石化行业公用工程资源的集成管理与优化案例-炼化企业公用工程系统智能优化技术
炼化企业公用工程系统管理

2.循环水 进水温度 回水温度 进水压力 回水压力 污垢系数
3.脱盐水 PH值 硬度 电导率(25℃) 二氧化硅 铁 铜 压力 温度
≤32℃ 42℃ 0.38-0.44MpaG 0.18-0.24MpaG ≤5×10-4m2.K/W
7-9 0
≤0.2μs/cm ≤0.02mg/l ≤0.02ppm ≤0.01ppm 0.5-0.85MpaG 常温
E.节约锅炉自用汽。利用炼油厂大量的工艺余热 预热,以节约不同压力等级的蒸汽。这项措施在我 国炼油厂已不同程度地推广应用。(本企业自用汽将 幅明显)
F.建立蒸汽管网智能检测系统,优化蒸汽管网运 行管理。良好的保温隔热,与流量匹配的管径设计 选择,合理的管网设计、布置,必要的温度、压力、 流量检测及远程监控仪表的设置,和应用计算机集 成蒸汽供应调度管理系统软件,可以使蒸汽管网的 散热和压降损失大幅度降低。调度通过监控实时掌 握管网的运行情况以及热量损失情况,及时调整供 汽压力、流量以及供汽方式等。这是蒸汽动力系统 优化的重要部分,也是企业节能降耗的有效措施。
3.炼化企业蒸汽动力系统优化措施
蒸汽是石化企业主要的能源之一,其蒸汽管网
大都形成了多环、多级、网状的复杂结构。管网内 部缺少温度、压力、流量等参数的测量点,至使管 理工作很大程度上依靠调度的经验,有时对管网流 程和操作工况的调整显得颇为被动;甚至蒸汽流向、 流量不明,蒸汽降质使用,放空现象得不到遏止, 造成能源浪费。(本企业就存在低压蒸汽放空的现象)
一般从以下几方面去考虑:
(1)提高转换效率,降低供汽能耗 提高锅炉 参数、实行热电联供,采用真空除氧和排汽回收利 用等技术。停开低压锅炉,而代以中压锅炉供汽 (一部分低压蒸汽由装置余热产生),可以使燃料 的热火用率提高10%以上。(本企业就是尽量压限低 压蒸汽产量)
青岛炼化打造数字化炼油厂

青岛炼化打造数字化炼油厂随着我国石油化工领域市场竞争的日益激烈,企业对安全运行、节约成本、降低污染、高效生产投入了越来越多的关注,对于大型炼化项目而言,DCS控制系统肩负着数据采集、优化流程、数据查询、事故分析等重任,是全流程控制的中枢核心。
中国石化青岛炼油化工有限责任公司(简称青岛炼化公司)坐落于风景优美的青岛经济技术开发区重化工园区,是中石化公司近年来重点投资建设的一座新型炼油厂。
青岛炼化公司一期1000万t/a炼油项目作为我国获批的第一个单系列千万吨级炼油项目,拥有目前国内最先进的炼油装置并采用了各种先进工艺设备,总投资共计103亿元,每年成品油产量超过700万t。
青岛炼化一期项目按照“大型化、系列化、集约化、信息化”的理念进行规划,建设包括1000万t/a常减压蒸馏、410万t/a柴油加氢精制、320万t/a加氢处理、290万t/a催化裂化及250万t/a延迟焦化等16套主要装置及相配套的储运系统、公用工程系统,项目规模和技术含量均达到国际先进水平。
该项目DCS系统集成规模(I/O点)达近4万点,工艺复杂,规模庞大,对DCS的数据处理能力、网络通信速度和系统开放性等要求远远超过一般项目。
全集成自动化理念2006年,青岛炼化在全厂DCS控制系统的项目筹备之初就把目标设定为“建立基于联合装置的数字化炼油厂”。
联合控制、安全集成青岛炼化针对大型联合生产装置的特点,对于控制系统采用了紧凑集中的布局方式。
全厂工艺装置的DCS 与安全仪表系统(SIS)、火灾和气体监测系统(FGS)、压缩机控制系统(CCS)等系统共用一个中央控制室,并且均通过DCS进行集中操作、控制和管理。
现场信号以就近的原则接入各个现场机柜室,再采用光纤通信传送至中控室,这样在大量节省电缆支出的同时可实现对不同生产装置的独立控制,在信息管理层面上它们又相互连接,组成全厂互联的自动化结构,实现了高度灵活的统一管理和调度架构。
安全是炼化企业的最为关注的主题之一,因而该项目采用一台OPC服务器作为DCS和MES两大系统间连接的数据接口,并设置了两道防火墙进行安全防护,构成一个大型冗余环形网结构。
化工系统工程在大型炼化一体化企业管理优化中的策略与模型

化工系统工程在大型炼化一体化企业管理优化中的策略与模型化工系统工程是一门综合性学科,通过运用系统理论和工程技术的知识与方法,对化工生产过程进行系统分析、设计、优化与控制。
在大型炼化一体化企业中,化工系统工程的应用可以提供有效的管理优化策略与模型,帮助企业实现资源高效利用、能耗降低、安全生产和环境保护的目标。
一、化工系统工程在大型炼化一体化企业中的应用大型炼化一体化企业涉及多个化工生产过程,包括原料处理、催化剂制备、反应器设计、装置运行和产品分离等。
通过应用化工系统工程的理论和方法,可以对这些过程进行模拟、优化和控制,实现企业的管理优化。
1.1 过程模拟和设计化工系统工程可以开展对生产过程的模拟和设计工作。
通过建立模型,可以分析、预测和评估不同操作条件对生产过程的影响,从而为工艺参数的优化和控制提供依据。
例如,在炼油生产中,可以通过模拟和设计工作确定最佳的操作温度、压力和催化剂用量,以提高产品质量和产量。
1.2 资源优化和能耗降低在大型炼化一体化企业中,资源优化和能耗降低是重要的管理目标。
化工系统工程可以通过优化调度和控制策略,实现资源的高效利用和能耗的降低。
例如,在石化企业中,可以通过合理的物料配送和设备优化配置,降低能耗和原料损耗。
1.3 安全生产和环境保护安全生产和环境保护是大型炼化一体化企业的重要任务。
化工系统工程可以通过建立安全评估模型和优化控制策略,提高生产过程的安全性和环境友好性。
例如,在化工企业中,可以通过建立模型和优化算法,实现对危险品储存和转运等环节的安全监控和管理。
二、化工系统工程在大型炼化一体化企业管理优化中的策略针对大型炼化一体化企业的管理优化,可以采用以下策略:2.1 数据采集与分析通过建立和完善数据采集系统,及时获取生产过程中的各项数据,并进行有效的分析。
基于数据分析结果,可实现对生产过程的监控和控制,及时发现问题和异常,并采取相应措施进行调整。
2.2 模型建立与优化建立生产过程的模型,并通过优化算法对模型进行求解,得到最佳的操作参数和控制策略。
过程系统集成在化工中的应用

过程系统集成在化工中的应用在化工领域,过程系统集成是一项至关重要的技术,它为优化化工生产流程、提高资源利用率、降低能耗和减少环境污染等方面发挥着关键作用。
过程系统集成,简单来说,就是将化工生产过程中的各个单元操作和设备进行合理的组合与协调,以实现整个系统的最优性能。
它不仅仅是简单地把各个部分拼凑在一起,而是要通过深入的分析和设计,使得整个化工生产系统达到高效、稳定和可持续的运行状态。
首先,过程系统集成在能源管理方面有着显著的应用。
在化工生产中,能源消耗通常是一个巨大的成本因素。
通过对生产过程中的能量流动进行分析和优化,可以实现能源的高效利用。
例如,采用热集成技术,将高温工艺流股的热量传递给低温工艺流股,从而减少对外部加热和冷却介质的需求。
这样的设计不仅降低了能源消耗,还降低了生产成本。
在物料回收与再利用方面,过程系统集成也表现出色。
化工生产中会产生大量的副产物和废弃物,如果不加以合理处理,不仅会造成资源的浪费,还会对环境造成严重的污染。
通过系统集成,可以建立有效的物料回收和循环利用系统。
例如,在某个化工生产流程中,对未反应完全的原料进行回收和再处理,使其重新进入生产流程,提高原料的利用率,减少废弃物的排放。
过程系统集成还能够优化化工生产的工艺流程。
通过对各个单元操作的分析和整合,可以去除不必要的步骤,简化流程,提高生产效率。
比如,在传统的生产工艺中,可能存在一些繁琐的中间环节,经过系统集成的优化,可以直接将两个相关的操作合并,减少设备投资和操作成本。
此外,过程系统集成在提高化工生产的安全性方面也发挥着重要作用。
通过对整个生产系统进行全面的风险评估和分析,可以识别潜在的危险点,并采取相应的预防措施。
例如,合理设计管道布局和压力控制系统,避免物料泄漏和爆炸等事故的发生。
在实际应用中,过程系统集成需要借助先进的软件工具和模拟技术。
这些工具可以帮助工程师对复杂的化工系统进行建模和分析,预测不同设计方案的性能和效果。
EIP炼油厂公用工程数据采集系统解决方案-管理资料

EIP炼油厂公用工程数据采集系统解决方案-管理资料一、系统概述大型炼油厂是加工工艺齐全,生产规模大的燃料、化工原料型企业,其许多生产装置由于应用了DCS,自动化水平很高,并且各装置的工程数据已纳入全厂的CIMS系统,。
但是水、电、气、暖等公用工程数据以及罐区数据、进出厂数据却是独立的,仍靠统计人员汇总,不适应现代化管理的要求。
为了准确且迅速地掌握并利用全厂信息,对生产状况进行有效的统筹平衡管理,优化资源配置,提高企业的经济效益,有必要建立“炼油厂全厂公用工程数据采集系统”将相对分散的数据先集中到计量中心,搞好物料平衡,再通过光纤进入全厂CIMS系统。
二、系统原理本系统软件由上位机系统软件和下位机软件两大部分组成,均采用C语言及汇编语言编写。
具有界面友好、实时性好、人工干预少、使用简单方便等优点。
全部软件的设计采用模块化方法,每一个模块完成某一功能,遵循并符合“自顶向下”的软件设计原则。
三、上位机功能:1、主要配置:机箱:IPC-810A/6113LP4/7271AT主板:FSC-1713VNA配件:P42.4/256M/80G2、功能实现:上位机主机采用工业PC机,并配备有打印机和大屏幕监视器。
上位机系统软件的主要功能是通过通信网络实现上位机与下位机间的数据传输,以及将下位机实时采集的数据进行各种处理,包括存入数据库、进行流图显示、历史趋势图和棒形图还有数据表的显示及各种要求的报表打印输出,管理资料《EIP炼油厂公用工程数据采集系统解决方案》(https://www.)。
3、上位机系统软件分成以下模块1)主模块:主要用于完成对整个系统各子功能的控制及调度。
2)流程图显示功能模块:主要完成各个工作区域的流程图和相应参数变化情况的显示。
3)历史趋势及棒形图显示模块:实现历史生产状况的趋势再现和与之对应时间点的棒形图及数据表格显示。
4)数据采集及通信模块:主要完成通信链路的建立及数据采集和传输。
数据采集及通信是本系统的核心。
信息化解决方案在石化行业企业级应用中的案例分析
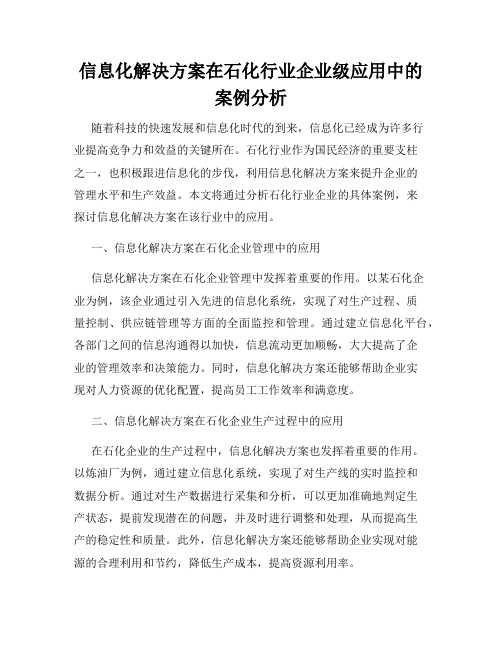
信息化解决方案在石化行业企业级应用中的案例分析随着科技的快速发展和信息化时代的到来,信息化已经成为许多行业提高竞争力和效益的关键所在。
石化行业作为国民经济的重要支柱之一,也积极跟进信息化的步伐,利用信息化解决方案来提升企业的管理水平和生产效益。
本文将通过分析石化行业企业的具体案例,来探讨信息化解决方案在该行业中的应用。
一、信息化解决方案在石化企业管理中的应用信息化解决方案在石化企业管理中发挥着重要的作用。
以某石化企业为例,该企业通过引入先进的信息化系统,实现了对生产过程、质量控制、供应链管理等方面的全面监控和管理。
通过建立信息化平台,各部门之间的信息沟通得以加快,信息流动更加顺畅,大大提高了企业的管理效率和决策能力。
同时,信息化解决方案还能够帮助企业实现对人力资源的优化配置,提高员工工作效率和满意度。
二、信息化解决方案在石化企业生产过程中的应用在石化企业的生产过程中,信息化解决方案也发挥着重要的作用。
以炼油厂为例,通过建立信息化系统,实现了对生产线的实时监控和数据分析。
通过对生产数据进行采集和分析,可以更加准确地判定生产状态,提前发现潜在的问题,并及时进行调整和处理,从而提高生产的稳定性和质量。
此外,信息化解决方案还能够帮助企业实现对能源的合理利用和节约,降低生产成本,提高资源利用率。
三、信息化解决方案在石化企业供应链管理中的应用石化企业的供应链管理也是一个复杂的系统工程,信息化解决方案在其中发挥着关键作用。
以某石化企业为例,通过引入信息化系统,实现了对供应链各个环节的实时监控和协调。
通过对供应商和分销商的信息进行采集和整合,可以实现供应链的透明化和可视化,提高协同效应,降低物流成本,并及时响应市场需求的变化。
此外,信息化解决方案还可以帮助企业实现对库存、销售和客户信息的整合和分析,提高对市场的敏感度,优化供应链配置,提高综合竞争力。
综上所述,信息化解决方案在石化行业企业级应用中发挥着重要作用。
炼化企业公用工程智能管控平台开发与应用

自动化仪表PROCESS AUTOMATION INSTRUMENTATION Vol.40No.8Aug.2019第40卷第8期2019年8月炼化企业公用工程智能管控平台开发与应用涂阳勤1,李瑞红2,王宽心1,王星棋2,韩文巧1(1.浙江中控软件技术有限公司,浙江杭州310053;2.中国石油化工股份有限公司洛阳分公司,河南洛阳471012)摘要:针对炼化企业公用工程系统的运行现状和存在的问题,开发了公用工程智能管控平台。
该平台基于化验分析数据,构建低压瓦斯排放量测算模型,实现对低压瓦斯排放量的测算。
同时,采用管网模拟手段,实现了管网中任意管段介质流速、压降、温降、燃料气热值、持液率等重要参数的软测量。
通过构建反向传播(BP)神经网络模型,预测未来一段时间内生产装置公用工程的产耗量。
以未来时间段内各生产装置公用工程的产耗预测数据为基础,以生产运行成本最低为目标,建立平衡调度优化模型,采用非线性规划算法进行寻优求解,实现公用工程的优化调度。
该平台系统通过构建实时监控、统计分析、绩效考核、管网模拟、产耗预测和调度优化等功能模块,实时监控公用工程从生产、存储、输送到回收消耗的全过程,减少了低压瓦斯的异常排放,提高了公用工程的资源利用率,为炼化企业的节能环保、挖潜增效发展战略提供强有力的支撑。
关键词:公用工程;智能管控;软测量;管网模拟;产耗预测;调度优化;神经网络;非线性规划中图分类号:TH-39文献标志码:A DOI:10.16086/ki.issnl000-0380.2018100025Development and Application of Intelligent Management and Control Platform for Utility Engineering in Refining and Chemical EnterprisesTU Yangqin1,LI Ruihong2,WANG Kuanxin1,WANG Xingqi2,HAN Wenqiao1(1.Zhejiang SUPCON Software Co.,Ltd.,Hangzhou310053,China;2.Luoyang Branch,China Petroleum Chemical Co.,Ltd.,Luoyang471012,China)Abstract:Aiming at the current operation status and existing problems of utility engineering systems in refinery and chemical enterprises,an intelligent management and control platform has been developed.The platform built a model of low-pressure gas emission based on laboratory analysis data,and realized the estimation of low-pressure gas emissions.At the same time,it realized soft sensing of important parameters such as medium flow rate,pressure drop,temperature drop,calorific value of fuel gas and liquid holdup in any section of the pipeline network by means of pipeline network simulation.The yield and consumption of utility engineering in the next period of time can be predicted by constructing back propagation(BP)neural network model.Based on the forecast data of production and consumption in the future,a balanced scheduling optimization model is established with the objective of lowest operation cost.The optimal scheduling of utility engineering can be implemented by using the non-linear planning algorithm.By building functional modules of real-time monitoring,statistical analysis,performance appraisal,pipeline network simulation,production and consumption prediction and scheduling optimization,the platform system can monitor the whole process of utility engineering ranging from production,storage,transportation to recovery,reduce the abnormal discharge of low-pressure gas and improve the utilization rate of resources.The platform provides strong support for energy saving,environmental protection,and the development strategy of mining potential and increasing efficiency of refining and chemical enterprises. Keywords:Utility engineering;Intelligent management and control;Soft sensing;Pipe net simulation;Production and consumption prediction;Scheduling optimization;Neural network;Nonlinear planningo引言炼化企业的公用工程包括常见的公用介质,如瓦斯、氢气、蒸汽等。
WN石化公司的ERP系统案例及案例分析

WN石化公司的ERP系统案例及案例分析一、引言随着全球化和信息化的发展,企业资源规划(ERP)系统已经成为现代企业管理的重要工具。
本文以WN石化公司为例,探讨其ERP系统的实施过程、取得的成效以及可能存在的问题,为其他企业提供参考和启示。
二、WN石化公司ERP系统实施背景WN石化公司是一家集石油勘探、生产、销售于一体的国有企业。
随着市场竞争的加剧和信息化的发展,公司决定引入ERP系统以提高管理效率、降低运营成本、优化资源配置。
三、ERP系统实施过程1、需求分析:明确公司的管理需求,确定ERP系统的功能模块。
2、系统选型:根据需求分析结果,选择合适的ERP系统。
3、实施规划:制定详细的实施计划,包括培训、数据准备、系统测试等。
4、培训与推广:对员工进行ERP系统的培训和推广,提高员工的意识和技能。
5、系统上线:完成系统测试后,正式上线运行。
四、ERP系统实施成效1、提高管理效率:通过ERP系统,各部门之间的信息传递更加顺畅,减少了重复劳动,提高了管理效率。
2、降低运营成本:ERP系统实现了业务流程的自动化处理,降低了人力成本和运营成本。
3、优化资源配置:ERP系统实现了对资源的实时监控和数据分析,为企业决策提供了有力支持,优化了资源配置。
4、提升客户满意度:通过ERP系统,企业能够更好地掌握客户需求和市场变化,提高了客户满意度。
五、ERP系统实施中可能存在的问题1、技术风险:ERP系统的实施需要强大的技术支持,如果技术能力不足,可能会影响系统的稳定性和可靠性。
2、数据质量:ERP系统的数据质量直接影响到企业的决策和运营,如果数据质量不高,可能会给企业带来损失。
3、员工接受度:ERP系统的实施需要员工的积极参与和支持,如果员工对系统的接受度不高,可能会影响系统的实施效果。
4、成本问题:ERP系统的实施需要投入大量的资金和人力成本,如果成本控制不当,可能会给企业带来负担。
六、结论与启示通过对WN石化公司ERP系统的案例分析,我们可以看到ERP系统在企业管理和运营中的重要作用。
- 1、下载文档前请自行甄别文档内容的完整性,平台不提供额外的编辑、内容补充、找答案等附加服务。
- 2、"仅部分预览"的文档,不可在线预览部分如存在完整性等问题,可反馈申请退款(可完整预览的文档不适用该条件!)。
- 3、如文档侵犯您的权益,请联系客服反馈,我们会尽快为您处理(人工客服工作时间:9:00-18:30)。
炼化企业公用工程系统智能优化技术
技术适用范围
适用于石化行业炼化企业、石化基地、化工园区公用工程资源的集成管理与优化。
技术原理及工艺
本技术包括氢气系统智能优化技术和蒸汽动力系统智能优化技术。
氢气系统分为供需子系统和回收子系统,通过分步建模及协同优化,建立氢气全系统优化模型,解决模型求解难的问题,形成了集成反应动力学供需子系统建模技术、氢气-轻烃-瓦斯三元协同优化技术等,并在此基础上结合数据采集处理技术和管网模拟优化技术开发了氢气系统智能优化平台,实现氢气资源的梯级利用,提高系统氢气利用效率,减少产氢装置供氢,节省燃料消耗及电耗,减少CO2排放;蒸汽动力系统智能优化技术是开发动力站锅炉、汽轮机、辅机等主要装置模型,通过联立方程法对系统进行计算求解,实现动力站系统的模拟。
同时,采用联立方程法对动力站与蒸汽管网进行系统集成,实现蒸汽产-输-用集成建模与优化。
在线模拟与优化平台建设技术原理图:
技术指标
(1)软件计算结果误差<3%;
(2)提高企业氢气系统氢气利用效率5~15%;
(3)降低企业蒸汽动力系统能耗3%。
技术功能特性
开发了大型复杂多源多阱蒸汽管网、热力系统及大机组数学建模及求解方法,开发了集成热电单元和蒸汽输送管网单元的蒸汽动力系统模拟优化软件(F-SET),实现了全厂蒸汽动力系统建模与集成优化。
与国内外同类软件相比,一是实现动力站-管网-装置整体建模与集成优化;二是区别于其他建模软件虚拟流股,创新性地采用管网的概念,更加贴合现场实际情况;三是实现系统的实时模拟与诊断,对企业优化操作、精益化管理提供支持。
应用案例
金陵石化分公司氢气系统智能优化项目。
技术提供单位
为中国石油化工股份有限公司大连石油化工研究院。
(1)用户用能情况简单说明
金陵公司1#PSA装置用来提浓1#、2#重整装置产氢及部分加氢装置废氢,装置操作压力 1.2MPa,产品氢压
力1.1MPa,由于耗氢装置需求,配置产品氢压机将压力升至2.6MPa,另外配置解吸气压缩机回收解吸废气,装置能耗高。
1#PSA下游装置为柴油加氢,对氢气纯度要求并不高。
过量提纯重整氢,不仅造成氢气浪费,同时使得装置能耗居高不下。
(2)实施内容及周期
结合金陵石化要求制定不同投资力度下的氢气系统改
造方案,并模拟计算。
针对投资方案中涉及的新增设备、改造设备等,进行经济核算,确定投资费用,并对氢网系统
优化方案进行校核。
实施周期12个月。
(3)节能减排效果及投资回收期
改造后,通过利用氢气系统智能优化技术对金陵公司氢
气系统开展梯级利用及加氢装置用氢优化,节约氢气2057.5Nm3/h,与优化前相比,电功耗增加238kW,减少供氢带来的节能量=氢气体积流量×密度×运行时间×氢
气标煤转换系数=2219.6tce;电耗增加带来的能耗折算标
煤为971.1tce,系统节能量为1248.5tce/a。
投资回收期约4个月。
未来五年推广前景及节能减排潜力
预计未来5年,推广应用比例可达到30%,可形成节能37.5万tce/a,减排CO2101.25万t/a。