现代粉末冶金材料与技术的发展分析
粉末冶金材料的分类及应用

粉末冶金材料的分类及应用粉末冶金材料的分类及应用粉末冶金材料的分类及应用【摘要】粉末冶金材料有着传统熔铸工艺不能获取的独特化学成分及物理性能,且具有一次成型等特点,因此被广泛应用。
本文主要从粉末冶金材料的主要分类入手,重点对其应用进行了阐述,希望给行业相关人士一定的参考和借鉴。
【关键词】:粉末冶金;材料;分类;应用0.引言所谓的粉末冶金材料指的是用几种金属粉末或者金属与非金属粉末为原料,通过配比、压制成型以及烧结等特殊工艺制成的各类材料的总称,而这种与熔炼和铸造明显不同的工艺也被统称为粉末冶金法。
因其生产流程与陶瓷制品比较类似,所以又被称为金属陶瓷法。
就目前而言,粉末冶金法不单是用来制取某些特殊材料的方法,也是一种优质的少切屑或者无切屑方法,且其具有材料利用率高、生产效率高,节省占地面积及机床等优点。
然而粉末冶金法也并非万能之法,其无论是金属粉末还是模具都有着较高的成本,且制品的形状和大小都受到一定的限制。
1.粉末冶金材料的主要分类1.1传统的粉末冶金材料第一,铁基粉末冶金材料。
作为最传统也是最基本的粉末冶金材料,其在汽车制造行业的应用最为普遍,并随着经济的迅猛发展,汽车工业的不断扩大,铁基粉末冶金材料的应用范围也就变得越来越广阔,因此其需求量也越来越大。
与此同时,铁基粉末冶金材料对其他行业来说也非常重要。
第二,铜基粉末冶金材料。
众所周知,经过烧结铜基制作的零件抗腐蚀性相对来说比较好,且其表面光滑没有磁性干扰。
用来做铜基粉末冶金材料的主要材料有:烧结的青铜材质、黄铜材质以及铜镍合金材料等,此外还有少量的具有弥散性的强化铜等材质。
在现代,铜基粉末冶金材料主要备用到电工器件、机械设备零件等各个制造类领域中,同时也对过滤器、催化剂以及电刷等有一定的作用。
第三,难熔金属材料。
因这类材料的熔点、硬度、强度都比较高,因此其主要成分为难熔性的金属及金属合金复合材料,主要被应用国防、航空航天以及和研究领域等。
第四,硬质合金材料。
粉末冶金材料的力学性能研究

粉末冶金材料的力学性能研究在现代材料科学领域,粉末冶金作为一种重要的制备方法,已经为各种行业提供了广泛应用的材料。
粉末冶金材料由于其特殊的微观结构和化学成分,具有独特的力学性能,因此对其力学性能进行深入研究具有重要意义。
本文将探讨粉末冶金材料的力学性能研究内容,以及常用的测试方法和技术。
一、粉末冶金材料的力学性能研究内容粉末冶金材料的力学性能研究内容涉及多个方面,包括材料的强度、韧性、硬度、疲劳寿命等参数。
下面将分别对这些参数进行介绍。
1. 材料的强度强度是材料在外力作用下抵抗破坏的能力。
对于粉末冶金材料来说,强度与其组织结构和成分密切相关。
通过研究不同加工工艺对材料强度的影响,可以优化材料的力学性能。
2. 材料的韧性韧性是材料在受力时发生塑性变形的能力。
粉末冶金材料通常具有较好的韧性,这是由于微观结构中存在着各向异性的孔洞,有利于能量的吸收和分散。
3. 材料的硬度硬度是指材料抵抗外力压入的能力,通常用于评估材料的抗磨性能和耐磨性。
粉末冶金材料的硬度可以通过给定的压缩试验进行评估,也可以通过显微硬度测试等方法进行测量。
4. 材料的疲劳寿命疲劳寿命是指材料在交变载荷下破坏的周期数。
粉末冶金材料的疲劳寿命与材料的强度、韧性、孔洞等因素有关。
通过研究材料的疲劳寿命,可以为工程应用提供依据。
二、粉末冶金材料力学性能测试方法和技术为了研究粉末冶金材料的力学性能,需要采用一些有效的测试方法和技术,下面列举几种常用的方法:1. 压缩试验压缩试验是评估材料强度和硬度的常用方法。
通过在标准条件下施加压缩荷载,可以测量材料在压缩过程中的应变和应力,从而得到材料的力学性能参数。
2. 弯曲试验弯曲试验通常用于评估材料的韧性。
通过在标准条件下施加弯曲力,可以测量材料在弯曲过程中的应变和应力,从而评估材料的韧性水平。
3. 疲劳试验疲劳试验用于评估材料在交变载荷下的疲劳寿命。
通过在交变载荷下对材料进行循环加载,可以确定材料的疲劳强度和疲劳寿命。
2024年粉末冶金工艺的基本工序(2篇)

2024年粉末冶金工艺的基本工序1、原料粉末的制备。
现有的制粉方法大体可分为两类:机械法和物理化学法。
而机械法可分为:机械粉碎及雾化法;物理化学法又分为:电化腐蚀法、还原法、化合法、还原-化合法、气相沉积法、液相沉积法以及电解法。
其中应用最为广泛的是还原法、雾化法和电解法。
2、粉末成型为所需形状的坯块。
成型的目的是制得一定形状和尺寸的压坯,并使其具有一定的密度和强度。
成型的方法基本上分为加压成型和无压成型。
加压成型中应用最多的是模压成型。
3、坯块的烧结。
烧结是粉末冶金工艺中的关键性工序。
成型后的压坯通过烧结使其得到所要求的最终物理机械性能。
烧结又分为单元系烧结和多元系烧结。
对于单元系和多元系的固相烧结,烧结温度比所用的金属及合金的熔点低;对于多元系的液相烧结,烧结温度一般比其中难熔成分的熔点低,而高于易熔成分的熔点。
除普通烧结外,还有松装烧结、熔浸法、热压法等特殊的烧结工艺。
4、产品的后序处理。
烧结后的处理,可以根据产品要求的不同,采取多种方式。
如精整、浸油、机加工、热处理及电镀。
此外,近年来一些新工艺如轧制、锻造也应用于粉末冶金材料烧结后的加工,取得较理想的效果。
2024年粉末冶金工艺的基本工序(2)2024年的粉末冶金工艺基本工序包括精细化粉末的制备、粉末成型、烧结和后处理等四个环节。
下面将详细介绍这些工序的主要内容。
一、精细化粉末的制备精细化粉末的制备是粉末冶金工艺的第一步,关乎着制备出高质量的粉末。
2024年,精细化粉末的制备将会注重以下几个方面的发展:1.1 原料的选择与准备:2024年,随着科学技术的进步,矿石和废料等资源的利用效率将取得显著提高。
在制备粉末时,将更加注重对原料的选择与准备,使得原料的化学成分更加纯净,杂质含量更低。
1.2 粉末的粒度控制:粉末的粒度对材料的性能影响巨大。
粒度过大会影响材料的强度和塑性,而粒度过小则会降低流动性。
因此,粉末的粒度控制将成为2024年粉末冶金工艺中的重要研究方向。
现代粉末冶金技术概述PPT.
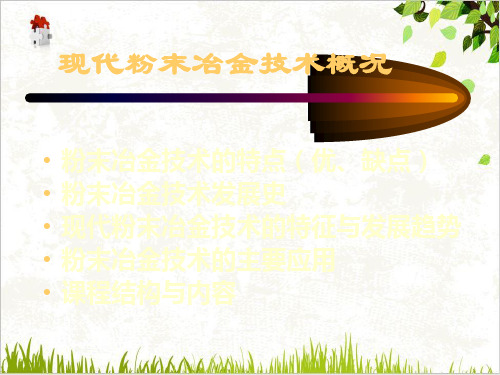
• PM Production of notch segment (槽型 件)for truck transmission
90
铸造 38
95
粉末冶金 28.5
85
冷成形 41
80
锻造
49
50 机械加工
82
100
0
材料利用率/%
0
100
零件的能耗/MJ·kg-1
各种生产工艺的材料的利用率与能耗
• 采用PM技术制备材料/产品的缺点:
❖ 1930年Hoganas公司开始用固相还原法 生产海绵铁。
块炼铁技术
• 随后出现Au(300年)、Ag、Cu、Sn (1000年)、 Pt粉及Pt块(1800年);
• 1910年Coolidge发明电灯W丝,奠定了近代粉 末冶金的基础;
• 1914年WC、MoC粉末出现(德国);
• 1927年德国Krupp公司生产硬质合金,导致了 金属切削技术的革命;
• 发展趋势
• 辐射领域越来越广 材料、应用
• 工艺过程的变异 粉末直接成形
• 多学科交叉点 技术手段、应用领域
• 朝特异性能、规模化、低成本方向 发展
粉末冶金技术的主要应用
▪ 粉末冶金零件市场
汽车工业是粉末冶金零件的最大应用市场
• 原料粉末价格较贵(Fe和Fe粉); • 成形模具成本高;靠产量规模降低费用; • 烧结制品残余孔隙影响性能; • 氧和杂质含量较高;制备高纯活性金属困
难;
粉末冶金技术发展史
❖ 公元前3000年以前,古埃及人使用陨铁; 公元前2300年左右出现块炼铁技术:固 相碳还原铁矿石(800~1000C)。通过 高温锻焊成各种器件。如公元300年左右 印度的Dehli Piller, 重6吨;我国西汉 (公元前113年)的刘胜墓出土的错金书 刀等。
现代冶金技术的种类和特点
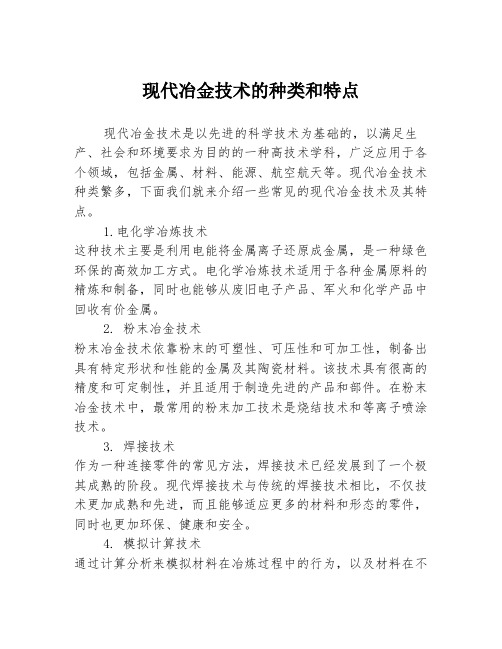
现代冶金技术的种类和特点现代冶金技术是以先进的科学技术为基础的,以满足生产、社会和环境要求为目的的一种高技术学科,广泛应用于各个领域,包括金属、材料、能源、航空航天等。
现代冶金技术种类繁多,下面我们就来介绍一些常见的现代冶金技术及其特点。
1.电化学冶炼技术这种技术主要是利用电能将金属离子还原成金属,是一种绿色环保的高效加工方式。
电化学冶炼技术适用于各种金属原料的精炼和制备,同时也能够从废旧电子产品、军火和化学产品中回收有价金属。
2. 粉末冶金技术粉末冶金技术依靠粉末的可塑性、可压性和可加工性,制备出具有特定形状和性能的金属及其陶瓷材料。
该技术具有很高的精度和可定制性,并且适用于制造先进的产品和部件。
在粉末冶金技术中,最常用的粉末加工技术是烧结技术和等离子喷涂技术。
3. 焊接技术作为一种连接零件的常见方法,焊接技术已经发展到了一个极其成熟的阶段。
现代焊接技术与传统的焊接技术相比,不仅技术更加成熟和先进,而且能够适应更多的材料和形态的零件,同时也更加环保、健康和安全。
4. 模拟计算技术通过计算分析来模拟材料在冶炼过程中的行为,以及材料在不同温度、应力和压强下的特性。
模拟计算技术配合实验测试,可以帮助冶金工程师更加深入地了解材料的性质和行为,更好地优化材料的工艺流程和加工工艺。
5. 热处理技术热处理技术涉及材料在高温或低温下的物理和化学性质的改变。
通过调整材料的温度、时间和冷却速度等参数,可以调整材料的硬度、强度、塑性和耐热等性能。
热处理技术广泛应用于各个领域,比如汽车、电子、航空、制造等。
通过不同的处理方式,可以制造出高强度、高硬度或高韧性的材料。
总之,现代冶金技术是一个充满活力和潜力的领域。
随着科技的进步和社会的发展,新的冶金技术和工艺将不断出现,为人类创造更加美好的未来。
金属粉末冶金在模具制造中的应用研究

金属粉末冶金在模具制造中的应用研究现代制造业的发展离不开高精度模具的应用,而金属粉末冶金技术作为一种先进的制造工艺,已经在模具制造领域发挥了重要作用。
本文将探讨金属粉末冶金在模具制造中的应用研究,包括其原理、优势以及面临的挑战。
一、金属粉末冶金的原理金属粉末冶金是利用金属粉末通过成型、烧结等工艺制备零件的技术。
其基本原理是将金属粉末与其他添加剂按一定比例混合,然后通过压制成型和烧结工艺,使金属粉末颗粒之间发生冶金结合,形成致密的金属零件。
金属粉末冶金技术具有灵活性强、材料利用率高、生产过程环保等优势。
通过调节金属粉末成分和粒度,可以实现不同材料性能的调控和优化。
因此,在模具制造中应用金属粉末冶金技术,可以有效提高模具的材料性能和使用寿命。
二、金属粉末冶金在模具制造中的应用1. 陶瓷模具制造金属粉末冶金技术在陶瓷模具制造中有广泛应用。
传统的陶瓷模具制造过程需要使用粘土等材料,且成本高、制作周期长。
而采用金属粉末冶金技术制造陶瓷模具,不仅可以提高模具的耐磨性和耐腐蚀性,还能够减少生产周期和成本。
2. 超硬模具制造超硬材料如金刚石、立方氮化硼等具有极高的硬度和耐磨性,常用于制造需要高度精密加工的工具。
金属粉末冶金技术可以制备具有高硬度的超硬合金材料,用于制造高效的模具。
这些模具不仅可以提高工具的寿命和加工效率,还可以降低加工过程中的能耗和废料产生。
3. 复合材料模具制造复合材料在航天航空、汽车、电子等行业得到了广泛应用。
而金属粉末冶金技术可以制备具有优良综合性能的复合材料模具,用于制造复杂的复合材料产品。
这些模具可以提供更高的加工精度和复杂度,满足现代工业对产品的多样化需求。
三、金属粉末冶金在模具制造中面临的挑战虽然金属粉末冶金技术在模具制造中具有广泛应用前景,但目前仍面临一些挑战。
首先,金属粉末的成本较高,制造成本较传统工艺高。
随着技术的进步和规模效应的发挥,相信金属粉末冶金技术的成本将会逐渐降低。
铝合金粉末冶金的研究及应用
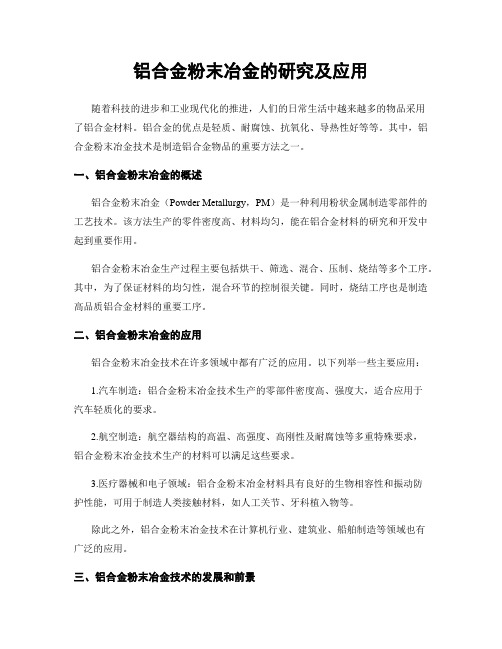
铝合金粉末冶金的研究及应用随着科技的进步和工业现代化的推进,人们的日常生活中越来越多的物品采用了铝合金材料。
铝合金的优点是轻质、耐腐蚀、抗氧化、导热性好等等。
其中,铝合金粉末冶金技术是制造铝合金物品的重要方法之一。
一、铝合金粉末冶金的概述铝合金粉末冶金(Powder Metallurgy,PM)是一种利用粉状金属制造零部件的工艺技术。
该方法生产的零件密度高、材料均匀,能在铝合金材料的研究和开发中起到重要作用。
铝合金粉末冶金生产过程主要包括烘干、筛选、混合、压制、烧结等多个工序。
其中,为了保证材料的均匀性,混合环节的控制很关键。
同时,烧结工序也是制造高品质铝合金材料的重要工序。
二、铝合金粉末冶金的应用铝合金粉末冶金技术在许多领域中都有广泛的应用。
以下列举一些主要应用:1.汽车制造:铝合金粉末冶金技术生产的零部件密度高、强度大,适合应用于汽车轻质化的要求。
2.航空制造:航空器结构的高温、高强度、高刚性及耐腐蚀等多重特殊要求,铝合金粉末冶金技术生产的材料可以满足这些要求。
3.医疗器械和电子领域:铝合金粉末冶金材料具有良好的生物相容性和振动防护性能,可用于制造人类接触材料,如人工关节、牙科植入物等。
除此之外,铝合金粉末冶金技术在计算机行业、建筑业、船舶制造等领域也有广泛的应用。
三、铝合金粉末冶金技术的发展和前景铝合金粉末冶金技术,在其其他领域的应用得到迅速发展和广泛应用的基础上,其研究和应用也逐步升级。
特别是随着高技术和智能化的应用,国内外铝合金粉末冶金技术也进一步提高和发展,成为新材料和科技的重要领域。
在当前的国际环境下,在“新能源、新技术、新材料”的背景下,铝合金粉末冶金技术发展具有广泛而重要的应用前景。
同时,铝合金粉末冶金技术也将成为我国未来工业发展的重要方向。
总之,铝合金粉末冶金技术的研究和应用在现代工业制造中具有重要意义。
随着科技的不断进步,其应用领域也在不断扩展,为我们的生活和经济发展带来更丰富的选择。
一体成型电感用软磁粉末应用现状及发展趋势

一体成型电感用软磁粉末应用现状及发展趋势一、内容描述随着电子技术的飞速发展,一体成型电感(InMold Electrolytic Capacitor,IMC)已经成为现代电子产品中不可或缺的关键元器件。
作为一种新型的电感技术,一体成型电感具有尺寸小、重量轻、性能优越等优点,因此在手机、平板电脑、笔记本电脑等消费电子产品中得到了广泛应用。
而软磁粉末作为一体成型电感的重要材料,其应用现状及发展趋势对于推动一体成型电感技术的发展具有重要意义。
本文首先介绍了一体成型电感的基本原理和结构特点,然后分析了软磁粉末在一体成型电感中的应用现状,包括原材料、生产工艺和性能测试等方面。
从市场需求和技术趋势两个方面对一体成型电感用软磁粉末的应用现状进行了详细阐述。
针对当前存在的问题和挑战,提出了一体化粉末冶金技术在一体成型电感制造中的应用前景,以期为我国一体成型电感产业的发展提供有益的参考。
A. 研究背景和意义一体成型电感(InMold Integrated Inductance,简称IML)是一种新型的电感技术,它将电感器与基板一体化制造,具有更高的可靠性、更小的尺寸和重量以及更好的散热性能。
随着电子行业的发展和对高性能、低功耗电子器件的需求不断增加,一体成型电感技术在各个领域得到了广泛的应用。
传统的软磁粉末材料在一体成型电感中的应用仍存在一些问题,如粉末颗粒尺寸较大、烧结过程中易产生气孔等,这些问题限制了一体成型电感性能的进一步提升。
研究和开发适用于一体成型电感的新型软磁粉末材料具有重要的理论和实际意义。
研究和开发适用于一体成型电感的新型软磁粉末材料有助于提高一体成型电感的整体性能。
通过优化粉末的成分和工艺参数,可以实现对粉末颗粒尺寸、磁性强度、矫顽力等性能的精确控制,从而提高一体成型电感的磁性能、饱和感应强度和温升等关键性能指标。
新型软磁粉末材料还可以通过引入具有特殊功能的纳米颗粒或功能基团来实现对一体成型电感的特殊性能要求,如高导热性、高耐腐蚀性等。
- 1、下载文档前请自行甄别文档内容的完整性,平台不提供额外的编辑、内容补充、找答案等附加服务。
- 2、"仅部分预览"的文档,不可在线预览部分如存在完整性等问题,可反馈申请退款(可完整预览的文档不适用该条件!)。
- 3、如文档侵犯您的权益,请联系客服反馈,我们会尽快为您处理(人工客服工作时间:9:00-18:30)。
现代粉末冶金材料与技术的发展1 概述粉末冶金是研究金属、合金、非金属和化合物的粉末及其材料的性质和制造理论与工艺的技术科学,是现代材料科学与工程发展最为迅猛的领域之一。
近代以来, 粉末冶金有了突破性进展,在西方发达国家更呈现出了加速发展的势态, 一系列新技术、新工艺大量涌现,例如, 超微粉或纳米粉制备技术、快速冷凝技术、机械合金化、粉末热等静压、温压、粉末热锻、粉末挤压、粉末注射形、粉末喷射成形、自蔓延高温合成、涂层技术、电火花烧结、反应烧结、超固相线烧结、瞬时液相烧结、激光烧结、微波烧结, 等等。
现代粉末冶金不但保持和发展了传统优点—实现少切削、无切削加工, 实现少偏析或无偏析, 低耗、节能、节材;易控制产品孔隙度;易实现金属一非金属复合、金属一高分子复合, 而且新技术赋予传统工艺步骤以新的内容和含义, 使粉末冶金成为制取各种高性能结构材料、特种功能材料和极限条件下工作材料的有效途径。
因此, 整个粉末冶金领域大大拓宽, 并向着纵深方向发展, 粉末冶金已由二类传统工艺技术发展成为一门新兴的技术科学, 它处于冶金科学与材料科学的交汇区, 并且已深入地渗透到几乎所有的冶金和材料科学的分支科学中去了。
由于技术上和经济上具有巨大的优越性,粉末冶金技术产品在国民经济的各个部门和国防建设的各个领域都得到了广泛应用, 对机械、电子、化工、能源、航空、航天乃至农业、医药、食品等产业的发展以及科技的进步, 都起到了重要的推动作用, 创造了巨大的社会财富, 带来了巨大的经济效益和社会效益。
2 现代粉末冶金发展的主要特点(一)新技术、新工艺大量涌现新技术新工艺的应用, 使得粉末的制备朝着超微、超细、速凝、高纯、均质、成分可调控、大规模、多品种方向发展, 粉末冶金材料的制造朝着复合、全致密、高性能、高精度、复杂形状、大批量系列化方向发展。
(二)新材料层出不穷粉末冶金已发展成为制取各种高性能结构材料和特种功能材料以及极限条件使用材料的有效途径。
这些新材料包括粉末低合金钢、粉末高温合金、粉末高速钢、粉末不锈钢、快速冷凝铝合金、快速冷凝钦合金、弥散强化合金、高温超导材料、钦铁硼永磁材料、特种陶瓷、金属基和陶瓷基复合材料、纳米材料、梯度功能材料、粉末摩擦材料、涂层硬质合金,等等。
(三)近净型成形技术的崛起加速了粉末冶金的迅速发展粉末冶金作为一项典型的近净型成形制造技术, 以它独有的少切削、无切削及节材、节能的技术特点, 在与传统的熔铸、机加工竞争中不断发展。
近几十年来,许多新的近型成形技术不断涌现, 如金属注射成形、粉末喷射成形、粉末热锻和粉末热等静压等使得粉末冶金产品更加接近最终产品形状, 并且拓宽了粉末冶金近型成形产品的范围。
(四)复合材料及其制造技术的发展为粉末冶金开拓了新的领域目前, 复合材料的发展形成由宏观复合形式向微观复合形式发展、由结构复合材料为主向与功能复合材料并重的局面。
粉末冶金以它独有的粉末混合、化学复合、机械合金化、涂层、骨架熔渗与浸溃、纤维网粉浆浇注、快速冷凝和原位复合等特长在复合材料制造中充分发挥自己的优势, 在金属基、陶瓷基复合材料和弥散强化、颗粒强化及纤维增强复合制造技术中显示鲜明的特色。
3 粉末冶金材料3.1 传统粉末冶金材料(1)铁基粉末冶金材料:铁基粉末冶金材料是最重要的粉末冶金材料之一, 特别是汽车行业的快速发展对铁基粉末冶金行业起了很大的推动作用。
(2)铜基粉末冶金材料:烧结铜基零件具有较好的耐蚀性、表面光洁及无磁性等优点。
铜基材料主要有烧结青铜(锡青铜和铝青铜) 、烧结黄铜、烧结镍银和烧结铜镍合金, 此外还有弥散强化铜(如Cu2Al2O3 ) 、烧结时效强化铜合金(Cu2Be 、Cu2Be2Co和Cu2Cr合金)以及用于减震的烧结Cu2Mn合金。
(3)难熔金属与硬质合金:难熔金属(钨、钼、钽、铌等) 及其合金、复合材料以其高熔点、高硬度、高强度等独特的物理与力学性能而广泛应用于国防军工、航空航天、电子信息、能源、防化、冶金和核工业等领域。
硬质合金是指以一种或多种难熔金属的碳化物(如碳化钨、碳化钛等) 作为硬质相, 用金属粘结剂作为粘结相, 经粉末冶金技术制造出来的材料。
硬质合金广泛用作切削刀具、矿用刀片和异型件, 已成为现代工业部门和新技领域不可缺少的工具材料, 被誉为“现代工业的牙齿”。
(4)粉末冶金电工材料:在电器、仪表及电工技术中, 广泛应用于各种分断和接通电路的电接触元件、电阻焊用的电极以及电机上用于转换电流的电刷。
在无线电技术中, 普遍使用各种难熔化合物制成的各种固定电阻器。
在真空技术中使用各种电子管阴极制品、各种电加热元件和热电偶材料。
以上这些材料常常采用粉末冶金技术制造, 统称为粉末冶金电工材料。
(5)烧结摩擦与减摩材料:摩擦材料以提高摩擦磨损性能为目的, 用于摩擦离合器与摩擦制动器的摩擦部分的材料称为摩擦材料。
烧结减摩材料是用粉末冶金方法制造的、具有低摩擦系数和高耐磨性能的金属材料或金属和非金属的复合材料。
3.2 先进粉末冶金材料(1)信息领域用粉末冶金材料:粉末冶金软磁材料按材质分类可分为金属软磁材料和铁氧体软磁材料。
铁氧体软磁材料出现较早, 是一种只能用粉末冶金烧结方法制造的软磁材料。
人们期望烧结软磁材料具有高的磁导率和饱和磁化强度或剩磁以及低的矫顽力,压粉磁芯或磁粉芯属于这一类材料。
金属软磁材料主要是铁及其合金, 其中有纯铁、磷铁、硅钢、铁镍金、铁钴合金、铁铝合金和铁铝硅合金等。
铁氧体软磁主要有锰锌、镁锌、镍锌铁氧体软磁材料。
(2)能源领域用粉末冶金材料:能源材料是指那些正在发展的、可能支撑新能源体系的建立,满足各种新能源以及节能新技术所要求的一类材料。
按使用目的可分为新能源材料、节能材料和储能材料。
(3)生物领域用粉末冶金材料:生物医用材料对于挽救生命、救治伤残、提高人类的生活质量具有重要的意义。
生物材料中的一些医用金属和合金, 医用生物陶瓷就属于粉末冶金材料。
(4)军事领域用粉末冶金材料:粉末冶金材料对军事工业作出了巨大的贡献, 在国防建设中有着巨大的潜力和竞争力。
粉末冶金材料广泛用于航空航天工业、核工业和兵器工业等军事领域。
4 粉末冶金技术4.1 粉末制备技术的发展粉末冶金材料和制品不断增多, 质量不断提高, 要求提供的粉末的种类也越来越多。
为了满足对粉末的各种要求, 出现了各种各样生产粉末的新方法。
从过程的实质来看, 现有制粉方法大体上可归纳为两大类, 即机械法和物理化学法。
从工业规模而言, 应用最广泛的是还原法、雾化法和电解法。
但随着科技的发展, 越来越多的新技术在粉末的制备过程中正起着越来越重要的作用。
(1)机械合金化:机械合金化是由Benjamin 等提出的一种制备合金粉末的高能球磨技术。
它是在高能球磨条件下, 利用金属粉末混合物的反复变形、断裂、焊合、原子间相互扩散或发生固态反应形成合金粉末。
机械合金化是在固态下实现合金化, 不经过气相、液相,不受物质的蒸气压、熔点等物理特性因素的制约, 使过去用传统熔炼工艺难以实现的某些物质的合金化和远离热力学平衡的准稳态、非平衡态及新物质的合成成为可能, 因此机械合金化的理论和应用方面的研究均显示出十分诱人的前景。
(2)喷雾干燥:喷雾干燥是指用雾化器将一定浓度的原料液喷射成雾状液滴, 并用热空气(或其它气体) 与雾滴直接接触的方式使之迅速干燥, 从而获得粉粒状产品的一种粉末制备过程。
采用喷雾干燥可以制备出质量均一、重复性良好的粉料, 并且缩短粉料的制备过程, 有利于自动化、连续化生产, 是大规模制备优良超微粉的有效方法。
4.1 粉末冶金成型技术的发展目前, 粉末冶金技术正向着高致密化、高性能化、集成化和低成本等方向发展。
近年来, 一系列粉末冶金新的成形技术层出不穷, 并呈现出加速发展态势, 粉末注射成形、温压成形、流动温压成形、喷射成形、高速压制成形等新技术不断涌现, 使得粉末高致密化成形技术得到了很大的发展。
(1)粉末注射成型:粉末注射成形是传统粉末冶金技术和先进塑料注射成形相结合而发展形成的一门新型粉末冶金近净成形技术。
它的基本工艺过程是: 首先将金属或陶瓷粉末与有机粘结剂均匀混合, 用注射成形机成形, 然后将成形坯中的粘结剂脱离, 最后经烧结致密化得到最终产品。
粉末注射成形的材料已经从早期的铁基、硬质合金、陶瓷等对杂质含量不敏感、性能要求不是非常苛刻的体系, 发展到了镍基高温合金、钛合金和铌材料。
材料应用领域也从结构材料向功能材料发展, 如热沉材料、磁性材料和形状记忆合金。
材料结构也从单一均匀结构向复合结构发展。
(2)温压成型:温压成形是从20 世纪90 年代新发展起来的一项新技术。
它是采用特制的粉末加热、粉末输送和模具系统, 将加有特殊润滑剂的混合粉末和模具加热至130~150 ℃温度进行刚性模压, 最后采用传统的烧结工艺进行致密化的技术。
利用该工艺可成形形状非常复杂的零件,如垂直于压制方向上的凹槽、孔以及螺纹孔等,而不需要后续二次机械加工。
(3)喷射成型:喷射成形(Spray Forming) 技术, 也称为喷射沉积( Spray Deposition) 或喷射铸造( Spray Casting ) 技术, 这是20 世纪80 年代以来工业发达国家在传统快速凝固P粉末冶金(RSPPM) 工艺基础上发展起来的一种全新的先进材料制备与成形技术。
(4)高速压制成型:高速压制技术是瑞典H¨ogan¨as AB 公司在2001 年推介的一种新技术。
高速压制生产零件的过程和传统的压制过程工序相同; 混合粉末加进送料斗中, 粉末通过送粉靴自动填充模腔压制成形之后, 零件被顶出并转入烧结工序。
所不同的是高速压制的压制速度比传统压制高500~1000 倍, 压机锤头速度高达2~30mPs , 液压驱动的锤头质量达5~1200kg , 粉末在0.02s 之内通过高能量冲击进行压制, 压制时产生强烈的冲击波。
通过附加间隔0.3s 的多重冲击能达到更高的密度。
与传统压制相比, 高速压制的铁基零件密度可提高0.3gPcm3 左右, 因而抗拉强度和屈服强度能相应地提高20 %~25 %。
高速压制压坯的径向弹性后效很小, 故脱模压力较小, 并且压坯密度均匀, 其偏差小于0.01gPcm3 。
该技术可以制得质量达5kg 以上的大型压坯以及高径比达到3 的压坯。
同时, HVC 技术还具有高生产率和低成本等特点。
4.1 粉末冶金烧结技术的发展粉末冶金烧结是指粉末或粉末压坯在适当的温度和气氛条件下加热所发生的现象或过程。
烧结工艺是决定粉末冶金制品性能的重要环节, 一直是人们研究的重点; 各种促进烧结的方法不断涌现, 如微波烧结、放电等离子烧结、自蔓延高温合成、烧结硬化等。