多轴电机控制传动系统
简析多电机同步控制技术

简析多电机同步控制技术我国现代工业的不断发展与机械自动化技术的不断提高,很多生产场合都无法满足现代工业的发展要求,其电机控制系统要求多台电机共同驱动一台设备运作。
在整个生产过程中,应尽量满足现代工业的发展需求,确保这些电机能够协调运行,所以多电机同步控制技术的应用越来越广泛,这种技术在机械传动系统中,尤其是卷接机组中,可以通过多个电机向多个主要机组,传递其生产需要的动力,这种传动方式是控制方式上的一大创新。
一、多电机同步控制技术为了保证多电机能够实现同步控制,可以通过两种方式:机械方式和电方式。
在同步控制技术应用初期,机械同步控制技术在工业自动化生产中广泛应用。
因为机械控制方式与传动连接十分可靠,这种连接在应用初期得到了广泛应用,但是这种机械控制方式有一些常见的缺点,整个系统智能运用一台电机作为动力输出,所以动力分配到各个单元的动力功率都比较小,很难进行系统同的维修工作,且系统只能获得有效的传动范围[1]。
机械同步控制系统通过齿轮、皮带、链条这些零件进行传动,造成整个系统出现劣迹误差,所以在整个控制过程中,系统的控制精度很容易受到影响。
工作人员在一些精度要求较高的环境,电方式的多电机协调控制更加灵活,拥有更高的精度和稳定性,并能在生产实践中,逐渐被完善。
二、卷接机中同步控制技术的应用流程多电机同步控制技术一般选用YJ27卷接机组,其机械设备结构复杂,且各个鼓轮的转速间应保持精准的比例关系。
现阶段,相关单位采用的是传统的机械式齿轮传动方式对各个鼓轮进行同步控制,从而保证系统精度,对于高速环境下的齿轮,工作人员应为其设置润滑系统,确保整个系统的传动链不会太长,机构系统导致传动造成过大,在连续工作时,造成设备损坏,润滑齿轮箱容易出现漏油,以及传动误差较大等现象,设备的维修量会大幅增加,传动系统速度的波动会影响卷接机的运用功能[2]。
(一)偏差耦合结构控制工作人员以YJ27卷接机组的几个主要的工作鼓轮作为研究对象,并总结这些设备的机械传动关系,得出他们之间的速度比例,然后算出每个鼓轮的负载特点,将与之相对的永磁同步电动机作为这种设备的驱动电机,在一定环境中建立起一个鼓轮的同步控制系统的仿真模型,然后通过这种仿真模型的相关原理,运用改进型屏偏差耦合对结构进行控制,制定模糊滑模控制策略,这也是一种比较理想的控制方法[3]。
《电力传动控制系统》期末考试复习题,模拟题
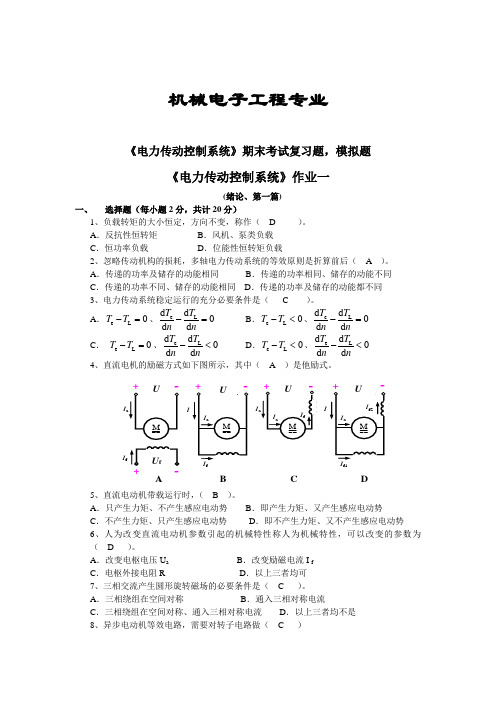
机械电子工程专业《电力传动控制系统》期末考试复习题,模拟题《电力传动控制系统》作业一(绪论、第一篇)一、 选择题(每小题2分,共计20分)1、负载转矩的大小恒定,方向不变,称作( D )。
A .反抗性恒转矩B .风机、泵类负载C .恒功率负载D .位能性恒转矩负载2、忽略传动机构的损耗,多轴电力传动系统的等效原则是折算前后( A )。
A .传递的功率及储存的动能相同B .传递的功率相同、储存的动能不同C .传递的功率不同、储存的动能相同D .传递的功率及储存的动能都不同3、电力传动系统稳定运行的充分必要条件是( C )。
A .e L 0T T -=、e L d d 0d d T T n n -= B .e L 0T T -<、e L d d 0d d T T n n-= C . e L 0T T -=、e L d d 0d d T T n n -< D .e L 0T T -<、e L d d 0d d T T n n -< 4、直流电机的励磁方式如下图所示,其中( A )是他励式。
5、直流电动机带载运行时,( B )。
A .只产生力矩、不产生感应电动势B .即产生力矩、又产生感应电动势C .不产生力矩、只产生感应电动势D .即不产生力矩、又不产生感应电动势6、人为改变直流电动机参数引起的机械特性称人为机械特性,可以改变的参数为( D )。
A .改变电枢电压U aB .改变励磁电流I fC .电枢外接电阻RD .以上三者均可7、三相交流产生圆形旋转磁场的必要条件是( C )。
A .三相绕组在空间对称B .通入三相对称电流C .三相绕组在空间对称、通入三相对称电流D .以上三者均不是8、异步电动机等效电路,需要对转子电路做( C )III f I I f1A B C DA .频率折合B .匝数折合C .频率折合和匝数折合D .不需要任何折合9、异步电动机的机械特性为一条( D )A .上翘的直线B .水平的直线C .下垂的直线D .非线性的曲线10、同步电动机的机械特性为一条( C )A .上翘的直线B .水平的直线C .下垂的直线D .非线性的曲线二、 填空题(每题2分,共计28分)1、 当T e = T L 时,电动机 运行,为稳态或静态。
电机及其传动系统 原理、控制、建模和仿真

电机及其传动系统原理、控制、建模和仿真电机及其传动系统是现代工业中常见的电力传动装置,其原理、控制、建模和仿真是电机学习的重要内容。
本文将从以下几个方面进行介绍。
一、电机原理:电机是将电能转化为机械能的装置。
按工作原理可以分为直流电机和交流电机两大类。
直流电机以直流电源为动力,通过磁场与电流的相互作用实现转动。
交流电机以交流电源为动力,通过电磁感应原理产生转动力。
电机工作原理涉及到电磁学、电路学和力学等多个学科的知识。
二、电机控制:电机控制是指通过对电机的电流、电压或磁场进行调节,使电机达到所需要的运动控制要求。
常见的电机控制方法有直接启动控制、启动电阻控制、电压调制控制、频率调制控制等。
在现代工业中,常使用的电机控制装置有变频器、PLC、单片机等。
三、电机建模:电机建模是指通过数学方法将电机的物理特性转化为数学模型,以便进行仿真计算和控制设计。
电机建模通常从电机的电磁特性和转动特性入手,运用电机理论和系统理论的知识,建立模型方程。
根据电机的类型和用途不同,建模方法也有所差异,常见的建模方法有瞬态模型、稳态模型、频域模型等。
四、电机仿真:电机仿真是指使用计算机软件对电机的运行过程进行模拟和分析。
通过仿真可以得到电机在不同工况下的性能指标、效率、负载特性等信息。
电机仿真可以辅助电机的设计和调试工作,提高工作效率。
常用的电机仿真软件有ANSYS、MATLAB/Simulink、ADAMS等。
综上所述,电机及其传动系统的原理、控制、建模和仿真是电机学习中不可忽视的内容。
只有深入理解电机原理,掌握电机的控制方法,灵活应用电机建模和仿真技术,才能在实际工程中高效地设计、操控和优化电机及其传动系统。
机电传动控制第五版课后答案--最全版

机电传动控制第五版课后答案--最全版机电传动控制是一门涉及机械、电气和控制等多领域知识的重要学科,对于相关专业的学生和从业者来说,掌握这门课程的知识至关重要。
而课后习题的答案则是检验学习成果、加深理解的重要工具。
以下为您提供机电传动控制第五版的课后答案,希望能对您的学习有所帮助。
第一章绪论1、机电传动控制的目的是什么?答:机电传动控制的目的是将电能转变为机械能,实现生产机械的启动、停止、调速、反转以及各种生产工艺过程的要求,以满足生产的需要,提高生产效率和产品质量。
2、机电传动系统由哪些部分组成?答:机电传动系统通常由电动机、传动机构、生产机械、控制系统和电源等部分组成。
电动机作为动力源,将电能转化为机械能;传动机构用于传递动力和改变运动形式;生产机械是工作对象;控制系统用于控制电动机的运行状态;电源则为整个系统提供电能。
3、机电传动系统的运动方程式是什么?其含义是什么?答:运动方程式为 T M T L =J(dω/dt) 。
其中,T M 是电动机产生的电磁转矩,T L 是负载转矩,J 是转动惯量,ω 是角速度,dω/dt 是角加速度。
该方程式表明了机电传动系统中电动机的电磁转矩与负载转矩之间的平衡关系,当 T M > T L 时,系统加速;当 T M < T L 时,系统减速;当 T M = T L 时,系统以恒定速度运行。
第二章机电传动系统的动力学基础1、为什么机电传动系统中一般需要考虑转动惯量的影响?答:转动惯量反映了物体转动时惯性的大小。
在机电传动系统中,由于电动机的转速变化会引起负载的惯性力和惯性转矩,转动惯量越大,系统的加速和减速过程就越困难,响应速度越慢。
因此,在设计和分析机电传动系统时,需要考虑转动惯量的影响,以确保系统的性能和稳定性。
2、多轴传动系统等效为单轴系统的原则是什么?答:多轴传动系统等效为单轴系统的原则是:系统传递的功率不变,等效前后系统的动能相等。
3、如何计算机电传动系统的动态转矩?答:动态转矩 T d = T M T L ,其中 T M 是电动机的电磁转矩,TL 是负载转矩。
机电传动系统的组成

机电传动系统的组成
机电传动系统的组成包括:电机、机械传动装置和控制系统。
1. 电机:电机是机电传动系统的核心组成部分,负责将电能转换为机械能等形式的能量输出。
常见的电机包括直流电机、交流电机和步进电机等。
根据具体应用的需求,选择适合的电机类型。
2. 机械传动装置:机械传动装置主要用于将电机的旋转运动转换为所需的线性运动、转动力矩或转速等。
常见的机械传动装置包括齿轮传动、皮带传动、链传动和联轴器等。
根据传动的需求和性能要求,选择合适的机械传动装置。
3. 控制系统:控制系统用于控制和实时监测机电传动系统的运行状态,常见的控制方式有手动控制和自动控制。
手动控制可以通过开关、按钮等手动操作来控制传动系统;自动控制则需要使用传感器、控制器、编码器等部件,通过采集和处理输入和输出信号,实现对传动系统的自动控制和调节。
以上是机电传动系统的主要组成部分,不同的应用领域和具体需求可能会有所不同,需要根据具体情况进行选择和配置。
多永磁电机传动系统的同步控制策略研究

多永磁电机传动系统的同步控制策略研究一、引言随着工业自动化和智能制造的快速发展,多永磁电机传动系统在工业生产中的应用越来越广泛。
然而,由于多个电机之间存在一定的耦合性,传统的独立控制策略往往难以实现多电机之间的同步控制。
因此,研究多永磁电机传动系统的同步控制策略具有重要的现实意义。
本文将围绕永磁电机控制原理、同步控制策略设计、同步控制策略实现、实验验证与分析、结论与展望等方面展开讨论。
二、永磁电机控制原理永磁电机是一种具有高效率、高转矩密度的电动机,其结构主要包括定子、转子和永磁体。
在永磁电机的控制中,主要采用矢量控制方法,通过控制定子电流的幅值和相位来控制电机的转速和转矩。
同时,矢量控制方法还可以减少电流和电压的谐波分量,提高电机的运行效率。
三、同步控制策略设计为了实现多永磁电机传动系统的同步控制,需要设计一种合适的同步控制策略。
该策略需要考虑多个电机之间的耦合性,采用一种协调控制方法来确保各个电机之间的同步运行。
具体而言,可以采用以下几种方法:1.分布式协调控制:通过在每个电机上安装独立的控制器,实现各个电机的独立控制。
同时,通过通信网络将各个电机的状态信息进行共享,从而实现对各个电机的协调控制。
2.主从控制:将其中一个电机作为主电机,其他电机作为从电机。
主电机的转速和转矩作为其他电机的参考值,通过调整其他电机的电流和电压来实现与主电机的同步运行。
3.模型预测控制:通过建立电机的数学模型,预测未来一段时间内的转速和转矩变化。
然后,根据预测值调整各个电机的电流和电压,以确保各个电机的同步运行。
四、同步控制策略实现为了实现上述同步控制策略,需要采用合适的算法和软件实现方法。
具体而言,可以采用以下几种方法:1.算法实现:根据所选择的同步控制策略,采用合适的算法来实现对各个电机的协调控制。
例如,可以采用PID算法、模糊控制算法等来实现对电机的精确控制。
2.软件实现:采用合适的编程语言和开发工具来实现同步控制策略的软件实现。
五轴联动数控机床的设计与研究
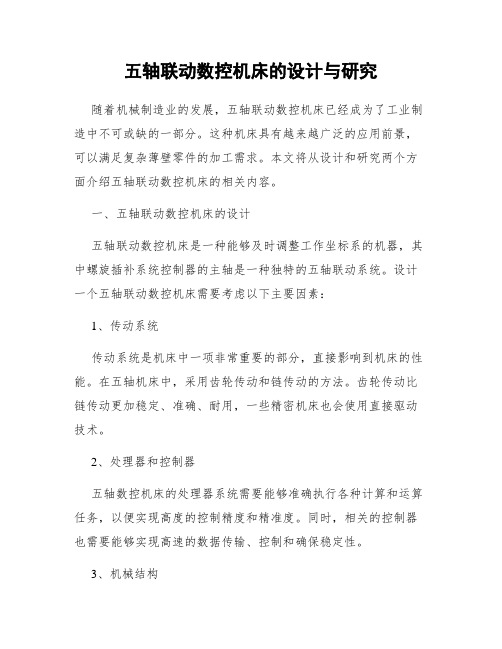
五轴联动数控机床的设计与研究随着机械制造业的发展,五轴联动数控机床已经成为了工业制造中不可或缺的一部分。
这种机床具有越来越广泛的应用前景,可以满足复杂薄壁零件的加工需求。
本文将从设计和研究两个方面介绍五轴联动数控机床的相关内容。
一、五轴联动数控机床的设计五轴联动数控机床是一种能够及时调整工作坐标系的机器,其中螺旋插补系统控制器的主轴是一种独特的五轴联动系统。
设计一个五轴联动数控机床需要考虑以下主要因素:1、传动系统传动系统是机床中一项非常重要的部分,直接影响到机床的性能。
在五轴机床中,采用齿轮传动和链传动的方法。
齿轮传动比链传动更加稳定、准确、耐用,一些精密机床也会使用直接驱动技术。
2、处理器和控制器五轴数控机床的处理器系统需要能够准确执行各种计算和运算任务,以便实现高度的控制精度和精准度。
同时,相关的控制器也需要能够实现高速的数据传输、控制和确保稳定性。
3、机械结构机械结构是机床中另一个非常重要的部分,通常采用刚性框架、机械手臂和伺服电机来实现五轴联动机床的稳定结构。
刚性框架具有高度的刚度和精度,可以保证零件的加工质量。
机械手臂则可以支持刀具运动,伺服电机则可以对刀具进行实时控制。
4、人机交互界面五轴联动数控机床需要有直观、易于操作的人机交互界面。
机床操作人员可以通过交互界面轻松调整五轴联动系数和各个轴的参数。
二、五轴联动数控机床的研究五轴联动数控机床的研究领域非常广泛,主要涉及以下方面:1、模型构建实现五轴联动的机床模型需要建立一个全球统一的数学模型,考虑到机床结构、动力和切削力等系数。
在五轴联动加工过程中,所有的轴向变量的运动都是依靠模型来进行研究和实践的。
2、刀路规划刀路规划在机床加工中是一个非常重要的环节,它直接影响到零件加工的质量。
在五轴联动中,刀路规划必须考虑到机床的轴向变量以及工件的加工要求。
为了提高零件的加工质量和加工效率,研究人员需要探索出一种先进的刀路规划算法。
3、控制技术五轴联动数控机床控制技术是这个领域的重点研究,它主要涉及到如何实现高精度控制和高速运动。
电机传动系统布置介绍

定制式布置:根据具体应用和需求,定制电机传动系统的布置方式,提高系统效率和性能。
布置方式的优缺点
集中式布置:优点是结构紧凑,便于维护;缺点是占用空间大,散热困难。
分散式布置:优点是节省空间,散热性好;缺点是结构复杂,维护困难。
演讲人
电机传动系统的定义
电机传动系统是利用电力驱动机械运动的装置
01
包括电机、传动机构、控制装置等部分
02
电机传动系统可以实现能量的转换和传递
03
广泛应用于各种机械设备和自动化系统中
04
电机传动系统的分类
直流电机传动系统:使用直流电作为电源,结构简单,控制方便
1
交流电机传动系统:使用交流电作为电源,功率大,效率高
05
安全可靠:保证电机传动系统的安全性和可靠性,防止故障发生
02
设计原则的应用实例
紧凑型设计:通过优化布局,减小体积和重量,提高传动效率
模块化设计:将传动系统划分为多个模块,便于维护和更换
集成化设计:将多个功能集成到一个部件中,降低成本和安装空间
智能化设计:采用智能控制技术,提高传动系统的响应速度和精度
延长使用寿命:定期维护与保养可以延长电机传动系统的使用寿命,降低维修成本。
维护与保养的具体内容
定期检查电机传动系统的各个部件,确保其正常工作
定期更换润滑油,保持传动系统的润滑
定期清洁传动系统,防止灰尘和杂物的积累
定期检查传动系统的紧固件,确保其紧固可靠
定期检查传动系统的电气系统,确保其正常工作
定期检查传动系统的冷却系统,确保其正常工作
定期检查传动系统的安全防护装置,确保其正常工作
- 1、下载文档前请自行甄别文档内容的完整性,平台不提供额外的编辑、内容补充、找答案等附加服务。
- 2、"仅部分预览"的文档,不可在线预览部分如存在完整性等问题,可反馈申请退款(可完整预览的文档不适用该条件!)。
- 3、如文档侵犯您的权益,请联系客服反馈,我们会尽快为您处理(人工客服工作时间:9:00-18:30)。
驱动模块原理图
驱动模块实物图
3、液晶显示模块原理
接收主控所发出的程序 命令,显示相应电机的编号、 转速。
4、电机模块原理
由单片机控制5个 24v 30瓦的电机,实现电机的加速、 减速和停止。
显示模块实物 电机模块实物
六、算法分析
#include<reg52.h> #include"pcf8591.h" #include"5110.h" sbit key_mode=P1^5; sbit key_up =P1^6; sbit key_down=P1^7; bit flago=0; bit flag=0; void delay_ms(int ms) {
与模拟信号地转换,再通过LM324产生稳定的三角波电压 与可控制电压的占空比(PWM)来实现直流电机的加速、 减速和选择的控制要求。
3、液晶显示模块
本系统的显示模块主要用到的是Nokia/诺基亚 5110 LCD.接收主控所发出的程序命令,显示相应电机8 的点阵LCD,可以显示3 行汉字, • 采用串行通信,接口信号线少; • 采用低电压供电,且具有掉电模式。 • 模块的体积很小
主控模块原理图
主控模板实物图
2、驱动模块原理
(1)PWM脉冲生成模块:它利用 LM324芯片产生PWM脉冲,通过改变 脉冲的占空比去调节电机的速度。 (2)PCF8591芯片接收模 块:PCF8591芯片接受到主控模块输 出的脉冲指令,其输出接入PWM脉冲 生成模块中,从而改变PWM的占空比。 (3)通信接口模块:它实现了主控 模块与电机,电机与电机之间的通 信。 (4)电机部分:由主控模块的按键 发出指令,通过调速驱动产生相对应 的脉冲频率来改来控制电机的转速。
} } }
}
if(key_down==0&&flag==1)
七、系统测试记录与结果分析
while(1) {
{ delay_ms(150);
if(key_mode==0) {
delay_ms(200); mode++; if(mode>=6) mode=1;flag=1;flago=1; } if(key_up==0&&flag==1) {
delay_ms(150); if(sudu[mode-1]<255) sudu[mode-1]+=5; flago=1;
4、电机模块 本系统由单片机控制5个 24v 30瓦的电机,
形成闭环控制系统。它主要有两部分组成:定子, 转子。
四、算法理论基础
五、每个部分原理
1、主控模块原理
(1)单片机最小系统:它是整个主控模块的核心,它负责接收电脑 所发送的程序指令,包括复位、晶振及单片机,这里我们使用的是 AT89C52RC单片机。 (2)电 源:采用直流5V的电压,为单片机供电。 (3)液晶接口:连接液晶显示屏,使电机的转速、编号在上面显示 出来。 (4)PCF8591 接 口:连接PCF8591芯片,PCF8591的功能包括多路 模拟输入、内置跟踪保持、8-bit模数转换和8-bit数模转换。 (5)串口通信:它主要是将接受来自CPU的并行数据字符转换为连续 的串行数据流发送出去,同时可将接受的串行数据流转换为并行的数 据字符供给CPU的器件。 (6)按 键:三个按键分别控制电机的编号、加速和减速。
三、设计方案
1、系统设计方案图
2、方案详细解释
多轴电机控制传动系统包括主控模块、调速 驱动模块、液晶显示模块、电机模块。 1、主控模块
接受电脑发送来的程序指令,数据处理后通过驱动 接口向调速驱动模块发送指令驱动电机转动。同时将数据 发送给显示屏并显示出来。
2、调速驱动模块 接受主控模块发送的指令给PCF8591实现数据信号
int i; while(ms--) {
for(i=0;i<110;i++); }
}
main() { unsigned char sudu[6]={0,0,0,0,0,0}; int mode=5; LCD_init(); LCD_clear(); LCD_write_string(1,0,"合肥求精"); LCD_write_string(1,1,"电机 "); LCD_write_string(1,2,"转速 "); LCD_write_Data(5,1,0,3); LCD_write_Data(5,2,0,3); sudu[0]=90;sudu[1]=90;sudu[2]=90; sudu[3]=90;sudu[4]=90; Write_PCF8591(0,sudu[0]); Write_PCF8591(1,sudu[1]); Write_PCF8591(2,sudu[2]); Write_PCF8591(3,sudu[3]); Write_PCF8591(4,sudu[4]);
设计单位:****** 项目成员:*** *** *** *** 项目组长:***
一、项目背景
随着现代化工业步伐的加快,一些企业 和工厂的规模越来越大,然而规模大了却带来 了许多问题:比如当生产线过长时,企业或工 厂必须对模式的改变进行相应的人员增加,这 样不仅增加了投入成本,也带来了许多不便。 而多轴控制传动系统正好解决了这些问题 。
多轴电机传动系统在现代生产中应用比 较广泛:
1、大型自动化加工基地; 2、自动机仪表车床。
二、设计思路
设计要求
• 要求用一块单片机系统控制5个 24v 30瓦的 电机,闭环控制系统。
• 实现对任意一个电机的加速、减速、停止 操作,
• 把每个电机的速度值,返回到系统板,并 用液晶显示。
• 可同时操作所有电机。
if(sudu[mode-1]>0)sudu[mode-1]-=5; if(sudu[mode-1]<90)sudu[mode-1]=90; flago=1; }
if(flago==1) {
flago=0; LCD_write_Data(5,1,mode,3); Write_PCF8591(mode-1,sudu[mode-1]); LCD_write_Data(5,2,sudu[mode-1]-90,3);