国外高分子材料新型注射成型技术(精)
PLA医美微针高速注塑成型技术的研究

PLA医美微针高速注塑成型技术的研究摘要:PLA医美微针注塑成型技术的研究旨在研究PLA材料的性能和PLA医美微针制造的工艺流程,并探究其在医美领域的应用前景。
通过对PLA材料的分析和实验,得出其高生物可降解、低毒性、低过敏性的优点,因此能够在医美微针制造中广泛应用。
同时,通过研究微针注塑成型工艺流程、模具设计及其制造、成型参数等方面,得出了一套完整的PLA医美微针注塑成型技术,并用实例进行了验证。
研究表明,PLA医美微针注塑成型技术具有简单、快速、成本低等优点,并在医美领域具有广阔的应用前景。
关键词:PLA材料;微针注塑成型;工艺流程;医美领域;应用前景PLA医美微针高速注塑成型技术的研究一、前言随着人们生活质量的提高和美容意识的增强,医美行业的发展越来越迅速。
微针注射治疗成为医美行业的重要手段之一,可以有效改善皮肤质量、淡化皱纹、改善皮肤色素等。
随着PLA材料在生物医学领域中的广泛应用,PLA材料制作微针注射器也成为研究热点。
本文旨在探究PLA医美微针注塑成型技术的研究现状和未来发展趋势,对PLA材料的性质和工艺流程进行详细分析和论述,为医美行业的发展提供一定的参考和借鉴价值,也有助于推动PLA材料的应用和开发。
二、PLA材料的分析和实验PLA,全称聚乳酸(Poly Lactic Acid),是一种重要的生物可降解高分子材料,由乳酸单体经过聚合得到。
PLA具有优异的物理性质和生物相容性,在医疗器械、药物缓释、绷带等生物领域得到广泛应用。
为了研究PLA材料在医美微针制造中的应用,对PLA材料进行了性能测试。
测试结果表明,PLA材料具有以下优点:1.高生物可降解性:PLA材料是可生物降解的高分子,可以在生物环境中自行降解,不会污染环境。
2.低毒性:PLA材料不含有害物质,没有毒性和副作用,是无害的生物材料。
3.低过敏性:PLA材料的生物相容性良好,不会引起过敏反应。
三、微针注塑成型工艺流程微针注塑成型是PLA医美微针制造的重要工艺,其步骤主要包括:1.模具设计:模具设计是微针注塑成型的关键,模具的大小、形状和尺寸对微针的制作起着决定性作用。
微注射成型技术国际最新发展与应用
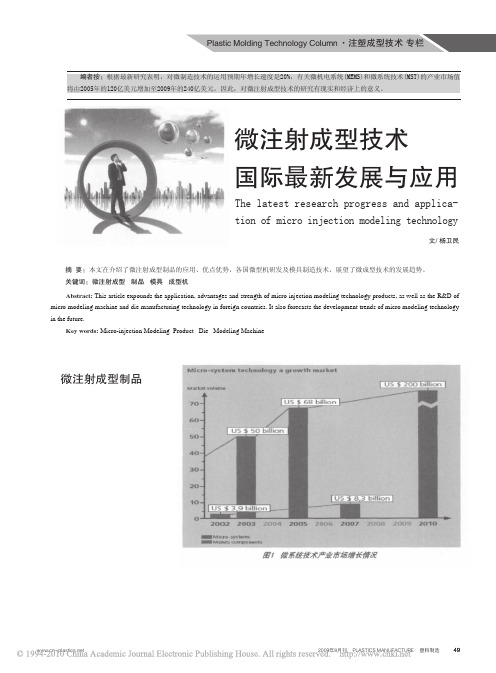
(2)微机械制件:电动齿轮控制 器、多纤维柱塞、微垫圈、辊子、微热 交换器、微齿轮和齿轮机架、注模相互 连接设备、电子零件、表芯、微机电组 件、微模片泵、液体分离器。
(3)微型光学制件如光学透镜、光 学纤维元件等、DVD塑料基层、导光板。
(4)微执行器如微开关等。 (5)医疗用微导管、微浓度测量 仪、生物芯片、微混合器、小型药用过 滤器、人造器官等。(如表1) 微塑件产品举例: Ribcon®连接器、红外线微型分光
Plastic Molding Technology Column ·注塑成型技术 专栏
编者按:根据最新研究表明,对微制造技术的运用预期年增长速度是20%,有关微机电系统(MEMS)和微系统技术(MST)的产业市场值 将由2005年的120亿美元增加至2009年的240亿美元。因此,对微注射成型技术的研究有现实和经济上的意义。
1、微注射成型技术发展于20世纪 80年代。20世纪90年代,欧洲、日本和 美国的一些公司就与科研机构合作开发 了各类专用微注射成型机。
2、目前国外主要设备供应厂商 包括Arburg、Battenefld、Dr.Boy、
射机的注射速度为200mm/s,电气伺服马 达驱动式注射机的注射速度为600mm/s, 而微注射成型工艺通常要求聚合物熔体 的注射速度达到800mm/s以上。
微注射成型制品
1、微机电系统的发展 (1)对微制造技术的运用预期年 增长速度是20%。 随着科学技术的进步,产品不断向 微型化方向发展,产生了新世纪产业需 求的微机电系统(MEMS)技术。 微机电一直是这几年备受瞩目的研 究方向,在光通讯、3C、生化等产业的 快速进步中已可看出,产品体积持续小 型化、轻量化、功能更多样化,加上IC 的制程纳米化技术的纯熟,微细化零组 件的生产制程将有急迫性的需求。对微 制造技术的运用预期年增长速度是20%。 (2)根据最新研究表明,随着对 微型制品需求的增加,有关微机电系统 (MEMS)和微系统技术(MST)的产业市场值 将由2005年的120亿美元增加至2009年的 240亿美元。(如图1所示)
聚双环戊二烯反应注射成型的研究进展

聚双环戊二烯反应注射成型的研究进展乔新峰;杨维成;付宏伟;罗勇【摘要】聚双环戊二烯(PDCPD)是采用反应注射成型(RIM)工艺制备的一种新型热固性工程塑料,具有优异的韧性与刚性双重力学性能,聚双环戊二烯正成为取代某些传统材料(PP、PE等)的新型高抗冲材料.综述了PDCPD的聚合机理、材料特点及性能、材料应用与改性研究,展望了PDCPD的发展趋势和应用领域.【期刊名称】《上海塑料》【年(卷),期】2017(000)004【总页数】6页(P9-14)【关键词】聚双环戊二烯;聚合机理;材料性能;改性【作者】乔新峰;杨维成;付宏伟;罗勇【作者单位】上海化工研究院有限公司,上海200062;上海化工研究院有限公司,上海200062;上海化工研究院有限公司,上海200062;上海化工研究院有限公司,上海200062【正文语种】中文【中图分类】O632.15聚双环戊二烯(PDCPD)是一种热固性材料,它是由双环戊二烯开环移位聚合反应制备得到,通常采用反应注射成型(RIM:reaction Injection moulding)工艺制备产品。
反应注射成型(RIM工艺)是成型过程中产生化学反应的一种注射成型方法。
该种材料成型方法所使用的原料不是聚合产物,而是将多种液态单体或预聚物按照一定的比例共混入反应注射器中,在共混过程中采用加压手段,共混均匀后注射到闭合模具中,最后在闭合模具内完成材料聚合固化成型。
反应注射成型是一种常用的材料加工方法,该方法既可以生产小型制品,亦可生产大型制件[1]。
由于所使用原料状态为液态,因而采用较小的压力即可以将反应原料快速充满模腔内,有利于降低模具造价,非常适用于生产大型制件。
该材料成型产品由初期的电视机外壳、家具等尺寸较小的制品逐渐发展到现今汽车工业领域中采用的各种高韧性、高品位制品,比如:方向盘、挡泥板、发动机罩等。
该材料成型技术己发展成当前高分子材料加工领域的一种前沿技术[2],它是塑料成型、树脂合成等工艺的一次革新,代表了高分子材料合成的新方向。
高分子材料成型加工(注射成型)详解

作用:将注射油缸的压力传给塑料,并使熔体注射 入模具 (4)分流梭
将物料流变成薄层,使塑料产生分流和收敛流动 加快热传递,缩短传热过程,避免物料过热分解 熔体在分流梭表面流速↑,剪切速度↑,产生较大的 摩擦热,使料温↑,有利于塑料的混合与塑化,有效 提高产量和质量
顿流体,通过圆形截面或平板狭缝形浇口。
ηa= Kγn-1 (n<1) 浇口的截面积↑ ,熔体体积流量↑
高分子材料成型加工
4. 熔体在模腔的流动:
4.1 熔体在典型模腔内的流动方式
4.2 熔体在模腔内的流动类型
高分子材料成型加工
三. 增密与保压过程: 1. 增密过程(压实过程) 2. 保压过程
4. 注射模具 成型零部件
凸模、凹模、型芯、 成型杆、镶块、动模、定模
浇注系统
主流道、分流道、浇口、 冷料阱、导向零件、分型 抽芯机构、顶出、加热、冷却、 排气
二. 注射机的工作过程
高分子材料成型加工
高分子材料成型加工
第二节 注射过程原理
一. 塑化过程 对塑料塑化的要求:塑料熔体进入模腔之前要 充分塑化,达到规定的成型温度。 塑化料各处的温度要均匀一致。 热分解物的含量达最小值。
高分子材料成型加工
2. 按注射机外形特征分类
高分子材料成型加工
高分子材料成型加工
3. 按注射机加工能力分类
注射量:注射机在注射螺杆(柱塞)作一次最大注射 行程时,注射装置所能达到的最大注射量
锁模力:注射机合模机构所能产生的最大模具闭紧力
4. 按注射机用途分类
高分子材料成型加工
二.注射机的基本结构
MIM工艺介绍及其应用

MIM工艺介绍及其应用MIM(Metal Injection Molding)工艺是一种将金属粉末与热塑性或热固性高分子混合,并通过注射成型和烧结工艺制造出复杂金属零件的技术。
MIM工艺结合了传统金属加工和塑料注射成型技术的优点,能够实现高精度、高复杂度的金属零件制造,并在很多行业得到广泛应用。
MIM工艺的制造过程主要包括以下几个步骤。
首先,将金属粉末与高分子材料混合,并制成类似塑料颗粒的混合物。
然后,将混合物注入金属注射成型机中,通过高压注射将其注射到预先设计好的模具中。
注射成型后,通过烧结工艺将混合物中的高分子材料去除,使金属粉末颗粒相互结合,形成致密的金属零件。
最后,对烧结后的零件进行精加工和表面处理,以实现最终的产品要求。
MIM工艺具有许多独特的优点,使其在各个领域得到广泛应用。
首先,MIM工艺可以制造出具有复杂形状和高精度的金属零件,可替代传统加工如铸造、机械加工等。
其次,MIM工艺可以生产不锈钢、合金、硬质合金等多种金属材料的零件,具有高强度和耐磨损性。
此外,MIM工艺还具有节约原材料、降低成本和提高生产效率的优势。
MIM工艺在汽车、电子、医疗器械、航空航天等行业中得到广泛应用。
在汽车行业,MIM工艺可用于制造发动机配件、承载结构件等关键零部件,提高汽车的性能和可靠性。
在电子行业,MIM工艺可用于制造手机壳、键盘、连接器等微小精密零件,提升产品的外观和功能。
在医疗器械领域,MIM工艺可应用于制造植入式医疗器械如人工关节、牙科支架等,提供定制化解决方案。
在航空航天领域,MIM工艺可用于制造航空发动机内部零部件,提高发动机的性能和可靠性。
总之,MIM工艺通过结合金属粉末和高分子材料,实现了复杂形状和高精度金属零件的制造,并在汽车、电子、医疗器械、航空航天等领域得到广泛应用。
随着材料科学和制造工艺的不断进步,MIM工艺将会在更多领域发挥重要作用,并为各行各业提供更多创新的解决方案。
MIM(Metal Injection Molding)工艺是一种先进的金属加工技术,通过将金属粉末与热塑性或热固性高分子混合,并通过注射成型和烧结工艺制造出具有复杂形状和高精度的金属零件。
高分子材料成形工艺

塑料加工
#2022
典型模具结构
#2022
单击此处添加大标题内容
六、塑料件的结构工艺性 在零件结构设计时应注意以下问题: 1.形状 塑件的内外表面形状应在满足使用要求的情况下尽可能易于成形,避免侧孔与侧凹,防止使用侧抽芯或瓣合模而使模具结构复杂,制造成本提高,增加塑件的修整量。 如图8-14所示为防止采用侧抽芯或瓣合分型模具的设计。 2.壁厚 塑件的壁厚应适当和均匀。图8-15所示为壁厚设计的示意图。表8-2为常用工程塑料壁厚参考值。 3.脱模斜度 为了便于脱模和抽芯,防止塑件表面在脱模时划伤,塑件与脱模方向平行的内、外表面应具有合理的脱模斜度,如图8-16所示。 4.加强筋 加强筋的主要作用是加强塑件的强度和刚度,避免塑件变形翘曲,如图8-17所示。筋的方向尽可能与料流方向一致,布局应合理,以减小变形和开裂(图8-18)。
单击此处添加大标题内容
二、快速成形技术的应用 1.快速模具制造 (1)间接制模 间接制模是用 RP技术制造零件原型,然后将原型作为样件用于传统的模具制造,是一种与传统的制模工艺相结合的制模方法。 (2)直接制模 直接制模是利用 RP技术将模具直接制造成形,它不需制作原型样件,是一种与传统的制模工艺完全不同的方法。 2.加速新产品开发 3.在医学中用于器官模型制作 4.与反求工程相结合形成快速设计制造闭环系统
塑料成形工艺 塑料成形方法 注射成形(Inject Forming) 又称注塑成形,其原理是将颗粒状态或粉状塑料从注射机的料斗送进加热的料筒中,经过加热熔融塑化成为粘流态熔体,在注射机柱塞或螺杆的高压推动下,以很大的流速通过喷嘴注入模具型腔,经一定时间的保压冷却定型后可保持模具型腔所赋予的形状,然后开模分型获得成形塑件。这样就完成了一次注射工作循环,如图8-6所示。注射成形是在专门的注射机上进行,图8-7所示为螺杆式注射机结构示意图。 第二节 塑料成形工艺
纳米注塑成型技术介绍
技术掌握难度高
该技术需要较高的技术 水平和经验,对操作人
员的技能要求较高。
材料选择受限
某些特殊材料在纳米注塑成 型过程中可能会出现流动不
均、填充困难等问题。
环境保护问题
在生产过程中可能产生 废料和有害物质,需要 采取相应的环保措施。
解决方案与应对策略
加强研发与培训
通过研发和技术培训,提高操作人员的技能 水平,降低技术掌握难度。
医疗领域
用于制造医疗器械和植入物等, 如人工关节、牙套等,提高产品
的生物相容性和机械性能。
Байду номын сангаас
02 纳米注塑成型技术发展历 程
起源与早期发展
起源
纳米注塑成型技术起源于20世纪90 年代,当时主要受到纳米材料和精密 注射成型技术的启发。
早期发展
在初期阶段,该技术主要关注于将纳 米粒子添加到传统塑料中以提高其性 能。
医疗器械制造
制造高精度、高性能的医 疗器械零部件,如人工关 节、牙科植入物等。
对环境和社会的影响
资源节约
纳米注塑成型技术能够实 现材料的高效利用,减少 浪费,有助于节约资源。
减少环境污染
通过优化注塑工艺,降低 废品率,减少废料对环境 的污染。
提高生产效率
纳米注塑成型技术能够提 高生产效率,降低生产成 本,有助于推动产业的发 展和进步。
THANKS FOR WATCHING
感谢您的观看
智能化控制技术
利用人工智能和机器学习技术,实 现注塑过程的智能控制和优化,提 高产品质量和生产效率。
产业应用前景
01
02
03
汽车制造业
利用纳米注塑成型技术制 造汽车零部件,提高零部 件性能、减轻重量、降低 成本。
新型注射成型技术及特点
Ke y Wo r d s
p o l y m e r , i n j e c t i o n , m o l d i n g , t e c h n o l o g y , f e a t u r e
高 分 子 材 料 的 主要 成 型方 法 有 挤 出 、 注射 、 吹
1 . 动 态 注射成 型
Wi t h he t d e v e l o p m e n t o f i n d u s t r y r e q u i r e m e n t , s o m e n o v e l i n j e c t i o n m o l d i n g t e c h n o l o g i e s w e r e a p p l i e d . I n
余 应力 , 使 制 品 的机 械 性 能显 著 提 高 。该 技 术 不 仅
此, 出现 了动态注射成型、 气辅成型、 水辅成型 、 超临 界流体注塑 、 注射压缩成型法、 模具滑合成型法 、 快 速热循环注塑成型等一批新型成型方法。下面就针
对这 些新 型成 型 方法作 一个 简介 。
收 稿 日期 : 2 0 1 2—1 2—0 3
作者简介 : 孟兵 ( 1 9 7 4 一
・
) , 男, 四川 邛崃人 , 博 士, 讲师 , 从事高分材料及成型 , 模具设计 , 模具 C A D / C A E等研究。
42 ・
新型注射成型技术及特 点
塑、 压延等 , 其中注射成 型能一次成型外形复杂 、 尺 寸精确的塑料制品, 成 型过程 自动化程度高 , 并可以 生产和制造较为复杂的制品, 在高分子材料 的成型
中占有 极其 重 要 的位 置 。近 年来 , 高分 子 制 品 向高 度集成 化 、 高度精 密化、 高 产 量 和 低 成 本 等 方 面 发
塑料先进成型技术第7章 反应注射成型技术
早期应用:聚氨酯弹性体和聚氨酯泡沫塑料,用于大型 厚壁制品生产。
一、反应注射成型的原理及特点
增强反应注射成型(RRIM): 1979年出现,用玻璃纤 维增强的聚氨酯RIM生产工艺,可拓宽应用领域,提高制 品刚性与强度;用于汽车挡泥板和车体板的生产。
7)具有设备投资及生产成本低、制件外表美观,耐冲击 性好,设计灵活性大等优点,特别适用于汽车覆盖件等大 型塑件的成型加工。
二、反应注射成型工艺流程
工艺过程:包含原料准备—贮存—计量—混合—充模— 固化—顶出—后处理等工序。
(1)原料准备:配制成A(异氰酸酯)、B(多元醇)两 种组分,B组分常含扩链剂、催化剂及其它助剂。
一、反应注射成型的原理及特点
应用拓展:不再局限于聚氨酯体系,已广泛应用于不饱 和聚酯、环氧树脂等快速固化类树脂和触媒,以及尼龙、 聚脲及聚环戊二烯、有机硅树脂和互穿聚合物网络等多种 材料;将RIM工艺用于橡胶与金属成型已成为高分子材料 加工领域的研究热点。
我国上世纪80年代初已引进RIM设备和原料,生产汽车 方向盘、聚氨酯泡沫塑料,但目前仍主要用于聚氨酯材料, 对其它种类材料的研究特别是工业应用还不广泛,RIM技 术普及更是任重道远。
一、反应注射成型的原理及特点
RIM与其它塑料成型技术比较,具有以下特点: 1)RIM是能耗最低的工艺之一。因液态原料所需注射压
力和锁模力仅为普通注射成型的1/100~1/40,耗能少。 2)RIM模腔压力小,约为0.3~1.0MPa,设备和模具所需
的投资少。
3)RIM所用体系多种多样,如聚氨酯、聚脲、尼龙、双 环戊二烯等。
高分子材料的加工成型技术
高分子材料的加工成型技术摘要:在现代社会发展潮流中,高分子材料的成型加工技术受到了社会各界人士的高度关注,且应用范围也在不断的扩展延伸。
鉴于此,深入分析高分子材料的加工成型技术以及应用,可以帮助我国研究成员更好的探究该领域的内容,促使高分子材料成型加工技术与各行业进行充分融合。
关键词:高分子材料;加工成型;技术应用引言随着聚合物在很多重要行业中的应用越来越广泛,在保证其经济性的基础上,我们应该加强聚合物成形工艺的研发,以确保其在生产成本和时间上的良好应用,促进国家的繁荣。
1.高分子材料的概述1.1高分子材料的分类高分子材料有很多种,橡胶,塑料,纤维,粘合剂,涂料等都在这一范畴之中,该种材料在很多领域都有很大的用途。
高分子又称为聚合物质,通过多次使用共价键联,将不计其数的简单相同的结构单位反复组合而形成。
目前,关于聚合物的种类有很多种,根据原料的种类划分,可以将其划分为自然物质和人造物质。
根据物料性质可分为橡胶、纤维、塑料、粘合剂、涂料等;根据用途的不同,可以将其划分为:普通高分子材料、特种高分子材料、功能性高分子材料。
当前,聚合物在建筑、交通、家电、工农业、航空等领域得到了越来越多的应用,并逐渐朝着功能化、智能化、精细化方向发展。
而国内在此领域的发展和科研工作起步较迟,亟需加强技术创新,加强技术人员培训,使聚合物成形工艺水平持续提升,才能走在国际前沿。
1.2高分子材料的成型性能在不同的物理条件下,聚合物的特性差异很大,所以在对聚合物的成形特性进行分析时,必须对聚合物的溶质特性有一定的认识。
已有的实验结果显示,非晶体聚合物的主要形态有玻璃态、高弹态、粘性态三种形态,但多数晶体物质仅有两种形态,即晶态和粘性态。
玻璃态、高弹态和晶体态是物料成形后所采用的形态,而粘流态则是物料在处理时所表现出的形态,不过,也有一些聚合物在高弹状态下完成处理加工作业。
聚合物的制造工艺一般是将聚合物材料制成熔化,放入模具和流动通道中,再经过降温再进行定型,从而使聚合物具有良好的流变性。
- 1、下载文档前请自行甄别文档内容的完整性,平台不提供额外的编辑、内容补充、找答案等附加服务。
- 2、"仅部分预览"的文档,不可在线预览部分如存在完整性等问题,可反馈申请退款(可完整预览的文档不适用该条件!)。
- 3、如文档侵犯您的权益,请联系客服反馈,我们会尽快为您处理(人工客服工作时间:9:00-18:30)。
国外高分子材料新型注射成型技术
发布时间:2004-3-21 14:51:09 浏览数:5引言
在21世纪已经到来的今天,高分子材料已经成为支持人类文明社会发展的科学进步的重要物质基础。
众所周知,高分子材料技术是以合成技术、改性技术、形体设计技术、成型加工技术、应用技术和回收再利用技术为基础的综合技术,但由于高分子材料是为了制造各种制品而存在的,因此从应用的角度来讲,以对其进行形状赋予为主要目的的成型加工技术有着重要的意义。
高分子材料的主要成型方法有挤出成型、注射成型、吹塑成型、压延成型、压制成型等等,其中注射成型因可以生产和制造形状较为复杂的制品,在高分子材料的成型加工方法中一直占有极其重要的位置。
本文主要参考近年来发表的日本有关成型加工方面的文献,着眼于高分子材料注射成型技术的最新发展动向,概要地介绍若干种用途较为广泛的注射成型新技术的原理。
气体辅助成型法(GAM,Cas Assist Molding)
GAM法的要点是在树脂充填(不完全充填)完成后,利用型腔内树脂冷却前的时间差,将具有一定压力的惰性气体迅速地注入成型品内部,此时气体可在成品壁较厚的部分形成空腔,这样即能使成品壁厚变得均匀,防止产生表面缩痕或收缩翘曲,使制品表面平整光滑。
GAM法近年来发展较快,国外很多公司为了进行专利回避,相继开发了具有不同特征的新方法,如日本旭化成公司的AGI法(Asahi Gas Iniection)、三菱工程塑料公司的CINPRES法(Controlled Internal Pressure)及出光石油化学公司的GIM法(Gas Injection Molding)等等,但各方法原理完全相同,如AGI法是将惰性气体(一般为N2)喷嘴设在注射机料口喷嘴内部,而CINPRES法是将惰性气体喷嘴设置在模具上,且可以是1个也可以是几个。
注射压缩成型法(IPM,Injection Press Molding)
IPM法技术由日本三菱重工业、名古屋机械制作所、出光石油化学等公司相继开发成功。
有整体压缩法和部分压缩法之分。
整体压缩法成型是首先在保持模具一定开度的状态下合模,将树脂充填(不完全充填)进去,而后利用油缸压缩使模具的动模移动至完全合模的情况下充填树脂(不完全充填),压缩不是靠整个动模移动,而是靠动模板上制品赋形面部分(可以是全体也可以是一部分)的移动而实现的。
注射压缩成型法的优点是可以采用较低的注射压力成型薄形制品或需较大成型压力的制品,一般适用流动性较差且薄壁的制品,如高分子量PC或纤维填充工程塑料等。
模具滑合成型法(DSI,Die SlideInection)
DSI法由日本制钢所开发.有DSI-2M法和M—DSI法之分,DSI-2M法主要用于中空制品制造,而M-DSI主要用于不同树脂的复合体制造,其原理完全相同。
如使用DSI-2M 法时,首先将中空制品一分为二,两部分分别注射,然后将两部分阴模(半成品仍在模具中)滑移至对合位置,在制品两部分结合缝再注人树脂(2次注射),最后得到完整的中空成型制品。
和吹塑品相比,该法制品具有表面精度好、尺寸精度高、壁厚均匀且设计自由度高(如L型)等优点。
在制造形状复杂的中空制品时,DSI和传统的二次熔接法(如超声波熔接)相比,其优点是:a不需要将半成品从模具中取出,因而可以避免半成品在模具外冷却引起的制品形状精度下降问题;b可以避免二次熔接法因产生局部应力而引起的熔接强度降低问题。
但为了提高制品的熔接强度,DSI法也应根据制品的要求,采取不同的接合形状。
如凹口对接:适用于对接合强度要求不高,但对外观形状要求较高的制品;嵌入对接:适用于即对接合强度要求较高,又对外观形状要求较高的制品;交织对接:适用对熔接性较差的塑料制品;封合对接:适用于即要求接合强度较高,又要求密封性较高的制品,如制造压力容器时一般需采用该方法。
此外,日本制钢所还开发其他12种接合形状,并对其适用性进行了较为详细的评价。
可见在DSI法中接合形状的设计是至关重要的。
剪切场控制取向成型法(SCORIM,Shear Controllcd Orientation Injection Molding)
SCORIM技术由英国Brunell大学开发,通常用于玻纤或碳纤维将不可避免地在垂直于流动方向上取向(和熔接痕方向平行),最终造成制品强度的降低。
它在模具上开设两个主流道,从注射喷嘴射出的熔融树脂将分别沿这两个主流道充满型腔,同时利用SCORIM装置将两个液压油缸的活塞分别设于主流道上,当熔融树脂充满型腔后,两活塞将一进一退反复振荡,此时熔接痕部位的玻纤或碳纤维将被迫沿着剪切力场方向取向,该技术不仅可提高熔接痕中度,也可消除制品内部的缩孔或表面的缩痕。
由于纤维增强是制备高强度制品的重要方法,因此有关利用剪切场控制纤维取向的注射成型新技术较多,除SCORIM法外,较典型的有:由德国Klockner Ferromatik Desma公司开发的推拉法(Push-Pull),该法和SCORIM法原理相同,主要区别是用两个注射机螺杆代替活塞进行反复振荡;日本宝理公司开发的层间正交法(Cross Layer Moldint)是在浇口垂直方向上设置两个加压杆或加压板,使制品芯部处于熔融状态的树脂再次取向,最终使处于制品表面层的纤维和处于芯层的纤维方向垂直,可以减少纤维增强制品力学性能下的各向异性。
硬化PC薄片表面镶嵌成型法(CFI Coated Film Insert Injection)
CFI法由三菱工程塑料公司开发,主要利用表面硬化或硬化并彩印的PC薄片进行表面镶嵌成型。
其概要是行将冲切好的PC薄片装在模具上,然后合模并在所定的条件下注射成型,既可以得到单面镶嵌,也可以得到双面镶嵌硬化PC薄片的制品。
该方法克服了对制品进行表面硬化处理难度大、效率低的缺点,可以先在平面状的PC薄片上进行涂装和硬化处理,再将其按所需形状冲切后镶八模具,而后靠注射树脂的压力和温度得到曲面状的制品,
适用于汽车或各种家电、OA(电脑办公用品)制品的铭板等。
采用CFI法时,中间的树脂层可以使用PC,也可以使用PS、AS、MS、PMMA等透明材料或ABS等不透明材料。
为了使PC薄片和中间树脂层之间有较好接合强度,一般要在接合面上事先涂有特殊的粘合层;为了使PC薄片表面上的硬化层不因过度弯曲或因热的作用而产生龟裂,制品的曲率半径应小于30mm,且模具温度应保持在70℃以下;为了使PC 薄片形成所要求的曲面形状,并使其和中间树脂层之间有较好的接合强度,中间层树脂的注射成型温度一般应高于290℃;为了使PC薄片不在流动树脂的剪切力作用下产生位移,应采取如真空吸合、打孔、磁吸(在PC薄片边缘贴上磁片)、或将PV薄片弯曲后人模具上设定的沟槽内等方法,使其固定在相应的位置上。
三菱工程塑料公司还开发了彩印PC薄片表面镶嵌成型法(PSI,Printed Sheet Insert Injection),PSI法中采用彩印的PC薄片,其成型原理和CFI法基本相同。
该方法所得制品的表面(可以是外表面也可以是内表面)为印刷面,而注射树脂一般采用透明材料以保证制品的透光性。
适用于需要有背光透出的汽车仪表或各种家电、OA制品的面板等。
直接注射成型法(DIM,Direct Injection Molding)
直接注射成型技术由日本岸本产业、KCK等公司开发成功,主要用于高浓度玻璃纤维、碳纤维或有机、无机粉体(如碳酸钙、木粉)等复合材料制品的注射成型。
在复合材料制备时,为了使填充剂均匀地分散在基体树脂中,传统的方法一般需将基体树脂和玻璃纤维等掺混并经双螺杆挤出机混炼造粒,这不仅造成较大的能量耗损,也带来如基体树脂的降解、氧化变色、玻璃纤维因过度剪切而切断等问题。
而直接注射成型法不经挤出机混炼造粒,可以将掺混物直接注射成制品,但由于注射网为单螺杆装置,且其长径比一般挤出机小,因此对直接注射成型技术而言,最关键的是如何提高螺杆的混炼效率。
直接注射成型技术通常是通过改变压缩段的螺杆构造来提高混炼效率的,该装置中不仅螺杆形状和密炼机转子相似,而且在料筒壁上开设了相瓦错开的沟槽,工作时其狭缝S部分可产生较大的剪切力,有利于树脂塑化和无机填充剂的分散,沟槽P部分可使溶融混合物反复实现混合-剪切-再混合的过程,有利于复合材料达到均质化的要求。
该装置只能用于复合材料的成型而不能用于纯树脂的成型,这是因为用于纯树脂成型时,狭缝S可产生较多的逆流使螺杆的输送效率降低,而用于复合材料成时,大量的无机填充剂所产生的增粘作用可抑制逆流的发化,此时装置才能同时具有混炼和输送功能。