鲁奇加压气化炉
鲁奇加压气化炉

2、 技术特点
采用碎煤加压式填料方式,即连接在炉体上部的煤锁将原料制成常温碎煤块,然后从进煤口经过气化炉的预热层,将温度提高至300℃左右。从气化剂入口吹进的助燃气体将煤点燃,形成燃烧层。燃烧层上方是反应层,产生的粗煤气从出口排出。炉篦上方的灰渣从底部出口排到下方连接的灰锁设备中,所以气化炉与煤锁﹑灰锁构成了一体的气化装置。
3、 典型代表产品
鲁奇炉的代表炉型即第三代MARK-IV/4型Ф3800mm加压气化炉, 炉体由内外壳组成,其间形成50mm的环形水冷夹套,是一种技术先进﹑结构更为合理的炉型。我公司为河南义马、大唐克旗等制做了多台鲁奇式气化炉。
煤气化技术是清洁利用煤炭资源的重要途径和手段。目前,国内自行开发和引进的煤气化技术种类很多,但总体上可以分为以下三大类:
鲁奇加压气化炉是由联邦德国鲁奇公司于1930年开发的,属第一代煤气化工艺,技术成熟可靠,是目前世界上建厂最多的煤气化技术。鲁奇气化炉是制取城市坑口煤气装置中的心脏设备。它适应的煤种广﹑气化强度大﹑气化效率高﹑粗煤气无需再加压即可远距离输送。
1999年 ,哈锅为河南义马制造了国内首台φ3800鲁奇技术加压气化炉。义马气化炉是国家“九五”重大技术装备科研攻关项目,该气化炉于2001年2月获科学技术部、财政部、国家计委、国家计贸委颁发的“九五”国家重点科技攻关计划优秀科技成果奖,2002年获中国机械工业科学技术三等奖。
一、移动床气化技术
以鲁奇为代表的加压块煤气化技术。鲁奇加压气化技术是由联邦德国鲁奇公司于1930年开发的,属第一代煤气化技术,技术成熟可靠,曾是世界上建厂最多的煤气化技术。鲁奇气化技术是制取城市煤气和合成气装置中的心脏设备。它适应的煤种广﹑气化强度较大﹑气化效率高。鲁奇气化技术的特点为:采用碎煤加压式供料方式,即连接在炉体上部的煤锁将煤块升压,加入气化炉的预热层,然后,下移至反应层,煤在反应层气化,反应热量取自于气化剂与燃烧形成的燃烧层。产生的粗煤气从出口排出。炉篦上方的灰渣从底部出口排到下方连接的灰锁中,所以气化炉与煤锁﹑灰锁构成了一体的气化装置。鲁奇炉的代表炉型即第三代MARK-IV型Ф3800mm加压气化炉, 炉体由内外壳组成,其间形成50mm的环形水冷夹套,用作保护炉的过热和产生蒸汽,结构更为合理的炉型。鲁奇公司为河南义马、大唐克旗等制做了多台鲁奇式气化炉。
鲁奇加压气化炉的运行与技术改造探讨
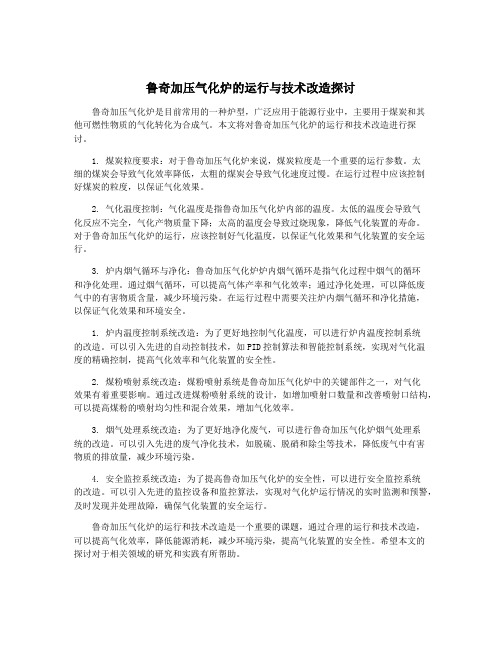
鲁奇加压气化炉的运行与技术改造探讨鲁奇加压气化炉是目前常用的一种炉型,广泛应用于能源行业中,主要用于煤炭和其他可燃性物质的气化转化为合成气。
本文将对鲁奇加压气化炉的运行和技术改造进行探讨。
1. 煤炭粒度要求:对于鲁奇加压气化炉来说,煤炭粒度是一个重要的运行参数。
太细的煤炭会导致气化效率降低,太粗的煤炭会导致气化速度过慢。
在运行过程中应该控制好煤炭的粒度,以保证气化效果。
2. 气化温度控制:气化温度是指鲁奇加压气化炉内部的温度。
太低的温度会导致气化反应不完全,气化产物质量下降;太高的温度会导致过烧现象,降低气化装置的寿命。
对于鲁奇加压气化炉的运行,应该控制好气化温度,以保证气化效果和气化装置的安全运行。
3. 炉内烟气循环与净化:鲁奇加压气化炉炉内烟气循环是指气化过程中烟气的循环和净化处理。
通过烟气循环,可以提高气体产率和气化效率;通过净化处理,可以降低废气中的有害物质含量,减少环境污染。
在运行过程中需要关注炉内烟气循环和净化措施,以保证气化效果和环境安全。
1. 炉内温度控制系统改造:为了更好地控制气化温度,可以进行炉内温度控制系统的改造。
可以引入先进的自动控制技术,如PID控制算法和智能控制系统,实现对气化温度的精确控制,提高气化效率和气化装置的安全性。
2. 煤粉喷射系统改造:煤粉喷射系统是鲁奇加压气化炉中的关键部件之一,对气化效果有着重要影响。
通过改进煤粉喷射系统的设计,如增加喷射口数量和改善喷射口结构,可以提高煤粉的喷射均匀性和混合效果,增加气化效率。
3. 烟气处理系统改造:为了更好地净化废气,可以进行鲁奇加压气化炉烟气处理系统的改造。
可以引入先进的废气净化技术,如脱硫、脱硝和除尘等技术,降低废气中有害物质的排放量,减少环境污染。
4. 安全监控系统改造:为了提高鲁奇加压气化炉的安全性,可以进行安全监控系统的改造。
可以引入先进的监控设备和监控算法,实现对气化炉运行情况的实时监测和预警,及时发现并处理故障,确保气化装置的安全运行。
鲁奇加压气化炉工艺操作

鲁奇加压气化炉工艺操作新疆广汇新能源造气车间--程新院一、相关知识1、影响化学平衡的因素有三点:①反应温度(T)、②反应压力(P)、③反应浓度(C)。
勒夏特列原理:如果改变影响化学平衡条件之一(T、P、C),平衡将向着能够减弱这种改变的方向移动。
2、气化炉内氧化层主反应方程式① 2C+O₂=CO₂(-Q)ΔH<0②2C+O₂=2CO(-Q)ΔH₂<0ΔH<ΔH₂3、气化炉内还原层主反应方程式③C+CO₂=2CO(+Q)ΔH₃>0④C+H₂O=CO+H₂(+Q)ΔH₄>0⑤C+2H₂=CH₄(+Q)ΔH5>0ΔH₃>ΔH₄>ΔH5|ΔH|>ΔH₃>|ΔH₂|>ΔH₄>ΔH₄4、煤灰熔点对气化炉的影响鲁奇气化炉的操作温度介于煤的DT(变形温度)和ST(软化温度)之间。
若入炉煤的灰熔点高,则操作时适当降低汽氧比,相应提高炉温,蒸汽分解率增加,煤气水产量低,气化反应完全,有利于产气。
但是受气化炉设计材料的制约,汽氧比不能无限制降低,否则可能会烧坏炉篦及内件。
因此受设备材质的局限,煤灰熔点不能太高,一般控制在1150℃≦DT≦1250℃。
反之,若煤灰熔点低,则操作时要适当提高汽氧比,相应降低炉温(防止炉内结渣,造成排灰困难),蒸汽分解率降低,煤气水产量增加,气化反应速度减缓,不利于产气。
因此入炉煤的灰熔点要尽可能在一定的范围内,不能变化太大。
二、汽氧比的判断鲁奇加压气化炉汽氧比是调整控制气化过程温度,改变煤气组份,影响副产品产量及质量的重要因素。
汽氧比过低,会造成气化炉结渣,排灰困难,不利于产气;汽氧比过高,会造成灰细或排灰困难,煤气水产量增加等。
因此,在不引起灰份熔融的情况下,尽可能采用低的汽氧比。
汽氧比的高低应该结合煤气组份中有效气体的含量、灰样和指标参数做出准确的判断!1、从煤气组份¹判断汽氧比的高低我们在实际操作中一般都根据CO2、CO、H2、CH₄来判断汽氧比的高低,下面分情况进行说明。
鲁奇加压气化炉的运行与技术改造探讨

鲁奇加压气化炉的运行与技术改造探讨鲁奇加压气化炉是一种用于生产工业原料和能源的设备,它可以将固体燃料,如煤、木材等,通过加压气化的方式转化为可燃气体,从而实现能源的高效利用。
随着能源需求的不断增加和环境保护意识的提高,对加压气化炉的运行和技术改造的探讨变得愈发重要。
本文将从加压气化炉的基本原理、运行情况以及技术改造方面展开讨论。
一、加压气化炉的基本原理鲁奇加压气化炉是一种通过给固体燃料施加高压,使其在高温下与氧气发生气化反应的设备。
其基本原理是将固体燃料加热至一定温度后,通过给予一定的高压使其与氧气发生气化反应,生成可燃气体和灰渣。
这种气化反应产生的可燃气体可以作为燃料供给燃烧设备,从而实现能源的利用。
二、加压气化炉的运行情况1. 原料选择:加压气化炉可以使用各种固体燃料,包括煤、木材、秸秆等。
在实际运行中,不同的原料会对气化反应的速度和产物的成分产生影响,因此在选择原料时需要进行综合考虑。
2. 气化反应:气化反应是加压气化炉的核心部分,其速度和效果对设备的运行效率和产物的质量有重要影响。
在实际操作中,需要控制气化反应的温度、压力和气体流速等参数,以保证气化反应的稳定和高效进行。
3. 清灰处理:加压气化炉在运行过程中会产生大量的灰渣,这些灰渣会对设备的正常运行产生影响。
需要定期进行清灰处理,确保设备的正常运行。
4. 安全管理:加压气化炉是一种高温高压设备,其运行安全至关重要。
在运行中需要加强对设备的监控和维护,确保设备的安全运行。
三、加压气化炉的技术改造随着科技的进步和能源需求的变化,对加压气化炉的技术改造变得愈发重要。
以下是一些可能的技术改造方向:1. 节能改造:通过提高设备的热效率和气化反应的效率,减少能源的消耗,从而实现节能降耗。
2. 环保改造:通过改进气化反应的参数控制和气体净化系统,降低气化过程中产生的有害气体排放,实现环保目标。
3. 自动化改造:通过引入自动控制系统,提高设备的稳定性和可靠性,减少人为操作的误差,提高生产效率。
鲁奇加压气化炉
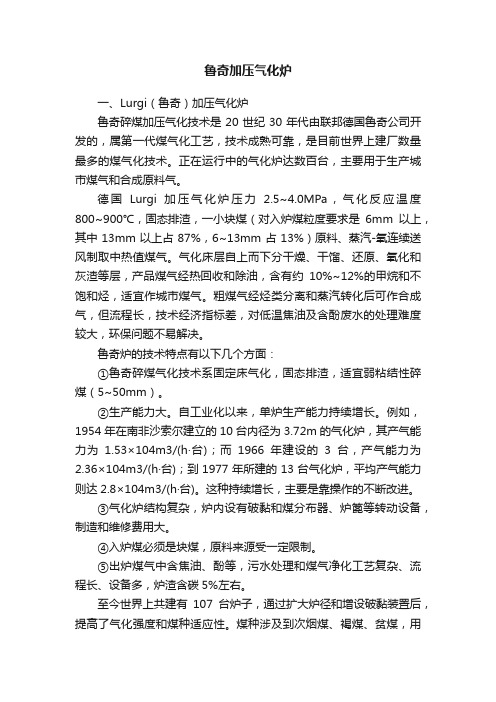
鲁奇加压气化炉一、Lurgi(鲁奇)加压气化炉鲁奇碎煤加压气化技术是20世纪30年代由联邦德国鲁奇公司开发的,属第一代煤气化工艺,技术成熟可靠,是目前世界上建厂数量最多的煤气化技术。
正在运行中的气化炉达数百台,主要用于生产城市煤气和合成原料气。
德国Lurgi加压气化炉压力 2.5~4.0MPa,气化反应温度800~900℃,固态排渣,一小块煤(对入炉煤粒度要求是6mm以上,其中13mm以上占87%,6~13mm占13%)原料、蒸汽-氧连续送风制取中热值煤气。
气化床层自上而下分干燥、干馏、还原、氧化和灰渣等层,产品煤气经热回收和除油,含有约10%~12%的甲烷和不饱和烃,适宜作城市煤气。
粗煤气经烃类分离和蒸汽转化后可作合成气,但流程长,技术经济指标差,对低温焦油及含酚废水的处理难度较大,环保问题不易解决。
鲁奇炉的技术特点有以下几个方面:①鲁奇碎煤气化技术系固定床气化,固态排渣,适宜弱粘结性碎煤(5~50mm)。
②生产能力大。
自工业化以来,单炉生产能力持续增长。
例如,1954年在南非沙索尔建立的10台内径为3.72m的气化炉,其产气能力为1.53×104m3/(h·台);而1966年建设的3台,产气能力为2.36×104m3/(h·台);到1977年所建的13台气化炉,平均产气能力则达2.8×104m3/(h·台)。
这种持续增长,主要是靠操作的不断改进。
③气化炉结构复杂,炉内设有破黏和煤分布器、炉篦等转动设备,制造和维修费用大。
④入炉煤必须是块煤,原料来源受一定限制。
⑤出炉煤气中含焦油、酚等,污水处理和煤气净化工艺复杂、流程长、设备多,炉渣含碳5%左右。
至今世界上共建有107台炉子,通过扩大炉径和增设破黏装置后,提高了气化强度和煤种适应性。
煤种涉及到次烟煤、褐煤、贫煤,用途为F-T合成、天然气、城市煤气、合成氨,气化能力8000~100000m3/h,气化内径最大 5.0m,装置总规模1100~11600t/d。
鲁奇炉工作原理
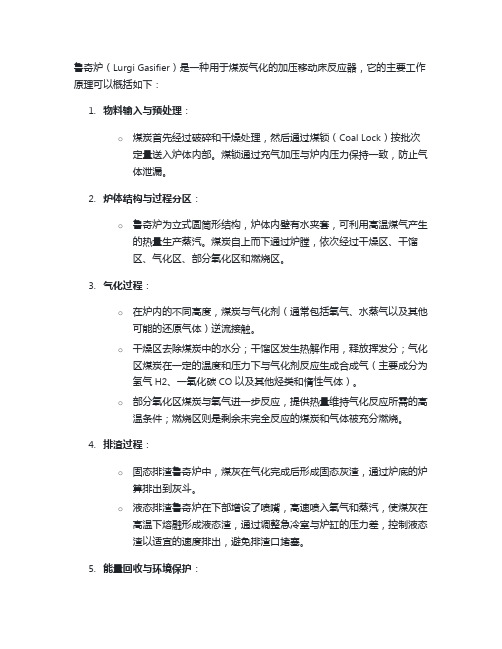
鲁奇炉(Lurgi Gasifier)是一种用于煤炭气化的加压移动床反应器,它的主要工作原理可以概括如下:1.物料输入与预处理:o煤炭首先经过破碎和干燥处理,然后通过煤锁(Coal Lock)按批次定量送入炉体内部。
煤锁通过充气加压与炉内压力保持一致,防止气体泄漏。
2.炉体结构与过程分区:o鲁奇炉为立式圆筒形结构,炉体内壁有水夹套,可利用高温煤气产生的热量生产蒸汽。
煤炭自上而下通过炉膛,依次经过干燥区、干馏区、气化区、部分氧化区和燃烧区。
3.气化过程:o在炉内的不同高度,煤炭与气化剂(通常包括氧气、水蒸气以及其他可能的还原气体)逆流接触。
o干燥区去除煤炭中的水分;干馏区发生热解作用,释放挥发分;气化区煤炭在一定的温度和压力下与气化剂反应生成合成气(主要成分为氢气H2、一氧化碳CO以及其他烃类和惰性气体)。
o部分氧化区煤炭与氧气进一步反应,提供热量维持气化反应所需的高温条件;燃烧区则是剩余未完全反应的煤炭和气体被充分燃烧。
4.排渣过程:o固态排渣鲁奇炉中,煤灰在气化完成后形成固态灰渣,通过炉底的炉箅排出到灰斗。
o液态排渣鲁奇炉在下部增设了喷嘴,高速喷入氧气和蒸汽,使煤灰在高温下熔融形成液态渣,通过调整急冷室与炉缸的压力差,控制液态渣以适宜的速度排出,避免排渣口堵塞。
5.能量回收与环境保护:o鲁奇炉的设计考虑了能源的高效利用和环保要求,炉壁夹套产生的蒸汽可用于发电或者作为工艺蒸汽循环使用。
o产生的煤气经过冷却、净化处理,分离出的产品包括清洁煤气、硫磺等,同时对废水和废气进行处理,以达到环保排放标准。
总的来说,鲁奇炉通过一系列复杂的化学反应将固体煤炭转化为便于运输和使用的合成气,实现了煤炭资源的有效转化和利用,同时也是洁净煤技术的重要组成部分,在煤化工产业中具有重要地位。
鲁奇加压气化炉

鲁奇加压气化炉1、第三代鲁奇加压气化炉第三代加压气化炉为例,该炉子的内径为3.8m,最大外径为4.128m,高为12.5m,工艺操作压力为3MPa。
主要部分有炉体、夹套、布煤器和搅拌器、炉算、灰锁和煤锁等,现分述如下。
①炉体加压鲁奇炉的炉体由双层钢板制成,外壁按3.6MPa的压力设计,内壁仅能承受比气化炉内高O.25MPa的压力。
两个简体(水夹套)之间装软化水借以吸收炉膛所散失的一些热量产生工艺蒸汽,蒸汽经过液滴分离器分离液滴后送入气化剂系统,配成蒸汽/氧气混合物喷入气化炉内一水夹套内软化水的压力3MPa,这样筒内外两两侧的压力相同,因而受力小。
夹套内的给水由夹套水循环泵进行强制循环。
同时夹套给水流过煤分布器和搅拌器内的通道,以防止这些部件超温损坏。
第三代鲁奇炉取消了早期鲁奇炉的内衬砖.燃料直接与水夹套内壁相接触,避免了在较高温度下衬砖壁挂渣现象,造成煤层下移困难等异常现象,另一方面,取消衬砖后,炉膛截面可以增大5%~10%左右,生产能力相应提高。
②布煤器和搅拌器如果气化黏结性较强的煤,可以加设搅拌器。
布煤器和搅拌嚣安装在同一转轴上,速度为15r/h左右。
从煤箱降下的煤通过转动布煤器上的两个扇形孔,均匀下落在炉内,平均每转可以在炉内加煤150~200mm厚。
搅拌器是一个壳体结构,由锥体和双桨叶组成,壳体内通软化水循环冷却。
搅拌器深入到煤层里的位置与煤的结焦性有关,煤一般在400~500℃结焦,桨叶要深入煤层约l.3m。
③炉算炉箅分四层,相互叠合固定在底座上,顶盖呈锥体。
材质选用耐热的铬钢铸造,并在其表面加焊灰筋。
炉箅上安装刮刀,刮刀的数量取决于下灰量。
灰分低,装1~2把;对于灰分较高的煤可装3~4把。
炉箅各层上开有气孔,气化剂由此进入煤层中均匀分布。
各层开孔数不太一样,例如某厂使用的炉算开孔数从上至下为:第一层6个、第二层16个、第三层16个、第四层28个。
炉箅的转动采用液压传动装置,也有用电动机传动机构来驱动,液压传动机构有调速方便、结构简单、工作平稳等优点。
鲁奇炉介绍及附属设备简介

气化炉内外壳生产期间温度不同,热膨胀量不同, 为降低温度差应力,在内套下部设计制造了波形膨胀节 如图13所示,用于吸收热膨胀量。正常生产期间,波形 膨胀节不但可吸收大约25-35mm的内壳热膨胀量,而且在 此还可以起到支撑灰渣的作用,这样可使灰渣在刮刀的 作用下均匀地排到灰锁中去。
2. 鲁奇第二代加压气化炉
在综合了第一 ④取消了衬砖, ①在炉内部设臵了传动 代气化炉的运行情 提高了气化炉的 的搅拌装臵和布煤器, ③入炉气 况后,鲁奇公司于 生产能力,也避 搅拌装臵有两个搅拌桨 免了由于在内衬 20化剂管与 世纪50年代推出 叶,其高度在炉内的干 ⑤灰锁设臵在炉底 传动轴分 上挂渣给生产操 了 φ2.6m,中间除 馏层,随着叶片的转动, 正中位臵,气化后 开,单独 作带来的不利影 灰的第二代气化炉, 在干馏层的煤焦受到了 产生的灰渣从炉篦 固定在炉 响; ②炉篦由单层平型改为 底侧壁上; 如图 8所示。 搅动,破坏了煤的黏结, 的周边环隙落下落 多层塔节型结构,气化
德士古气化炉(结构见图3)属于 湿法进料气流床的一种,最早引进该技 术的是山东鲁南化肥厂,1993年投产。 目前,我国已有山东鲁南、上海焦化、 )装臵投运,有些已 具有10多年运行经验,到目前为止运行 基本良好,显示了水煤浆气化技术的先 进性。但是,德士古气化炉对煤质限制 比较严格,成浆性差和灰分较高,还存 在耐火砖成本高、寿命短和煤浆泵磨损 大、维修成本高等问题。
气流床:粉煤与气化剂( O2 、水蒸 气)一起从喷嘴高速吹入炉内,快速 气化。特点是不副产焦油,生成气中 甲烷含量少。主要以德士古气化炉和 壳牌气化炉为代表;
二、3种先进的煤气化工艺
我国引进并被广泛采用的三种先进煤气化
工艺分别是:壳牌气化炉、德士古气化炉、鲁 奇气化炉。
- 1、下载文档前请自行甄别文档内容的完整性,平台不提供额外的编辑、内容补充、找答案等附加服务。
- 2、"仅部分预览"的文档,不可在线预览部分如存在完整性等问题,可反馈申请退款(可完整预览的文档不适用该条件!)。
- 3、如文档侵犯您的权益,请联系客服反馈,我们会尽快为您处理(人工客服工作时间:9:00-18:30)。
一、Lurgi(鲁奇)加压气化炉
鲁奇碎煤加压气化技术是20世纪30年代由联邦德国鲁奇公司开发的,属第一代煤气化工艺,技术成熟可靠,是目前世界上建厂数量最多的煤气化技术。
正在运行中的气化炉达数百台,主要用于生产城市煤气和合成原料气。
德国Lurgi加压气化炉压力2.5~4.0MPa,气化反应温度800~900℃,固态排渣,一小块煤(对入炉煤粒度要求是6mm以上,其中13mm以上占87%,6~13mm占13%)原料、蒸汽-氧连续送风制取中热值煤气。
气化床层自上而下分干燥、干馏、还原、氧化和灰渣等层,产品煤气经热回收和除油,含有约10%~12%的甲烷和不饱和烃,适宜作城市煤气。
粗煤气经烃类分离和蒸汽转化后可作合成气,但流程长,技术经济指标差,对低温焦油及含酚废水的处理难度较大,环保问题不易解决。
鲁奇炉的技术特点有以下几个方面:
①鲁奇碎煤气化技术系固定床气化,固态排渣,适宜弱粘结性碎煤(5~50mm)。
②生产能力大。
自工业化以来,单炉生产能力持续增长。
例如,1954年在南非沙索尔建立的10台内径为3.72m的气化炉,其产气能力为1.53×104m3/(h·台);而1966年建设的3台,产气能力为2.36×104m3/(h·台);到1977年所建的13台气化炉,平均产气能力则达2.8×104m3/(h·台)。
这种持续增长,主要是靠操作的不断改进。
③气化炉结构复杂,炉内设有破黏和煤分布器、炉篦等转动设备,制造和维修费用大。
④入炉煤必须是块煤,原料来源受一定限制。
⑤出炉煤气中含焦油、酚等,污水处理和煤气净化工艺复杂、流程长、设备多,炉渣含碳5%左右。
至今世界上共建有107台炉子,通过扩大炉径和增设破黏装置后,提高了气化强度和煤种适应性。
煤种涉及到次烟煤、褐煤、贫煤,用途为F-T合成、天然气、城市煤气、合成氨,气化能力8000~100000m3/h,气化内径最大5.0m,装置总规模1100~11600t/d。
与UGI炉相比,Lurgi炉有效地解决了UGI炉单炉产气能力小的问题。
山西化肥厂单台气化炉最大生产能力达38000 m3/h(标)。
同时,由于在生产中使用了碎煤,
也使煤的利用率得到了相应提高。
但是,固定床炉的一些关键问题仍然没有能够得到解决。
Lurgi炉对煤种和煤质要求较高,只能使用弱黏结烟煤和褐煤,灰熔点(氧化气氛)大于1500℃.对强黏结性、热稳定性差、灰熔点低以及粉状煤则难以使用。
第三代Lurgi炉在炉内增设了搅拌器用于破焦,但也仅局限于黏结性较小的煤种。
Lurgi气化工艺的另一个问题是进料用灰锁上、下阀使用寿命仅为5~6个月,明显增加了运行成本。
究其原因,真正的问题存在于固定层气化工艺本身。
二、液态排渣鲁奇(BGL)炉
1984年鲁奇公司和英国煤气公司联合开发了BGL液态排渣鲁奇炉,将固体燃料全部气化生产燃料气和合成气。
BGL炉操作压力 2.5~3.0MPa,气化温度在1400~1600℃,超过了灰渣流动温度,灰渣呈液态形式排出。
炉结构比传统的Lurgi 炉简单,取消了转动炉篦。
与固体排渣法相比较,液态排渣加压气化法的主要特点是:
①气化强度高,生产能力大;
②水蒸气耗量低,水蒸气分解率提高;
③煤气中可燃组分增加,热值提高;
④煤种适应性强;
⑤碳转化率、气化效率和热效率均有提高;
⑥对环境污染减少。
液态排渣法固定床加压气化具有一系列优点,因而受到广泛重视。
但是由于高温、高压的操作条件,对于炉衬材料、熔渣池的结构和材质以及熔渣排出的有效控制都有待于不断改进。