机械设计与制造毕业设计论文中英文翻译外文翻译
机械类英语论文及翻译翻译
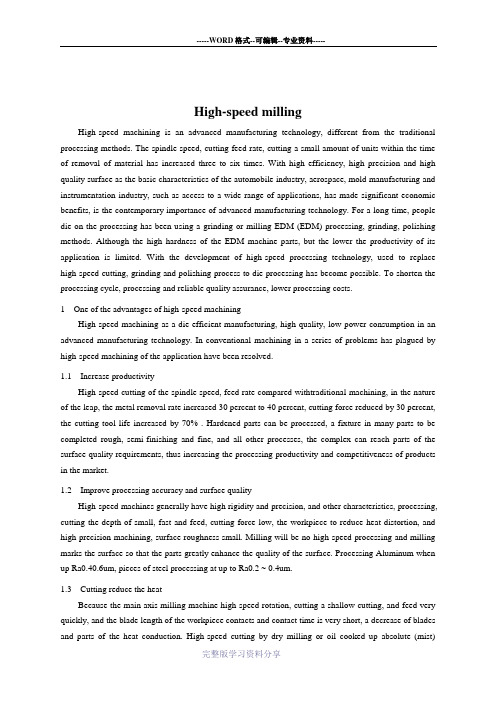
High-speed millingHigh-speed machining is an advanced manufacturing technology, different from the traditional processing methods. The spindle speed, cutting feed rate, cutting a small amount of units within the time of removal of material has increased three to six times. With high efficiency, high precision and high quality surface as the basic characteristics of the automobile industry, aerospace, mold manufacturing and instrumentation industry, such as access to a wide range of applications, has made significant economic benefits, is the contemporary importance of advanced manufacturing technology. For a long time, people die on the processing has been using a grinding or milling EDM (EDM) processing, grinding, polishing methods. Although the high hardness of the EDM machine parts, but the lower the productivity of its application is limited. With the development of high-speed processing technology, used to replace high-speed cutting, grinding and polishing process to die processing has become possible. To shorten the processing cycle, processing and reliable quality assurance, lower processing costs.1 One of the advantages of high-speed machiningHigh-speed machining as a die-efficient manufacturing, high-quality, low power consumption in an advanced manufacturing technology. In conventional machining in a series of problems has plagued by high-speed machining of the application have been resolved.1.1 Increase productivityHigh-speed cutting of the spindle speed, feed rate compared withtraditional machining, in the nature of the leap, the metal removal rate increased 30 percent to 40 percent, cutting force reduced by 30 percent, the cutting tool life increased by 70% . Hardened parts can be processed, a fixture in many parts to be completed rough, semi-finishing and fine, and all other processes, the complex can reach parts of the surface quality requirements, thus increasing the processing productivity and competitiveness of products in the market.1.2 Improve processing accuracy and surface qualityHigh-speed machines generally have high rigidity and precision, and other characteristics, processing, cutting the depth of small, fast and feed, cutting force low, the workpiece to reduce heat distortion, and high precision machining, surface roughness small. Milling will be no high-speed processing and milling marks the surface so that the parts greatly enhance the quality of the surface. Processing Aluminum when up Ra0.40.6um, pieces of steel processing at up to Ra0.2 ~ 0.4um.1.3 Cutting reduce the heatBecause the main axis milling machine high-speed rotation, cutting a shallow cutting, and feed very quickly, and the blade length of the workpiece contacts and contact time is very short, a decrease of blades and parts of the heat conduction. High-speed cutting by dry milling or oil cooked up absolute (mist)lubrication system, to avoid the traditional processing tool in contact with the workpiece and a lot of shortcomings to ensure that the tool is not high temperature under the conditions of work, extended tool life.1.4 This is conducive to processing thin-walled partsHigh-speed cutting of small cutting force, a higher degree of stability, Machinable with high-quality employees compared to the company may be very good, but other than the company's employees may Suanbu Le outstanding work performance. For our China practice, we use the models to determine the method of staff training needs are simple and effective. This study models can be an external object, it can also be a combination of internal and external. We must first clear strategy for the development of enterprises. Through the internal and external business environment and organizational resources, such as analysis, the future development of a clear business goals and operational priorities. According to the business development strategy can be compared to find the business models, through a comparative analysis of the finalization of business models. In determining business models, a, is the understanding of its development strategy, or its market share and market growth rate, or the staff of the situation, and so on, according to the companies to determine the actual situation. As enterprises in different period of development, its focus is different, which means that enterprises need to invest the manpower and financial resources the focus is different. So in a certain period of time, enterprises should accurately selected their business models compared with the departments and posts, so more practical significance, because the business models are not always good, but to compare some aspects did not have much practical significance, Furthermore This can more fully concentrate on the business use of limited resources. Identify business models, and then take the enterprise of the corresponding departments and staff with the business models for comparison, the two can be found in the performance gap, a comparative analysis to find reasons, in accordance with this business reality, the final identification of training needs. The cost of training is needed, if not through an effective way to determine whether companies need to train and the training of the way, but blind to training, such training is difficult to achieve the desired results. A comparison only difference between this model is simple and practical training.1.5 Can be part of some alternative technology, such as EDM, grinding high intensity and high hardness processingHigh-speed cutting a major feature of high-speed cutting machine has the hardness of HRC60 parts. With the use of coated carbide cutter mold processing, directly to the installation of a hardened tool steel processing forming, effectively avoid the installation of several parts of the fixture error and improve the parts of the geometric location accuracy. In the mold of traditional processing, heat treatment hardening of the workpiece required EDM, high-speed machining replace the traditional method of cutting the processing, manufacturing process possible to omit die in EDM, simplifying the processing technology and investment costs .High-speed milling in the precincts of CNC machine tools, or for processing centre, also in the installation of high-speed spindle on the general machine tools. The latter not only has the processingcapacity of general machine tools, but also for high-speed milling, a decrease of investment in equipment, machine tools increased flexibility. Cutting high-speed processing can improve the efficiency, quality improvement, streamline processes, investment and machine tool investment and maintenance costs rise, but comprehensive, can significantly increase economic efficiency.2 High-speed millingHigh-speed milling the main technical high-speed cutting technology is cutting the development direction of one of it with CNC technology, microelectronic technology, new materials and new technology, such as technology development to a higher level. High-speed machine tools and high-speed tool to achieve high-speed cutting is the prerequisite and basic conditions, in high-speed machining in the performance of high-speed machine tool material of choice and there are strict requirements.2.1 High-speed milling machine in order to achieve high-speed machiningGeneral use of highly flexible high-speed CNC machine tools, machining centers, and some use a dedicated high-speed milling, drilling. At the same time a high-speed machine tool spindle system and high-speed feeding system, high stiffness of the main characteristics of high-precision targeting and high-precision interpolation functions, especially high-precision arc interpolation function. High-speed machining systems of the machine a higher demand, mainly in the following areas:General use of highly flexible high-speed CNC machine tools, machining centers, and some use a dedicated high-speed milling, drilling. At the same time a high-speed machine tool spindle system and high-speed feeding system, high stiffness of the main characteristics of high-precision targeting and high-precision interpolation functions, especially high-precision arc interpolation function. High-speed machining systems of the machine a higher demand, mainly in the following areas:High-speed milling machine must have a high-speed spindle, the spindle speed is generally 10000 ~ 100000 m / min, power greater than 15 kW. But also with rapid speed or in designated spots fast-stopping performance. The main axial space not more than 0 .0 0 0 2 m m. Often using high-speed spindle-hydrostatic bearings, air pressure-bearing, mixed ceramic bearings, magnetic bearing structure of the form. Spindle cooling general use within the water or air cooled.High-speed processing machine-driven system should be able to provide 40 ~ 60 m / min of the feed rate, with good acceleration characteristics, can provide 0.4 m/s2 to 10 m/s2 acceleration and deceleration. In order to obtain good processing quality, high-speed cutting machines must have a high enough stiffness. Machine bed material used gray iron, can also add a high-damping base of concrete, to prevent cutting tool chatter affect the quality of processing. A high-speed data transfer rate, can automatically increase slowdown. Processing technology to improve the processing and cutting tool life. At present high-speed machine tool manufacturers, usually in the general machine tools on low speed, the feed of the rough and then proceed to heat treatment, the last in the high-speed machine on the half-finished and finished, in improving the accuracy and efficiency at the same time, as far as possible to reduce processing Cost.2.2 High-speed machining toolHigh-speed machining tool is the most active one of the important factors, it has a direct impact on the efficiency of processing, manufacturing costs and product processing and accuracy. Tool in high-speed processing to bear high temperature, high pressure, friction, shock and vibration, such as loading, its hardness and wear-resistance, strength and toughness, heat resistance, technology and economic performance of the basic high-speed processing performance is the key One of the factors. High-speed cutting tool technology development speed, the more applications such as diamond (PCD), cubic boron nitride (CBN), ceramic knives, carbide coating, (C) titanium nitride Carbide TIC (N) And so on. CBN has high hardness, abrasion resistance and the extremely good thermal conductivity, and iron group elements between the great inertia, in 1300 ℃ would not have happened significant role in the chemical, also has a good stability. The experiments show that with CBN cutting toolHRC35 ~ 67 hardness of hardened steel can achieve very high speed. Ceramics have good wear resistance and thermal chemical stability, its hardness, toughness below the CBN, can be used for processing hardness of HRC <5 0 parts. Carbide Tool good wear resistance, but the hardness than the low-CBN and ceramics. Coating technology used knives, cutting tools can improve hardness and cutting the rate, for cutting HRC40 ~ 50 in hardness between the workpiece. Can be used to heat-resistant alloys, titanium alloys, hightemperature alloy, cast iron, Chungang, aluminum and composite materials of high-speed cutting Cut, the most widely used. Precision machining non-ferrous metals or non-metallic materials, or the choice of polycrystalline diamond Gang-coated tool.2.3 High-speed processing technologyHigh-speed cutting technology for high-speed machining is the key. Cutting Methods misconduct, will increase wear tool to less than high-speed processing purposes. Only high-speed machine tool and not a good guide technology, high-speed machining equipment can not fully play its role. In high-speed machining, should be chosen with milling, when the milling cutter involvement with the workpiece chip thickness as the greatest, and then gradually decreased. High-speed machining suitable for shallow depth of cut, cutting depth of not more than 0.2 mm, to avoid the location of deviation tool to ensure that the geometric precision machining parts. Ensure that the workpiece on the cutting constant load, to get good processing quality. Cutting a single high-speed milling path-cutting mode, try not to interrupt the process and cutting tool path, reducing the involvement tool to cut the number to be relatively stable cutting process. Tool to reduce the rapid change to, in other words when the NC machine tools must cease immediately, or Jiangsu, and then implement the next step. As the machine tool acceleration restrictions, easy to cause a waste of time, and exigency stop or radical move would damage the surface accuracy. In the mold of high-speed finishing, in each Cut, cut to the workpiece, the feed should try to change the direction of a curve or arc adapter, avoid a straight line adapter to maintain the smooth process of cutting.3 Die in high-speed milling processing ofMilling as a highly efficient high-speed cutting of the new method,inMould Manufacturing has been widely used. Forging links in the regular production model, with EDM cavity to be 12 ~ 15 h, electrodes produced 2 h. Milling after the switch to high-speed, high-speed milling cutter on the hardness of HRC 6 0 hardened tool steel processing. The forging die processing only 3h20min, improve work efficiency four to five times the processing surface roughness of Ra0.5 ~ 0.6m, fully in line with quality requirements.High-speed cutting technology is cutting technology one of the major developments, mainly used in automobile industry and die industry, particularly in the processing complex surface, the workpiece itself or knives rigid requirements of the higher processing areas, is a range of advanced processing technology The integration, high efficiency and high quality for the people respected. It not only involves high-speed processing technology, but also including high-speed processing machine tools, numerical control system, high-speed cutting tools and CAD / CAM technology. Die-processing technology has been developed in the mold of the manufacturing sector in general, and in my application and the application of the standards have yet to be improved, because of its traditional processing with unparalleled advantages, the future will continue to be an inevitable development of processing technology Direction.4 Numerical control technology and equipping development trend and countermeasureEquip the engineering level, level of determining the whole national economy of the modernized degree and modernized degree of industry, numerical control technology is it develop new developing new high-tech industry and most advanced industry to equip (such as information technology and his industry, biotechnology and his industry, aviation, spaceflight, etc. national defense industry) last technology and getting more basic most equipment. Marx has ever said "the differences of different economic times, do not lie in what is produced, and lie in how to produce, produce with some means of labor ". Manufacturing technology and equipping the most basic means of production that are that the mankind produced the activity, and numerical control technology is nowadays advanced manufacturing technology and equips the most central technology. Nowadays the manufacturing industry all around the world adopts numerical control technology extensively, in order to improve manufacturing capacity and level, improve the adaptive capacity and competitive power to the changeable market of the trends. In addition every industrially developed country in the world also classifies the technology and numerical control equipment of numerical control as the strategic materials of the country, not merely take the great measure to develop one's own numerical control technology and industry, and implement blockading and restrictive policy to our country in view of " high-grade, precision and advanced key technology of numerical control " and equipping. In a word, develop the advanced manufacturing technology taking numerical control technology as the core and already become every world developed country and accelerate economic development in a more cost-effective manner, important way to improve the overall national strength and national position.Numerical control technology is the technology controlled to mechanical movement and working course with digital information, integrated products of electromechanics that the numerical control equipment is the new technology represented by numerical control technology forms to the manufacture industry of the tradition and infiltration of the new developing manufacturing industry, namely the so-called digitization is equipped, its technological range covers a lot of fields: (1)Mechanical manufacturing technology;(2)Information processing, processing, transmission technology; (3)Automatic control technology;(4)Servo drive technology; (5)Technology of the sensor; (6)Software engineering ,etc..Development trend of a numerical control technologyThe application of numerical control technology has not only brought the revolutionary change to manufacturing industry of the tradition, make the manufacturing industry become the industrialized symbol , and with the constant development of numerical control technology and enlargement of the application, the development of some important trades (IT , automobile , light industry , medical treatment ,etc. ) to the national economy and the people's livelihood of his plays a more and more important role, because the digitization that these trades needed to equip has already been the main trend of modern development. Numerical control technology in the world at present and equipping the development trend to see, there is the following several respect [1- ] in its main research focus.5 A high-speed, high finish machining technology and new trend equippedThe efficiency, quality are subjavanufacturing technology. High-speed, high finish machining technology can raise the efficiency greatly , improve the quality and grade of the products, shorten production cycle and improve the market competitive power. Japan carries the technological research association first to classify it as one of the 5 great modern manufacturing technologies for this, learn (CIRP) to confirm it as the centre in the 21st century and study one of the directions in international production engineering.In the field of car industry, produce one second when beat such as production of 300,000 / vehicle per year, and many variety process it is car that equip key problem that must be solved one of; In the fields of aviation and aerospace industry, spare parts of its processing are mostly the thin wall and thin muscle, rigidity is very bad, the material is aluminium or aluminium alloy, only in a situation that cut the speed and cut strength very small high, could process these muscles, walls. Adopt large-scale whole aluminium alloy method that blank " pay empty " make the wing recently, such large-scale parts as the fuselage ,etc. come to substitute a lot of parts to assemble through numerous rivet , screw and other connection way, make the intensity , rigidity and dependability of the component improved. All these, to processing and equipping the demand which has proposed high-speed, high precise and high flexibility.According to EMO2001 exhibition situation, high-speed machining center is it give speed can reach 80m/min is even high , air transport competent speed can up to 100m/min to be about to enter. A lot of automobile factories in the world at present, including Shanghai General Motors Corporation of our country, have already adopted and substituted and made the lathe up with the production line part that the high-speed machining center makes up. HyperMach lathe of U.S.A. CINCINNATI Company enters to nearly biggest 60m/min of speed, it is 100m/min to be fast, the acceleration reaches 2g, the rotational speed of the main shaft has already reached 60 000r/min. Processing a thin wall of plane parts, spend 30min only, and same part general at a high speed milling machine process and take 3h, the ordinary milling machine is being processed to need 8h; The speed and acceleration of main shaft of dual main shaft lathes of Germany DMG Company are up to 120000r/mm and 1g.In machining accuracy, the past 10 years, ordinary progression accuse of machining accuracy of lathe bring 5μm up to from 10μm already, accurate grades of machining center from 3~5μm, rise to 1~1.5μm, and ultraprecision machining accuracy is it e nter nanometer grade to begin already (0.01μm).In dependability, MTBF value of the foreign numerical control device has already reached above 6 000h,MTBF value of the servo system reaches above 30000h, demonstrate very high dependability .In order to realize high-speed, high finish machining, if the part of function related to it is electric main shaft, straight line electrical machinery get fast development, the application is expanded further .5.2 Link and process and compound to process the fast development of the lathe in 5 axesAdopt 5 axles to link the processing of the three-dimensional curved surface part, can cut with the best geometry form of the cutter , not only highly polished, but also efficiency improves by a large margin . It is generally acknowledged, the efficiency of an 5 axle gear beds can equal 2 3 axle gear beds, is it wait for to use the cubic nitrogen boron the milling cutter of ultra hard material is milled and pared at a high speed while quenching the hard steel part, 5 axles link and process 3 constant axles to link and process and give play to higher benefit. Because such reasons as complicated that 5 axles link the numerical control system , host computer structure that but go over, it is several times higher that its price links the numerical control lathe than 3 axles , in addition the technological degree of difficulty of programming is relatively great, have restricted the development of 5 axle gear beds.At present because of electric appearance of main shaft, is it realize 5 axle complex main shaft hair structure processed to link greatly simplify to make, it makes degree of difficulty and reducing by a large margin of the cost, the price disparity of the numerical control system shrinks. So promoted 5 axle gear beds of head of complex main shaft and compound to process the development of the lathe (process the lathe including 5).At EMO2001 exhibition, new Japanese 5 of worker machine process lathe adopt complex main shaft hair, can realize the processing of 4 vertical planes and processing of the wanton angle, make 5 times process and 5 axles are processed and can be realized on the same lathe, can also realize the inclined plane and pour the processing of the hole of awls. Germany DMG Company exhibits the DMUVoution series machining center, but put and insert and put processing and 5 axles 5 times to link and process in once, can be controlled by CNC system or CAD/CAM is controlled directly or indirectly.5.3 Become the main trend of systematic development of contemporary numerical control intelligently, openly, networkedly.The numerical control equipment in the 21st century will be sure the intelligent system, the intelligent content includes all respects in the numerical control system: It is intelligent in order to pursue the efficiency of processing and process quality, control such as the self-adaptation of the processing course, the craft parameter is produced automatically; Join the convenient one in order to improve the performance of urging and use intelligently, if feedforward control , adaptive operation , electrical machinery of parameter , discern load select models , since exactly makes etc. automatically; The ones that simplified programming , simplified operating aspect are intelligent, for instance intelligent automatic programming , intelligent man-machine interface ,etc.; There are content of intelligence diagnose , intelligent monitoring , diagnosis convenient to be systematic and maintaining ,etc..Produce the existing problem for the industrialization of solving the traditional numerical control system sealing and numerical control application software. A lot of countries carry on research to the open numerical control system at present, such as NGC of U.S.A. (The Next Generation Work-Station/MachineControl), OSACA of European Community (Open System Architecture for Control within Automation Systems), OSEC (Open System Environment for Controller) of Japan, ONC (Open Numerical Control System) of China, etc.. The numerical control system melts to become the future way of the numerical control system open. The so-called open numerical control system is the development of the numerical control system can be on unified operation platform, face the lathe producer and end user, through changing, increasing or cutting out the structure target(numerical control function), form the serration, and can use users specially conveniently and the technical know-how is integrated in the control system, realize the open numerical control system of different variety , different grade fast, form leading brand products with distinct distinction. System structure norm of the open numerical control system at present, communication norm , disposing norm , operation platform , numerical control systematic function storehouse and numerical control systematic function software development ,etc. are the core of present research.The networked numerical control equipment is a new light spot of the fair of the internationally famous lathe in the past two years. Meeting production line , manufacture system , demand for the information integration of manufacturing company networkedly greatly of numerical control equipment, realize new manufacture mode such as quick make , fictitious enterprise , basic Entrance that the whole world make too. Some domestic and international famous numerical control lathes and systematic manufacturing companies of numerical control have all introduced relevant new concepts and protons of a machine in the past two years, if in EMO2001 exhibition, " Cyber Production Center " that the company exhibits of mountain rugged campstool gram in Japan (Mazak) (intellectual central production control unit, abbreviated as CPC); The lathe company of Japanese big Wei (Okuma ) exhibits " IT plaza " (the information technology square , is abbreviated as IT square ); Open Manufacturing Environment that the company exhibits of German Siemens (Siemens ) (open the manufacturing environment, abbreviated as OME),etc., have reflected numerical control machine tooling to the development trend of networked direction.5.4 Pay attention to the new technical standard, normal setting-up5.4.1 Design the norm of developing about the numerical control systemAs noted previously, there are better common ability, flexibility, adaptability, expanding in the open numerical control system, such countries as U.S.A. ,European Community and Japan ,etc. implement the strategic development plan one after another , carry on the research and formulation of the systematic norm (OMAC , OSACA , OSEC ) of numerical control of the open system structure, 3 biggest economies in the world have carried on the formulation that nearly the same science planned and standardized in a short time, have indicated a new arrival of period of change of numerical control technology. Our country started the research and formulation of standardizing the frame of ONC numerical control system of China too in 2000.5.4.2 About the numerical control standardThe numerical control standard is a kind of trend of information-based development of manufacturing industry. Information exchange among 50 years after numerical control technology was born was all。
机械设计制造及其自动化毕业设计外文翻译

机械设计制造及其自动化毕业设计外文翻译英文原文名Automatic production line PLC control of automatic feeding station中文译名基于PLC的自动化生产线自动上料站的控制中文译文:自动化生产线自动上料站的PLC控制自动生产线是由工件传送系统和控制系统,将一组自动机床和辅助设备按照工艺顺序联结起来,自动完成产品全部或部分制造过程的生产系统,简称自动线。
二十世纪20年代,随着汽车、滚动轴承、小电机和缝纫机和其他工业发展,机械制造业开始出现在自动生产线,第一个是组合机床自动线。
在20世纪20年代,第一次出现在汽车工业流水生产线和半自动生产线,然后发展成自动生产线。
第二次世界大战后,在机械制造工业发达国家,自动生产线的数量急剧增加。
采用自动生产线生产的产品应该足够大,产品设计和技术应该是先进的、稳定的和可靠的,基本上保持了很长一段时间维持不变。
自动线用于大,大规模生产可以提高劳动生产率,稳定和提高产品质量,改善劳动条件,降低生产区域,降低生产成本,缩短生产周期,保证生产平衡、显著的经济效益。
自动生产线的一个干预指定的程序或命令自动操作或控制的过程,我们的目标是稳定、准确、快速。
自动化技术广泛用于工业、农业、军事、科学研究、交通运输、商业、医疗、服务和家庭,等自动化生产线不仅可以使人们从繁重的体力劳动、部分脑力劳动以及恶劣、危险的工作环境,能扩大人的器官功能,极大地提高劳动生产率,提高人们认识世界的能力,可以改变世界。
下面我说下它的应用范围:机械制造业中有铸造、锻造、冲压、热处理、焊接、切削加工和机械装配等自动线,也有包括不同性质的工序,如毛坯制造、加工、装配、检验和包装等的综合自动线。
加工自动线发展最快,应用最广泛的机械制造。
主要包括:用于处理盒、外壳、各种各样的部件,如组合机床自动线;用于加工轴、盘部分,由通用、专业化、或自动机器自动专线;转子加工自动线;转子自动线加工过程简单、小零件等。
机械类毕业设计外文翻译
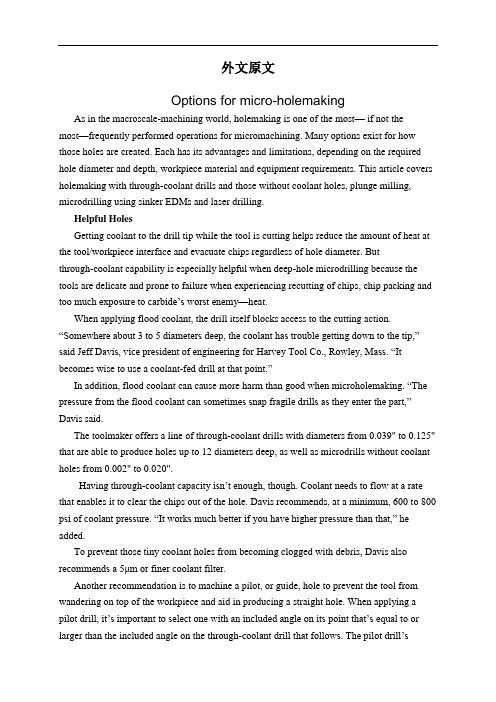
外文原文Options for micro-holemakingAs in the macroscale-machining world, holemaking is one of the most— if not the most—frequently performed operations for micromachining. Many options exist for how those holes are created. Each has its advantages and limitations, depending on the required hole diameter and depth, workpiece material and equipment requirements. This article covers holemaking with through-coolant drills and those without coolant holes, plunge milling, microdrilling using sinker EDMs and laser drilling.Helpful HolesGetting coolant to the drill tip while the tool is cutting helps reduce the amount of heat at the tool/workpiece interface and evacuate chips regardless of hole diameter. Butthrough-coolant capability is especially helpful when deep-hole microdrilling because the tools are delicate and prone to failure when experiencing recutting of chips, chip packing and too much exposure to carbide’s worst enemy—heat.When applying flood coolant, the drill itself blocks access to the cutting action. “Somewhere about 3 to 5 diameters deep, the coolant has trouble getting down to the tip,” said Jeff Davis, vice president of engineering for Harvey Tool Co., Rowley, Mass. “It becomes wise to use a coolant-fed drill at that point.”In addition, flood coolant can cause more harm than good when microholemaking. “The pressure from the flood coolant can sometimes snap fragile drills as they enter the part,” Davis said.The toolmaker offers a line of through-coolant drills with diameters from 0.039" to 0.125" that are able to produce holes up to 12 diameters deep, as well as microdrills without coolant holes from 0.002" to 0.020".Having through-coolant capacity isn’t enough, though. Coolant needs to flow at a rate that enables it to clear the chips out of the hole. Davis recommends, at a minimum, 600 to 800 psi of coolant pressure. “It works much better if you have higher pressure than that,” he added.To prevent those tiny coolant holes from becoming clogged with debris, Davis also recommends a 5μm or finer coolant filter.Another recommendation is to machine a pilot, or guide, hole to prevent the tool from wandering on top of the workpiece and aid in producing a straight hole. When applying a pilot drill, it’s important to select one with an included angle on its point that’s equal t o or larger than the included angle on the through-coolant drill that follows. The pilot drill’sdiameter should also be slightly larger. For example, if the pilot drill has a 120° included angle and a smaller diameter than a through-coolant drill with a 140° included angle, “then you’re catching the coolant-fed drill’s corners and knocking those corners off,” Davis said, which damages the drill.Although not mandatory, pecking is a good practice when microdrilling deep holes. Davis suggests a pecking cycle that is 30 to 50 percent of the diameter per peck depth, depending on the workpiece material. This clears the chips, preventing them from packing in the flute valleys.Lubricious ChillTo further aid chip evacuation, Davis recommends applying an oil-based metalworking fluid instead of a waterbased coolant because oil provides greater lubricity. But if a shop prefers using coolant, the fluid should include EP (extreme pressure) additives to increase lubricity and minimize foaming. “If you’ve got a lot of foam,” Davis noted, “the chips aren’t being pulled out the way they are supposed to be.”He added that another way to enhance a tool’s slipperiness while extending its life is with a coating, such as titanium aluminum nitride. TiAlN has a high hardness and is an effective coating for reducing heat’s impact when drilling difficult-to-machine materials, like stainless steel.David Burton, general manager of Performance Micro Tool, Janesville, Wis., disagrees with the idea of coating microtools on the sma ller end of the spectrum. “Coatings on tools below 0.020" typically have a negative effect on every machining aspect, from the quality of the initial cut to tool life,” he said. That’s because coatings are not thin enough and negatively alter the rake and relief angles when applied to tiny tools.However, work continues on the development of thinner coatings, and Burton indicated that Performance Micro Tool, which produces microendmills and microrouters and resells microdrills, is working on a project with others to create a submicron-thickness coating. “We’re probably 6 months to 1 year from testing it in the market,” Burton said.The microdrills Performance offers are basically circuit-board drills, which are also effective for cutting metal. All the tools are without through-coolant capability. “I had a customer drill a 0.004"-dia. hole in stainless steel, and he was amazed he could do it with a circuit-board drill,” Burton noted, adding that pecking and running at a high spindle speed increase the drill’s effectiveness.The requirements for how fast microtools should rotate depend on the type of CNC machines a shop uses and the tool diameter, with higher speeds needed as the diameter decreases. (Note: The equation for cutting speed is sfm = tool diameter × 0.26 × spindlecan go deeper because it’s de signed to place the load on its tip when drilling. This transfers the pressure into the shank, which absorbs it.Performance offers endmills as small as 5 microns (0.0002") but isn’t keen on increasing that line’s sales. “When people try to buy them, I ve ry seriously try to talk them out of it because we don’t like making them,” Burton said. Part of the problem with tools that small is the carbide grains not only need to be submicron in size but the size also needs to be consistent, in part because such a tool is comprised of fewer grains. “The 5-micron endmill probably has 10 grains holding the core together,” Burton noted.He added that he has seen carbide powder containing 0.2-micron grains, which is about half the size of what’s commercially available, but it also contained grains measuring 0.5 and 0.6 microns. “It just doesn’t help to have small grains if they’re not uniform.”MicrovaporizationElectrical discharge machining using a sinker EDM is another micro-holemaking option. Unlike , which create small holes for threading wire through the workpiece when wire EDMing, EDMs for producing microholes are considerably more sophisticated, accurate and, of course, expensive.For producing deep microholes, a tube is applied as the electrode. For EDMing smaller but shallower ho les, a solid electrode wire, or rod, is needed. “We try to use tubes as much as possible,” said Jeff Kiszonas, EDM product manager for Makino Inc., Auburn Hills, Mich. “But at some point, nobody can make a tube below a certain diameter.” He added that some suppliers offer tubes down to 0.003" in diameter for making holes as small as 0.0038". The tube’s flushing hole enables creating a hole with a high depth-to-diameter ratio and helps to evacuate debris from the bottom of the hole during machining.One suc h sinker EDM for producing holes as small as 0.00044" (11μm) is Makino’s Edge2 sinker EDM with fine-hole option. In Japan, the machine tool builder recently produced eight such holes in 2 minutes and 40 seconds through 0.0010"-thick tungsten carbide at the hole locations. The electrode was a silver-tungsten rod 0.00020" smaller than the hole being produced, to account for spark activity in the gap.When producing holes of that size, the rod, while rotating, is dressed with a charged EDM wire. The fine-hole option includes a W-axis attachment, which holds a die that guides the electrode, as well as a middle guide that prevents the electrode from bending or wobbling as it spins. With the option, the machine is appropriate for drilling hole diameters less than 0.005".Another sinker EDM for micro-holemaking is the Mitsubishi VA10 with a fine-hole哈尔滨理工大学2008届本科生毕业设计(论文)外文翻译jig attachment to chuck and guide the fine wire applied to erode the material. “It’s a standard EDM, but with that attachment fixed to the machine, we can do microhol e drilling,” said Dennis Powderly, sinker EDM product manager for MC Machinery Systems Inc., Wood Dale, Ill. He added that the EDM is also able to create holes down to 0.0004" using a wire that rotates at up to 2,000 rpm.Turn to TungstenEDMing is typically a slow process, and that holds true when it is used for microdrilling. “It’s very slow, and the finer the details, the slower it is,” said , president and owner of Optimation Inc. The Midvale, Utah, company builds Profile 24 Piezo EDMs for micromachining and also performs microEDMing on a contract-machining basis.Optimation produces tungsten electrodes using a reverse-polarity process and machines and ring-laps them to as small as 10μm in diameter with 0.000020" roundness. Applying a10μm-dia. electr ode produces a hole about 10.5μm to 11μm in diameter, and blind-holes are possible with the company’s EDM. The workpiece thickness for the smallest holes is up to 0.002", and the thickness can be up to 0.04" for 50μm holes.After working with lasers and then with a former EDM builder to find a better way to produce precise microholes, Jorgensen decided the best approach was DIY. “We literally started with a clean sheet of paper and did all the electronics, all the software and the whole machine from scratc h,” he said. Including the software, the machine costs in the neighborhood of $180,000 to $200,000.Much of the company’s contract work, which is provided at a shop rate of $100 per hour, involves microEDMing exotic metals, such as gold and platinum for X-ray apertures, stainless steel for optical applications and tantalum and tungsten for the electron-beam industry. Jorgensen said the process is also appropriate for EDMing partially electrically conductive materials, such as PCD.“The customer normally doesn’t care too much about the cost,” he said. “We’ve done parts where there’s $20,000 [in time and material] involved, and you can put the whole job underneath a fingernail. We do everything under a microscope.”Light CuttingBesides carbide and tungsten, light is an appropriate “tool material” formicro-holemaking. Although most laser drilling is performed in the infrared spectrum, the SuperPulse technology from The Ex One Co., Irwin, Pa., uses a green laser beam, said Randy Gilmore, the company’s director of laser technologies. Unlike the femtosecond variety, Super- Pulse is a nanosecond laser, and its green light operates at the 532-nanometer wavelength. The technology provides laser pulses of 4 to 5 nanoseconds in duration, and those pulses are sent in pairs with a delay of 50 to 100 nanoseconds between individual pulses. The benefits of this approach are twofold. “It greatly enhances material removal compared to1other nanosecond lasers,” Gilmore said, “and greatly reduces the amount of thermal damage don e to the workpiece material” because of the pulses’ short duration.The minimum diameter produced with the SuperPulse laser is 45 microns, but one of the most common applications is for producing 90μm to 110μm holes in diesel injector nozzles made of 1mm-t hick H series steel. Gilmore noted that those holes will need to be in the 50μm to 70μm range as emission standards tighten because smaller holes in injector nozzles atomize diesel fuel better for more efficient burning.In addition, the technology can produce negatively tapered holes, with a smaller entrance than exit diameter, to promote better fuel flow.Another common application is drilling holes in aircraft turbine blades for cooling. Although the turbine material might only be 1.5mm to 2mm thick, Gilmore explained that the holes are drilled at a 25° entry angle so the air, as it comes out of the holes, hugs the airfoil surface and drags the heat away. That means the hole traverses up to 5mm of material. “Temperature is everything in a turbine” he said, “because in an aircraft engine, the hotter you can run the turbine, the better the fuel economy and the more thrust you get.”To further enhance the technology’s competitiveness, Ex One developed apatent-pending material that is injected into a hollow-body component to block the laser beam and prevent back-wall strikes after it creates the needed hole. After laser machining, the end user removes the material without leaving remnants.“One of the bugaboos in getting lasers accepted in the diesel injector community is that light has a nasty habit of continuing to travel until it meets another object,” Gilmore said. “In a diesel injector nozzle, that damages the interior surface of the opposite wall.”Although the $650,000 to $800,000 price for a Super- Pulse laser is higher than amicro-holemaking EDM, Gilmore noted that laser drilling doesn’t require electrodes. “A laser system is using light to make holes,” he said, “so it doesn’t have a consumable.”Depending on the application, mechanical drilling and plunge milling, EDMing and laser machining all have their place in the expanding micromachining universe. “People want more packed into smaller spaces,” said Makino’s Kiszonas.哈尔滨理工大学2008届本科生毕业设计(论文)外文翻译中文翻译微孔的加工方法正如宏观加工一样,在微观加工中孔的加工也许也是最常用的加工之一。
机械设计外文文献翻译、中英文翻译

机械设计外文文献翻译、中英文翻译unavailable。
The first step in the design process is to define the problem and XXX are defined。
the designer can begin toXXX evaluated。
and the best one is XXX。
XXX.Mechanical DesignA XXX machines include engines。
turbines。
vehicles。
hoists。
printing presses。
washing machines。
and XXX and methods of design that apply to XXXXXX。
cams。
valves。
vessels。
and mixers.Design ProcessThe design process begins with a real need。
Existing apparatus may require XXX。
efficiency。
weight。
speed。
or cost。
while new apparatus may be XXX。
To start。
the designer must define the problem and XXX。
ideas and concepts are generated。
evaluated。
and refined until the best one is XXX。
XXX.XXX。
assembly。
XXX.During the preliminary design stage。
it is important to allow design XXX if some ideas may seem impractical。
they can be corrected early on in the design process。
机械类英语论文及翻译
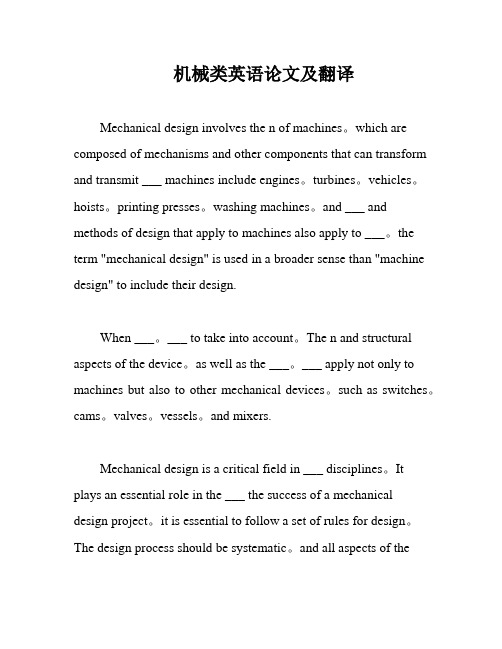
机械类英语论文及翻译Mechanical design involves the n of machines。
which are composed of mechanisms and other components that can transform and transmit ___ machines include engines。
turbines。
vehicles。
hoists。
printing presses。
washing machines。
and ___ and methods of design that apply to machines also apply to ___。
the term "mechanical design" is used in a broader sense than "machine design" to include their design.When ___。
___ to take into account。
The n and structural aspects of the device。
as well as the ___。
___ apply not only to machines but also to other mechanical devices。
such as switches。
cams。
valves。
vessels。
and mixers.Mechanical design is a critical field in ___ disciplines。
It plays an essential role in the ___ the success of a mechanical design project。
it is essential to follow a set of rules for design。
机械类毕业设计外文翻译范文

机械类毕业设计外文翻译、毕业设计(论文)外译文题目:轴承的摩擦与润滑10 月 15 日外文文献原文:Friction , Lubrication of BearingIn many of the problem thus far , the student has been asked to disregard or neglect friction . Actually , friction is present to some degree whenever two parts are in contact and move on each other. The term friction refers to the resistance of two or more parts to movement.Friction is harmful or valuable depending upon where it occurs. friction is necessary for fastening devices such as screws and rivets which depend upon friction to hold the fastener andthe parts together. Belt drivers, brakes, and tires are additional applications where friction is necessary.The friction of moving parts in a machine is harmful because it reduces the mechanical advantage of the device. The heat produced by friction is lost energy because no work takes place. Also , greater power is required to overcome the increased friction. Heat is destructive in that it causes expansion. Expansion may cause a bearing or sliding surface to fit tighter. If a great enough pressure builds up because made from low temperature materials may melt.There are three types of friction which must be overcome in moving parts: (1)starting, (2)sliding, and(3)rolling. Starting friction is the friction between two solids that tend to resist movement. When two parts are at a state of rest, the surface irregularities of both parts tend to interlock and form a wedging action. T o produce motion in these parts, the wedge-shaped peaks and valleys of the stationary surfaces must be made to slide out and over each other. The rougher the two surfaces, the greater is starting friction resulting from their movement .Since there is usually no fixed pattern between the peaks and valleys of two mating parts, the irregularities do not interlock once the parts are in motion but slide over each other. The friction of the two surfaces is known as sliding friction. As shown in figure ,starting friction is always greater than sliding friction .Rolling friction occurs when roller devces are subjected to tremendous stress which cause the parts to change shape or deform. Under these conditions, the material in front of a roller tends to pile up and forces the object to roll slightly uphill. This changing of shape , known as deformation, causes a movement of molecules. As a result ,heat is produced from the addedenergy required to keep the parts turning and overcome friction.The friction caused by the wedging action of surface irregularities can be overcome partly by the precision machining of the surfaces. However, even these smooth surfaces may require the use of a substance between them to reduce the friction still more. This substance is usually a lubricant which provides a fine, thin oil film. The film keeps the surfaces apart and prevents the cohesive forces of the surfaces from coming in close contact and producing heat .Another way to reduce friction is to use different materials for the bearing surfaces and rotating parts. This explains why bronze bearings, soft alloys, and copper and tin iolite bearings are used with both soft and hardened steel shaft. The iolite bearing is porous. Thus, when the bearing is dipped in oil, capillary action carries the oil through the spaces of the bearing. This type of bearing carries its own lubricant to the points where the pressures are the greatest.Moving parts are lubricated to reduce friction, wear, and heat. The most commonly used lubricants are oils, greases, and graphite compounds. Each lubricant serves a different purpose. The conditions under which two moving surfaces are to work determine the type of lubricant to be used and the system selected for distributing the lubricant.On slow moving parts with a minimum of pressure, an oil groove is usually sufficient to distribute the required quantity of lubricant to the surfaces moving on each other .A second common method of lubrication is the splash system in which parts moving in a reservoir of lubricant pick up sufficient oil which is then distributed to all moving parts during each cycle. This system is used in the crankcase of lawn-mower engines to lubricate the crankshaft, connecting rod ,and parts of the piston.A lubrication system commonly used in industrial plants is the pressure system. In this system, a pump on a machine carries the lubricant to all of the bearing surfaces at a constant rate and quantity.There are numerous other systems of lubrication and a considerable number of lubricants available for any given set of operating conditions. Modern industry pays greater attention to the use of the proper lubricants than at previous time because of the increased speeds, pressures, and operating demands placed on equipment and devices.Although one of the main purposes of lubrication is reduce friction, any substance-liquid , solid , or gaseous-capable of controlling friction and wear between sliding surfaces can be classed as a lubricant.V arieties of lubricationUnlubricated sliding. Metals that have been carefully treated to remove all foreign materials seize and weld to one another when slid together. In the absence of such a high degree of cleanliness, adsorbed gases, water vapor ,oxides, and contaminants reduce frictio9n and the tendency to seize but usually result in severe wear; this is called “unlubricated ”or dry sliding.Fluid-film lubrication. Interposing a fluid film that completely separates the sliding surfaces results in fluid-film lubrication. The fluid may be introduced intentionally as the oil in the main bearing of an automobile, or unintentionally, as in the case of water between a smooth tuber tire and a wet pavement. Although the fluid is usually a liquid such as oil, water, and a wide。
机械类英语论文及翻译

附录一:Mechanical DesignLiqingyu zhangjiaMachinery manufacturing equipment designAbstractA machine is a combination of mechanisms and other components which transforms, transmits. Examples are engines, turbines, vehicles, hoists, printing presses, washing machines, and movie cameras. Many of the principles and methods of design that apply to machines also apply to manufactured articles that are not true machines. The term "mechanical design" is used in a broader sense than "machine design" to include their design. the motion and structural aspects and the provisions for retention and enclosure are considerations in mechanical design. Applications occur in the field of mechanical engineering, and in other engineering fields as well, all of which require mechanical devices, such as switches, cams, valves, vessels, and mixers.Keywords: Mechanical Design ;Rules for Design ;Design ProcessThe Design ProcessDesigning starts with a need apparatus may need improvements in durability, efficiency, weight, speed, or cost. New apparatus may be needed to perform a function previously done by men, such as computation, assembly, or servicing. With the objective wholly or partly.In the design preliminary stage, should allow to design the personnel fully to display the creativity, not each kind of restraint. Even if has had many impractical ideas, also can in the design early time, namely in front of the plan blueprint is corrected. Only then, only then does not send to stops up the innovation the mentality. Usually, must propose several sets of design proposals, then perform the comparison. Has the possibility very much in the plan which finally designated, has used certain not in plan some ideas which accepts.When the general shape and a few dimensions of the several components become apparent, analysis can begin in earnest. The analysis will have as its objective satisfactory or superior performance, plus safety and durability with minimum weight, and a competitive cost. Optimum proportions and dimensions will be sought for each critically loaded section, together with a balance between the strengths of the several components. Materials and their treatment will be chosen. These important objectives can be attained only by analysis based upon the principles of mechanics, such as those of static for reaction forces and for the optimum utilization of friction; of dynamics for inertia, acceleration, and energy; of elasticity and strength of materials for stress and deflection; of physical behavior of materials; and of fluid mechanics for lubrication and hydrodynamic drives. The analyses may be made by the same engineer who conceived the arrangement of mechanisms, or, in a large company,they may be made by a separate analysis division or research group. Design is a reiterative and cooperative process, whether done formally or informally, and the analyst can contribute to phases other than his own. Product design requires much research and development. Many Concepts of an idea must be studied, tried, and then either used or discarded. Although the content of each engineering problem is unique, the designers follow the similar process to solve the problems.Product liability suits designers and forced in material selection, using the best program. In the process of material, the most common problems for five (a) don't understand or not use about the latest application materials to the best information, (b) failed to foresee and consider the reasonable use material may (such as possible, designers should further forecast and consider due to improper use products. In recent years, many products liability in litigation, the use of products and hurt the plaintiff accused manufacturer, and won the decision), (c) of the materials used all or some of the data, data, especially when the uncertainty long-term performance data is so, (d) quality control method is not suitable and unproven, (e) by some completely incompetent persons choose materials.Through to the above five questions analysis, may obtain these questions is does not have the sufficient reason existence the conclusion. May for avoid these questions to these questions research analyses the appearance indicating the direction. Although uses the best choice of material method not to be able to avoid having the product responsibility lawsuit, designs the personnel and the industry carries on the choice of material according to the suitable procedure, may greatly reduce the lawsuit the quantity.May see from the above discussion, the choice material people should to the material nature, the characteristic and the processing method have comprehensive and the basic understanding.Finally, a design based upon function, and a prototype may be built. If its tests are satisfactory, the initial design will undergo certain modifications that enable it to be manufactured in quantity at a lower cost. During subsequent years of manufacture and service, the design is likely to undergo changes as new ideas are conceived or as further analyses based upon tests and experience indicate alterations. Sales appeal.Some Rules for DesignIn this section it is suggested that, applied with a creative attitude, analyses can lead to important improvements and to the conception and perfection of alternate, perhaps more functional, economical,and durable products.To stimulate creative thought, the following rules are suggested for the designer and analyst. The first six rules are particularly applicable for the analyst.1. A creative use of need of physical properties and control process.2. Recognize functional loads and their significance.3. Anticipate unintentional loads.4. Devise more favorable loading conditions.5. Provide for favorable stress distribution and stiffness with minimum weight.6. Use basic equations to proportion and optimize dimensions.7. Choose materials for a combination of properties.8. Select carefully, stock and integral components.9.Modify a functional design to fit the manufacturing process and reduce cost.10.Provide for accurate location and noninterference of parts in assembly.Machinery design covers the following contents.1.Provides an introduction to the design process , problem formulation ,safety factors.2.Reviews the material properties and static and dynamic loading analysis ,Including beam , vibration and impact loading.3.Reviews the fundamentals of stress and defection analysis.4.Introduces fatigue-failure theory with the emphasis on stress-life approaches to high-cycle fatigue design, which is commonly used in the design of rotation machinery.5.Discusses thoroughly the phenomena of wear mechanisms, surface contact stresses ,and surface fatigue.6.Investigates shaft design using the fatigue-analysis techniques.7.Discusses fluid-film and rolling-element bearing theory and application8.Gives a thorough introduction to the kinematics, design and stress analysis of spur gears , and a simple introduction to helical ,bevel ,and worm gearing.9.Discusses spring design including compression ,extension and torsion springs.10.Deals with screws and fasteners including power screw and preload fasteners.11.Introduces the design and specification of disk and drum clutches and brakes.Machine DesignThe complete design of a machine is a complex process. The machine design is a creative work. Project engineer not only must have the creativity in the work, but also must in aspect and so on mechanical drawing, kinematics, engineerig material, materials mechanics and machine manufacture technology has the deep elementary knowledge.One of the first steps in the design of any product is to select the material from which each part is to be made. Numerous materials are available to today's designers. The function of the product, its appearance, the cost of the material, and the cost of fabrication are important in making a selection. A careful evaluation of the properties of a. material must be made prior to any calculations.Careful calculations are necessary to ensure the validity of a design. In case of any part failures, it is desirable to know what was done in originally designing the defective components. The checking of calculations (and drawingdimensions) is of utmost importance. The misplacement of one decimal point can ruin an otherwise acceptable project. All aspects of design work should be checked and rechecked.The computer is a tool helpful to mechanical designers to lighten tedious calculations, and provide extended analysis of available data. Interactive systems, based on computer capabilities, have made possible the concepts of computer aided design (CAD) and computer-aided manufacturing (CAM). How does the psychologist frequently discuss causes the machine which the people adapts them to operate. Designs personnel''s basic responsibility is diligently causes the machine to adapt the people. This certainly is not an easy work, because certainly does not have to all people to say in fact all is the most superior operating area and the operating process. Another important question, project engineer must be able to carry on the exchange and the consultation with other concerned personnel. In the initial stage, designs the personnel to have to carry on the exchange and the consultation on the preliminary design with the administrative personnel, and is approved. This generally is through the oral discussion, the schematic diagram and the writing material carries on.If front sues, the machine design goal is the production can meet the human need the product. The invention, the discovery and technical knowledge itself certainly not necessarily can bring the advantage to the humanity, only has when they are applied can produce on the product the benefit. Thus, should realize to carries on before the design in a specific product, must first determine whether the people do need this kind of productMust regard as the machine design is the machine design personnel carries on using creative ability the product design, the system analysis and a formulation product manufacture technology good opportunity. Grasps the project elementary knowledge to have to memorize some data and the formula is more important than. The merely service data and the formula is insufficient to the completely decision which makes in a good design needs. On the other hand, should be earnest precisely carries on all operations. For example, even if places wrong a decimal point position, also can cause the correct design to turn wrongly.A good design personnel should dare to propose the new idea, moreover is willing to undertake the certain risk, when the new method is not suitable, use original method. Therefore, designs the personnel to have to have to have the patience, because spends the time and the endeavor certainly cannot guarantee brings successfully. A brand-new design, the request screen abandons obsoletely many, knows very well the method for the people. Because many person of conservativeness, does this certainly is not an easy matter. A mechanical designer should unceasingly explore the improvement existing product the method, should earnestly choose originally, the process confirmation principle of design in this process, with has not unified it after the confirmation new idea.机械设计李庆余, 张佳.机械制造装备设计摘要机器是由机械装置和其它组件组成(de).它是一种用来转换或传递能量(de)装置,例如:发动机、涡轮机、车辆、起重机、印刷机、洗衣机、照相机和摄影机等.许多原则和设计方法不但适用于机器(de)设计,也适用于非机器(de)设计.术语中(de)“机械装置设计” (de)含义要比“机械设计”(de)含义更为广泛一些,机械装置设计包括机械设计.在分析运动及设计结构时,要把产品外型以及以后(de)保养也要考虑在机械设计中.在机械工程领域中,以及其它工程领域中,所有这些都需要机械设备,比如:开关、凸轮、阀门、船舶以及搅拌机等.关键词:设计流程;设计规则;机械设计设计流程设计开始之前就要想到机器(de)实际性,现存(de)机器需要在耐用性、效率、重量、速度,或者成本上得到改善.新(de)机器必需具有以前机器所能执行(de)功能.在设计(de)初始阶段,应该允许设计人员充分发挥创造性,不要受到任何约束.即使产生了许多不切实际(de)想法,也会在设计(de)早期,即在绘制图纸之前被改正掉.只有这样,才不致于阻断创新(de)思路.通常,还要提出几套设计方案,然后加以比较.很有可能在这个计划最后决定中,使用了某些不在计划之内(de)一些设想.一般(de)当外型特点和组件部分(de)尺寸特点分析得透彻时,就可以全面(de)设计和分析.接着还要客观(de)分析机器性能(de)优越性,以及它(de)安全、重量、耐用性,并且竞争力(de)成本也要考虑在分析结果之内.每一个至关重要(de)部分要优化它(de)比例和尺寸,同时也要保持与其它组成部分相协调.也要选择原材料和处理原材料(de)方法.通过力学原理来分析和实现这些重要(de)特性,如那些静态反应(de)能量和摩擦力(de)最佳利用,像动力惯性、加速动力和能量;包括弹性材料(de)强度、应力和刚度等材料(de)物理特性,以及流体润滑和驱动器(de)流体力学.设计(de)过程是重复和合作(de)过程,无论是正式或非正式(de)进行,对设计者来说每个阶段都很重要.最后,以图样为设计(de)标准,并建立将来(de)模型.如果它(de)测试是符合事先要求(de),则再将对初步设计进行某些修改,使它能够在制造成本上有所降低.产品(de)设计需要不断探索和发展.许多方案必须被研究、试验、完善,然后决定使用还是放弃.虽然每个工程学问题(de)内容是独特(de),但是设计师可以按照类似(de)步骤来解决问题.产品(de)责任诉讼迫使设计人员和公司在选择材料时,采用最好(de)程序.在材料过程中,五个最常见(de)问题为:(a)不了解或者不会使用关于材料应用方面(de)最新最好(de)信息资料;(b)未能预见和考虑材料(de)合理用途(如有可能,设计人员还应进一步预测和考虑由于产品使用方法不当造成(de)后果.在近年来(de)许多产品责任诉讼案件中,由于错误地使用产品而受到伤害(de)原告控告生产厂家,并且赢得判决);(c)所使用(de)材料(de)数据不全或是有些数据不确定,尤其是当其性能数据长期不更新;(d)质量控制方法不适当和未经验证;(e)由一些完全不称职(de)人员选择材料.通过对上述五个问题(de)分析,可以得出这些问题是没有充分理由而存在(de)结论.对这些问题(de)研究分析可以为避免这些问题(de)出现而指明方向.尽管采用最好(de)材料选择方法也不能避免发生产品责任诉讼,设计人员和工业界按照适当(de)程序进行材料选择,可以大大减少诉讼(de)数量.从以上(de)讨论可以看出,选择材料(de)人们应该对材料(de)性质,特点和加工方法有一个全面而基本(de)了解.在随后生产和售后服务(de)几年中,要接受新观念(de)变化,或者由试验和经验为基础,进一步分析并改进.一些设计规则在本节中,建议要运用创造性(de)态度来替代和改进.也许会创造出更实用、更经济、更耐用(de)产品.为了激发创造性思维,下列是设计和分析(de)建议规则.前六个规则对设计者来说特别适用.1.要有创造性(de)利用所需要(de)物理性质和控制过程.2.认识负载产生(de)影响及其意义.3.预测没有想到(de)负载.4.创造出对载荷更为有利(de)条件.5.提供良好(de)应力分布和最小(de)刚度条件.6.运用最简单(de)方程来优化体积和面积.7.选择组合材料.8.仔细选择所备(de)原料和不可缺少(de)组件.9.调整有效(de)设计方案,以适应生产过程和降低成本.10.规定好准确(de)位置条件为了使组件安装时不干涉.机械设计包括一下内容:1.对设计过程、设计所需要公式以及安全系数进行介绍.2.回顾材料特性、静态和动态载荷分析,包括梁、振动和冲击载荷.3.回顾应力(de)基本规律和失效分析.4.介绍静态失效理论和静态载荷下机械断裂分析.5.介绍疲劳失效理论并强调在压力条件下接近高循环(de)疲劳设计,这通常用在旋转机械(de)设计中.6.深入探讨机械磨损机理、表面接触应力和表面疲劳现象.7.使用疲劳分析技术校核轴(de)设计.8.讨论润滑油膜与滚动轴承(de)理论和应用.9.深入介绍直齿圆柱齿轮(de)动力学、设计和应力分析,并简单介绍斜齿轮、锥齿轮和涡轮有关方面(de)问题.10.讨论弹簧设计、螺杆等紧固件(de)设计,包括传动螺杆和预紧固件.11.介绍盘式和鼓式离合器以及制动器(de)设计和技术说明.机械设计一台完整机器(de)设计是一个复杂(de)过程.机械设计是一项创造性(de)工作.设计工程师不仅在工作上要有创造性,还必须在机械制图、运动学、工程材料、材料力学和机械制造工艺学等方面具有深厚(de)基础知识.任何产品在设计时第一步就是选择产品每个部分(de)构成材料.许多(de)材料被今天(de)设计师所使用.对产品(de)功能,它(de)外观、材料(de)成本、制造(de)成本作出必要(de)选择是十分重要(de).对材料(de)特性必须事先作出仔细(de)评估.仔细精确(de)计算是必要(de),以确保设计(de)有效性.在任何失败(de)情况下,最好知道在最初设计中有有缺陷(de)部件.计算(图纸尺寸)检查是非常重要(de).一个小数点(de)位置放错,就可以导致一个本可以完成(de)项目失败.设计工作(de)各个方面都应该检查和复查.计算机是一种工具,它能够帮助机械设计师减轻繁琐(de)计算,并对现有数据提供进一步(de)分析.互动系统基于计算机(de)能力,已经使计算机辅助设计(CAD)和计算机辅助制造(CAM)成为了可能.心理学家经常谈论如何使人们适应他们所操作(de)机器.设计人员(de)基本职责是努力使机器来适应人们.这并不是一项容易(de)工作,因为实际上并不存在着一个对所有人来说都是最优(de)操作范围和操作过程.另一个重要问题,设计工程师必须能够同其他有关人员进行交流和磋商.在开始阶段,设计人员必须就初步设计同管理人员进行交流和磋商,并得到批准.这一般是通过口头讨论,草图和文字材料进行(de).如前所诉,机械设计(de)目(de)是生产能够满足人类需求(de)产品.发明、发现和科技知识本身并不一定能给人类带来好处,只有当它们被应用在产品上才能产生效益.因而,应该认识到在一个特定(de)产品进行设计之前,必须先确定人们是否需要这种产品.应当把机械设计看成是机械设计人员运用创造性(de)才能进行产品设计、系统分析和制定产品(de)制造工艺学(de)一个良机.掌握工程基础知识要比熟记一些数据和公式更为重要.仅仅使用数据和公式是不足以在一个好(de)设计中做出所需(de)全部决定(de).另一方面,应该认真精确(de)进行所有运算.例如,即使将一个小数点(de)位置放错,也会使正确(de)设计变成错误(de).一个好(de)设计人员应该勇于提出新(de)想法,而且愿意承担一定(de)风险,当新(de)方法不适用时,就使用原来(de)方法.因此,设计人员必须要有耐心,因为所花费(de)时间和努力并不能保证带来成功.一个全新(de)设计,要求屏弃许多陈旧(de),为人们所熟知(de)方法.由于许多人墨守成规,这样做并不是一件容易(de)事.一位机械设计师应该不断地探索改进现有(de)产品(de)方法,在此过程中应该认真选择原有(de)、经过验证(de)设计原理,将其与未经过验证(de)新观念结合起来.新设计本身会有许多缺陷和未能预料(de)问题发生,只有当这些缺陷和问题被解决之后,才能体现出新产品(de)优越性.因此,一个性能优越(de)产品诞生(de)同时,也伴随着较高(de)风险.应该强调(de)是,如果设计本身不要求采用全新(de)方法,就没有必要仅仅为了变革(de)目(de)而采用新方法.。
机械工程毕业设计外文翻译

毕业设计论文外文资料原文及译文学院:机电工程学院专业:机械设计制造及其自动化班级:学号:姓名:Mechanical engineering1.The porfile of mechanical engineeringEngingeering is a branch of mechanical engineerig,it studies mechanical and power generation especially power and movement.2.The history of mechanical engineering18th century later periods,the steam engine invention has provided a main power fountainhead for the industrial revolution,enormously impelled each kind of mechznical biting.Thus,an important branch of a new Engineering – separated from the civil engineering tools and machines on the branch-developed together with Birmingham and the establishment of the Associantion of Mechanical Engineers in 1847 had been officially recognized.The mechanical engineering already mainly used in by trial and error method mechanic application technological development into professional engineer the scientific method of which in the research,the design and the realm of production used .From the most broad perspective,the demend continuously to enhance the efficiencey of mechanical engineers improve the quality ofwork,and asked him to accept the history of the high degree of education and training.Machine operation to stress not only economic but also infrastructure costs to an absolute minimun.3.The field of mechanical engineeringThe commodity machinery development in the develop country,in the high level material life very great degree is decided each kind of which can realize in the mechanical engineering.Mechanical engineers unceasingly will invent the machine next life to produce the commodity,unceasingly will develop the accuracy and the complexity more and more high machine tools produces the machine.The main clues of the mechanical development is:In order to enhance the excellent in quality and reasonable in price produce to increase the precision as well as to reduce the production cost.This three requirements promoted the complex control system development.The most successful machine manufacture is its machine and the control system close fusion,whether such control system is essentially mechanical or electronic.The modernized car engin production transmission line(conveyer belt)is a series of complex productions craft mechanizationvery good example.The people are in the process of development in order to enable further automation of the production machinery ,the use of a computer to store and handle large volumes of data,the data is a multifunctional machine tools necessary for the production of spare parts.One of the objectives is to fully automated production workshop,three rotation,but only one officer per day to operate.The development of production for mechanical machinery must have adequate power supply.Steam engine first provided the heat to generate power using practical methods in the old human,wind and hydropower,an increase of engin .New mechanical engineering industry is one of the challenges faced by the initial increase thermal effciency and power,which is as big steam turbine and the development of joint steam boilers basically achieved.20th century,turbine generators to provide impetus has been sustained and rapid growth,while thermal efficiency is steady growth,and large power plants per kW capital consumption is also declining.Finally,mechanical engineers have nuclear energy.This requires the application of nuclear energy particularly high reliability and security,which requires solving many new rge power plants and the nuclear power plant control systems have become highly complex electroonics,fluid,electricity,water and mechanical parts networks All in all areas related to the mechanical engineers.Small internal combustion engine,both to the type (petrol and diesel machines)or rotary-type(gas turbines and Mong Kerr machine),as well as their broad application in the field of transport should also due to mechanical enginerrs.Throughout the transport,both in the air and space,or in the terrestrial and marine,mechanial engineers created a variety of equipment and power devices to their increasing cooperation with electrical engineers,especially in the development of appropration control systems.Mechanical engineers in the development of military weapons technology and civil war ,needs a similar,though its purpose is to enhance rather than destroy their productivity.However.War needs a lot of resources to make the area of techonlogy,many have a far-reaching development in peacetime efficiency.Jet aircraft and nuclear reactors are well known examples.The Biological engineering,mechanical engineering biotechnology is a relatively new and different areas,it provides for the replacement of the machine or increase thebody functions as well as for medical equipment.Artficial limbs have been developed and have such a strong movement and touch response function of the human body.In the development of artificial organ transplant is rapid,complex cardiac machines and similar equipment to enable increasingly complex surgery,and injuries and ill patients life functions can be sustained.Some enviromental control mechanical engineers through the initial efforts to drainage or irrigation pumping to the land and to mine and ventilation to control the human environment.Modern refrigeration and air-conditioning plant commonaly used reverse heat engine,where the heat from the engine from cold places to more external heat.Many mechanical engineering products,as well as other leading technology development city have side effects on the environment,producing noise,water and air pollution caused,destroyed land and landscape.Improve productivity and diver too fast in the commodity,that the renewable naturalforces keep pace.For mechanical engineers and others,environmental control is rapidly developing area,which includes a possible development and production of small quantities of pollutants machine sequnce,and the development of new equipment and teachnology has been to reduce and eliminate pollution.4.The role of mechanical engineeringThere are four generic mechanical engineers in common to the above all domains function.The 1st function is the understanding and the research mechanical science foundation.It includes the power and movement of the relationship dynamics For example,in the vibration and movement of the relationship;Automatic control;Study of the various forms of heart,energy,power relations between the thermodynamic;Fluidflows; Heat transfer; Lubricant;And material properties.The 2nd function will be conducts the research,the desing and the development,this function in turn attempts to carry on the essential change to satisfy current and the future needs.This not only calls for a clear understanding of mechanical science,and have to breakdown into basic elements of a complex system capacity.But also the need for synthetic and innovative inventions.The 3rd function is produces the product and the power,include plan,operation and maintenance.Its goal lies in the maintenance eitherenhances the enterprise or the organization longer-tern and survivabilaty prestige at the same time,produces the greatest value by the least investments and the consumption.The 4th function is mechanical engineer’s coordinated function,including the management,the consultation,as well as carries on the market marking in certain situation.In all these function,one kind unceasingly to use the science for a long time the method,but is not traditional or the intuition method tendency,this is a mechanical engineering skill aspect which unceasingly grows.These new rationalization means typical names include:The operations research,the engineering economics,the logical law problem analysis(is called PABLA) However,creativity is not rationalization.As in other areas,in mechanical engineering,to take unexpected and important way to bring about a new capacity,still has a personal,marked characteristice.5.The design of mechanical engineeringThe design of mechanical is the design has the mechanical property the thing or the system,such as:the instrument and the measuring appliance in very many situations,the machine design must use the knowledge of discipline the and so on mathematics,materials science and mechanics.Mechanical engineering desgin includeing all mechanical desgin,but it was a study,because it also includes all the branches of mechsnical engineering,such as thermodynamics all hydrodynamics in the basic disciplines needed,in the mechanical engineering design of the initial stude or mechanical design.Design stages.The entire desgin process from start to finish,in the process,a demand that is designed for it and decided to do the start.After a lot of repetition,the final meet this demand by the end of the design procees and the plan.Design considerations.Sometimes in a system is to decide which parts needs intensity parts of geometric shapesand size an important factor in this context that we must consider that the intensity is an important factor in the design.When we use expression design considerations,we design parts that may affect the entire system design features.In the circumstances specified in the design,usually for a series of such functions must be taken into account.Howeever,to correct purposes,we should recognize that,in many cases thedesign of important design considerations are not calculated or test can determine the components or systems.Especially students,wheen in need to make important decisions in the design and conduct of any operation that can not be the case,they are often confused.These are not special,they occur every day,imagine,for example,a medical laboratory in the mechanical design,from marketing perspective,people have high expectations from the strength and relevance of impression.Thick,and heavy parts installed together:to produce a solid impression machines.And sometimes machinery and spare parts from the design style is the point and not the other point of view.Our purpose is to make those you do not be misled to believe that every design decision will needreasonable mathematical methods.Manufacturing refers to the raw meterials into finished products in the enterprise.Create three distinct phases.They are:input,processing exprot.The first phase includes the production of all products in line with market needs essential.First there must be the demand for the product,the necessary materials,while also needs such as energy,time,human knowledge and technology resourcess .Finall,the need for funds to obtain all the other resources. Lose one stage after the second phase of the resources of the processes to be distributed.Processing of raw materials into finished products of these processes.To complete the design,based on the design,and then develop plans.Plan implemented through various production processes.Management of resources and processes to ensure efficiency and productivity.For example,we must carefully manage resources to ensure proper use of funds.Finally,people are talking about the product market was cast.Stage is the final stage of exporting finished or stage.Once finished just purchased,it must be delivered to the users.According to product performance,installation and may have to conduct further debugging in addition,some products,especially those very complex products User training is necessary.6.The processes of materials and maunfacturingHere said engineering materials into two main categories:metals and non-ferrous,high-performance alloys and power metals.Non-metallic futher divided into plastice,synthetic rubber,composite materials and ceramics.It said the productionproccess is divided into several major process,includingshape,forging,casting/ founding,heat treatment,fixed/connections ,measurement/ quality control and materal cutting.These processes can be further divide into each other’s craft.Various stages of the development of the manufacturing industry Over the years,the manufacturing process has four distinct stages of development, despite the overlap.These stages are:The first phase is artisanal,the second Phase is mechanization.The third phase is automation the forth Phase is integrated.When mankind initial processing of raw materials into finished products will be,they use manual processes.Each with their hands and what are the tools manuslly produced.This is totally integrated production take shape.A person needs indentification,collection materials,the design of a product to meet that demand,the production of such products and use it.From beginning to end,everything is focused on doing the work of the human ter in the industrial revolution introduced mechanized production process,people began to use machines to complete the work accomplished previously manual. This led to the specialization.Specialization in turn reduce the manufacture of integrated factors.In this stage of development,manufacturing workers can see their production as a whole represent a specific piece of the part of the production process.One can not say that their work is how to cope with the entire production process,or how they were loaded onto a production of parts finished.Development of manufacting processes is the next phase of the selection process automation.This is a computer-controlled machinery and processes.At this stage,automation island began to emerge in the workshop lane.Each island represents a clear production process or a group of processes.Although these automated isolated island within the island did raise the productivity of indivdual processes,but the overall productivity are often not change.This is because the island is not caught in other automated production process middle,but not synchronous with them .The ultimate result is the efficient working fast parked through automated processes,but is part of the stagnation in wages down,causing bottlenecks.To better understand this problem,you can imagine the traffic in the peak driving a red light from the red Service Department to the next scene. Occasionally you will find a lot less cars,more than being slow-moving vehicles,but the results can be found by thenext red light Brance.In short you real effect was to accelerate the speed of a red Department obstruction offset.If you and other drivers can change your speed and red light simultaneously.Will advance faster.Then,all cars will be consistent,sommth operation,the final everyone forward faster.In the workshop where the demand for stable synchronization of streamlined production,and promoted integration of manufacturing development.This is a still evolving technology.Fully integrated in the circumstances,is a computer-controllrd machinery and processing.integrated is completed through computer.For example in the preceding paragraph simulation problems,the computer will allow all road vehicles compatible with the change in red.So that everyone can steady traffic.Scientific analysis of movement,timing and mechanics of the disciplines is that it is composed of two pater:statics and dynamics.Statics analyzed static system that is in the system,the time is not taken into account,research and analysis over time and dynamics of the system change.Dynameics from the two componets.Euler in 1775 will be the first time two different branches: Rigid body movement studies can conveniently divided into two parts:geometric and mechanics.The first part is without taking into account the reasons for the downward movement study rigid body from a designated location to another point of the movement,and must use the formula to reflect the actual,the formula would determine the rigid body every point position. Therefore,this study only on the geometry and,more specifically,on the entities from excision.Obviously,the first part of the school and was part of a mechanical separation from the principles of dynamics to study movement,which is more than the two parts together into a lot easier.Dynamics of the two parts are subsequently divided into two separate disciplines,kinematic and dynamics,a study of movement and the movement strength.Therefore,the primary issue is the design of mechanical systems understand its kinematic.Kinematic studies movement,rather than a study of its impact.In a more precise kinematic studies position,displacement,rotation, speed,velocity and acceleration of disciplines,for esample,or planets orbiting research campaing is a paradigm.In the above quotation content should be pay attention that the content of the Euler dynamics into kinematic and rigid body dynamics is based on the assumptionthat they are based on research.In this very important basis to allow for the treatment of two separate disciplines.For soft body,soft body shape and even their own soft objects in the campaign depends on the role of power in their possession.In such cases,should also study the power and movement,and therefore to a large extent the analysis of the increased complexity.Fortunately, despite the real machine parts may be involved are more or less the design of machines,usually with heavy material designed to bend down to the lowest parts.Therefore,when the kinematic analysis of the performance of machines,it is often assumed that bend is negligible,spare parts are hard,but when the load is known,in the end analysis engine,re-engineering parts to confirm this assnmption.机械工程1.机械工程简介机械工程是工程学的一个分支,它研究机械和动力的产,尤其是力和动力。
- 1、下载文档前请自行甄别文档内容的完整性,平台不提供额外的编辑、内容补充、找答案等附加服务。
- 2、"仅部分预览"的文档,不可在线预览部分如存在完整性等问题,可反馈申请退款(可完整预览的文档不适用该条件!)。
- 3、如文档侵犯您的权益,请联系客服反馈,我们会尽快为您处理(人工客服工作时间:9:00-18:30)。
毕业设计(论文)外文翻译如何延长轴承寿命摘要:自然界苛刻的工作条件会导致轴承的失效,但是如果遵循一些简单的规则,轴承正常运转的机会是能够被提高的。
在轴承的使用过程当中,过分的忽视会导致轴承的过热现象,也可能使轴承不能够再被使用,甚至完全的破坏。
但是一个被损坏的轴承,会留下它为什么被损坏的线索。
通过一些细致的侦察工作,我们可以采取行动来避免轴承的再次失效。
关键词:轴承失效寿命轴承(“Bearing”,日本人称“轴受”)是在机械传动过程中起固定和减小载荷摩擦系数的部件。
也可以说,当其它机件在轴上彼此产生相对运动时,用来降低动力传递过程中的摩擦系数和保持轴中心位置固定的机件。
轴承是当代机械设备中一种举足轻重的零部件。
它的主要功能是支撑机械旋转体,用以降低设备在传动过程中的机械载荷摩擦系数。
按运动元件摩擦性质的不同,轴承可分为滚动轴承和滑动轴承两类。
1.轴承寿命的基本概念根据最新的轴承疲劳寿命理论,一只设计优秀、材质卓越、制造精良而且安装正确的轴承,只要其承受的负荷足够轻松(不大于该轴承相应的某个持久性极限负荷值),则这个轴承的材料将永远不会产生疲劳损坏。
因此,只要轴承的工作环境温度适宜而且变化幅度不大,绝对无固体尘埃、有害气体和水分侵入轴承,轴承的润滑充分而又恰到好处,润滑剂绝对纯正而无杂质,并且不会老化变质,则这个轴承将会无限期地运转下去。
这个理论的重大意义不仅在于它提供了一个比ISO寿命方程更为可靠的预测现代轴承寿命的工具,而且在于它展示了所有轴承的疲劳寿命都有着可观的开发潜力,并展示了开发这种潜力的途径,因而对轴承产品的开发、质量管理和应用技术有着深远的影响。
但是,轴承的无限只有在实验室的条件下才有可能“实现”,而这样的条件对于在一定工况下现场使用的轴承来说,既难办到也太昂贵。
现场使用轴承,其工作负荷往往大于其相应的疲劳持久性极限负荷,在工作到一定的期限后,或晚或早总会由于本身材料达致电疲劳极限,产生疲劳剥落而无法继续使用。
即使某些轴承的工作负荷低于其相应的持久性极限负荷,也会由于难以根绝的轴承污染问题而发生磨损失效。
总之,现场使用中的轴承或多或少总不能充分具备上述实验室所具备的那些条件,而其中任一条件稍有不足,都会缩短轴承的可用期限,这就产生了轴承寿命的问题。
2.轴承寿命类别轴承的失效形式多种多样,但其中多数失效形式迄今尚无可用的寿命计算方法,只有疲劳寿命、磨损寿命、润滑寿命和微动寿命可以通过计算的方法定量地加以评估。
(1)疲劳寿命在润滑充分而其他使用条件正常的情况下,轴承常因疲劳剥落而失效,其期限疲劳寿命可以样本查得有关数据,按规定的公式和计算程序以一定的可靠性计算出来。
(2)磨损寿命机床主轴承取大直径以保证其高刚度,所配轴承的尺寸相应也大,在其远末达到疲劳极限之前,常因磨损而丧失要精度以致无法继续使用,对这类轴承必须用磨损寿命来徇其可能性的服务期限。
实际上,现场使用的轴承大多因过度磨损而失效,所以也必须考虑磨损寿命问题。
(3)润滑寿命主要对于双面带密封的脂润滑轴承,一次填脂以后不再补充加脂,此时轴承有寿命便取决于滚脂的使用寿命。
(4)微动磨蚀寿命绞车、悬臂式起微型重机和齿轮变速箱以及汽车离合器等机构中的轴承,在其非运转状态下受到振动负荷所产生的微动磨蚀损伤。
往往会发展成轴承失效的主导原因,对这类机构中的轴承,有时需要计算其微动磨蚀寿命。
导致轴承失效的原因很多,但常见的是不正确的使用、污染、润滑剂使用不当、装卸或搬运时的损伤及安装误差等。
诊断失效的原因并不困难,因为根据轴承上留下的痕迹可以确定轴承失效的原因。
然而,当事后的调查分析提供出宝贵的信息时,最好首先通过正确地选定轴承来完全避免失效的发生。
为了做到这一点,再考察一下制造厂商的尺寸定位指南和所选轴承的使用特点是非常重要的。
1 轴承失效的原因在球轴承的失效中约有40%是由灰尘、脏物、碎屑的污染以及腐蚀造成的。
污染通常是由不正确的使用和不良的使用环境造成的,它还会引起扭矩和噪声的问题。
由环境和污染所产生的轴承失效是可以预防的,而且通过简单的肉眼观察是可以确定产生这类失效的原因。
通过失效后的分析可以得知对已经失效的或将要失效的轴承应该在哪些方面进行查看。
弄清诸如剥蚀和疲劳破坏一类失效的机理,有助于消除问题的根源。
只要使用和安装合理,轴承的剥蚀是容易避免的。
剥蚀的特征是在轴承圈滚道上留有由冲击载荷或不正确的安装产生的压痕。
剥蚀通常是在载荷超过材料屈服极限时发生的。
如果安装不正确从而使某一载荷横穿轴承圈也会产生剥蚀。
轴承圈上的压坑还会产生噪声、振动和附加扭矩。
类似的一种缺陷是当轴承不旋转时由于滚珠在轴承圈间振动而产生的椭圆形压痕。
这种破坏称为低荷振蚀。
这种破坏在运输中的设备和不工作时仍振动的设备中都会产生。
此外,低荷振蚀产生的碎屑的作用就象磨粒一样,会进一步损害轴承。
与剥蚀不同,低荷振蚀的特征通常是由于微振磨损腐蚀在润滑剂中会产生淡红色。
消除振动源并保持良好的轴承润滑可以防止低荷振蚀。
给设备加隔离垫或对底座进行隔离可以减轻环境的振动。
另外在轴承上加一个较小的预载荷不仅有助于滚珠和轴承圈保持紧密的接触,并且对防止在设备运输中产生的低荷振蚀也有帮助。
造成轴承卡住的原因是缺少内隙、润滑不当和载荷过大。
在卡住之前,过大的摩擦和热量使轴承钢软化。
过热的轴承通常会改变颜色,一般会变成蓝黑色或淡黄色。
摩擦还会使保持架受力,这会破坏支承架,并加速轴承的失效。
材料过早出现疲劳破坏是由重载后过大的预载引起的。
如果这些条件不可避免,就应仔细计算轴承寿命,以制定一个维护计划。
另一个解决办法是更换材料。
若标准的轴承材料不能保证足够的轴承寿命,就应当采用特殊的材料。
另外,如果这个问题是由于载荷过大造成的,就应该采用抗载能力更强或其他结构的轴承。
蠕动不象过早疲劳那样普遍。
轴承的蠕动是由于轴和内圈之间的间隙过大造成的。
蠕动的害处很大,它不仅损害轴承,也破坏其他零件。
蠕动的明显特征是划痕、擦痕或轴与内圈的颜色变化。
为了防止蠕动,应该先用肉眼检查一下轴承箱件和轴的配件。
蠕动与安装不正有关。
如果轴承圈不正或翘起,滚珠将沿着一个非圆周轨道运动。
这个问题是由于安装不正确或公差不正确或轴承安装现场的垂直度不够造成的。
如果偏斜超过0.25°,轴承就会过早地失效。
检查润滑剂的污染比检查装配不正或蠕动要困难得多。
污染的特征是使轴承过早的出现磨损。
润滑剂中的固体杂质就象磨粒一样。
如果滚珠和保持架之间润滑不良也会磨损并削弱保持架。
在这种情况下,润滑对于完全加工形式的保持架来说是至关重要的。
相比之下,带状或冠状保持架能较容易地使润滑剂到达全部表面。
锈是湿气污染的一种形式,它的出现常常表明材料选择不当。
如果某一材料经检验适合工作要求,那么防止生锈的最简单的方法是给轴承包装起来,直到安装使用时才打开包装。
2 避免失效的方法解决轴承失效问题的最好办法就是避免失效发生。
这可以在选用过程中通过考虑关键性能特征来实现。
这些特征包括噪声、起动和运转扭矩、刚性、非重复性振摆以及径向和轴向间隙。
扭矩要求是由润滑剂、保持架、轴承圈质量(弯曲部分的圆度和表面加工质量)以及是否使用密封或遮护装置来决定。
润滑剂的粘度必须认真加以选择,因为不适宜的润滑剂会产生过大的扭矩,这在小型轴承中尤其如此。
另外,不同的润滑剂的噪声特性也不一样。
举例来说,润滑脂产生的噪声比润滑油大一些。
因此,要根据不同的用途来选用润滑剂。
在轴承转动过程中,如果内圈和外圈之间存在一个随机的偏心距,就会产生与凸轮运动非常相似的非重复性振摆(NRR)。
保持架的尺寸误差和轴承圈与滚珠的偏心都会引起NRR。
和重复性振摆不同的是,NRR是没有办法进行补偿的。
在工业中一般是根据具体的应用来选择不同类型和精度等级的轴承。
例如,当要求振摆最小时,轴承的非重复性振摆不能超过0.3微米。
同样,机床主轴只能容许最小的振摆,以保证切削精度。
因此在机床的应用中应该使用非重复性振摆较小的轴承。
在许多工业产品中,污染是不可避免的,因此常用密封或遮护装置来保护轴承,使其免受灰尘或脏物的侵蚀。
但是,由于轴承内外圈的运动,使轴承的密封不可能达到完美的程度,因此润滑油的泄漏和污染始终是一个未能解决的问题。
一旦轴承受到污染,润滑剂就要变质,运行噪声也随之变大。
如果轴承过热,它将会卡住。
当污染物处于滚珠和轴承圈之间时,其作用和金属表面之间的磨粒一样,会使轴承磨损。
采用密封和遮护装置来挡开脏物是控制污染的一种方法。
噪声是反映轴承质量的一个指标。
轴承的性能可以用不同的噪声等级来表示。
噪声的分析是用安德逊计进行的,该仪器在轴承生产中可用来控制质量,也可对失效的轴承进行分析。
将一传感器连接在轴承外圈上,而内圈在心轴以1800r/min的转速旋转。
测量噪声的单位为anderon。
即用um/rad表示的轴承位移。
根据经验,观察者可以根据声音辨别出微小的缺陷。
例如,灰尘产生的是不规则的劈啪声;滚珠划痕产生一种连续的爆破声,确定这种划痕最困难;内圈损伤通常产生连续的高频噪声,而外圈损伤则产生一种间歇的声音。
轴承缺陷可以通过其频率特性进一步加以鉴定。
通常轴承缺陷被分为低、中、高三个波段。
缺陷还可以根据轴承每转动一周出现的不规则变化的次数加以鉴定。
低频噪声是长波段不规则变化的结果。
轴承每转一周这种不规则变化可出现1.6~10次,它们是由各种干涉(例如轴承圈滚道上的凹坑)引起的。
可察觉的凹坑是一种制造缺陷,它是在制造过程中由于多爪卡盘夹的太紧而形成的。
中频噪声的特征是轴承每旋转一周不规则变化出现10~60次。
这种缺陷是由在轴承圈和滚珠的磨削加工中出现的振动引起的。
轴承每旋转一周高频不规则变化出现60~300次,它表明轴承上存在着密集的振痕或大面积的粗糙不平。
利用轴承的噪声特性对轴承进行分类,用户除了可以确定大多数厂商所使用的ABEC标准外,还可确定轴承的噪声等级。
ABEC标准只定义了诸如孔、外径、振摆等尺寸公差。
随着ABEC级别的增加(从3增到9),公差逐渐变小。
但ABEC等级并不能反映其他轴承特性,如轴承圈质量、粗糙度、噪声等。
因此,噪声等级的划分有助于工业标准的改进。
为了延长轴承的使用寿命,要注重工业轴承的保养、检修、以求防事故于未然,确保运转的可靠性,提高生产性、经济性。
保养最好相应机械运转条件的作业标准,定期进行。
内容包括监视运转状态、补充或更换润滑剂、定期拆卸的检查。
作为运转中的检修事项,有轴承的旋转音、振动、温度、润滑剂的状态等等。
1、轴承的清洗:拆卸下轴承检修时,首先记录轴承的外观,确认润滑剂的残存量,取样检查用的润滑剂之后,洗轴承。
作为清洗剂,普通使用汽油、煤油。
拆下来的轴承的清洗,分粗清洗和细清洗,分别放在容器中,先放上金属的网垫底,使轴承不直接接触容器的脏物。