某100万吨烟气量焦化厂余热回收
焦化系统余热回收利用

工业技术82 2015年53期焦化系统余热回收利用张美玲鞍山华泰焦耐工程技术有限公司,辽宁鞍山114001摘要:焦化企业在生产过程中会产生大量的热量,而这些热量一直被焦化企业所忽视,造成了资源的巨大浪费,在我国构建生态可持续发展、实现企业节能减排的当前时代背景下,焦化企业要重视对余热的回收,通过余热回收实现资源的最大利用,并且为企业增效提供重要的创收途径。
关键词:焦化系统;余热回收;改造措施中图分类号:TQ520.5 文献标识码:A 文章编号:1671-5810(2015)53-0082-02导言某煤化工有限公司现设计年产120万吨焦炭生产线,生产过程中产生荒煤气,荒煤气被氨水喷洒冷却至90℃左右,荒煤气中的焦油等同时被冷凝下来,煤气和冷凝下来的焦油等同氨水一起经过吸煤气管送入煤气净化车间,净化车间利用横管换热器间接冷却煤气到25℃,同时循环水可达到40℃,循环水利用凉水架降温,严重浪费能源。
如果这些余热不进行回收利用,不仅浪费了宝贵的能源,也污染了环境。
因此,本文结合某某煤化工有限公司的实际情况,针对焦化系统余热回收利用方面的内容进行了分析,以供参考。
1 焦化工艺简析在焦化企业生产过程中,备煤车间将配置好的煤装入到煤塔中,相关工作人员将煤按照作业计划从煤塔中取出相应重量的煤炭之后,装入装煤车之后,将其推入碳化室内,然后煤炭在碳化室内经过系列的高温作业之后形成焦炭,并且与此同时产生荒煤气。
此外,经过焦化处理工艺,煤在碳化室内经过干馏过程会产生大量的荒煤气,而这些荒煤气会聚集到碳化室顶部的空间,然后这些荒煤气则会经过系列的管道进入集气管,而荒煤气的温度要在700℃左右,而这些热量却没有被焦化企业所有效的应用起来,而是其在相应的桥管中被氨水喷洒之后冷却下来了,无形之中造成了大量热量的损失。
与此同时,来自焦化系统90℃左右的荒煤气首先通过气液分离器实现气液分离,分离出的粗煤气由上部出来,进入横管初冷器分两段冷却。
焦炉烟气余热回收发电技术分析

焦炉烟气余热回收发电技术分析任国平【摘要】煤焦化行业是高污染、高排放的行业,所排放的焦炉烟气温度一般大于300℃,既浪费能源又污染环境,是急需解决的问题.针对目前焦化企业焦炉烟气余热资源无序排放的现状,提出了采用先进的热管技术回收焦炉烟气热能及使用螺杆动力机取代传统汽轮发电机技术的新方案,分析了实施改造前后的能源消耗和经济效益.结果表明,焦炭生产能力为90万t/a的焦化厂,将烟气温度由300℃降至150℃,可回收能量折标准煤量为7598 t/a,由机组发电产生的经济效益为127.60万元/a.因此采取先进可靠的焦炉烟气余热发电技术是焦化行业实现节能减排和可持续发展的较好选择.【期刊名称】《洁净煤技术》【年(卷),期】2014(020)003【总页数】4页(P87-89,94)【关键词】焦炉;烟气;余热发电;螺杆动力机发电机【作者】任国平【作者单位】长治市荣信节能科技服务有限公司,山西长治046000【正文语种】中文【中图分类】X750 引言随着中国资源循环利用体系和节能减排工作的逐步推进,煤化工作为高耗能、高排放产业,面临着巨大的环境和市场等压力[1]。
炼焦工业是伴随着钢铁、冶金行业的重要基础产业,炼焦过程的自身能耗约占整个焦化厂全部能耗的70%,其中能源消耗量占焦化气体(焦炉煤气)产能的40%~50%。
因此,焦化行业是节能减排的重点行业,努力降低炼焦能耗也是一项重要任务。
目前焦炉生产中,供给整个焦炉的热量和空气量是用加热煤气体积流量和分烟道吸力来控制的[2]。
但由于各种原因,在相同煤气流量和分烟道吸力下,单位时间进入焦炉加热用总热量和氧量是变化的。
一般都突破计划加热耗能量(计划耗能量约为2%,无论采用何种气源加热)[3]。
实际生产中为确保生产熟焦质量,防止出生焦,加热煤气量略高于设计指标1%~2%。
为确保燃烧安全,空气过剩系数为1.2左右,亦略大于设计指标,这在炼焦加热控制过程属于正常的调节控制范围[4]。
余热回收计算公式
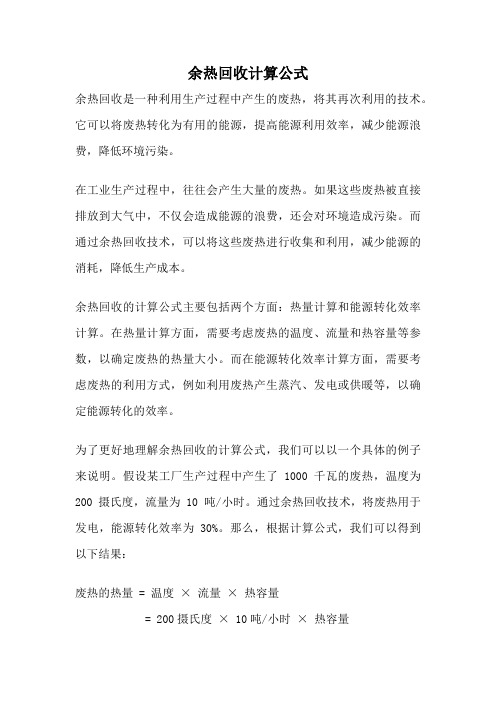
余热回收计算公式余热回收是一种利用生产过程中产生的废热,将其再次利用的技术。
它可以将废热转化为有用的能源,提高能源利用效率,减少能源浪费,降低环境污染。
在工业生产过程中,往往会产生大量的废热。
如果这些废热被直接排放到大气中,不仅会造成能源的浪费,还会对环境造成污染。
而通过余热回收技术,可以将这些废热进行收集和利用,减少能源的消耗,降低生产成本。
余热回收的计算公式主要包括两个方面:热量计算和能源转化效率计算。
在热量计算方面,需要考虑废热的温度、流量和热容量等参数,以确定废热的热量大小。
而在能源转化效率计算方面,需要考虑废热的利用方式,例如利用废热产生蒸汽、发电或供暖等,以确定能源转化的效率。
为了更好地理解余热回收的计算公式,我们可以以一个具体的例子来说明。
假设某工厂生产过程中产生了1000千瓦的废热,温度为200摄氏度,流量为10吨/小时。
通过余热回收技术,将废热用于发电,能源转化效率为30%。
那么,根据计算公式,我们可以得到以下结果:废热的热量 = 温度× 流量× 热容量= 200摄氏度× 10吨/小时× 热容量能源转化的效率 = 发电量 / 废热热量= 发电量 / (200摄氏度× 10吨/小时× 热容量)根据以上计算公式,我们可以计算出废热的热量和能源转化的效率,并据此评估余热回收的效果。
通过合理的设计和优化,可以提高能源转化效率,实现废热的最大利用。
余热回收的计算公式是对废热的热量和能源转化效率进行计算的公式。
通过合理应用这些公式,可以实现废热的高效利用,提高能源利用效率,减少环境污染,为可持续发展做出贡献。
烟气余热回收技术方案

烟气余热回收技术方案1. 背景介绍烟气是许多工业生产过程中产生的一种重要废气。
燃烧产生的烟气中含有大量的热量,如果不进行有效的回收利用,将会造成能源的浪费和环境的污染。
因此,烟气余热回收技术成为了重要的研究方向之一。
本文将介绍一种烟气余热回收技术方案,以实现高效能源利用和环境保护。
2. 技术原理该烟气余热回收技术方案基于换热原理,通过烟气与工艺流体之间的热量交换,实现热能回收。
具体的技术原理如下:1.烟气预处理:在烟气进入烟道前,对其进行预处理,去除大颗粒的烟尘和其他污染物,以确保烟气的净化程度和换热器的正常运行。
2.烟气与工艺流体换热:将烟气通过烟道引导至烟气换热器中,与工艺流体进行热量交换。
工艺流体可以是水、油等,在换热器内与烟气进行流体间的热交换,使烟气中的热量传递给工艺流体,从而实现热能的回收利用。
3.对工艺流体进行冷却:烟气中的热能传递给工艺流体后,工艺流体温度升高。
为了保证回收后的热能能够有效利用,需要对工艺流体进行冷却。
这可以通过使用冷却器或进行进一步的热量转移实现。
4.回收后的热能利用:冷却后的工艺流体可以用于供热、供暖或其他工业生产过程中的热能需求,从而实现能源的高效利用。
3. 技术优势该烟气余热回收技术方案具有以下优势:•高效能源利用:通过回收烟气中的热能,将原本浪费的能源转化为可用的能源,提高能源利用率。
•环境保护:减少煤、油等能源的消耗,降低二氧化碳等温室气体的排放,对环境具有积极的影响。
•经济效益:通过烟气余热的回收利用,降低了企业的能源消耗成本,提高了企业的经济效益。
•可持续发展:烟气余热回收技术是一种可持续发展的技术,有助于提高能源的可再生利用率,减少对自然资源的依赖。
4. 技术应用烟气余热回收技术可以应用于各个领域,包括但不限于以下几个方面:•工业生产:适用于钢铁、化工、电力等工业生产过程中产生的烟气,将烟气中的余热转化为工艺流体的热能需求,减少能源浪费。
•建筑供热:可将烟气余热应用于建筑供热系统中,为建筑提供温暖的供暖水源,减少传统能源的消耗。
干熄焦

1 定义及特征干熄焦余热发电技术,是指采用循环气体将红焦吹扫降温冷却,利用红焦的显热加热循环气体后,再由循环气体与余热锅炉进行换热,产生蒸汽用来发电的技术。
在这一过程中,循环气体在系统内循环吸热、放热,以间接换热介质的作用来完成整个系统的热量传递,最终实现回收红焦的显热进行发电的目的。
干熄焦余热发电技术具如下优势特征:(1)节能和经济效益在焦炉的热平衡中被红焦带走的热量相当于焦炉加热所需热量的37%,干熄焦可回收红焦热量的80%。
干熄焦过程中,被加热的循环气体经余热锅炉换热产生蒸汽,循环气体温度下降后,再循环使用,从而有效地利用红焦的显热,并可将回收的焦粉进行再利用;利用余热锅炉产生的高温高压蒸汽进入汽轮发电机组做功发电,最终将红焦的显热转换为电能,节能及经济效益十分明显。
(2)环境效益干熄焦采用循环气体在密闭的干熄炉内对红焦进行冷却,可以免除湿熄焦过程中酚、氰化合物和硫化合物等有害物质对周围设备的腐蚀和对大气的污染。
通过对焦粉的收集和处理,最后以高净化烟气排入大气。
(3)提高焦炭质量干法熄焦过程是在循环气体逆流换热的过程中缓慢而均匀进行的,它没有湿法熄焦过程中存在的剧冷作用,干熄焦后焦炭机械强度、耐磨性、反应后强度均有明显提高,反应性降低。
干熄焦过程中,因料层相对运动,增加了焦块之间的相互摩擦与碰撞,起到了焦炭的整粒作用,提高了焦块的均匀性。
焦炭在预存室保温相当于在焦炉中的闷炉,进一步提高焦块的成熟度,使其结构致密化。
(4)扩大炼焦煤源在保持原焦炭质量不变的条件下,采用干熄焦可以降低强粘结性的焦、肥煤配入量的10%~20%,有利于保护资源和降低焦炭成本。
2 系统构成干熄焦余热发电系统主要包括:干熄炉系统、气体循环系统、干熄焦余热锅炉系统、焦粉回收系统、红焦运输系统、冷焦运输系统、检修迁车台系统、地面环境除尘系统、空气压缩系统、汽轮机及发电机组系统、电站循环冷却水系统;电站化学水处理系统;站用电系统;电气接入系统;电站动控制系统;电站室外汽水管道系统;电站室外给水、排水、消防管网系统;以及为上述各系统配套土建、通讯、照明、环保、劳动安全与卫生、消防、供暖等辅助系统。
焦化热管余热回收系统的结构设计

焦化热管余热回收系统的结构设计
焦化热管余热回收系统是一种利用焦化炉废热进行能源回收的热能利用设备。
其结构设计主要包括余热烟气管道、余热烟气换热器、余热循环泵、余热蒸汽发生器、余热蒸汽管道、余热蒸汽负荷设备等组成部分。
1. 余热烟气管道
余热烟气管道是将焦化炉产生的热烟气引入到余热回收系统的管道,其设计要考虑到烟气的温度、流量和化学成分等因素。
管道应该具有耐高温、耐腐蚀的特性,同时要考虑到管道布置的合理性和安全性。
2. 余热烟气换热器
余热烟气换热器是将余热烟气中的热能传递给工作介质的设备,其设计应该考虑到换热器的材质、换热面积、换热效率以及清洗和维护的方便性等因素。
3. 余热循环泵
余热循环泵是用来将余热烟气换热器中的工作介质循环输送的泵,其设计应考虑到泵的扬程、流量、耐高温和耐腐蚀的特性,以及泵的运行稳定性和维护方便性等因素。
5. 余热蒸汽管道
余热蒸汽管道是将余热蒸汽输送到热负荷设备的管道,其设计要考虑到蒸汽的温度、压力和流量等参数,同时要考虑到管道的材质、布置和绝热措施等设计要求。
6. 余热蒸汽负荷设备
余热蒸汽负荷设备是利用余热蒸汽进行能源利用的设备,如锅炉、蒸汽发动机、热水供应系统等,其设计要考虑到设备的热效率、传热面积、蒸汽负荷和控制系统等设计要求。
烟气余热回收技术方案
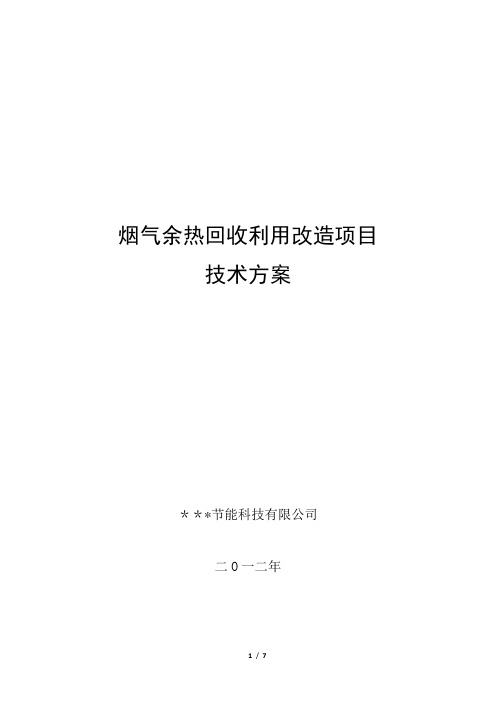
烟气余热回收利用改造项目技术方案***节能科技有限公司二O一二年一、运行现状锅炉房配备2.1MW锅炉2台(一用一备),供热面积5万m2;**炉配备2。
1MW 锅炉2台(一用一备),供热面积4。
5万m2。
经监测,**锅炉房2台锅炉正常运行排烟温度在150—-170℃,平均热效率在89%,**锅炉房2台锅炉正常运行排烟温度在160-180℃,平均热效率在88%,(标准应不高于160℃).锅炉系统运行进出水温差较小,排烟热损失较大,同时影响锅炉热效率的提高,回收利用潜力明显.二、技术介绍烟气冷凝回收利用技术是国家第一批特种设备节能技术推荐目录中的成熟技术。
有着显著的节能效益。
主要原理:1m3天然气燃烧后会放出9450kcal的热量,其中显热为8500kcal,水蒸气含有的热量(潜热)为950kcal。
对于传统燃气锅炉可利用的热能就是8500kcal的显热,供热行业中常规计算天然气热值一般以8500kcal/nm3为基础计算。
这样,天然气的实际总发热量9450kcal与天然气的显热8500kcal比例关系以百分数表示就为:111%,其中显热部分占100%,潜热部分占11%,所以对于传统燃气锅炉来说还是有很多热量白白浪费掉。
普通天然气锅炉的排烟温度一般在120—-250℃,这些烟气含有8%-—15%的显热和11%的水蒸气潜热。
加装烟气冷凝器的主要目的就是通过冷凝器把烟气中的水蒸气变成凝结水,最大限度地回收烟气中含有的潜热和显热,使回收热量后排烟温度可降至100℃左右,同时烟气冷却后产生的凝结水得到及时有效地排出(1 nm3天然气完全燃烧后,可产生1。
66kg水),并且大大减少了co2、co、nox等有害物质向大气的排放,起到了明显的节能、降耗、减排及保护锅炉设备的作用.从而达到节能增效的目的。
三、改造方案3.1、设备选型烟气余热回收器选用瑞典爱瑞科(AIREC)板式烟气热回收器。
瑞典AIREC公司是世界上唯一一家钎焊式模块化非对称流量板式换热器的专业生产制造商,凭借独到的设计理念,雄厚的产品开发能力和多年行业丰富的实践经验使AIREC成为在非对称流量换热领域的真正领导者.irCross21由多块板片重叠冲压在一起,在真空和高温的环境下,板片用铜或镍焊接在一起,具有很高的机械强度,更大的传热面积,更高的效率,更轻便小巧。
焦化厂焦炉烟道废气余热利用途径及设计方案

焦化厂焦炉烟道废气余热利用途径及设计方案1、热管技术:用热管余热锅炉回收焦炉烟道废气余热生产蒸汽技术,因其投资省,见效快而快速发展。
烟道废热余热回收生产蒸汽的工艺原理:热流体的热量由热管传给放热端水套管内的水,并使其汽化,所产汽—水混合物经蒸汽上升管达到汽包,经集中分离后再经蒸汽主控阀输出。
由于热管不断将热量输入水套管内的水,并通过外部汽—水管道的上升及下降完成基本的汽—水循环,达到将热流体降温,并转化为蒸汽的目的。
焦炉烟道废气余热生产蒸汽的工艺流程:在焦炉主烟道翻板阀前开孔,将焦炉主烟道废气引出,经调节型蝶阀入余热回收系统,换热降温后约170 ℃的烟气通过风机抽送,再经开关型蝶阀排入主烟道翻板阀后的地下主烟道,最后经焦炉烟囱排入大气。
锅炉水被加热后汽化,经汽包并计量后并入蒸汽管网,供各生产车间使用。
余热回收系统由软化水处理装置、除氧器、水箱、除氧给水泵、锅炉给水泵、热管蒸汽发生器、软水预热器汽包、上升管、下降管等组成。
其核心技术是热管技术回收烟气中的显热,将软化水加热成水蒸气,其工艺流程图如图图所示。
焦炉烟道废气余热回收生产蒸汽系统是一项节能减排工程,产生的饱和蒸汽可并入焦化厂蒸汽管网,供低压蒸汽用户使用。
2、煤调湿:煤调湿是将炼焦煤在装炉前除去一部分水分,保持装炉煤水分稳定在6%左右,然后装炉炼焦。
利用焦炉烟道废气煤调湿工艺不但可以节省能源,减少废气、废水、废热的排放,而且可以提高装炉煤堆密度及炼焦初期升温速度、缩短结焦时间,从而实现节能降耗的目的。
煤调湿装置的热源主要有导热油、蒸汽和焦炉烟道废气等。
相比较而言,以导热油和蒸汽为热源的煤调湿工艺存在设备繁琐、运行费用高等问题;以焦炉烟道废气为热源的煤调湿工艺可以利用废气余热干燥入炉煤,热效率高,节能效果好。
目前以焦炉烟道废气为热源的煤调湿工艺主要有流化床式、风动选择式和沸腾流化床式等。
2.1、流化床煤调湿:XXX厂采用焦炉烟道废气对煤料干燥的流化床煤调湿装置,其工艺流程为:将粉碎后的煤料由煤仓送往流化床干燥机,从分布板进入的焦炉烟道废气直接与煤料接触,对煤料进行干燥,调湿后的粗煤粒从干燥机排入螺旋输送机,剩余的煤粉随焦炉烟道废气进入袋式除尘器,回收的煤粉通过螺旋输送机送入皮带机上,为抑制扬尘,采用加湿机对干煤粉适当加湿,使煤粉和粗煤粒一起经皮带机送到焦炉煤塔,工艺流程图见下图。
- 1、下载文档前请自行甄别文档内容的完整性,平台不提供额外的编辑、内容补充、找答案等附加服务。
- 2、"仅部分预览"的文档,不可在线预览部分如存在完整性等问题,可反馈申请退款(可完整预览的文档不适用该条件!)。
- 3、如文档侵犯您的权益,请联系客服反馈,我们会尽快为您处理(人工客服工作时间:9:00-18:30)。
山西某煤焦化有限公司100万吨焦炉余热回收项目
技术方案
晋盛集团股份有限公司廊坊市晋盛节能技术服务有限公司烟气余热回收与脱硫脱硝集成化项目部2
目录一、前言二、余热锅炉技术方案三、余热回收工艺四、余热回收系统主要设备五、电气部分六、技术经济指标七、工程清单八、工程界区九、效益分析一、前言备煤车间送来的配合煤装入煤塔,装煤车按作业计划从煤塔取煤,经计量后装入炭化室内。煤料在炭化室内经过一个结焦周期的高温干馏制成焦炭并产生荒煤气。炭化室内的焦炭成熟后,用推焦车推出,经拦焦车导入熄焦车内,并由电机车牵引熄焦车到熄焦塔内进行喷水熄焦。熄焦后的焦炭卸至凉焦台上,冷却一定时间后送往筛焦工段,经筛分按级别贮存待运。煤在炭化室干馏过程中产生的荒煤气汇集到炭化室顶部空间,经过上升管、桥管进入集气管。约800℃左右的荒煤气在桥管内被氨水喷洒冷却至84℃左右。荒煤气中的焦油等同时被冷凝下来。煤气和冷凝下来的焦油等同氨水一起经过吸煤气管送入煤气净化车间。焦炉加热用的焦炉煤气,由外部管道架空引入。焦炉煤气经预热后送到焦炉地下室,通过下喷管把煤气送入燃烧室立火道底部与由废气交换开闭器进入的空气汇合燃烧。燃烧后的废气经过立火道顶部跨越孔进入下降气流的立火道,再经蓄热室,又格子赚把废气的部分显热回收后,经过小烟道、废气交换开闭器、分烟道、总烟道、烟囱排入大气。对于其中经总烟道进入烟囱热烟气的仍有较大的余热回收价值。为响应国家节能减排的号召,且从企业降低生产成本的目的出发,山西亚鑫煤焦化有限公司拟对现有100万吨/年焦炉烟道气的余热进行回收,目前该焦炉总耗煤气量约为180000Nm3/H,排烟温度约为260℃,大量热量被直接排入大气,能源浪费严重,而目前集团中蒸汽还存在较大缺口且入炉煤含水量较高,若能利用该部分热量产生蒸汽,就能达到节约煤气/降低生产成本的目的。4
具体项目方案设计如下:烟气先经过余热锅炉换热产生0.8mpa饱和蒸汽,出余热锅炉后温度降到160℃。焦炉已知参数:1、烟道气成分如下:CO2H20O2N2
6.4120.063.6869.85
2、烟气流量(Nm³/h):1500003、烟气温度(℃):210-2604、饱和蒸汽压力(mpa):0.8
设计参数:1、出余热锅炉烟气温度(℃):1702、余热锅炉设计蒸发量(t/h):4.2-7t/h3、余热锅炉设计压力(mpa):1.04、锅炉系统阻力(pa):<10005、烟气系统阻力(pa):<30005
二、余热锅炉技术方案余热回收工艺流程图
技术方案如下:该系统由热管蒸气发生器、软水预热器、汽包、上升管、下降管、外连管路和控制仪表等组成,并且互相独立。主要技术特点:1、地下烟道开孔技术:如何实现地下主烟道在焦炉正常行产情况下在线开孔,是本项目成功实施的第一关键。我公司根据多次地下烟道的开孔经验,成功总结出一套行之有效施工方案。6
地下烟道路截面尺寸如上图所示。7
开孔及布筋图支模示意图
支撑系统图
60×80木枋 =3001cm厚竹胶板@
@立杆 =1200@
梁底短管 =500
两侧支模短管 =500@
架管支撑系统
2、防止地下烟道、余热回收设备、引风机间环流形成的技术。由于地下烟道翻板阀与地下烟道周围的150-200的环隙,在风机工作的过程中,风机出口压头大于风机进口压头,且进口压头低于烟囱吸力,因此在设备烟气进口处与风机出口处间地下烟道有环流存在。经验告诉我们在这种情况下,增大风机功率是没有作用
φ48架管60×60×15木枋φ12对拉螺杆@700
水平施工缝3厚300宽钢板止水带φ14钢筋(L=100mm)与对拉螺杆焊接
与对拉螺杆焊接40×40×3钢板止水环
300竹胶板
50×70木枋@3008的,因为随风机功率的增加,其环量也在增加,其结局是或影响焦炉总烟道负压度从而影响焦炉的正常生产,或影响余热回收的正常产汽量,这也是一般设备制造厂家在焦炉余热回收上失败的原因之一。我们公司科学严谨的技术分析,在工艺设计上采取安全保障措施,从根本上避免了这一情况的发生。3、地下双烟道吸力不平衡调节技术。由于在实际生产过程中,两个地下烟吸力往往是不一致的,而风机的进口吸力是一样的,如何调整两个地下烟道吸是本项工程的另一关键技术。9
三、余热回收工艺1、烟气工艺流程在地下主烟道翻板阀前开孔,将主烟道300℃废热烟气从两条地下总烟道路引出,经钢制分烟道汇聚到钢制总烟道,经余热回收系统换热降温到160-170℃后,经锅炉引风机进入脱硫塔后再进入主烟道翻阀后的地下烟道,经烟囱排空。工艺系统组成:A地下总烟道;b地上钢制烟道;c余热锅炉系统;d引风机;e烟囱2、水汽系统工艺流程外来20℃的原水经过软化水处理系统,到软化水箱,由软化水箱经水泵进入除氧器,经除氧器除氧后。再由给水泵补入软水预热器,然后进入锅炉汽包,汽包水和蒸汽发生器内水自然循环,在汽包内蒸汽与水分离产生0.8MPa饱和蒸汽。1水系统的供水量每小时8吨,供水压力~0.3MPa,水源由软水总管供给软化水处理系统,然后经软化水箱进入除氧器,除氧器提供补水管,将处理后的水补给软水预热器。②系统软化水采用全自动软水器,他可将软水器运行及再生的每一个步骤实现自动控制并采用流量感应器来启动再生。③从软化水箱到除氧器和软水预热器的给水系统均配两台电动给水泵(均为一开一备),水泵扬程除满足系统压力外,还要克服水柱爬升高度及沿程阻力。④软水预热器、蒸汽发生器、汽包、软化水系统、除氧器均设有排污出水口,可定期清除内部残留污物及水垢。系统水箱设有给水取样;蒸汽聚集器设有水取样点,对换热器水进行取样。10
四、余热回收系统主要设备1、余热换热器系统换热器本体范围内的主要系统如下:(1)蒸汽及水加热系统:蒸汽输出;
汽水取样系统;给水系统;排污系统。(2)疏放水系统换热器本体范围内的各设备、管道的最低点设置疏、放水点,确保各下降管、省煤器、蒸发器等的进出口联箱疏、放水的畅通。(3)排污系统在蒸汽聚集器的盐段设连续排污,在水系统的下联箱设定期排污,排去适量的换热器污水以确保蒸汽品质。在换热器本体下部配置1台定期排污扩容器,排污降温池布置在换热器本体下部,且预留好排污降温池位置。(4)汽水取样系统--换热器本体汽水取样,取样系统包括:给水取样:PH值、电导率、O2
炉水取样:PH值、磷酸根、电导率
2、余热换热器系统设计:(1)换热器烟气进口至出口,烟气阻力小于1000Pa。(2)系统正常排污量不超过换热器给水流量的3%。(3)换热器疏放水系统能在一个小时内,将整台换热器的水以重力放空。11
(4)管道、阀门、排污扩容器及附件的设计压力和设计温度的确定符合标准规范有关确定。(5)负责提供换热器与其它设备之间的接口设计,并提供换热器接口清单表。(6)换热器设有水压试验接口,提供试验方法和详细说明(包括试验用水的水质和水温)。(7)换热器的取样点、监视点、排污点、放气点及停炉放水点全部带有根部阀,如为法兰连接配带反向法兰、垫片及紧固件。(8)供测量烟道及余热换热器本体各段温度的测量元件。(9)在符合设计条件及系统正常投运时,保证达到以下运行性能:①换热器在设计工况参数下能达到额定值。并保证长期安全运行,所有附件及配供的测控设备均能正常投运。②主蒸汽额定汽温偏差为±5℃,在可能运行的条件工况下,各段受热面的金属壁温都在允许范围之内。③换热器从启动到最大连续负荷范围内,水循环安全可靠。④换热器适用于露天布置,并采取适当防雨,避雷的措施。⑤换热器设计在定压运行下有良好的对负荷变动的适应性,在变负荷运行时,换热器应有足够的安全可靠性,以适应系统或控制装置在运行中产生的偏差。⑥换热器设计中有有效的停炉保护措施,并提供有关设备及系统3余热换热器汽水系统工艺及设备布置余热换热器包括:蒸发器一、蒸发器二、省煤器、共三组受热面以及蒸汽聚集器、热力除氧器。余热换热器采取立式布置,分成受热面部分和公用部分。4、换热器整体布置12
热管换热器分成热管联箱、热管支架、等组件。公用部分分成二层设置,均为钢结构。一层布置蒸发器、省煤器。二层布置蒸汽聚集器、热力除氧器设置在现有转运站一层内布置锅炉给水泵、除氧水泵,软水箱、汽水取样分析装置。蒸汽聚集器及内部装置蒸汽聚集器直段长度约为6000mm,两端相配椭球形封头,并设有人孔装置。筒体和封头的材料均为Q345R。该蒸汽聚集器通过两个支座(一个活动支座,一个固定支座)搁置在钢架梁上,蒸汽聚集器的中心线标高为12m。由省煤器来的水从蒸汽聚集器前部进入分配管。蒸汽聚集器内的汽水分离元件为均汽孔板和丝网捕沫器,布置在蒸汽聚集器顶部。蒸汽聚集器正常水位在蒸汽聚集器中心线以下100mm处,正常水位范围为±75mm。蒸汽聚集器内设有磷酸盐加药管、连续排污管、紧急放水管、再循环管。底部为集中下降管。在蒸汽聚集器上还设有双色水位计、压力表和安全阀(2个)等装置,以供换热器运行时监督、控制用。
5.设备设计、制造执行的标准和规程换热器的设计、制造、检验和验收必须符合相关国家标准:GB3087~2008无缝管材GB4457~4460—2003图样GB1800~1803—79公差与配合GB1182~1184—96形状和位置公差GB/T131—2006《机械制图表面粗糙度符号及其注法》GB3505—2009《表面粗糙、术语、表面及其参数》JB/T5994—92《装配通用技术要求》GB984—85《堆焊焊条》GB985—88《气焊、手工电弧焊及气体保护焊焊缝坡口的基本形式与尺寸》GB50235—2010《工业金属工程施工及验收规范》GB/T13237—91《优质碳素结构钢冷轧薄板和钢带》HG/T3181-2009《高频电阻焊螺旋翅片管》GB150-1998《钢制压力容器》JB4708-92《钢制压力容器焊接工艺评定》JB/T4730-2005《特种设备无损检测》GB5117-1995《碳钢焊条》