玻璃熔窑的冷修改造及相关措施
玻璃熔窑拱顶砌筑质量保证措施

砖之 间的距离处处相等。
12 施工时 ,一般 是在两端各砌筑 一块拱脚砖 ,仔 . 细 找正位置 ,复核其跨 度 、标 高、角度均无误后 ,即 以
23 拱顶砖缝要小 ,研合砖缝时 ,要 一块一块地上 . 下揉动2~3 ,并且 一面砌 筑 ,一 面 用皮 锤敲打 ,使 次 其固定。
5 2 5 灰 缝 大且 灰浆不 饱满 :灰缝 是砌体 的薄 弱 ..
部位 ,灰 缝大 且不饱 满时 ,会 因力量传 递不均 而造成 砖块滑落 。 5 2 4受 力不均匀 :拱顶在受 力后 内力分布十分复 ..
要求。
14拱脚砖体较大 ,搬动不便。 实际砌筑 时,可 以 .
在 已砌完砖 的大面上涂抹泥浆 ( 迎浆 ),将被砌砖靠近
后揉动数次 ,再 用皮锤打 紧。
15 砌 完 的拱 脚表 面应 平整 ,角 度应正 确 ,不得 .
半甚至更 多。 )
们
维普资讯
24 锁砖必须锁紧 ,太松或松 紧不匀都会直接影响 .
拱顶质量 。
杂 ,且 随着外 力变化 而不 断改变 。如果 紧拉条控 制不
好 ,极 容易形成 拱顶 的受 力不均 ,使砖 块 的受力有大
25 拱顶应尽量在 当天砌完 ,且锁砖砌完后 ,要用 .
稀泥灌缝 。拆除拱胎后 ,用干刷清理拱顶 内表面泥浆 , 并 用湿抹布擦洗。
一
确 、牢 固 ;②拱脚梁是 否与立柱靠死 ;③上拉条是否已
调整 固定 。
无碱玻璃纤维熔窑后期维护方案探析

() 1 强化 液面 线 附近 外 层 池 壁砖 的冷 却 效 果 , 求 冷却 风 风 速 要
大 于 1 / , 面线位 置池 壁砖 温度 不高 于 5 0 ; 0 m s液 0℃
( ) 除熔窑 液 面线附 近 的致 密铬 砖外 层 ( 3中6 位 置 ) 液 2拆 图 距 面深 3 0 m 以上 的所有 保温 砖 , 强致 密铬 砖 的保温 效果 ; 0 m 增 的多孔 铬砖 。
0 — g a s Ta k r a e fE l s n Fu n c
Y N a , H NG死e z u L U Q , A o g—d n A GH o Z A — h ,I iW NGD n og
自 19 9 7年 国 内首条万 吨 池窑 拉丝 生产 线在 泰 山玻璃 纤维 有 限公 司投 产 以来 , 璃纤 维 池窑 技术 打破 发 玻
公 司 3窑与 1窑 都是 单元 窑 , 各个 部位 选用 的耐火 材 料基 本 相 同 。1窑 在 20 04年 曾经 停 产冷 修 , 据 根 1窑停 产冷 修采 集 的耐火 材料 侵蚀 数 据分 析 , 窑 重点 侵蚀 部 位 有 : 料 口拐角 、 泡 、 液 洞 、 壁液 面线 熔 投 鼓 流 池 附近 。如果 对 以上部 位进 行 重点 维护 , 降低 耐火 材料 的侵蚀 速度 , 即可延 长熔 窑 的使用 寿命 。我们确 认将 上
鼓 泡有 强化 玻璃 液 的 均 化 和澄 清 效 果 , 高 玻 璃 液 质 量 的作 用 。通 提 过鼓 泡器 在池底 将净 化 的压 缩 空 气从 窑底 鼓 入 玻 璃 液 中 , 缩 空气 在 上 压
升 的过程 中吸 收 了玻 璃液 中的小气 泡 , 其 本 身迅 速 变 大 , 搅 动 四周 的 使 并 玻 璃 液 , 到强 制均 化 和 促 进 澄清 玻 璃 的 目的 。但 是鼓 泡 也 带 有 负 面 的 达
玻璃窑炉实施方案模板

玻璃窑炉实施方案模板玻璃窑炉实施方案模板一、项目背景介绍1.1 项目概述:本项目旨在对现有玻璃窑炉进行改造和升级,提高玻璃产能和质量,减少能耗和污染排放。
1.2 项目目标:通过改造和升级玻璃窑炉,提高玻璃产能至少20%以上,降低能耗和污染排放30%以上。
1.3 实施方案背景:目前玻璃行业面临生产成本上升和环境压力增大的问题,迫切需要对玻璃窑炉进行改造和升级。
二、项目实施方案2.1 技术研究与论证:通过对玻璃生产工艺和技术的研究,选择合适的改造和升级方案,并进行实施前的技术论证。
2.2 设备采购与安装:根据改造和升级方案,采购适应性能要求的设备,并进行安装和调试。
2.3 生产线改造升级:对现有的玻璃生产线进行改造和升级,包括炉膛结构、燃烧系统、废气处理系统等方面的改善。
2.4 运行调试与优化:在改造和升级完成后,对玻璃窑炉进行运行调试和优化,确保其稳定运行和达到预期效果。
2.5 人员培训与管理:对相关人员进行培训,提高其对新设备和工艺的操作和管理能力,确保项目的顺利实施和运营。
三、项目进度计划3.1 前期准备阶段:包括技术研究与论证、设备采购与安装等工作。
预计耗时2个月。
3.2 实施阶段:包括生产线改造升级、运行调试与优化等工作。
预计耗时3个月。
3.3 后期运行阶段:包括人员培训与管理、项目验收与评估等工作。
预计持续6个月。
四、项目资源需求4.1 人力资源:包括项目经理、技术专家、设备安装人员、调试工程师等。
4.2 财力资源:估算改造和升级所需的设备采购费用、工程费用和人员培训费用等。
4.3 时间资源:合理安排项目进度,确保各个环节之间的协调和配合。
五、风险与控制措施5.1 技术风险:在改造和升级过程中,可能出现技术难题和设备故障等问题,需要有相应的技术支持和备用设备。
5.2 运行风险:改造和升级完成后,需对玻璃窑炉进行运行调试和优化,确保其稳定运行和达到预期效果。
5.3 经济风险:改造和升级过程中,需预留一定的资金用于技术研究、设备采购和后期运营等方面的支持。
延长玻璃熔窑使用寿命的几项措施
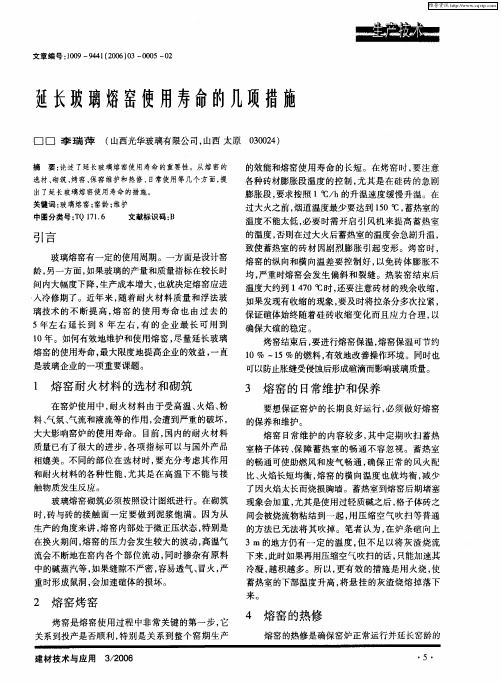
关键词 : 玻璃熔窑 ; 窑龄 ; 维护 中图分类号 : Q 116 T 7 . 文献标识码 : B
温度不能太低 , 必要时需开启引风机来提高蓄热室
的温度 , 否则在过大火后蓄热室的温度会急剧升温,
引言
玻璃熔窑有一定的使用周期 。一方面是设计窑
龄, 另一方面, 如果玻璃的产量和质量指标在较长时 间内大幅度下降 , 生产成本增大 , 也就决定熔窑应进
了 因火焰太 长而烧 损胸 墙 。蓄热 室到熔 窑后 期堵 塞
大大影 响窑炉的使用 寿命。 目前 , 国内的耐火材料
质量已有了很大 的进步 , 各项指标可 以与国外产 品
相媲美 。不 同的部位在选材 时, 要充分考虑其作用 和耐火材料的各种性能 , 尤其是在高温下不能 与接
触物 质 发生反应 。
入冷修期了。近年来 , 随着耐火材料质量 和浮法玻 璃技术 的不断提 高 , 窑 的使 用 寿命 也 由过去 的 熔
5 年左 右延 长到 8年左 右 , 的企业 最长 可用 到 有
确保大碹的稳定 。 烤窑结束后 , 要进行熔窑保温 , 熔窑保温可节约 l 0% 一 5 l %的燃料, 有效地改善操作环境。同时也 可以防止胀缝受侵蚀后形成碹滴而影响玻璃质量。
致使蓄热室的砖 材因剧烈膨胀 引起变形。烤窑时, 熔窑 的纵向和横 向温差要控制好 , 以免砖体膨胀不
均, 严重时熔窑会发生偏斜和裂缝 。热装窑结束后 温度大约到 l 7 0℃时, 4 还要注意砖材的残余收缩 , 如果发现有收缩 的现象 , 要及时将拉条分多次拉紧, 保证碹体始终随着硅砖 收缩变化而且应力合理, 以
选材 、 砌筑 、 烤窑 、 窑维护和热修 、 保 日常使用等几个方 面, 提
旧电熔砖在玻璃熔窑冷修中的使用要求

第45卷第3期2017年6月玻璃与搪瓷GLASS &ENAMELVol. 45 No.3Jun.2017旧电熔砖在玻璃熔窑冷修中的使用要求$张勤学\刘春2(1.中国中轻国际工程有限公司,北京100026;2.重庆晶华窑炉工程有限公司,四川重庆400700)摘要:从旧电熔砖选用及加工、旧电熔砖砌筑两个方面阐述了玫璃熔窑冷修使用旧电熔砖的要求,以达到延长冷修后熔窑窑龄的目的。
关键词:玫璃熔窑;旧电熔砖;冷修中图分类号:TQ171.6+23.5 文献标志码:B 文章编号= 1000-2871(2017)03-0021-03D01:10.13588/ki.g.e.l000-2871.2017.03.005Operational Requirements of Using UsedFusion Cast Refractory in GlassFurnace during Cold RepairZHANG Qinxue, LIU Chun近年来,玻璃企业为了降低玻璃熔窑耐火材料成本,在熔窑冷修中大量使用旧电熔砖,但由于在使用时 没有严格要求,冷修后的熔窑又很快出现穿火、漏料、侵蚀快等问题,缩短了熔窑的使用寿命。
本文较详细地 阐叙了在玻璃熔窑冷修中使用旧电熔砖的要求,对中小玻璃企业进行熔窑冷修有一定指导意义。
1旧电熔砖的选用及加工《日用玻璃熔窑设计一般规定》中对玻璃熔窑各个部位使用的电熔砖类型、质量有明确要求。
旧电熔砖 由于经历过玻璃液侵蚀或高温火焰冲刷,不可避免地会出现被侵蚀、被烧损、炸裂等情况,再利用时必须挑 选,并按要求加工。
(1)加工前准备a企业外购旧电熔砖在购买之前应严格检验外观和质量,并取样送国家级耐火材料质量监督检测单位出具质量检验报告,以免影响玻璃液质量或过早烧损。
b企业自有旧电熔砖如需用在铺面、池壁等直接接触玻璃液的部位,应检验其化学成分,防止其成分影响冷修后熔窑的玻璃液。
c加工前应将所有旧电熔砖按照33#无缩孔、33#普通浇铸、41#无缩孔等类别分别归类,并在现场按区域堆放。
梯度增氧助燃玻璃窑炉熔化部和冷却部结构的改进设计

梯度增氧助燃玻璃窑炉熔化部和冷却部结构的改进设计黄治斌牟竹生(秦皇岛玻璃工业研究设计院有限公司秦皇岛市066001 )摘要玻璃窑炉应用梯度增氧助燃后,燃烧产物的温度、碱蒸气和水蒸气含量以及NOx浓度等均发生了变化,导致熔化 部和冷却部各部位的作业环境和耐火材料使用过程中损毁的原因也发生了改变,本课题在合理选取熔化部和冷却部各部位耐火材料材质的基础上,对熔化部和冷却部窑池结构以及上部空间结构进行了改进设计,以适应梯度增氧助燃上、中、下 部分层燃烧结构,达到了降低整个窑炉N〇J_放浓度的目的,同时也提高了熔化部和冷却部整体结构的安全稳定性,降低 了窑炉的能耗,延长了窑炉的使用寿命。
关键词梯度增氧助燃熔化部和冷却部燃烧产物耐火材料碱蒸气和水蒸气作业环境安全稳定性中图分类号:TQ171 文献标识码:A文章编号:1003-1987(2019)04-0021 -05The Improve Design for Glass Furnace Melter Endand Working End of Gradient Increase Combustion OxygenHUANG Zhibin?MU Zhusheng(Qinhuangdao glass industry research and design institute Company Limited,Qinhuangdao,066001 ) Abstract:After gradient increase combustion oxygen,the temperature^basic vapor and water vapor and NOx content of combustion products that are produced by glass furnace are varied,so that the work environment and damage reason of melter end and working end refractory are varied.On the basis of choice reasonable refractory,This article improve structural design of tanks and superstructure for melter end and working end,In order to adapt to up、centre and below zone of combustion for gradient increase combustion oxygen and reduce emission concentration.The security and stability of melter end and working end are enhanced^saving energy consume of glass furnace and extending life of glass furnace. Key Words:gradient increase combustion oxygen,melter end and working end,combustion products, refractory,basic vapor and water vapor,work environment,security and stability〇引言玻璃窑炉的梯度增氧助燃就是在传统的空气 -燃料燃烧的窑炉中,增加符合一定纯度、温 度、压力、流量要求的氧气,在小炉喷火口下部 喷嘴间隔砖处,以合适的角度喷人到窑炉火焰空 间,实现氧气-燃料燃烧,从而降低燃烧产物中NOx的浓度,通过区域可控的弥散燃烧方式和梯 度控氧控料燃烧技术,在玻璃窑炉内形成符合生 产工艺要求的熔化玻璃配合料的温度曲线,在为 下一工序热工设备一锡槽提供优质玻璃液的同 时,降低整个窑炉废气中NOx排放浓度和熔化玻 璃液的热耗。
浮法玻璃熔窑节能技术及途径.
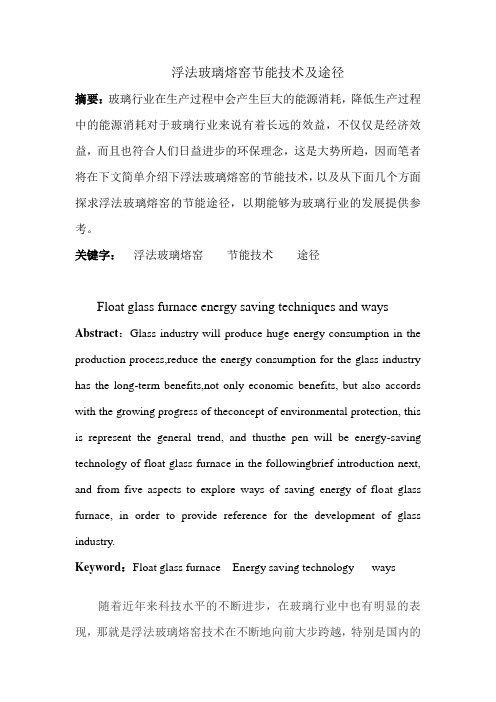
浮法玻璃熔窑节能技术及途径摘要:玻璃行业在生产过程中会产生巨大的能源消耗,降低生产过程中的能源消耗对于玻璃行业来说有着长远的效益,不仅仅是经济效益,而且也符合人们日益进步的环保理念,这是大势所趋,因而笔者将在下文简单介绍下浮法玻璃熔窑的节能技术,以及从下面几个方面探求浮法玻璃熔窑的节能途径,以期能够为玻璃行业的发展提供参考。
关键字:浮法玻璃熔窑节能技术途径Float glass furnace energy saving techniques and ways Abstract:Glass industry will produce huge energy consumption in the production process,reduce the energy consumption for the glass industry has the long-term benefits,not only economic benefits, but also accords with the growing progress of theconcept of environmental protection, this is represent the general trend, and thusthe pen will be energy-saving technology of float glass furnace in the followingbrief introduction next, and from five aspects to explore ways of saving energy of float glass furnace, in order to provide reference for the development of glass industry.Keyword:Float glass furnace Energy saving technology ways 随着近年来科技水平的不断进步,在玻璃行业中也有明显的表现,那就是浮法玻璃熔窑技术在不断地向前大步跨越,特别是国内的保温材料和耐火材料都在原基础上取得了巨大的进步,有进步虽然可喜,但是尚不足以与国外同领域的技术相比肩,或许通过以下数字大家能够更直观地看出差距所在,国外较先进的浮法玻璃熔窑技术最高产生55%的热效率,而我国最高产生40%。
玻纤池窑节能技术改造方案及措施分析

玻纤池窑节能技术改造方案及措施分析玻纤池窑节能技术改造分析方法玻璃纤维大多采用单元窑生产,这种窑熔化面积较小,约50㎡左右,一般采用金属换热器预热空气,高温烟气与玻璃液逆向流动,火焰不换向工作稳定,使用高热值燃料,多对烧嘴对称布置在熔窑两侧。
这种窑型的主要优点是:熔化的玻璃液质量好,容易调节温度曲线,可以实现自动化操作,结构简单,占地少,建造快。
它的主要缺点是热效率低,燃料消耗大。
现在,我国已把保护环境,节能减排作为一项长期国策,并且我国的能耗指标与国外也有较大的差距。
为此,各个玻纤厂采取各种方法以降低能耗,如采用纯氧燃烧、维持高的熔化率、窑体保温、电助熔技术、余热利用、稳定窑的热工制度等方法,取得了一定的成效。
下面结合我公司实际对玻纤池窑采用的一些节能方法进行分析,期望对节能工作有一些指导或参考意义。
1纯氧燃烧技术1.1纯氧燃烧原理燃烧是可燃物与空气中的氧气在一定的温度下发生激烈的化学反应而放出热量,从而达到加热物料的目的。
采用纯氧燃烧就是将空气中的氧气单独分离出来,所得的氧气纯度要求≥90%,这和空气助燃相比就大大降低了氮气(空气中氮气含量约为79%)的含量,从而大大降低了废气的排放量,也就是大大减少了废气带走的热量。
现在工业上制备氧气的方法一般有两种,一是低温冷冻制氧,就是根据构成大气的各种气体可在不同温度下液化和蒸馏的原理从空气中分离出氧气,这种方法制备的氧气为液态,使用时需气化。
二是变压吸附法,这是一种根据分子筛对空气的氮气与氧气选择性吸附的原理从空气中分离获得氧气的方法,生产的氧气纯度达93%以上,我公司目前选用此法。
1.2节能原理根据以上的纯氧燃烧原理,我们认为纯氧燃烧产生节能的原因主要为两个,一是由于采用纯氧,所以燃烧后废气的量大大减少,而废气的温度变化不大,从而废气带走的热量大大下降,从而达到节能的目的;二是由于采用纯氧燃烧,燃烧速度加快,氮气含量大大降低,从而使实际火焰温度很高,根据有些资料表明最高可达2690℃,而预热空气助燃的最高温度为1800℃,由于火焰温度的升高,辐射给物料的有效热量增加,而玻璃池窑内的物料得到的热量的40%左右是由火焰辐射传递的,从而降低了能耗。
- 1、下载文档前请自行甄别文档内容的完整性,平台不提供额外的编辑、内容补充、找答案等附加服务。
- 2、"仅部分预览"的文档,不可在线预览部分如存在完整性等问题,可反馈申请退款(可完整预览的文档不适用该条件!)。
- 3、如文档侵犯您的权益,请联系客服反馈,我们会尽快为您处理(人工客服工作时间:9:00-18:30)。
玻璃熔窑的冷修改造及相关措施 玻璃熔窑冷修改造的主要目的有:增加熔化能力、提高熔化质量、节能降耗、延长窑龄。针对每一项改造目的都有若干相应的改造措施,有些改造措施只能对熔窑的某一项经济技术指标进行改进,有些改造措施可以使熔窑的多项指标得到改进。
玻璃熔窑运行到窑龄的后期,窑体经常会出现局部构造薄弱受损的现象,再运行下去就有可能出现大面积坍塌;或者出现能耗升高、产品质量变差、运行效益降低的情况。在出现这样的情况之前,就应作好熔窑的冷修准备工作了。
一般情况下停窑就要放玻璃水,然后拆除旧窑建新窑,即对玻璃熔窑进行“冷修”;也有对熔窑进行“热修”的情况,热修通常是在窑体出现局部破损、其余部位都还良好的情况下进行,在热修期间要短时停产或减产,还要对熔窑进行保温,热修之后马上恢复生产。
玻璃熔窑是大型、量少、不定型的热工设备,很少在冷修中仍按原图纸不变重新建造,往往或多或少都要进行一些技术改造,有的还要进行大改造。改造的目的大体有:①增加熔化能力、②提高熔化质量、③节能降耗、④延长窑龄,这样四项内容中的若干项。
根据不同的改造目的,可有不同的改造措施,有些改造措施只能对熔窑的某一项经济技术指标进行改进,有些改造措施可以使熔窑的多项指标得到改进,比如:设计合理的窑形尺寸、使用高热值燃料和高性能喷枪、订购质量优良的耐火材料等,对玻璃熔窑增加熔化能力、提高熔化质量、节能降耗、廷长窑龄都很有利。
一.增加玻璃熔窑熔化能力的措施 根据国内外浮法玻璃熔窑的运行经验,对于浮法玻璃熔窑自身结构来说,增加熔化能力的主要措施可归纳为:窑形尺寸、燃料与喷枪、耐火材料、全窑宽投料、加大予熔区、增加火焰覆盖率、增加喷枪数量、提高熔化温度、电助熔等等这样几项措施。
1.窑形主要工艺尺寸合理:窑形主要工艺尺寸要与熔化能力相匹配,特别是熔化部和熔化区的池宽、池长尺寸和池长与池宽之比至关重要,偏小了达不到熔化能力、偏大了既影响熔化质量又对节能不利。
2.高热值燃料和高效能喷枪:要提高玻璃熔窑的熔化能力,需要使用高热值燃料并配备高效能喷枪,才能在熔化区内达到理想的高温熔化效果,熔化温度对玻璃熔窑的熔化能力起决定性作用,高热值燃料包括:重油、液化石油气(LPG)、天然气等。玻璃熔窑的喷枪安装形式大体有两种:①小炉内点燃的喷枪,包括顶插式、侧插式、底插式;②小炉外点燃的喷枪,为炉下式。目前国内多数玻璃熔窑使用的是炉下式喷枪,维修更换都比较方便。相比较而言,小炉内点燃的喷枪比小炉外点燃的喷枪效率要高一些,但投资较大,维修更换不太方便。
3.全窑宽投料技术:以往的相当于熔化部池宽80%左右的缩窄投料口,由于投料机的布料斗(俗称簸萁)的宽度要比投料池还要窄一些,因而配合料在窑内的分布宽度也就是窑宽的70%左右,这样窄的料带进入窑内,显然窑内火焰对配合料的加热面积没有得到很好的利用。而采用全窑宽投料池,配合料在窑内的分布宽度可以达到熔化部池宽的90%左右,窑内火焰对配合料的加热面积就得到了比较充分的利用,这对熔窑的熔化能力和熔化玻璃液质量大有挺高。采用全窑宽投料池要比采用缩窄的投料池可增加熔化能力8~10%左右。
4.加大予熔区长度:通常所说的予熔区长度为l#小炉中心线至熔化部前端的尺寸,实际的予熔区还包括L型吊墙鼻区之下的部位。进入窑内的玻璃配合料经过较长的予熔区受热升温,对提高熔化能力是很有利的。
5.增加火焰覆盖率:火焰覆盖率定义为全窑小炉喷火口总宽度尺寸占熔化区长度尺寸的百分比。火焰覆盖率越大,窑内火焰分布越均匀,对熔化作用越有利,能够提高熔窑的熔化能力。
6.增加喷枪数量:国内许多座熔窑的运行结果表明:小炉内采用2支枪布置时,窑内火焰分布不太均匀:而采用3支枪以上的多枪布置时,窑内火焰分布的均匀性就提高了很多。窑内火焰分布均匀,也相当于增加了火焰覆盖率,对熔化作用有利,能提高熔窑的熔化能力。
7.提高熔化温度:高温熔化对提高熔化能力是很有效的,采用高温熔化是指在熔化区内的热点之前温度制度要取较高的温度曲线,热点温度要达到1590℃或更高一些。这要在熔窑结构条件具备(包括窑型尺寸合理、采用高热值燃料和高效能喷枪、耐火材料性能优良)的情况下进行。
有资料介绍:前苏联的垂直引上窑熔化部胸墙温度,平均温度每提高10℃,熔窑的单位产量平均增加4%。还有一种说法:熔化温度由1560℃提高至1600℃,可使玻璃熔窑产量增加12%~15%。根据这些资料可以大致地认为:熔化温度每升高10℃,可以增加熔化能力3%~4%。 8.电助熔:提供电助熔设备的国外商家(英国F.I.C公司)曾明确表示:电助熔可提高熔化能力10%左右。对于新建浮法线的熔窑,只要没有场地狭小等限制的时候,是没有必要一开始就上电助熔设备的。往往是熔窑投产之后,发现熔化能力不足时考虑上电助熔。
二.提高玻璃液熔化质量的措施 对于浮法玻璃熔窑自身结构来说,提高玻璃液熔化质量的主要措施可归纳为:窑形尺寸、燃料与喷枪、耐火材料、大澄清区、池底铺面、搅拌设施、拦挡设施、空间分隔、窑压稳定、温度恒定等,这样一些措施。
1.窑形主要工艺尺寸合理:与熔化能力相匹配的窑形主要工艺尺寸,特别是熔化部和熔化区的池宽、池长尺寸和池长与池宽之比对熔化质量也至关重要,偏大或偏小都会对熔化的玻璃液质量产生不良影响。
2.高热值燃料和高效能喷枪:要熔化高质量浮法玻璃,必须使用高热值燃料并配备高效能喷枪,才能在熔化区内达到理想的高温熔化效果,熔化温度对玻璃熔窑的熔化能力和熔化的坡璃液质量都起决定性作用。
3.熔窑各部位耐火材料配置得当并保征质量:接触玻璃液部位和可能剥落后落入玻璃液内的耐火材料对玻璃液质量影响很大,重点部位是热点之后的小炉喷火口和冷却部的池底、池壁以及冷却部的出口平碹要用耐冲刷性能优良的砖材,熔窑各部位耐火材料都要配置得当并保让质量。
4.比较长的澄清区:在熔化区内刚生成的玻璃液内包含很多气泡和灰泡(小气泡)要在澄清区内排出:同时刚生成的玻璃液的化学成分和温度、密度、黏度都不相同,很不均匀,必须进行均化。有比铰长的澄清区,才能使更多的气泡排出,玻璃液的均化作用也更明显。
窑池底部的池底铺面结构:玻璃液在窑池底部的流动(常与表面流动方向相反)会对池底产生冲刷,被冲刷掉的池底耐火材抖粉末都要进入玻璃液内,而且不易熔化掉,是产生玻璃液熔化缺陷的重要原因之一,池底采用耐冲刷性能好的耐火材料就可比较好地解决这一问题。
6.玻璃液搅拌装置:搅拌作用能明显地提高玻璃液的均匀性,减少由于玻璃液的化学成分、温度、密度、黏度等不均匀造成的玻璃缺陷。常见的搅拌装置有水平搅拌器和垂直搅拌器,相比较而言,水平搅拌器结构简单,比较耐用,而垂直搅拌器的搅拌作用更好一些。 7.玻璃液表面漂浮物拦挡装置:在玻璃熔窑内,玻璃液表面有时会出现一些漂浮物,这些漂浮物主要来自两个原因:一是未熔化的玻璃配合料渣滓;二是熔窑运行中窑体结构上剥落或掉落的耐火材料颗粒或碎块。在浮法玻璃熔窑的卡脖处设置大水包,作用之一就是用来拦截玻璃液表面漂浮物的。
8.熔化部与冷却部之间的上部空间分隔装置:由于受换向等作用的影响,熔化部内的温度、窑压、气氛等对冷却部有一定的周期影响,这对于生产优质浮法玻璃是很不力的。卡脖吊墙的作用就是把熔化部和冷却部的上部空间最大限度地分隔开,卡脖吊墙的分隔作用越强越好。
9.冷却部的窑压调节装置:为了稳定浮法玻璃的生产,要求冷却部内的窑压要略高于熔化部的窑压,并且可调。冷却部的微调风系统主要就是用来调节冷却部的窑压的。
10.冷却部的温度调节装置:能够保持冷却部的温度恒定,对生产优质浮法玻璃非常重要,尤其是冷却部的末端出口处的玻璃液温度,很小的波动就会对玻璃的内在质量产生很明显的影响,许多外国玻璃熔窑在冷却部都设有温度调节装置,多是采用风或水的冷却装置,也有采用升温加热措施的。
11.高温熔化:高温熔化对提高玻璃液的熔化质量是很有效的,采用高温熔化是指在熔化区内的热点之前温度制度要取较高的温度曲线,热点温度要达到1590℃或再高一些。
12.防止偏料粘边:偏料粘边现象是玻璃熔窑运行中比较容易出现的情况,沾边的玻璃原料残渣到达热点之后就很难熔化了,要严重影响玻璃质量,一定要采取各种可行措施防止偏斜粘边,防止各种原因造成未熔化好的原料残渣在热点之后出现。
另外还有鼓泡、窑坎、电助熔等一些措施,对于某些小吨位熔窑或特种玻璃熔窑提高熔化质量有一定的作用。浮法玻璃熔窑吨位大、惯性强,采用鼓泡、窑坎、电助熔等措施对提高熔化质量体现不出来多大作用,而且还可能带来某些隐患。
三.节能降耗措施 对于浮法玻璃熔窑自身结构来说,节约能耗的主要措施可归纳为:窑形尺寸、燃料与燃烧、火焰高度、全窑宽投料、窑体保温、窑体密封、格子体配置、浅池、窄卡脖、作业制度等这样一些措施。 1.窑形尺寸:窑形主要工艺尺寸要设计合理,与熔化能力相匹配的窑形主要工艺尺寸,特别是熔化部和熔化区的长、宽尺寸和长、宽比例是有合理的最佳值的。达到了这个最佳值时,不但熔窑的熔化能力和熔化质量都能得到保证,而且能耗最低。国内许多玻璃熔窑能耗高的主要原因是熔化区的长度尺寸偏大,窑内火焰分散,热流密度低,达不到应有的熔化温度。
2.燃料与燃烧:使用高热值燃料并配备高效能喷枪,才能在熔化区内达到理想的高温熔化效果。选择合适的燃料、空气比例,使火焰长度为窑宽的3/4;对喷枪进行精确调整,达到合适的燃料供给角度和流速;实现燃烧过程自动调节;将换火时间调到最小限度;连续控制烟气成分,是玻璃熔窑节能的基本条件。
3.火焰高度:应尽量减少窑内火焰与玻璃液面之间的高度,从小炉喷火口喷入窑内的火焰,应当是既不能对玻璃液面产生扰动作用、又要尽量靠近玻璃液面。国外许多熔窑采用“顶插、侧插、底插”式喷枪,喷火口挂钩砖之上即为小炉炕面砖,小炉炕面顶比池壁顶高出大约500mm(470~580mm之间),助燃空气在小炉内倾斜向下俯冲与燃料相遇后燃烧生成火焰喷入窑内,火焰紧贴玻璃液面又不扰动液面,热效率比较高。
目前国内自行设计的玻璃熔窑基本都采用炉下式喷枪,要在喷火口挂钩砖和小炉炕面舌头砖之间设喷枪用的“喷嘴砖”,喷嘴砖高度一般为200mm,这样小炉炕面比池壁顶就要高出大约700mm(670~780mm之间)。火焰与玻璃液面之间的高度也就增加了200mm,显然这就使火焰远离了玻璃液面,降低了火焰的热效率,大约要降低3~5%,小炉炕面顶比池壁顶高出的越多火焰热效率越低。
4.全窑宽投料技术:采用全窑宽投料技术产生的节能效果,可以从两个方面来说:其一是在熔制工艺上,全窑宽投料池投入窑内的配合料带更宽、更薄,加大了配合料的受热表面积和透热性,使熔化区内的热量更多更快地被配合料吸收,从而减少了热量向窑外的损失。其二在熔窑结构上,采用全窑宽投料池可以把熔化部的池宽和池长做得略小一些,这就减少了整个窑体的表面散热损失,从而产生节能效果。