重油催化裂化
100万吨-年重油催化裂化的初步设计
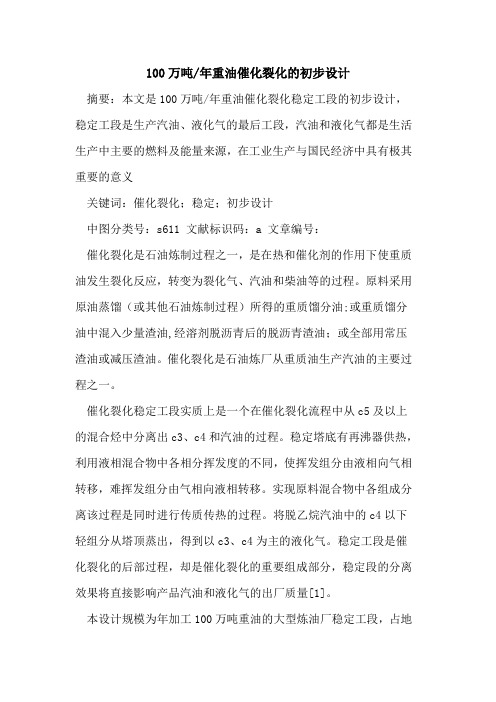
100万吨/年重油催化裂化的初步设计摘要:本文是100万吨/年重油催化裂化稳定工段的初步设计,稳定工段是生产汽油、液化气的最后工段,汽油和液化气都是生活生产中主要的燃料及能量来源,在工业生产与国民经济中具有极其重要的意义关键词:催化裂化;稳定;初步设计中图分类号:s611 文献标识码:a 文章编号:催化裂化是石油炼制过程之一,是在热和催化剂的作用下使重质油发生裂化反应,转变为裂化气、汽油和柴油等的过程。
原料采用原油蒸馏(或其他石油炼制过程)所得的重质馏分油;或重质馏分油中混入少量渣油,经溶剂脱沥青后的脱沥青渣油;或全部用常压渣油或减压渣油。
催化裂化是石油炼厂从重质油生产汽油的主要过程之一。
催化裂化稳定工段实质上是一个在催化裂化流程中从c5及以上的混合烃中分离出c3、c4和汽油的过程。
稳定塔底有再沸器供热,利用液相混合物中各相分挥发度的不同,使挥发组分由液相向气相转移,难挥发组分由气相向液相转移。
实现原料混合物中各组成分离该过程是同时进行传质传热的过程。
将脱乙烷汽油中的c4以下轻组分从塔顶蒸出,得到以c3、c4为主的液化气。
稳定工段是催化裂化的后部过程,却是催化裂化的重要组成部分,稳定段的分离效果将直接影响产品汽油和液化气的出厂质量[1]。
本设计规模为年加工100万吨重油的大型炼油厂稳定工段,占地面积约1000㎡,厂房为l型,分四个车间,吸收车间、解吸及再吸收车间和稳定车间,还有辅助设施,有控制室、配电室及生活区间。
在主要生产车间里有4个精馏塔、2个中间罐。
1.1原料规格100万吨/年重油催化裂化稳定工段的初步设计产品规格见如下表1-1[2]。
表1-1 原料规格1.2产品特点(1)汽油无色至淡黄色的易流动液体。
危险特性:极易燃烧。
其蒸气与空气可形成爆炸性混合物。
遇明火、高热极易燃烧爆炸。
与氧化剂能发生强烈反应。
其蒸气比空气重,能在较低处扩散到相当远的地方,遇明火会引着回燃。
(2)液化气危险特性:极易燃,与空气混合能形成爆炸性混合物。
重油催化裂化

重油催化裂化(residue fluid catalytIC cracking,即RFCC)工艺的产品是市场极需的高辛烷值汽油馏分,轻柴油馏分和石油化学工业需要的气体原料。
由于该工艺采用了分子筛催化剂、提升管反应器和钝化剂等,使产品分布接近一般流化催化裂化工艺。
但是重油原料中一般有30%~50%的廉价减压渣油,因此,重油流化催化裂化工艺的经济性明显优于一般流化催化工艺,是近年来得到迅速发展的重油加工技术。
㈠重油催化裂化的原料所谓重油是指常压渣油、减压渣油的脱沥青油以及减压渣油、加氢脱金属或脱硫渣油所组成的混合油。
典型的重油是馏程大于350℃的常压渣油或加氢脱硫常压渣油。
与减压馏分相比,重油催化裂化原料油存在如下特点:①粘度大,沸点高;②多环芳香性物质含量高;③重金属含量高;④含硫、氮化合物较多。
因此,用重油为原料进行催化裂化时会出现焦炭产率高,催化剂重金属污染严重以及产物硫、氮含量较高等问题。
㈡重油催化裂化的操作条件为了尽量降低焦炭产率,重油催化裂化在操作条件上采取如下措施:1、改善原料油的雾化和汽化由于渣油在催化裂化过程中呈气液相混合状态,当液相渣油与热催化剂接触时,被催化剂吸附并进入颗粒内部的微孔,进而裂化成焦炭,会使生焦量上升,催化活性下降。
因此可见,为了减少催化剂上的生焦量,必须尽可能地减少液相部分的比例,所以要强化催化裂化前期过程中的雾化和蒸发过程,提高气化率,减少液固反应。
2、采用较高的反应温度和较短的反应时间当反应温度提高时,原料的裂化反应加快较多,而生焦反应则加快较少。
与此同时,当温度提高时,会促使热裂化反应的加剧,从而使重油催化裂化气体中C1、C2增加,C3、C4 减少。
所以宜采用较高反应温度和较短的反应时间。
㈢重油催化裂化催化剂重油催化裂化要求其催化剂具有较高的热稳定性和水热稳定性,并且有较强的抗重金属污染的能力。
所以,目前主要采用Y型沸石分子筛和超稳Y型沸石分子筛催化剂。
㈣重油催化裂化工艺1、重油催化裂化工艺与一般催化裂化工艺的异同点两工艺既有相同的部分,亦有不同之处,完全是由于原料不同造成的。
催化裂化是目前石油炼制工业中最重要的二次加工过程,也是

(1)环境空气 根据建设项目可能对大气环境造成的影响程度和范围以及项目所在地区的 环境敏感程度,确定评价工作等级如下: 拟建项目装置产生的主要大气污染物为烟尘、SO2、NOx,根据《环境影响 评价技术导则—大气环境》(HJ/T2.2-2008)中的估算模式对项目的大气环境评价 工作进行分级。根据项目的工程分析结果,选择 TSP 和 SO2 来确定评价工作等 级,计算最大地面浓度占标率 Pi,及第 i 个污染物的地面浓度达标准限值 10%时 所对应的最远距离 D10%。 根据估算模式的计算结果,Pmax=4.308%<10%,最大浓度出现的距离(1.9km)
(3)声环境
根据《兰州市饮用水源保护区、大气、噪声功能区划图》,声环境兰新铁路 以南为一类区,兰新铁路以北,化工街、生产街、广河路、合水北路、西固东路 以南地区及兰州石化分公司东区专用铁路以东,环行东路以西,西固东路以北的 三角地带为二类区,其余地区为三类区,主要交通干线两侧为四类区。
1.3.2 环境质量标准
西固路以北的工业区(西起西柳沟,东至水上公园,北至黄河,南至西固路)为大 气三类区,其余部分均为二类区。根据《国务院关于酸雨控制区和二氧化硫污染 控制区有关问题的批复》(国函(1998)5 号),兰州市区为 SO2 控制区。
(2)地表水环境
根据《兰州市城市生活饮用水的保护区区划方案》,地表水在一水厂排泥口 以上为Ⅱ类水域,以下为Ⅲ类水域。
厂界外声环境功能区类别
昼间夜间Biblioteka 36555
表 1.6-9
施工阶段
土石方 打桩 结构 装修
建筑施工场界噪声限值(GB12523-1990) 单位:dB(A)
主要噪声源
噪声限值
昼间
夜间
推土机、挖掘机、装载机
催化裂化
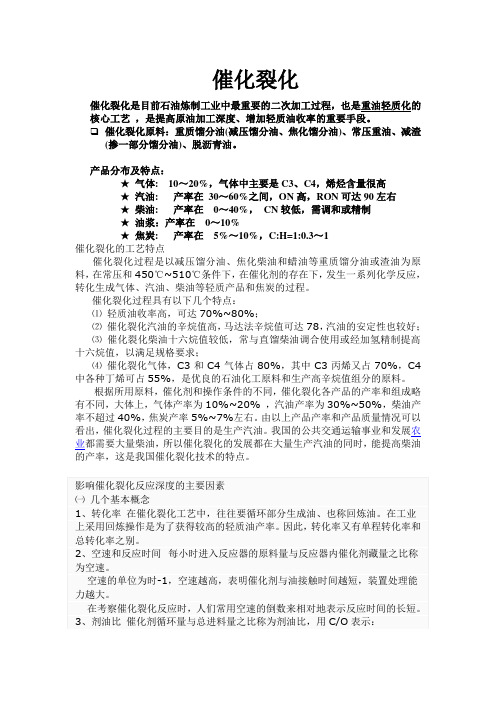
催化裂化催化裂化是目前石油炼制工业中最重要的二次加工过程,也是重油轻质化的核心工艺,是提高原油加工深度、增加轻质油收率的重要手段。
催化裂化原料:重质馏分油(减压馏分油、焦化馏分油)、常压重油、减渣(掺一部分馏分油)、脱沥青油。
产品分布及特点:★气体: 10~20%,气体中主要是C3、C4,烯烃含量很高★汽油: 产率在30~60%之间,ON高,RON可达90左右★柴油: 产率在0~40%,CN较低,需调和或精制★油浆:产率在0~10%★焦炭: 产率在5%~10%,C:H=1:0.3~1催化裂化的工艺特点催化裂化过程是以减压馏分油、焦化柴油和蜡油等重质馏分油或渣油为原料,在常压和450℃~510℃条件下,在催化剂的存在下,发生一系列化学反应,转化生成气体、汽油、柴油等轻质产品和焦炭的过程。
催化裂化过程具有以下几个特点:⑴轻质油收率高,可达70%~80%;⑵催化裂化汽油的辛烷值高,马达法辛烷值可达78,汽油的安定性也较好;⑶催化裂化柴油十六烷值较低,常与直馏柴油调合使用或经加氢精制提高十六烷值,以满足规格要求;⑷催化裂化气体,C3和C4气体占80%,其中C3丙烯又占70%,C4中各种丁烯可占55%,是优良的石油化工原料和生产高辛烷值组分的原料。
根据所用原料,催化剂和操作条件的不同,催化裂化各产品的产率和组成略有不同,大体上,气体产率为10%~20% ,汽油产率为30%~50%,柴油产率不超过40%,焦炭产率5%~7%左右。
由以上产品产率和产品质量情况可以看出,催化裂化过程的主要目的是生产汽油。
我国的公共交通运输事业和发展农业都需要大量柴油,所以催化裂化的发展都在大量生产汽油的同时,能提高柴油的产率,这是我国催化裂化技术的特点。
在同一条件下,剂油比大,表明原料油能与更多的催化剂接触。
㈡影响催化裂化反应深度的主要因素影响催化裂化反应转化率的主要因素有:原料性质、反应温度、反应压力、反应时间。
1、原料油的性质原料油性质主要是其化学组成。
石油化工重油催化裂化工艺技术_0

石油化工重油催化裂化工艺技术随着社会的飞速发展,我国的石油工业的发展也有了很大的提高。
石油化工催化裂化工艺是重油的轻质化和改质的重要手段,加强对催化裂化工艺的优化设计,提高石油催化裂化的效率。
催化裂化反应的特点是顺序反应,得到各种合格的产品后,最终剩余的是焦炭,将其在再生器中烧掉,减少对环境造成的污染,因此,石油化工催化裂化工艺具有非常好的环保特性。
标签:石油化工;重油催化裂化;工艺技术通过催化裂化工艺技术的应用,提高原油的加工深度,得到合格的轻质油品,满足石油炼制生产工艺的技术要求。
增加石油炼制生产的产品的品种,不断提高产品的质量,为石油化工企业创造最佳的经济效益。
因此,有必要对石油化工催化裂化生产工艺技术进行优化,应用最先进的生产技术,获得更高的产品收率。
1 重油催化裂化工艺概述重油催化裂化生产过程中,采用分子筛催化剂,应用流化床反应器等设备,通过合理控制催化裂化的生产运行参数,得到合格的汽油馏分和轻质的柴油馏分,为化工生产创造了最佳的经济效益。
重油原料中含有一定量的渣油,价格相对便宜,因此,合理组织催化裂化生产,能够为石油化工生产带来巨大的经济效益。
我国的石油炼制工艺,以重油催化裂化工艺为主,应用该项技术措施,生产出更多的清洁能源,满足环保的技术要求,成为新时期的油品生产工艺。
因此,优化设计重油催化裂化生产工艺技术,加强对渣油的处理,以最少的投入,获得最佳的经济效益,才是石油化工生产的目标。
2 石油化工催化裂化工艺技术优化2.1 催化裂化工艺流程的优化石油化工催化裂化工艺基本由五大部分组成,反应再生系统、分馏系统、吸收稳定系统、产品的脱硫精制系统和烟气能量回收系统。
将几大系统结合起来,更好地完成催化裂化的效果。
节约催化剂的用量,加快对焦炭的燃烧速度,通过再生系统的作用,及时恢复催化剂的活性,使其达到最佳的催化裂化的状态,得到更多的汽油、柴油以及液化气产品,满足石油化工催化裂化的产品质量标准,为石油炼制创造可观的利润。
石油化工重油催化裂化工艺技术

石油化工重油催化裂化工艺技术石油化工重油催化裂化工艺技术是一种将重油转化为轻质油和化学品的过程。
该过程主要利用催化剂的作用,在高温高压条件下,使重油的大分子裂解成小分子,同时发生异构化、芳构化和氢转移等反应,以获得更多的轻质油和化学品。
催化剂的选择:催化剂是该技术的核心,其选择对产品的质量和产量有着至关重要的影响。
目前,常用的催化剂包括酸性催化剂、金属催化剂和金属氧化物催化剂等。
工艺条件的控制:工艺条件包括反应温度、压力、空速等,这些因素对产品的质量和产量都有着极大的影响。
因此,精确控制这些工艺条件是重油催化裂化工艺技术成功应用的关键。
产品的质量和性能:重油催化裂化工艺技术生产的产品具有高辛烷值、低硫含量等特点,被广泛应用于汽油、柴油、航空煤油等领域。
在应用方面,石油化工重油催化裂化工艺技术适用于不同类型重油,如减压渣油、催化裂化残渣油、脱沥青油等。
对于不同工业应用,可根据实际需求选择合适的工艺技术。
例如,对于生产高质量汽油和柴油的需求,可以选择更为精细的催化剂和严格的工艺条件;对于生产高附加值化学品的需求,则可以通过调整工艺流程和催化剂类型来增加化学品产量。
虽然石油化工重油催化裂化工艺技术在提高石油利用率、生产高质量石油化工产品方面具有重要作用,但也面临着一些挑战。
催化剂的活性、选择性和稳定性是该技术的关键,而目前催化剂的研究与开发尚存在诸多困难。
重油催化裂化过程中产生的固体废物和废气等对环境造成了严重影响,亟需解决。
由于重油资源的有限性,需要进一步探索和研发更为高效、环保的石油化工技术,以适应未来可持续发展的需要。
石油化工重油催化裂化工艺技术在石油化工产业中具有重要地位。
随着经济的发展和科技的进步,该技术将不断完善和优化,提高石油利用率和生产效率,同时注重环保和可持续发展。
未来,需要加强催化剂的研发与优化,减少环境污染,提高技术的绿色性和可持续性。
应积极探索新的石油化工技术,以应对全球能源危机和环境问题的挑战。
重油催化裂化装置主要工艺流程说明
重油催化裂化装置主要工艺流程说明一. 反再系统1.反应部分混合蜡油和常(减)压渣油分别由罐区原料罐送入装置内的静态混合器(D-214)混合均匀后,进入原料缓冲罐(D-203/1),然后用原料泵(P-201/1.2)抽出,经流量控制阀(8FIC-230)后与一中回流换热(E-212/1.2),再与油浆(E-201/1.2)换热至170~220℃,与回炼油一起进入静态混合器(D-213)混合均匀。
在注入钝化剂后分三路(三路设有流量控制)与雾化蒸汽一起经六个进料喷嘴进入提升管,与从二再来的高温再生催化剂接触并立即汽化,裂化成轻质产品(液化气、汽油、柴油)并生成油浆、干气及焦炭。
新增焦化蜡油流程:焦化蜡油进装后先进焦化蜡油缓冲罐(D-203/2),然后经焦化蜡油泵(P-201/3.4)提压至1.3MPa 后分为两路:一路经焦化蜡油进提升管控制阀(8FIC242)进入提升管反应器的回炼油喷嘴或油浆喷嘴,剩余的焦化蜡油经另一路通过D-203/2的液位控制阀(8LIC216)与进装蜡油混合后进入原料油缓冲罐(D-203/1)。
新增常压热渣油流程:为实现装置间的热联合,降低装置能耗,由南常减压装置分出一路热常渣(约350℃),经8FIQC530直接进入D-213(原料油与回炼油混合器)前,与原料混合均匀后进入提升管原料喷嘴。
反应油气、水蒸汽、催化剂经提升管出口快分器分离出大部分催化剂,反应油气经过沉降器稀相沉降,再经沉降器(C-101)内四组单级旋风分离器分离出绝大部分催化剂,反应油气、蒸汽、连同微量的催化剂细粉经大油气管线至分馏塔人档下部。
分馏塔底油浆固体含量控制<6g/L。
旋分器分出的催化剂通过料腿返回到汽提段,料腿装有翼阀并浸没在汽提段床层中,保证具有正压密封,防止气体短路,汽提蒸汽经环形分布器进入汽提段的上中下三个部位使催化剂不仅处于流化状态,并汽提掉催化剂夹带的烃油气,汽提后的催化剂通过待生滑阀进入一再催化剂分布器。
重油催化裂化工艺应注意什么
重油催化裂化工艺应注意什么?1.工艺简述催化裂化是重质油轻质化的重要加工过程。
以馏分油为原料有流化床和提升管(包括同轴)催化裂化。
以常压重油或掺入减压渣油为原料有两段再生的重油催化裂化。
简要工艺过程是以常压重油或减压馏分油掺入减压渣油为原料经预热到300℃左右,与回炼油一起进入沉降器下部提升管,再与再生器来的730℃的再生催化剂接触在反应温度480~500℃的条件下进行裂化、异构化、芳构化和氢转移等反应。
反应物经旋风分离器分离出催化剂后进入分馏塔。
分馏出的柴油产品直接装置;富气和粗汽油再分别进入吸收稳定系统和脱硫系统,进一步分离出干气、液化气和稳定汽油产品。
反应后的催化剂经再生循环使用。
烟气经三级旋风分离回收催化剂,然后,驱动烟机做功和进入废热锅炉生产蒸汽后排入大气。
2.危险部位2.1反应、再生系统反应器是油料与高温催化剂进行接触反应的设备,再生器是压缩风与催化剂混合流化烧焦的设备,两器之间有再生斜管和待生斜管连通。
如果两器的压差和料位控制不好,将出现催化剂倒流,流化介质互串而导致设备损坏或爆炸事故。
反应沉降器提升管是原料与730℃的高温催化剂进行接触反应的场所,其衬里容易被冲刷脱落,造成内壁腐蚀烧红或穿孔,严重时导致火灾爆炸事故。
2.2分馏系统温度高达360℃,含有催化剂粉沫的重油在高速流动下,容易冲蚀管线设备,造成烫伤或火灾事故。
分馏塔底液面超高至油气线入口时,就会造成反应器憋压,若处理不当,会导致催化剂倒流的恶性事故。
当分馏塔顶油气分离器液面超高,会造成富气带液,损坏气压机。
2.3吸收稳定系统该系统压力高达1.45MPa统中的瓦斯、液态烃、汽油等腐蚀设备容易引起泄漏,造成中毒和火灾爆炸事故。
2.4四机组四机组指(气轮机—蒸汽轮机—主风机—电动/发电机),是装置能量综合利用的重要设备,如果其中某一部分发生故障,会使机组停运,甚至停工。
2.5废热锅炉及外取热器包这是产生3.5MPa中压蒸汽的场所,液面失灵、汽包于锅,会发生设备损坏或爆炸事故。
重油催化裂化基础知识
重油催化裂化基础知识广州石化总厂炼油厂重油催化裂化车间编一九八八年十二月第一章概述第一节催化裂化在炼油工业生产中的作用催化裂化是炼油工业中使重质原料变成有价值产品的重要加工方法之一。
它不仅能将廉价的重质原料变成高价、优质、市场需要的产品,而且现代化的催化裂化装置具有结构简单,原料广泛(从瓦斯油到常压重油),运转周期长、操作灵活(可按多产汽油、多产柴油,多产气体等多种生产方法操作),催化剂多种多样,(可按原料性质和产品需要选择合适的催化剂),操作简便和操作费用低等优点,因此,它在炼油工业中得到广泛的应用。
第二节催化裂化生产发展概况早在1936年美国纽约美孚真空油公司(SoCony vacu um co)正式建立了工业规模的固定床催化裂化装置。
由于所产汽油的产率及辛烷值均比热裂化高得多,因而一开始就受到人们的重视,并促进了汽车工业发展。
如图所示,片状催化剂放在反应器内不动,反应和再生过程交替地在同一设备中进行、属于间歇式操作,为了使整个装置能连续生产,就需要用几个反应器轮流地进行反应和再生,而且再生时放出大量热量还要有复杂的取热设施。
由于固定床催化裂化的设备结构复杂,钢材用量多、生产连续性差、产品收率及性质不稳定,后为移动床和流化床催化裂化所代替。
第一套移动床催化裂化装置和第一套流化床催化裂化(简称FCC 装置都是1942年在美国投产的固定床反应器移动床催化裂化的优点是使反应连续化。
它们的反应和再生过程分别在不同的两个设备中进行,催化裂化在反应器和再生器之间循环流动,实现了生产连续化。
它使用直径约为3毫米的小球型催化剂。
起初是用机械提升的方法在两器间运送催化剂,后来改为空气提升,生产能力较固定床大为提高、产品质量也得到了改善。
由于催化剂在反应器和再生器内靠重力向下移动、速度很缓慢,所以对设备磨损很小,但移动床的设备仍较复杂,耗钢量仍较大,特别是处理量在80 万吨/年以上的大型装置、移动床远不如流化床优越。
催化裂化工艺介绍
1.0催化裂化催化裂化是原料油在酸性催化剂存在下,500℃左右、1× 105~3× 105Pa 在下发生裂解,生成轻质油、气体和焦炭的过程。
催化裂化是现代化炼油厂用来改质重质瓦斯油和渣油的核心技术,是炼厂获取经济效益的重要手段。
催化裂化的石油炼制工艺目的:1)提高原油加工深度,得到更多数量的轻质油产品;2)增加品种,提高产品质量。
催化裂化是炼油工业中最重要的一种二次加工工艺,是重油轻质化和改质的重要手段之一,已成为当今石油炼制的核心工艺之一。
1.1催化裂化的发展概况催化裂化的发展经历了四个阶段:固定床、移动床、流化床和提升管。
见下图:流化床在全世界催化裂化装置的总加工能力中,提升管催化裂化已占绝大多数。
移动床提升管(并列式)1.2催化裂化的原料和产品1.2.1原料催化裂化的原料围广泛,可分为馏分油和渣油两大类。
馏分油主要是直馏减压馏分油(VGO),馏程350-500℃,也包括少量的二次加工重馏分油如焦化蜡油等,以此种原料进行催化裂化称为馏分油催化裂化。
渣油主要是减压渣油、脱沥青的减压渣油、加氢处理重油等。
渣油都是以一定的比例掺入到减压馏分油中进行加工,其掺入的比例主要受制于原料的金属含量和残炭值。
对于一些金属含量低的石蜡基原有也可以直接用常压重油为原料。
当减压馏分油中掺入渣油使通称为RFCC。
以此种原料进行催化裂化称为重油催化裂化。
1.2.2产品催化裂化的产品包括气体、液体和焦炭。
1、气体在一般工业条件下,气体产率约为10%-20%,其中含干气和液化气。
2、液体产物1)汽油,汽油产率约为30%-60%;这类汽油安定性较好。
2)柴油,柴油产率约为0-40%;因含较多芳烃,所有十六烷值较低,由重油催化裂化得到的柴油的十六烷值更低,这类柴油需经加氢处理。
3)重柴油(回炼油),可以返回到反应器,已提高轻质油收率,不回炼时就以重柴油产品出装置,也可作为商品燃料油的调和组分。
4)油浆,油浆产率约为5%-10%,从催化裂化分馏塔底得到的渣油,含少量催化剂细粉,可以送回反应器回炼以回收催化剂。
- 1、下载文档前请自行甄别文档内容的完整性,平台不提供额外的编辑、内容补充、找答案等附加服务。
- 2、"仅部分预览"的文档,不可在线预览部分如存在完整性等问题,可反馈申请退款(可完整预览的文档不适用该条件!)。
- 3、如文档侵犯您的权益,请联系客服反馈,我们会尽快为您处理(人工客服工作时间:9:00-18:30)。
对重油催化裂化分馏塔结盐原因分析及对策
王春海
内容摘要
分析了重油催化裂化装置发生分馏塔结盐现象的原因,并提出了相应的对策。
分馏塔结盐是由于催化原料中的有机、无机氯化物和氮化物在提升管反应器中发生反应生成HCl和NH3 ,二者溶于水形成NH4Cl溶液所致。
可采取尽可能降低催化原料中的含盐量、对分馏塔进行在线水洗、利用塔顶循环油脱水技术等措施,预防和应对分馏塔结盐现象的发生。
关键词: 重油催化裂化分馏塔结盐氯化铵水洗循环油脱水
目前,催化裂化装置( FCCU)普遍通过掺炼渣油及焦化蜡油进行挖潜增效,但由于渣油中的氯含量和焦化蜡油中的氮含量均较高,势必导致FCCU 分馏塔发生严重的结盐现象。
另外,近年来国内市场柴油消费量迅速增长,尽管其生产量增长也很快,但仍不能满足市场的需求。
因此许多FCCU 采用降低分馏塔塔顶温度(以下简称顶温)的操作来增产柴油,但顶温低致使分馏塔顶部水蒸气凝结成水,水与氨(NH3)和盐酸(HCl)一起形成氯化铵(NH4Cl)溶液,从而加速分馏塔结盐。
随着分馏塔内盐层的加厚,沉积在塔盘上的盐层会影响传质传热效果,致使顶温失控而造成冲塔;沉积在降液管底部的盐层致使降液管底部高度缩短,塔内阻力增加,最终导致淹塔.。
可见,如何避免和应对分馏塔结盐现象的发生,是FCCU 急需解决的生产难题。
一、分馏塔结盐原因及现象分析
(一)原因
随着FCCU所用原料的重质化,其中的氯和氮含量增高。
在高温临氢催化裂化的反应条件下,有机、无机氯化物和氮化物在提升管反应器中发生反应生成HCl和NH3 ,其反应机理可用下式表示:
:
催化裂化反应生成的气体产物将HCl和NH3从提升管反应器中带入分馏塔,在分馏塔内NH3 和HCl与混有少量蒸汽的油气在上升过程中温度逐渐降低,当温度达到此环境下水蒸气的露点时,就会有冷凝水产生,这时NH3和HCl溶于水形成NH4Cl溶液。
NH4Cl溶液沸点远高于水的沸点,其随塔内回流液体在下流过程中逐渐提浓,当盐的浓度超过其在此温度下的饱和浓度时,就会结盐析出,沉积在塔盘及降液管底部。
(二)现象
1.由于塔顶部冷凝水的存在,形成塔内水相内回流 ,致使塔顶温度难以控制 ,顶部循环泵易抽空,顶部循环回流携带水。
2.由于沉积在塔盘上的盐层影响传热效果,在中段回流量、顶部循环回流量发生变化时,塔内中部、顶部温度变化缓慢且严重偏离正常值。
3.由于沉积在塔盘上的盐层影响传质效果,导致汽油、轻柴油馏程发生重叠,轻柴油凝
点及汽油干点严重不合格。
4.由于结盐析出沉积在分馏塔抽出口,致使轻柴油抽出量明显降低甚至无法抽出。
5.水样中氯离子或氨离子含量很高。
上述现象可作为判断分馏塔是否发生结盐的依据。
当然,在发生换热设备 (如稳定塔底或脱吸塔底再沸器)泄漏、塔板吹翻等设备事故时,也有可能伴随出现上述现象。
如设备问题已排除,便应当确定是发生了结盐。
二、分馏塔结盐预防及处理措施
(一)加强原料脱盐
催化原料中的盐类在目前的电脱盐水平下不可能全部脱除,只能尽可能降低原料中的含盐量。
特别是原油中的有机氯通过电脱盐及常减压蒸馏是除不掉的,其中的氮化物也不能彻底清除,这是导致分馏塔结盐的关键因素。
国内多套同类FCCU的操作经验表明,控制原料中的盐含量低于5mg/L时比较安全,基本不会造成分馏塔冲塔;而原料盐含量高于6 mg/L 时则危险较大。
因此依据原油性质,选择适宜的脱盐技术并采用最佳破乳剂和优化操作条件,是从源头上解决分馏塔结盐的根本措施。
(二)操作预防措施
1.尽可能减少进入分馏塔的水蒸气量,并适当加大反应系统的预提升干气量。
这样可以降低分馏塔顶部水蒸气分压,使其露点温度降低,减少冷凝水的产生,进而减少NH4 Cl溶液的产生,提高分馏塔的操作弹性。
2. 选择合适的塔顶操作温度。
根据分馏塔总注气量和塔顶分压计算分馏塔顶水蒸气分压,由此查出对应的水蒸气饱和温度。
控制分馏塔顶温度比该温度高5℃以上,从而保证分馏塔内不生成液态水,进而避免分馏塔结盐。
3.控制适宜的塔顶循环量、中段循环量及其返塔温度,稳定分馏塔中部及顶部温度,避免因塔内温度波动导致冷凝水产生。
4.分馏塔结盐是不断聚积形成的,因此对其预测十分必要。
对原料的含盐量及塔顶循环回流中的含量进行定期检验分析,密切注意分馏状况,判断汽油、柴油馏程是否重叠;调整分馏塔各段取热分配量,适当提高塔顶负荷,减少顶部循环回流量,补充适量冷回流,以增加塔顶汽液两相流量,保证较高的温度和油气分压,降低NH4Cl析出结晶的速度。
5.平稳操作,避免波动。
操作大幅度波动是导致分馏塔顶循环泵抽空的主要原因。
随着
装置运行时间的延长,分馏塔顶部塔盘结盐越来越多,导致塔顶通透性越来越差。
如遇操作幅度波动将加速塔顶结盐,严重时将直接导致分馏塔冲塔。
所以,装置运行至后期,平稳操作尤为重要。
(三)分馏塔在线水洗
分馏塔结盐后,压降增大到30~50kPa,塔顶温度难以控制,柴油组分冲至塔顶,汽油和柴油质量无法保证。
为了维持生产,通常都采取对分馏塔进行在线水洗的应急措施。
新鲜水自顶循环返塔线返回塔内,控制适宜的温度,使塔顶蒸汽凝结成水,与注入的新鲜水形成内回流,沿塔盘自上而下流动,油气不凝结,仍从塔顶馏出,洗塔水在下流过程中溶解塔盘上的铵盐、冲走塔盘上的浮垢,最后自塔的适当位置排出。
洗塔过程中要慢慢加大上水量,控制好分馏塔塔顶和中部温度,以防止顶部的水落到塔底造成冲塔,确保轻柴油质量合格。
从污水排放口监测盐含量变化情况,以盐含量不再降低作为洗塔结束、恢复正常操作的判断依据。
(四)塔顶循环油脱水
1.塔外脱水
分馏塔顶循环油由泵从分馏塔上部塔盘抽出,经过空冷、冷却器进行冷却,进行油水分离后返回顶层塔盘。
采取塔顶循环油脱水技术后,每小时的脱水量约为1.5 t,水蒸气的露点温度也降低了4℃,分馏塔顶温降低,柴油馏程拓宽,柴油产率增加,这也使得分馏塔的取热负荷具有更好的操作弹性,为控制塔顶水蒸气的冷凝提供了良好的条件,从而进一步防止NH4Cl析出堵塞塔盘现象的发生。
另外,增加塔顶循环油脱水操作后又可以使溶解在水中的NH4Cl随该系统离开分馏塔,从而降低了分馏塔的结盐倾向,使装置平稳运行。
由于在装置处理量不变的情况下,反应系统经大油气线进入分馏塔的热量不变,在增产柴油的情况下,分馏塔上部温度会持续降低,因此可充分计算分馏塔余热,在塔顶循环及中段回流段增设适宜的热量回收设备,以保持分馏塔操作稳定。
2.塔内脱水
对塔顶循环油采取塔内脱水时,需在分馏塔内安装个集水箱,箱体内嵌个自动脱水器,脱水器脱出的水自压返回至分馏塔顶油水分离罐中。
该脱水方式简单、投资少。
同塔外脱水一样,该技术也可以有效防止分馏塔顶部结盐,降低顶温,拓宽柴油馏程,增加柴油收率。
此外,也需新增换热器,进行余热回收。
3.结束语
为了预防和处理分馏塔结盐现象,应从多方面综合考虑,首先要加强“一脱四注”操作,从源头尽可能降低催化原料中的含盐量;其次,当出现分馏塔顶结盐时,可采取在线水洗的应
急措施;另外,采取塔顶循环油脱水技术,不但能有效解决分馏塔结盐问题,还可降低分馏塔塔顶温度,拓宽柴油馏程,增产柴油。
参考文献:
【1】杨相伟,刘惠丽,牛长令.分馏塔结盐的原因分析、处理及预防.【J】.石油化工安全技术, 2003 .
【2】唐家俊.催化装置分馏塔顶部结盐的原因分析及对策.【J】.中外能源, 2006.
【3】达建文,苟社全. 超声波强化原油破乳电脱盐技术的工业实践【 J】.炼油技术与工程, 2006 .
【4】王金凤,吴丽梅,陈建军,等.高速电脱盐技术的应用 .【J】.化工科技, 2008.
【5】李宁.原油中氯对催化分馏塔的危害及解决措施 .【J】.天然气与石油, 2005.
【6】孙德立.分馏塔结盐的分析与对策.【J】. 辽宁工学院学报:自然科学版, 2001.
【7】关晓珍,张广清. 催化分馏塔塔顶结盐原因分析.【J】石油化工腐蚀与防护, 2001.。