旋风DPM问题
化工生产车间旋风分离器技术问答

化工生产车间旋分分离器技术问答1、旋风分离器的工作原理是什么?旋风分离器是利用惯性离心力分离气-固混合物的设备。
在气固混合物外旋过程中由于固相颗粒密度较大,所受的离心力也大,从而被甩向外围并与器壁碰撞后失去动能,滑落至锥形底部,经除尘管定时排出。
外旋流到达器底后在漩涡中心的压强差作用下沿中心向上折回,形成自下而上的内旋流,最后净化气体由筒体中央的排气管排出。
2、旋风分离器的优点是什么?结构简单,没有运动部件,操作不受温度和压强的限制,分离效率可以高达70%~90%,可以分离出小到5um以下的颗粒,对5um 以下细微颗粒分离效率较低,可用后接袋滤器或湿法除尘装置的方法来捕集。
3、旋风分离器的缺点是什么?其缺点是:气体在器内的流动阻力较大对器壁的磨损较严重分离效率对气体流量的变化较为敏感等。
4、影响旋风分离器分离效果的因素有哪些?(1)颗粒直径,直径越大分离效果越好所以旋风分离效果与颗粒直径的平方成正比;(2)颗粒密度,颗粒密度大就意味着颗粒质量大那么颗粒所产生的离心力大,则分离效果就好。
(3)线速度:线速度大,产生的离心力大则分离效果好,但是,压强降则随进口气速的平方倍增长,气体涡流程度加剧,反而不利于分离,为了使旋风分离器的操作经济有效,进口气体流速通常控制在10~25m/s的范围内。
(4)气体黏度:分离效果与气体黏度成反比,气体黏度大分离效果不好;(5)旋风分离器的分离效果跟分离器的直径成反比,分离器直径越大气固分离越难;(6)提高分离器进口固相含量有利于颗粒的聚积,可以提高分离效率,同时有利于抑制气体涡流,所以提高进口气体中固相含量对旋风分离器的分离效率及压强降均有利;(7)温度提高,气体的黏度增大,则降低了分离器的分离效率,所以,温度高不利于分离。
旋风除尘器性能的影响因素
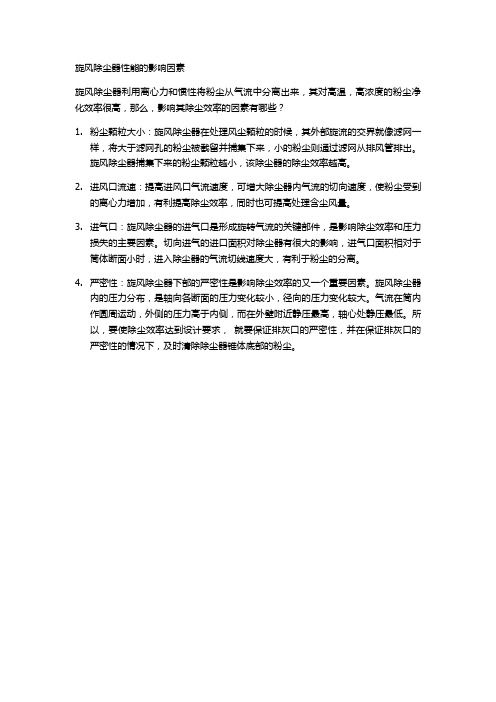
旋风除尘器性能的影响因素
旋风除尘器利用离心力和惯性将粉尘从气流中分离出来,其对高温,高浓度的粉尘净化效率很高,那么,影响其除尘效率的因素有哪些?
1.粉尘颗粒大小:旋风除尘器在处理风尘颗粒的时候,其外部旋流的交界就像滤网一
样,将大于滤网孔的粉尘被截留并捕集下来,小的粉尘则通过滤网从排风管排出。
旋风除尘器捕集下来的粉尘颗粒越小,该除尘器的除尘效率越高。
2.进风口流速:提高进风口气流速度,可增大除尘器内气流的切向速度,使粉尘受到
的离心力增加,有利提高除尘效率,同时也可提高处理含尘风量。
3.进气口:旋风除尘器的进气口是形成旋转气流的关键部件,是影响除尘效率和压力
损失的主要因素。
切向进气的进口面积对除尘器有很大的影响,进气口面积相对于筒体断面小时,进入除尘器的气流切线速度大,有利于粉尘的分离。
4.严密性:旋风除尘器下部的严密性是影响除尘效率的又一个重要因素。
旋风除尘器
内的压力分布,是轴向各断面的压力变化较小,径向的压力变化较大。
气流在筒内作圆周运动,外侧的压力高于内侧,而在外壁附近静压最高,轴心处静压最低。
所以,要使除尘效率达到设计要求,就要保证排灰口的严密性,并在保证排灰口的严密性的情况下,及时清除除尘器锥体底部的粉尘。
旋风除尘效率误差分析

旋风除尘效率误差分析
旋风除尘器的各个部分都有相应的尺寸比例,各比例关系的变化会影响旋风除尘器的效率和压力损失,其中除尘器直径、入口尺寸和排气管直径是主要影响因素。
需要注意的是,当超过限度时,有利因素也可以转化为不利因素。
另外,有些因素有利于提高除尘效率。
但是,会增加压力损失。
因此,应该考虑各种因素的调整。
旋风除尘器的进风口是形成旋转气流的关键部件,也是影响除尘器效率压力的损失的主要因素。
切向风口的面积对除尘器的影响很大。
当进风面积相对于筒体截面积较小时,进入除尘器的气流切向速度较大,有利于除尘。
筒体直径时旋风除尘器的基本尺寸。
旋转气流的且行速度与粉尘产生的离心力和筒体直径成反比。
在相同切向速度下,筒体直径越小,气流的旋转半径越小,颗粒所受的离心力越大,粉尘颗粒越容易造成堵塞,特别时对粘性物料。
排气管的直径和插入对旋风除尘器的除尘效率有很大影响。
排气管的直径应选择适当的值。
如果排气管的直径减小,可以减小到内部涡流的旋转范围。
排气管不易排出粉尘,可以提高除尘效率,但同时,由于排气管的气缸管太近,虽然可以显著减小风道直径的阻力损失,但排气管出口速度加快,阻力损失增大,容易形成内外旋流的“短路”现象,使外旋流中的部分粉尘直接混入排气管排出,从而降低除尘效率。
一般认为排气管直径为气缸直径的0.5-0.6倍,如果排气管插入过浅,容易时含尘气流直接进入排气管,影响除尘效率。
当排气管插入较深时,容易增加气流与管壁之间的摩擦面,增加阻力损失。
同时
缩短了排气管与锥筒底部的距离,增加了粉尘二次返混的机会。
排气管的插入应略低于进气口底部。
FLUENT系列资料:7
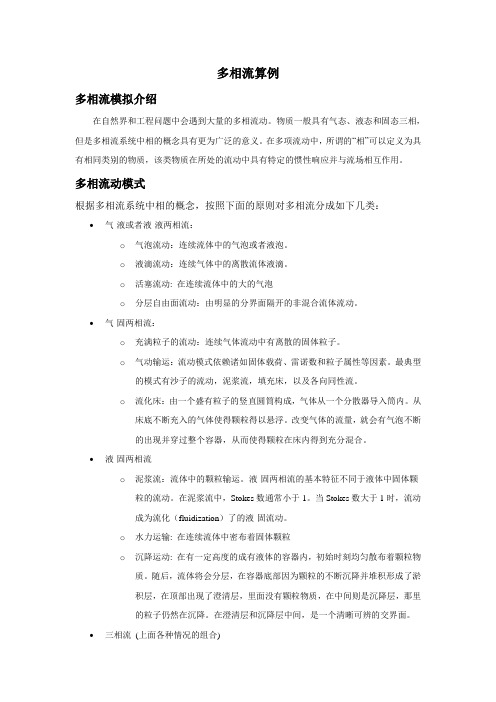
多相流算例多相流模拟介绍在自然界和工程问题中会遇到大量的多相流动。
物质一般具有气态、液态和固态三相,但是多相流系统中相的概念具有更为广泛的意义。
在多项流动中,所谓的“相”可以定义为具有相同类别的物质,该类物质在所处的流动中具有特定的惯性响应并与流场相互作用。
多相流动模式根据多相流系统中相的概念,按照下面的原则对多相流分成如下几类:∙气-液或者液-液两相流:o气泡流动:连续流体中的气泡或者液泡。
o液滴流动:连续气体中的离散流体液滴。
o活塞流动: 在连续流体中的大的气泡o分层自由面流动:由明显的分界面隔开的非混合流体流动。
∙气-固两相流:o充满粒子的流动:连续气体流动中有离散的固体粒子。
o气动输运:流动模式依赖诸如固体载荷、雷诺数和粒子属性等因素。
最典型的模式有沙子的流动,泥浆流,填充床,以及各向同性流。
o流化床:由一个盛有粒子的竖直圆筒构成,气体从一个分散器导入筒内。
从床底不断充入的气体使得颗粒得以悬浮。
改变气体的流量,就会有气泡不断的出现并穿过整个容器,从而使得颗粒在床内得到充分混合。
∙液-固两相流o泥浆流:流体中的颗粒输运。
液-固两相流的基本特征不同于液体中固体颗粒的流动。
在泥浆流中,Stokes数通常小于1。
当Stokes数大于1时,流动成为流化(fluidization)了的液-固流动。
o水力运输: 在连续流体中密布着固体颗粒o沉降运动: 在有一定高度的成有液体的容器内,初始时刻均匀散布着颗粒物质。
随后,流体将会分层,在容器底部因为颗粒的不断沉降并堆积形成了淤积层,在顶部出现了澄清层,里面没有颗粒物质,在中间则是沉降层,那里的粒子仍然在沉降。
在澄清层和沉降层中间,是一个清晰可辨的交界面。
∙三相流(上面各种情况的组合)多相系统的例子各流动模式对应的例子如下:∙气泡流例子:抽吸,通风,空气泵,气穴,蒸发,浮选,洗刷∙液滴流例子:抽吸,喷雾,燃烧室,低温泵,干燥机,蒸发,气冷,刷洗∙活塞流例子:管道或容器内有大尺度气泡的流动∙分层自由面流动例子:分离器中的晃动,核反应装置中的沸腾和冷凝∙粒子负载流动例子:旋风分离器,空气分类器,洗尘器,环境尘埃流动∙风力输运例子:水泥、谷粒和金属粉末的输运∙流化床例子:流化床反应器,循环流化床∙泥浆流例子:泥浆输运,矿物处理∙水力输运例子:矿物处理,生物医学及物理化学中的流体系统∙沉降例子:矿物处理多相建模方法计算流体力学的进展为深入了解多相流动提供了基础。
旋风除尘器方案

1. 引言空气污染是全球范围内的重要环境问题之一,对人类健康和生态系统造成了严重的影响。
其中,工业生产过程中产生的粉尘污染是主要原因之一。
为了解决这一问题,旋风除尘器被广泛应用于工业领域,本文将介绍旋风除尘器的工作原理、设计方案以及性能评价。
2. 工作原理旋风除尘器利用离心力和重力分离出含有粉尘颗粒的气体。
其主要组成部分包括进气口、旋风分离室、底部排气口和收尘桶。
当粉尘污染气体进入进气口后,由于进气口处的导流体板的作用,气流形成旋涡。
较大的粉尘颗粒受到离心力作用被抛出而沉积在分离室底部的收尘桶中,而较小的粉尘颗粒则随气流通过排气口排出。
3. 设计方案3.1 进气口设计进气口设计的关键是要使气体顺利进入旋风分离室,并形成旋涡。
通常采用锥形设计,由于气体通过突然变窄的进气口,速度增加,压力降低,从而形成旋涡。
3.2 旋风分离室设计旋风分离室是整个除尘器的核心部分。
其设计应能够有效分离出粉尘颗粒,同时尽量减小压力损失。
分离室通常采用圆柱形设计,底部为圆锥形。
分离室内壁通常采用光滑的材料制成,以减少气流的阻力,并避免颗粒附着。
3.3 排气口设计排气口的设计应尽量减小压力损失,并有效排出含有粉尘颗粒的气体。
排气口通常位于分离室的顶部,采用管道连接至排气系统。
3.4 收尘桶设计收尘桶用于收集被分离出的粉尘颗粒,其设计应尽量减小粉尘再悬浮的可能性,并方便清理和维护。
4. 性能评价旋风除尘器的性能评价主要包括效率和压力损失。
效率是指除尘器对粉尘颗粒的分离能力,通常用分离效率来衡量。
压力损失是指气流通过除尘器时所受到的压力降低。
性能评价可以通过实验测试和数值模拟来进行。
5. 结论旋风除尘器作为一种常用的工业粉尘处理设备,具有简单、经济、高效的特点,被广泛应用于各个工业领域。
在设计和制造过程中,需要注意进气口、旋风分离室、排气口和收尘桶的合理设计,以达到最佳的除尘效果。
同时,通过性能评价可以对除尘器的效率和压力损失进行量化分析,进一步优化除尘器的设计和运行。
旋风除尘器的设计与计算
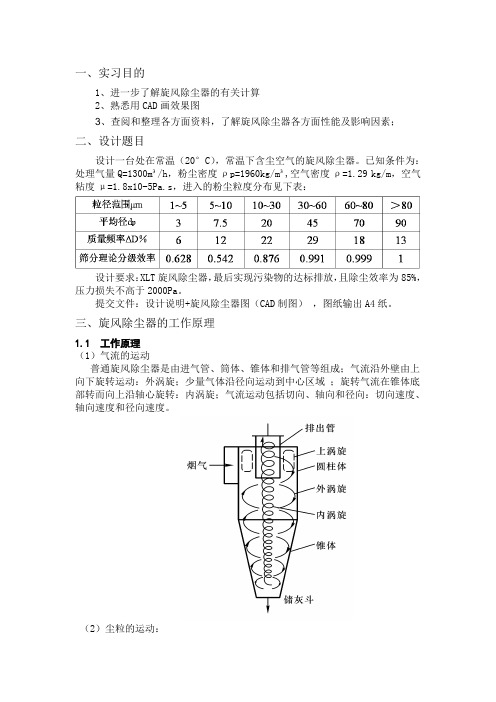
一、实习目的1、进一步了解旋风除尘器的有关计算2、熟悉用CAD画效果图3、查阅和整理各方面资料,了解旋风除尘器各方面性能及影响因素;二、设计题目设计一台处在常温(20°C),常温下含尘空气的旋风除尘器。
已知条件为:处理气量Q=1300m³/h,粉尘密度ρp=1960kg/m³,空气密度ρ=1.29 kg/m,空气粘度μ=1.8x10-5Pa.s,进入的粉尘粒度分布见下表:设计要求:XLT旋风除尘器,最后实现污染物的达标排放,且除尘效率为85%,压力损失不高于2000Pa。
提交文件:设计说明+旋风除尘器图(CAD制图),图纸输出A4纸。
三、旋风除尘器的工作原理1.1 工作原理(1)气流的运动普通旋风除尘器是由进气管、筒体、锥体和排气管等组成;气流沿外壁由上向下旋转运动:外涡旋;少量气体沿径向运动到中心区域;旋转气流在锥体底部转而向上沿轴心旋转:内涡旋;气流运动包括切向、轴向和径向:切向速度、轴向速度和径向速度。
(2)尘粒的运动:切向速度决定气流质点离心力大小,颗粒在离心力作用下逐渐移向外壁;到达外壁的尘粒在气流和重力共同作用下沿壁面落入灰斗;上涡旋-气流从除尘器顶部向下高速旋转时,一部分气流带着细小的尘粒沿筒壁旋转向上,到达顶部后,再沿排出管外壁旋转向下,最后从排出管排出。
1.2特点(1)旋风除尘器与其他除尘器相比,具有结构简单、占地面积小、投资低、操作维修方便以及适用面宽的优点。
(2)旋风除尘器的除尘效率一般达85%左右,高效的旋风除尘器对于输送、破碎、卸料、包装、清扫等工业生产过程产生的含尘气体除尘效率可达95%-98%,对于燃煤炉窑产生烟气的除尘效率可以达到92%-95%。
(3)XLT 旋风除尘器的主要特点(4)旋风除尘器捕集<5μm 颗粒的效率不高,一般可以作为高浓度除尘系统的预除尘器,与其他类型高效除尘器合用。
可用于10μm 以上颗粒的去除,符合此题的题设条件。
旋风除尘器引起漏风的原因及影响磨损的因素

旋风除尘器引起漏风的原因1.除尘器进出口连接法兰的漏风主要是由于连接件使用不当引起的,例如螺栓没有拧紧、垫片不够均匀、法兰面不平整等。
2.除尘器的本体漏风的原因主要是磨损,对旋风除尘器而言本体磨损是经常发生的。
特别是下椎体因为含尘气流在旋转或冲击除尘器本体时磨损特别严重,根据现场经验当气体含尘质量浓度超过10g/m³在不到100天时间里可能磨坏3㎜厚的钢板。
3.旋风除尘器卸灰装置的漏风是除尘器漏风的又一个重要方面。
卸灰阀多用于机械自动式如重锤式等这些阀严密性较差,稍有不当即产生漏风。
这是除尘器运行管理的重要环节。
旋风除尘器影响分割粒径的二次效应当尘粒稍小于临界粒径时效率则为零,但实际上的效率曲线与理论效率曲线是不一致的,造成差异的原因就是二次效应。
接近较小粒径区,实际效率高于理论效率,即高于0%;而对稍大于分割粒径的尘粒,实际效率低于理论效率,即低于100%。
前一个区域的结果表示,理应逸出的尘粒却由于聚集或被较大的尘粒撞向器壁而脱离气流并被捕集。
后一个区域的情况意味着,理应沉降入灰斗的尘粒却随干净空气一起排空,其原因有:1.撞向内部漩涡2.进入灰斗的气流将灰重新卷出3.涡流引起的夹带4.当向内漂移超过离心力时,会使尘粒进入内漩涡。
旋风除尘器影响磨损的因素1、磨损与负荷关系在高浓度、高速度含尘气流不断冲刷下,除尘器极易被磨损。
一般认为冲蚀磨损量与冲刷速度的2-3次方呈正比关系。
除尘器一般先在钢板上磨出沟槽,然后被加速磨损,直至磨穿。
除尘器的磨损都随灰尘负荷、灰尘密度和硬度以及气体速度的增加而加快,随构成除尘器壁的材料硬度的增加而减慢。
灰尘浓度低时,一般有较轻磨损。
浓度增大,被磨损的面积也增大。
2、磨损与气速关系磨损与气体速度成指数关系。
矩形弯头,指数为2;垂直射流的冲击,大约是2.5-3。
在相同的气流速度下,20°-30°时是磨损最严重的冲击角度。
3、磨损与粒径关系流体动力学理论认为,空气中的小粒子造成的磨损应当较小。
旋风除尘方案

旋风除尘方案1. 引言空气质量的改善日益引起人们的重视,尤其是工业生产过程中产生的粉尘对环境和人体健康的影响。
为了有效地处理工业粉尘问题,旋风除尘器被广泛应用于各个行业。
本文将介绍旋风除尘器的原理、结构和工作流程,并探讨其在工业环境中的应用。
2. 旋风除尘器原理旋风除尘器是一种利用离心力将粉尘从气流中分离的设备。
其原理基于粉尘在离心力作用下沿气流方向运动的规律。
当气流穿过旋风除尘器的长筒时,由于长筒的结构和形状,气流会产生旋转运动。
在气流旋转过程中,重的粉尘颗粒受到离心力的作用被甩到筒壁上,而干净的气体则通过顶部的出口排出。
3. 旋风除尘器结构旋风除尘器一般由以下几个主要部分组成:3.1 进气口进气口是旋风除尘器的入口,负责将含有粉尘的气流引入除尘器中进行处理。
进气口通常位于除尘器的一侧,并通过导流板来引导气流进入。
3.2 旋风筒旋风筒是旋风除尘器的核心部分,也是离心分离的场所。
旋风筒一般为圆筒形状,内部装有导流板和旋风叶片。
其主要作用是引导气流进行旋转,从而产生离心力,将粉尘分离。
3.3 出气口出气口位于除尘器的顶部,用于排放处理后的干净气体。
通常,出气口与旋风筒通过一个连接管相连。
3.4 粉尘收集桶粉尘收集桶位于旋风除尘器的底部,并负责收集分离出的粉尘。
粉尘收集桶一般具有易于清理的设计,方便定期清理和维护。
4. 旋风除尘器工作流程旋风除尘器的工作流程可以分为以下几个步骤:4.1 进气含有粉尘的气流通过进气口进入旋风除尘器。
4.2 旋转在旋风筒内部,气流开始进行旋转运动。
由于旋风筒内的导流板和旋风叶片的作用,气流呈螺旋状运动,并产生离心力。
4.3 分离在离心力的作用下,重的粉尘颗粒被甩到旋风筒的壁上,形成粉尘层。
而干净的气体则从旋风除尘器顶部的出气口排出。
4.4 收集分离出的粉尘颗粒通过重力作用下落到底部的粉尘收集桶中进行收集。
4.5 排空定期清理和维护粉尘收集桶,以确保旋风除尘器的正常运行。
- 1、下载文档前请自行甄别文档内容的完整性,平台不提供额外的编辑、内容补充、找答案等附加服务。
- 2、"仅部分预览"的文档,不可在线预览部分如存在完整性等问题,可反馈申请退款(可完整预览的文档不适用该条件!)。
- 3、如文档侵犯您的权益,请联系客服反馈,我们会尽快为您处理(人工客服工作时间:9:00-18:30)。
为什么不考虑颗粒间的相互运动?
旋风分离器的人 口质量浓度 C =3 0g/m,对应的颗粒相的体积分率 =C/p《1%, 模拟
空间属稀相范畴,可以忽略颗粒之间的碰撞.
为什么选用随机游走模型?
可以采用两相耦合的颗粒随机轨道模型进行计算.但由于旋风分离器内湍流强度较大, 需
要考虑颗粒在湍流气流中的扩散运动,对此采用随机游走模型和涡生存时间模型计算颗粒的
湍流扩散效应.
怎么确定弹性系数?
气相流场计算的壁面处采用无滑移边界条件,对近壁网格点用壁面函数近似处理. 颗粒对
壁面的碰撞恢复系数根据旋风分离器的壁面位置不同分别选取不同的碰撞恢复系数进行试
算确定, 当计算的分离效率与实验结果比较吻合时,确定此碰撞恢复系数.在环形空间,
气速较高,颗粒难以沉积在器壁, 碰撞恢复系数取0.90~1.0;在分离空间,自上而下,随
着颗粒的旋转动量损失,反弹作用逐步减弱,碰撞恢复系数取为0.6 0~0.9;灰斗空间颗粒
的碰撞恢复系数取为0.05~0.50.