汽车零部件断裂失效分析
轮毂螺母垫片断裂失效分析

AUTO TIME153AUTO PARTS | 汽车零部件时代汽车 轮毂螺母垫片断裂失效分析谢仔新宇星紧固件(嘉兴)股份有限公司 浙江省嘉兴市 314305摘 要: 材料为ML40Cr 的车轮轮毂螺母在装配后发现垫片断裂失效现象,通过宏观检查、断口分析、金相检测、硬度检测、化学成分分析、综合分析分析、氢含量测定等方法对垫片断裂原因进行分析。
结果表明:垫片表面在挤压过程中产生的微裂纹,在酸洗、镀锌等过程中,氢沿裂纹渗入基体,由于垫片硬度要求较高,从而导致氢脆开裂并扩展。
最终在装配应力作 用下发生断裂失效。
关键词:ML40Cr 轮毂螺母 断裂 硬度 氢脆轮毂螺母在装配后发现有垫圈开裂现象。
在其中部分轮毂中发现有1-2只开裂现象。
该螺母和垫圈材料均为ML40Cr,该垫圈加工工艺为:原材料球化—酸洗磷皂化—拉丝—切料压扁—退火—磷皂化—冷挤压—热处理—压圈—镀锌,热处理后硬度为38-44HRC。
为检查该批产品的断裂原因,以便防止后期在出现类似质量问题,笔者对断裂垫片进行检验和分析。
1 理化检查1.1 宏观观察实物如图1所示,材料为ML40Cr,从实物可见,垫圈存在两处开裂,为方便描述,现将两处分别标记为1#和2#。
1#2#图1 试样宏观形貌采用体视显微镜对样品进行宏观检查,图2所示为两处断口宏观形貌,可见断面均粗糙,隐约可见放射痕迹,放射痕迹收敛于垫圈内侧凹槽处(红色虚线框标记处),因此,该处为裂纹源区。
观察裂纹源区附近表面,可见存在金属堆积现象,如图3所示。
1.2 断口分析采用扫描电子显微镜分别对1#和2#断面进行微观形貌观察,图4所示为断面低倍形貌,可见,断面均可见放射状痕迹,裂纹 源区分别位于A1区和A2区边缘,为方便描述,现将断面分为A1、B1、C1和A2、B2、C2不同区域进一步描述。
图5为断面A1区微观形貌,断面为冰糖状沿晶形貌,并伴有晶间二次裂纹,局部晶面可见“鸡爪纹”。
图6所示为断面C2区微观形貌,可见为“冰糖状”沿晶形貌,并伴有晶间二次裂纹,局部晶面可见“鸡爪纹”。
汽车零部件的失效机理及其分析教材

第五节 汽车零部件变形失效机理
零件在使用过程中,由于承载或内部应力的作 用,使零件的尺寸和形状改变的现象称为零件的变形。 零件变形失效的类型有:
弹性变形失效
塑性变形失效 蛹变失效
第六节 汽车零部件失效分析方法
一.失效分析的基本思路
按分析检验项目进行失效分析
按失效模式进行分析 系统工程分析方法
影响因素 防治措施
思考题
1. 气缸-活塞环的磨损规律是什么? 为什么? 2. 零件磨损量如何测定?
参考答案
1. 气缸-活塞环的磨损规律是什么?为什么?
规律:高度方向,上大下小;圆周方向不规则
影响因素:磨料、工作气体压力、润滑和腐蚀 物质。 2. 零件磨损量如何测定?
直接测量法:表面测量法、称重法、刻痕法和 快速磨损法; 间接测量法:光谱分析法和同位素法。
四.提高汽车零件抗疲劳断裂的方法
延续疲劳裂纹萌生时间 降低疲劳裂纹扩展的速率 提高疲劳裂纹门槛值△km长度
思考题
1.
疲劳断裂与磨损的区别
损伤形式 比较因素 损坏形式 受力情况 表面变形 初始裂纹 疲劳磨损 疲劳断裂
第四节 汽车零部件腐蚀失效及其机 理
零件受周围介质作用而引起的损坏称为零件的 腐蚀。按腐蚀机理可分为化学腐蚀和电化学腐蚀, 汽车上约20%的零件因腐蚀而失效。
第一节 汽车零部件失效的概念及分 类
一.失效的概念
汽车零部件失去原设计所规定的功能称为失 效。 失效不仅是指完全丧失原定功能,而且还包 含功能降低和有严重损伤或隐患、继续使用 会失去可靠性及安全性的零部件。
二、失效的基本类型
三.零件失效的基本原因
汽车零部件的失效模式及分析
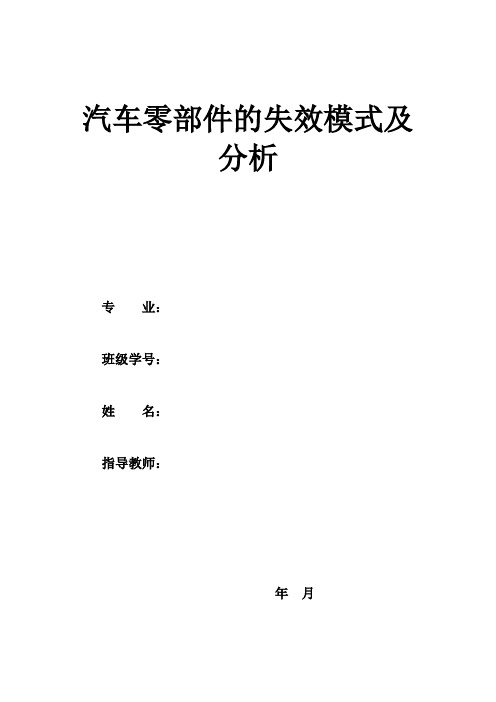
汽车零部件的失效模式及分析专业:班级学号:姓名:指导教师:年月摘要汽车零件失效分析,是研究汽车零件丧失其规定功能的原因、特征和规律;研究其失效分析技术和预防技术,其目的在与分析零部件失效的原因,找出导致失效的责任,并提出改进和预防措施,从而提高汽车可靠性和使用寿命。
目录第一章汽车零部件失效的概念及分类 (1)一、失效的概念 (1)二、失效的基本分类型 (1)三、零件失效的基本原因 (2)第二章汽车零部件磨损失效模式与失效机理 (3)一、磨料磨损及其失效机理 (3)二、粘着磨损及其失效机理 (4)三、表面疲劳磨损及其失效机理 (5)四、腐蚀磨损及其失效机理 (5)五、微动磨损及其失效机理 (6)第三章汽车零部件疲劳断裂失效及其机理 (8)第四章汽车零部件腐蚀失效及其机理 (9)第五章汽车零部件变形失效机理 (10)参考文献 (11)第一章汽车零部件失效的概念及分类一、失效的概念汽车零部件失去原设计所规定的功能称为失效。
失效不仅是指完全丧失原定功能,而且功能降低和严重损伤或隐患、继续使用会失去可靠性及安全性的零部件。
机械设备发生失效事故,往往会造成不同程度的经济损失,而且还会危及人们的生命安全。
汽车作为重要的交通运输工具,其可靠性和安全性越来越受到重视。
因此,在汽车维修工程中开展失效分析工作,不仅可以提高汽车维修质量,而且可为汽车制造部门提供反馈信息,以便改进汽车设计和制造工艺。
二、失效的基本分类型按失效模式和失效机理对是小进行分类是研究失效的重要内容之一。
失效模式是失效件的宏观特征,而失效机理则是导致零部件失效的物理、化学或机械的变化原因,并依零件的种类、使用环境而异。
汽车零部件按失效模式分类可分为磨损、疲劳断裂、变形、腐蚀及老化等五类。
汽车零件失效分类一个零件可能同时存在几种失效模式或失效机理。
研究失效原因,找出主要失效模式,提出改进和预防措施,从而提高汽车零部件的可靠性和使用寿命。
三、零件失效的基本原因引起零件是小的原因很多,主要可分为工作条件(包括零件的受力状况和工作环境)、设计制造(设计不合理、选材不当、制造工艺不当等)以及使用与维修等三个方面。
汽车零部件的失效模式及其分析

扩展的横向裂纹。
总之,磨料磨损机理是属于 磨料的机械作用,这种机械作用 在很大程度上与磨料的性质、形 状及尺寸大小、固定的程度及载 荷作用下磨料与被磨表面的机械
性能有关。
四、粘着磨损及其失效机理
v 定义:摩擦副相对运 动时,由于固相焊合 作用的结果,造成接 触面金属损耗的现象 称为粘着磨损。
v 是缺油或油膜破坏 后发生干摩擦的结果; 是指一个零件表面上 的金属转移到另一个 零件表面上,而产生 的磨损。
第一节汽车零部件失效的概念及分类 一、失效的概念; 二、失效的基本类型; 三、零件失效的基本原因;
一、失效的概念 汽车零部件失去原设计所 规定的功能称为失效。失效不 仅是指完全丧失原定功能,而 且还包含功能降低和有严重损 伤或隐患、继续使用会失去可 靠性和安全性的零部件。
二、失效的基本形式
按失效模式和失效机理对失效进行分
第二章汽车零部件的失效模式及其分析
❖ 难点: ❖ 1.汽车摩擦学-混合摩擦; ❖ 2.粘着磨损;微动磨损; ❖ 3.腐蚀磨损; ❖ 4.提高汽车零件抗疲劳断裂的方法; ❖ 5.基础件析,是研究 汽车零部件丧失其功能的原因、特 征和规律;目的在于:分析原因, 找出责任,提出改进和预防措施, 提高汽车可靠性和使用寿命。
磨料磨损的失效机理(假说)
以 微 量 切 削 为 主 的 假 说 ;塑 性 金 属 同固定的磨料摩擦时:磨屑呈螺旋形、 弯 曲 形 等 ;在 金 属 表 面 内 发 生 ⑴ 塑 性 挤 压 、形 成 擦 痕 ;⑵ 切 削 金 属 ,形 成 磨 屑 ;
以压痕为主的假说:对塑性较大的 材料;磨料在压力作用下压入材料表 面,梨耕另一金属表面,形成沟槽,使 金属表面受到严重的塑性变形压痕两 侧金属已经破坏,磨料极易使其脱落。
发动机连杆螺栓断裂失效分析

2021年 第4期 热加工771 序言对于汽车发动机而言,连杆螺栓不仅是将螺栓头部和螺杆联接在一起的紧固件,还是联接连杆大端轴承座与轴承盖使之成一体的重要螺栓。
连杆螺栓不仅受到装配时的预紧力[1],在发动机的运行中还要承受活塞连杆往复运动惯性力和连杆旋转离心力的交变载荷作用,而且在气缸的压缩和做功行程中,还要受到每分钟上千次交变应力的冲击[2]。
各种失效模式的研究和案例也时有报道[3-6],对汽车用断裂螺栓进行失效分析,研究其产生故障的特征、规律及原因,可为汽车的生产、使用或维修中采取有针对性地改进和预防措施提供理论依据,防止同类故障再次发生[7]。
2020年2月,某故障发动机在拆机之后发现其中一缸的进、排气部位缸体被击穿,连杆外露,另有紧固连杆的两根螺栓发生断裂(见图1)。
通过对断裂螺栓进行失效分析,主要包括断口分析、材料鉴定、拧紧工艺排查等方面,对螺栓的整个生命周期环节做了梳理,试图从螺栓的设计、生产检测以及拧紧工艺等方面找出螺栓断裂的原因,并解决连杆螺栓断裂问题。
2 连杆螺栓2.1 化学成分分析断裂螺栓规格为M8×1.0×40-6h ,其强度等级为10.9级,螺栓材料SCM435,是JIS G4035—2003中的一种热轧钢线材,属于低合金结构用钢,主要合金元素是Cr 、Mo 。
表1列出JIS G4035—2003中SCM435化学成分标准要求和断裂螺栓的化学成分分析结果,符合要求。
发动机连杆螺栓断裂失效分析叶枫,陈旺湘,胡志豪,马照龙浙江义利汽车零部件有限公司 浙江义乌 322000摘要:故障发动机被拆解之后发现固定连杆轴瓦的两根螺栓发生了断裂,通过对断裂螺栓进行宏观观察、SEM 显微分析以及对断口附近材料进行材质分析,研究确认连杆螺栓的断裂形式、原因,并提出相关改进措施。
结果表明:连杆螺栓断裂性质属于疲劳断裂,其中一根螺栓是完全疲劳断裂,另一根是部分疲劳和部分剪切断裂。
什么原因导致端子断裂?端子断裂失效分析

什么原因导致端⼦断裂?端⼦断裂失效分析⼀站式的材料检测、分析与技术咨询服务什么原因导致端⼦断裂?端⼦断裂失效分析美信检测失效分析实验室1. 案例背景失效样品为某汽车接地线束的固定端⼦,⽣产流程为:原料铜管→裁剪→冲压成型→表⾯镀锡→装配→振动试验(19万次)→断裂;其可靠性测试中6个成品经振动试验19万次后其中⼀个断裂,委托⽅要求分析该断裂失效端⼦的失效机理,并给出改进建议。
2. 分析⽅法简述外观检查中可观察到失效样品断裂的2部分能⽆缝对接,断裂位置在冲压形成的台阶折线处。
⼀站式的材料检测、分析与技术咨询服务将失效样品断⼝⽤超声波清洗⼲净,然后在SEM下放⼤观察断⼝形貌,⾼倍下发现断⼝存在明显的疲劳条带;低倍下观察到断⼝两侧低中间⾼,为两侧先开裂再向中间扩展形成的中间凸起断⼝形貌,结合据委托⽅提供的样品振动19万次后断裂信息,判断样品为双向⾼周疲劳断裂模式。
失效样品先去镀层,再进⾏化学成分分析,结果表明失效样品材质为纯铜,材料不存在异常。
失效样品和正常样品分别镶样,进⾏⾦相分析,失效样品腐蚀前⾦相观察未发现明显缺⼀站式的材料检测、分析与技术咨询服务陷,腐蚀后可观察到⼤变形区域的纤维状α相,⼩变形量区域为α相组织,伴有较多孪晶;正常样品腐蚀前⾦相观察发现样品表⾯的折弯处存在微裂纹,裂纹填充满锡,推断裂纹为冷加⼯成型造成的,腐蚀后可观察到⾦相组织为α相组织,伴有较多孪晶。
3. 分析与讨论从断⼝分析可知,样品断⼝形貌主要为⾼周期疲劳断裂特征,根据客户提供的震动试验资料,样品试验过程是振幅为12mm左右的周期振动,19万次后断裂,符合低应⼒⾼疲劳周期的双向⾼周疲劳断裂特征,两侧裂纹⽆锡填充,说明为镀锡后开裂,为冷机加⼯造成应⼒折叠形成的开裂。
从化学成分可知失效样品的铜含量在99.99%,材质为纯铜,材料不存在异常。
⼀站式的材料检测、分析与技术咨询服务从⾦相图⽚可知,失效样品与正常样品的⾦相组织都为α相组织,伴有较多孪晶,为冷机加⼯残留内应⼒较⼤的特征;正常样品可观察到填充锡的微裂纹,为冷机加⼯缺陷,这些表⾯微裂纹可能会成为开裂源。
发动机凸轮轴断裂失效分析和预防
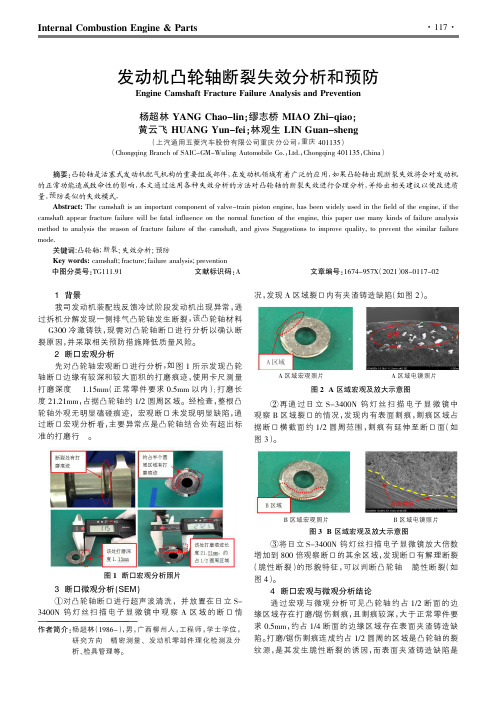
———————————————————————作者简介:杨超林(1986-),男,广西柳州人,工程师,学士学位,研究方向为精密测量、发动机零部件理化检测及分析、检具管理等。
3断口微观分析(SEM)①对凸轮轴断口进行超声波清洗,并放置在日立S-3400N 钨灯丝扫描电子显微镜中观察A 区域的断口情②再通过日立S-3400N 钨灯丝扫描电子显微镜中观察B 区域裂口的情况,发现内有表面割痕,割痕区域占据断口横截面约1/2圆周范围,割痕有延伸至断口面(如图3)。
③将日立S-3400N 钨灯丝扫描电子显微镜放大倍数增加到800倍观察断口的其余区域,发现断口有解理断裂(脆性断裂)的形貌特征,可以判断凸轮轴为脆性断裂(如图4)。
4断口宏观与微观分析结论通过宏观与微观分析可见凸轮轴约占1/2断面的边缘区域存在打磨/锯伤割痕,且割痕较深,大于正常零件要求0.5mm ,约占1/4断面的边缘区域存在表面夹渣铸造缺A 区域宏观照片A 区域电镜照片图2A 区域宏观及放大示意图图1断口宏观分析照片B 区域宏观照片B 区域电镜照片图3B 区域宏观及放大示意图进一步加速凸轮轴断裂的诱因。
凸轮轴断口裂源区的表面打磨割伤痕迹会引起应力集中,加速初期裂纹的形成,渣铸造缺陷会加剧裂纹扩展,最终导致凸轮轴整体发生快速的解理断裂(脆性断裂)。
分析认为,大面积较深的打磨锯伤割痕是造成凸轮轴发生脆性断裂的诱因。
黑色箭头是裂纹扩展方向,详见图5。
其余性能检测硬度检测AFFRI LD300布氏硬度计对断裂凸轮轴硬度个检测点进行硬度检测,检测数据见表1,其硬度要求为207~262HBW,实测平均值为238.50HBW,检测结果合格。
金相检测Leica DMI3000M金相显微镜对做好的断口样件进行金相分析,对腐蚀前的断口样件进行放大所示,对照相关图谱可以样件的石墨类型为:脆断裂。
②断裂凸轮轴存在打磨/锯伤的现象,并超出打磨的要求,大面积较深的打磨/锯伤区域是本次凸轮轴断裂失效的主要原因,该原因主要是凸轮轴供应商对质量管控上的疏忽,未严格按照标准的要求进行打磨和修复作业。
汽车零部件断裂失效分析简述(岑举
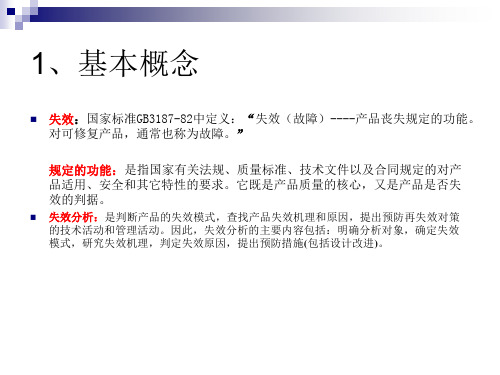
结构和配合的特性、载荷的性质和幅值、大多的内在质量缺陷、工作 和运行的状态、应力状态等等,都属于力学分析的范畴。他们不仅决 定了是否开裂,还总体上决定了以什么形式或在什么部位开裂。
设计的使用应力(各种指标)和强度(各种指标)技术条件;
关注实际的使用应力(工况)及制造质量分布的偏移和变化; 两者分布曲线相交则产生失效。 目前的失效分析和认知程度、评价主要还是在定性的水平上。
技术条件 设计应力
制造质量 使用应力、工况
2.5 断裂分析要素
从可靠性理论中断裂的应力模型得知,应力和强度是断裂分析的两大 要素,两个要素中哪一个贡献较大?最为活跃?如何地感知和评价是 断裂分析中的一个焦点;
关于灰色系统
是对内部结构可以部分了解或可以综合运用逻辑推理的方法进行 分析的系统。
从人类实践的绝对性来看,人类可以穷尽对机电失效规律及其预 防的认识,但从对失效分析的个别实践和认识来看,又总是在有 限的空间内进行的。因此,对失效特点和规律的认识又往往是有 限的和相对的,这就决定了失效分析的研究和发展总是处于一 个灰色系统内。 (失效分析的持续性、阶段性、可认知性和无止境性) (失效分析的病理学研究方法和流行病学研究方法)
式等原因引发局部产生微动磨损现 象,导致疲劳开裂。这类问题在轴 孔配合结构中最多体现。
疲劳断裂
案例20、某连杆销孔疲劳开裂 在挤压载荷作用下的疲劳开裂; 表现出了对油孔边缘处应力集中
的敏感性。
疲劳断裂
案例22、剪切应力疲劳开裂
半轴、钢板弹簧等零件,产生在高强韧性的零件中; 属于应变疲劳的性质,也称为高应力低周疲劳; 扭转的应力状态更有部件及断裂失效特性
- 1、下载文档前请自行甄别文档内容的完整性,平台不提供额外的编辑、内容补充、找答案等附加服务。
- 2、"仅部分预览"的文档,不可在线预览部分如存在完整性等问题,可反馈申请退款(可完整预览的文档不适用该条件!)。
- 3、如文档侵犯您的权益,请联系客服反馈,我们会尽快为您处理(人工客服工作时间:9:00-18:30)。
压板刚性约束
钢板弹簧中心孔断裂
结构特性: 钢板弹簧由多片不等长和不等曲率的钢板叠合而成。 U形螺栓以内为“平直段”,装配后使板簧稳定,工作中不承受弯曲载 荷。 中心孔为总成装配的工艺孔。 分析要点: 作为简支梁结构,如果板簧的平直段承受弯曲载荷,发生弯曲变形,其 中心孔部位弯矩最大,有效截面最小,加之应力集中,该部位最大弯曲应力 会数倍于其他部位的正常工作应力。 开裂特性: 为高应力低周弯曲疲劳断裂,疲劳源在孔边缘处,疲劳区很小; 分多片簧和少片簧两类,影响因素不同。
钢板弹簧疲劳开裂
• •
钢板弹簧早期高应力低周疲劳断裂; 裂纹源起源于材料内部的大块夹杂处, 夹杂的主要成分是Al、Mg、Ca、O等元素 。
汽车零部件脆性断裂
• 零件的脆性断裂也较为常见,材料的性质是重要的 条件之一,但实际情况中硬性应力状态更重要,即 指双向拉应力状态。该应力状态限制了材料的塑性 变形条件而产生脆性断裂。 • 脆性断裂不等于材料脆性,应力状态(平面应变) 的影响更大。
与结构件失效相关的约束
• 螺栓锁紧约束(压紧约束、摩擦约束) • 刚性约束 • 间隙约束(轴承间隙、轴颈间隙约束)
• 机械结构中,结构件靠约束以驱使或保证其完成特定的功能,其特定 的约束条件一旦破坏或丧失,会破坏其运行或运动状态,产生异常或 是附加的工况 ,使得结构件承担了不应有、无法承受的载荷,产生异 常的力学状态,引起疲劳开裂失效。
案例2 少片弹簧中心孔疲劳断裂
失效特征及原因
少片弹簧疲劳断裂的性质与多片簧相同; 由于少片簧的结构特点,中间段的刚性相对较 低(没有凸出的平直段),其平直段的刚度需要板 簧压板协助予以保证。 该类型的疲劳开裂与弹簧压板的疲劳断裂和弯 曲变形相伴发生; 板簧平直段和板簧压板抗弯刚性和强度不足, 导致板簧平直段以及板簧压板承受异常的弯曲载荷 是引起板簧中心孔疲劳断裂的原因。载荷过大也应 该考虑。
案例1 多片簧中心孔疲劳断裂
失效特征及原因 为高应力低周疲劳开裂,疲劳源位于中心孔内角处,疲劳区很小, 与板簧的冲击性载荷相对应; 在双驱动桥结构的板簧上更多见,而且多发生在最短的几片板簧 上;(这可能主要与该类弹簧的刚性较大有关) 断裂的原因是由于U形螺栓未能有效地锁紧或是松动,引起中心孔 承受附加弯矩。
脆性断裂断口
钢板弹簧脆性断裂
• 钢板弹簧脆性弯曲断裂,裂纹 源区为萘状断口; • 近表面处局部沿晶、粗大的微 裂纹,并伴随有氧化脱碳现象; • 为热处理过烧所致。
汽车零部件断裂失效分析
约束失控
约束(constraint) 对质点系中各“质点(结构件)”的位置和速度预先施加的几 何学或运动学的限制。 常见的约束有柔性绳索或链条约束、光滑接触面约束、圆柱形 铰链和球形铰链约束、铰链支座约束等。约束限制质点系中各质点 的自由运动,故约束对质点系有作用力,称约束反力,简称约束力。
钢板弹簧中心孔疲劳开裂
• 关注约束的有效性; • 断裂力学要素:简支梁弯矩 最大部位、应力集中、应变 集中。 • 同时也应考虑少片簧平直段 的自身刚性和约束结构刚性。
钢板弹簧压板边缘处疲劳断裂
• • 关注局部异常的表面异常硬化会增加疲劳裂纹萌生的敏感性。 考虑异常的擦伤、表面挤压磕碰伤与表面强力喷丸有什么差别或作用。
4 汽车零部件疲劳断裂分析
4.1疲劳断裂形式
• • 断口分析是疲劳分析的重要环节,包括结构、应力分布场、载荷 形式、异常工况、应力的大小等因素特征都会有所体现; 也要关注断口或失效性质的转化及相关的条件。
疲劳断口形态
疲劳断口形态
贝壳纹形成机理
关注那些随机 性冲击载荷、 台架试验的连 续不变的载荷 和铸铁的疲劳 断口,有时并 不十分典型。
钢板弹簧疲劳断裂与磕碰伤
• 轧制过程中磕碰伤引起疲劳断裂。
板簧前卷耳疲劳开裂
• 关注冲击载荷的作用,关注车辆的动力和制动性能,道路情 况,关注断裂的部位和结构特性; • 关注对失效认识的不断深化和少片簧的中间段刚性不足,如果与板簧中心孔断裂有关则应该有异常 接触印记; • 压板的弯曲在先,实际的失效形式应该是弯曲,要点是弯曲的连续性, 交通肇事的弯曲脆断中会有断裂件弯曲的一类问题。