统计过程控制SPC第二版
统计过程控制SPC第二版

例如,原材料的质量不符合规定要求;机 器设备带病运转;操作者违反操作规程; 测量工具带系统性误差,等等。由于这些 原因引起的质量波动大小和作用方向一般 具有一定的周期性或倾向性,因此比较容 易查明,容易预防和消除。又由于异常波 动对质量特性值的影响较大,因此,一般 说来在生产过程中是不允许存在的。
是
否
np或p图 p图
关心的是 单位零件缺陷数吗?
是
样本容量 是否恒定?
是
否
C或U图 U图
二、控制图
计量型控制图
二、控制图 计数型控制图
二、控制图 4、控制图应用的二个阶段
从生产过程中,定期抽取样本,测量各样 本的质量特性值,然后将测得的数据加以 统计分析,判断过程是否处于稳定受控状 态,从中发现过程异常原因(特殊原因), 从而及时采取有效对策,使过程恢复到正 常稳定受控状态。
预防与检测
检测——容忍浪费
在生产部门,通过检查最终产品并剔除不合格产品。不合格的总是不合格。 在管理部门,经常靠检查或重新检查工作来找出错误 这实质上是“死后验尸”,造成时间和材料等的浪费
计数型:通常是指不用仪器即可测出的数 据。计件如不合格件数;计点如PCB上的 漏焊数、溢胶数等
计量型 计数型
计件型 计点型
二、控制图 2、控制图的构成
18 17 16 15 14 13 12 11 10
9 8 7 6 5
1
2
3
4
点落在该区间的概率为99.7%
5
6
7
8
9
+3
Average
-3
10
二、控制图
▪ ……
二、控制图
计数型控制图
不良率控制图(P图) 不良品数控制图(Pn图) 缺陷数控制图(C图) 单位缺陷数控制图(U图)
SPC培训教材(第二版)

统计预测
检验+SPC
全面质量管理 20世纪60年代以来
系统保证
SPC、TQM 6Sigma…
在品质管理发展过程中,SPC 是品质保障的重要工具!
6
客户及标准体系对SPC应用要求
客户要求
-全球产业链之中,供应商必须采用SPC控制其制程; -要求供应商提供过程数据和过程能力;
体系标准要求
-ISO9000、TS16949、QS-9000认证的关键部分; -减少过程不稳定,提高产品质量;
过程品质改进需要
-解决品质顽症,促使工作流的改进; -适应新的生产节拍;
7
工厂SPC应用现状分析
行业内企业普遍面临的问题
管理水平和人员素质跟不上企业发展的要求,工艺和质量的管 控水平不足,影响企业生产高端产品的能力。
外部市场的竞争以及客户对质量提出了更高的要求。 劳动力、生产资源成本不断攀升,降低生产和质量成本成为企
「ISO9000」要求为客戶提供合格的产品,只有稳定而一贯的「过程」与 「系统」,才能保证长期做出合格的产品。然而,如何检核此一贯「过程」 与「系统」仍然稳定的存在?这必须仰赖SPC来发挥功能。
5
质量管理与SPC的关系
质量检验 19世纪末—20世纪30年代
人来保证
事后把关
统计质量控制 20世纪40-50年代
---改变操作 如:培训操作人员、变换输入材料等; ---改变设计 如:设备、沟通方式和相互关系、过程整体设计等; 对输出采取措施:探测并纠正不符合规范的产品,而没有处理过程中根本问 题,可能会持续的对产品进行100%挑选、返工等,直到过程改善了。
2
课程大纲
• 第1章 持续改进和统计过程控制 • 第2章 控制图
SPC-2

Table of Contents/目录
Section 1: Introduction/引言
1) 2) 3) 4) 5) History of Quality Management /质量管理发展的阶段 Statistical Technology of Quality Management /质量管理中的统计技术 QMS Requirements to Statistical Technology / 各质量体系对统计技术的要求 History of SPC/ SPC的发展 SPC&SQC/ SPC与SQC
Section 1: Introduction/引言
将相似工序同类分布的产品质量特征值数据,通过数学方法变换程 同一分布,从而可以累积起来称为大样本进行处理。主要有:通用 图法、相对公差法及美军固定样本容量法。
– 选控控制图(Cause-Selecting Control Chart):前述控制图都是全 控图,及对所有异因都加以控制。而选控图是选择部分异因加以 控制,它由我国张公绪教授1980年提出。它对统计诊断理论起到 重要的作用。 – 彩虹图 – 多元控制图:1947年侯铁林(H. Hotelling)提出多元T2图控制 图,从此开辟了多元质量控制的时代。
– – Measurement of Two sided Spec (bilateral) /双边公差的指数 Measurement of One Side Tolerance /单边公差的指数
Section 4 : Control Chart/控制图概述
1) 2) Control Chart Theory/ 控制图的原理 Benefits of Control Charts /控制图的作用
spc(第二版)

本手册所描述控制图的选用程序第Ⅰ章持续改进及统计过程控制概述在今天的经济气候下,为了事业昌盛,我们——汽车制造商,供方及销售商必须致力于不断改进。
我们必须寻找更有效的方法来提供产品及服务。
这些产品和服务必须不断地在价值上得以改进。
我们必须重视内部以及外部的顾客,并将顾客满意作为企业的主要目标。
为了达到这一目标,我们组织中的每一个人都必须确保不断改进及使用有效的方法。
本手册涉及到第二个领域的某些要求。
它描述了能使我们致力于的改进更有效的几种基本的统计方法。
为了完成不同的任务需要不同程度的理解。
本手册的对象是见习生以及刚开始从事统计法应用的管理人员。
对于现在正在应用更先进技术的人员,本手册也可作为他们学习这些基本方法的参考文献。
本手册并没有包括所有的基本方法。
附录H所列的参考文献或手册中阐述了其他的基本方法(例如:检查清单、流程图、排列图、因果分析图等)及一些先进的方法(如其他控制图、试验设计、质量功能展开等)。
本书所述的基本统计方法包括与统计过程控制及过程能力分析有关的方法。
本手册的第1章阐述了过程控制的背景知识,解释了一些重要的概念:如变差的特殊及普通原因,并介绍了控制图,这个用来分析及监控过程非常有效的工具。
第Ⅱ章描述了构造和使用计量型数据控制图表(定量的数据,或测量)的 -X—R,-X—s图,中位数图以及X—MR(单值及移动极差)图。
这一章还介绍了过程能力的概念并讨论了广泛应用的指数及比值。
第Ⅲ章介绍了用于计数型数据(定性数据或计数值)的几种控制图:p图、np图及u 图。
第Ⅳ章介绍了测量系统分析的内容并列举了适当的例子。
附录包括分组及过度调整的例子,如何使用控制图的流程图、常数及公式表、标准正态分布以及可复制的空白表等。
术语索引给出了本手册所使用的术语及符号的解释,参考文献一节向读者提供了进一步学习的材料。
在开始讨论之前,需进行六点说明:1.收集数据并用统计方法来解释它们并不是最终目标,最终目标应是对读者的过程不断加深理解。
SPC经典解读

SPC经典解读统计过程控制(SPC)第二版是在美国质量协会(ASQ)及汽车工业行动集团(AIAG)支持下,由戴勒斯勒,福特和通用汽车公司供应商质量要求特别工作组认可的统计过程控制(SPC)工作组所开发的.任何供应商可以利用本手册来建立与戴勒斯勒,福特和通用汽车公司中任一个供应商评定系统要求相关的信息本手册并不意图去限制适用某特定过程或商品的SPC方法的发展.第二SPC第一版前言SPC第一版是在美国质量控制协会(ASQC)汽车部供方质量要求编写组和汽车工业行动集团(AIAG)的共同支持下,由戴勒斯勒,福特和通用汽车公司的质量和供应商评定人员编制.本手册可看成是对统计过程控制的介绍,它并不限制适用于某特定过程或商品的SPC方法的发展.也不诣在综合所有的SPC技术.第三SPC第二版六点说明通过收集来的数据,运用统计方法来解释过程,并不是最终目标.最终目标应该是在观测过程中,不断加深理解,并将增长的知识作为行动的基础.测量系统对适当的数据分析来说是很关键的,在对过程运用统计方法来解释之前,应对所收集的数据进行变差分析.否则就可能作出不恰当的决定.本手册统计方法的介绍是建立在测量系统处于受控状态,这一假设前提的基础上的.研究变差和应用统计知识来改进性能的基本概念适用于任何领域.SPC代表过程控制,但以前统计方法常用于零件而不是过程.应用统计技术来控制输出(零件等)仅仅是第一步.只有这些方法用在产生输出的过程,并成为努力的重点,才能在改进质量/提高生产率/降低成本上充分发挥作用.要真正理解SPC统计技术需要与过程控制的实际相联系,实际工作经验是无法取代.本手册可看成是应用统计方法的第一步,它提供了被普遍接受的方法,并在许多场合得以运用.然而还是存一些不例外的情况,在这些情况下,盲目的使用这些方法是不恰当的.本手册不替代从业者对提高统计方法的知识和理论的需要,当发现有更先进的统计方法运用比本手册所述内容更选进时,建议向具有一定的统计理论知识与实践经验的人请教有关它的适宜性.任何情况下,所用的程序都必须满足顾客的要求.第四过程控制需要控测(容忍浪费)和预防(避免浪费)通过质量控制来检验最终产品,并剔除不符合产品,这是使用控测的方法,它允许将时间和材料投入到生产不一定有用的产品或服务中去,是浪费的.通过一开始就不产生无用的输出,从而避免浪费的更用效的策略是------ 预防过程控制系统,如下图过程控制系统是一个反馈系统.SPC是运用统计技术的反馈系统,但也存在不使用统计技术的反馈系统.过程是通过产生输出的供应商,生产者,设备,输入材料,方法和环境,及使用输出的顾客的集合共同作用.过程的性能取决于供应商与顾客间的沟通,过程设计和实施的方式,及运作和管理的方式等.过程控制系统的其它部分只有在维持整个系统的良好水准,或提高整个过程的性能时才有用.过程实际性能,是通过研究过程输出而获得相关信息的.但有关性能最有用的信息,还是通过对过程本身,及其内在的变化的认识得到的.过程特性(如:温度,时间,速率,产能,延迟等,而不是产品特性),因该成为我们努力的焦点,据此确定这些特性的目标值(达到高效益状态时),而后进行监测控制.在异常时,及时对应处置,若不及时适当处理,否则收集的信息就白费了.过程采取措施,主要有改变操作,如作业员培训,变换输入材料改变过程本身基本要素,如设备,人员沟通方试,过程作为一个整体设计.输出采取措施,主要是往往仅限对输出控制,并纠正不符合产品,而没有处理过程中的根本性问题.当持续不能满足要求,可能性就有必要对所有产品进行挑选,返工或报废,这种情况持续到对过程采取有效措施验证OK为止.对输出采取措施,只可作为不稳定或没有能力的过程的临时措施.综述,措施对应要把重点放在过程,而非输出,管理对就要把重点落在预防而非控测.第五过程变异的普通原因与特殊原因过程分布每件产品尺寸与别的产品不同,但它们形成一个模型.若稳定,则可以绘制成一个分布.分布描述有三种情况:位置,宽度,形状.过程仅存在变差的普通原因,随着时间推移,过稳的输出形成一个稳定的分布并预测;若存在变差的特殊原因,随差时间推移,过程输出不稳定.变差的普通原因与物殊原因过程变差,任何过程包含引起变差的很多原因.有的原因引起短期的零件间的差异;有的原因需要经过较长时间后才对输出造成变化.故量测量的周期和测量时的条件很关键,因为会影响到观测到的总变差的数量.管理过程并减少变差,应该是以最小的变差保持目标位置.追踪造成变差的来源,首先应把变差源区分成普通与特殊的原因.普通原因,指那些始终作用于过程的多种变差业源.随着时间的推移,一个过程中的普通原因会产生一个稳定的且可重复的分布.我们称为:处于统计上受控制的状态.或统计受控.物殊原因,指引起变差会影响过程输出,这些因素通常是间歇的,不可预测的.其在控制图表现的信号是:一个或多个点超出控制限,或在控制限内的点出现非随机模式.除非所有的特性原因被识别出来且采取了措施,否则将继续以不可预测的方式来影响过程物殊原因造成过程分布的改变有些有害,有些有利.对于一些成熟的过程,存在一个稳定发生的特殊原因,是许可的,但就有控制计划保证符合要求.系统措施和局部措施局部措施,通常用来消除变差的特殊原因,与过程直接相关的人员来实施,大约可纠正15%的过程问题系统措施,通常用来消除变差的普通原因,几乎要采取管理上的纠正措施.大约可纠正85%的过程问题,如当需要管理者对系统采取措施(选择更好的材料商),而却采取局部措施(调机),这是不对的.过程控制与过程能力过程控制系统的目的,就是对过程当前和将来的状态作出预测,对便对影响过程的措施作出经济合理的决定. 这些决定需要平衡时未要取措施,不需要平衡时却采取了措施.这两种风险过程控制下运行指的是仅存在造成变差的普通原因.这样过程控制系统的作用是:当出现变差的特殊原因时,发出统计信号和不存在特殊原因时避免提供错误信息.若特殊原因有用则永久保持,否则给予消除.过程控制系统可以作为一个一次性的评估工具,但是过程控制系统的真正的好处只有在把它作为一个持续学习的工具而不是符合性判定的工具(好/坏,稳定/不稳定,有能力/没有能力)使用才能实现.控制与能力过程能力需考虑一定程度上的相对概念:过程能力与过程性能.过程能力由造成变差的普通原因确定,通常代表过程本身最佳性能.当过程在统计受控状态下运行,过程能力可以得到证实,与规范无关.内外部顾客更关心过程性能,也就是过程总的输出以及与他们的要求(定义为规范)的关系,而不是过程变差.一般来讲,处于统计受控的过程服从可预测的正态分布,其位置,宽度和形状不变化.此时对过程采取的措施就是将位置定位在目标值上.若分布宽度是不可接受的,通常采用系统措施减少普通原因引起的变差来改进过程.过程控制,首先应通过探测并消除变差的特殊原因,使过程处于统计受控状态,这样即可预测,也可评定其满足顾客期望的能力.这是持续改进的基础统计受控4类型:1能力可接受,且过程受控;2能力不可接受,但过程受控;3能力可接受,但过程不受控;4 能力不可接受,且过程不受控.但有些顾客对第3类情况允许,主要原因是对产品规范内的变差不敏感.对特殊原因采取的措施所发生的成本比任何顾客得到的利益大.从经济上考虑,可允许存在特殊原因包括刀具磨损,周期性变化等.当特殊原因被识别,应记录过往与现在的一致性及可预见性用于预测工具所使用的各类过程指数和比率作用,要求所用于统计分析的数据是处于统计受控状态的过程收集.(在汽车工业中可接受的做法是在一个过程被证明处于统计受控状态后才计算过程能力.在不稳定过程收集的数据进行预测是毫无价值的.其间特殊原因对过程影会使预测失效)过程指数估计分2种,一则利用子组内变差估计,二则利用总变差估计.使用不同指数是因为没有一种指数可以广泛应用所有过程,也没有一个过程可由一个指数来完全描述.过程改进循环的各个阶段示意图,如下6. 过程改进循环与过程控制分析过程过程改进前,必须对过程有基本子解,需从以下问题入手在过程的每个步骤,期望得到什么?交付结果的可操作的定义是什么?过程中有什么问题会发生?对过程变差我们了解什么,哪些变差是最敏感的?过程是否在生产废品或需要的返工品?过程是否在统计受控状态下进行?过程是否有能力?过程是否可靠?维护过程过程是动态变化的,必须监控过程的性能,当所使用的统计工具表明过程已改变,应立即采取有效的措施.通常很容易停止在本过程.因为任何一个组织公司的资源是有限的.这是众多组织的一个明显的竞争劣势.要达到世界级水准,就要用稳定有计划的努力来进入下一个阶段(改进过程)改进过程当顾客对工程规范内的变差表示敏感时,持续改进的价值只有在变差缩小后才能实现.如:实验设计(DOE),当新的过程参数确定后,现回转到过程分析,并循环运行.过程控制和改进工具过程控制常犯的两种错误:错误1,将事实上的系统(普通原因)的变差,描述成特殊原因的变差或错误.造成过程调整(干预)错误2, 将事实上的特殊原因的变差,描述成普通原因的变差或错误.常不去试差找特殊原因管理变差的(探测特殊原因)的有效方法------ 直方图,但不幸的是正态分布并不能保证没有特殊原因在起作用,也就是说,某些特殊原因可能在不改变正态分的情况下改变过程,同样一个非正态分布也可能没有特殊原因,但它的分布是非对称的.使用一个可用正态形式描述的过程分布,目的是确定特殊原因何时会影响它,换句话说:从上次观察开始,或在抽样的期间内,过程是否发生改变.休哈特的数据展示的两个规则:数据应该总是以这种方法保存,使证据保存在这些数据中,而所有的预测都可能由这些数据作出.任何时候使用平均值,极差或直方图汇总数据时,如果该数据基于时间做展示的话,汇总应该不能误导用户有采取任何使用者不愿意的措施控制限计算:中心线(CL)=分析的统计量的均值上控制限(UCL)=中心线(CL)+ 3×均值的标准差下控制限(LCL)=中心线(CL)- 3×均值的标准差若有证据表明存在变差的特殊原因,应对过程进行研究,并确定它影的是什么.若普通原因造成变差过大,则过程不能生产一致的符合顾客要求的产品,必须调查过程本身,一般采取管理措施来改进系统.改进循环的目的是理解过程及变差,以提高它的性能.过程受控改进,其工作重点就经常放在减少过程中的普通原因变差上.若减少这种变差,就会缩小控制图上的控制限.许多不熟悉控图的人觉得是对过程的一种惩罚,因为其没有意识到过程错误的产生不受控的点的机会是相同的,与控制限无关.8. 控制图有效使用的益处控制图有效使用的益处,直接与下列事项有关:管理哲学:组织是如何管理的会直接影响SPC的有效性.如:使组织关注减少变差;工程哲学:工程如何使用数据开展设计,将会对最终产品的变差等级和类型有影响;如:使工程人员关注变差减少.制造:如何开发/操作和转换系统,可以影响最终产品的变差等级和类型.在过程稳定前,勿将控制图发放到操作人员.应该在过程稳定后才将过程的职责转移给生产继续阅读。
统计过程控制SPC第二版精品培训
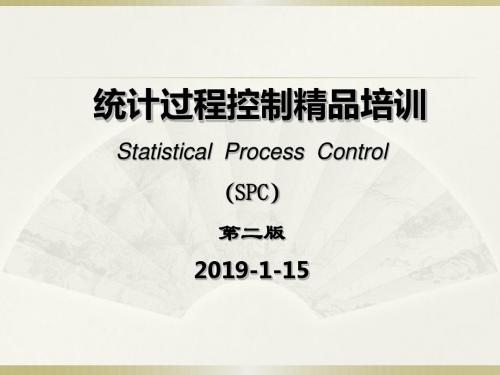
八、计数型数据控制图 1、p 图 2、np图 3、c 图 4、u 图 九、过程能力分析及控制图的判读
1.品管方法历程
690,000 300,800 66,807
一、正确认识SPC
Average Company 一般公司
Best in class 世界标杆公司
6,210
233 3.4 1σ
方法
产品检查 品管7手法 (5S、QCC、ISO9001)
事后检验的质量控制方法已不能适应当时经济发展的要求,
必须改进质量管理方式。于是,英、美等国开始着手研究用 统计方法代替事后检验的质量控制方法。 ◆1924年,美国的休哈特博士提出将3Sigma原理运用于生产 过程当中,并发表了著名的“控制图法”,对过程变量进行
控制,为统计质量管理奠定了理论和方法基础。
1、与过程相关的控制图 2、使用控制图的准备 3、X bar-R 图 4、X bar-s 图 5、X med-R图 6、X -Rm图
二、基本的统计概念
概率与抽样介绍 1、主要的统计学名词 2、正态分布的基本知识 3、中心极限定理 4、主要的统计参数 5 、统计推断&假设检定
三、持续改进及SPC概述
1、过程控制系统 2、变差的普通原因及特殊原因 3、局部措施和对系统采取措施 4、过程控制和过程能力 5、过程改进循环及过程控制 6、控制图
一、正确认识SPC
2. SPC兴起的背景
美国沃尔特•休哈特博士于1924年发明控制图,开启 了统计品管的新时代
「经验挂帅时代」的结束
如果工作经验对产品质量有举足轻重的影响(例如:手工裁缝),那么, SPC就没有太多挥洒的空间。相反地,如果某一公司开始将经验加以整理,
而纳入设备、过程或系统时;也就是说,该公司开始宣告「经验挂帅时代」
统计过程控制(SPC)—培训教材(第二版)

过程设计 和开发
产品和 过程确定
反馈、评定 和纠正措施
样件制作
试生产
批量生产
7、“过程分析(乌龟图)”在统计过程控制(SPC)中的运用: 过程分析(乌龟图)审核工作表
使用什么方式进行 ⑤
(材料/设备/装置)
填写机器(包括试验设备),材 料,计算机系统,过程中所使用
的软件等的详细说明
由谁进行? ⑥
(能力/技能/知识/培训)
2、统计过程控制(SPC)的定义: 使用诸如控制图等统计技术来分析制造过程或
其输出,以便采取适当的措施,为达到并保持统计 控制状态从而提高或改进制造过程能力。
3、 ISO/TS 16949:2002体系对 SPC 的要求:
ISO 9001:2000质量管理体系—要求 8 测量、分析和改进 8.1 总则
铸造不良情况检查表
项目 地点
日期 废品数 不良分类
欠铸 冷隔 小砂眼 粘砂 其他 合计
铸造质量不良 质检科
1月 2月
224 258
240 256
151 165
75
80
14
18
704 777
收集人 XXX 日期
记录人 XXX 班次
2000年1月-6月
3月 4月 5月
356 353 332
283 272 245
统计过程控制
Statistical Process Control (SPC)
一、统计过程控制(SPC)概述
1、统计过程控制(SPC)的概念: 指 Statistical Process Control (统计过
程控制)的英文简称。 S ( Statistical ) 统计 P ( Process ) 过程 C ( Control ) 控制
SPC手册第二版

I S O/T S16949:2002统计过程控制S P C(培训资料仅供参考)统计过程控制(S P C)参考手册第二版,2005年7月出版1992年版第二次印刷, 1995年3月印制 (仅新封面)?1992、?1995、?2005版权由戴姆勒克莱斯勒公司、福特汽车公司和通用汽车公司所有中文繁体版台湾地区总经销品士股份有限公司地址:台北市111忠诚路二段58号4楼电话:+886 2 2833 2112,传真:+886 2 2833 2119g.twtw中文简体版大陆地区总经销北京品士质量管理顾问有限公司地址:北京市海淀区知春路9号坤讯大厦1107室电话:+86 10 8232 2089 , +86 10 8232 7247传真:+86 10 8232 2070Email:info@AIAG服务专线:+1 248 358 3003第二版前言本参考手册是在美国质量协会(American Society for Quality,ASQ)及汽车工业行动集团(Automotive Industry Action Group, AIAG)支持下,由戴姆勒克莱斯勒、福特和通用汽车公司供应商质量要求特别工作组认可的统计过程控制(SPC)工作组所开发的。
负责第二版的工作小组准备是戴姆勒克莱斯勒公司、Delphi公司、福特汽车公司、通用汽车公司、Omnex公司和Robert Bosch公司的质量和供应商评定人员与汽车工业行动集团(AIAG)合作组成的。
特别工作组的任务是将在戴姆勒克莱斯勒、福特和通用汽车公司各自的供应商评定系统中使用的参考手册,报告格式和技术术语进行标准化处理。
据此,任何供应商可以利用本手册来建立与戴姆勒克莱斯勒、福特和通用汽车公司中任一个供应商评定系统要求相应的信息。
第二版编制了自1991年原有的手册出版后汽车工业行业SPC技术发展的需求和变动。
本手册是对统计过程控制的一种介绍。
它并不意图去限制适用某特定过程或商品的SPC方法的发展。
- 1、下载文档前请自行甄别文档内容的完整性,平台不提供额外的编辑、内容补充、找答案等附加服务。
- 2、"仅部分预览"的文档,不可在线预览部分如存在完整性等问题,可反馈申请退款(可完整预览的文档不适用该条件!)。
- 3、如文档侵犯您的权益,请联系客服反馈,我们会尽快为您处理(人工客服工作时间:9:00-18:30)。
二、控制图 3、控制图的分类
计量型控制图 计数型控制图
二、控制图 计量型控制图
▪ 均值-极差控制图 ( ▪ 均值-标准差控制图 ( ▪ 单值-移动极差控制图 ( ▪ ……
统计特证数
2、样本中位数:
➢ 把收集到的统计数据按大小顺序重新排列, 排在正中的那个数就是中位数;
当n为奇数时,正中间的数只有一个,当n为偶数时, 中位数为正中两个数的算术平均值。
➢ 中位数也是表示数据集中位置的一种特征数 ,只是较样本平均值所表示的数据集中位置要 粗略一些,但是可减少计算的工作量 。
10
二、控制图
控制图的要素
➢ 纵坐标:数据(质量特性值或其统计量)
➢ 横坐标:按时间顺序抽样的样本编号
➢ 上虚线:上控制界限UCL
➢ 下虚线:下控制界限LCL
➢ 中实线:中心线CL
控制界限=平均值±3σ
二、控制图 控制图原理
1) 3 σ原理: 若变量X服从正态分布,那么,在 ±3σ 范
围内包含了99.73% 的数值。 2) 中心极限定理:
❖ 计数型:通常是指不用仪器即可测出的数 据。计件如不合格件数;计点如PCB上的 漏焊数、溢胶数等
计量型 计数型
计件型 计点型
二、控制图 2、控制图的构成
18 17 16 15 14 13 12 11 10
9 8 7 6 5
1
2
3
4
点落在该区间的概率为99.7%
5
6
7
8
9
+3s
Average
-3s
管理控制图 实际的变化发生在此处
USL
UCL
将导致在此 处耗费时间 查找原因
一、SPC的基本原理
“SPC就像房屋中的烟雾探测器:只要这 种装置备有电池,并且被正确安置以及 旁边有人监听,那么它就可以提前发出 警报使你有足够时间阻止房屋起火”
——《6 Sigma管理法 追求卓越的阶梯 》
二、控制图
一、SPC的基本原理 3 σ原理
68% 95% 99.7%
一、SPC的基本原理
SPC的意义
➢ 全面、及时了解质量信息,信息共享 ➢ 有效监测和预防,提高生产率 ➢ 提高客户满意度,赢得更多客户 ➢ 保持产品和服务质量的稳定性及进一步的持续改进 ➢ 降低总的质量成本
一、SPC的基本原理
SPC的意义 有效监测与预防
统计过程控制SPC第二 版
内容提要
一、SPC的基本原理 二、控制图 三、过程能力研究
一、SPC的基本原理
Statistical: (统计)以概率统计学为基础,用科 学的方法分析数据、得出结论;
Process: (过程)有输入-输出的一系列的活动 ;
Control: (控制)事物的发展和变化是可预测的 ;
在管理部门,经常靠检查或重新检查工作来找出错误 这实质上是“死后验尸”,造成时间和材料等的浪费
预防——避免浪费
通过对生产过程的监视和控制,第一步就可以避免生产无用的输出,是 避免浪费的有效方法。
当今,汽车制造商、供方及销售商采用有效的预防措施,持续不断改进 ,提供内、外部顾客满意的产品和服务作为主要目标。
例如,原材料的质量不符合规定要求;机 器设备带病运转;操作者违反操作规程; 测量工具带系统性误差,等等。由于这些 原因引起的质量波动大小和作用方向一般 具有一定的周期性或倾向性,因此比较容 易查明,容易预防和消除。又由于异常波 动对质量特性值的影响较大,因此,一般 说来在生产过程中是不允许存在的。
1、质量特性的分类 2、控制图的构成 3、控制图的分类 4、控制图应用的二个阶段 5、控制限的计算 6、判异准则
二、控制图 1、质量特性分类
计量型:用各种计量仪器测出、以数值形 式表现的测量结果,包括用量仪和检测装 置测的零件直径、长度、形位误差等,也 包括在制造过程状态监控测得的切削力、 压力、温度、浓度等。
因此,产品质量波动具有普遍性和永恒性。当生 产过程处于统计控制状态时,生产出来的产品的 质量特性数据,其波动服从一定的分布规律,这 就是产品质量的规律性。
例如,原材料的成分和性能上的微小差异;机器设备的轻微振动;温度、 湿度的微小变化;操作方法、测量方法、检测仪器的微小差异,等等。要 消除造成这些波动的随机因素,在技术上难以达到,在经济上的代价也很 大。因此,一般情况下这些质量波动在生产过程中是允许存在的,所以称 为正常波动。公差就是承认这种波动的产物。
变差的原因
变差的普通原因和特殊原因
普通原因:是指过程在受控的状态下,出现的具有稳定的且可 重复的分布过程的变差的原因。
普通原因表现为一个稳定系统的偶然原因。只有过程变差的普 通原因存在且不改变时,过程的输出才可以预测。
是过程变差的偶然因素。永远存在,不可查明。
特殊原因:(通常也叫可查明原因)
是指造成不是始终作用于过程的变差的原因,即当它 们出现时将造成(整个) 过程的分布改变。只用特殊 原因被查出且采取措施,否则它们将继续不可预测的 影响过程的输出。
) ) )
二、控制图
计数型控制图
▪ 不良率控制图(P图) ▪ 不良品数控制图(Pn图) ▪ 缺陷数控制图(C图) ▪ 单位缺陷数控制图(U图)
二、控制图 选择合适的控制图
是
计量型数据吗?
否
性质上是否均匀
或不能按子组取样?
是
否
子组容量≥ 9?
否 是
关心的是 不合格品率吗?
是
否
样本容量
是否恒定?
是
否
解释
中心线(Central 控制图上的一条线,代表所给数据平均值。 Line)
过程均值(
一个特定过程特性的测量值分布的位置即为过程均值,通常
Process Average 用 X 来表示。
)
链(Run)
控制图上一系列连续上升或下降,或在中心线之上或之下的 点。它是分析是否存在造成变差的特殊原因的依据。
基于所收集的信息而对过程采取措施
对过程采取措施,使重要特性(过程或输 出)接近目标值,保持过程输出变差在可接受 的界限内。
采取措施包括
改变操作(操作者培训、变换输入材料)
或改变过程本身更基本的因素(如:修复设备 、人的交流和关系如何
或整个过程的设产品规范等
统计特证数
3、 样本方差:样本方差是衡量统计数据分散
程度的一种特征值。
S2=
S2—样本方差 n—样本个数
X—样本平均值 Xi—每个样本的实测值
统计特证数
4、样本标准偏差:S样本方差的正平方根作为
样本标准偏差
S=(
)
S__样本偏差 n—样本个数
X—样本平均值 Xi___每个样本的实测值
每件产品的尺寸与别的都不同
两个或多个连续样本值中最大值和最小值之差。
质量的波动性
➢ 产品质量具有波动性和规律性,从统计学的角度 来看,产品质量波动可分成正常波动和异常波动。 ➢ 质量管理的一项重要工作,就是要找出产品质量 波动规律,把正常波动控制在合理范围内,消除系 统原因引起的异常波动。生产现场通过控制图的运 用,对过程质量加以测量、记录并进行控制管理, 以及时反映和区分正常波动与异常波动。
np或p图 p图
关心的是 单位零件缺陷数吗?
是
样本容量 是否恒定?
是
否
C或U图 U图
二、控制图
计量型控制图
二、控制图 计数型控制图
质量的波动性
⒈正常波动:
正常波动是由随机原因引起的产品波动。对这些随机因 素的消除,在技术上难以达到,经济上代价也很大,因此, 一般情况下,是允许存在的——公差就是承认这种波动的产 物。产品质量具有波动性和规律性。
在生产实践中,即便操作者、机器、原材料、加工方法 、测试手段、生产环境等条件相同,但生产出的一批产品的 质量特性数据却并不完全相同,总是存在着差异,这就是产 品质量的波动性。
我们把仅有正常波动的生产过程称为处于统计控制状态,简称为受控状态 或稳定状态。
质量的波动性
⒉异常波动:
异常波动是由系统原因引起的产品质量波动,又 称特殊波动,由于这些因素引起的质量波动大小和作 用方向一般具用一定的周期性或倾向性,因此比较容 易查明,容易预防和消除,又由于异常波动对质量特 性值的影响较大,因此,在生产中是不允许存在的。 有异常波动的生产过程称为处于非统计控制状态,简 称为失控状态或不稳定状态。
范围
范围
范围
范围
但它们形成一个模型,若稳定,可以描述为一个分布
范围
范围
分布可以通过以下因素来加以区分
位置
分布宽度
范围 形状
或这些因素的组合
如果仅存在变差的普通原因, 随着时间的推移,过程的输 出形成一个稳定的分布并可 预测。
范围
如果存在变差的特殊 原因,随着时间的推 移,过程的输出不 稳定。
范围
目标值线 预测
变差(Variation 过程的单个输出之间不可避免的差别;变差的原因可分为两
)
类:普通原因和特殊原因。
特殊原因( Special Cause)
一种间断性的,不可预计的,不稳定的变差根源。有时被称 为可查明原因,它存在的信号是:存在超过控制限的点或存 在在控制限之内的链或其它非随机性的图形。
一、SPC常用术语解释
采取措施后
——应监测措施效果。 ——对输出采取措施:即对输出的不符合规范的产品 进行检测、分类(合格、报废、返工)。如果不分析过程 中的根本原因,不对过程采取校正措施或验证,这是时 间和材料的极大浪费。
一个过程控制系统可以称为一个反馈系统。