《设备故障诊断》知识点汇总
设备故障诊断要点

第二节 设备故障诊断技术 及其实施过程
(三)按照按诊断的直接对象分类
各种不同的对象,诊断方法、诊断的技术、诊断的设备都有 很大区别,按照机械零件、液压系统、旋转机械、往复机械 、工程结构等来进行区分。
表7-3
诊断技术名称 机械零件诊断技术 液压系统诊断技术 旋转机械诊断技术 往复机械诊断技术 工程结构诊断技术 工艺流程诊断技术 生产系统诊断技术 电器设备诊断技术
绝对判断标准是根据对某类机器长期使用、观察、维 修与测试后的经验总结 , 并由企业、行业协会或国家归纳 成表格或图表形式 ,作为一种标准供工程界应用。该标准 是在确定了正确的诊断方法后才可制定的标准。使用时 必须注意判断标准的制定及适用的范围等,才能选用。
(2)相对判断标准
相对判断标准是对机器的同一部位定期测定,并按时 间先后进行比较,以正常情况下的值为初始值。根据实 测值与该值的倍数比来进行判断的方法。
第一节
环境因 素 机械能 主要影响
设备故障概述
典型故障
表7-1 环境影响及引起的故障
产生振动、冲击、压力、 机械强度降低、功能受影响、磨损加剧、 加速度、机械应力等 过量变形、疲劳破坏、机件断裂 产生热老化、氧化、软 电气性能变化、润滑性能降低、机械应 化、熔化、粘性变化、固 力增加、磨损加剧、机械强度降低、腐蚀 化、脆化、热胀冷缩及热 加速、热疲劳破坏、密封性能破坏 应力等 产生受潮、干燥、脆化、 功能受影响、电气性能下降、机械性 腐蚀、电蚀、化学反应及 能降低、保护层损坏、表面变质、化学反 污染等 应加剧、机械断裂 产生脆化、加热、蜕化、 表面变质、材料褪色、热老化、氧化、 电离及磁化 材料的物理、化学、电气性能发生变化
第二节 设备故障诊断技术 及其实施过程
设备故障诊断内容模版
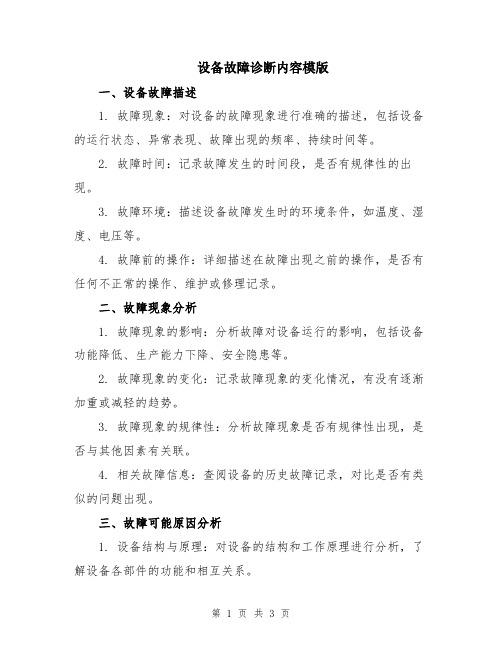
设备故障诊断内容模版一、设备故障描述1. 故障现象:对设备的故障现象进行准确的描述,包括设备的运行状态、异常表现、故障出现的频率、持续时间等。
2. 故障时间:记录故障发生的时间段,是否有规律性的出现。
3. 故障环境:描述设备故障发生时的环境条件,如温度、湿度、电压等。
4. 故障前的操作:详细描述在故障出现之前的操作,是否有任何不正常的操作、维护或修理记录。
二、故障现象分析1. 故障现象的影响:分析故障对设备运行的影响,包括设备功能降低、生产能力下降、安全隐患等。
2. 故障现象的变化:记录故障现象的变化情况,有没有逐渐加重或减轻的趋势。
3. 故障现象的规律性:分析故障现象是否有规律性出现,是否与其他因素有关联。
4. 相关故障信息:查阅设备的历史故障记录,对比是否有类似的问题出现。
三、故障可能原因分析1. 设备结构与原理:对设备的结构和工作原理进行分析,了解设备各部件的功能和相互关系。
2. 设备使用状况:分析设备的使用状况,包括设备的运行时间、工作负荷、维护保养情况等。
3. 设备部件检查:检查设备各部件是否存在异常情况,如松动、脱落、损坏等。
4. 设备参数检查:检查设备参数是否正常,如电压、电流、温度、压力等,与设备规格进行对比。
5. 相关设备对比:对比其他相同型号设备的使用情况,是否有类似问题出现。
6. 设备软件检查:检查设备软件是否存在故障,如程序错误、设置问题等。
四、故障排除与解决方案1. 解决方案的确定:根据故障原因分析结果,制定相应的解决方案,包括更换部件、调整参数、修复软件等。
2. 故障排除步骤:按照解决方案的步骤进行故障排除,记录每一步的操作和结果。
3. 故障排除过程中的注意事项:记录故障排除过程中需要特别注意的事项,如安全操作、避免二次损坏等。
4. 故障排除的结果评估:对故障排除后的设备进行测试和评估,确认故障是否已经解决。
五、故障修复和预防措施1. 故障修复记录:详细记录故障修复的过程和结果,包括更换的部件、修复的软件等。
设备故障诊断内容

设备故障诊断内容设备故障诊断是指通过一系列的步骤和方法,对发生故障设备进行分析和判断,找出故障原因,并根据分析结果进行修复和维护的过程。
设备故障诊断是维修过程中非常重要的一环,它直接关系到维修的效率和质量。
设备故障诊断通常包括以下几个步骤:1. 收集故障信息2. 分析故障现象3. 确定可能的故障原因4. 进一步验证和确认故障原因5. 制定修复方案6. 执行修复方案7. 验证修复效果8. 编写故障报告下面将详细介绍每个步骤的内容。
1. 收集故障信息在进行设备故障诊断之前,需要首先收集相关的故障信息。
这些信息可以包括故障现象的描述、故障出现的频率和时间、故障引起的影响等。
收集故障信息的目的是为了进一步分析和研究故障原因,并为后续的故障诊断提供依据。
2. 分析故障现象在收集了足够的故障信息之后,需要对故障现象进行分析。
分析故障现象的目的是通过比对实际现象与设备正常工作状态之间的差异,进一步确定故障出现的具体位置和可能的原因。
这个步骤需要仔细观察和检查设备的各个部位,并记录下可能存在问题的地方。
3. 确定可能的故障原因在分析故障现象的基础上,可以初步确定故障的可能原因。
可能的故障原因可以根据故障现象的特点和设备的工作原理来推断。
这个过程需要运用专业的知识和经验,并参考设备的相关文档和资料。
4. 进一步验证和确认故障原因在确定了可能的故障原因之后,需要进行进一步的验证和确认。
可以通过排除法来验证不同的故障原因,并通过实际的测试和观察来确认故障是否存在。
这个过程可能需要使用特殊的测试设备和工具,并进行一系列的操作和调整。
5. 制定修复方案在确认了故障原因之后,需要制定相应的修复方案。
修复方案应该明确具体的步骤和操作,并考虑到修复的可行性和安全性。
在制定修复方案时,还需要考虑到设备的可维修性和经济性,以便选择最合适的修复方法。
6. 执行修复方案在制定了修复方案之后,可以进行实际的修复操作。
修复操作需要按照制定的步骤进行,并注意操作的细节和安全措施。
设备故障诊断内容

设备故障诊断内容设备故障诊断与一般监测、监控系统的区别主要在于系统的软件方面,它不仅能监测设备运行的参数,而且能根据监测结果进行评价,分析设备的故障类型与原因。
它是将监测、控制、评价融为一体的系统。
它的软件主要功能是:①信号采集和处理软件,采集合适的信号样本,对其进行各种分析处理,提取和凝聚故障特征信息,提高诊断的灵敏度和可靠度。
②故障诊断和状态评价软件,对信号分析处理结果进行比较、判断,依据一定的判别规则得出诊断结论。
或是由系统自动地诊断出状态的水平和各种故障存在的倾向性及严重性;或是帮助工程技术人员结合其他条件全面作出判断或决策。
对于设备的诊断,一是防患于未然,早期诊断;二是诊断故障,采取措施。
其主要内容包括:(1)正确选择与测取设备有关状态的特征信号所测取的信号应该包含设备有关状态的信息,例如,诊断起重机桁架有无裂纹不能靠测取桁架各点温度来判定,因温度信号中不包含裂纹有无的信息。
而测取桁架的振动信号则可达到目的,因为振动信号中包含了结构有无裂纹的信息,这种信号即称为特征信号。
(2)正确地从特征信号中提取设备有关状态的有用信息(征兆)从特征信号直接判明设备状态的有关情况,查明故障的有无,一般是比校难的。
例如,从结构的振动信号一般难以直接判明结构有无裂纹,还需根据振动理论、信号分析理论、控制理论等提供的理论与方法,加上试验研究,对特征信号加以处理,提取有用的信息(称为征兆),才有可能判明设备的有关状态。
征兆信息包括结构的物理参数(如质量、刚度等)、结构的模态参数(如固有频率、模态阻尼等),设备的工作特性(如耗油率、工作转速、功率等),信号统计特性及其他特征量。
(3)根据征兆进行设备的状态诊断一般很难直接采用征兆来进行设备的状态诊断,识别设备的状态。
因此,可采用多种模式识别理论与方法,对征兆加以处理,构成判别准则,进行状态的识别与分类。
状态诊断是设备诊断的重点,而特征信号与征兆的获取正确与否,则是能否进行正确状态诊断的前提。
设备故障诊断

设备故障诊断
对于设备故障诊断,可以按照以下步骤进行:
1. 观察和收集信息:首先需要观察设备故障的现象和表现,并且收集相关的信息,例如设备的历史记录、使用情况、
维护记录等。
2. 分析现象和问题:根据观察到的现象和收集到的信息,
分析设备故障的可能原因,可以先进行一些简单的排查,
例如检查设备的电源是否接通、检查连接线是否松动等。
3. 测试和验证:根据可能的原因,进行一系列测试和验证,以确定故障的具体原因。
这可能包括使用测试仪器、测量
设备的电压、电流、温度等数据,以及进行其他适当的测试。
4. 确定故障原因:根据测试和验证的结果,确定设备故障
的具体原因。
可能的原因包括电路故障、机械故障、软件
故障等。
5. 解决故障:根据故障的具体原因,采取相应的措施来解
决故障。
这可能涉及更换损坏的零件、修复电路、重装软
件等。
6. 预防措施:在解决故障后,需要采取一些预防措施,以
防止类似的故障再次发生。
这可能包括定期检查设备、维
护设备、进行培训和指导等。
需要注意的是,设备故障诊断需要具备相关的知识和技能,如果遇到复杂的故障或者不确定如何处理时,建议寻求专
业人士的帮助。
《设备故障诊断》知识点汇总

1.1.设备故障诊断的含义设备故障诊断是指应用现代测试分析手段和诊断理论方法,对运行中的机械设备出现故障的机理、原因、部位和故障程度进行识别和诊断,并且根据诊断结论,确定设备的维修方案和防范措施。
1.2.设备故障诊断的过程信号采集→信号处理→故障诊断→诊断决策→故障防治与控制1.3.设备故障诊断的特性多样性、层次性、多因素相关性、延时性、不确定性1.4.三种维修制度事后维修(故障维修)、定期维修(计划维修)、状态监测维修(预知性维修)1.5设备故障的类型有哪些①结构损伤性故障(裂纹、磨损、腐蚀、变形、断裂、剥落和烧伤)②运动状态劣化性故障(机械位置不良、刚性不足、摩擦、流体激振非线性的谐波共振)1.6设备故障诊断的功能①不停机不拆卸的状态下检测②可预测设备的可靠性程度③确定故障来源,提出整改措施1.7.设备状态监测与故障诊断的技术和方法振动信号监测诊断技术(普遍性、信息量丰富、易处理与分析)声信号监测诊断技术(声音监听法、频谱分析法、声强法)温度信号监测诊断技术润滑油的分析诊断技术其他无损检测诊断技术1.8.设备故障状态的识别方法信息比较诊断法、参数变化诊断法、模拟试验诊断法、函数诊断法、故障树分析诊断法、模糊诊断法、神经网络诊断法、专家系统2.1信号的含义和分类信号是表征客观事物状态或行为信息的载体分类:确定性信号与非确定性信号;连续信号和离散信号;能量信号和功率信号;时限与频限信号2.2.信号时域分解直流分量和交流分量脉冲分量实部分量和虚部分量正交函数分量2.3.信号的时域统计均值均方值方差2.4.时域相关分析相关系数:2.5.频谱分析法利用傅里叶变换的方法对振动的信号进行分解,并按频率顺序展开,使其成为频率的函数,进而在频率域中对信号进行研究和处理的一种过程,称为频谱分析2.6.振动监测的基本参数振幅、频率、相位2.7.旋转机械常用的振动信号处理图形轴心轨迹:轴颈中心相对于轴承座在轴线垂直平面内的运动轨迹转子振型:转子轴线上各点的振动位移所连成的一条空间曲线轴颈涡动中心位置:在滑动轴承中,轴颈中心在激扰力作用下是绕着某一中心点运动的波特图:描述转子振幅和相位随转速变化的关系曲线,纵坐标为振幅和相位,横坐标为转子的转速或转速频率极坐标图:把转子的振幅与相位随转速的变化关系用极坐标的形式表示出来(直观,方便,清晰,抗干扰)三维坐标图(级联图、瀑布图):随转速上升,机械振动的基础幅指上升阶比谱分析:将频谱图上横坐标的每个频率值除以某个参考频率值(读数清晰、周期采样、精度高)3.1旋转机械的故障类型有哪些①转自不平衡②转子不对中③滑动轴承故障④转子摩擦⑤浮动环密封故障3.2转子不平衡的概念转子受材料质量、加工、装配以及运行中多种因素的影响,其质量中心和旋转中心线中间存在一定量的偏心距,使得转子在工作时形成周期性的离心力干扰,在轴承上产生动载荷,从而引起机器振动的现象不平衡产生的离心力大小3.3转子不平衡振动的故障特征①不平衡故障主要引起转子或轴承径向振动,在转子径向测点上得到的频谱图,转速频率成分具有突出的峰值②单纯的不平衡振动,转速频率的高次谐波幅值很低,因此在时域上的波形是一个正弦波③转子的轴心轨迹形状基本上为一个圆或者椭圆,这意味着置于转轴同一截面上相互垂直的两个探头,其信号相位差接近90°④转子的进动方向为同步正进动⑤除了悬臂转子外,对于普通两端支撑的转子,不平衡在轴向上的振幅一般不明显⑥转子振幅对转速变化很敏感,转速下降,振幅将明显下降3.4转子不平衡振动的原因①固有质量不平衡(设计错误、材料缺陷、加工与装配误差、动平衡方法不正确)②转子运行中的不平衡(转子弯曲、转子平衡状态破坏)3.5怎样区别转子弯曲不平衡和质量不平衡①振幅随转速的变化:质量不平衡与转速之间按照固定的关系式变化,弯曲的没有固定的②相位随转速的变化:质量的相位处于变动中,弯曲的基本不变③振幅随负荷变化:质量的振动不随负荷变化,弯曲的会3.6转子不对中故障的特征①改变了轴承中的油膜压力②轴承的振动幅值随转子负荷的增大而增高③平行不对中主要引起径向振动④不对中使刚性联轴节两侧的转子振动产生相位差⑤从振动频率上分析,不同类型的转子和不同形式的不对中情况引起的振动频率是不相同的⑥大型涡轮机械上多跨转子的不对中,一般伴随有其他故障因素,因而振动情况更为复杂⑦转子之间的不对中,由于在轴承不对中方向上产生了一个预加载荷,轴颈运动的轴心轨迹形状为椭圆形,随着预加载荷的增大,轨迹形状将变为香蕉形、“8”字形或外圈中产生一个内圈等形状3.7转子不对中故障的原因①初始安装对中超差②冷态对中时没有正确估计各个转子中心线的热态升高量,工作时出现主动转子与从动转子动态对中不良③轴承架热膨胀不均匀④管道力作用⑤机壳变形或移位⑥地基不均匀下沉⑦基础变形⑧转子弯曲,同时产生不平衡和不对中故障3.8不对中故障的监测方法①静态检测法(打表发、激光对中法、联轴节表面状态检测法)②动态监测法(振动诊断法、激光对中法、Dodd棒测量法、电涡流绝对值测量法、轴承油膜压力测量法)3.9滑动轴承常见故障的原因和防治措施①巴氏合金松脱(重新浇注)②轴承异常磨损、刮伤、拉毛(轴承装配缺陷、轴承加工误差、转子发生大振动、止推轴承设计误差、供油系统问题)③轴承疲劳(轴承比压合适、轴承间隙合适、用薄的巴氏合金、控制轴瓦温度)④轴承腐蚀⑤轴承气蚀⑥轴承壳体松动⑦轴承间隙不适当⑧轴承温度过高3.10油膜振荡的概述高速滑动轴承的一种特有故障,由油膜力产生的自激振动,转子发生油膜振荡时输入的能量很大,足以引起转子轴承系统零部件的损坏3.11油膜振荡的机理和特点是轴颈涡动运动与转子自振频率相吻合时发生的大幅度共振现象,其特点往往是来势很猛,瞬时间振幅突然升高,很快发生局部油膜破裂,引起轴颈与轴瓦之间摩擦,发出强烈的吼叫声,将严重损坏轴承和转子3.12轴承发生油膜振荡的故障特征①油膜振荡是一种自激振动,维持振动的能量是由轴本身在旋转中产生,它不受外部激励力的影响②高速轻载转子,发生油膜振荡的转速总是高于转子系统的一阶临界转速二倍以上③油膜振荡是一种非线性的油膜共振④轴心轨迹形状紊乱、发散,很多不规则的轨迹叠加成花瓣形状⑤由于转子发生激烈的自激振动,引起轴承油膜破裂,因而会同时发生轴颈和轴瓦的碰撞摩擦,时而发生巨大的吼叫声⑥惯性现象:当转子转速一旦进入油膜共振区,升高转速,振荡频率不变,振幅并不下降3.13油膜不稳定的防止措施①避开油膜共振区域②增加轴承比压③减小轴承间隙④控制适当的轴瓦预负荷⑤选用抗振性好的轴承⑥调整油温4.1往复式压缩机的故障类型与故障原因①压缩机热力参数异常(排气量降低、吸排气压力不正常、温度不正常、工况的改变、油路故障)②压缩机主要零部件的机械故障(气阀故障、活塞杆断裂、连杆螺栓断裂、曲轴断裂、活塞卡住、咬住或撞裂)③压缩机故障振动/动力学故障(曲柄连杆机构的运动惯性力、压缩机故障振动(汽缸、机体和基础振动)和不正常声音(运动机构、汽缸、吸气阀、排气阀故障)4.2气阀故障的形式①阀片损坏②弹簧折断③气阀漏气4.3气阀故障监测和诊断的方法①阀盖安装传感器获得振动信号或噪声信号②在阀室安装位移传感器监测阀片运动规律信号③用P-V示功图监测④测量吸、排气腔内的脉动压力和温度变化4.4压力脉动给压缩机带来哪些不利影响①可能使压缩机的指示功率增加②降低气阀的使用寿命③使得排气量增大或者减小④破坏安全阀的严密性⑤引起管道和设备的振动4.5管道压力脉动的防治措施①采用合理的吸排气顺序②装设缓冲器③装设声学滤波器④装设孔板⑤配置合适的集气管⑦避免管道中气流方向和流速的突变4.6管道机械共振的原因气流压力脉动引起气柱共振以及任何一种激振力4.7管道机械共振的诊断方法①测试方法②计算方法4.8管道机械共振的防治措施①改变支撑条件②采用动力减振器5.1齿轮常见的故障①齿的断裂(疲劳断裂和过负荷断裂)②齿的磨损(粘着磨损、磨粒磨损、腐蚀磨损)③齿面疲劳(点蚀、剥落)④齿面擦伤和划痕5.2齿轮主要的常规激励和故障激励①刚度激励②传动误差(制造误差、装配误差、轮齿损伤误差、外部激励误差)③啮合冲击④节线冲击5.3齿轮故障的特征①啮合频率及其谐波成分②幅值调制和频率调制所形成的边频带③由齿轮转速频率的低次谐波所构成的附加脉冲④由齿轮加工误差形成的隐含成分5.4倒频谱的含义功率谱对数的功率谱(傅里叶逆变换),即把时间信号x(t)的功率谱函数G(f)取对数,再进行傅里叶变换,其表达式为5.5倒频谱的优点①有效的提取和识别频谱上的周期成分②受传输途径的影响很小5.6齿轮故障的诊断方法①细化谱分析法②倒频谱分析法③时域同步平均法④自适应消噪技术(振动信号诊断)⑤噪声诊断6.1为什么说滚动轴承是最易损坏的承受冲击的能力差,在冲击载荷下容易发生故障、滚动轴承在滚动体上的载荷分布不均匀,在载荷线下面的一个滚动体受力最大,内圈和外圈上各点所受的应力和应力循环次数不同6.2滚动轴承的故障形式转速n<1r/min————塑性变形转速n>10r/min————疲劳剥落(点蚀)、磨粒磨损、裂纹和断裂、压痕、腐蚀、电蚀、胶合(粘着)、微动磨损、烧损6.3滚动轴承故障的检测方法根据轴承的振动和声音检测根据轴承的温度或润滑油的温度检测根据轴承的磨损颗粒检测根据轴承的间隙变化检测根据轴承中的油膜电阻变化检测6.4引起滚动轴承振动的原因外部激励因素:转子的不平衡、不对中、流体激励、结构共振等震动传递本身内部原因:Ⅰ由于轴承结构本身引起的振动①滚动体通过载荷方向产生的振动②套圈的固有振动③轴承弹性特性引起的振动Ⅱ由于轴承形状和精度问题引起的振动①套圈、滚道和滚动体波纹度引起的振动②滚动体大小不均匀和内外圈偏心引起的振动Ⅲ由于轴承使用不正当或装配不正确引起的振动①滚道接触表面局部性缺陷引起的振动②润滑不良,由摩擦引起的振动③装配不正确,轴颈偏斜产生的振动6.5轴承故障引发的激振力有哪些①波形随机,杂乱无章②激励力为尖峰形的脉冲波③激励稳态,成正弦波6.6轴承振动信号中频率域的特点①频谱具有宽频带特性,并且随着缺陷的种类、形状、轴承尺寸和转速而变化三频段:0~20kHz,转子和轴承的故障特性频率(不对中、不平衡)20~60kHz,轴承其他元件的固有频率大于60kHz,属于声发射范围(润滑不良、胶合、剥落裂纹)6.7轴承故障振动检测技术和诊断方法①低频信号接收法②冲击脉冲法(SP M)③共振解调法④光纤传感器技术⑤电涡流传感器技术7.1油样分析技术的概述通过对油液的采样和分析处理,取得设备各摩擦副的磨损状况信息,从而对设备所处工作状态作出科学的判断。
技能培训资料:设备故障判断

一、描述故障的特征参量1 .设备或部件的输出参数设备的输出与输入的关系以及输出变量之间的关系都可以反映设备的运行状态。
2 .设备零部件的损伤量变形量、磨损量、裂纹以及腐蚀情况等都是判断设备技术状态的特征参量。
3 .设备运转中的二次效应参数主要是设备在运行过程中产生的振动、噪声、温度、电量等。
设备或部件的输出参数和零部件的损伤量都是故障的直接特征参量而二次效应参数是间接特征参量。
使用间接特征参量进行故障诊断的优点是,可以在设备运行中并且无需拆卸的条件下进行。
不足之处是间接特征参量与故障之间的关系不是完全确定的。
二、故障诊断的实施过程1 .状态监测通过传感器采集设备在运行中的各种信息,将其转变为电信号或其它物理量,再将获取的信号输入到信号处理系统进行处理。
2 .分析诊断根据监测到的能够反映设备运行状态的征兆或特征参数的变化情况或将征兆与模式进行比较,来判断故障的存在、性质、原因和严重程度以及发展趋势。
3 .治理预防根据分析诊断得出的结论确定治理修正和预防的办法。
状态监测是故障诊断的基础和前提;故障诊断是对监测结果的进一步分析和处理,诊断是目的。
三、振动测量根据能否用确定的时间关系函数来描述振动分为确定性振动和随机振动。
1.振动的基本参数(1)振幅:振动体或质点距离平衡位置的幅度。
(2)频率:每秒振动的次数,用HZ表示。
(3)周期:振动一次所需要的时间,频率和周期互为倒数。
(4)相位:表示振动部分相对与其他振动部分或固定部分所处的位置。
2 .振动位移对时间的一阶导数是速度、速度对时间的一阶导数是加速度加速度对时间积分得速度、速度对时间积分得位移。
因此,位移、速度、加速度这三者,只要测得其中之一,即可通过微分积分的关系求出另外的两个物理量。
3 .常用的测振传感器(结构和应用)压电加速度传感器是基于压电晶体的压电效应工作的,压电式加速度计无需外电源,属于能量转换型传感器。
它由压紧弹簧、质量块、压电晶片和基座等部分组成,其中,压电晶片是加速度计的核心,压电晶体输出电荷与振动的加速度成正比,灵敏度高而且稳定。
设备故障诊断

设备故障诊断作为现代社会不可或缺的重要设备,各种机械设备的运作稳定与否对生产效率、安全生产等方面都有着至关重要的影响。
然而随着科技的不断发展,设备硬件的复杂性和软件的庞大性呈现增长趋势,设备故障的诊断和维修变得更加复杂和困难。
本文将针对日常生产设备故障诊断问题进行探讨,探讨如何快速准确的找出故障原因并进行维护。
一、设备故障发现任何机器设备的故障都会在一定时间内逐渐形成,因此第一步便是选择故障检测的时间。
如果你想监视某一特定部件的故障条件,可以选择在该部件容易故障的时间检测。
例如,当工厂正在进行切割或负荷测试时检测,有助于确定是否存在过载或过热故障产生的风险。
其次,需要正确记录故障的标志和间隔。
记住标志和间隔,能帮助你随时追踪设备故障和预警。
最后,也必须了解措施的使用周期,这将有助于确定许多部件的故障,并减少寻找可能原因的时间。
二、设备故障的判断方法在确立故障现象后,应确认故障的部位。
通常,由于某部件的故障结果导致产品质量下降,故障原因可从减少产品质量的部件开始。
可以将故障原因分为以下类型:1.硬件故障:这是最普遍、最显而易见的故障类型,通常用于检查部件或机器本身有问题。
2.软件故障:如程序、固件、电机驱动器、检测设备和触发设备等部件。
这种故障类型往往需要通过现场操作进行故障诊断,重新加载或调整软件功能。
3.供电故障:这是设备故障的最常见原因之一。
虽然产品的部件本身没有故障,但如果部件没有得到足够的电力,则可能导致机器运转不稳定或无法正常工作。
三、设备故障的解决当故障原因明确后,下一步是执行正确的解决方案。
在许多情况下,保养可能是最简单、最有效的解决方案。
如果部件洁净,有规律地进行维护,就可能减少损坏机器的风险。
此外,一些简单的修理操作可能会解决问题。
例如,更换烧坏的保险丝或重新拧紧松动的螺钉。
最后,如果部件很大或者故障的原因比较复杂,需要专业的技术人员进行处理,以确保工作的质量。
综上所述,设备故障诊断需要具备一定的技术和实践能力。
- 1、下载文档前请自行甄别文档内容的完整性,平台不提供额外的编辑、内容补充、找答案等附加服务。
- 2、"仅部分预览"的文档,不可在线预览部分如存在完整性等问题,可反馈申请退款(可完整预览的文档不适用该条件!)。
- 3、如文档侵犯您的权益,请联系客服反馈,我们会尽快为您处理(人工客服工作时间:9:00-18:30)。
1.1.设备故障诊断的含义设备故障诊断是指应用现代测试分析手段和诊断理论方法,对运行中的机械设备出现故障的机理、原因、部位和故障程度进行识别和诊断,并且根据诊断结论,确定设备的维修方案和防范措施。
1.2.设备故障诊断的过程信号采集→信号处理→故障诊断→诊断决策→故障防治与控制1.3.设备故障诊断的特性多样性、层次性、多因素相关性、延时性、不确定性1.4.三种维修制度事后维修(故障维修)、定期维修(计划维修)、状态监测维修(预知性维修)1.5设备故障的类型有哪些①结构损伤性故障(裂纹、磨损、腐蚀、变形、断裂、剥落和烧伤)②运动状态劣化性故障(机械位置不良、刚性不足、摩擦、流体激振非线性的谐波共振)1.6设备故障诊断的功能①不停机不拆卸的状态下检测②可预测设备的可靠性程度③确定故障来源,提出整改措施1.7.设备状态监测与故障诊断的技术和方法振动信号监测诊断技术(普遍性、信息量丰富、易处理与分析)声信号监测诊断技术(声音监听法、频谱分析法、声强法)温度信号监测诊断技术润滑油的分析诊断技术其他无损检测诊断技术1.8.设备故障状态的识别方法信息比较诊断法、参数变化诊断法、模拟试验诊断法、函数诊断法、故障树分析诊断法、模糊诊断法、神经网络诊断法、专家系统2.1信号的含义和分类信号是表征客观事物状态或行为信息的载体分类:确定性信号与非确定性信号;连续信号和离散信号;能量信号和功率信号;时限与频限信号2.2.信号时域分解直流分量和交流分量脉冲分量实部分量和虚部分量正交函数分量2.3.信号的时域统计均值均方值方差2.4.时域相关分析相关系数:2.5.频谱分析法利用傅里叶变换的方法对振动的信号进行分解,并按频率顺序展开,使其成为频率的函数,进而在频率域中对信号进行研究和处理的一种过程,称为频谱分析2.6.振动监测的基本参数振幅、频率、相位2.7.旋转机械常用的振动信号处理图形轴心轨迹:轴颈中心相对于轴承座在轴线垂直平面内的运动轨迹转子振型:转子轴线上各点的振动位移所连成的一条空间曲线轴颈涡动中心位置:在滑动轴承中,轴颈中心在激扰力作用下是绕着某一中心点运动的波特图:描述转子振幅和相位随转速变化的关系曲线,纵坐标为振幅和相位,横坐标为转子的转速或转速频率极坐标图:把转子的振幅与相位随转速的变化关系用极坐标的形式表示出来(直观,方便,清晰,抗干扰)三维坐标图(级联图、瀑布图):随转速上升,机械振动的基础幅指上升阶比谱分析:将频谱图上横坐标的每个频率值除以某个参考频率值(读数清晰、周期采样、精度高)3.1旋转机械的故障类型有哪些①转自不平衡②转子不对中③滑动轴承故障④转子摩擦⑤浮动环密封故障3.2转子不平衡的概念转子受材料质量、加工、装配以及运行中多种因素的影响,其质量中心和旋转中心线中间存在一定量的偏心距,使得转子在工作时形成周期性的离心力干扰,在轴承上产生动载荷,从而引起机器振动的现象不平衡产生的离心力大小3.3转子不平衡振动的故障特征①不平衡故障主要引起转子或轴承径向振动,在转子径向测点上得到的频谱图,转速频率成分具有突出的峰值②单纯的不平衡振动,转速频率的高次谐波幅值很低,因此在时域上的波形是一个正弦波③转子的轴心轨迹形状基本上为一个圆或者椭圆,这意味着置于转轴同一截面上相互垂直的两个探头,其信号相位差接近90°④转子的进动方向为同步正进动⑤除了悬臂转子外,对于普通两端支撑的转子,不平衡在轴向上的振幅一般不明显⑥转子振幅对转速变化很敏感,转速下降,振幅将明显下降3.4转子不平衡振动的原因①固有质量不平衡(设计错误、材料缺陷、加工与装配误差、动平衡方法不正确)②转子运行中的不平衡(转子弯曲、转子平衡状态破坏)3.5怎样区别转子弯曲不平衡和质量不平衡①振幅随转速的变化:质量不平衡与转速之间按照固定的关系式变化,弯曲的没有固定的②相位随转速的变化:质量的相位处于变动中,弯曲的基本不变③振幅随负荷变化:质量的振动不随负荷变化,弯曲的会3.6转子不对中故障的特征①改变了轴承中的油膜压力②轴承的振动幅值随转子负荷的增大而增高③平行不对中主要引起径向振动④不对中使刚性联轴节两侧的转子振动产生相位差⑤从振动频率上分析,不同类型的转子和不同形式的不对中情况引起的振动频率是不相同的⑥大型涡轮机械上多跨转子的不对中,一般伴随有其他故障因素,因而振动情况更为复杂⑦转子之间的不对中,由于在轴承不对中方向上产生了一个预加载荷,轴颈运动的轴心轨迹形状为椭圆形,随着预加载荷的增大,轨迹形状将变为香蕉形、“8”字形或外圈中产生一个内圈等形状3.7转子不对中故障的原因①初始安装对中超差②冷态对中时没有正确估计各个转子中心线的热态升高量,工作时出现主动转子与从动转子动态对中不良③轴承架热膨胀不均匀④管道力作用⑤机壳变形或移位⑥地基不均匀下沉⑦基础变形⑧转子弯曲,同时产生不平衡和不对中故障3.8不对中故障的监测方法①静态检测法(打表发、激光对中法、联轴节表面状态检测法)②动态监测法(振动诊断法、激光对中法、Dodd棒测量法、电涡流绝对值测量法、轴承油膜压力测量法)3.9滑动轴承常见故障的原因和防治措施①巴氏合金松脱(重新浇注)②轴承异常磨损、刮伤、拉毛(轴承装配缺陷、轴承加工误差、转子发生大振动、止推轴承设计误差、供油系统问题)③轴承疲劳(轴承比压合适、轴承间隙合适、用薄的巴氏合金、控制轴瓦温度)④轴承腐蚀⑤轴承气蚀⑥轴承壳体松动⑦轴承间隙不适当⑧轴承温度过高3.10油膜振荡的概述高速滑动轴承的一种特有故障,由油膜力产生的自激振动,转子发生油膜振荡时输入的能量很大,足以引起转子轴承系统零部件的损坏3.11油膜振荡的机理和特点是轴颈涡动运动与转子自振频率相吻合时发生的大幅度共振现象,其特点往往是来势很猛,瞬时间振幅突然升高,很快发生局部油膜破裂,引起轴颈与轴瓦之间摩擦,发出强烈的吼叫声,将严重损坏轴承和转子3.12轴承发生油膜振荡的故障特征①油膜振荡是一种自激振动,维持振动的能量是由轴本身在旋转中产生,它不受外部激励力的影响②高速轻载转子,发生油膜振荡的转速总是高于转子系统的一阶临界转速二倍以上③油膜振荡是一种非线性的油膜共振④轴心轨迹形状紊乱、发散,很多不规则的轨迹叠加成花瓣形状⑤由于转子发生激烈的自激振动,引起轴承油膜破裂,因而会同时发生轴颈和轴瓦的碰撞摩擦,时而发生巨大的吼叫声⑥惯性现象:当转子转速一旦进入油膜共振区,升高转速,振荡频率不变,振幅并不下降3.13油膜不稳定的防止措施①避开油膜共振区域②增加轴承比压③减小轴承间隙④控制适当的轴瓦预负荷⑤选用抗振性好的轴承⑥调整油温4.1往复式压缩机的故障类型与故障原因①压缩机热力参数异常(排气量降低、吸排气压力不正常、温度不正常、工况的改变、油路故障)②压缩机主要零部件的机械故障(气阀故障、活塞杆断裂、连杆螺栓断裂、曲轴断裂、活塞卡住、咬住或撞裂)③压缩机故障振动/动力学故障(曲柄连杆机构的运动惯性力、压缩机故障振动(汽缸、机体和基础振动)和不正常声音(运动机构、汽缸、吸气阀、排气阀故障)4.2气阀故障的形式①阀片损坏②弹簧折断③气阀漏气4.3气阀故障监测和诊断的方法①阀盖安装传感器获得振动信号或噪声信号②在阀室安装位移传感器监测阀片运动规律信号③用P-V示功图监测④测量吸、排气腔内的脉动压力和温度变化4.4压力脉动给压缩机带来哪些不利影响①可能使压缩机的指示功率增加②降低气阀的使用寿命③使得排气量增大或者减小④破坏安全阀的严密性⑤引起管道和设备的振动4.5管道压力脉动的防治措施①采用合理的吸排气顺序②装设缓冲器③装设声学滤波器④装设孔板⑤配置合适的集气管⑦避免管道中气流方向和流速的突变4.6管道机械共振的原因气流压力脉动引起气柱共振以及任何一种激振力4.7管道机械共振的诊断方法①测试方法②计算方法4.8管道机械共振的防治措施①改变支撑条件②采用动力减振器5.1齿轮常见的故障①齿的断裂(疲劳断裂和过负荷断裂)②齿的磨损(粘着磨损、磨粒磨损、腐蚀磨损)③齿面疲劳(点蚀、剥落)④齿面擦伤和划痕5.2齿轮主要的常规激励和故障激励①刚度激励②传动误差(制造误差、装配误差、轮齿损伤误差、外部激励误差)③啮合冲击④节线冲击5.3齿轮故障的特征①啮合频率及其谐波成分②幅值调制和频率调制所形成的边频带③由齿轮转速频率的低次谐波所构成的附加脉冲④由齿轮加工误差形成的隐含成分5.4倒频谱的含义功率谱对数的功率谱(傅里叶逆变换),即把时间信号x(t)的功率谱函数G(f)取对数,再进行傅里叶变换,其表达式为5.5倒频谱的优点①有效的提取和识别频谱上的周期成分②受传输途径的影响很小5.6齿轮故障的诊断方法①细化谱分析法②倒频谱分析法③时域同步平均法④自适应消噪技术(振动信号诊断)⑤噪声诊断6.1为什么说滚动轴承是最易损坏的承受冲击的能力差,在冲击载荷下容易发生故障、滚动轴承在滚动体上的载荷分布不均匀,在载荷线下面的一个滚动体受力最大,内圈和外圈上各点所受的应力和应力循环次数不同6.2滚动轴承的故障形式转速n<1r/min————塑性变形转速n>10r/min————疲劳剥落(点蚀)、磨粒磨损、裂纹和断裂、压痕、腐蚀、电蚀、胶合(粘着)、微动磨损、烧损6.3滚动轴承故障的检测方法根据轴承的振动和声音检测根据轴承的温度或润滑油的温度检测根据轴承的磨损颗粒检测根据轴承的间隙变化检测根据轴承中的油膜电阻变化检测6.4引起滚动轴承振动的原因外部激励因素:转子的不平衡、不对中、流体激励、结构共振等震动传递本身内部原因:Ⅰ由于轴承结构本身引起的振动①滚动体通过载荷方向产生的振动②套圈的固有振动③轴承弹性特性引起的振动Ⅱ由于轴承形状和精度问题引起的振动①套圈、滚道和滚动体波纹度引起的振动②滚动体大小不均匀和内外圈偏心引起的振动Ⅲ由于轴承使用不正当或装配不正确引起的振动①滚道接触表面局部性缺陷引起的振动②润滑不良,由摩擦引起的振动③装配不正确,轴颈偏斜产生的振动6.5轴承故障引发的激振力有哪些①波形随机,杂乱无章②激励力为尖峰形的脉冲波③激励稳态,成正弦波6.6轴承振动信号中频率域的特点①频谱具有宽频带特性,并且随着缺陷的种类、形状、轴承尺寸和转速而变化三频段:0~20kHz,转子和轴承的故障特性频率(不对中、不平衡)20~60kHz,轴承其他元件的固有频率大于60kHz,属于声发射范围(润滑不良、胶合、剥落裂纹)6.7轴承故障振动检测技术和诊断方法①低频信号接收法②冲击脉冲法(SP M)③共振解调法④光纤传感器技术⑤电涡流传感器技术7.1油样分析技术的概述通过对油液的采样和分析处理,取得设备各摩擦副的磨损状况信息,从而对设备所处工作状态作出科学的判断。
7.2常用的油样分析技术①光谱分析(SOA):原子吸收光谱测定法、原子发射光谱测定法、X射线荧光光谱测定法②铁谱分析③颗粒计数器④磁塞7.3声发射的概述材料在外载荷(如力、热、电、磁等)或内力的作用下以弹性波的形式释放应变能的现象7.4声发射信号传播过程声发射源→材料中传播→传感器耦合界面→传感器→声发射仪接收信号→信号处理→数据显示7.5声发射信号的表征参数①计数和计数率②幅度和幅度分布③声发射源定位7.6声发射检测仪器的作用①接收声发射信号②处理信号③显示声发射数据7.7声发射仪器的分类接收信号的通道数目:单通道、双通道、多通道7.8声发射检测的研究及应用领域①石油化工工业②电力工业③材料试验④民用工程⑤航天和航空工业⑥金属加工⑦交通运输业⑧其他8.1专家系统的概述专家系统是人工智能研究的一个分支,是一个拥有大量专业的计算机程序系统,它应用人工智能技术,根据专家提供的领域只是进行推理和判断,模拟人类专家的决策过程,解决那些只有人类专家才能解决的复杂问题8.2专家系统的结构知识库(基本事实、规则和其他有关信息)、推理机(核心)、人机接口8.3专家系统包括哪些基本问题专家系统是一个知识处理系统,包括知识的获取、表示(核心)和利用三个基本问题8.4常用的知识表示方法有哪些产生式表示、框架表示、谓词逻辑表示、过程表示8.5产生式表示的形式IF<条件>THE N<结论>8.6产生式系统的组成规则库、综合数据库、推理机(控制策略和推理方式)8.7产生式表示的优缺点优点:模块化、一致性、自然性缺点:推理效率低8.8专家系统的推理方式有哪些基于规则的推理(正向、反向和混合推理缺点:知识获取困难和推理脆弱性)基于模型的推理(缺点:推理效率低和系统模型难以建立)基于案例的推理(优点:知识获取容易、具有学习功能、适应力强、易接受;缺点:检索困难、不保证得到最佳方案)。