板类结构铸钢件平浇冒口设计的探讨
冒口设计参考
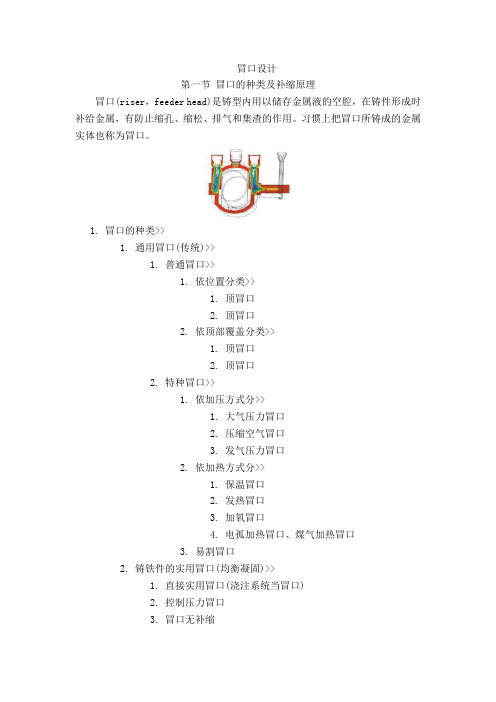
冒口设计第一节冒口的种类及补缩原理冒口(riser,feeder head)是铸型内用以储存金属液的空腔,在铸件形成时补给金属,有防止缩孔、缩松、排气和集渣的作用。
习惯上把冒口所铸成的金属实体也称为冒口。
1.冒口的种类>>1.通用冒口(传统)>>1.普通冒口>>1.依位置分类>>1.顶冒口2.顶冒口2.依顶部覆盖分类>>1.顶冒口2.顶冒口2.特种冒口>>1.依加压方式分>>1.大气压力冒口2.压缩空气冒口3.发气压力冒口2.依加热方式分>>1.保温冒口2.发热冒口3.加氧冒口4.电孤加热冒口、煤气加热冒口3.易割冒口2.铸铁件的实用冒口(均衡凝固)>>1.直接实用冒口(浇注系统当冒口)2.控制压力冒口3.冒口无补缩2.冒口形状冒口的形状有圆柱形、球顶圆柱形、长(腰)圆柱形、球形及扁球形等多种3.通用冒口补缩原理>>1.基本条件>>1.冒口凝固时间大于或等于铸件(被补缩部分)的凝固时间2.有足够的金属液补充铸件的液态收缩和凝固收缩,补偿浇注后型腔扩大的体积3.在凝固期间,冒口和被补缩部位之间存在补缩通道,扩张角向着冒口2.选择冒口位置的原则>>1.冒口应就近设在铸件热节(hotspot)的上方或侧旁2.冒口应尽量设在铸件最高、最厚的部位。
对低处的热节增设补贴或使用冷铁,造成补缩的有利条件3.冒口不应设在铸件重要的、受力大的部位,以防组织粗大降低强度4.冒口位置不要选在铸造应力集中处,应注意减轻对铸件的收缩阻碍,以免引起裂纹5.尽量用一个冒口同时补缩几个热节或铸件6.冒口布置在加工面上,可节约铸件精整工时,零件外观好7.不同高度上的冒口,应用冷铁使各个冒口的补缩范围隔开3.冒口有效补缩距离的确定>>冒口的有效补缩距离为冒口作用区与末端区长度之和,它是确定冒口数目的依据,与铸件结构、合金成分及凝固特性、冷却条件、对铸件质量要求的高低等多种因素有关,简称为冒口补缩距离1.铸钢件冒口的补缩距离有色合金的冒口补缩距离外冷铁的影响补贴(padding)的应用第二节铸钢件冒口的设计与计算铸钢件冒口属于通用冒口,其计算原理适用于实行顺序凝固的一切合金铸件。
精密铸造铸件工艺及浇冒口系统设计

第六章铸件工艺设计第一节概述为了生产优质而价廉的包模铸件,做好工艺设计是十分重要的。
在做工艺设计之前,首先要考虑选用包模铸造工艺生产时,在质量、工艺和经济方面的几个问题。
1.铸件质量的可靠性对于铸件质量上的要求,一般是包括两个方面,一是保证技术要求的尺寸精度、几何精度和表面光洁度,二是保证机械性能和其它工作性能等内在质量方面的要求。
包模铸造具有少切削、无切削的突出优点。
近年来,由于冶金技术、制模、制壳材料和工艺以及检测技术等方面的发展,包模铸件的外部和内在质量不断提高,所以它的应用范围愈来愈广。
不少锻件、焊接件、冲压件和切削加工件,都可以用熔模铸造方法生产。
这对于节约机械加工工时和费用,节约金属材料,提高劳动生产率和降低成本都具有很大意义。
但是,熔模铸造生产的铸件,由于冶金质量、热型浇注引起的晶粒粗大、表面脱碳以及内部缩松等方面的原因,铸件的机械性能(尤其是塑性),还存在一些缺陷。
对于某些受力大和气密性要求高的铸件,采用包模铸造时,应充分考虑零件在产品上的作用和性能要求,以确保其使用可靠。
有些结构件改用包模铸造生产时,必须考虑原用合金的铸造性能是否能满足零件的质量要求,否则就需要更改材质。
2.生产工艺上的可能性和简易性熔模铸造虽然可以铸造形状十分复杂的、加工量甚少甚至不加工的零件,但零件的材质、结构形状、尺寸大小和重量等,必须符合熔模铸造本身的工艺要求。
如铸件最小壁厚、最大重量、最大平面面积、最小孔槽以及精度和光洁度要求等,都要考虑到工艺上的可能性和简易性。
3.经济上的合理性采用包模铸造在经济上是否合理,要从多方面考虑。
按每公斤的价格来说,包模铸件与同类型锻件相近甚至还高些,但是由于大幅度减少了加工量,因而零件最终成本还是低的。
但也有些零件,可以利用机械化程度较高的方法生产,例如用自动机床高速加工、精密锻造、冷挤压、压力铸造等等,这时,用包模铸造法生产在经济上的优越性就不一定显著,甚至成本还可能高一些,所以在这种情况下,就不一定选用这种方法了。
精密铸造铸件工艺与浇冒口系统设计
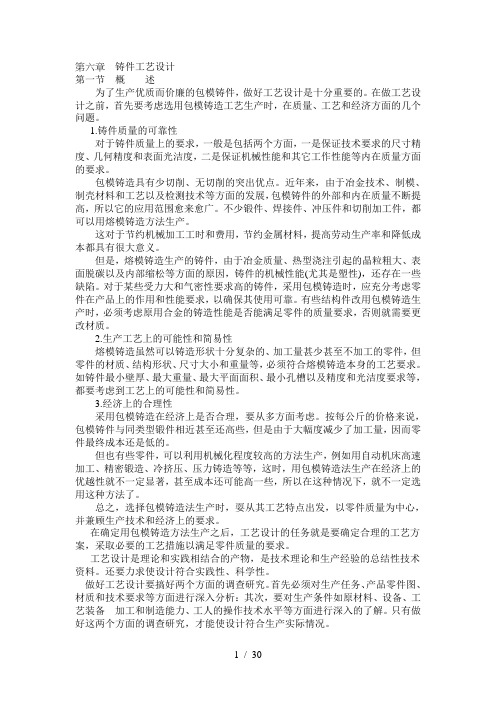
第六章铸件工艺设计第一节概述为了生产优质而价廉的包模铸件,做好工艺设计是十分重要的。
在做工艺设计之前,首先要考虑选用包模铸造工艺生产时,在质量、工艺和经济方面的几个问题。
1.铸件质量的可靠性对于铸件质量上的要求,一般是包括两个方面,一是保证技术要求的尺寸精度、几何精度和表面光洁度,二是保证机械性能和其它工作性能等内在质量方面的要求。
包模铸造具有少切削、无切削的突出优点。
近年来,由于冶金技术、制模、制壳材料和工艺以及检测技术等方面的发展,包模铸件的外部和内在质量不断提高,所以它的应用范围愈来愈广。
不少锻件、焊接件、冲压件和切削加工件,都可以用熔模铸造方法生产。
这对于节约机械加工工时和费用,节约金属材料,提高劳动生产率和降低成本都具有很大意义。
但是,熔模铸造生产的铸件,由于冶金质量、热型浇注引起的晶粒粗大、表面脱碳以及内部缩松等方面的原因,铸件的机械性能(尤其是塑性),还存在一些缺陷。
对于某些受力大和气密性要求高的铸件,采用包模铸造时,应充分考虑零件在产品上的作用和性能要求,以确保其使用可靠。
有些结构件改用包模铸造生产时,必须考虑原用合金的铸造性能是否能满足零件的质量要求,否则就需要更改材质。
2.生产工艺上的可能性和简易性熔模铸造虽然可以铸造形状十分复杂的、加工量甚少甚至不加工的零件,但零件的材质、结构形状、尺寸大小和重量等,必须符合熔模铸造本身的工艺要求。
如铸件最小壁厚、最大重量、最大平面面积、最小孔槽以及精度和光洁度要求等,都要考虑到工艺上的可能性和简易性。
3.经济上的合理性采用包模铸造在经济上是否合理,要从多方面考虑。
按每公斤的价格来说,包模铸件与同类型锻件相近甚至还高些,但是由于大幅度减少了加工量,因而零件最终成本还是低的。
但也有些零件,可以利用机械化程度较高的方法生产,例如用自动机床高速加工、精密锻造、冷挤压、压力铸造等等,这时,用包模铸造法生产在经济上的优越性就不一定显著,甚至成本还可能高一些,所以在这种情况下,就不一定选用这种方法了。
冒口的计算

冒口的计算1)冒口设计原理铸件冒口主要在铸钢件上使用。
铸铁件只用于个别的厚大件的灰铸铁件和球铁件上。
金属液在液态降温和凝固过程中,体积要收缩。
铸件的体收缩大约为线收缩的3倍。
因此,铸钢的体收缩通常按3---6%考虑,灰铸铁按2---3%,不过由于灰铸铁和球墨铸铁凝固时的石墨化膨胀,可以抵消部分体积收缩,所以如果壁厚均匀,铸型紧实度高,通常不需要设计冒口。
冒口补缩铸件是有一定的范围叫有效补缩距离,设为L对厚度为h的板状零件通常L=3-5h 。
对棒状零件L=(25-30)/h式子中,h-铸件厚度2)冒口尺寸的基本计算方法冒口计算介绍如下。
最常用的方法是,冒口直径 D=d0+h当铸件存在热节时,可以把h换成热节的直径T即可即D=do+T 。
冒口颈是冒口和铸件的连接通道,冒口里的金属液都是经由冒口颈补缩到铸件里的对冒口颈的截面是有要求的,通常取冒口颈的直径 dj=(0.6-0.8)T 。
冒口高度 H=(1.5-2.5)D 。
H的高度还应该考虑要高于需要补缩部位的高度,否则就成了反补缩了,铸件补缩了冒口,这是要避免的。
3)其它计算方法常用的经验计算方法还有不计算需要估算补缩的金属液,直接将热节园的直径乘个系数得出冒口直径。
例如简单件D=(1.05-1.15)T 外形简单,热节比较集中。
复杂件D=(1.40-1.80)T 外形复杂,例如有许多筋条和铸件的其余部分连接。
中间件D=(1.15-1.40)T 介于以上两种之间。
铸造生产的条件千差万别,因素太多,以至于所有的计算公式都是近似的有条件的。
往往一个公式不一定适用于所有的场合。
所以公式中往往有取值范围较大的系数供用户结合本单位的情况选择。
铸件冒口设计的原则及方法

图 4 冒口放在两热节之间的工艺对比
放在最后凝固的部位和几何热节处,形成 的接触热节和冒口补缩液流通效应的影 响,会使冒口安放处铸件的凝固时间延长, 相应增加对冒口补缩时间的要求,同时也 对热节处的内在质量产生不利的影响。为 此,文献[4]提出了动态顺序凝固的概念。 动态顺序凝固是指冒口离开热节,放在近 热节处,利用冒口根处形成的接触热节和 冒口补缩液的流通效应,实现铸件各部分 朝向冒口的顺序凝固。其实质是使铸件的 几何热节与设置冒口形成的接触热节相分 离,并控制次热节处所形成的接触热节,使 其凝固模数比几何热节的大,比冒口的小, 将凝固顺序由薄壁→次热节→几何热节→ 几何热节处的接触热节→冒口,改变为薄 壁→几何热节→次热节处的接触热节→冒 口,既避免了接触热节处热量过分集中,又 利用接触热节的热效应,在冒口和几何热 节之间形成补缩通道,保证冒口对几何热 节的补缩。
采用模数法计算出的冒口体积,应该
用补缩液量法进行校核,即冒口体积 V 应 r
满足式(1)。
3.2 热节圆比例法
热节圆比例法是一种经验性方法。采
用作图法或几何公式计算出热节圆直径 T, 然后根据铸件不同截面形状确定例系数α的数值多来源于工程实
科技创新导报 Science and Technology Innovation Herald
101
科技创新导报 2008 NO.27 Science and Technology Innovation Herald
工 程 技 术
图 5 冒口直径与铸件厚度热节圆直径的 关系
使膨胀压力得以控制,避免铸型扩大,一般
铸件凝固过程中,冒口液面不断下降, 体积减少,散热表面积增加,冒口模数动态
变小;铸件获得补缩液体后热量增加,凝固
薄壁铸钢件工艺设计探讨

薄壁铸钢件工艺设计探讨摘要:薄壁铸钢件在生产过程中容易出现裂纹、缩孔、浇不足以及砂气孔缺陷,其生产工艺与一般铸钢件的生产工艺不同,凝固过程不但要遵循顺序凝固原则,且要兼顾同时凝固原则。
本文根据笔者多年从事此类的设计开发经验,结合我厂在实际生产中几个典型薄壁铸钢件产品的生产情况,提出对薄壁铸钢件在工艺设计中一些问题的探讨和对该类型产品在设计中一些注意要点进行归纳和总结。
关键词:薄壁铸钢件、工艺设计、裂纹、顺序凝固一、前言薄壁铸钢件的生产是一个系统复杂的工程,其凝固过程复杂,铸造过程影响因素很多,质量控制难度大,常易出现裂纹、变形、浇不足以及砂气孔问题。
因此,对于薄壁铸钢件的工艺设计方法和思路与一般的铸钢件的设计有着较大的不同。
其工艺设计更注重要求合理的地开设浇冒口,布置冷铁、拉筋,最大限度减少砂芯、砂型在凝固收缩过程中产生的阻力。
笔者根据多年以来从事此类的设计开发经验,对该类型产品生产过程中常见问题的成因进行分析,在设计上合理实施工艺对策,在消除和减少薄壁铸钢件在生产过程中常见问题的产生方面获得了一些经验。
本文以我厂生产实际中的几个典型薄壁铸钢件产品为例,重点阐述薄壁铸钢件工艺设计的思路和方法,以及对生产过程中常见问题的成因分析及一些解决措施进行归纳总结。
二、薄壁铸钢件工艺设计的一般思路1.产品结构及技术条件分析作为铸造生产厂,多数以根据用户提供的产品图纸做用户所需产品,笔者经过多年时间的设计开发经历感觉到,在用户提供的这些产品图纸中,产品结构往往与我们铸造工作者希望适合铸造产品结构有时会存在一些炯意。
尤其对于薄壁铸钢件来说,其产品结构设计如果对铸造不合理,我们铸造工作者可能会花费很多精力和想很多办法去解决由于结构不合理产生的铸造缺陷,往往这些问题最终得不到彻底的解决。
笔者认为,对于薄壁铸钢的生产,前期的产品结构分析是很重要的,铸造工作者在不影响产品最终使用和其结构强度的情况下,是可以适当与用户沟通,争取提出一些结构上的改进和建议,笔者多年以来在这些方面有过切身的体会,并在这些方面取得了一些进步。
重力浇铸冒口设计原则
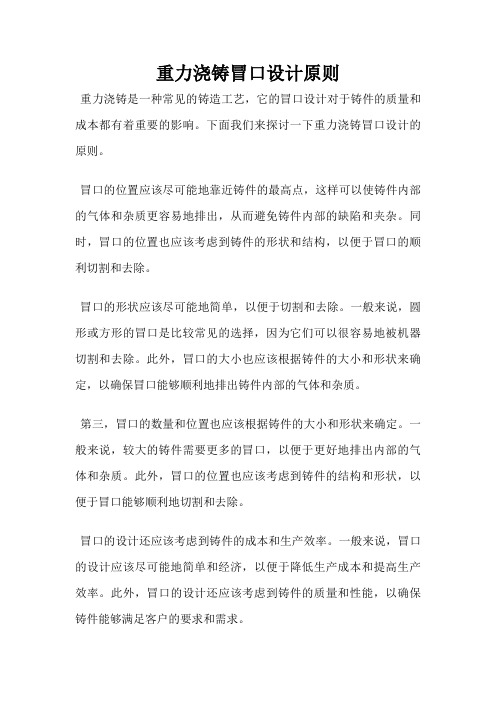
重力浇铸冒口设计原则
重力浇铸是一种常见的铸造工艺,它的冒口设计对于铸件的质量和成本都有着重要的影响。
下面我们来探讨一下重力浇铸冒口设计的原则。
冒口的位置应该尽可能地靠近铸件的最高点,这样可以使铸件内部的气体和杂质更容易地排出,从而避免铸件内部的缺陷和夹杂。
同时,冒口的位置也应该考虑到铸件的形状和结构,以便于冒口的顺利切割和去除。
冒口的形状应该尽可能地简单,以便于切割和去除。
一般来说,圆形或方形的冒口是比较常见的选择,因为它们可以很容易地被机器切割和去除。
此外,冒口的大小也应该根据铸件的大小和形状来确定,以确保冒口能够顺利地排出铸件内部的气体和杂质。
第三,冒口的数量和位置也应该根据铸件的大小和形状来确定。
一般来说,较大的铸件需要更多的冒口,以便于更好地排出内部的气体和杂质。
此外,冒口的位置也应该考虑到铸件的结构和形状,以便于冒口能够顺利地切割和去除。
冒口的设计还应该考虑到铸件的成本和生产效率。
一般来说,冒口的设计应该尽可能地简单和经济,以便于降低生产成本和提高生产效率。
此外,冒口的设计还应该考虑到铸件的质量和性能,以确保铸件能够满足客户的要求和需求。
重力浇铸冒口设计是铸造工艺中非常重要的一环,它的设计原则应该考虑到铸件的形状、结构、大小、成本和生产效率等多个方面。
只有合理地设计冒口,才能够保证铸件的质量和性能,从而满足客户的要求和需求。
v法冒口和浇口的比例
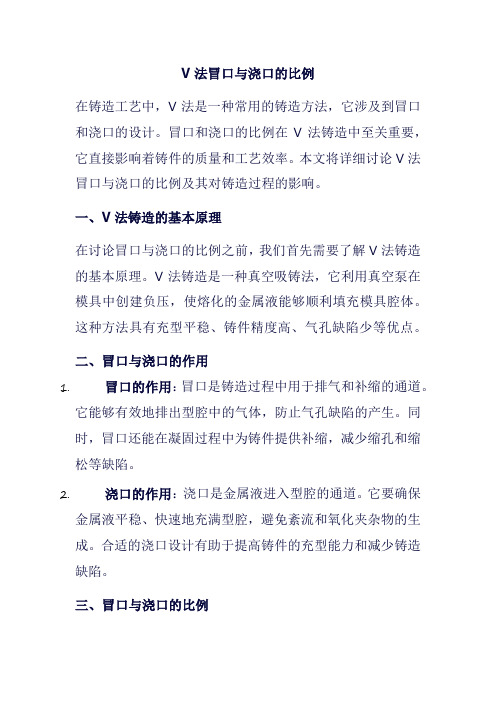
V法冒口与浇口的比例在铸造工艺中,V法是一种常用的铸造方法,它涉及到冒口和浇口的设计。
冒口和浇口的比例在V法铸造中至关重要,它直接影响着铸件的质量和工艺效率。
本文将详细讨论V法冒口与浇口的比例及其对铸造过程的影响。
一、V法铸造的基本原理在讨论冒口与浇口的比例之前,我们首先需要了解V法铸造的基本原理。
V法铸造是一种真空吸铸法,它利用真空泵在模具中创建负压,使熔化的金属液能够顺利填充模具腔体。
这种方法具有充型平稳、铸件精度高、气孔缺陷少等优点。
二、冒口与浇口的作用1.冒口的作用:冒口是铸造过程中用于排气和补缩的通道。
它能够有效地排出型腔中的气体,防止气孔缺陷的产生。
同时,冒口还能在凝固过程中为铸件提供补缩,减少缩孔和缩松等缺陷。
2.浇口的作用:浇口是金属液进入型腔的通道。
它要确保金属液平稳、快速地充满型腔,避免紊流和氧化夹杂物的生成。
合适的浇口设计有助于提高铸件的充型能力和减少铸造缺陷。
三、冒口与浇口的比例冒口与浇口的比例在V法铸造中需要根据具体情况进行优化。
这个比例取决于多个因素,如铸件的结构、尺寸、壁厚以及所需的工艺参数等。
一般而言,冒口的大小应足以排气和补缩,而浇口的大小应确保金属液顺利充满型腔。
如果冒口过大,可能会导致金属液的过早凝固,阻碍补缩和排气的进行。
而冒口过小,则可能无法有效排气,导致气孔缺陷。
同样地,浇口过大可能会导致金属液冲击型腔壁,产生紊流和夹杂物,而浇口过小则可能导致充型不足。
因此,确定合适的冒口与浇口比例是V法铸造中的关键任务。
这通常需要通过实验和模拟来确定最佳比例。
铸造工程师需要综合考虑各种因素,以达到最佳的工艺效果和铸件质量。
四、结论通过对V法铸造中冒口与浇口比例的讨论,我们可以看到这一比例对铸造过程和铸件质量的重要性。
合适的冒口与浇口比例能够确保金属液的平稳充型、有效排气和补缩,从而减少铸造缺陷,提高铸件质量。
在实际应用中,铸造工程师需要根据具体需求和条件,通过实践、实验和模拟来确定最优的冒口与浇口比例。