催化裂化(分析的很全面)
催化裂化装置烟气脱硫系统结垢原因分析及应对措施

催化裂扮装置烟气脱硫系统结垢原因分析及应对措施引言在石油化工生产过程中,催化裂扮装置广泛应用于石化行业中,它能够将重油转化为轻油和石油气,满足日益增长的能源需求。
然而,催化裂扮装置烟气脱硫系统在运行过程中会产生结垢问题,严峻影响设备的正常运行和脱硫效果。
本文将对催化裂扮装置烟气脱硫系统结垢问题的原因进行分析,并提出相应的应对措施。
一、催化裂扮装置烟气脱硫系统结垢原因分析1. 硫酸铵结垢烟气脱硫系统中使用的吸纳液中常含有硫酸铵,随着脱硫液循环使用,硫酸铵溶液中的硫酸铵会被氧化生成硫酸,而硫酸在高温环境中溶解度较低,容易结晶沉积在设备内壁上。
2. 碳酸钙结垢烟气脱硫液中常含有一定量的钙离子,烟气中的二氧化碳与钙离子反应生成碳酸钙,而碳酸钙在高温条件下结晶沉积,导致结垢问题。
3. 硫酸钙结垢烟气脱硫液中的硫酸钙浓度过高,超过了饱和度,或者温度提高时,硫酸钙会从溶液中析出结晶,生成结垢。
二、催化裂扮装置烟气脱硫系统结垢应对措施1. 控制吸纳液质量提高吸纳液性能,控制吸纳液中硫酸铵的浓度,缩减硫酸铵被氧化的速度。
增加吸纳液的循环次数,降低硫酸铵的浓度,缩减结垢的可能性。
2. 控制钙离子含量通过分析烟气成分,合理控制脱硫液中的钙离子含量,缩减碳酸钙的生成,降低烟气脱硫系统的结垢风险。
可以实行预处理方法,如提前剔除烟气中的二氧化碳等方法。
3. 降低硫酸钙浓度通过加强脱硫液的循环,增加氧化还原剂的投加量等方式,降低硫酸钙浓度,控制其不超过饱和度,缩减硫酸钙的析出。
4. 定期清洗结垢定期对烟气脱硫设备进行清洗,去除结垢,保证设备的通畅。
可以接受化学清洗或机械清洗等方式,依据结垢的状况选择合适的清洗剂和清洗方法。
5. 加强监测与维护加强对催化裂扮装置烟气脱硫系统的监测与维护,定期检查设备是否存在结垢状况,准时实行措施进行处理,防止结垢问题进一步恶化。
结论催化裂扮装置烟气脱硫系统结垢问题的产生主要与硫酸铵、碳酸钙、硫酸钙的析出有关。
催化裂化提高汽油收率操作分析

催化裂化提高汽油收率操作分析摘要:通过对催化裂化装置操作调整的分析,改善操作,有效提高汽油收率。
关键词:催化裂化;操作调整;汽油收率催化裂化装置的汽油是原油进提升管经过裂化反应,通过分馏塔组分切割,再经过吸收稳定精馏分离而出来的。
下面通过对装置操作调整分析,确定怎样来提高汽油收率。
本文从反应再生系统,分馏系统,吸收稳定系统三个方面的操作调整,分析对汽油收率的影响。
1.反应再生系统的操作1.1 反应温度催化裂化反应是吸热反应,反应温度升高有利于裂化反应的进行,由于我们反应温度一般投自动控制,提高反应温度的同时再生滑阀开大,增加催化剂循环量,增加催化剂活性中心,增加反应深度。
则提高反应温度,汽油收率增加。
但当反应温度提至很高时,热裂化反应趋于重要,汽油组分开始减少,干气组分明显增多。
表1 反应温度与汽油收率图1 反应温度与汽油收率由表1和图1中可以看出,其他条件不变时,提高反应温度,汽油收率增加.反应温度在504℃时,汽油收率最高。
505℃时,汽油收率开始下降,干气收率增加。
1.2急冷介质在反应温度不变情况下,提高汽油收率另一种手段就是在提升管反应部分喷入急冷介质,提高剂油比和反应深度,减少二次裂化和热裂化,从而提高汽油收率。
急冷介质一般用粗汽油或者水或者两者混合。
但急冷介质的喷入会影响系统的油气分压,分流塔产品质量的控制需相应调整。
1.3 再生温度本装置再生器采用重叠式两段再生型式。
两个再生器重叠布置,一段再生位于二段再生上面。
一再贫氧、CO部分燃烧;二再富氧再生、CO完全燃烧。
催化裂化反应所需热量是通过再生器内完全再生的热催化剂提供的,所以再生温度的高低也直接影响催化剂循环量的大小。
再生温度高则催化剂循环量降低,反应的催化剂活性中心减少,反应深度降低,汽油收率降低。
表2 再生温度与汽油收率图2再生温度与汽油收率由表2与图2可以看出其他条件不变时,汽油收率随再生温度升高而降低,但当再生温度降至670℃以下后,再生器烧焦效果变差,再生器稀相出现尾燃。
催化裂化原理

全世界 中国 美国 日本 西欧
4
4.1 概述
二、催化裂化的开展历程 催化裂化自1936年实现工业化至今经历了四个阶段: 固定床、挪动床、流化床和提升管。
Fixed Bed
Moving Bed
5
4.1 概述
Fluid Bed
H R C¨ C H
+ 特点:不能在溶液中离解出来自由存在;
只能吸附在催化剂外表上参加化学反响。
19
4.3 烃类的催化裂化反响
正碳离子形成:烯烃的双键中一个键断开,并在含H多的C 上加上一个H+,使含H少的另一个C缺少一对电子。
2、形成碳离子条件 (1)存在烯烃 来源:原料本身、热反响产生。 (2)存在质子H+ 来源:由催化剂的酸性中心提供。 H+不称氢离子,存在于Cat.的活性中心,不能分开Cat.外表。
34
4.3 烃类的催化裂化反响
没有考虑到反响深度对反响热的影响。 (3)以催化碳为基准表示。 催化碳指在催化裂化反响 过程中生成焦碳中的炭。 当反响T为510℃时,反响 热9127kJ/kg催化碳。 假设反响T不在510℃,需 乘以其它反响T下的校正系数。
35
4.3 烃类的催化裂化反响
催化碳的计算: 催化碳=总碳-附加碳-可汽提碳
24
4.3 烃类的催化裂化反响
(5)叠合反响 正碳离子和烯烃结合在一起,生成大分子正碳离子:
H CH3 CCH3 +H2C CH CH2 CH3
+ CH3 H
CH3 CHCH2 C CH2 CH3 +
(6)反响终止 正碳离子放出H+还给Cat.而变成烯烃,反响终止:
催化裂化装置非计划停工原因分析及
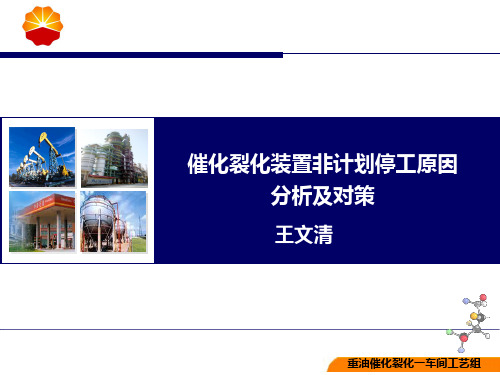
三、催化裂化装置非计划停工原因分析及对策
❖油浆系统结焦 • 油浆系统结焦原因 :
(1)油浆系统性质变差是油浆系统结焦的重要原因; (2)分馏塔温度变化时油浆系统结焦的直接原因。随 着油浆温度的升高,轻馏分逐渐蒸发,油浆浓缩,生焦性 能增加。同时,油浆中的烯烃、多环芳烃产生缩合反应, 当温度升高到一定值时,缩合反应速度会升高得很快。 (3)油浆的停留时间。当油浆在某一高温下停留时间 足够长时,油浆中将有焦炭生成。 (4)油浆流速过低,容易使缩合物沉积在管道表面结焦。
重油催化裂化一车间工艺组
三、催化裂化装置非计划停工原因分析及对策
❖油浆系统结焦 • 防范措施 :
(3)选用气蚀余量较大的机泵,避免油浆泵不上量而 引发大量催化剂沉积在分馏塔底。
(4)选用合适的油浆阻垢剂,从装置投用起连续注入, 防止油浆中不溶物附着在换热器的管壁。
(5)适当的外甩油浆,调节油浆排放物量以降低油浆 相对密度,控制油浆中稠环芳烃浓度。
重油催化裂化一车间工艺组
三、催化裂化装置非计划停工原因分析及对策
❖油浆系统结焦 • 防范措施 :
(6)降低循环油浆返塔温度,加大油浆返塔下 部入口量。用极冷油浆极冷,既可加强对塔底的冲 刷作用,防止催化剂堆积在分馏塔底的缓流区而结 焦,又可使塔底油浆快速降温,防止油浆组分因高 温聚合而结焦。
重油催化裂化一车间工艺组
一般意义的紧急停工是指装置部分设备或工艺生 产在故障状态下紧急切断提升管进料,维持分馏、 稳定部分油品循环,两器进行流化状态。如果设备 或生产故障短时间内解决不了,并有进一步扩大的 趋势,可将装置全面紧急停工。
重油催化裂化一车间工艺组
二、催化裂化装置紧急停工条件及处理原则
催化裂化知识

催化裂化知识催化裂化是一种重要的炼油工艺,通过催化剂的作用将重质石油馏分转化为轻质产品。
在催化裂化过程中,石油馏分经过加热后与催化剂接触,发生裂化反应,生成较轻质的烃类化合物。
催化裂化技术广泛应用于石油炼制行业,使得石油资源得以充分利用。
催化裂化的原理是通过催化剂的作用降低反应的活化能,加快反应速率。
催化剂是一种能够提供活性位点的物质,它能够吸附反应物分子并改变其化学键,从而促进反应的进行。
常用的催化剂有酸性催化剂、碱性催化剂和金属催化剂等。
在催化裂化过程中,石油馏分首先被预热至适宜的温度,然后进入催化剂床层。
在催化剂的作用下,石油馏分中的大分子化合物发生裂化反应,生成烃类产品。
裂化反应主要包括裂解、重排和异构化等过程。
裂解是指将长链烃分子裂解为短链烃分子,重排是指短链烃分子发生位置变化,异构化是指短链烃分子发生结构变化。
催化裂化的反应条件主要包括温度、压力和催化剂的选择等。
温度是影响催化裂化反应速率和产物分布的重要因素。
适宜的温度能够提高反应速率,但过高的温度会导致生成焦炭等副产物。
压力对催化裂化反应的影响相对较小,一般较低的压力即可满足反应的需求。
催化剂的选择对反应的效果有着重要影响,不同的催化剂对产品分布、产率和选择性有不同的影响。
催化裂化技术的应用使得石油炼制过程更加灵活多样,能够根据市场需求灵活调整产品结构。
通过合理的催化剂设计和反应条件控制,可以实现不同产品的选择性裂化。
催化裂化不仅能够提高汽油产率,还能够产生重要的石化原料,如乙烯、丙烯等。
催化裂化技术的发展也为石油炼制行业的绿色转型提供了重要支持。
然而,催化裂化过程中也存在一些问题。
首先,催化剂的失活是一个严重的问题,随着反应的进行,催化剂会逐渐失去活性,需要定期更换。
其次,催化裂化反应的过程较复杂,需要综合考虑反应的热力学和动力学特性,以及催化剂的选择和反应条件的控制。
此外,催化裂化过程中还会产生大量的副产物,如焦炭和烟气,对环境造成一定的污染。
催化裂化产品方案分析
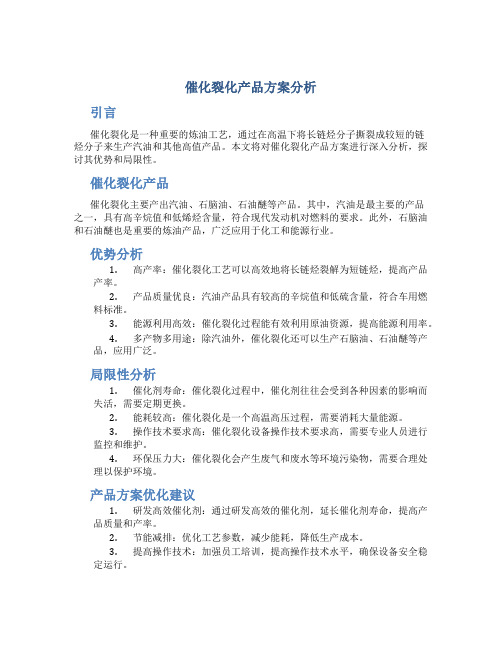
催化裂化产品方案分析引言催化裂化是一种重要的炼油工艺,通过在高温下将长链烃分子撕裂成较短的链烃分子来生产汽油和其他高值产品。
本文将对催化裂化产品方案进行深入分析,探讨其优势和局限性。
催化裂化产品催化裂化主要产出汽油、石脑油、石油醚等产品。
其中,汽油是最主要的产品之一,具有高辛烷值和低烯烃含量,符合现代发动机对燃料的要求。
此外,石脑油和石油醚也是重要的炼油产品,广泛应用于化工和能源行业。
优势分析1.高产率:催化裂化工艺可以高效地将长链烃裂解为短链烃,提高产品产率。
2.产品质量优良:汽油产品具有较高的辛烷值和低硫含量,符合车用燃料标准。
3.能源利用高效:催化裂化过程能有效利用原油资源,提高能源利用率。
4.多产物多用途:除汽油外,催化裂化还可以生产石脑油、石油醚等产品,应用广泛。
局限性分析1.催化剂寿命:催化裂化过程中,催化剂往往会受到各种因素的影响而失活,需要定期更换。
2.能耗较高:催化裂化是一个高温高压过程,需要消耗大量能源。
3.操作技术要求高:催化裂化设备操作技术要求高,需要专业人员进行监控和维护。
4.环保压力大:催化裂化会产生废气和废水等环境污染物,需要合理处理以保护环境。
产品方案优化建议1.研发高效催化剂:通过研发高效的催化剂,延长催化剂寿命,提高产品质量和产率。
2.节能减排:优化工艺参数,减少能耗,降低生产成本。
3.提高操作技术:加强员工培训,提高操作技术水平,确保设备安全稳定运行。
4.加强环保措施:加大对环保设施的投入,完善废气处理设施,降低环境影响。
结论催化裂化是一种重要的炼油工艺,可以高效生产汽油等产品,但也存在一定的局限性。
通过不断优化产品方案,提高工艺技术水平,可以更好地发挥催化裂化的优势,实现经济效益和环保双赢。
催化裂化的工艺特点及基本原理

催化裂化的工艺特点及基本原理催化裂化是一种重要的石油加工工艺,其开发和应用对于提高石油产业发展水平具有重要的意义。
催化裂化工艺的特点和基本原理如下:一、工艺特点:1.高选择性:催化裂化工艺可以将石油馏分中的大分子烃化合物按照其碳数分解为较低碳数的烃化合物,其中可选择的烃化合物主要是汽油和液化气。
因此,催化裂化可以提高汽油和液化气产率,达到更好的操作经济效益。
2.产物分布广:催化裂化反应不仅可以生成汽油和液化气,还可以生成较低碳数的烃化合物,如乙烯、丙烯等。
因此,催化裂化反应可以提供多种不同碳数的烃化合物,满足不同需求。
3.增塔体积积极:催化裂化工艺采用固定床反应器,反应器内填充了催化剂颗粒,因此反应器体积较大。
大体积的反应器可以增加催化裂化反应的容量,提高石油裂解速率,并且还可以增加反应过程的稳定性和可控性。
4.废气利用:催化裂化反应产生的废气中含有非常丰富的烃化合物和能量,可以通过适当的处理和回收利用,从而得到更好的经济效益,并减少对环境的污染。
二、基本原理:催化裂化反应是通过催化剂的作用来进行的,其基本原理如下:1.裂解反应:石油中的长链烃化合物在催化剂的作用下发生热裂解反应,将大分子烷烃分解成较小分子的烃化合物。
这种反应是一个链状反应过程,会生成一系列的短链烃化合物和碳氢烃中间体。
2.重排反应:短链烃化合物和碳氢烃中间体在催化剂的作用下发生重排反应,重新组合成不同碳数的烃化合物。
3.芳构化反应:在催化裂化过程中,由于催化剂特殊的性质,烃化合物还会发生芳构化反应,生成芳烃类化合物,如苯、甲苯等。
4.积碳反应:由于裂化过程产生的碳元素会在催化剂表面析出,形成碳黑,导致催化剂失活。
因此,催化裂化还需要定期对催化剂进行再生,以保持其活性。
综上所述,催化裂化工艺具有高选择性、广泛的产物分布、增塔体积积极和废气利用等特点。
其基本原理包括裂解反应、重排反应、芳构化反应和积碳反应。
催化裂化工艺的开发和应用有助于提高石油产业的经济效益和环境可持续性。
催化裂化工艺原理
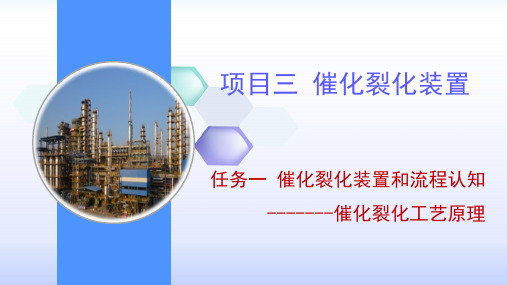
ห้องสมุดไป่ตู้
(3)氢转移反应 两个烯烃分子之间发生氢转移,变成烷烃和 二烯烃; 环烷烃或环烷-芳烃放出氢使烯烃饱和而自 身变成稠环芳烃。
8
(4)芳构化反应 烯烃环化脱氢生成芳烃。
C-C-C-C-C=C-C
CH3
9
3、环烷烃 (1)环断裂生成烯烃,烯烃继续反应; (2)长侧链断裂; (3)通过氢转移转化为芳烃;
RCH2 +
正碳离子的基本来源是由一个烯烃分子获得一
个氢离子而生成,如:
CnH2n + H+
CnH2n+1 +
12
1、正碳离子的形成
(1)烯烃与质子酸(H+)作用
RCH=CH2 + H+
+ RCHCH3
(2)芳烃与质子酸(H+)作用
+ H+
+
13
(3)烷烃在非质子酸中心脱去H-
RCH2CH2 + L
+ RCHCH2CH3
+ RC—CH3
CH3
15
正碳离子进一步异构化和β-断裂, 导致气体中C3、C4含量很高
(2)β-断裂反应
正碳离子裂解生成烯烃和碳数较少的正碳离子。
RCH2CH2CH+CH3 (3)氢转移反应
RC+H2 +CH2=CHCH3
16
17
(三)石油馏分的催化裂化反应特征
1. 各烃类的吸附竞争和对反应的阻滞作用
22
2. 复杂的平行——顺序反应
重质石油馏分 中间馏分
汽油 气体
缩合产物
焦炭
23
二、催化裂化催化剂
催化剂的作用: (1)促进化学反应,提高反应器的处理能力 催化剂能使反应活化能降低,提高反应速率,如 石油馏分的热裂化反应的活化能约为210~293kJ/mol, 而催化裂化反应其活化能降至42~125 kJ/mol,从而 大大提高反应速率。
- 1、下载文档前请自行甄别文档内容的完整性,平台不提供额外的编辑、内容补充、找答案等附加服务。
- 2、"仅部分预览"的文档,不可在线预览部分如存在完整性等问题,可反馈申请退款(可完整预览的文档不适用该条件!)。
- 3、如文档侵犯您的权益,请联系客服反馈,我们会尽快为您处理(人工客服工作时间:9:00-18:30)。
芳构化反应
反应能力较弱,汽油 ON 的提高主要靠裂化和异构化反应。 辛烷值大小顺序:芳烃、异构烯烃>异构烷烃、烯烃>环烷烃 >正构烷烃
二、石油馏分的催化裂化
气-固非均相催化反应过程
外扩散
反应先决 条件
原料分子由主气流扩散到催化剂外表面
内扩散
吸附 反应 脱附 内扩散 外扩散
原料分子由催化剂外表面扩散到内表面
催化剂上的焦炭含量还与剂油比有关
③
剂油比,C/O
催化剂循环量 t / h) ( 剂油比C / O 总进料量(t / h)
C/O反映了单位催化剂上有多少原料进行了反应,并在其
上沉积焦炭。
C/O上升,单位催化剂上积炭下降,催化剂活性下降慢。
C/O大,原料与催化剂接触更充分,有利于提高反应速度。
(2).反应温度
对于床层反应器,反应温度用反应器床层温度表示 对于提升管反应器,用提升管出口温度表示
① 反应温度提高,在其他条件不变的情况下,转化率提高 ② 反应温度的改变可改变热裂化和催化裂化反应的比例 温度提得很高,热裂化反应严重,但主要仍是催化裂化反应
气体产品中C1和C2相对增加,产品的不饱和度增加
在选择性上,环烷烃和烷烃原料相当,芳烃的选择性较差。
碱性氮化物会引起催化剂中毒而使其活性下降。裂化原 料中的含硫化合物(0.3%~1.6%)对催化裂化反应速度
影响不大,但使产品质量下降。
原料中的有机金属化合物在高温下发生分解而使金属沉 积在催化剂表面,造成催化剂污染,使催化剂的活性下
降和催化剂的选择性变差。
稠环芳烃>稠环环烷烃>烯烃>带烷基侧链的单环芳烃>环烷烃> 烷烃 各种烃类在催化剂表面上的化学反应速度大小: 烯烃>大分子单烷基侧链的单环芳烃>异构烷烃及环烷烃>小分 子单烷基侧链的单环芳烃>正构烷烃>稠环芳烃
认识这个特点对指导生产有实际意义:
选择合适的催化原料 对芳香基原料或催化裂化油浆则应选择合适的反应条件或 者先通过预处理来减少其中的稠环芳烃而使其成为优质的 裂化原料,如循环油可作如下处理:
(4). 反应压力
油气分压升高,反应物浓度升高,反应速度升高,同
时生焦速度升高,而且对生焦的影响比较明显,因此
在工业上一般不采用较高的反应压力,一般为1~
加氢→含环烷烃较多→优质裂化原料 溶剂抽提分离出芳烃(化工原料)→裂化
2.复杂的平行—顺序反应
平行-顺序反应的重要特征: 反应深度对产品产率分布有重要影响。
在提升管油剂混合处,产物收率和转化率增加很快,因此
这个区域为快速反应区,以一次反应为主(占整个反应的
50%~70%);提升管的中下部一般称为主要反应区,而 上部称为二次反应区和汽油改质区。
分子量高的比分子量低的易于裂化
环烷烃比烷烃易于裂化
采用分子筛催化剂时:
★ 分子量大小的影响相对较低 ★ 烃类组成对分子筛催化剂和硅酸铝的影响也有差别
K>12 的原料属高裂化性能的烷烃类; K=11.3~12.0 的原料,属中等裂化性能的环烷烃类; K<11.3 的原料,则属难裂化的芳烃类
提高整个转化率 (其它条件不变)
提高处理能力 (转化率提高)
提高催化剂的活性还有利于促进氢转移反应和异
构化反应,对提高产品质量有利。
催化剂的活性取决于它的结构和组成。
② 活性和催化剂表面上的积炭有关
催化剂表面积炭量↗,活性↙ 。
单位催化剂上焦炭沉积量主要与催化剂在反应器内
的停留时间有关。
★ 计算体积空速时,进料量的体积是按20℃的液体体积计
假反应时间
1 / 空速
空速倒数不是真正的反应时间,只是相对的反映反应时
间的长短,故称为假反应时间。假反应时间越长,则反 应时间越长。
提升管反应器(停留时间):
2~4秒
提升管反应器的体积 R V 停留时间 油气对数平均体积流量 对 V
生成小分子的烷烃和烯烃,生成的烷烃还可以进一步 分解成更小的分子。
烷烃反应特点:
异构烷烃的反应速度比正构烷烃快 烷烃分解时,分子中碳链两端的碳碳键很少发生分解 烷烃的裂化可写成通式:
Cn H2n2 Cm H2m CP H2P2
(2). 烯烃
烯烃是一次分解反应的产物,很活泼,反应速度快,在
第九章 催化裂化
Catalytic Cracking
第一节
概述
燃料生产中一个重要的问题 如何将原油中的重质馏分油甚至渣油转化成轻 质燃料产品 重质油轻质化
从大分子分解为较小的分子
主要依靠分解反应(热反应和催化反应)
从低H/C的组成转化成较高H/C的组成
脱 碳(溶剂脱沥青、催化裂化、焦炭化等)
初次反应产物再继续进行的反应叫做二次反应。二次反应
(提升管反应深度控制技术)
多种多样,但并非对我们的生产都有利,应适当加以控制。
对大多数工业装置,原料油的单程转化深度较低(50%~
60%),为了提高原料的转化深度和轻质油收率,大部分工
业装置采用回炼操作,即将产物分馏后的“未反应原料”
与新鲜混合重新进提升管反应器进行反应。
工业装置上常用回炼操作来提高轻质油的收率 回炼比与转化率的关系:
回炼比 (总转化率/单程转化率 1 )
降低单程转化率,回炼比高,反应深度降低,柴油不易二
次裂化,柴油产率升高,柴油十六烷值升高,凝点降低。
回炼比升高,反应所需热量升高,原料预热炉负荷增大, 反应器负荷增大,处理量降低。
气体 汽油 焦炭 转化率 100% 100
单程转化率:指总进料(包括新鲜原料、回炼油、回炼油
浆)一次通过反应器的转化率 反映了反应条件 的苛刻程度
气体 汽油 焦炭 单程转化率 100% 总进料
总转化率:以新鲜原料为基准不考虑回炼油和回炼油浆
气体 汽油 焦炭 总转化率 100% 新鲜原料
600 500 400 300 200 100 0 18 28 38 48 58 68 78 转 化 率 ( 以 < 2 0 5 产 物 计 算)
四、影响催化裂化反应的主要因素
1.几个基本概念
① 转化率:表示催化裂化反应中的反应深度,若以原料 量为100,则:
100 未转化的原料量 转化率 100% 100
氢转移反应的kt值大,因此,前两类反应速度提高得快,于
是汽油中烯烃和芳烃的含量升高,汽油的辛烷值有所提高, 但汽油的安定性变差。
一般工业生产装置采用的反应温度约为460~520℃,在我国, 现阶段主要以生产柴油方案,催化裂化反应温度一般采用 470~510℃。
(3) 原料性质
采用分子筛催化剂和无定型硅酸铝催化剂相比,在反 应速度方面有两点区别: 使用无定型硅酸铝催化剂时:
C C-C=C
Ⅱ.分子中的双键向中间方向移动
C C C C C C C C C C C C
Ⅲ.烯烃空间结构的变化
C C C
C
C C C C
③氢转移反应
受氢剂
供氢剂
烯烃 环烷烃 烷烃 芳香烃
烯烃 烯烃 烷烃 二烯烃
氢转移反应是催化裂化反应所特有的反应,是造成催化裂 化汽油饱和程度高的主要原因。
催化裂化过程中是一个重要的中间产物和最终产物。
① 分解反应 烯烃发生的主要反应,遵循以下规律:(与烷烃相似)
烯烃的分解反应速度比烷烃分解速度快得多 大分子的烯烃分解反应速度比小分子快 异构烯烃的分解速度比正构烯烃快
② 异构化反应 Ⅰ. 分子骨架结构改变,正构烯烃变成异构烯烃
C-C-C=C
放热反应
④ 环化反应和芳构化反应
烯烃可环化成环烷烃并脱氢成为芳烃
C C C C C =C C
C
C
(3). 环烷烃 ① 环烷烃的环可以断裂成烯烃,烯烃再继续上述的各反应
C C C C C C C =C C C C
环烷烃的结构中有叔碳原子,分解反应速度较快 ② 环烷烃也可以通过脱氢转化成芳烃
(4)芳 香 烃
连接在苯核上的烷基侧链易断裂成小分子的烯烃,而且
断裂位置主要位于侧链同苯核连接的键上。
多环芳烃的裂化反应速度很低,它们的主要反应是缩合
成稠环芳烃,最后生成焦炭。
R1 CH =CH2
+R1CH = CH2
R2
+ 2H2
原料
中间物
裂化 H-转移 裂化 异构化
产物
烷烃&异构烷烃
烷烃 烯烃
异构烯烃 芳香烃 焦炭
③ 反应温度对各类反应的影响不同(影响产品分布)
催化裂化是平行-顺序反应,可简化为:
一般情况下,kt2> kt1> kt3,故提高反应温度,反应速度
增大的程度为:△V2>△V1>△V3。
同样转化率下,温度升高,气体产率升高,汽油产率下
降,焦炭产率下降。
④
反应温度对产品质量的影响
提高反应温度,分解反应(产生烯烃)和芳构化反应的kt值比
二、催化裂化的发展过程
分解等反应生成气体、汽油等小分子产物
催化裂化反应 缩合反应生成焦炭 反 应:吸热过程 再 生:放热过程
催化裂化
技术发展:反应-再生型式(工艺)和催化剂性能
催化裂化的发展可以分成以下几个阶段:
1.天然白土和固定床催化裂化
2.合成硅铝催化剂和移动床催化裂化 ① 移动床催化裂化 ② 流化床催化裂化 3.分子筛催化剂和提升管催化裂化
原料分子在催化剂内表面吸附 原料分子反应生成产物 产物分子从催化剂内表面脱附 构成表面化学反应 产物分子从催化剂内表面扩散到外表面 FCC反应的控制步骤 产物分子由催化剂外表面扩散到主气流