汽车横向稳定杆生产工艺简介
稳定杆 技术要求

稳定杆技术要求
稳定杆是一种用于支撑和固定结构物的装置,它需要具备一定的技术要求以确保其稳定性和可靠性。
以下是常见的稳定杆的技术要求:
1. 强度和刚度:稳定杆需要具备足够的强度和刚度来抵抗外部荷载和横向力,以保持结构的稳定性。
这可以通过选择合适的材料和结构设计来实现。
2. 抗震性能:稳定杆需要具备一定的抗震性能,能够在地震或其他振动情况下保持稳定。
这可以通过设计具有一定的弹性和阻尼特性的结构来实现。
3. 耐久性:稳定杆需要具备良好的耐久性,能够长期承受外部环境和气候条件的影响,不容易发生腐蚀、变形或疲劳破坏。
4. 安装便捷性:稳定杆需要便于安装和拆卸,能够快速、准确地固定和调整结构。
5. 可调性:稳定杆需要具备一定的可调性,能够根据实际需要调整长度、角度或高度,以适应各种不同的应用场景。
6. 综合成本:稳定杆的设计和制造成本要合理,并且运维成本较低,以达到经济和实用的目的。
总之,稳定杆的技术要求主要涉及其强度、刚度、抗震性能、
耐久性、安装便捷性、可调性和综合成本等方面,以确保其稳定性和可靠性。
螺旋弹簧横向稳定杆减振器设计指南

减振器储油缸直径 Dc = (1.35 ~ 1.57)D ,工作缸与储油缸壁厚一般取 1.5~2.0 mm 。
选择减振器尺寸时主要考虑一下两点:在工作速度范围内油液压力适当,能够得到稳定的阻力值,
8
容易保证油封的可靠性;减振器具有足够的散热面积,防止因温度过高引起阻力衰减或减振器早期失效。 作缸径的确定:
可根据减振器最大拉伸阻力和最大允许压力近似求出工作缸径。
( ) D = 4Fmax (mm) πp 1 − λ2 式中: D -作缸径, mm ; p -工作缸允许最大压力,一般为 3~4 N / mm2 ; F max -减振器最大拉伸阻力, N ; λ -减振器杆直径与工作缸之比,双筒减振器为 0.4~0.5,单筒减振器为 0.3~0.35。
Cϕb
=
1 2
⋅
P f
L2
=
3 EIL2
(6)
l l 2⎢⎣⎡
3 − a3 + L (a + b)2 + 4
1
2
2 2
(b
+
c
)⎥⎦⎤
当角钢度给定时,可求得所需要的稳定杆直径 d 为
l l d
=
4
128 3π
⋅
Cϕb L2 E
⎡ ⎢⎣
3 − a3 + 1 (a + b)2 + 4
1
2
2 2
(b
+
c
)⎥⎦⎤
(7) 按弹簧指数 C = Dm / d 及 K ' 的表达式(见式 24 下的说明求得 K ' ,运用式(24)求出载荷 P1 ,
34MnB5钢汽车空心稳定杆疲劳失效分析

Science &Technology Vision 科技视界0引言汽车稳定杆能够防止汽车车身发生较大的横向倾斜和横向角振动,从而在车辆转弯或者颠簸时起到提高驾驶员及乘客的舒适性[1]。
某车型新开发的空心稳定杆在台架试验过程中提前发生疲劳失效,疲劳试验结果约为15万次,未达到要求的25万次,而同批次的其他零件疲劳试验结果基本约为40万次。
该零件材质均为34MnB5-P 酸洗板,零件加工工艺流程为:酸洗板→分条→焊接→热处理(退火)→酸洗润滑→冷拔→热处理(正火)→矫直切管(精密钢管)→冷弯成型→热处理(淬火+回火)→矫正→(内防腐)→端头加工→喷丸→磷化→涂装→成品[2-5]。
由于提前失效零件的化学成分、洛氏硬度检测均满足技术规范要求,因此本文通过对失效零件开展断口形貌及组织进行分析,以确定该零件提前断裂失效原因。
1试验结果和分析1.1断口形貌零件断裂位置位于稳定杆右侧橡胶固定点,断口宏观形貌如图1a,可以看出断口基本与钢管轴向垂直,其断口呈现出典型的扭转疲劳断口,且该断口可以分为2个(裂纹扩展区、过载瞬断区)部分。
采用扫描电镜对断口进行观察,结果如图1(b~d)。
可以看出:(1)裂纹起裂点均位于管内壁,从内壁首先向外壁扩展贯穿,然后沿着管壁向两侧扩展;(2)起裂点位置附近未见明显的凹坑、夹杂物等缺陷;(3)裂纹起裂点附近及扩展区呈现典型的脆性断口特征,由于受到交变应力作用,使得垂直于裂纹扩展方向存在明显的微裂纹;(4)过载瞬断位置呈现典型的韧窝形貌,为典型的韧性断裂。
图1断口SEM 形貌34MnB5钢汽车空心稳定杆疲劳失效分析刘阳汪永国崔磊马聪吴胜付(马鞍山钢铁股份有限公司技术中心,安徽马鞍山243000)【摘要】采用34M n B 5钢加工的某车型汽车空心稳定杆在评估过程中未达到设计使用寿命,提前发生疲劳断裂失效。
为分析该部分零件提前失效原因,采用金相显微镜、扫描电镜对失效零件断口、金相组织进行检测分析。
横向稳定杆断裂原因分析及改善

横向稳定杆断裂原因分析及改善■张月,胡赞,杨丽卉,陈然摘要:某横向稳定杆在试验过程中未达到设计使用寿命即发生断裂。
对断裂稳定杆进行断口分析及理化检测分析表明,稳定杆表面局部硬度偏低导致稳定杆发生疲劳断裂。
结合稳定杆的生产工艺过程分析,得出成形及热处理过程中冷速问题是引起稳定杆表面局部硬度偏低、导致稳定杆断裂的主要原因。
通过改善问题点,从而避免了稳定杆断裂的再次发生。
关键词:横向稳定杆;失效;疲劳断裂;热处理;冷却速度横向稳定杆是汽车悬挂中横向布置的扭杆弹簧,起到防止车身在转弯时发生过大的横向侧倾和改善平顺性的作用。
某横向稳定杆在试验时发生断裂。
该稳定杆的材质为60Si2MnA,硬度要求36~42HRC,生产工艺流程为:下料→端部锻造→打孔、镗孔→整体加热成形→淬火→回火→校型→喷丸强化→喷涂→标识→包装储存。
1. 断口分析稳定杆断裂于弯折过渡位置(见图1),位于稳定杆最大应力分布位置——衬套安装位置附近。
断面较平齐,没有明显的塑性变形特征,断口(见图2)呈典型的疲劳断口特征,由疲劳裂纹源、裂纹扩展区和最后断裂区组成。
疲劳裂纹源起于稳定杆表面,裂纹源区未发现磕碰痕迹,肉眼可见由多个台阶组成、源区约占1.5mm宽度范围,疲劳起源为多点起源。
疲劳扩展区约占整个断口面积的60%。
裂纹早期扩展区光滑平坦且呈黄色,已发生锈蚀,贝纹线不明显;后期扩展区贝纹线清晰可见。
最后断裂区较粗糙,平面区可见快速扩展的放射线,边缘区为剪切唇。
通过扫描电子显微镜进行微观观察(见图3~图5),未观察到其他明显异常,疲劳扩展区可见明显的疲劳辉纹(见图4),最后断裂区为韧窝特征(见图5)。
2. 理化分析(1)化学成分稳定杆化学成分检测结果(见表1)符合图1 稳定杆断裂位置图2 断口宏观形貌图3 裂纹源区微观形貌图4 疲劳扩展区微观形貌60Si2MnA (GB/T 1222—2016)材质要求。
(2)金相组织 在断口位置附近分别取横、纵截面样品制备金相样,纵截面样垂直稳定杆一侧断口的裂纹源切取(金相I ),横截面样从稳定杆另一侧断口附近切取(金相II )。
汽车连杆的加工工艺流程

汽车连杆的加工工艺流程
一、施工前准备工作:
1. 检查机床是否能正常运转,加工设备是否齐全可用。
2. 根据产品图纸和工艺参数准备好所需的原材料。
3. 洁净加工区域,确保环境清洁。
二、主要加工工艺:
1. 原材料粗采型:采用锤冲模具对原材料进行粗型采样,得到近似的尺寸。
2. 磨削:采用车削机对粗采型的零件进行精磨,得到尺寸公差为±0.02的制成品。
3. 冷焊:将两个零部件进行冷焊,形成连杆主体。
4. 橡胶缓冲装配:在连杆两端安装橡胶缓冲装置。
5. 表面处理:采用砂纸擦亮连杆表面,进行除锈和脱油处理。
6. 集成测试:对加工好的连杆进行机能性能测试。
7. 包装运输:对合格的产品进行塑料或纸包装,便于运输。
三、库存管理:按产品数量和时间要求及时补充原材料,合格品按产品
需求分类存储。
简析大客车横向稳定杆的虚拟疲劳

简析⼤客车横向稳定杆的虚拟疲劳相关推荐简析⼤客车横向稳定杆的虚拟疲劳 论⽂关键词:横向稳定杆;有限元分析;虚拟疲劳分析论⽂相关查阅:、、、、、论⽂相关查阅: 论⽂摘要:根据⼤客车横向稳定杆的⼏何参数、载荷及约束情况,建⽴了横向稳定杆的有限元分析模型。
基于疲劳寿命预测的相关理论,结合Abaqus有限元分析软件和nSoft疲劳分析软件进⾏虚拟疲劳分析,在较短的时间内获得了横向稳定杆的疲劳寿命分布、寿命薄弱位置等信息。
结果表明,虚拟疲劳分析能⼤⼤缩短产品的开发周期,减少试验的⼯作量,降低开发成本。
在多数轿车和客车上,为了防⽌车⾝在转向⾏驶等情况下发⽣过⼤的横向倾斜,在悬架中均设有横向稳定杆。
横向稳定杆由弹簧钢制成,呈扁平的U形横向地安装在汽车的前端或后端。
汽车转向时车⾝侧倾,横向稳定杆⼀端下移,另⼀端则上移,⽽中部对于车架并⽆相对运动,于是横向稳定杆便被扭转。
弹性的横向稳定杆所产⽣的扭转的内⼒矩阻碍了悬架弹簧的变形,从⽽减⼩汽车的侧倾,使其保持良好的姿态。
在实际⼯作状态中,横向稳定杆常会受到⼤⼩不同的扭⼒作⽤,随着受⼒次数的增加,某些部位会出现疲劳破坏。
因此,疲劳寿命是设计中必须要考虑的⼀个重要因素,有必要对横向稳定杆进⾏虚拟疲劳分析。
某新型双层⼤客车,前、后悬架各安装⼀套横向稳定杆。
本⽂基于Abaqus有限元分析软件进⾏线性静⼒分析,结合nSoft疲劳分析软件,对横向稳定杆进⾏虚拟疲劳分析。
1、虚拟疲劳分析的⽅法与过程 1.1疲劳分析的⽅法疲劳是在某点或某些点承受扰动应⼒,且在⾜够多的循环扰动之后形成裂纹或完全断裂的材料中发⽣的局部的、永久结构变化的发展过程。
零件在循环加载下产⽣疲劳破坏所需的应⼒或应变循环数称为疲劳寿命。
按破坏时循环数的⾼低,疲劳分为⾼周疲劳和低周疲劳。
⾼周疲劳受应⼒幅控制,⼜称应⼒疲劳。
⾼周疲劳是各种机械中最常见的,简称疲劳。
低周疲劳受应变幅控制,⼜称应变疲劳。
根据疲劳破坏的形式,常⽤三种疲劳分析⽅法: S_N名义应⼒法、e-N局部应变法、LEFM裂纹扩展寿命法。
ESP生产线工艺流程
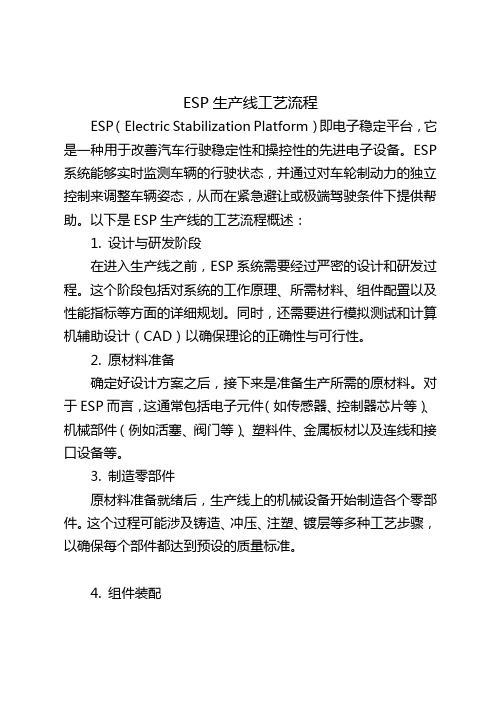
ESP生产线工艺流程ESP(Electric Stabilization Platform)即电子稳定平台,它是一种用于改善汽车行驶稳定性和操控性的先进电子设备。
ESP 系统能够实时监测车辆的行驶状态,并通过对车轮制动力的独立控制来调整车辆姿态,从而在紧急避让或极端驾驶条件下提供帮助。
以下是ESP生产线的工艺流程概述:1. 设计与研发阶段在进入生产线之前,ESP系统需要经过严密的设计和研发过程。
这个阶段包括对系统的工作原理、所需材料、组件配置以及性能指标等方面的详细规划。
同时,还需要进行模拟测试和计算机辅助设计(CAD)以确保理论的正确性与可行性。
2. 原材料准备确定好设计方案之后,接下来是准备生产所需的原材料。
对于ESP而言,这通常包括电子元件(如传感器、控制器芯片等)、机械部件(例如活塞、阀门等)、塑料件、金属板材以及连线和接口设备等。
3. 制造零部件原材料准备就绪后,生产线上的机械设备开始制造各个零部件。
这个过程可能涉及铸造、冲压、注塑、镀层等多种工艺步骤,以确保每个部件都达到预设的质量标准。
4. 组件装配制造好的零部件将进入装配阶段,此时,工人或自动化机器人会根据既定流程将它们组装成ESP系统的子模块。
例如,传感器模块、液压单元或者电子控制单元(ECU)。
5. 电子组件焊接与封装对于ESP系统中的电子部件,需要通过焊接技术将电路板上的电子元件连接起来,并进行封装保护,以防潮湿和其他环境因素导致性能降低。
6. 质量检测与测试每个子模块装配完成后,必须经过严格的质量检测和功能测试。
包括但不限于耐压试验、电子元件功能检验、信号响应时间测量等,确保每一部分都能正常工作,满足安全标准。
7. 集成组装所有通过测试的子模块将被整合到一起,形成完整的ESP系统。
这个环节要求非常高的精度和操作规范,因为任何小的错误都可能影响到整个系统的性能。
8. 系统级测试完成集成后,整个ESP系统将安装到相应的试验台上进行系统级的测试。
轻型载货汽车匹配横向稳定杆探析
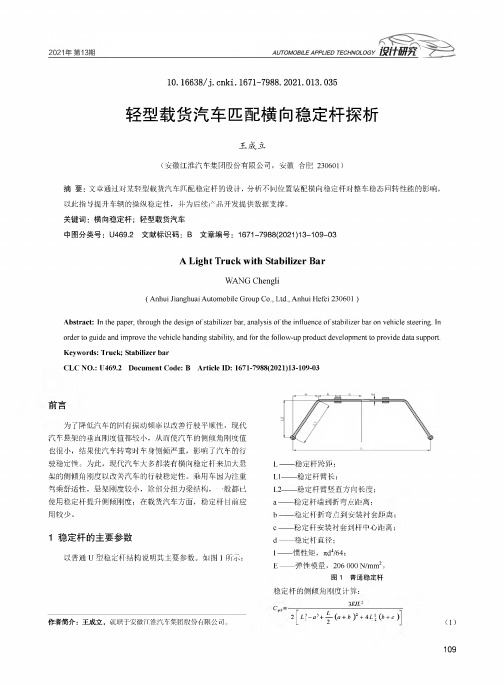
8 308.0
前簧上质量(kg)
2 521.7
后簧上质量(kg)
4 820.0
整车质心高度(mm)
1 500.0
前簧下质量质心高度(mm)
397.0
后簧下质量质心高度(mm)
397.0
前轴侧倾中心高度(mm)
414.0
后桥侧倾中心高度(mm)
570.5
轴距(mm)
3 845.0
质心到前轴距离(mm)
图4侧倾角刚度影响
稳定杆对于侧倾,并不是稳定杆侧倾角刚度越大越好, 有研究表明,继续增大横向稳定杆刚度,对减小车身侧倾角 的工程意义不大,如图4所示。
3计算整车匹配稳定杆的侧倾度⑶
以某卡车车型为例,我们分别计算四种情况下(无稳定 杆、带前稳定杆、带后稳定杆、前后均带杆)车辆侧倾度和 0.4 g侧向加速度的侧倾角。
2 524.1
质心到后轴距离(mm)
1 320.9
簧上质量(kg)
7 341.7
簧上质心高度(mm)
1 6452
簧上质量质心距前轴距离(mm) 2 524.3
簧上质量质心師轴距离(mm)
1 320.7
前板簧距(m)
0.8
后板簧距(m)
1.0
总侧倾角刚度系数(N-m/(°))
8 585.5
hp (mm)
最大输入扭矩(N.m)
转向型式
前
型式
后
型式
6MT 6.091/3.650/2.274/1.478/
1.000/0.774/5.645 539
循环球式、动力转向 钢板弹簧式 钢板弹簧式
气压(kPa) 轮胎规格
数目(前/后)
670 8.25R16
- 1、下载文档前请自行甄别文档内容的完整性,平台不提供额外的编辑、内容补充、找答案等附加服务。
- 2、"仅部分预览"的文档,不可在线预览部分如存在完整性等问题,可反馈申请退款(可完整预览的文档不适用该条件!)。
- 3、如文档侵犯您的权益,请联系客服反馈,我们会尽快为您处理(人工客服工作时间:9:00-18:30)。
汽车横向稳定杆 (Stabilizer Bar or Torsion Bar) 生产工艺简介
现代轿车为了追求舒适性,悬架都很软,即固有频率很低,为提高悬架的侧
倾角刚度,减小横向倾斜,悬架中大部分都设有横向稳定杆,以保证良好操纵稳
定性。横向稳定杆属于汽车的二类安全件,其生产厂家属于汽车整车厂(OEM)
配套体系中的第一供应链(Teir 1)供应商,生产厂家的质量管理体系(QMS)
必须通过汽车行业质量管理体系ISO/TS16949:2002的认证。
横向稳定杆由弹簧钢制造,呈扁平的U形,横向地安装在汽车前端或后端,
(大部分安装在车架和控制臂之间,也有安装在轮毂等其他位置的。)因需避让
底盘上的各种零部件,横向稳定杆具有多样性和复杂性。一般来说,一部轿车至
少有一根前稳定杆,大部分的还有一根后稳定杆。其他车辆,如卡车也至少有一
根稳定杆。车型不同则形状不同,同一辆车前后杆也不同,相互间也无相似之处。
平面结构极少,大部分都是空间结构,而且形状极其复杂。部分车型的稳定杆已
经开始采用空心结构,我司也正在和合肥工业大学合作开发空心稳定杆和相关新
材料的开发。
横向稳定杆的主要生产和检验手段是加热成型、锻造、淬火、回火、探伤、
表面强化、喷涂、硬度检测、元素分析和金相分析等。成品主要指标有空间几何
尺寸,表面硬度、刚度、疲劳强度,外观要求等。
我们安庆市恒瑞达汽车零部件制造有限公司(ANQING HRD
AUTOMOBILE SPARE PARTS MANUFCTURE CO., LTD.)是生产包括横向稳
定杆在内的汽车杆件开发、生产、销售和服务的专业提供商。
横向稳定杆的主要材料是弹簧钢,一般由客户提供的图纸决定。主要材质为:
60Si2Mn(SUP7)、60Si2MnA、55CrMn(SUP9、55Cr3)、50CrVA(SUP10)。
材料规格一般为ф18-ф40圆钢不等。这些材料主要由专业的特种钢材生产厂家
生产,我司根据销售和生产计划提前向这些厂家订购(或定做)上述材料。
购进材料后,我们首先要核对材料规格和数量以及随货的质量保证书,并由
公司质量部对其进行来料检验(IQC),检验合格后方可办理入库手续。检验项
目有尺寸检验、化学元素分析、物理性能(主要是硬度)和金相分析。
制造部根据市场部的销售计划和销售合同制定生产计划,并根据技术部制定
的材料消耗定额向库房领料,领料后根据技术部制定的工艺和标准和制造部本身
的设备操作规程组织生产,质量部组织检验。
根据定单的大小和配套的不同阶段,我们将生产工艺和生产组织方式分为大
批量(5万件以上)和小批量(包含样件试制)两种。
在定单很小以及为整车厂提供样件时,我们采用分段成型的生产制造工艺,
主要工艺路线为:
下料(Shear)—根据对图纸的放样结果,用锯床(Cutting machine)将原
材料按规定长度切割成一段一段的坯料。
校直(Rectify)—发现有坯料的直线度不好时,用压力机(Press machine)
对其进行校直。
部分加热(Partial Heating)—在小批量生产时,我们根据不同产品图纸和
要求分部对坯料进行加热,能使用中频感应加热炉(Mid-frequency
induction furnace)的,我们尽量使用中频感应加热炉;特别是中间工
序需要加热时,杆件已部分弯曲成型,不能进入中频感应加热炉时,
我们采用乙炔氧气(C2H2-O2)燃烧加热。
锻造(Forging)—加热后(在800℃以上),根据工艺安排有的局部在曲柄
压力机(Crank press machine)上用锻模锻造成型。
弯曲成型(Bending)—加热后(在800℃以上),根据工艺安排有的局部在
手动成型模具上手动成型。
切边、冲孔(Cutting、hole)—加热后(在800℃以上),根据工艺安排有
的局部在曲柄压力机(Crank press machine)上使用冲模进行切边、
冲孔。
淬火(Quenching)—上述工序全部结束,并经过序间检验(IPQC)合格后,
用箱式电阻炉(Box resistance furnace)进行加热,在满足一定的时间
和温度条件后(一般为900-950℃、30Min)装夹在专用杆件淬火机
(Hyd.clip quenching machine)上进入淬火油池进行淬火。
回火(Tempering)—在淬火结束后48小时内必须对工件进行回火,既保证
硬度和刚度,又防止工件开裂。回火在回火炉(Tempering furnace)
里进行。
表面强化(Surface hardening)—为进一步提高工件的疲劳强度,还要使用
抛丸机(Blasting machine)对工件进行表面强化处理。
探伤(Non-breaking failure detector with magnetic)—为保证横向稳定杆产
品的质量,还必须使用磁粉探伤机(Detector with magnetic machine)
对工件进行100%的探伤。
表面喷涂(Surface spraying)—根据不同客户的图纸要求,我们使用高压静
电喷粉、漆线(High-voltage electrostatic coating line)对横向稳定杆
的表面进行喷粉或者喷漆以提高产品的耐腐蚀性以及符合客户的外观
要求。
印字、包装等(Print、Packing)—最后,我们按照客户的要求在产品上印
字。在经过最终检验(FQC)合格后,按照我们的规范或者客户的要
求进行包装并经出厂检验(OQC)合格后即可交付客户。
在接到正式定单后,我们会采用大批量的生产工艺路线;或者我们经过合同
评审决定直接采用大批量的生产工艺路线送样,大批量工艺路线为:
下料(Shear)—根据对图纸的放样结果,用锯床(Cutting machine)将原
材料按规定长度切割成一段一段的坯料。
校直(Rectify)—发现有坯料的直线度不好时,用压力机(Press machine)
对其进行校直。
整体加热(Heating)—使用中频感应加热炉(Mid-frequency induction
furnace)的,对坯料进行整体加热。
整体成型(Bending)—加热后(在950℃左右),在液压全自动成型机
(Auto-hyd. Forming machine)一次全部直接成型。
余热淬火(Quenching)—从液压全自动成型机里出来的坯料直接装夹在专
用杆件淬火机(Hyd.clip quenching machine)上进入淬火油池进行淬
火。
后道其他工序同小批量一样,大批量生产工艺主要是在整体加热、直接整体
成型和余热直接淬火上比小批量生产工艺大大提高了产品的生产效率、过程能
力,降低了成本。但液压全自动成型机的一次投入比较大,而且是专用设备,产
品变更后就没有任何价值。
为保证产品质量,我司检测设备有金属元素分析仪(Analyzing instrument
for chemical element)、碳硫分析仪(Analyzing instrument for C.S)、材料金相
组织分析仪(Analyzing instrument for material metallography)、刚度检测机
(Rigidity property testing machine)、疲劳实验机(Fatigue testing machine)和
盐雾实验机(Salt spray test machine)。
一般来说,打入一个新的整车厂按照ISO/TS16949:2002的要求必须的程序有
APQPⅠ-Ⅴ(产品质量先期策划、即CP控制计划、FMEA产品潜在失效模式分
析、 MSA测量系统分析、SPC统计技术等)和OTS(小样件批准程序)以及最
后的PPAP生产件批准程序。