某电厂水冷壁管泄漏失效案例分析
火电厂锅炉20G水冷壁管失效分析

火电厂锅炉20G水冷壁管失效分析摘要:近年来,火电机组参与深度调峰,机组利用小时数不断下降,对机组水汽系统的结垢腐蚀产生了明显影响,造成锅炉水冷壁的腐蚀速率和结垢速率明显增加。
在实际运行中,由于机组运行工况变化,锅炉水冷壁管酸性腐蚀情况明显增多,且酸性腐蚀一旦形成,锅炉水冷壁管在较短运行时间内就会出现减薄脱碳现象,钢材韧性和强度降低,很容易发生爆管泄漏,对机组的安全运行带来较大的危害。
为了充分研究水冷壁酸性腐蚀问题,对其水冷壁管酸性腐蚀发生爆管泄漏的情况开展跟踪分析,从技术监督、水汽品质、化学清洗等方面,对机组减少结垢腐蚀,降低水冷壁管腐蚀爆管风险,提出相关措施和建议。
关键词:水冷壁;失效分析;20G;氧腐蚀;显微组织引言烟化法是在烟化法余热锅炉(以下简称烟化炉)中加入高温熔渣,用含煤粉空气射流使渣液强烈搅动,煤粉燃烧产生的热量,使渣液升温并维持冶炼反应所需的温度,燃烧产生的一氧化碳气体在高温流动条件下,把渣中的金属氧化物还原成金属单体。
被氧化还原出来的易挥发物随烟气脱离吹炼池进入烟化法余热锅炉,在余热锅炉内二次燃烧,经辐射室、对流室、连接烟道、省煤器后排出,进入收尘系统,此过程中烟气温度一般很高,达1200~1300℃,投料时烟气温度又较低,所以余热锅炉运行过程中会产生较大的温度循环。
烟气的粘结性较强,需要考虑水冷壁管高温结焦及低温积灰的情况。
1水冷壁结构某火电厂锅炉为WGF440/13.7-1型循环流化床锅炉,其额定蒸发量为440t/h,运行时水冷壁内介质压力为11.0MPa、介质温度320℃、炉膛温度900~950℃,水冷壁材质为20G,规格为准60mm×6.5mm。
锅炉自投入运行以来,每年有3~4次停炉检修,检修时间最长达50d。
锅炉累计运行8×104h,锅炉水冷壁管左侧第36根在高度40.5m处发生爆管。
2试验与分析2.1泄漏管样宏观检查对泄漏管的位置、来源、原始状态等进行检查,泄漏位置均处于高热负荷区或水汽循环不良部位,泄漏部位上、下及左、右相邻管段均未发现胀粗变形或被吹损的情况。
电站锅炉水冷壁管失效分析

电站锅炉水冷壁管失效分析摘要:作为锅炉的重要组成部分,水冷壁管主要用于吸收炉膛内部高温烟气和火焰散发的热量,这个过程中水冷壁管内介质会出现受热蒸发等一系列现象,能够有效保护锅炉的炉墙,本身具有抗热疲劳性能和热传导性能。
但在电站锅炉运行过程中水冷壁管出现泄露问题会比较常见,将严重影响锅炉运行的稳定性和安全性。
因此,电站要注意这一问题,制定针对性地解决措施,避免锅炉出现故障停炉等一系列问题。
关键词:电站锅炉;水冷壁管;失效;措施某企业#5电站锅炉折焰角水冷壁管子在使用过程中发生了爆裂,现对断裂部位进行力学性能、材质成分分析,腐蚀物和管内垢样成分检测分析,以及管子劣化现象金相和硬度分析。
1电站锅炉水冷壁管泄漏原因分析1.1水循环路线不畅引起水冷壁爆管现阶段大型煤粉电站锅炉通常采用直流锅炉,自热循环方式,水冷壁通常采用螺旋管圈加垂直管圈布置方式,水循环可靠性高,辐射热量可以被及时带离,水冷壁管的运行温度控制在壁温计算规定的合理范围内。
另因自然循环中水循环在实际运行中可能出现的停滞倒流现象,使得水冷管壁内部汽水混合物的流动性无法达到预期要求,无法及时带走水冷壁管所吸收的热量,使得这些蒸汽形成汽塞,这一位置的水冷管壁无法及时冷却,管壁温度急剧升高,不仅会在一定程度上降低水冷管壁的机械强度,还会增加水冷管壁出现爆管等一系列现象的概率。
经分析,造成上述现象主要原因如下:锅炉启动过程中,水循环处于不稳定运行状态,这一时期锅炉内部火焰分布并不是非常均匀,受热较少的管壁较为容易出现水循环故障问题;锅炉内部水冷壁管壁出现严重结焦问题,影响水冷壁吸收热量,容易出现水冷壁内部水循环问题;考虑到定排时间问题,锅炉下联箱的定排门存在严重内漏现象,导致水冷壁这部分路线出现比较严重的循环问题;由于现在电网要求,部分电厂不能够长期带满负荷或者高负荷运行,长期低负荷运行成为常态。
1.2管内壁结垢对水冷壁管泄露的影响现有锅炉给水均需化学处理,通常采用CWT或者AWT,这种化学除盐水无法有效去除水中的所有盐分。
火电厂安全教育警示教育事故案例

事故案例一、某电厂1月15日8号炉水冷壁泄漏分析报告(一)、事件经过2017年1月15日15:23,8号机组负荷820MW,“炉管泄漏”报警信号发出,现场检查锅炉前墙8层半发现异音,判断为受热面泄漏,申请停炉处理。
1月16日5:50,机组解列。
经检修处理后,机组于2月3日13:03并网恢复。
(二)、检查情况1.设备概况8号炉为东方锅炉(集团)股份有限公司生产的DG3000/26.15-Ⅱ1型高效超超临界参数变压直流炉、一次再热、平衡通风、运转层以上露天布置、固态排渣、全钢构架、全悬吊结构Π型锅炉。
炉膛宽为33973.4mm,深度为15558.4mm,高度为64000mm,整个炉膛四周为全焊式膜式水冷壁,炉膛由下部螺旋盘绕上升水冷壁和上部垂直上升水冷壁两个不同的结构组成,两者间由过渡水冷壁和混合集箱转换连接,介质流向自下而上。
上部垂直水冷壁管子规格为Φ31.8×7.5,材料为SA-213T12,节距63.5 mm,前墙共布置534根,分别引入11只出口集箱,最终由各集箱出口连接管引入水冷壁出口混合集箱。
2.现场检查情况停炉冷却后检查发现前墙水冷壁出口左数第6集箱左数第33根泄漏,位置在8层半观火孔标高上约1米,泄漏方向朝向炉内,爆口呈喇叭状,爆口边缘锋利,管子明显胀粗,爆口长度约33mm,宽度约9mm(见附图1、2),从爆口宏观形貌分析判断为短时过热造成。
对泄漏管内部及对应入口、出口联箱进行内窥镜检查,未发现异物(见附图3),检查发现该管段有一只焊缝内部周圈凸起明显(见附图4),测量最大凸起部位对应管道内径为12.1mm(水冷壁管子规格为Φ31.8×7.5,内径为16.8mm),检查此管段工地焊口共5只,测量内部管径分别为16.2mm、16.1mm、15.9mm、15.8mm、15.6mm。
3.取样检验情况对8号炉前墙水冷壁出口左数第6集箱左数第33根爆口管进行取样分析,爆口处、爆口边缘的金相组织为铁素体+碳化物,铁素体晶粒沿形变方向被拉长,球化级别为4-5级(见附图5);爆口背面,金相组织为铁素体+珠光体,球化级别2.5级(见附图6)。
某600MW机组侧墙水冷壁管横向裂纹原因分析

某600MW机组侧墙水冷壁管横向裂纹原因分析摘要:某600MW超临界机组在长期深度调峰工况下,水平烟道侧墙水冷壁管泄漏导致机组非计划停运,停炉消缺检查中发现泄漏水冷壁管表面出现横向裂纹,特对此横向裂纹进行分析,并根据实际的处理情况,对此类事故提出了预防建议。
关键词:水冷壁;深度调峰;泄漏;横向裂纹一、前言某电厂的600MW锅炉是一台参与深度调峰、负荷波动大的超临界参数变压直流炉,型号为DG1920/25.4-Ⅱ型,采用一次再热、单炉膛、尾部双烟道结构、固态排渣、全悬吊结构、前后壁对冲燃烧,由东方锅炉厂设计制造。
该机组于2014年1月正式投产,累计运行时间约 5.9 万小时。
机组运行过程中锅炉水平烟道侧墙水冷壁(规格φ31.8×7.5,材质15CrMoG)发生泄漏,此次事故中水平烟道右侧墙水冷壁管出现表面横向裂纹,具体为水平烟道右侧墙标高约68m处水冷壁管炉后往炉前数第 2、3、4 根管母材表面存在横向裂纹,第2、3、4、10、11根管(以下称 2#、3#、4#、10#、11#管)焊缝附近存在横向裂纹,本文进行了分析,并根据实际处理情况,对此类事故提出了预防建议。
二、理化检验1、宏观分析本次选取5根,编号分别为2#、3#、4#、10#、11#的水冷壁管,其中 2#、3#、4#管长度约 1.1 米,10#、11#管长度约 0.6 米;2#、3#、4#、10#、11#管向烟侧、背烟侧外壁呈橘红色,壁厚未见异常减薄,2#、3#、4#、10#、11#管向烟侧焊缝附近可见横向裂纹;2#、3#、4#管母材向烟侧外壁可见密集分布的疑似裂纹。
选取2#管横向裂纹人工掰开后可见裂纹由外壁向壁厚深度方向呈扇形分布,裂纹断口呈暗红色,对断口清洗后外壁原始断口可见贝壳纹花样,原始内壁断口可见较多台阶,具有明显宏观疲劳开裂特征。
对2#、3#、4#、10#、11#管母材向/背烟侧分别制取长约18mm纵截面金相试样,观察内外壁裂纹分布情况。
某电站锅炉水冷壁泄漏事故原因分析及处理措施

某电站锅炉水冷壁泄漏事故原因分析及处理措施摘要:对某火力发电厂锅炉燃烧器改造和水冷壁酸洗后运行水冷壁泄漏,换管后运行再次泄漏,从宏观检查、光谱分析、硬度试验、金相检验、拉伸试验等进行原因分析,并采取有效处理措施,以满足机组安全运行的要求。
关键词:锅炉;水冷壁;再次泄漏;原因分析;处理措施1基本情况某电厂4号锅炉型号为HG-1021/18.2-540/540-PM27,2017年6月大修期间进行了燃烧器改造和水冷壁酸洗等工作。
酸洗后对后水中间集箱内窥镜检查,未发现异物。
并网运行期间后水冷壁泄漏。
更换泄漏的水冷壁管后,开机运行时后墙水冷壁管再次泄漏。
停炉检查,泄漏位置为后墙水冷壁从炉右数第154根、中间集箱往上2m处,系上次爆管换管处。
电厂将原泄漏点堆焊处理过的管子与同批次新管(规格:Φ31×5.5mm,材质:15CrMo)送样作泄漏原因分析。
2试验方法及结果2.1宏观检查泄漏水冷壁管因经堆焊处理,看不到原始形貌;观察内壁泄漏处裂纹长约120mm,无明显张口,有脆性开裂特征。
如图1。
2.2光谱分析分别在新管和泄漏管泄漏口往下1m的母材上取样光谱分析,分析结果均符合相关标准要求。
如表1。
2.3硬度试验在泄漏壁管泄漏口往下1m处母管上取样布氏硬度试验,硬度值为203HB,高于DL/T 438-2016《火力发电厂金属技术监督规程》要求值(母材HB135~195),不合格。
如表2。
2.4金相检验对新管管样母材横截面(4号样品)、泄漏管泄漏口处(1号样品)及泄漏口往下1m处(2、3号样品)母材取样金相检验,组织均为珠光体+铁素体,珠光体球化等级为2级,未发现异常组织。
如图2~图9。
2.5拉伸试验新管管样母材(2号)和泄漏管泄漏口往下1m处母材(1号)拉伸试验。
所得新管抗拉强度(Rm)717MPa、屈服强度(ReL)641MPa、断后伸长率(A)13%;泄漏水冷壁管的抗拉强度(Rm)679.5MPa、屈服强度(ReL)600MPa、断后伸长率(A)18%。
神华米东热电厂2号锅炉水冷壁管泄漏原因分析
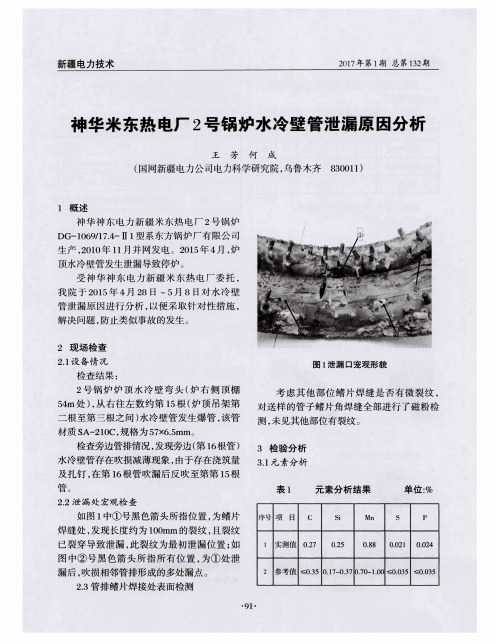
生产 , 2 0 1 0 年l 1 月 并 网发 电 。2 0 1 5 年4 月, 炉 顶水 冷壁 管发生 泄漏 导致 停炉 。 受 神 华 神 东 电 力新 疆 米 东 热 电 厂 委 托 , 我院于 2 0 1 5 年 4月 2 8日 ~5 月 8日对 水 冷 壁 管 泄漏 原 因进 行 分析 , 以便采 取 针 对性 措 施 , 解决 问题 , 防止类 似事 故 的发生 。 2 现 场检 查
元素 分析 结果
C S i Mn
单 位: %
S P
如图 l 中①号黑色箭头所指位置 , 为鳍片
焊缝 处 , 发 现长 度约 为 1 0 0 mm的裂纹 , 且 裂纹 已裂穿 导 致泄 漏 , 此 裂纹 为最 初 泄 漏位 置 ; 如
l 实测 值 0 . 2 7
表2
序 号 泄 漏 处 硬 度
硬 度测量 结 果
l 2 3
单位 : H B
4 5 平 均 1 4 8
表 3 水冷 壁 管及鳍 片焊 缝金相 组织
1 4 3 l 4 5 l 5 2 l 4 8 l 5 l
样 品名称
组织
附图
远 离 泄 漏 处 硬 度
0 . 2 5
0 . 8 8
0 . 0 2 l 0 . 0 2 4
图 中②号黑色箭头所指所有位 置 , 为①处泄
漏后 , 吹损相 邻管 排形 成 的多处漏 点 。
2 . 3管排 鳍 片焊接 处表 面检测
・
2 参考值 ≤0 3 5 0 . 1 7 - 0 - 3 7 0 . 7 0 - 1 . 0 0 ≤0 . 0 3 5 ≤0 . 0 3 5
热电厂锅炉水冷壁管失效原因探究

热电厂锅炉水冷壁管失效原因探究[摘要]在检测锅炉水汽质量、水处理设备过程中,发现大量锅炉存在结垢、腐蚀情况,现就几个典型结垢、爆管事例进行具体分析。从锅炉运行、水质管理、水处理设备运行管理、炉内加药控制等方面进行分析锅炉结垢、腐蚀甚至爆管的原因,提出锅炉管理、水处理作业人员、水质监测管理、科学加药控制等相关措施,为今后锅炉运行中出现水处理不当类似问题提供经验和参考。[关键词]水冷壁管;腐蚀;水处理;锅炉;爆管1热电厂锅炉水冷壁管事故简析在热电厂中,锅炉水冷壁管、热交换器、汽轮机、发电机等都是重要的机组设备,电厂不间断供电主要依赖于其设备和部件的持续正常运行,如果单台设备出现故障,整个供电系统将会受到严重的影响。其中,锅炉水冷壁管内部暴露于流动蒸汽的高压和高温下,外部暴露于燃烧产物的高温下,是锅炉管、蒸汽过热器元件和化工厂转化管等热交换系统的关键部件;并且锅炉水冷壁管主要用于吸收炉膛内火焰和高温气体流动产生的辐射热量,具有冷却和保护炉壁的作用。近年来,在我国发生了诸多热电厂非计划停机事故,造成了严重的经济损失和人员伤亡,并且对电厂整体运行环境也造成了严重的破坏。经过调查分析,锅炉水冷壁管泄漏、爆管等原因造成失效是导致事故的主要原因之一。2典型锅炉结垢腐蚀情况分析2.1事例一2.1.1爆管发生过程某公司一台自然循环蒸汽锅炉,该锅炉为双锅筒D型布置的水管室燃炉结构,于2020年1月1日投入使用,连续运行至2020年2月28日锅炉水冷壁爆管,漏水导致锅炉报废;在2020年8月5日更换锅炉后重新投入使用,连续运行至2020年10月26日水冷壁中间部位再次发生爆管漏水事故;在2021年2月25日更换锅炉后重新投入使用,连续运行至2021年3月30日水冷壁中间部位再次爆管漏水。拆除锅炉的水位计,发现其汽、水连接管内部结生约2mm厚的白色水垢,拆开下集箱,发现大量白色水垢沉积于管底部。2.1.2试验分析现场采集锅炉给水箱、软水器出口水质样品,根据《锅炉用水和冷却水分析方法硬度的测定》GB/T6909-2018的铬黑T测试法,检测水样硬度,按照GB/T1576-2018要求,该锅炉给水硬度严重超过标准要求,容易引发锅炉受热面发生结垢、腐蚀现象。现场割管采集垢样,垢样呈白色,取适量垢样,置入烧杯中,加入5%盐酸溶液后,产生大量气泡,同时垢样基本溶解。根据《蒸汽和热水锅炉化学清洗规则》GB/T34355-2017附录G中结垢物类型鉴别方法,可判定该结垢物以碳酸盐为主,符合硬度超标引发结垢的特征。2.2事例二某公司一台自然循环蒸汽锅炉,该锅炉型号为SZL10-1.6-BMF,在检测锅炉水汽质量、水处理设备过程中,发现连续几个月给水硬度、锅水pH、全碱度、磷酸根均不符合要求。现场检验发现,锅筒内部、集箱等水侧水垢覆盖面达90%,水垢厚度小于1mm;水汽检测药剂浓度、药剂存储环境不符合标准要求,检测结果不能反映水质的真实情况。2.3事例三某医院一台自然循环蒸汽锅炉,该锅炉型号为SG50L,检测发现给水pH偏低、锅水pH、全碱度偏高,均不符合标准要求,锅炉安置于中间楼层的蒸汽消毒室,该锅炉使用单位未进行水质检测,长达2个月不排污,锅水高度浓缩,存在安全隐患。2.4事例四某公司一台自然循环蒸汽锅炉,该锅炉型号为WNS3-1.25-Y,检测发现连续几个月给水pH偏低,不符合标准要求,该锅炉使用单位未进行水质检测,导致给水长期不合格。3原因分析3.1管理不当引起锅炉结垢锅炉使用单位管理人员不重视水处理工作,对锅炉运行状况不了解,未设置专业水处理作业人员,未建立锅炉及水处理相关管理制度,未建立锅炉及水处理运行操作指导书,水处理工作混乱,随意性大,导致锅炉用水长期不达标。3.2锅炉作业人员操作不当引起锅炉结垢锅炉使用单位作业人员未经过专业培训,或培训后未深入学习理解水处理基础知识,对水处理设备随意操作,连续2个月24小时满负荷运行,操作人员在锅炉运行期间盲目操作,关闭水处理设备,导致水处理设备未能正常运行,无法制水,将自来水直接泵入锅炉中,因自来水中含有大量钙镁离子,不能满足锅炉给水要求,导致锅炉内部受热面结垢严重。3.3锅炉用水水质指标检测不当引起锅炉结垢锅炉使用单位水处理设备为全自动软水器或反渗透装置,设备安装后及制水时均未进行水质分析化验,企业未配备水质检测相关试剂,无法确定水处理设备制水能力,导致司炉人员不能准确判断水处理设备制水能力是否达到锅炉给水要求,直接将水处理设备出水泵入锅炉中。3.4垢下腐蚀引起锅炉水冷壁爆管水处理设备不能正常运行,无法去除原水中全部的钙镁离子,导致无法满足锅炉给水要求,给水泵入锅炉中后,引起锅炉内部受热面结生大量水垢,锅炉运行工况下,产生沉积物下介质浓缩腐蚀。锅炉金属表面本有致密的Fe3O4钝化膜,在锅炉运行过程中,当锅水浓缩到一定倍数时,Cl-达到一定浓度,聚集在碳钢本体有缺陷部位,随着Cl-浓度的增加,钝化膜的击穿电位降低,钝化膜的破坏加快,而且高浓度的Cl-导致金属表面不能及时形成Fe3O4钝化膜。当钝化膜被破坏时,金属本体易发生腐蚀。当给水中含有氯化物、硬度超标时,生成CaCl2和MgCl2进入锅炉,发生水解产生HCl,同时生成Ca(OH)2和Mg(OH)2沉积物,由于受热面存在大量沉积物,形成密闭腔体,致使HCl在沉积物下浓缩,HCl浓度逐步升高,在腐蚀坑内形成闭塞腐蚀电池,持续腐蚀金属本体,甚至腐蚀穿孔,因而造成碳钢脱碳,金相组织受到破坏。由于反应产物CH4会在金属内部产生压力,使金属组织逐渐形成裂纹,金属本体承压能力下降,发生爆管事故。4措施4.1锅炉使用单位加强水处理作业管理企业水处理系统应符合国家标准锅炉用水要求,符合要求的水处理系统是锅炉安全生产的前提。企业若不严格执行国家锅炉用水标准,导致锅炉存在安全风险,企业运行成本有所增加,经济效益降低,为促使锅炉安全、节能地运行,应加强水处理系统管理。4.2合理选择水处理方法和系统根据原水水质,以技术可靠、经济合理为原则,选择合适的水处理方法和系统,确保水处理设备出水符合国家锅炉用水标准要求。当原水总硬度超高或原水水质随季节变化较大时,一级软水器出水可能无法达到标准要求,水处理设备建议采用复合式配备,即两级串联软水器或者采用软水器+反渗透联合。当原水碳酸盐硬度较高时,水处理设备建议采用交换容量大的设备,即弱酸阳离子交换设备或不足量酸再生氢离子交换树脂的氢-钠离子串联系统。当原水水质悬浮物、有机物等杂质含量较高时,水处理设备建议采用预处理装置+软水器,预处理流程为混凝-澄清-过滤,去除原水中大部分悬浮物、有机物、胶体等杂质,以避免后续水处理设备、水处理出水被污染,影响水汽质量。4.3提高水处理作业人员的专业技术水平锅炉使用单位为确保锅炉安全运行,应当了解水处理系统的重要性,应配备专业的水处理作业人员,应严格按照国家法规执行锅炉相关的标准和要求。水处理作业人员专业技术水平应保持与时俱进,用人单位应定期为其安排专业培训机构进行学习、培训,以确保其水处理知识的先进性。4.4定期对锅炉除垢对于锅炉内部,当水垢厚度大于1mm及以上或受热面严重锈蚀时应除垢,据统计清除受热面1mm的水垢可提高锅炉效率3%~5%。使用单位应定期进行锅炉内部检查,根据锅炉实际结垢、腐蚀情况,采取碱煮、酸洗、机械除垢等除垢措施,以确保锅炉受热面清洁、无垢运行。5结语锅炉水冷壁管是热电厂重要的机组设备,为了实现锅炉管、蒸汽过热器元件和化工厂转化管等热交换系统的热量传递,需要长时间在高温的环境中运行。因此,锅炉水冷壁极容易由于材料缺陷、热疲劳、氧化、腐蚀、蠕变和焊接等原因,导致出现泄漏和爆管等各种故障,影响整个供电系统的正常运行。为了减少锅炉水冷壁管失效造成的严重后果,对其实施科学合理、实时有效的安全监测是热电厂安全运营管理工作的重要内容。参考文献[1]杨希锐.超超临界锅炉内螺旋水冷壁管横向开裂原因分析[J].材料保护,2021,54(11):192-196.[2]袁继禹,李林,张亚宁等.干煤粉气流床气化炉反应室水冷壁温度场分析[J].化工设备与管道,2021,58(04):37-41.[3]王毅斌,张思聪,谭厚章等.劣质烟煤低氮燃烧模式下水冷壁高温腐蚀与硫化物沉积形成分析[J].中国电机工程学报,2020,40(24):8058-8066+8242.。
某电厂~#2锅炉水冷壁管泄漏原因分析

由于梳 形板 的对 接焊 缝存 在 焊 接 缺 陷 ( 部 未 根
焊透 ) 来 的隐患 为 : 焊缝 的有效 受 力 面积 减 小 , 带 使
平 均应 力水平 增 高 ; 未焊 透相 当于 缺 口 , 在较 大的 存
应 力集 中。
在运行 当 中, 炉 的启/ 、 锅 停 负荷 变 化 、 烧 的变 燃
摘
要: 针对水冷壁管紧 固梳形板对接焊缝处出现的开裂泄漏现象 , 通过对部件 结构 、 力状况 、 行环境 、 受 运 焊接质量等
的综合分析 , 确认 了引起开裂的主要因素 , 有针对性提 出了处理措施 。 关键词 : 水冷壁 ; 梳形板 ; 热应力 ; 撕裂 ; 泄露 中图分类号 :K2 3 3 T 2 . 1 文献标志码 : B 文章编号 :6 4—15 (0 1 0 — 0 3— 2 17 9 121 )1 05 0
图 2 水冷壁 、 梳形板结构俯视 图
() 2 炉墙 密封 ;
( ) 固燃烧器 , 3紧 防止喷燃 器 的角度 变动 。
2 检 查 分 析
泄 漏现 场检查 发现 :
( ) 梳形 板 的原 安装 对接 焊缝整 条开 裂 ( 12块 割
下后 的裂 纹 如 图 3所 示 ) 裂 纹 长 度 的 内侧 一 端 在 ,
板 与管 子 、 板与管 子 的角焊缝 为单 面连续 焊 , 钢 焊脚
尺寸 4 mm; 钢板 与钢板 的角焊 缝 , 面连 续焊 , 脚 单 焊 尺寸 5 n 。梳形板 之 间的对 接焊 缝无 明确要 求 , mr 对 该处 的结 构进行 了分 析 。梳 形板 的作 用是 :
( ) 过燃 烧 器 四周 的 紧 固密 封 板 , 部 位 的 1通 该 水冷 壁管 承担整个 燃 烧 器 13的重量 ( / 其余 23的 /
- 1、下载文档前请自行甄别文档内容的完整性,平台不提供额外的编辑、内容补充、找答案等附加服务。
- 2、"仅部分预览"的文档,不可在线预览部分如存在完整性等问题,可反馈申请退款(可完整预览的文档不适用该条件!)。
- 3、如文档侵犯您的权益,请联系客服反馈,我们会尽快为您处理(人工客服工作时间:9:00-18:30)。
某电厂水冷壁管泄漏失效案例分析
发表时间:
2017-11-22T16:21:51.753Z 来源:《电力设备》2017年第19期 作者: 方宙锋 孙清
[导读] 摘要:某电厂1000MW锅炉的螺旋水冷壁标高45米处后墙发生爆管泄漏,通过对其外观形貌、金相组织、硬度等分析发现管子涨
粗、组织发生相变、硬度淬硬,都说明管子在短时间内高温超过相变点,强度急剧下降,最终发生短时超温爆管。
(华电江苏能源有限公司句容发电厂 江苏镇江 212413)
摘要:某电厂1000MW锅炉的螺旋水冷壁标高45米处后墙发生爆管泄漏,通过对其外观形貌、金相组织、硬度等分析发现管子涨粗、
组织发生相变、硬度淬硬,都说明管子在短时间内高温超过相变点,强度急剧下降,最终发生短时超温爆管。在寻找短时超温爆管的原因
时,发现在水冷壁前墙标高
17米处同根管子发生泄漏,泄漏原因为不规范补焊时母材被烧穿,长期运行中发生泄漏导致介质流出,导致后
墙同根管道标高
45米处介质流量较少,热量不能及时带走,从而最终引发标高45米处短时超温爆管。
关键词:水冷壁;泄漏;短时超温;失效分析
3
综合分析
7#
管段及“7#下”管段均明显胀粗,且组织相变,管子淬硬,说明7#管段超温幅度很大(超过相变点),其强度急剧下降,管子向火面
胀粗,在温度最高处鼓包破裂,为短时超温爆管。
1#
管位于7#管下方,且为同一介质通道,在其被2#管吹损泄漏后,由于漏点较小,管内压力没有释放,但水流量会大幅度下降,导致
上方的热负荷最高区域的
7#管段发生传热恶化,温度急剧上升并发生爆管,爆口附近的焊缝亦出现过烧开裂。
2#
管泄漏是因为内壁焊瘤位置开裂所致,可能是在不规范补焊时母材被烧穿,整个厚度方向为粗大焊态组织,其力学性能极差,长期
运行中极易发生开裂泄漏。
4
结论
根据试验及分析结果,判断爆管过程如下:17米标高处的2#管段在安装过程中由于焊接操作不当导致母材损伤,在补焊时不规范操作
母材被烧穿,内壁出现焊瘤,该位置长期运行后开裂泄漏,将
1#管吹损泄漏,导致45米热负荷最高区域同一介质通道的7#管发生干烧,急
剧超温后短时间内鼓包爆管。
8#
管上、下割管处及7#上割管位置显微组织及硬度均正常;7#下割管位置亦发生相变淬硬,割管不到位。