铸钢件冒口的设计规范
完整版铸钢件冒口的设计与计算
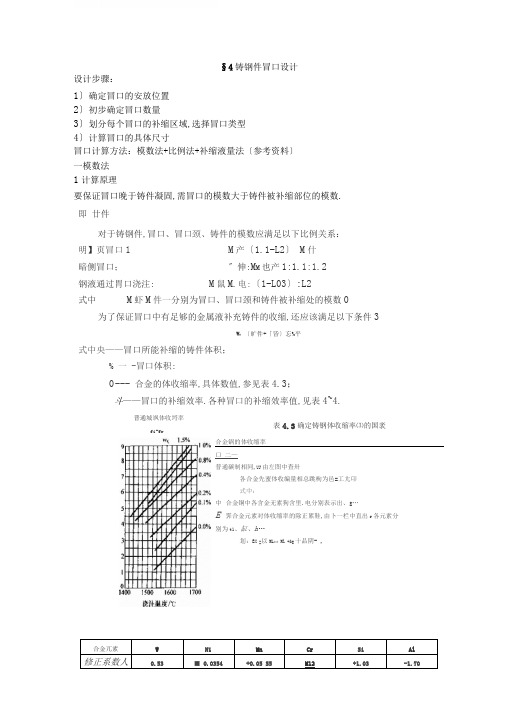
§4铸钢件冒口设计设计步骤:1〕确定冒口的安放位置2〕初步确定冒口数量3〕划分每个冒口的补缩区域,选择冒口类型4〕计算冒口的具体尺寸冒口计算方法:模数法+比例法+补缩液量法〔参考资料〕一模数法1计算原理要保证冒口晚于铸件凝固,需冒口的模数大于铸件被补缩部位的模数.即 廿件对于铸钢件,冒口、冒口颈、铸件的模数应满足以下比例关系:明】页冒口1M 产〔1.1-L2〕 M 什 暗侧冒口;〞伸:M M 也产1:1.1:1.2 钢液通过胃口浇注:M 鼠M.电:〔1-L03〕:L2 式中 M 虾M 件一分别为冒口、冒口颈和铸件被补缩处的模数0为了保证冒口中有足够的金属液补充铸件的收缩,还应该满足以下条件3W V 〔旷件+「皆〕忘%平式中央——冒口所能补缩的铸件体积;% 一 -冒口体积:0 --- 合金的体收缩率,具体数值,参见表4.3;斗——冒口的补缩效率.各种冒口的补缩效率值,见表4~4.表4.3确定铸钢体收缩率⑶的国袤 合金锅的体收缩率 口 二—普通碳制相同,UJ 由左图中查卅各合金先蜜体收编量相总跳枸为邑=工尢卬式中:中 合金铜中各含金无素狗含里.电分别表示出、g …E 霁合金元素对体收缩率的除正累鞋,由卜一栏中直出r 各元素分别为t1、缸、h …划:EX =以ML** Ml +&g 十品阴- ,合金兀素W Ni Mn Cr Si Al 修正系数人0.53 ■ 0.0354 +0.05 S5 M12 +1.03 -1.70 普通城飒体收埒率fi-fr总结:M冒=1.2M件P127式4-5,左边为总收缩量,右边为由冒口补充量2计算步骤1〕计算铸件模数根据铸件需补缩部位,划分补缩区,分别计算铸件的模数.计算方法:公式计算+图表计算—表4-5 〔p128-130〕.2〕计算冒口及胃口颈模数.根据热节的位置,确定胃口的类型,再根据式〔4-2〕或式〔4-3〕、式〔4-4〕. 即可计算出国口及冒口颈模数计算举例;铸钢件在下部法上处放置暗冒口补缩. 如图4-3三所示.求吩和利用表4・5中上形体计算公式,法兰处o=200mm, b—lOOnun*非散热面可得:“*0x20 …M 社=—j ---- ——cm = 3.636cm件2〔10 + 20〕-5因浇口通过冒口,故:1.05Mr = 374 cm 加冒=L2A/件=436 cmS 中左边的冒口颈…W R=〔22X 10X2〔22+10〕]四4一箝补缩铸钢件法兰的目口颈cm- 3.43cm,小于3.74cm,不能满足补缩要求,在铸件热节处将出现缩松口采用右边的冒口颈,必=Q0X 12V[2QO+I2〕]crti=3.75cm,满足了要求.计算M件用L形体计算公式,为什么不用法兰体公式去套呢?〔法兰体高度b无法确定〕图4-33B-B剖面图中200应改为220,因计算M B时用的数值是220;另外, 冒口直径为〔|〕220,其冒口颈宽也应为220.〔A-A剖面图中200改否.〕采用右边的A-A剖面冒口颈满足了要求,A-A剖面冒口颈尺寸怎么得来的呢?不要瞎懵,可列式M仝^=3.74=20X/[2 〔20+X〕],求出X=12.生产中可根据M冒数值查出标准侧冒口,得冒口尺寸〔直径、高等〕,冒口颈尺寸,冒口体积、重量,能补缩的铸件体积及重量〔 M冒结合一查〕.3〕确定铸钢件体收缩率由表4-3求出.例如,ZG270-500的平均W C=0.35%,假设浇注温度为1560℃,可从表4-3 查出=4.7%〔碳钢e V= e C〕.£V如何查出的呢?浇注温度为1560 C; W C=0.40%, ev=5%; W C=0.20%,&V=3.8%;据此列式〔5-3.8〕 / 〔0.4-0.2〕 = 〔5-X〕 / 〔0.4-0.35〕,解出X=4.7 〔插入法,比例法〕4〕确定冒口形状和尺寸查相关表格.5〕确定冒口数目6〕校核冒口的最大补缩水平.二比例法〔热节圆法〕使冒口根部直径大于铸件被补缩处热节圆直径或壁厚, 再以冒口根部直径来确定其他尺寸.D=cd式中D ……冒口根部直径;c ••…比例系数,参见表4-6;〔查表步骤〕d ……铸件被补缩热节处内切圆直径.可用作图法画出图4-34热节圆直件a 〕壁厚均匀b 〕壁面和交查表步骤:1〕选取比例系数c 〔先按铸件结构选择冒口类型,再选比例系数〕2〕确定冒口高度〔根据直径 D 确定〕;3〕确定每个冒口长度或冒口个数〔根据冒口延伸度确定〕.三铸件工艺出品率的校核表4-7说明校核方法.采用普通冒口时,冒口尺寸 可根据表中数值进行验算 和调整,即将冒口重量代入 计算后,假设工艺出品率低于 表中数值,那么冒口尺寸偏 大,可适当减小冒口高度; 假设高于表中数值,那么应加大 冒口尺寸或增加冒口个数.四冒口计算举例 见p133例题.图535 ZG35SiMn 铸钢齿轮铸件1模数法工艺出品率= 铸件重量铸件重量+浇铸系统重 量+冒口重量轮缘与轮辐的交接处为热节,其直径d按作图法得50〔大于轮缘厚40〕;按作图法且考虑热节增大,见P126图4-31,dy=d+〔10~30〕,取d=60 〔见P134比例法〕.轮缘热节处按表4-5应为板与杆的相交体,由图4-35可得a=d=60mm, b=180mm,c=24mm.2比例法〔热节圆法〕作业:如下列图铸钢齿圈坯件ZG25,为一圆环,中径〔|〕920,厚80,高240, 有三种补缩方案:3个6190冒口, 3个6190冒口和3个冷铁,尺寸为:宽100X厚50X高240, 6个6190冒口.按有效补缩距离检验,冒口数目是否足够?。
冒口设计参考
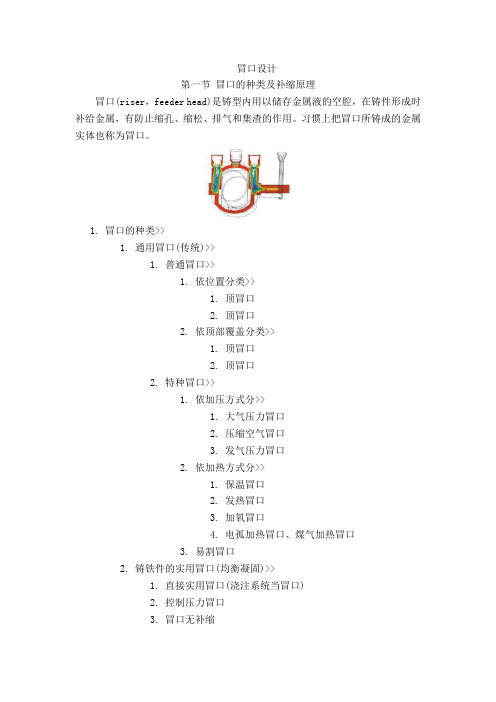
冒口设计第一节冒口的种类及补缩原理冒口(riser,feeder head)是铸型内用以储存金属液的空腔,在铸件形成时补给金属,有防止缩孔、缩松、排气和集渣的作用。
习惯上把冒口所铸成的金属实体也称为冒口。
1.冒口的种类>>1.通用冒口(传统)>>1.普通冒口>>1.依位置分类>>1.顶冒口2.顶冒口2.依顶部覆盖分类>>1.顶冒口2.顶冒口2.特种冒口>>1.依加压方式分>>1.大气压力冒口2.压缩空气冒口3.发气压力冒口2.依加热方式分>>1.保温冒口2.发热冒口3.加氧冒口4.电孤加热冒口、煤气加热冒口3.易割冒口2.铸铁件的实用冒口(均衡凝固)>>1.直接实用冒口(浇注系统当冒口)2.控制压力冒口3.冒口无补缩2.冒口形状冒口的形状有圆柱形、球顶圆柱形、长(腰)圆柱形、球形及扁球形等多种3.通用冒口补缩原理>>1.基本条件>>1.冒口凝固时间大于或等于铸件(被补缩部分)的凝固时间2.有足够的金属液补充铸件的液态收缩和凝固收缩,补偿浇注后型腔扩大的体积3.在凝固期间,冒口和被补缩部位之间存在补缩通道,扩张角向着冒口2.选择冒口位置的原则>>1.冒口应就近设在铸件热节(hotspot)的上方或侧旁2.冒口应尽量设在铸件最高、最厚的部位。
对低处的热节增设补贴或使用冷铁,造成补缩的有利条件3.冒口不应设在铸件重要的、受力大的部位,以防组织粗大降低强度4.冒口位置不要选在铸造应力集中处,应注意减轻对铸件的收缩阻碍,以免引起裂纹5.尽量用一个冒口同时补缩几个热节或铸件6.冒口布置在加工面上,可节约铸件精整工时,零件外观好7.不同高度上的冒口,应用冷铁使各个冒口的补缩范围隔开3.冒口有效补缩距离的确定>>冒口的有效补缩距离为冒口作用区与末端区长度之和,它是确定冒口数目的依据,与铸件结构、合金成分及凝固特性、冷却条件、对铸件质量要求的高低等多种因素有关,简称为冒口补缩距离1.铸钢件冒口的补缩距离有色合金的冒口补缩距离外冷铁的影响补贴(padding)的应用第二节铸钢件冒口的设计与计算铸钢件冒口属于通用冒口,其计算原理适用于实行顺序凝固的一切合金铸件。
铸件冒口设计的原则及方法

图 4 冒口放在两热节之间的工艺对比
放在最后凝固的部位和几何热节处,形成 的接触热节和冒口补缩液流通效应的影 响,会使冒口安放处铸件的凝固时间延长, 相应增加对冒口补缩时间的要求,同时也 对热节处的内在质量产生不利的影响。为 此,文献[4]提出了动态顺序凝固的概念。 动态顺序凝固是指冒口离开热节,放在近 热节处,利用冒口根处形成的接触热节和 冒口补缩液的流通效应,实现铸件各部分 朝向冒口的顺序凝固。其实质是使铸件的 几何热节与设置冒口形成的接触热节相分 离,并控制次热节处所形成的接触热节,使 其凝固模数比几何热节的大,比冒口的小, 将凝固顺序由薄壁→次热节→几何热节→ 几何热节处的接触热节→冒口,改变为薄 壁→几何热节→次热节处的接触热节→冒 口,既避免了接触热节处热量过分集中,又 利用接触热节的热效应,在冒口和几何热 节之间形成补缩通道,保证冒口对几何热 节的补缩。
采用模数法计算出的冒口体积,应该
用补缩液量法进行校核,即冒口体积 V 应 r
满足式(1)。
3.2 热节圆比例法
热节圆比例法是一种经验性方法。采
用作图法或几何公式计算出热节圆直径 T, 然后根据铸件不同截面形状确定例系数α的数值多来源于工程实
科技创新导报 Science and Technology Innovation Herald
101
科技创新导报 2008 NO.27 Science and Technology Innovation Herald
工 程 技 术
图 5 冒口直径与铸件厚度热节圆直径的 关系
使膨胀压力得以控制,避免铸型扩大,一般
铸件凝固过程中,冒口液面不断下降, 体积减少,散热表面积增加,冒口模数动态
变小;铸件获得补缩液体后热量增加,凝固
铸钢车桥铸件技术规范

铸钢车桥铸件技术规范铸钢车桥铸件技术规范一、铸件第一次抛丸1、铸件经第一次抛丸,粘砂90%以上基本抛干净,允许拐角有不超过2毫米厚的粘砂。
2、浇冒口切割线的粘砂要彻底清除干净。
二、表面质量1、非加工面1.1表面粗糙度:连片和单个小刺高于基面1.5毫米要磨除1.2浇冒口痕迹、披缝、多肉、粘砂、氧化皮必须清除1.3冷隔凹陷的痕迹长小于40毫米,深小于1毫米不焊补。
长大于40毫米一律焊补。
1.4错箱值不大于2毫米。
1.5铸件弯曲变形量不影响整体机械加工。
1.6热处理后铸件焊补可不进行二次热处理2、加工面2.1浇口、冒口痕迹、披缝、多肉长度小于80毫米,凸出要小于3毫米;长度大于80毫米,凸出要小于5毫米。
2.2 凹陷不超过所在平面加工余量2/3.2.3 热处理后再焊补要进行二次低温热处理。
三、不允许存在的缺陷1、铸件不得有未经修补、影响使用寿命的裂纹、冷隔、缩松,夹砂等缺陷。
2、铸件不得有较大连片密集气孔、缩孔、砂眼和铁豆;3、铸件不得有危及与该铸件直接配合的零件寿命的任何铸造缺陷;4、铸件不得有不符合图样和技术要求的其他缺陷。
四、允许存在无须修补的缺陷1 在非加工面上:1.1单个缺陷(砂眼、气孔)小于5毫米,深度小于壁厚的1/4,在直径100毫米圆内小于5个,一般一个独立表面总数不多于12个,间距大于10毫米1.2 缩孔、缩松不大于该处热节圆1/42 在加工后存在的缺陷:2.1非主要工作面上孤立的圆滑的凹孔、非裂纹式沟槽,缺陷不大于5毫米。
深度小于该壁厚的1/4,数量在直径100毫米圆内小于4个,一个独立表面上不多于10个,间隙大于40毫米。
2.2 主要工作面上孤立的圆滑的凹孔、非裂纹式沟槽,缺陷不大于3毫米,深度小于3毫米,总面积不超出所在面的1%,间隔大于40毫米。
注:以上凹陷的缺陷,也可以用金属修补胶进行修补。
五、铸件尺寸公差应符合图纸的技术要求六、铸件重量公差±3%七、铸件化学成分和力学性能、金相组织、硬度7.1 化学成分(%)①残余元素总量不超过1%② ZG35Mn为广西方盛厂家专用的材质7.2 机械性能注:⑴ZG270—500,适用于厚度小于等于100mm的铸件,当铸件厚度超过100mm时,表中的σ0.2仅供设计使用。
铸铁件冒口定量设计课件

(4)横浇道模数 Mh
Mh=f横.f2.Mc
f横=0.75~0.85 f2 ——收缩模数系数 Mc ——铸件模数 根据横浇道模数Mh,求出横浇道尺寸
10 浇注系统充填与补缩一体化设计
(1)充填设计(保证浇注时间,大流量,平稳 洁净,有合理的流态,可控的流动路径)
(2)补缩设计(足够的补缩时间和补缩量) (3)取二者较大者,再核算 (4)给出二者都满足的尺寸
(5)内浇道模数Mn
Mn=f内f2.f4Mc f内=0.35~0.40 f2 ——收缩模数系数 f4 ——冒口颈长度系数 f4=0.8~1.0 Mc ——铸件模数 根据内浇道模数Mn,求出内浇道尺寸
11 铸铁件冒口系列
12 结论
(1)冒口位置不要放在铸件的几何热节上; (2)冒口颈 短、 厚、 宽。 (3)铸铁件收缩时间分数,流通效应系数对
提高中国铸件在国际市场上 的竞争力
谢谢
Qm= G Mc3
3 铸铁件均衡凝固冒口设计方法
(1)收缩模数计算法(3f法) (2)查表法 (3)分段比例查表法
4 收缩模数计算法(3 f法)
(1)冒口体模数MR MR=f1f2f3Mc
f1 ——冒口平衡系数 f2 ——收缩模数系数 f3 ——冒口压力系数 Mc ——铸件模数
取f1=1.2 f2=√P f3=1.1~1.3
冒口,冒口颈大小的影响显著。 (4)无冒口铸造的本质是浇注系统当冒口。
均衡凝固技术1988年获 国家科技进步二等奖
1989年国家科委成都均衡凝固推广班
谢谢
联系方式 地址:710048 西安理工大学608信箱
《铸造技术》杂志 电话/传真: 即时联系: Email:
附件
提高铸造企业工艺水平和 铸件品质
铸造工艺学冒口设计
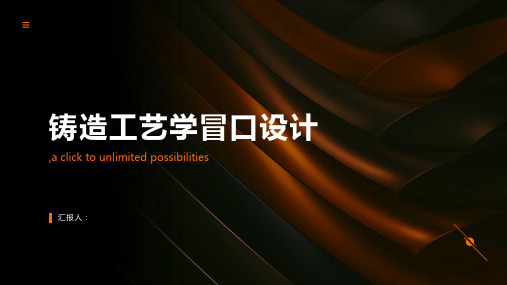
铸造工艺学是一门 研究金属材料成型 规律和工艺方法的 科学
铸造工艺学涉及到 金属材料的性能、 组织结构、成分和 加工方法等方面
铸造工艺学是机械 制造领域中重要的 分支之一
铸造工艺学在汽车 、航空航天、能源 等领域有着广泛的 应用
铸造工艺学的研究对象和内容
添加标题
研究对象:铸造工艺学是研究铸造生产过程及其相关技术的一门学科,包括铸造材料、铸造设备、铸造工 艺等方面的内容。
置,以获得最佳补缩效果
注意浇注温度对冒口的影响
浇注温度过低可能导致冒口 补缩不足,产生缩孔、缩松 等缺陷
合适的浇注温度需要根据合 金种类、铸件结构、浇注系
统等因素固,影响补缩效果
在实际生产中,可以通过调 整浇注温度来优化冒口设计,
提高铸件质量
注意浇注时间对冒口的影响
优化冒口位置: 将冒口设置在 铸件的非重要 部位或应力集 中区域,以减 少后续加工或 修复工作量。
考虑环保因素: 选择环保型冒 口材料,减少 废弃物对环境 的影响,降低
处理成本。
05 冒口设计的具体方法
确定冒口的位置
确定冒口的位置:根据铸件的结构和尺寸,选择合适的冒口位置,以保证铸件的质量和生产效 率。
球墨铸铁材质的冒口设计实例
材质特性:球墨铸 铁具有高强度、高 韧性、耐磨性等特 点
冒口设计原则:根 据铸造工艺要求, 确定冒口的位置、 大小和形状
实例分析:以某实 际生产中的球墨铸 铁零件为例,详细 介绍冒口的设计过 程和优化方案
效果评估:通过对 比分析,阐述优化 后的冒口设计对提 高铸件质量、降低 废品率等方面的作 用
添加 标题
壁厚对冒口尺寸的影响:壁厚越大,需要的 冒口体积也越大,以补偿铸件凝固过程中的 收缩。
重力浇铸冒口设计原则
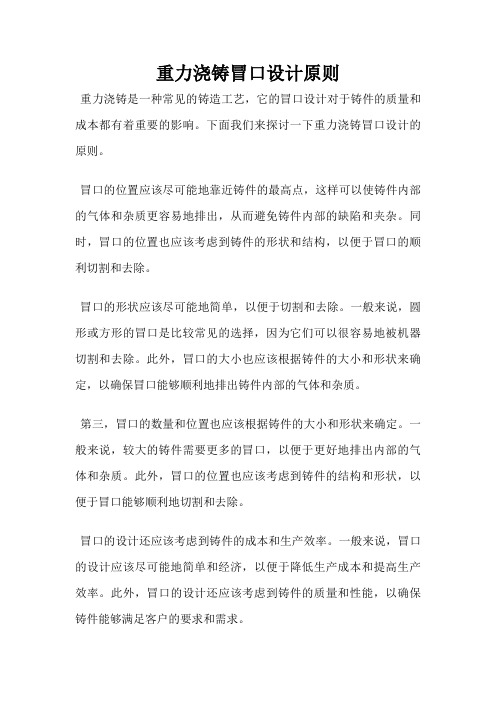
重力浇铸冒口设计原则
重力浇铸是一种常见的铸造工艺,它的冒口设计对于铸件的质量和成本都有着重要的影响。
下面我们来探讨一下重力浇铸冒口设计的原则。
冒口的位置应该尽可能地靠近铸件的最高点,这样可以使铸件内部的气体和杂质更容易地排出,从而避免铸件内部的缺陷和夹杂。
同时,冒口的位置也应该考虑到铸件的形状和结构,以便于冒口的顺利切割和去除。
冒口的形状应该尽可能地简单,以便于切割和去除。
一般来说,圆形或方形的冒口是比较常见的选择,因为它们可以很容易地被机器切割和去除。
此外,冒口的大小也应该根据铸件的大小和形状来确定,以确保冒口能够顺利地排出铸件内部的气体和杂质。
第三,冒口的数量和位置也应该根据铸件的大小和形状来确定。
一般来说,较大的铸件需要更多的冒口,以便于更好地排出内部的气体和杂质。
此外,冒口的位置也应该考虑到铸件的结构和形状,以便于冒口能够顺利地切割和去除。
冒口的设计还应该考虑到铸件的成本和生产效率。
一般来说,冒口的设计应该尽可能地简单和经济,以便于降低生产成本和提高生产效率。
此外,冒口的设计还应该考虑到铸件的质量和性能,以确保铸件能够满足客户的要求和需求。
重力浇铸冒口设计是铸造工艺中非常重要的一环,它的设计原则应该考虑到铸件的形状、结构、大小、成本和生产效率等多个方面。
只有合理地设计冒口,才能够保证铸件的质量和性能,从而满足客户的要求和需求。
铸钢件冒口的设计与计算-推荐下载

§4 铸钢件冒口设计设计步骤:1)确定冒口的安放位置2)初步确定冒口数量3)划分每个冒口的补缩区域,选择冒口类型4)计算冒口的具体尺寸冒口计算方法:模数法+比例法+补缩液量法(参考资料)一模数法1 计算原理要保证冒口晚于铸件凝固,需冒口的模数大于铸件被补缩部位的模数。
总结:M冒=1.2M件P127式4-5,左边为总收缩量,右边为由冒口补充量。
2 计算步骤1)计算铸件模数根据铸件需补缩部位,划分补缩区,分别计算铸件的模数。
计算方法:公式计算+图表计算-表4-5(p128-130)。
计算M件用L形体计算公式,为什么不用法兰体公式去套呢?(法兰体高度b无法确定)图4-33B-B剖面图中200应改为220,因计算M B时用的数值是220;另外,冒口直径为φ220,其冒口颈宽也应为220。
(A-A剖面图中200改否.)采用右边的A-A剖面冒口颈满足了要求,A-A剖面冒口颈尺寸怎么得来的呢?不要瞎懵,可列式M颈=3.74=20X/[2(20+X)],求出X=12.生产中可根据M冒数值查出标准侧冒口,得冒口尺寸(直径、高等),冒口颈尺寸,冒口体积、重量,能补缩的铸件体积及重量(M冒结合εV查)。
3)确定铸钢件体收缩率由表4-3求出。
例如,已知ZG270-500的平均W C=0.35%,若浇注温度为1560°C,可从表4-3查出εV=4.7%(碳钢εV=εC)。
如何查出的呢?浇注温度为1560°C;W C=0.40%,εV=5%;W C=0.20%,εV=3.8%;据此列式(5-3.8)/(0.4-0.2)=(5-X)/(0.4-0.35),解出X=4.7(插入法,比例法)4)确定冒口形状和尺寸查相关表格。
5)确定冒口数目6)校核冒口的最大补缩能力。
二比例法(热节圆法)见p133例题。
1 模数法轮缘与轮辐的交接处为热节,其直径d按作图法得50(大于轮缘厚40);按作图法且考虑热节增大,见P126图4-31,dy=d+(10~30),取d=60(见P134比例法)。
- 1、下载文档前请自行甄别文档内容的完整性,平台不提供额外的编辑、内容补充、找答案等附加服务。
- 2、"仅部分预览"的文档,不可在线预览部分如存在完整性等问题,可反馈申请退款(可完整预览的文档不适用该条件!)。
- 3、如文档侵犯您的权益,请联系客服反馈,我们会尽快为您处理(人工客服工作时间:9:00-18:30)。
铸钢件冒口的设计规
钢水从液态冷却到常温的过程中,体积发生收缩。
在液态和凝固状态下,钢水的体积收缩可导致铸件产生缩孔、缩松。
冒口的作用就是补缩铸件,消除缩孔、缩松缺陷。
另外,冒口还具有出气和集渣的作用。
1、冒口设计的原则和位置
1.1冒口设计的原则
1.1.1、冒口的凝固时间要大于或等于铸件(或铸件被补缩部分)的凝固时间。
1.1.2、冒口所提供的补缩液量应大于铸件(或铸件被补缩部分)的液态收缩、凝固收缩和型腔扩大量之和。
1.1.3、冒口和铸件需要补缩部分在整个补缩的过程中应存在通道。
1.1.4、冒口体要有足够的补缩压力,使补缩金属液能够定向流动到补缩对象区域,以克服流动阻力,保证铸件在凝固的过程中一直处于正压状态,既补缩过程终止时,冒口中还有一定的残余金属液高度。
1.1.5、在放置冒口时,尽量不要增大铸件的接触热节。
1.2、冒口位置的设置
1.2.1、冒口一般应设置在铸件的最厚、最高部位。
1.2.2、冒口不可设置在阻碍收缩以及铸造应力集中的地方。
1.2.3、要尽量把冒口设置在铸件的加工面或容易清除的部位。
1.2.4、对于厚大件一般采用大冒口集中补缩,对于薄壁件一般采用小冒口分散补缩。
1.2.5、应根据铸件的技术要求、结构和使用情况,合理的设置冒口。
1.2.6、对于清理冒口困难的钢种,如高锰钢、耐热钢铸件的冒口,要少放或不放,非放不可的,也尽量采用易割冒口或缩脖型冒口。
2、设置冒口的步骤与方法
冒口的大小、位置及数量对于铸钢件的质量至关重要。
对于大型铸钢件来说,必须把握技术标准及使用情况,充分了解设计意图,分清主次部位,集中解决关键部位的补缩。
以模数法为例,冒口设计的步骤如下:
2.1、对于大、中型铸钢件,分型面确定之后,首先要根据铸件的结构划分补缩围,并计算铸件的模数(或铸件被补缩部分的模数)M铸。
2.2、根据铸件(或铸件被补缩部分)的模数M铸,确定冒口模数M冒。
2.3、计算铸件的体收缩ε。
2.4、确定冒口的具体形状和尺寸。
2.5、根据冒口的补缩距离,校核冒口的数量。
2.6、根据铸件结构,为了提高补缩距离,减少冒口的数量,或者使冒口的补缩通道畅通,综合设置外冷铁及冒口增肉。
2.7、校核冒口的补缩能力,要求ε(V冒+V件)≤V冒η。
3、设计冒口尺寸的方法
3.1、模数法
在铸件的材料、铸型的性质和浇注条件确定之后,铸件的凝固时间决定于铸件的模数。
模数M=V/A(厘米),V—体积(厘米3);A—散热面积(厘米2)。
随着办公条件的改善,计算机的普及,模数可以用计算机进行计算。
方法是:用SolidWorks软件画出铸件(或铸件被补缩部分)的立体图,计
算出铸件的体积和散热面积,然后用公式M=V/A计算模数。
冒口的凝固时间大于铸件的凝固时间,冒口的模数一般是铸件模数的 1.1~1.2倍,M冒=1.1~1.2M铸
对于厚实铸件,如:圆柱体、块状铸件,用模数法确定的冒口往往偏
大,故必须采取一些方法加快铸件的凝固,同时延长冒口的凝固时间。
通
常采用以下方法:1、加放、外冷铁;2、补浇冒口;3、采用保温冒口。
采用以上措施后,M冒=KM铸,K按下表进行选择。
铸件壁厚铸件模数冷铁及冒口补浇情况K
≤100
不下冷铁 1.25~1.2
局部下冷铁 1.2~1.1
100~200 下冷铁,冒口不补浇 1.1~1.0
>200
下较多冷铁,冒口不补浇 1
>14.5 下满冷铁,冒口补浇一次0.9
>23 下满冷铁,冒口补浇二次0.9~0.85 >28.5 下满冷铁,冒口补浇3~4次0.85~0.80
注:对于要求比较高的铸件、探伤件,尽量不放冷铁。
3.2、热节圆法
根据铸件壁厚部位热节圆的大小来确定冒口尺寸的一种方法。
热节圆法主要适用于轮形铸件,一般冒口与热节不连通,需要用滚热节圆的方法确定冒口增肉,然后确定冒口尺寸。
可以用绘图软件画出铸件热节的形状,然后画出热节的切圆,即为热节圆。