值达到工作应力1/3—2/3,并使装置的输出功率不超过额定功率的80% 。
因为只有在工作应力的1/3—2/3处工件才不会受到损伤,同时也能提高疲劳寿命。
若&动=&工作构件不但受到损伤,而且疲劳寿命下降。
(2)动应力是使构件残余应力消除的必要条件。
在亚共振频率下,振动具有放大动应力的作用,达到加速残余应力消除的目的,为了在时效中,对构件不造成损伤,根据经验动应力可适当控制在:铸铁件±25--±40N/m㎡铸铁淬火导轨件±15N/m㎡铸刚件±35--±50N/ m㎡焊接件±50--±80N/ m㎡也可根据动态电阻应变仪测定,用公式计算。
ZS3000 振动时效 操作规程

ZS3000 振动时效操作规程一:时效准备1、按工艺要求用橡胶垫(或废旧轮胎、方木等)将工件支撑,橡胶垫的支撑位置应尽量靠近工件共振时的节线处。
2、将激振器用两个弓形卡具装夹于适当位置,位置应尽量靠近工件共振时的波峰处,弓形卡具一定要拧紧以免卡具松动,激振器掉落损坏。
3、将传感器吸紧在工件共振时的波峰处,因工件共振时可能有多个波峰,传感器和激振器尽量不要放在工件的同一个波峰处。
说明:传感器一般安装在工件刚性较弱、振动较强的位置,例如工件钢板较薄的位置或者工件的边角位置等。
4、用五芯电缆将激振器和控制箱连接,注意航空插头的方向并连接牢固。
5、用传感器线将传感器和控制箱连接。
6、根据被处理工件的重量及尺寸大小,粗略估计并调整激振器的偏心距至合适度数。
激振力调节说明:拧下激振器前段上部的堵丝,用内六方扳手通过激振器前端部旋转激振器转子到合适位置,即可从激振器前段上部的堵丝孔内插入内六方扳手,用插入的内六方扳手松开紧固螺钉,再用内六方扳手通过激振器前端部旋转激振器转子到合适位置,比如30或者60,拧紧紧固螺钉,拧上堵丝即可。
7、将控制箱电源线接好,并插入电源插座,注意本机使用220V 50~60HZ电源。
二、时效处理:1、打开控制箱开关,液晶屏幕此时显示开机界面。
2、按控制箱前面板“▼”键,进入时间设定界面,每按一下“▲”键时间增加5分钟,一般工件时间设定在20~25分钟即可。
3、按控制箱前面板“运行/停止”键,即进入并自动完成整个时效全过程,时效处理完毕设备自动停机。
若某个(些)参数不合适,彩屏会自动给出修正提示,操作者按提示调整完毕,即可再次进入时效处理过程。
4.处理完毕,屏幕显示振前和振后各种曲线和数据,按“打印”键可将彩屏上显示的a—f、a—t曲线及数据打印,以备长久保存。
5.关机。
岔管时效处理方案 - 振动时效
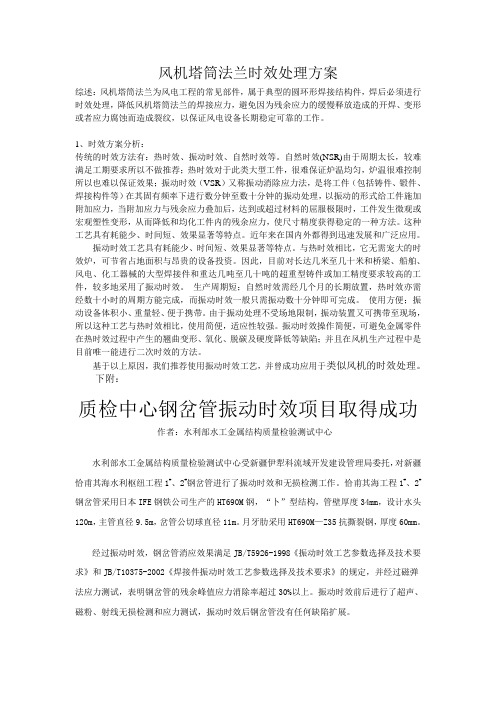
风机塔筒法兰时效处理方案综述:风机塔筒法兰为风电工程的常见部件,属于典型的圆环形焊接结构件,焊后必须进行时效处理,降低风机塔筒法兰的焊接应力,避免因为残余应力的缓慢释放造成的开焊、变形或者应力腐蚀而造成裂纹,以保证风电设备长期稳定可靠的工作。
1、时效方案分析:传统的时效方法有:热时效、振动时效、自然时效等。
自然时效(NSR)由于周期太长,较难满足工期要求所以不做推荐;热时效对于此类大型工件,很难保证炉温均匀,炉温很难控制所以也难以保证效果;振动时效(VSR)又称振动消除应力法,是将工件(包括铸件、锻件、焊接构件等)在其固有频率下进行数分钟至数十分钟的振动处理,以振动的形式给工件施加附加应力,当附加应力与残余应力叠加后,达到或超过材料的屈服极限时,工件发生微观或宏观塑性变形,从而降低和均化工件内的残余应力,使尺寸精度获得稳定的一种方法。
这种工艺具有耗能少、时间短、效果显著等特点。
近年来在国内外都得到迅速发展和广泛应用。
振动时效工艺具有耗能少、时间短、效果显著等特点。
与热时效相比,它无需宠大的时效炉,可节省占地面积与昂贵的设备投资。
因此,目前对长达几米至几十米和桥梁、船舶、风电、化工器械的大型焊接件和重达几吨至几十吨的超重型铸件或加工精度要求较高的工件,较多地采用了振动时效。
生产周期短;自然时效需经几个月的长期放置,热时效亦需经数十小时的周期方能完成,而振动时效一般只需振动数十分钟即可完成。
使用方便;振动设备体积小、重量轻、便于携带。
由于振动处理不受场地限制,振动装置又可携带至现场,所以这种工艺与热时效相比,使用简便,适应性较强。
振动时效操作简便,可避免金属零件在热时效过程中产生的翘曲变形、氧化、脱碳及硬度降低等缺陷;并且在风机生产过程中是目前唯一能进行二次时效的方法。
基于以上原因,我们推荐使用振动时效工艺,并曾成功应用于类似风机的时效处理。
下附:质检中心钢岔管振动时效项目取得成功作者:水利部水工金属结构质量检验测试中心水利部水工金属结构质量检验测试中心受新疆伊犁科流域开发建设管理局委托,对新疆恰甫其海水利枢纽工程1#、2#钢岔管进行了振动时效和无损检测工作。
振动时效.doc
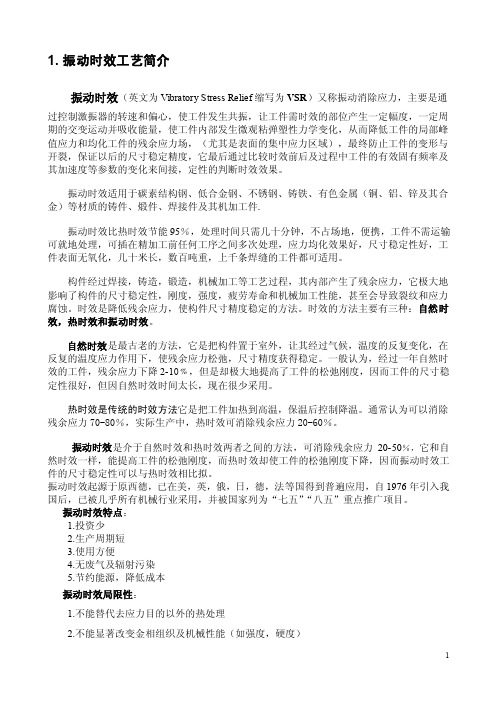
1. 振动时效工艺简介振动时效(英文为Vibratory Stress Relief缩写为VSR)又称振动消除应力,主要是通过控制激振器的转速和偏心,使工件发生共振,让工件需时效的部位产生一定幅度,一定周期的交变运动并吸收能量,使工件内部发生微观粘弹塑性力学变化,从而降低工件的局部峰值应力和均化工件的残余应力场,(尤其是表面的集中应力区域),最终防止工件的变形与开裂,保证以后的尺寸稳定精度,它最后通过比较时效前后及过程中工件的有效固有频率及其加速度等参数的变化来间接,定性的判断时效效果。
振动时效适用于碳素结构钢、低合金钢、不锈钢、铸铁、有色金属(铜、铝、锌及其合金)等材质的铸件、煅件、焊接件及其机加工件.振动时效比热时效节能95%,处理时间只需几十分钟,不占场地,便携,工件不需运输可就地处理,可插在精加工前任何工序之间多次处理,应力均化效果好,尺寸稳定性好,工件表面无氧化,几十米长,数百吨重,上千条焊缝的工件都可适用。
构件经过焊接,铸造,锻造,机械加工等工艺过程,其内部产生了残余应力,它极大地影响了构件的尺寸稳定性,刚度,强度,疲劳寿命和机械加工性能,甚至会导致裂纹和应力腐蚀。
时效是降低残余应力,使构件尺寸精度稳定的方法。
时效的方法主要有三种:自然时效,热时效和振动时效。
自然时效是最古老的方法,它是把构件置于室外,让其经过气候,温度的反复变化,在反复的温度应力作用下,使残余应力松弛,尺寸精度获得稳定。
一般认为,经过一年自然时效的工件,残余应力下降2-10﹪,但是却极大地提高了工件的松弛刚度,因而工件的尺寸稳定性很好,但因自然时效时间太长,现在很少采用。
热时效是传统的时效方法它是把工件加热到高温,保温后控制降温。
通常认为可以消除残余应力70-80%,实际生产中,热时效可消除残余应力20-60%。
振动时效是介于自然时效和热时效两者之间的方法,可消除残余应力20-50%,它和自然时效一样,能提高工件的松弛刚度,而热时效却使工件的松弛刚度下降,因而振动时效工件的尺寸稳定性可以与热时效相比拟。
振动时效
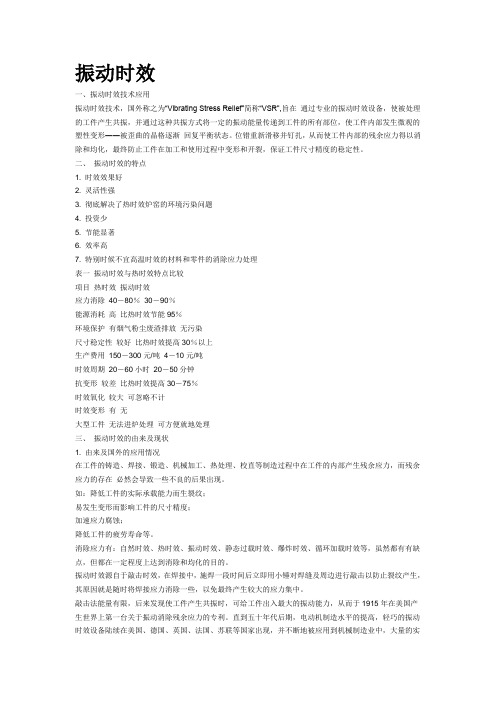
振动时效一、振动时效技术应用振动时效技术,国外称之为“Vibrating Stress Relief”简称“VSR”,旨在通过专业的振动时效设备,使被处理的工件产生共振,并通过这种共振方式将一定的振动能量传递到工件的所有部位,使工件内部发生微观的塑性变形――被歪曲的晶格逐渐回复平衡状态。
位错重新滑移并钉扎,从而使工件内部的残余应力得以消除和均化,最终防止工件在加工和使用过程中变形和开裂,保证工件尺寸精度的稳定性。
二、振动时效的特点1. 时效效果好2. 灵活性强3. 彻底解决了热时效炉窑的环境污染问题4. 投资少5. 节能显著6. 效率高7. 特别时候不宜高温时效的材料和零件的消除应力处理表一振动时效与热时效特点比较项目热时效振动时效应力消除40-80%30-90%能源消耗高比热时效节能95%环境保护有烟气粉尘废渣排放无污染尺寸稳定性较好比热时效提高30%以上生产费用150-300元/吨4-10元/吨时效周期20-60小时20-50分钟抗变形较差比热时效提高30-75%时效氧化较大可忽略不计时效变形有无大型工件无法进炉处理可方便就地处理三、振动时效的由来及现状1. 由来及国外的应用情况在工件的铸造、焊接、锻造、机械加工、热处理、校直等制造过程中在工件的内部产生残余应力,而残余应力的存在必然会导致一些不良的后果出现。
如:降低工件的实际承载能力而生裂纹;易发生变形而影响工件的尺寸精度;加速应力腐蚀;降低工件的疲劳寿命等。
消除应力有:自然时效、热时效、振动时效、静态过载时效、爆炸时效、循环加载时效等,虽然都有有缺点,但都在一定程度上达到消除和均化的目的。
振动时效源自于敲击时效,在焊接中,施焊一段时间后立即用小锤对焊缝及周边进行敲击以防止裂纹产生,其原因就是随时将焊接应力消除一些,以免最终产生较大的应力集中。
敲击法能量有限,后来发现使工件产生共振时,可给工件出入最大的振动能力,从而于1915年在美国产生世界上第一台关于振动消除残余应力的专利。
- 1、下载文档前请自行甄别文档内容的完整性,平台不提供额外的编辑、内容补充、找答案等附加服务。
- 2、"仅部分预览"的文档,不可在线预览部分如存在完整性等问题,可反馈申请退款(可完整预览的文档不适用该条件!)。
- 3、如文档侵犯您的权益,请联系客服反馈,我们会尽快为您处理(人工客服工作时间:9:00-18:30)。
振动时效基本工艺方法
绵阳市重力机电设备有限公司 -12-05 15:06:28 作者:SystemMaster 来
源: 文字大小:[大][中][小]
振动时效基本工艺方法
振动时效的效果是经过正确的工艺方法来实现的, 工艺方法包括振动频率的选择, 激振点及支承点和振动时间确定等。
RSR ( G) 系列具备高度智能化的专家级软件系统, 能完全自动完成振动时效工艺的整个电控过程, 包括主振和副振频率的选择, 时效处理的时间确定和区分不同类型结构件的工艺过程等, 能提供相当准确的加工资料和符合标准的曲线。
可完全消除人为误差和避免因操作疏忽而造成不可挽回的损失。
由于在实际运用中, 不同的结构件有着不同的工艺方法, 经验的积累是完成工艺工作必不可少的事, 在本篇中介绍的基本工艺方法可供参考。
但要提醒各位的是RSR ( G) 系列完善的软件控制系统具备在各种情况下( 包括外部工艺即激振点和支承点选择不适当) 可自动调节完成振动时效工艺过程的电控操作过程, 而且取得最佳的处理效果。
以下就振动时效工艺的基本方法简要介绍, 供在实际操作中使用手动和半自动时的参考。
一、基本工艺参数
1、振动频率的选择
振动时效是在激振器所产生的周期性外力——激振力的作用下在某一频率使金属结构件共振, 产生足够的动应力来致使内部残余应力消除或匀化来达到时效目的。
每一种金属结构件均有几种不同振型的共振频率, 与结构件本身的形状、重量、材质和结构钢性等因素有关。
振动时效设备在一定的频率范围内经过扫频可检测出不同振型的数个共振频率( 即出现振动最大的峰值频率) , 在正常情况下
RSR ( G) 会自动选择最佳的共振频率为主振频率( 其振型称为主振振型) , 为补充主振振型的不足, 在5%的情况下还需选择与主振型不同的另一次低共振频率为附振频率( 其振型称为附振振型) 。
RSR ( G) 系列设备对主振频率和附振频率的选择是由软件完成的, 其选择准确性高而且避免了人为因素造成的加工效果不佳等。
对于某些特殊结构件, 可能其共振频率超出了设备的频率范围, 此时可选择大激振力的设备( 如3508) 采用”分频法”——即在一阶共振频率的对应1/3和1/5等频率上对工件进行时效处理。
2、振动幅值的选择
时效处理的振动一般选择在亚共振区, 亚共振区即共振峰值的前沿对应最大振动幅值的
1/3-2/3处。
选择亚共振区进行时效处理, 不会对结构件造成任何疲劳损伤, 相反还会提高工件的疲劳寿命( 具体见JB/T9526) 。
RSR ( G) 经过自动分析软件自动选择振幅, 在时效加工过程中自动检测振幅的变化, 实现自动频率调节控制振幅。
3、激振力的确定
激振力的大小是经过工件承受动应力值大小来衡量的, 是振动时效工艺的一个重要参数, 直接影响振动时效的效果, RSR ( G) 系列经过改变偏心轮的偏心距即可调节激振力大小( 即施加于结构件的动应力的大小) 。
RSR系列设备用加速度值间接反映动应力值的大小, 一般来说动应力大则相应的加速度大, 对于不同的结构件在时效处理时对动应力的要求不一样, 主要结构件的激振力可参照下表所列的主振频率和附振频率的加速度峰值来进行。
激振力调节对应加速度选择表:
在有条件的情况下我们也可用动态电阻应变仪来实际测量动应力, 用以确定激振力的大小, 有关数据的表明, 在共振频率下, 最佳动应力为: 焊接结构件为0.07-0.10KN/mm2, 铸铁件不小于0.015KN/mm2。
RSR ( G) 系列的激振力为轮式无级调节方式, 用户可根据实践来选择合适的激振力, 还可根据计算公式来确定激振力的大小:
F=(Q/G)ω2rsin(ωt)
F—激振力( KN) Q—偏心环重( kg/100)
G—重力加速度ω—角速度 r—偏心距( mm)
4、激振点和支撑点的选择
当金属结构件以某种振型的共振频率振动时, 其振动值最大处称为波峰, 最小处称为波节( 也称为节线或节点) 。
正确的选择方法是以主振频率的振型为主, 兼顾辅振频率的振型, 激振器夹持在工件振峰处。
支承点尽可能选择在振动的波节处, 传感器则应放在远离激振器的另一波峰处。
下图为一梁形工件的工艺安装示例。
注意: 工件放置于支承体上, 应保持水平稳定, 激振器夹持面应平整, 保证底部与工件可靠的面接触。
支承体应选择有一定弹性的材料( 如橡胶、轮胎、泡沫塑料和木材等) , 超大型工件还能够选择较松软的土地, 以减少工件——支承——地基三者之间的刚性行击。
如何寻找和确定工件的波峰和波节, 常见的方法是:
( 1) 撒沙法
工件在共振频率上激振时, 如果在工件平面的各部位撒一些干沙, 观察沙粒振动形成的状态: 沙子集聚在
位置为波节, 跳动激烈点为波峰。
( 2) 传感器测试法
将传感器依次放在工件不同的位置上, 观察加速度值的大小, 最大值处为波峰, 最小值处为波节。
确定主振频率( 即主振振型) 的波峰和波节的位置后, 再按激振点及支承点的选择原则调整支承和激振器的位置, 这样可获得最佳的振动效果。
RSR ( G) 系列由于具备高度智能化的专家级软件系统, 因此只要基本符合主振频率( 主振振型) 的工艺即可, 要求并不很高, 即使工艺准确性不够软件也会自动判断效正, 一般情况下, 可不必考虑作为补充的辅振频率( 辅振振型) 的激振点和支承点位置是否准确等情况, 即可完成多振型处理的全自动过程。
5、激振时间的确定
在振动时效的处理过程中, 随着残余应力的降低和匀化, 工件的共振频率及振幅( 或动应力) 等均随之变化当残余应力的降低和匀化过程完成后, 这些参数也随之稳定, 这样振动时效的时间可由这些参数的变化情况来确定。
RSR ( G) 系列完全摒弃了手动操作, 而且其高度智能化的软件系统保证了全自动工艺过程的完成, 适应各种恶劣的工作环境, 因此完全避免了人为误差, 特别是杜绝了生产过程中弄虚作假的情况, 为产品的质量检验提供了可靠的依据。
二、工艺操作和调试
1、初调准备
RSR ( G) 系列产品采用木箱包装, 控制器包装箱采用了防震措施, 但在经过长途运输后, 为防止意外, 设备开箱时需进行检查和试机。
具体步骤如下:。