多轴联动系统耦合控制的分析与仿真
基于LabVIEW的多轴运动控制系统半实物仿真平台设计

基于LabVIEW的多轴运动控制系统半实物仿真平台设计基于LabVIEW的多轴运动控制系统半实物仿真平台设计摘要:随着工业自动化的不断发展,多轴运动控制系统在工业生产中的应用日益广泛。
为了提高系统的性能并减少实际试验中的风险与成本,本文设计了基于LabVIEW的多轴运动控制系统半实物仿真平台。
该平台通过软件仿真实现多轴运动控制的动态展示,使用户能够更直观地了解系统的工作原理以及调试参数。
本文首先介绍了多轴运动控制系统的基本原理和结构,然后详细阐述了平台的设计思路和实现过程,并通过实例验证了平台的可行性和有效性。
最后,对平台的不足之处进行了总结,并对未来的工作进行了展望。
关键词:多轴运动控制系统;半实物仿真平台;LabVIEW;动态展示;仿真实例1.引言多轴运动控制系统是一种广泛应用于机械加工、自动化生产等领域的高精度控制系统。
它通过控制驱动器和伺服电机来实现工作物体在多个轴向上的运动控制,可以实现较高的定位精度和运动速度,并且具有反馈控制的能力。
然而,为了确保系统的安全性和可靠性,在实际开发和试验中需要耗费大量的时间和资源。
因此,设计一种能够在实际试验之前对系统进行全面验证和调试的仿真平台具有重要的意义。
2.多轴运动控制系统的基本原理和结构多轴运动控制系统由伺服电机、传感器、运动控制器以及上位机等组成。
其中,伺服电机通过驱动器转换电能为机械能,可以控制物体的位置和速度。
传感器用于实时反馈物体的状态信息,如位置、速度和加速度等。
运动控制器是系统的核心部件,负责接收传感器的反馈信号,并通过控制算法生成合适的输出信号控制伺服电机。
上位机是用户与系统交互的界面,通过上位机可以输入运动参数和控制指令,实现运动轨迹的规划和控制。
3.基于LabVIEW的多轴运动控制系统半实物仿真平台设计为了满足对多轴运动控制系统进行全面仿真和调试的需求,本文设计了一种基于LabVIEW的半实物仿真平台。
该平台实现了具有动态展示功能的多轴运动控制系统的仿真,使用户能够更加直观地了解系统的工作原理和调试参数。
基于曲线插补的多轴联动交叉耦合控制方法

基于曲线插补的多轴联动交叉耦合控制方法赵国勇;赵玉刚【摘要】针对高精度轮廓跟踪需要,将曲线插补和交叉耦合控制器结合起来进行研究。
在每个采样周期根据各轴反馈的实际刀具位置与插补缓冲区中存储的一定数量的插补点,研究了一种"三点圆弧法"轮廓误差计算模型,并研究了轮廓误差补偿修正量计算及分配方法。
在数控试验台上跟踪一段三次非均匀有理B样条轮廓曲线,对比试验表明,所提出的基于曲线插补的轮廓误差交叉耦合控制方法能够有效减小轮廓误差,获得更高轮廓精度。
%Aiming at the tracking demand of high precision contour,the cross-coupled controller integrated with curve interpolation was studied.According to the real cutter positions from each axis feedback and the interpolation dots stored in the interpolation buffer in every sampling period,a "three-point arc approach" contour error computing model was developed.Moreover,the contour error compensated correction quantity computation and distribution approach was put forward.A cubic Non-Uniform Rational B-Spline Curve(NURBS)profile curve on the numerial control experiment table was tracked.The experiment results showed that the developed contour error cross-coupled control approach based on curve interpolation could effectively reduce contour error and obtain satisfactory contour precision.【期刊名称】《计算机集成制造系统》【年(卷),期】2011(017)009【总页数】5页(P1968-1972)【关键词】曲线插补;交叉耦合控制;轮廓误差;补偿修正量;机床【作者】赵国勇;赵玉刚【作者单位】山东理工大学精密制造与特种加工省级重点实验室,山东淄博255049;山东理工大学精密制造与特种加工省级重点实验室,山东淄博255049【正文语种】中文【中图分类】TH13数控机床轮廓精度的提高与机床各进给轴的动态特性是否匹配密切相关。
多轴联动系统耦合控制的分析与仿真

多轴联动系统耦合控制的分析与仿真摘要:建立了多轴联动系统的同步误差模型,将交叉耦合结构等效为一种带敏感函数的模型,并用以分析耦合控制器对交叉耦合系统性能的影响。
在Matlab/Simulink环境下对双轴和三轴交叉耦合系统进行仿真,验证了本文的分析结论。
关键词:多轴联动;交叉耦合;同步误差1 引言多轴联动系统广泛应用于各类精密机械加工、编织、缠绕及轧钢等机电一体化设备。
随着自动化水平及生产工艺要求的不断提高,现有控制方式已不能完全适应现代化生产的需要。
因此,研究开发高性能的多轴协调控制策略具有普遍的现实意义和广泛的应用前景。
现今的多轴联动系统存在两种较为典型的结构,一种是非耦合结构,另一种是交叉耦合结构[1]。
前者各个单轴控制系统独立运行,相互之间的控制没有任何电气上的连接,每台电机各自跟踪给定的位置信号,这种结构较为简单,但是当各轴的位置输出出现不同步时,仅能依靠单轴控制器来矫正误差,这种情况下同步误差较大,不能满足一些对同步性能要求较高的应用场合;交叉耦合控制结构是将各台电机输出的位置信号进行比较,从而得到一个同步误差补偿信号,再经过耦合控制器进行放大后分别前馈到单轴系统的输入端,各轴都修正本轴的状态以与其它轴实现快速同步,系统能够很好地抑制因某一台电机输出受到扰动而出现的同步误差,从而获得良好的同步控制精度[2-4]。
然而耦合结构中耦合控制器的增益受系统稳定性的限制不能设计得过大,否则会急剧恶化稳定性,因而设计耦合控制器时需要严格控制增益大小。
本文对双轴和三轴驱动系统进行了研究,根据工程实际定义了两种情况下同步误差的概念,然后推导了耦合环节引入前后同步误差的关系模型。
由这一关系模型分析了耦合控制器所起的作用,并探究了过大的增益对系统稳定性的具体影响。
最后,通过Matlab/Simulink环境下的仿真结果验证分析结论。
2双轴系统2.1 双轴同步误差模型在两电机联动实现位置轨迹控制的场合,X轴和Y轴的位移分别由两套电机系统执行,输出为两台电机转子位置角度,两台电机通过十字滑台或其他机械部件相连,将转子位置角度转换为X轴和Y轴的位移,共同实现被控制对象的二维运动轨迹。
基于滑模和PI的多轴转向系统交叉耦合控制

制。以 纵行转 向 为例仿真验证 了 控制算法的 有效性。
关键 词 :工程车辆 转 向系统i滑模控制i交叉耦合控制 中图分类号 :T 2 1 P 7. 4 文献标志码 :A 文章编号 :17 —7 8(0 00 —0 1 —6 6 3 102 1) 1 0 5
B in 0 9 , hn ) e'g1 1 1C ia j i 0
A b t a t a n o s u t n v hcewh c d p n e td v nb -xsse r g s tm stesu yp ooy e te s r c :T kig ac n t ci e il ih i i e e d n r e y 8 a i tei ys r o sn i n e a td r ttp , h h co sc u l g c n o ta g sd su sd t mp o ete c n o ra c rc . ekn mai n lsso r s-o p i o t l r t y i ic se o i r v o tu c u a y Th ie t a ay i fmut a i te ig n r s e h c l—x sse r i n s se n o ss n o pige rri to u e . c r igt ewo kn r il f lcr- y r ui e v e h ns , y tm a dc n it t u l ro i r d c e c n sn d Ac o d t r igp i p eo ee toh d a l s rom c a im n o h nc c
多机协同控制系统的建模与仿真

多机协同控制系统的建模与仿真近年来,随着工业自动化水平的不断提高,越来越多的机器人和自动化设备投入使用,这些设备具有独立的智能控制系统,但在某些应用场景下,需要多个设备协同完成任务。
因此,多机协同控制系统的设计和建模成为了近年来的研究热点之一。
本文将介绍多机协同控制系统的建模和仿真方法。
一、多机系统的基本构成多机协同控制系统是由多个单独的控制系统组成,通过通信或其他方式协同工作,完成特定的任务。
在多机系统中,每个独立的控制系统都可以看做是一个子系统,这些子系统之间通过信号或数据交换实现协同工作。
为了更好地理解多机协同控制系统的构成,我们先来了解一下单独控制系统的基本构成。
单独的控制系统包括三部分:传感器、执行机构和控制器。
传感器用于测量某些物理量,如温度、速度、角度等,将测量值转换成电信号后发送给控制器。
控制器对传感器采集的信号进行处理,根据预设的控制策略产生控制指令,将指令发送给执行机构。
执行机构将接收到的指令转换成机械运动或能量输出,实现对被控制对象的控制。
对于多机协同控制系统,其基本构成与单独控制系统类似,包括传感器、执行机构和控制器,但可能会涉及到网络通信模块和协同控制模块的设计。
二、多机协同控制系统的建模方法多机协同控制系统的建模方法有多种,其中最常用的是基于状态空间法的建模方法。
状态空间法是系统建模和分析中广泛使用的一种数学方法,其核心思想是将系统的输入、输出和状态转移关系用数学方程描述出来,然后将它们转化为矩阵形式,方便进行分析和求解。
在多机协同控制系统中,整个系统可以看做是若干个子系统的集合,每个子系统都有自己的输入、输出和状态。
因此,对于多机协同控制系统的建模,通常先建立子系统的状态方程,然后构建整个系统的状态方程,最后进行仿真和分析。
三、多机协同控制系统的仿真方法多机协同控制系统的仿真方法有多种,其中最常用的是基于MATLAB/Simulink的仿真方法。
MATLAB/Simulink是广泛应用于系统建模与仿真的软件平台,其提供了丰富的工具箱和函数库,能够方便地进行系统建模和仿真。
两轴变增益交叉耦合控制系统的仿真分析

·控制与检测·
文章编号: 1001 - 2265 ( 2010 ) 12 - 0080 - 03
ε= ( P xa - P xo ) 槡
2
善系统轮廓精度的实质是将系统开环的轮廓控制变 [9 ] 为闭环轮廓控制 。 变增益交叉耦合控制器是根据各运动轴的反馈 信息, 实时修正轮廓误差模型的增益, 以寻求最佳的 补偿律反馈到各轴, 从而达到及时补偿轮廓误差的 [6 ] Cx 和 Cy 取 目的 。即对于同一轮廓上的不同位置, 值不同。根据式( 4 ) ( 5 ) 设计变增益交叉耦合控制框 架如图 2 所示。
L = { ( x( t) , yt, t∈[ 0, 2 π]}
2
廓控制误差而采用变增益交叉耦合控制算法是有效 [9 ] 可取的, 且在机床数控系统中有良好的发展前景 。 已有的交叉耦合控制多是针对两轴系统, 而随着计 , 算机性能的提高和运算速度的大大加快 使得对两 轴以上耦合系统进行研究成为可能 。
) (
) (
) +…
2
忽略高阶项后得:
( 4)
— —电机与负载的转动惯量之和; 式中: J— kf — — —常值比例系数。
其中,
2
2. 1
变增益交叉耦合控制系统
轮廓误差定义
{
C x = sinθ -
Ex 2ρ
Ey C y = cosθ + 2ρ
( 5)
两轴控制系统在运行过程中存在两种误差: 跟 踪误差和轮廓误差。 跟踪误差是在某一时刻实际位 置与期望位置的距离, 轮廓误差则是实际轮廓与期 [5 ] 望轮廓的最短距离 。 两轴变增益交叉耦合控制系 统, 轮廓误 差 是 加 工 过 程 中 两 轴 相 互 作 用 生 成 的 。 曲线路径轮廓误差模型如图 1 所示。
《并联机构解耦机理研究与仿真分析》

《并联机构解耦机理研究与仿真分析》篇一一、引言随着工业自动化与机器人技术的不断发展,并联机构因其高精度、高负载能力和高运动性能等优点,在工业生产、医疗康复、航空航天等领域得到了广泛应用。
然而,由于并联机构的结构复杂性,其运动学和动力学耦合问题成为制约其性能进一步提升的关键因素。
因此,对并联机构解耦机理的研究与仿真分析具有重要的理论意义和实际应用价值。
二、并联机构概述并联机构是一种由动平台和多个驱动支链组成的机器人机构,其驱动支链与动平台直接相连,具有较高的运动灵活性和承载能力。
然而,由于多支链的耦合作用,使得并联机构的运动控制和力学分析变得复杂。
解耦是提高并联机构性能的关键技术之一,通过解耦可以降低机构的耦合度,提高机构的运动精度和承载能力。
三、解耦机理研究针对并联机构的解耦机理,本文主要从以下几个方面进行研究:1. 数学模型建立:建立并联机构的数学模型,包括运动学模型和动力学模型。
通过分析机构的运动学和动力学特性,揭示机构中各支链的耦合关系。
2. 解耦方法研究:针对并联机构的耦合问题,提出多种解耦方法,包括基于雅可比矩阵的解耦方法、基于能量优化的解耦方法和基于智能算法的解耦方法等。
通过对比分析,找出适用于不同类型并联机构的解耦方法。
3. 解耦效果评估:通过仿真和实验验证解耦方法的有效性,评估解耦后机构的运动精度、承载能力和运动性能等指标,为机构优化提供依据。
四、仿真分析为了进一步研究并联机构的解耦机理,本文采用仿真分析的方法,对典型并联机构进行解耦仿真。
具体步骤如下:1. 选取典型的并联机构,如Stewart平台等,建立机构的三维模型。
2. 根据机构的运动学和动力学特性,建立机构的数学模型。
3. 采用合适的解耦方法对机构进行解耦处理,得到解耦后的机构模型。
4. 通过仿真软件对解耦前后的机构进行仿真分析,比较机构的运动精度、承载能力和运动性能等指标。
5. 根据仿真结果,评估解耦方法的有效性,为实际机构的优化提供依据。
基于FPGA的交叉耦合控制器的设计与实现
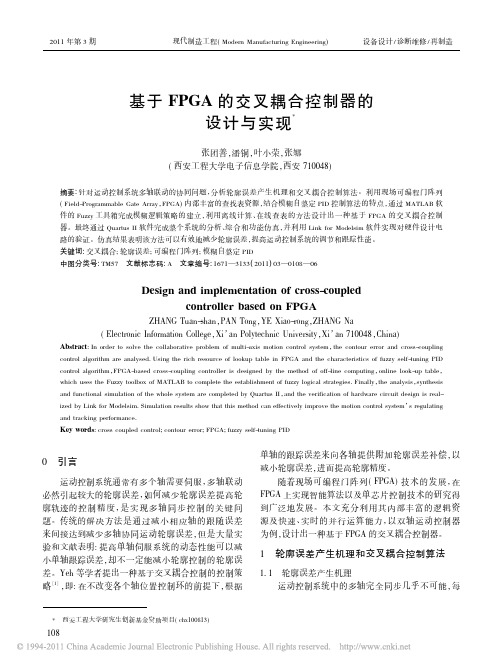
2011年第3期现代制造工程(Modern Manufacturing Engineering)设备设计/诊断维修/再制造基于FPGA的交叉耦合控制器的设计与实现*张团善,潘铜,叶小荣,张娜(西安工程大学电子信息学院,西安710048)摘要:针对运动控制系统多轴联动的协同问题,分析轮廓误差产生机理和交叉耦合控制算法。
利用现场可编程门阵列(Field-Programmable Gate Array,FPGA)内部丰富的查找表资源,结合模糊自整定PID控制算法的特点,通过MATLAB软件的Fuzzy工具箱完成模糊逻辑策略的建立,利用离线计算、在线查表的方法设计出一种基于FPGA的交叉耦合控制器。
最终通过Quartus II软件完成整个系统的分析、综合和功能仿真,并利用Link for Modelsim软件实现对硬件设计电路的验证。
仿真结果表明该方法可以有效地减少轮廓误差,提高运动控制系统的调节和跟踪性能。
关键词:交叉耦合;轮廓误差;可编程门阵列;模糊自整定PID中图分类号:TM57文献标志码:A文章编号:1671—3133(2011)03—0108—06Design and implementation of cross-coupledcontroller based on FPGAZHANG Tuan-shan,PAN Tong,YE Xiao-rong,ZHANG Na(Electronic Information College,Xi’an Polytechnic University,Xi’an710048,China) Abstract:In order to solve the collaborative problem of multi-axis motion control system,the contour error and cross-coupling control algorithm are analysed.Using the rich resource of lookup table in FPGA and the characteristics of fuzzy self-tuning PID control algorithm,FPGA-based cross-coupling controller is designed by the method of off-line computing,online look-up table,which uses the Fuzzy toolbox of MATLAB to complete the establishment of fuzzy logical strategies.Finally,the analysis,synthesis and functional simulation of the whole system are completed by Quartus II,and the verification of hardware circuit design is real-ized by Link for Modelsim.Simulation results show that this method can effectively improve the motion control system’s regulating and tracking performance.Key words:cross coupled control;contour error;FPGA;fuzzy self-tuning PID0引言运动控制系统通常有多个轴需要伺服,多轴联动必然引起较大的轮廓误差,如何减少轮廓误差提高轮廓轨迹的控制精度,是实现多轴同步控制的关键问题。
- 1、下载文档前请自行甄别文档内容的完整性,平台不提供额外的编辑、内容补充、找答案等附加服务。
- 2、"仅部分预览"的文档,不可在线预览部分如存在完整性等问题,可反馈申请退款(可完整预览的文档不适用该条件!)。
- 3、如文档侵犯您的权益,请联系客服反馈,我们会尽快为您处理(人工客服工作时间:9:00-18:30)。
多轴联动系统耦合控制的分析与仿真
发表时间:2018-07-03T10:36:17.270Z 来源:《电力设备》2018年第9期作者:李仁伟
[导读] 摘要:建立了多轴联动系统的同步误差模型,将交叉耦合结构等效为一种带敏感函数的模型,并用以分析耦合控制器对交叉耦合系统性能的影响。
(国网北京顺义供电公司北京顺义 101300)
摘要:建立了多轴联动系统的同步误差模型,将交叉耦合结构等效为一种带敏感函数的模型,并用以分析耦合控制器对交叉耦合系统性能的影响。
在Matlab/Simulink环境下对双轴和三轴交叉耦合系统进行仿真,验证了本文的分析结论。
关键词:多轴联动;交叉耦合;同步误差
1 引言
多轴联动系统广泛应用于各类精密机械加工、编织、缠绕及轧钢等机电一体化设备。
随着自动化水平及生产工艺要求的不断提高,现有控制方式已不能完全适应现代化生产的需要。
因此,研究开发高性能的多轴协调控制策略具有普遍的现实意义和广泛的应用前景。
现今的多轴联动系统存在两种较为典型的结构,一种是非耦合结构,另一种是交叉耦合结构[1]。
前者各个单轴控制系统独立运行,相互之间的控制没有任何电气上的连接,每台电机各自跟踪给定的位置信号,这种结构较为简单,但是当各轴的位置输出出现不同步时,仅能依靠单轴控制器来矫正误差,这种情况下同步误差较大,不能满足一些对同步性能要求较高的应用场合;交叉耦合控制结构是将各台电机输出的位置信号进行比较,从而得到一个同步误差补偿信号,再经过耦合控制器进行放大后分别前馈到单轴系统的输入端,各轴都修正本轴的状态以与其它轴实现快速同步,系统能够很好地抑制因某一台电机输出受到扰动而出现的同步误差,从而获得良好的同步控制精度[2-4]。
然而耦合结构中耦合控制器的增益受系统稳定性的限制不能设计得过大,否则会急剧恶化稳定性,因而设计耦合控制器时需要严格控制增益大小。
本文对双轴和三轴驱动系统进行了研究,根据工程实际定义了两种情况下同步误差的概念,然后推导了耦合环节引入前后同步误差的关系模型。
由这一关系模型分析了耦合控制器所起的作用,并探究了过大的增益对系统稳定性的具体影响。
最后,通过Matlab/Simulink环境下的仿真结果验证分析结论。
2双轴系统
2.1 双轴同步误差模型
在两电机联动实现位置轨迹控制的场合,X轴和Y轴的位移分别由两套电机系统执行,输出为两台电机转子位置角度,两台电机通过十字滑台或其他机械部件相连,将转子位置角度转换为X轴和Y轴的位移,共同实现被控制对象的二维运动轨迹。
设T为被控对象期望达到的参考位置,P=[P1 P2]T为被控对象的实际位置,为目标位置轨迹的角度。
图1 双轴系统同步误差模型
理想情况下目标会沿着两台电机联动输出的位置信号运动,其路线为给定轨迹,然而实际情况中会由于各种扰动和控制精度的限制,实际运动的轨迹通常与给定轨迹存在偏差,由图1定义单轴跟踪误差e和双轴同步误差分别为
(1)
(2)
式中L=[-sinθ cosθ]为变换矩阵。
由式(2)可知,双轴同步误差是由单轴跟踪误e1,e2和轨迹角度θ共同决定的。
2.2 交叉耦合控制系统
双轴交叉耦合系统中,X轴和Y轴系统的跟踪误差被转换为同步误差后经过耦合控制器前馈到系统输入端,通过双轴之间的耦合提升系统的同步性能,其结构如图2(a)所示。
图2 双轴交叉耦合控制系统
图2中分别为X轴和Y轴电机调速系统的输入和输出转速信号,c为同步误差。
C为耦合控制器,通常采用比例(P)控制,即C=kc;Gp1(s),F1(s),Gp2(s)和F2(s)分别为X轴和Y轴系统的位置环控制器和前馈控制器。
交叉耦合系统中的X轴和Y轴均为带前馈的典型伺服系统,由调速系统,位置环控制器和前馈控制器组成。
引入交叉耦合环节前后,双轴系统的简化结构框图如图3所示,图3(a)为双轴并联运行的非耦合结构,图3(b)为交叉耦合结构。
图中M=diag(M1,M2),o为非耦合结构下的同步误差。
(a) 非耦合控制系统 (b) 交叉耦合系统图3 控制系统简化框图由图3(a)可得非耦合结构下跟踪误差和同步误差的表达式分别为
(3)
(4) 从图3(b)可得交叉耦合结构下同步误差c为
(5) 由矩阵求逆引理可知
(6) 将式(4)和式(6)代入式(5)可得
(7) 对式(7)再次应用矩阵求逆引理变换可得
(8) 式中F=(1 + LMLTkc)-1。
式(8)为交叉耦合系统的同步误差模型,描述了双轴系统引入交叉耦合环节前后同步误差的关系。
定义F为同步误差传递函数,可以将F 看作系统的敏感函数,用于交叉耦合系统的性能分析,当F的增益小于1时同步误差减小,同步性能提升。
另外,从式(8)中也可以看出,耦合控制器的增益kc的大小直接影响着F的值,通过调整kc能够达到减小同步误差的目的,但同时M的具体结构未知,通常M中会存在建模误差以及系统的扰动,因而当kc较大时式(8)所描述系统的稳定性难以保证。
3 三轴系统
图4 三轴系统同步误差模型将同步误差的概念扩展到三轴系统中,图4中为输入位置信号,为实际位置,e和ε分别为单轴跟踪误差和三轴同步误差,均以向量形式表示,V为与给定轨迹同方向的单位列向量,L为单位行向量,与V垂直,且与V和e位于同一平面。
定义三轴系统的跟踪误差为
(9) 用、和分别表示X轴、Y轴和Z轴的进给速率,则V可表示为
(10) 由几何关系可知
(11)
,(12) 三轴系统的同步误差可定义为
(13)
将式(10)-(12)代入式(13)可得到
(14) 对比式(2)和式(13)可以看出,三电机系统的同步误差与双轴有相似的结构,因而也可以带入式(8),即三轴交叉耦合系统也可用式(8)来描述。
4 仿真分析为验证在不同耦合控制器增益下耦合控制策略对多轴联动系统的控制效果,使用Matlab/Simulink软件中的SimPowerSystems模块进行仿真,各轴给定跟踪位置信号为斜坡轨迹,斜坡角度为45°,各轴的进给速率均为100mm/s。
仿真中所使用的电机为永磁同步电机,XYZ轴的电机参数如表1所示。
首先验证双轴交叉耦合控制的效果,取XY两轴,电机空载启动,2s时电机Y突加5Nm负载转矩,验证受负载突变干扰时系统的同步性和稳定性。
选取耦合控制器增益kc=20、40,仿真结果如图5所示。
表1 电机参数
真结果如图。