宝钢冷轧核心技术研发历程
宝钢不锈钢冷连轧技术开发
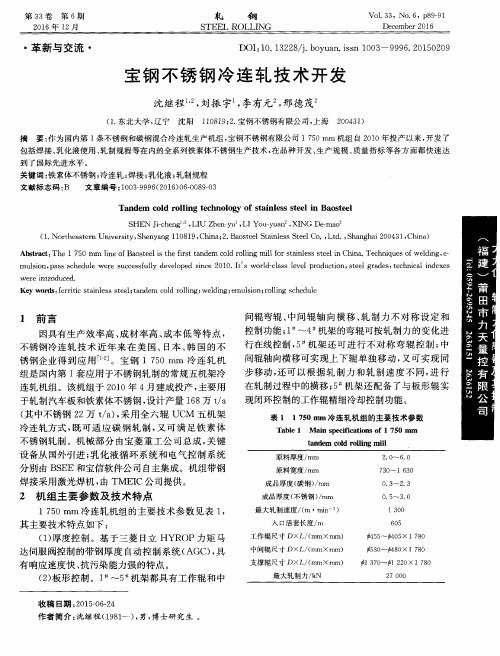
间辊 弯辊 、 中 间辊 轴 向 横 移 、 轧 制力 不 对 称 设 定 和 控制功 能 ; 1 ~ 4 机架 的弯 辊可按 轧 制 力 的变 化进 行 在线 控制 , 5 # 机 架 还 可进 行 不 对 称 弯 辊 控 制 ; 中
Ta b l e 1 M ai n s pe c i f i c at i o n s o f 1 75 0 I I l m
于轧制汽车板和铁素体不锈钢 , 设计产量 1 6 8 万t / a ( 其 中不锈 钢 2 2万 t / a ) , 采 用 全 六 辊 UC M 五 机 架 冷 连 轧方 式 , 既 可适 应 碳 钢 轧 制 , 又 可 满 足 铁 素 体 不 锈钢 轧 制 。机械 部 分 由宝 菱 重 工 公 司 总成 , 关 键 设备从 国外引进 ; 乳化液循环 系统 和电气控制系统 分别由 B S E E和宝 信软 件公 司 自主集 成 。机组 带 钢 焊 接采 用 激光 焊机 , 由T ME I C公 司提供 。
we r e i n t r o d u c e d . Ke y wo r d s : f e r r i t i c s t a i n l e s s s t e e l ; t a n d e m c o l d r o l l i n g; we l d i n g; e mu l s i o n ; r o l l i n g s c h e d u l e
1 前 言
因具有生产效率高、 成材率高、 成本低等特点 , 不 锈 钢冷 连 轧 技 术 近 年 来 在 美 国、 日本 、 韩 国 的不 锈 钢企 业 得 到 应 用 [ 1 - e ] 。宝 钢 l 7 5 0 mm 冷 连 轧 机 组 是 国 内第 1 套 应 用 于不 锈钢 轧制 的 常规五 机架 冷
宝钢冷轧核心技术研发历程

宝钢冷轧核心技术研发历程冷轧是冶金流程中非常重要的变形工序,在金属相变点温度以下,将轧件压缩到理想的厚度,使其具有良好的力学性能、优良的表面质量、精密的尺寸精度,可以广泛应用于汽车、家电、电子、建筑、包装等各个行业。
虽然近年来随着热轧设备的不断进步,热卷箱、无头轧制、边部加热、层流冷却边部遮蔽等设备的开发使用,一定程度上提高了热轧产品的温度均匀性,但热轧产品的性能和厚度均匀性仍然无法和冷轧产品相媲美。
此外,冷轧产品的表面质量、冲压性能、电磁性能,也是热轧产品无法达到的。
以硅钢为例,我国曾大力推广以高效的冷轧硅钢取代落后热轧硅钢,“以冷代热”以节约在传输和转换过程中损耗的电能。
冷轧作为“轧薄、轧亮、轧精”的工序,有着无可替代的功能和优势,将来还将不断发展。
宝钢从1988年第1条冷轧机组投产以来,经过20年的生产和研发,经历了一条从引进消化到不断改进,发展到自主创新的道路,引领着国内冷轧技术的发展。
冷轧机核心技术的发展如果往前追溯,钢的冷轧最早始于19世纪中叶的德国,当时只能生产宽度20~25 mm的冷轧钢带。
美国在1920年第一次成功地轧制出宽带钢,并很快由单机不可逆轧制而跨入单机可逆式轧制。
1926年阿姆柯公司巴特勒工厂建成四机架冷连轧机。
冷轧带钢生产经历了漫长的发展过程,从最初的单张轧制到现在的成卷轧制,从可逆轧机到全连续轧机再到酸轧联合机组的多种生产工艺,装备水平和自动化程度不断提高。
特别是20世纪七、八十年代,冷轧技术在全连续和自动化技术的带动下,出现了一个快速发展的阶段。
现代冷轧生产技术基本上以连续化、高速化和专业化为特征,出现了全连续冷连轧机组、酸洗一冷连轧联合机组、酸洗一冷连轧一连退联合机组等全连续设备冷轧设备,出现了出口速度达到2000 m/min以上的冷连轧机,出现了专业生产镀锡原板、极薄板的冷连轧机等等。
1958年鞍钢建成了我国第一套冷带钢轧机,即1700 mm四辊可逆轧机,之后的几十年仅鞍钢和太钢有几台单机架可逆轧机可以生产宽带钢,不仅效率低,装备水平也差,产品品种和质量无法和世界先进水平竞争。
宝钢冷轧方向发展及现状

宝钢冷轧方向发展及现状宝钢冷轧方向发展及现状一、创建改革开放后,上海家用电器、搪瓷制品、自行车、电冰箱、罐头食品等加工工业蓬勃发展,所用冷轧薄卷板、镀锡卷板的数量急剧上升,国内供应缺口很大,70%靠进口解决。
为此市冶金工业局在“七五”发展规划中提出建立一个年产30万吨冷轧薄卷板的专业厂,而后再通过第二期工程发展至50万吨,并生产镀锡板等产品,满足市场需要,优化产品结构。
此项目得到市政府领导的支持。
1988年,项目经国家计委批准,列为上海市重点工程之一,有上海第一钢铁厂、上海实事公司、中国物资开发投资公司、美国上海太平洋合股有限公司共同投资,建立中美合资益昌薄板有限公司。
第一期工程的基建投资为7.11亿元,其中外汇6970万美元。
该项目于1989年2月16日动工建设;七大生产机组的设备分别由法国、奥地利和美国引进。
1990年11月29日,五机架连轧机组先行试车,轧出第一卷0.5毫米厚的冷轧卷板。
1991年2月15日,七大机组全线开通,辅助设施全部运行,经10个月的负荷试车和试生产,当年产冷轧薄卷板47279吨,1992年达到13.84万吨,1993年增至17.55万吨。
二、生产机组酸洗机组益昌薄板厂生产的冷轧卷板,采用热轧卷板作为坯料。
轧制前需先进行酸洗,将黏附在热轧卷板中的氧化铁皮清除掉,以确保冷轧板在轧制时的表面质量。
该厂在设计和引进设备的过程中即着眼于工艺的先进性,预计二期工程的产量将达到年产50万吨的水平,故酸洗能力必须大于此数;还需具有良好的酸回收装置,既能节约酸的用量,又不致造成环境的污染。
经对国外拟引进的两条生产线的比较和论证,最后选择了奥地利鲁特纳(RUTHNA)公司生产的“推拉式酸洗机组”。
该机组是20世纪80年代末世界上推拉式酸洗机组中速度最快的一套,最大运行速度每分钟180米,年酸洗能力为55.8万吨,能满足二期工程的需要;同时,该机组还配备了酸再生装置,酸回收率可达99%以上。
宝钢初轧工艺技术的进步与发展

宝钢初轧工艺技术的进步与发展宝钢分公司初轧工厂为宝钢一期建设项目,在宝钢二期建设项目投产之前,从炼钢到成材,必须通过初轧开坯来衔接,初轧在宝钢这一钢铁联合企业中起着承上启下的作用,是由钢转材的关键中间生产工序。
初轧工厂经过全面达标期、稳定运行期、精益运行期三个阶段的发展,工艺装备、生产技术和产品研发不断进步,自1985年9月投产至年末累计生产坯材多万吨为宝钢的发展做出了巨大贡献,取得了显著经济效益和社会效益。
1 初轧工厂概况宝钢分公司初轧工厂整套设备从日本引进,是全球最后一套以模铸钢锭为原料的大型方/板坯初轧机,也代表着初轧工艺与装备的最高水平。
工厂年设计生产能力300万,t其中板坯118万,t方坯122万,t管坯60万t。
1.1 主要工艺装备初轧工厂于1985年9月20日投产,经过二十多年的发展,目前主要工艺装备组成如下:均热跨主要有6组均热炉共18个均热坑(其中4组为蓄热式)、1座步进梁式大方坯加热炉、4组兼具加热与缓冷功能的保温坑;主轧线主要工艺设备有2台串列布置Φ1300初轧机、热火焰清理机、剪切机、立平布置6机架连轧机、飞剪、热锯、冷床等设备;精整设备主要包括:火焰清理设备、抛丸机、探伤设备(磁粉表面探伤与超声波探伤)、砂轮修磨机、矫直机(压力矫直与十辊矫直)、退火炉、砂轮切割锯、砂轮剥皮机、车削剥皮机等主要设备,以上述设备为基础组成2条圆管坯机械清理线、2条小方坯机械清理线、1条大方坯机械清理线及1条板坯人工清理线。
工厂均热跨与主轧制线呈“T”字形布置,板坯、方坯、管坯精整跨分别沿主轧跨及其后平行分布。
1.2 生产历程在投产后至1990年的5年全面达标期内,初轧产线生产顺行,产量提升迅速,1988年、1989年连续两年产量超过设计能力,收得率、工序能耗等主要经济指标实现全面达标,如图1~3所示。
图1:初轧工厂历年产量变化趋势图2:全面达标期主要锭型收得率增长趋势图3:全面达标期工序能耗下降趋势随着1989年宝钢二期1930mm连铸项目的投产,模铸钢锭量总体有所下降。
宝钢不锈钢冷轧简介

• (5) 5#机架还配备了与板形辊实现闭环控制的工作 辊精细冷却控制功能,进一步提高了对板形的控 制能力; • (6) 设置了1#机架前馈和反馈控制、5#机架前馈 和反馈控制,以及1#机架的轧辊偏心补偿控制功 能等。 • (7) 轧制润滑系统采用同种基油的高、低浓度的乳 化液循环冷却系统,各种轧制条件下的乳化液供 应模式切换灵活,很好满足了轧制碳钢软钢和高 强钢、以及铁素体不锈钢的需要。 • (8) 机组设有自动和手段机架清洗系统,保证了在 钢种切换前机架内部的清洁。
典型冷轧机。
• 多辊轧机是指一个机架内轧辊数多于4个的轧机,早期是 六辊式和十二辊式的。现在普遍使用排列顺序为1、2、3
、4的森吉米尔型二十辊轧机,即每个工作辊是由2个第一
中间辊、3个第二中间辊和4个外支撑辊支撑,最后组装到 整体机架中。
• 这种结构使得轧机刚性很大、工作辊绕度很小。工作辊是
由弹性模量很大的材质制成的,能承受很大的轧制压力, 加上较完善的辊形调节系统,所以多辊轧机可以轧制极薄 带钢和变形困难的硅钢、不锈钢,以及高强度的铬镍合金 材料。
• 焊接条件: • 两带钢厚差:h21.3h1,h2-h11.0mm • (碳钢与碳钢,奥氏体与奥氏体不锈钢焊接) • h21.2h1,h2-h10.6mm • (碳钢与不锈钢,非奥氏体与非奥氏体不锈钢 焊接) • 带钢表面状况:经酸洗的热轧/冷轧板 • 两带钢材质:一般冷轧板和不锈钢
• 注:*1-低碳钢系碳当量≤0.45% • [碳当量]= C+Mn/6+Si/24+Ni/40+Cr/5+Mo/4+V/14 • *2-超低碳钢C<0.01% • *3-高强钢最大抗张强度750MPa • *4-√标示可以使用,×标示不根据 实验室结果确定。 • *6-焊后退火处理:适用于HSS 650MPa及其以 上强度品种
轧制技术新进展
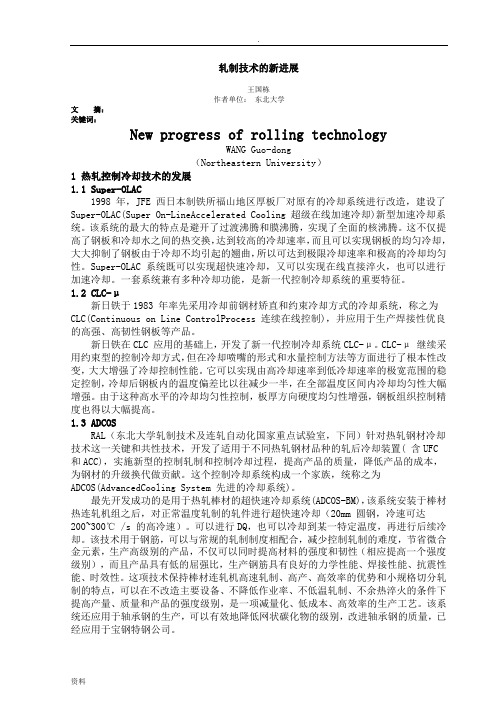
轧制技术的新进展王国栋作者单位:东北大学文摘:关键词:New progress of rolling technologyWANG Guo-dong(Northeastern University)1 热轧控制冷却技术的发展1.1 Super-OLAC1998 年,JFE 西日本制铁所福山地区厚板厂对原有的冷却系统进行改造,建设了Super-OLAC(Super On-LineAccelerated Cooling 超级在线加速冷却)新型加速冷却系统。
该系统的最大的特点是避开了过渡沸腾和膜沸腾,实现了全面的核沸腾。
这不仅提高了钢板和冷却水之间的热交换,达到较高的冷却速率,而且可以实现钢板的均匀冷却,大大抑制了钢板由于冷却不均引起的翘曲,所以可达到极限冷却速率和极高的冷却均匀性。
Super-OLAC 系统既可以实现超快速冷却,又可以实现在线直接淬火,也可以进行加速冷却。
一套系统兼有多种冷却功能,是新一代控制冷却系统的重要特征。
1.2 CLC-μ新日铁于1983 年率先采用冷却前钢材矫直和约束冷却方式的冷却系统,称之为CLC(Continuous on Line ControlProcess 连续在线控制),并应用于生产焊接性优良的高强、高韧性钢板等产品。
新日铁在CLC 应用的基础上,开发了新一代控制冷却系统CLC-μ。
CLC-μ继续采用约束型的控制冷却方式,但在冷却喷嘴的形式和水量控制方法等方面进行了根本性改变,大大增强了冷却控制性能。
它可以实现由高冷却速率到低冷却速率的极宽范围的稳定控制,冷却后钢板内的温度偏差比以往减少一半,在全部温度区间内冷却均匀性大幅增强。
由于这种高水平的冷却均匀性控制,板厚方向硬度均匀性增强,钢板组织控制精度也得以大幅提高。
1.3 ADCOSRAL(东北大学轧制技术及连轧自动化国家重点试验室,下同)针对热轧钢材冷却技术这一关键和共性技术,开发了适用于不同热轧钢材品种的轧后冷却装置( 含UFC 和ACC),实施新型的控制轧制和控制冷却过程,提高产品的质量,降低产品的成本,为钢材的升级换代做贡献。
简述冷轧带钢生产工艺流程
简述冷轧带钢生产工艺流程# [简述冷轧带钢生产工艺流程]## 一、冷轧带钢的历史:从传统到现代1. 早期的冷轧探索- 其实啊,冷轧带钢的历史那可有些年头了。
在很久以前,人们就开始尝试对金属进行冷加工。
就好比我们做面食的时候,会把面团擀平,早期的冷轧就有点像这样,只不过是对金属材料。
最初,冷轧只是一些简单的手工操作,铁匠们会用简单的工具对铁条进行冷压,让它变得更薄更平整。
这就像是用手把一块厚厚的泥巴捏薄一样,虽然很原始,但这就是冷轧的雏形。
- 在工业革命之后,随着机械制造的发展,冷轧带钢有了初步的机械加工方式。
一些简单的轧机被发明出来,能够对钢带进行小规模的冷轧生产。
但是这个时候的冷轧带钢产量很低,质量也不太稳定,就像刚开始学做饭,做出来的菜味道时好时坏。
1.2 现代冷轧带钢的发展- 随着科学技术的不断进步,冷轧带钢迎来了大发展时期。
就像汽车从老爷车发展到现代的各种高性能汽车一样。
在20世纪,新的轧机技术、控制系统和材料科学的发展,让冷轧带钢的生产发生了翻天覆地的变化。
现在的冷轧带钢生产可以精确控制钢带的厚度、宽度和表面质量,产量也大大提高。
比如说,现在一个大型的冷轧带钢工厂一天生产的钢带量,可能比以前一个小工厂一年生产的都多。
## 二、冷轧带钢的制作过程:从原料到成品1. 原料准备- 冷轧带钢的原料一般是热轧带钢。
这就好比我们做蛋糕,热轧带钢就是蛋糕的胚子。
在把热轧带钢作为冷轧原料之前,要对它进行一些处理。
首先要检查它的表面质量,就像我们挑选水果一样,把有瑕疵的地方挑出来。
如果热轧带钢表面有氧化皮之类的东西,还要进行酸洗,这就像是给钢带洗个澡,把脏东西去掉。
只有干净、质量合格的热轧带钢才能进入冷轧工序。
1.1 冷轧轧制- 冷轧轧制是冷轧带钢生产的核心环节。
说白了就是用轧机把钢带压薄。
这个轧机就像一个超级大的擀面杖。
钢带在轧机里被上下两个轧辊挤压,就像面团在擀面杖下被擀薄一样。
不过,这个过程可不像擀面团那么简单。
4.国内冷轧产能产线篇--顾敏华
华东 华北 东北 华中 华南 西南 西北
0
华东总产能3055万吨;华北总产能1957万吨;东北总产能1137万吨;华中总产能 985万吨;华南总产能430万吨;西南总产能272万吨;西北总产能210万吨。全国 共有冷轧产能8046万吨左右。
全国冷轧产能发展图
8500 7500 6500 5500 4500 3500 2500 1500
500
2003年 2004年 2005年 2006年 2007年 2008年 2009年 2010年 2011年
• 2003年前我国冷轧产能仅有749万吨,2009年产能累计达到6773万 吨,较03年增长了800%之多,而到2011年国内冷轧产能将达到8026 万吨。
国内冷轧产能产线篇
国内冷轧产线发展史
• 60年代鞍钢拥有我国第一套单机架宽 带冷轧机
• 70年代武钢拥有我国第一套宽 1700mm冷连轧机轧板带生产线
• 80年代宝钢拥有我国第一条2030mm 全连续式冷轧机
• 2005年鞍钢自主研发的1780mm型宽 带钢冷轧生产线
国内冷轧轧机类型
• 按制方式来分有可逆冷轧机和串列 式冷连轧机两大类
• 可逆冷轧机又可分为单机架可逆冷轧机和 双机架可逆冷轧机;串列式冷连轧机可分 为常规冷连轧机、全连续冷连轧机、酸洗 一冷轧联合机组和酸洗一冷轧一连续退火 联合生产线。
按连续式轧机(酸连轧)和推拉式 (可逆式)轧机 分类
产线情况
38% 62%
连续式 推拉式
产能情况 32%
68% 连续式 推拉式
冷轧生产工艺流程图
全国冷轧产线分布图
全国冷轧分区域产线图
60
50
华东
40
华北
宝钢冷轧带钢生产简介0708
新酸洗
设计年产量:75万t/年,2004年产量86.9万t 产品品种:低碳钢、结构钢、汽车结构钢、压力容器钢等 产品规格:1.0~6.0×800~1650 mm 最大卷重:38.6t 钢卷内径:φ760 mm 钢卷外径:φ2150 mm 工艺段最大速度:120m/min 入口活套:340m 出口活套:216m 拉矫最大延伸率:3.0% 工艺特点:浅槽酸洗
宝钢股份公司冷轧厂概况(1)
• 产品涵盖了普冷板、电镀锌、热镀锌、彩涂板、镀锡板、 电工钢、耐指纹板、酸洗热轧板等众多品种,并具备规模 产生高质量汽车外板、电机电气用材、高档家用电气用材 和高级包装用材。
• 设计年产量为512万吨,而04年实际产量已突破了604万吨 商品材这样一个极具挑战性的水平。
宝钢冷轧带钢生产简介0708
辊轴
平衡 缸
压
块
金属套
-
-筒
+ +
+
++
+
-
+ + -
a)
CVC4
b)
图1-2 2030CVC4和DSR轧机DSR
宝钢冷轧带钢生产简介0708
板形控制执行机构: 1. G1~G3工作辊正液压弯辊, 2. G4~G5工作辊正负液压弯辊, 3. G5 CVC工作辊轴向位移或DSR液压胀辊, 4. 工作辊36段分区冷却 控制模式: 1. 过程设定G1~G4工作辊正负液压弯辊 2. G5闭环控制 平直度仪:ABB Stressometer平直度仪 最大轧制速度: 1900m/min
(无光) 工艺段最高速度:480m/min 工艺特点:采用了不溶性阳极,电镀电流闭环控制,
边缘罩系统。
宝钢国内独家开发成功冷轧TRIP
宝钢国内独家开发成功冷轧TRIP
佚名
【期刊名称】《重型机械科技》
【年(卷),期】2004()4
【摘要】TRIP钢即相变诱导塑性钢,宝钢开发成功的TRIP钢,强度级别为
600Mpa,因这种车板强度高,大致能使车身减薄10%~20%,从而减少了车中和车身成本,亦降低了油耗,为打造减轻环境污染的“环境友好车”创造了良好条件。
【总页数】1页(P48-48)
【关键词】冷轧;TRIP钢;塑性;减薄;相变;宝钢;强度;开发成功;环境友好;中和
【正文语种】中文
【中图分类】TH133.332;TG142
【相关文献】
1.VFS5000D速冻食品包装机填补国内空白/软包装马蹄笋填补国内空白/新型球形棒糖包装机填补国内空白/宝钢冷轧包装材覆盖国内所有品种二次冷轧镀铬板填补国内空白/美国公司开发出新的塑料包装成型机 [J],
2.粗铜无氧化掺氮还原火法精炼工艺/适用于铝电解槽用炭块的加热装置/紫杂铜一步电解生产阴极铜的方法/电流直热式铝型材加热装置/铝合金型材表面涂装方法及专用设备/大型钨单晶/一种铜连铸熔炼炉的保温炉密封炉盖/高密度钨合金/铝冷轧机板型控制新技术/从含钨废料中回收钨的新工艺/铜阳极炉还原氧化铜的还原剂和还原方法/碳化钨涂覆金刚石的新方法/制造钛细粉末的新工艺/阳极杆矫直技术开发成功/国内最大直径多晶硅/数字成像传感器/熔融金属取样器/铝基稀土合金研制
成功 [J],
3.自主开发成功冷轧板形控制技术是宝钢的又一新跨越 [J], 无
4.宝钢国内独家开发成功冷轧TRIP钢 [J], 晓兰
5.宝钢开发成功一次搪瓷工艺用冷轧板 [J], 卫星
因版权原因,仅展示原文概要,查看原文内容请购买。
- 1、下载文档前请自行甄别文档内容的完整性,平台不提供额外的编辑、内容补充、找答案等附加服务。
- 2、"仅部分预览"的文档,不可在线预览部分如存在完整性等问题,可反馈申请退款(可完整预览的文档不适用该条件!)。
- 3、如文档侵犯您的权益,请联系客服反馈,我们会尽快为您处理(人工客服工作时间:9:00-18:30)。
宝钢冷轧核心技术研发历程
冷轧是冶金流程中非常重要的变形工序,在金属相变点温度以下,将轧件压缩到理想的厚度,使其具有良好的力学性能、优良的表面质量、精密的尺寸精度,可以广泛应用于汽车、家电、电子、建筑、包装等各个行业。
虽然近年来随着热轧设备的不断进步,热卷箱、无头轧制、边部加热、层流冷却边部遮蔽等设备的开发使用,一定程度上提高了热轧产品的温度均匀性,但热轧产品的性能和厚度均匀性仍然无法和冷轧产品相媲美。
此外,冷轧产品的表面质量、冲压性能、电磁性能,也是热轧产品无法达到的。
以硅钢为例,我国曾大力推广以高效的冷轧硅钢取代落后热轧硅钢,“以冷代热”以节约在传输和转换过程中损耗的电能。
冷轧作为“轧薄、轧亮、轧精”的工序,有着无可替代的功能和优势,将来还将不断发展。
宝钢从1988年第1条冷轧机组投产以来,经过20年的生产和研发,经历了一条从引进消化到不断改进,发展到自主创新的道路,引领着国内冷轧技术的发展。
冷轧机核心技术的发展
如果往前追溯,钢的冷轧最早始于19世纪中叶的德国,当时只能生产宽度20~25 mm的冷轧钢带。
美国在1920年第一次成功地轧制出宽带钢,并很快由单机不可逆轧制而跨入单机可逆式轧制。
1926年阿姆柯公司巴特勒工厂建成四机架冷连轧机。
冷轧带钢生产经历了漫长的发展过程,从最初的单张轧制到现在的成卷轧制,从可逆轧机到全连续轧机再到酸轧联合机组的多种生产工艺,装备水平和自动化程度不断提高。
特别是20世纪七、八十年代,冷轧技术在全连续和自动化技术的带动下,出现了一个快速发展的阶段。
现代冷轧生产技术基本上以连续化、高速化和专业化为特征,出现了全连续冷连轧机组、酸洗一冷连轧联合机组、酸洗一冷连轧一连退联合机组等全连续设备冷轧设备,出现了出口速度达到2000 m/min以上的冷连轧机,出现了专业生产镀锡原板、极薄板的冷连轧机等等。
1958年鞍钢建成了我国第一套冷带钢轧机,即1700 mm四辊可逆轧机,之后的几十年仅鞍钢和太钢有几台单机架可逆轧机可以生产宽带钢,不仅效率低,装备水平也差,产品品种和质量无法和世界先进水平竞争。
1978年初,武钢从国外成套引进1700mm 五机架冷连轧设备,之后宝钢引进建成2030mm、1420 mm和1550 mm冷连轧机,实现了国内冷轧设备质的飞跃。
近年来,国内各大钢铁企业纷纷上马冷连轧生产线,部分民
营企业也跃跃欲试。
随着用户对冷轧板带产品的要求越来越苛刻,带动相关技术不断进步。
纵观冷轧技术的发展历程,不外乎围绕两个问题展开:一是如何提高质量,并稳定保持;二是如何低成本生产。
冷轧产品最关注的质量指标,也就是冷轧产品的特点,包括力学性能、表面质量、尺寸精度三个方面,其中尺寸精度包括厚度精度、板形精度和边降精度。
如何根据用户需求不断提高质量,并稳定保持,是每一个冷轧技术人员的追求。
冷轧过程的成本主要包括电能消耗、乳化液消耗、轧辊消耗等,如何在保证稳定生产和高质量的同时降低这些消耗,直接关系到产品的竞争力。
围绕这两个问题,各国学者和技术人员在冷轧技术上开展了大量的研究,形成了三大方面的冷轧核心技术,包括:稳定通板技术、表面控制技术、精密轧制技术。
稳定通板技术的发展经历了连续轧制技术开发、工艺过程设定技术使用、钢卷重量增加、振动抑制技术研究等过程。
表面控制技术经历了轧制润滑剂开发、轧辊材质改进、轧辊毛化技术开发等过程。
精密轧制技术包括厚度控制技术、板形控制技术和边降控制技术。
厚度控制技术经历了液压压下技术开发、滚动轴承代替油膜轴承技术、厚度自动控制技术开发等过程,目前国际上先进机组的厚度控制精度达到±0.5%~±1.2%(根据厚度不同而变化);板形控制技术经历了液压弯辊技术开发、HC系列轧机和CVC系列轧机开发、板形自动控制技术开发等过程,目前国际上先进机组的板形控制精度达到5~12 I Unit(根据厚度不同而变化);边降控制技术经历了K—WRS轧机开发、EDC技术开发、边降自动控制技术开发等过程,目前国际上先进的边降控制指标达到5μm(距边部100 mm位置厚度与距边部15mm位置厚度之差)。
宝钢在冷轧核心技术方面的研发
宝钢现有6套冷连轧机组,在建2条。
2030、1420和1730mm轧机分别于1988年、1998年和2007年投产,都是从德国SMS和西门子引进的。
1550和1800 mm轧机分别是1999年和2003年投产的,都是从日本三菱日立和日立电气公司引进的。
这5套冷连轧机组分别代表了当时西方和东方最先进的轧钢技术。
2030 mm冷连轧机1996年将第5机架CVC改造为DSR,2005年由西门子完成三电系统改造,1420 mm冷连轧机2006年由西门子对厚度和板形控制系统进行改造,1550mm轧机2005年对轧机凸度仪和边降仪进行改造。
1220mm轧机系50年代由美国麦斯塔(MESTA)公司设计制造,1989年从法国索拉克(SOLLAC)公司引进,2000年由日本三菱对其进行全面改造。
不锈钢
分公司和梅钢各有l条冷连轧机组正在建设。
此外,宝钢在冷轧薄板厂建有双机架二次冷轧机组1条,还有轧制硅钢、不锈钢、特殊钢的单机架冷轧机组若干条。
宝钢在冷轧后处理线上还有很多平整机组。
宝钢在20年冷轧生产的基础上,在冷轧厂、硅钢部、薄板厂、宝日汽车板、研究院等多个部门和单位的通力合作下,开展了大量冷轧核心技术的研发。
宝钢在稳定通板技术、表面控制技术、精密轧制技术三个方面的研究情况如下表:
冷轧机核心技术研发与工程的结合
宝钢在通板稳定技术、表面控制技术、精密轧制技术等方面,从全套引进到自主研究改进,走了一条迅速提高的捷径,技术水平达到了较高的水准。
同时由于市场竞争的关系,宝钢越来越买不到先进的技术,而且,宝钢经过大量冷轧工艺装备方面的科研、改造,结合20多年的冷轧生产实践,积累了大量的研究成果和经验,已经具备了良好的基础,可以进一步进行提炼和提升,以形成宝钢自主知识产权的轧钢工艺装备技术。
另一方面,通过工程中应用创新技术,可以直接提升工程的水平,建成别人无法仿制的机组。
因此,将研发与工程结合,不仅是宝钢自身发展的需要,也是提升研发实力和水平的重要手段。
宝钢在研发与工程的结合方面,已经进行了很多探索,例如冷轧取向硅钢建设工程、梅钢冷轧工程等。