机械式自动变速器换挡过程标定系统设计
电控机械式自动变速器换挡过程控制

3 试验分析
AM T 换挡过程控制试验是在桑塔纳 2000 轿
车上进行的。 图 6 为没有进行换挡过程控制的传统 换挡过程图, 图 7 为改进后的换挡过程控制。
图 3 离合器分离与接合速度
11
挡 21
挡 31
挡 41
挡 51
挡
213 离合器的控制
离合器控制的好与坏, 决定汽车起步、 换挡过程 的品质。 实现离合器的最佳控制可以减小传动系统 零部件冲击, 提高其使用寿命与乘坐舒适性。 图4 为 离合器控制系统框图, 由此可实现图 3 所示的离合 器分离与接合速度的精确控制[ 5 ]。
收稿日期: 2001 12 24 3 国家 “九五” 科技重点攻关项目 ( 项目编号: 96A 050401) 郭立书 吉林大学汽车学院 博士生, 130025 长春市 葛安林 吉林大学汽车学院 教授 博士生导师 张 泰 青岛建筑工程学院机械学院 副教授, 266033 青岛市 岳英杰 装甲兵技术学院车辆工程系 副教授, 130117 长春市
( 2)
式中 J m ax ——乘坐满意的冲击度最大值 即
M Rw dT c ≤J m ax i 0 ig Γ dt
( 3)
式中 T e ——发动机净输出扭矩 I e、 角速度 Ξe ——发动机转动惯量、 整理式 ( 8) 得 d Ξe ( 9) T c= T e- I e dt 换挡前, 式 ( 9 ) 中 T e 可以通过发动机稳态扭矩
© 1995-2004 Tsinghua Tongfang Optical Disc Co., Ltd. All rights reserved.
离合器位 移传感器 挡位信号 制动信号 发动机转速 控制 单元 电磁阀 离合器 液压缸
机械式AT变速器换挡过程标定系统设计
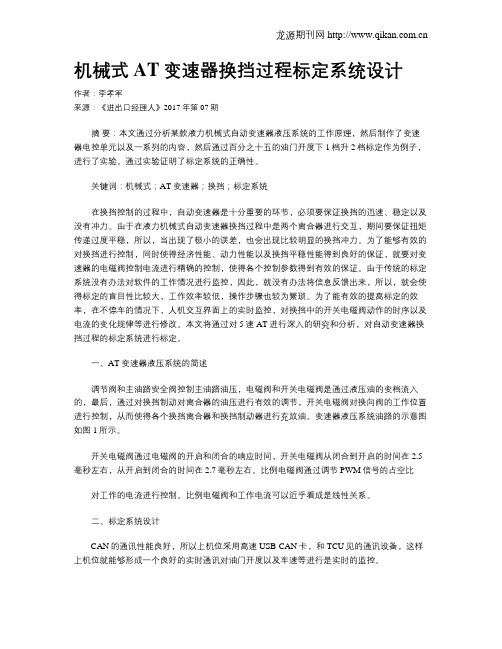
机械式AT变速器换挡过程标定系统设计作者:李孝军来源:《进出口经理人》2017年第07期摘要:本文通过分析某款液力机械式自动变速器液压系统的工作原理,然后制作了变速器电控单元以及一系列的内容,然后通过百分之十五的油门开度下1档升2档标定作为例子,进行了实验。
通过实验证明了标定系统的正确性。
关键词:机械式;AT变速器;换挡;标定系统在换挡控制的过程中,自动变速器是十分重要的环节,必须要保证换挡的迅速、稳定以及没有冲力。
由于在液力机械式自动变速器换挡过程中是两个离合器进行交互,期间要保证扭矩传递过度平稳,所以,当出现了极小的误差,也会出现比较明显的换挡冲力。
为了能够有效的对换挡进行控制,同时使得经济性能、动力性能以及换挡平稳性能得到良好的保证,就要对变速器的电磁阀控制电流进行精确的控制,使得各个控制参数得到有效的保证。
由于传统的标定系统没有办法对软件的工作情况进行监控,因此,就没有办法将信息反馈出来,所以,就会使得标定的盲目性比较大,工作效率较低,操作步骤也较为繁琐。
为了能有效的提高标定的效率,在不停车的情况下,人机交互界面上的实时监控,对换挡中的开关电磁阀动作的时序以及电流的变化规律等进行修改。
本文将通过对5速AT进行深入的研究和分析,对自动变速器换挡过程的标定系统进行标定。
一、AT变速器液压系统的简述调节阀和主油路安全阀控制主油路油压,电磁阀和开关电磁阀是通过液压油的变档流入的,最后,通过对换挡制动对离合器的油压进行有效的调节,开关电磁阀对换向阀的工作位置进行控制,从而使得各个换挡离合器和换挡制动器进行充放油。
变速器液压系统油路的示意图如图1所示。
开关电磁阀通过电磁阀的开启和闭合的响应时间,开关电磁阀从闭合到开启的时间在2.5毫秒左右,从开启到闭合的时间在2.7毫秒左右。
比例电磁阀通过调节PWM信号的占空比对工作的电流进行控制。
比例电磁阀和工作电流可以近乎看成是线性关系。
二、标定系统设计CAN的通讯性能良好,所以上机位采用高速USB-CAN卡,和TCU见的通讯设备,这样上机位就能够形成一个良好的实时通讯对油门开度以及车速等进行是实时的监控。
自动变速器换挡控制系统PPT课件
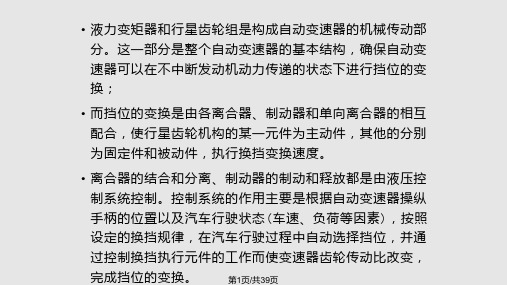
2.主油路油压
• 主油路油压由油压电磁阀控制产生。
• 油压电磁阀是一种线性脉冲式电磁阀,电控组件根据节 气门位置传感器测得的节气门开度,计算并控制油压电 磁阀的脉冲信号占空比,借以改变油压电磁阀泄油口的 大小,产生随节气门开度变化的节气门油压。
• 节气门开度越大,脉冲信号占空比越小,油压电磁阀的
第32页/共39页
5.发动机制动作用的控制
电子控制自动变速器的强制离合器或强制制动器 (为利用发动机的制动作用而设置的执行元件)的工作是 由电子控制单元通过电磁阀来控制。
电子控制单元按照设定的发动机制动控制程序,在操 纵手柄位置、车速、节气门开度等因素满足一定条件(如: 操纵手柄位于前进低挡位置,且车速大于10km/h,节气 门开度小于1/8)时,向强制离合器电磁阀或强制制动器 电磁阀发出电信号,打开强制离合器或强制制动器的控制 油路,使之接合,使自动变速器具有反向传递动力的能力, 从而在汽车滑行时实现发动机制动。
• 多功能开关装在变速器壳体的操纵手柄上,由变 速杆进行控制,故有时也被称为档位开关。
• 主要功能:
指示选档操纵手柄位置 倒档信号灯的开启 空档起动
第13页/共39页
(三)电磁阀的结构和原理
• 电液式自动变速器使用电磁阀作为控制系统的执行器,通过电磁阀控制液压系统中的换档阀,以使离合器、 制动器等执行元件工作,从而实现自动换档。
• 通电,电磁阀使阀芯或滑阀开启泄油孔,压力下 降;不通电,在弹簧力作用下阀芯或滑阀关闭泄 油孔,压力上升。
• 占空比:在一个脉冲周期内,通电的时间为A,断 电的时间为B,则占空比=A/(A+B)×100%, 其变化范围在0~100%。
第18页/共39页
机械式自动变速器选换挡系统设计及试验研究的开题报告

机械式自动变速器选换挡系统设计及试验研究的开题报告
一、选题背景
随着汽车行业的快速发展,机械式自动变速器已经成为了新一代汽车的标配之一。
机械式自动变速器通过改变不同齿轮之间的传动比来达到车辆的变速,能够满足不同
速度和转矩要求,提高行车的平稳性和舒适性。
目前,机械式自动变速器的选换挡系统是由机械结构和液压控制系统相结合实现的。
然而,在实际应用过程中,由于液压控制系统的故障或者机械结构的设计不合理
等因素可能导致选换挡不及时或者不准确,从而影响驾驶安全和车辆性能。
因此,本文旨在探究机械式自动变速器选换挡系统设计的优化策略,通过试验研究验证设计方案的可行性和有效性。
二、研究内容和方法
本文将从以下几个方面展开研究:
1.机械式自动变速器选换挡系统的设计:通过分析传动系统的结构和工作原理,研究选换挡系统的设计,并优化其结构和参数。
2.选换挡系统的试验研究:采取实验室试验和道路试验相结合的方法,对优化后的选换挡系统进行测试,并对实验结果进行分析和总结。
3.验证设计方案的可行性和有效性:以选换挡时间、精度和稳定性为评价指标,对比优化前后的选换挡效果,验证设计方案的可行性和有效性。
三、预期成果
1.机械式自动变速器选换挡系统的设计方案。
2.选换挡系统的试验结果及数据分析报告。
3.设计方案的可行性和有效性认证报告。
四、研究意义和应用价值
本文研究能够提高机械式自动变速器选换挡系统的选换准确性和可靠性,提高汽车的安全性和行驶舒适性,对于汽车行业具有重要的实用价值和推广应用价值。
AMT自动换挡变速系统设计

AMT自动换挡变速系统设计摘要:介绍了一种以Freescale(飞思卡尔)MC9S12DJl28Mw 为核心的嵌入式AMT 系统。
说明了该系统的工作原理、技术特点以及应用状况。
同时还讲述了其硬件结构和软件设计思想。
关键词:AMT;MCU;嵌入式单片机O 引言随着现代汽车工业的迅猛发展,节能环保,低排放,高效舒适,不可质疑地被推为汽车设计首要指标。
在各种类型的自动档变速器中,电控机械式自动变速器(Automated Mechanical Transmission,以下简称AMT),具有传动效率高、结构紧凑、成本低、易于制造、工作可靠及操纵方便等优点,尤其是其省油的特点适合于我国大、中巴与载重车应用。
比其它自动档变速器节油9%以上。
本文介绍一种以Freeseale(飞思卡尔)MC9S12DJl28MW 为核心的嵌入式AMT 系统。
1 AMT 自动换挡变速系统简介该系统是一种集机械、电子、液(汽)压为一体的自控系统。
由信号采集单元采集发动机的工作状态、车辆行驶速度状态、油门状态、刹车状态等。
集成电子控制单元相对各信号源进行分析、处理、并发出指令,执行机构完成相应动作,从而实现自动换挡。
匹配过程简单,并能在满足发动机排放的要求下很好的与整车同时满足气体排放要求。
始终使整车性能处于最佳状态,具有机械继承性强,传动效率高,燃油经济性高,操作简单等优点。
同时该系统还有自我诊断功能,在系统出现故障时显示故障信息代码,提示驾驶员的注意,便于维护人员进行修理。
2 AMT 自动换挡变速器系统组成及工作原理2.1 组成AMT 自动换挡变速系统是在传统的固定式的变速箱和干式离合器的基础上,加装相应的电气执行机构,传感器,电子控制单元等组成。
系统框图如图1 所示,AMT 自动换挡变速系统包括:MCU 数据处理系统;信号采集系统(发动机转速、车速等);选。
机械式自动变速器换挡过程标定系统设计

机械式自动变速器换挡过程标定系统设计机械式自动变速器是一种常见的汽车传动装置,它通过齿轮的转动来实现不同档位之间的换挡。
为了提高变速器的性能和可靠性,需要对其进行标定,以确保换挡过程的流畅性和准确性。
本文将介绍一种机械式自动变速器换挡过程标定系统的设计方案。
一、系统架构机械式自动变速器换挡过程标定系统由传感器、控制器、执行器、电源、显示器等组成。
其中,传感器用于检测齿轮的位置和速度,控制器负责读取传感器信号并控制执行器动作,执行器则根据控制器指令实现换挡动作,电源为系统提供能量供给,显示器用于显示系统运行状态和换挡结果。
二、传感器设计传感器是整个系统的核心部件,它的准确度和灵敏度直接影响到系统的性能表现。
为了实现齿轮位置和速度的实时监测,我们选择使用霍尔传感器和编码器。
霍尔传感器通过检测齿轮旋转时的磁场变化来确定齿轮的位置,编码器则通过齿轮上的齿条使传感器处于正弦波输出。
这种设计不仅能够实现高精度的齿轮测量,而且具有较高的抗干扰能力和可靠性。
三、控制器设计控制器主要用于读取传感器信号并控制执行器动作。
为了实现快速、准确的换挡,我们采用了嵌入式系统设计方案。
具体来说,我们使用了基于ARM微处理器的控制器,配合低功耗高性能的嵌入式实时操作系统。
该系统具有强大的计算和控制能力,能够实现高速、高精度的换挡操作。
四、执行器设计执行器是实现换挡的关键部件,它包括电磁阀、液压缸等,能够实现快速、精准的换挡操作。
具体上,我们采用了一组电磁阀和液压缸,电磁阀用于控制液压缸的活塞运动,从而实现换挡动作。
该设计方案具有响应速度快、稳定性好的特点,能够有效提高变速器性能和可靠性。
五、电源设计电源主要用于为系统提供能量供给,我们选用了12V直流电源,使系统具有低功耗、高效率等特点。
同时,为了保证电源的稳定性和可靠性,我们还设计了过压、过流保护等功能,以避免意外事故和设备损坏。
六、显示器设计为了方便系统的维护和操作,我们设计了一个液晶显示器。
基于CCP的机械自动变速器控制单元标定系统

标定变量数据到内存。监测模块主要是负责监测任劳的 处理,启动或停止监测量数据的传输,在监测窗口显示 或者暂停显示接收到的监测量数据,对监测量历史
数据进行离线分析以及将监测量数据保存到磁盘监测量 数据文件。通倍模块主要是负责为PC机与ECU电控单元之 间的通倍提供接口。标定页面包括图形标定
窗口、表掐标定窗口和监测窗口。可以对表掐中的数字 进行改动编辑;在二维图形标定窗口中,可以用鼠标对 曲线进行拖拽改动;这些窗口,只要对其中任意一
寄存器,验收码和验收屏蔽寄存器,总线定时寄存器以 及输出控制寄存器;CCP协议的初始化包括数据获取DAQ 的配置(数据缓冲区的设置)以及各命令的
程序实现。6结束语标定系统是汽车电子控制系统开发的 重要工具。本文介绍的是…个面向汽车机械式自动变速器 控制单元的标定系统,具1242006.0
8计算机工程与应用有参数标定和实时检测功能,有良好 的标定操作界面。最大特点是具有直接拖动曲线的功能, 使标定MAP图时更直观;最后自动生成对应
和ECU中通倍控制程序的编写,主要是CCP协议的实现以 及独立CAN控制器SJA1000的驱动。3.2系统硬件结构系统 硬件总体结构如所示。根据
AMT系统的功能需求,下位机主控制器选用80C196KCkc, 80C196KC单片机是一个68引脚式大规模集成电路芯片。 其功能强,性能/价掐
比高,使用方便。由于其没有CAN接口,所以采用独立 CAN控制器SJA1000来完成CAN通倍。采用PCA82C250收发 器来进行CAN通倍的
的组织,只要上位机有数据获取命令下来,CCP协议驱动 器就会连续的将DAQ列表中的数据发送给上位机,这样就 实现了对ECU中数据的监测。CCP协
议提供的通倍服劳主要包括通倍连接(上接102页)5系 统下位机ECU中的程序是AMT控制程序的一个中断处理程 序,在AMT运行过程中若上位机有通
车辆自动变速器构造原理与设计方法课件:自动变速器换档控制系统 -

换挡控制 主油路油压控制 模式选择控制 锁定离合器控制 发动机制动控制 改善换挡感觉控制 输入轴转速传感器控制 故障诊断和失效保护控制
换挡电磁阀A 换挡电磁阀B 锁定正时电磁阀 锁定电磁阀 主油路油压电磁阀
指示灯显示诊断故障码
圖7.15 自動變速器電控系統組成
❖ 1.換檔控制
❖ 換檔控制是指自動變速器換檔時刻控制,即當汽車行駛速度 達到一定車速時,使自動變速器自動升檔或降檔。
圖7.8車速感測器的工作原理 1—停車鎖定齒輪;2—車速感測器;3—永久磁鐵;4—感應線圈;5—電控組件
❖ 3.工作油溫度感測器
工作油溫度感測器安裝在自動變速器油底殼 內的液壓閥體上,用於檢測工作油的溫度, 電控組件根據工作油溫度等信號進行換檔控 制,油壓控制和鎖
定離合器控。
❖ 工作油溫度感測器
的安裝位置及電阻
❖ 4.鎖止離合器控制 ❖ 自動變速器鎖止離合器的接合和分離是由電控組件橾縱鎖定
電磁閥來完成的。 ❖ 5.發動機制動控制 ❖ 以3行星排辛普森式4檔行星齒輪變速器和雙行星排辛普森式
4檔行星齒輪變速器 為例。 ❖ 6.改善換檔品質控制 ❖ 自動變速器改善換檔品質控制有以下幾種方法,即換檔油壓
控制、減扭矩控制和N-D換檔控制。 ❖ 7.輸入軸轉速感測器控制 ❖ 自動變速器電控組件根據輸入軸轉速感測器的電信號可以檢
❖ 2.主油路油壓控制
❖ 當代轎車電子控制自動變速器的電液式控制系統已經取消了 由節氣門拉線控制的節氣門閥,主油路油壓由一個油壓電磁 閥控制產生。
❖ 3.自動模式選擇控制
❖ 自動變速器選擇不同的驅動模式,可以滿足不同的使用要求。 在經濟模式中,可以在獲得良好的燃油經濟性的情況下進行 換檔,換檔車速較低,動力性能發揮稍差。在動力模式中, 可以在發揮較好動力性能的情況下進行換檔。在標準模式中, 可以同時兼顧動力性和經濟性的發揮。目前新型自動變速器 的控制系統由電控組件進行控制,可以取消模式選樣開關, 由電控組件自動進行模式選擇控制。
- 1、下载文档前请自行甄别文档内容的完整性,平台不提供额外的编辑、内容补充、找答案等附加服务。
- 2、"仅部分预览"的文档,不可在线预览部分如存在完整性等问题,可反馈申请退款(可完整预览的文档不适用该条件!)。
- 3、如文档侵犯您的权益,请联系客服反馈,我们会尽快为您处理(人工客服工作时间:9:00-18:30)。
从图中可知,在正常工作区域,该变速器中比例电磁
阀输出油压与其工作电流近似成线性关系。
饱和区 1.0
控 制 油 压/MPa
0.8
0.6
线性区
0.4
CAN 卡
TCU
0.2 控制 死区
0 0 0.5 1.0 1.5 2.0 2.5 3.0
图 5 标定系统结构
3.1 TCU 硬件设计
工 作 电 流 /A 图 3 比例电磁阀工作特性曲线
0 0 5 10 15 20 25 30 时 间 /ms
图 2 开关电磁阀动态响应特性
点的信号,如油门开度、车速等信号,从而高效、实时
地监控车辆的运行状态。
上位机
试验车辆
比例电磁阀的工作电流通过调节 PWM 信号的
占空比来控制,如图 3 为当主油路油压为 1 MPa 时
测得的比例电磁阀输出油压与其工作电流间关系。
充油油压。
电 流/A
1.5 1.0 0.5
0 113.6
114.0
电 流/A
1.5 1.0 0.5
0
113.6
114.0
114.4 114.8 时 间 /s
(a)SLU 阀
115.2
114.4 114.8 时 间 /s
(b)SLT 阀
115.2
115.6 115.6
—7—
·设计·计算·研究·
电 流/A
主题词:自动变速器 换挡品质 标定系统 设计 中图分类号:U463.212 文献标识码:A 文章编号:1000-3703(2012)05-0005-04
Design of Calibration System for AMT Shifting Process
Sun Lu1, Wu Guangqiang1,2, Wang Leilei1, Wen Dongsheng1 (1. Tongji University; 2. Tokyo University)
主油路安全阀
主油压调节阀 油路其它部分
W
油泵 W
比例电磁阀
P R ND W
换向阀
W
滤清器 换挡杆
换挡制动器
W
换挡离合器
开关电磁阀
图 1 液压油路示意
觹 基金项目:国家自然科学基金资助项目(51175379) 2012 年 第 5 期
—5—
·设计·计算·研究·
开关电磁阀的动态特性是指电磁阀由开启到闭 滤波,C2、R2 和 R3 构成 RC 滤波电路。
TCU 系统的整体结构如图 6 所示。
比例电磁阀驱动电路原理如图 4 所示, 比例电
磁阀驱动芯片采用 BTS5090。
GND 1
PWM0 2 3 4 5
PB0 6 7
U1
Vs
GN OUT0
DIN0 OUT0
DENOUT0
IS
NC
DSEL
OUT1
IN1
NC
OUT1 OUT1
BTS5090
+12V
GND
是 重新校验? 否
校验成功?
否 报错提示
是 通知 TCU 修改内部参数
修改成功? 是
实车运行
否 报错提示
图 8 上位机程序结构
开始
检测 CAN 网络中上位机发给 TCU 的指令
否 收到上位机指令?
是 根据 CAN 协议对接收到的信号进行解码
将解码后的信号发到接收数组中
收到校验指令?
否
是 将接收到的数据发回上位机
素的影响,所以,对电磁阀工作电流的研究可以转化
为对采样电阻两端电压的研究。 但由于采样电阻两
端电压较小,不能由微处理器模拟采样口直接处理,
故 本 文 采 用 固 定 增 益 为 20 倍 的 差 分 放 大 器
AD8200 对其进行放大, 同时为了降低高频噪声的
干扰,设计低通滤波电路。 AD8200 和 C1 构成 1 阶
15 14 GND 比例阀 SLS 13 D1
R2 C2 R3 U2
5 OUT A2 4
12
SLS
6 +VS A1 3
11
+5ห้องสมุดไป่ตู้ 7 NC GND 2
10
S1
SLSG 8 +IN -IN 1
9
8
D2 开关阀 S1
GND
AD8200 采样电阻 R1
PAD1 C1
GND GND
GND
图 4 驱动电路原理
Key words:Automatic transmission,Shifting quality,Calibration system,Design
1 前言
换挡过程控制是自动变速器的关键技术, 它要 求换挡迅速、平稳、无冲击。 在液力机械式自动变 速 器 中 , 电 磁 阀 工 作 频 率 约 300 Hz, 所 以 微 小 的 控 制 误 差 也 会 导 致 明 显 的 换 挡 冲 击[1,2]。 为 了 实 现 对换挡过程的精确控制,满足动力性、经济性和换 挡平顺性的要求, 必须对变速器电磁阀控制电流 进行精确的实车在线匹配标定, 以确定各项控制 参数。 传统的标定系统往往无法有效监控软件的 执行状况并对反馈信息进行协同处理来定位关键 参数,所以标定时常带有较大的盲目性,且操作繁 琐,效率低下。 为提高标定效率,可在不停车情况 下通过具有良好人机交互界面的上位机实时监控 车辆状态, 并对换挡过程中开关电磁阀的动作时 序、 比例电磁阀工作电流变化规律等参数进行在 线 修 正 。 本 文以某 5 速 AT 作为研究对象,开发自动
否 收到参数修改指令?
是 将 接 收 数 组 中 数 据 写 入 Flash 中 指 定 位 置
将写入 Flash 中的数据与接收数组中数据校验
校验成功?
否 通知 TCU 修改失败
是 通知上位机修改成功
返回
图 9 下位机程序结构 2012 年 第 5 期
标定程序的操作系统主要有 2 个模块, 分别为 电磁阀标定模块和加速度模块。 在电磁阀标定模块 中, 显示开关电磁阀的动作时序和比例电磁阀的目 标电流;在加速度模块中,可实时显示整车纵向加速 度信号和采样电阻电压信号, 并将采样电阻电压信 号转换为电磁阀的电流进行存储。
·设计·计算·研究·
机械式自动变速器换挡过程标定系统设计 *
孙 鲁 1 吴光强 1,2 王雷雷 1 温东生 1 (1.同济大学;2.东京大学)
【摘要】分析了某款液力机械式自动变速器液压系统的工作原理及其电磁阀特性,设计制作了变速器电控单 元 (TCU),制定上下位机 CAN 通信协 议,编 写 下 位 机 flash 控 制 代 码 ,开 发 了 基 于 LabVIEW 的 标 定 系 统 上 位 机 软 件 ,并 以 15% 油门开度下 1 挡升 2 挡标定为例进行了实车试验。 结果表明,该变速器换挡最大冲击度降到了 8.34 m/s,相 对标定前降低了约 63% ,从而验证了标定系统的正确性。
4 实车试验
试验以车辆在 15%油门开度、平直柏油路面下 的 1 升 2 挡为例,对换挡过程进行实车在线标定。
图 10 为 车 辆 标 定 前 的 一 次 1 升 2 挡 中 SLU 阀 、SLT 阀 和 SLS 阀 的 电 流 信 号 和 整 车 纵 向 加 速 度信号。 从图中可知,该次 1 升 2 挡中最大冲击度 为 22.59 m/s3,且冲击出现在换挡过程前半段。 由换 挡过程分析可知,造成该次冲击的主要原因是变速 器制动器接合过早。 SLU 阀控制 1 升 2 挡中制动器 的减压调节阀,而减压调节阀控制输出油压与 SLU 阀工作电流成反比, 所以 冲 击 是 由 于 SLU 阀 工 作 电流过小而导致的。 SLS 阀控制换挡支路的油压, 且 SLS 阀的油压与工作电流成反比,所以可以认为 预 充 油 阶 段 SLS 阀 的 工 作 电 流 较 小 造 成 制 动 器 接 合过快。 因此,应适当提高换挡前阶段 SLU 阀的工 作电流以降低制动器的结合油压,适当提高 SLS 阀 在制动器预充油阶段的工作电流以降低制动器的预
图 7 实车试验中的 TCU
—6—
汽车技术
·设计·计算·研究· 3.2 标定系统上、下位机软件设计
标定系统上、下位机程序结构分别如图 8 和图 9 所示。
开始
初始化设备
启动设备
设备启动成功?
否
是
初始化变量
检查设备
修改需要标定的参数
向 TCU发送修改后的参数
否 发送成功?
是
发送握手校验信号
接收 TCU 发上来的信号 数据校验
【Abstract】Operating principle and its solenoid valve characteristic of a hydraulic AMT hydraulic system are analyzed, and a TCU is designed. Then, based on the communication protocol of CAN, a flash operation code of the lower computer is made and an upper computer calibration program is edited in LabVIEW. Finally, an onboard test is conducted to 1 -2 shifting with 15% throttle opening. The test results show that the maximum shifting impact strength of this transmission drops to 8.34m/s, approx. 63% lower than that before calibration, thus proving correctness of the calibration system.