鲁奇加压气化炉工艺操作
鲁奇加压气化炉的正常操作调整与故障处理
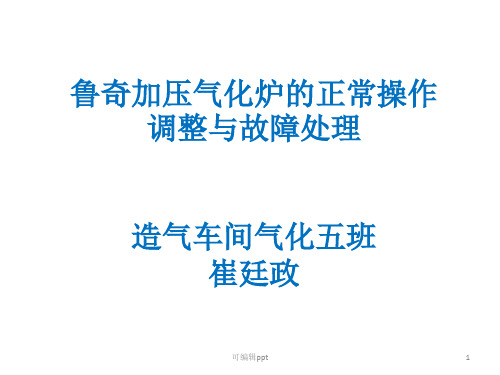
煤斗向煤锁加煤的阀门,以前为插板式,第三代炉以
后改为圆筒型,不论改为何种结构形式的煤溜槽阀,
其关闭后都与煤锁上阀之间有一定的空间,该空间用
于煤锁上阀开、关动作,以使上阀关严。所以操作中
要注意:在一个加煤循环中,煤溜槽阀只能打开一次,
以防止多次开关上阀动作空间充满煤后造成上阀的无
法关严,而影响气化炉的运行。
灰锁上、下阀的严密性实验压力必须按要求是压力进行,
即实验时上、下阀承受的压差ΔP为1.0MPa,这样可以及时 发现阀门泄露,及时处理,以延长上、下阀的使用寿命。
可编辑ppt
7
5、灰锁膨胀冷凝器的冲洗与充水
对于灰锁设有膨胀冷凝器的气化炉,其充水与冲洗 的正确操作很重要。灰锁泄压后,应按规定时间对 膨胀冷凝器底部进行冲洗,以防止灰尘堵塞灰锁泄 压中心管。冲洗完毕后应将膨胀冷凝器充水至满位 后,充水时应注意不能过满或过少,过满时水会溢 入灰锁造成灰湿、灰锁挂壁,影响灰锁容积;过少 则在灰锁泄压时很快蒸发,造成灰锁干泄,导致灰 尘堵塞泄压中心管,使灰锁泄压困难,所以必须正 确掌握冲洗与充水量,以保证灰锁的正常工作。
导致工况恶化若气化炉的负荷过等问题。根据经
验,气化炉负荷一般应控制在85%~120%,最低负荷
一般不得低于50%。
可编辑ppt
4
2、汽氧比的调整
汽氧比是气化炉正常操作的重要调整参数之一。调整汽氧比,
实际上是调整炉内火层的反应温度,气化炉出口煤气成分也随
① 当灰锁压力泄压至2.0MPa时停止泄压,检查上阀严密 性,查看灰锁压力是否回升。若在规定时间内(5s)压力回 升大于0.1MPa,则说明上阀泄露,应充压后再次关闭;若在 5s内小于0.1MPa,说明上阀关闭严密。
鲁奇加压气化炉的开、停车操作
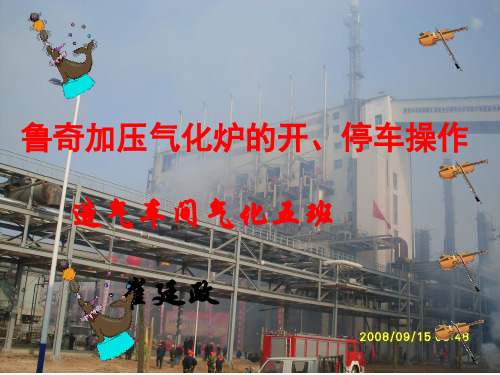
2、常压热备炉的停车与再开车
无论何种原因使气化炉在压力下停车超过30min, 则气化炉必须卸压,根据需要进行常压热备停车或交付 检修停车。 (1)、常压热备炉停车 :按压力热备停车后继续进行 以下步骤。 ① 关闭氧气、蒸汽管线的手动截止阀。 ② 将氧气管线上的盲板倒至盲位。 ③ 将气化炉压力调节阀投自动,打开气化炉通往火 炬的卸压阀,气化炉开始卸压。卸压速度小于 50kPa/min。卸压过程应注意夹套液位稳定,应及时补 水以防夹套干锅。 ④ 压力卸至0.15MPa时可全开火炬电动阀。 ⑤ 压力卸至常压后,打开夹套放空阀。转动炉篦少 量排灰,然后停炉篦,关灰锁上、下阀。
③气化炉加煤完成后,应转动炉篦半圈,以除去加 煤过程形成的煤粉。 (6) 气化炉煤层升温 :鲁奇加压气化炉的点火是用 过热蒸汽将煤加热到一定温度,在该温度下煤与氧 有较快的反应速度,利用煤的氧化、燃烧特性,通 入空气(或氧气)点火,升温操作步骤如下:①将 气化炉出口通往火炬管线上的阀门打开。②将过热 蒸汽引至入炉蒸汽电动阀前,打开该管段的导淋阀 暖管至蒸汽过热。③打开蒸汽电动阀约5%开度。 ④缓慢打开入炉蒸汽调节阀,调节入炉蒸汽流量为 5000kg/h(该流量是经温度、压力校正后的实际值)。 在向炉内通入蒸汽时必须很缓慢地调整,因为在常 压下若气流速度过快会造成炉内小粒度煤被气流带 出,造成废热锅炉及煤气水管线堵塞。
(2)、常压热备炉再开车 : 停车故障消除后,停车时间 小于8h,气化炉可直接通空气点火开车。 ① 倒通空气管线上的盲板,打开截止阀,关闭夹套放 空阀。 ② 转动炉篦1~2圈排灰。 ③ 打开空气流量调节阀向气化炉通空气量约1500Nm3/h。 ④ 取样分析煤气中CO2、O2含量,若CO2大于10%(体 积分数),O2含量逐渐下降,说明炉内火已点着。 ⑤ 当煤气中的O2含量为1%时,打开蒸汽电动阀,用入 炉蒸汽调节阀控制通入少量蒸汽,按煤种不同控制煤气中 CO2含量。 ⑥ 用气化炉压力调节阀缓慢将气化炉压力提高到 0.3MPa。 ⑦ 根据需要转动炉篦,进行加煤、排灰,以培养炉内 火层,按照气化炉原始开车中空气点火后的步骤继续进行。
碎煤加压气化(鲁奇)生产过程的控制(2024版)

33、计时器T-11启动,TC阀自动开。
34、若10秒内,TC阀全开,则“循环完成”信号出现。开启炉篦,灰锁开始受灰。
35、若10秒内,TC阀未全开,则“TC阀未全开”报警。
36、人工按“开”按钮,全开TC阀。
F
PV1
PV2
DV
CF
TC
BC
F
F
F
煤
一、煤锁控制程序(半自动) 煤锁加煤过程为间歇性的控制,通过操作阀门,使煤锁充压,泄压来实现加煤过程。一般操作方式分为现场手动与控制室遥控。而控制室又分为自动、半自动、手动。
2、人工按“关”按钮,关BC阀,监听铿锵声,观察限位指示,直至关严。
1、出现低料位或T=50℃、煤锁空”信号发出,灯光明,喇叭响。
37、“循环完成” 信号出现。
灰锁排灰程序(现场手动操作) 将三位开关切至现场手动操作,即可进行现场操作。 操作程序(以灰锁上阀打开,灰锁满为循环开端)
DV1
DV2
PV
F
F
F
F
充水
TC
BC
FV
1、炉篦已转到设定圈数或运行不超过1小时,炉篦自动停,如果不能自动停,则手动停,复位转数累积器。 注意点:a、“灰锁满”报警铃声响。 b、复位转数累积器。 c、如果不能自动停,则手动停。
6、当压力卸至0.0025MPa后,开BC阀,向灰斗排灰。
灰锁排灰程序(现场手动操作) 将三位开关切至现场手动操作,即可进行现场操作。 操作程序(以灰锁上阀打开,灰锁满为循环开端)
一、煤锁控制程序(手动)FPV1源自PV2DVCF
TC
鲁奇气化炉正常操作、维护和事故处理档
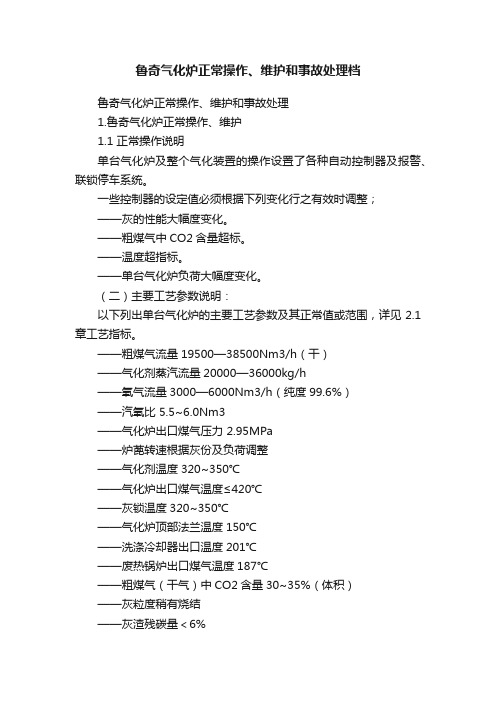
鲁奇气化炉正常操作、维护和事故处理档鲁奇气化炉正常操作、维护和事故处理1.鲁奇气化炉正常操作、维护1.1 正常操作说明单台气化炉及整个气化装置的操作设置了各种自动控制器及报警、联锁停车系统。
一些控制器的设定值必须根据下列变化行之有效时调整;——灰的性能大幅度变化。
——粗煤气中CO2含量超标。
——温度超指标。
——单台气化炉负荷大幅度变化。
(二)主要工艺参数说明:以下列出单台气化炉的主要工艺参数及其正常值或范围,详见2.1章工艺指标。
——粗煤气流量19500—38500Nm3/h(干)——气化剂蒸汽流量20000—36000kg/h——氧气流量3000—6000Nm3/h(纯度99.6%)——汽氧比 5.5~6.0Nm3——气化炉出口煤气压力 2.95MPa——炉蓖转速根据灰份及负荷调整——气化剂温度320~350℃——气化炉出口煤气温度≤420℃——灰锁温度320~350℃——气化炉顶部法兰温度150℃——洗涤冷却器出口温度201℃——废热锅炉出口煤气温度187℃——粗煤气(干气)中CO2含量30~35%(体积)——灰粒度稍有烧结——灰渣残碳量<6%1.2 气化炉操作指南注:本部分仪表都写的是第一系列的位号,第二、三系列和第一系列相同。
在正常操作中,主要工艺参数的控制参照2.1工艺指标一节,详细的控制及处理措施参照下述气化炉操作指南,其目的是为了帮助操作者找出偏离正常条件的原因及相应的处理措施。
a)混合管前后温差TDI-21CT007气化剂混合管前后温差高说明气化剂温度低。
气化剂温度低,最严重的情况可能由于气化剂中O2含量高而引起,这将导致渣块的形成和严重的影响炉篦的运行,此外,如果灰床低将会对炉篦带来损坏性影响,遇有这种情况应检查下述项目:1)检查汽氧比,如果低,增加蒸汽流量,提高汽氧比。
2)检查粗煤气中CO2含量,如偏低,提高汽氧比,相应提高了汽化剂温度。
3)检查灰粒度及灰质情况,如果有大块融渣形成,增加汽氧比,相应提高了气化剂温度。
关于鲁奇加压气化工艺的几点介绍

量产生蒸汽,经汽液分离后并
入气化剂中。夹套内产的饱和
蒸汽,无单独的集汽包,而是
利用夹套上部空间起汽液分离
作用,为了提高分离效果,在
内外壳体上焊有挡板。
气化炉内外壳体生产期
间由于温度不同,热膨胀量不
同,为降低温度差应力,在内
套下部设计制造成波形膨胀节,48mm
用于吸收热膨胀量。
正常生产期间,波形膨
2)气化炉出口温度降低,灰锁温度升高时,应降低炉篦转 速,减少排灰量。
3)气化炉出口温度和灰锁温度同时升高时,说明炉内有沟 流、风洞现象,应降负荷,适当提高汽氧比,正反转炉篦来 均匀布气,必要时加大炉篦转速以破坏风洞。
加负荷前的确认: 检查原料煤的质量指标和供给情况; 检查蒸汽和氧气的供给情况,氧气的纯度;
型均是一个双层筒体结构的反应器,
这种内外筒结构的目的在于尽管炉
内各层温度高低不一,但内筒体由
于有锅炉水的冷却,基本保持在锅
炉水在该操作压力下的蒸发温度,
不会因过热而损坏。由于内外筒受
热后的膨胀量不尽相同,一般在内
筒设有补偿装置。
夹套宽度为48mm,总
容积为13.3M3,充满锅炉水,
以吸收气化反应传给内筒的热
电机到炉篦大轴的转动比(速比)为596:1,炉篦大轴到炉篦转动比为6:1。
炉篦设在气化炉底部,其是气化炉的关键部件,设置其作用是:
1)使汽化剂均匀分布到气化炉的横断面;
2)排灰并维持一定的灰层高度;
3)破碎灰渣块,使灰渣粒度减小,防止灰锁阀门堵塞;
4)保持煤层、灰层在移动中达到均衡。作为均匀灰层条件,目的是防止汽化 剂在煤层中形成沟流。
3、煤气中CO2含量:CO2含量的变化对汽氧比的变化反应最敏感,在 煤种相对稳定的情况下,CO2超出设定范围要及时调整汽氧比,以适应 气化炉运行的需要。
鲁奇气化项目部工艺
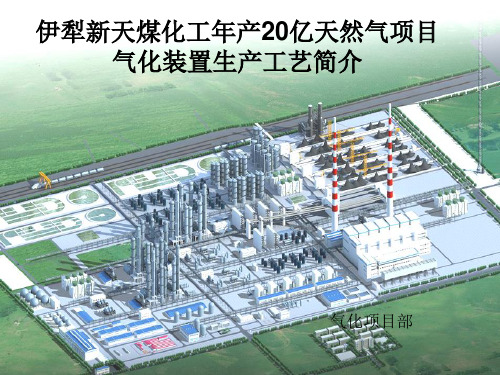
▪ 液态排渣
本装置采用第三代鲁奇气化炉,气化炉结构如 下:
▪ 炉体
▪ 夹套
▪ 炉篦 ▪ 灰锁
▪ 煤锁 ▪ 洗涤冷却器
(1)煤锁
▪ 煤通过煤锁由常压系统间歇地加入 到气化炉内,容积18.7m3,设计 压力4.6MPa,设计温度250℃350 ℃ ,操作温度20-150℃。采 用上下阀门加煤形式。高负荷时每 小时向气化炉加煤3-5次,每次 加煤时间约 8-10min。
与气化工艺有关的技术指标
▪ 1:气化强度:
▪ 气化强度是指单位时间内,单位横截面积上气化的原料煤 量,以㎏∕( M2.h )表示。 在实际生产中气化强度常以单 位时间,单位横截面积上的粗煤气量来表示〔M3(标) ∕㎡ .h , 影响气化强度的因素较多,原料煤的性质(煤种粒度 )和气化过程的操作条件(压力、温度、汽氧比等)均对气 化强度有较大影响。
▪ 缺点: ▪ (1)蒸汽分解率低,气化过程的热效率有所降低; ▪ (2)气化炉有复杂的传动机构,易损件多,设备检修频繁; ▪ (3)废水量大,废水处理复杂; ▪ (4)只能气化小块煤。
▪ 煤质要求: ▪ (1)需块煤(一般入炉煤在5~50mm之间); ▪ (2)灰熔融性软化温度大于1200℃; ▪ (3)除强粘结性煤外都能气化。
▪ 炉篦传动改为侧向传动
▪ 灰锁改在炉体下部正中, 下灰
第三代MARKIII (我们采用的炉型) (直径3.8m; 单炉产气量 35000-50000 Nm3/h)
▪ 改进了煤分布器和破粘装置
▪ 改进多层炉篦
▪ 改进了传动机构和控制系统
BGL气化炉 (单炉产气
75000Nm3/h )
▪ 去掉炉蓖改为喷 嘴
▪
⑴C+O2=CO2+408.8MJ
鲁奇加压气化炉的开、停车操作
04
鲁奇加压气化炉开、停车 操作的常见问题及解决方
案
开车过程中的常见问题及解决方案
开车过程中,气化炉内温度和压力上升缓慢,可能导致 开车失败
开车过程中,气化炉内出现严重结渣或堵塞现象,影响 气化效果
解决方案:检查气化炉的加热系统是否正常工作,确保 燃料供应充足,并适当增加助燃空气流量。
解决方案:停车后进行清渣或疏通作业,加强原料煤的 破碎和筛分,控制气化炉的操作温度和压力。
加强设备维护和保养
制定维护计划
根据设备运行状况和维修周期, 制定合理的维护计划,确保设备
正常运行。
定期检查
对设备进行定期检查,发现潜在问 题及时处理,避免设备故障影响生 产。
保养与润滑
定期对设备进行保养和润滑,延长 设备使用寿命,提高设备运行效率。
优化开、停车流程和管理制度
流程优化
对开、停车流程进行详细分析, 找出瓶颈和不合理环节,进行优 化改进。
开车流程
启动加压系统,将气化炉内压力逐渐 升至正常操作压力。
观察气化炉内的反应情况,调整原料 气流量、压力等参数,确保气化反应 正常进行。
打开供气系统,向气化炉内通入原料 气。
随着气化反应的进行,逐步增加气化 炉的负荷,直至达到正常生产能力。
开车过程中的注意事项
01
密切关注气化炉内的反 应情况,如发现异常应 及时停车检查。
停车过程中的常见问题及解决方案
停车过程中,气化炉内温度和 压力下降过快,可能导致设备
损坏或停车失败
停车过程中,气化炉内出现回 火或爆炸现象,危及设备和人 员安全
解决方案:适当减缓停车速度 ,控制气化炉的降温和降压速 率,同时加强设备的维护和保
养。
鲁奇碎煤加压气化工艺分析
鲁奇碎煤加压气化工艺分析一、鲁奇加压气化发展史鲁奇炉是德国鲁奇煤气化公司研究生产的一种煤气化反应器。
该炉型的发展经历了漫长的过程,其发展过程可分为三个阶段。
1、第一阶段:任务是证明煤炭气化理论在工业上实现移动床加压气化。
1936年至1954年,鲁奇公司进行了34次试验。
在这基础上设计了MARK—Ⅰ型气化炉。
该炉型的特点是炉内设有耐火砖,灰锁置于炉侧,气化剂通过炉篦主轴通入炉内。
炉身较短,炉径较小。
这种炉气化强度低,产气量仅为4500~8000Nm3/h,而且仅适用于褐煤气化。
2、第二阶段:任务是扩大煤种,提高气化强度。
为此设计出了第二代气化炉,其特点是(1)改进了炉篦的布气方式。
(2)增加了破粘装置,灰锁置于中央,炉篦侧向传动,(3)去掉了炉膛耐火砖。
炉型有MARK—Ⅱ型与MARK—Ⅲ型。
单台炉产气量为14000~17000Nm3/h。
3、第三阶段:任务是继续提高气化强度和扩大煤种适用范围。
设计了MARK—Ⅳ型炉,内径3.8米,产气量35000~50000Nm3/h,其主要特点是:(1)增加了煤分布器,改进了破粘装置,从而可气化炼焦煤以外的所有煤。
(2)设置多层炉篦,布气均匀,气化强度高,灰渣残炭量少。
(3)采用了先进的制造技术与控制系统,从而增加了加煤排灰频率,运转率提高到80%以上。
4、第四代加压气化炉:第四代加压气化炉是在第三代的基础上加大了气化炉的直径(达Ф5m),使单炉生产能力大为提高,其单炉产粗煤气量可达75000m3(标)/h(干气)以上。
目前该炉型仅在南非sasol公司投入运行。
今后鲁奇炉的发展方向:(1)降低汽氧比,提高气化层温度,扩大煤种适用范围,灰以液态形式排出,从而提高蒸汽分解率,增加热效率,大幅度提高气化强度,气化强度可由2.4t/m2h提高到3-5t/m2h.煤气中的甲烷可下降到7%以下。
(2)提高气化压力,根据鲁尔—100型炉实验,当压力由2.5Mpa提高到10.0Mpa,煤的转化率及气化强度可成倍增加,氧与蒸汽的消耗减少,煤的粒度也可以减少。
关于鲁奇加压气化工艺的几点介绍可修改全文
气化炉内外壳体生产期间 由于温度不同,热膨胀量不同, 为降低温度差应力,在内套下 部设计制造成波形膨胀节,用 48mm 于吸收热膨胀量。
正常生产期间,波形膨胀 节不但可吸收大约25~35mm 的内壳热膨胀量,而且在此还 可以起到支撑灰渣的作用,这 样可使灰渣在刮刀的作用下均 匀地排到灰锁中去。
夹套上部空间
剂在煤层中形成沟流。
炉篦分为五层,从下至 上逐层叠合固定在底座上, 顶盖呈锥形,炉篦材质选用 耐热耐磨的絡锰合金钢铸造。 最底层炉篦的下面设有三个 灰刮刀安装口,灰刮刀的数 量由气化原料煤的灰分含量 来决定。灰分含量较少时安 装1-2把刮刀,灰分高的安 装3把刮刀。支承炉篦的止 推轴承上开有注油孔,由外 部高压注油泵通过油管注入 止推轴承面进行润滑,该润 滑油为耐高温的过热汽缸油。 炉篦的传动采用变频电机传 动。由于气化炉直径较大, 为使炉篦受力均匀由两台电 动机对称布置。
1、气化炉排出灰渣的状态:颜色、粒度、含碳量。
灰渣粒度较大,量多,火层温度过高,说明汽氧比偏低。
灰渣中残炭量高,细灰量多且无熔渣,说明火层反应温度低,汽氧比偏 低。
2、原料煤的灰熔点:在灰熔点允许的情况下,应尽量降低汽氧比,以 提高反应层的温度,若灰熔点发生变化,要及时调整汽氧比。
3、煤气中CO2含量:CO2含量的变化对汽氧比的变化反应最敏感,在煤 种相对稳定的情况下,CO2超出设定范围要及时调整汽氧比,以适应气 化炉运行的需要。
➢ 增大炉篦转速,观察下灰量; ➢ 观察压差、压力、温度、流量的变化; ➢ 对出口气体进行分析。 ➢ 气化炉夹套耗水量正常
在气化炉工况稳定的情况下,增加负荷100Nm3/10min逐次递 增至所需负荷,原则上限定每小时增加负荷不能超过 1000Nm3;减负荷500Nm3/5min逐次递减至所需负荷,在加 减负荷过程中,要求保证气化炉工况和系统压力的稳定。
鲁奇气化工艺及设备原理概述
四、煤气水分离工段设备及功能
1、煤气水膨胀器: 含油煤气水膨胀器:是将煤气水冷却及低温甲醇洗工 段来的含油煤气水膨胀至常压后送入油分离器进行含油煤 气水分离; 含尘煤气水膨胀器:是将气化及煤气水冷却工段来的 含尘煤气水膨胀至常压后送入初焦油油分离器进行含尘煤 气水分离。 2、煤气水分离器 油分离器:是把由含油煤气水膨胀器膨胀至常压后的煤气 水采用重力沉降的方法进行油和煤气水分离。
二、气化工段所属设备及作用
1、气化工段主要设备及功能 灰 锁:将气化炉内产生 高温高压的灰渣排到灰渣沟 中。灰锁直接联接在气化炉 的底部法兰上,有效容积8m3 ,顶阀、底阀是液压操作。 灰锁连续不断的接收气化炉 旋转炉篦的排灰,正常情况 与气化炉相通,压力相等, 排灰时灰锁泄压至常压。
二、气化工段所属设备及作用
三、煤气水分离工段工艺流程
在81/82—F05中设有TPI板和活性炭吸附框,能有效清 除焦油、中油和粉尘。从400#煤气冷却工段来的含油煤 气水和500#净化工段来的含油煤气水被单独送往80— F001膨胀器膨胀至大气压,煤气水靠重力流入80— F002油分离器,在此煤气水中比水轻的中油被上浮分离 出来。煤气水则溢流进入80—B002,与前面的煤气水混 合后,经过80—P004泵送往80—F006过滤器过滤除尘、 除油后送往80—B003贮罐贮存缓冲,之后再送往850# 汽提装置。
二、气化工段所属设备及作用 2、气化工段附属设备及功能 夹套汽液分离器:分离气化炉内夹套产生的自产蒸 汽中夹带的液滴。分离出的气体并在过热蒸汽管线 ,作为汽化剂进入炉内。分离出的液体进入夹套, 作为循环锅炉水使用。 旋风分离器:利用重力离心力的原理分离煤锁泄至 常压后的带有煤尘的残余煤锁气。分离出的气体通 过顶部管线放空到大气中,底部的煤尘定期进行排 放。
- 1、下载文档前请自行甄别文档内容的完整性,平台不提供额外的编辑、内容补充、找答案等附加服务。
- 2、"仅部分预览"的文档,不可在线预览部分如存在完整性等问题,可反馈申请退款(可完整预览的文档不适用该条件!)。
- 3、如文档侵犯您的权益,请联系客服反馈,我们会尽快为您处理(人工客服工作时间:9:00-18:30)。
鲁奇加压气化炉工艺操作
新疆广汇新能源造气车间--程新院
一、相关知识
1、影响化学平衡的因素有三点:①反应温度(T)、②反应压力(P)、
③反应浓度(C)。
勒夏特列原理:如果改变影响化学平衡条件之一(T、P、C),平衡将向着能够减弱这种改变的方向移动。
2、气化炉内氧化层主反应方程式
① 2C+O₂=CO₂(-Q)ΔH<0
②2C+O₂=2CO(-Q)ΔH₂<0
ΔH<ΔH₂
3、气化炉内还原层主反应方程式
③C+CO₂=2CO(+Q)ΔH₃>0
④C+H₂O=CO+H₂(+Q)ΔH₄>0
⑤C+2H₂=CH₄(+Q)ΔH5>0
ΔH₃>ΔH₄>ΔH5
|ΔH|>ΔH₃>|ΔH₂|>ΔH₄>ΔH₄
4、煤灰熔点对气化炉的影响
鲁奇气化炉的操作温度介于煤的DT(变形温度)和ST(软化温度)之间。
若入炉煤的灰熔点高,则操作时适当降低汽氧比,相应提高炉温,蒸汽分解率增加,煤气水产量低,气化反应完全,有利于产气。
但是受气化炉设计材料的制约,汽氧比不能无限制降低,否则可能会烧坏炉篦及内件。
因此受设备材质的局限,煤灰熔点不能太高,
一般控制在1150℃≦DT≦1250℃。
反之,若煤灰熔点低,则操作时要适当提高汽氧比,相应降低炉温(防止炉内结渣,造成排灰困难),蒸汽分解率降低,煤气水产量增加,气化反应速度减缓,不利于产气。
因此入炉煤的灰熔点要尽可能在一定的范围内,不能变化太大。
二、汽氧比的判断
鲁奇加压气化炉汽氧比是调整控制气化过程温度,改变煤气组份,影响副产品产量及质量的重要因素。
汽氧比过低,会造成气化炉结渣,排灰困难,不利于产气;汽氧比过高,会造成灰细或排灰困难,煤气水产量增加等。
因此,在不引起灰份熔融的情况下,尽可能采用低的汽氧比。
汽氧比的高低应该结合煤气组份中有效气体的含量、灰样和指标参数做出准确的判断!
1、从煤气组份¹判断汽氧比的高低
我们在实际操作中一般都根据CO2、CO、H2、CH₄来判断汽氧比的高低,下面分情况进行说明。
¹:我公司白石湖煤产气组份
a、煤气组份中CO2和CH₄同时降低,CO和H2同时升高,这种情况最容易判断,根据还原层反应方程式
③C+H₂O=CO+H₂ΔH₃>0
④C+CO₂=2COΔH₄>0
上述反应都为吸热反应,只有提供足够的热量才能促使上述反应速度加快,生成物增加。
所以,当CO和H2同时升高时,说明炉温高,汽氧比低。
再结合灰样,若灰样中有大量较坚硬的渣块,相应的可能夹套耗水大,气化剂温(T008)度偏低,温差(TD007)偏高,此时可适当提高汽氧比。
相反,若CO和H2同时降低,灰样中大块少,可适当降低汽氧比。
b、煤气组份中CO和H2没有同步变化,而是CO2和H2偏低,CO和CH₄偏高,则说明炉温低,汽氧比高,应该适当降低汽氧比。
单独根据H2低、CH₄高来看,说明炉温低。
可为什么CO2低、CO高呢?[方程式④C+CO₂=2CO ΔH₄>0] 由于炉温低,汽氧比高,造成灰细,床层孔隙率小,床层阻力大,CO₂在炉内停留时间长,相当于增加反应物浓度,有利于CO的生成,大量的CO₂被还原程CO。
因此该适当降低汽氧比,提高炉温。
必要时结合灰样再做调整!
c、煤气组份中CO2没有明显的变化,CO偏低,H2含量增加,CH₄含量减少。
这种情况说明炉温过高²,应适当增加汽氧比降低炉温再看气体分析和灰样的变化有无好转!²:我们知道,当汽氧比低,炉温高时,CO和H2含量增加,CO2和CH₄含量偏低。
可为什么会有上述的情况,因为氧化层的主反应
① 2C+O₂=CO₂(-Q)ΔH<0
②2C+O₂=2CO(-Q)ΔH₂<0
ΔH<ΔH₂
都为放热反应,当炉温过高时,抑制了CO₂和CO的生成,又因为
|ΔH|≈4|ΔH₂|,所以氧化层产物中CO₂含量基本不变,CO含量偏低。
致使整个煤气组份中CO2没有明显的变化,CO偏低,H2含量增加,CH₄含量减少。
再结合灰样和指标参数加以肯定判断!
2、从灰样判断汽氧比的高低
若要从灰样来判断汽氧比的高低,就要根据灰样的颜色、粒度和残炭含量来具体分析,灰样颜色基本由煤中所含矿物质种类和含量来决定,作为操作工,我们无法改变煤质。
下面根据灰样粒度和残炭分情况进行判断:
a、灰样大部分为自然状的小颗粒,块状极少,残炭偏多。
说明炉温低,汽氧比高,应该降汽氧比,运行3-4小时再看灰进行调整。
b、灰样大部分为自然形成的大块,没有刮刀切痕,细灰和残炭量极少,此时的汽氧比为最佳,再结合煤气气体组份加以肯定判断,不做汽氧比的调整。
c、灰样中有大量的小渣块,不是自然形成,表面有明显的刮刀切痕,而且粉末状细灰量也有不少。
此时,说明汽氧比低,炉温高,应该适当增加汽氧比,运行3-4小时再结合煤气组份进行判断调整。
d、灰样中有部分颗粒状细灰,也有粒度较大的渣块,而且大块敲碎后里面裹着碳。
这种情况说明入炉煤质较差,煤灰熔点高低不等,造成部分低灰熔点的灰被熔融,包裹了部分高灰熔点的煤,导致炉内反应不完全,造成碳流失,煤气产率下降,工况出现波动。
此时应该适当提高汽氧比,降低炉温,让气化反应温度达到入炉煤最低灰熔点以下。
同时,也应该向相关部门反映情况,及时调整入炉煤。
三、问题判断与处理
1.炉内结渣
现象有:灰样中有大量的渣块,炉篦正反转电流都高,夹套耗水量可能会比平时增大,出口温度呈逐渐上涨趋势或者持续在380℃以上夹套耗水量大,排灰困难,灰锁温度偏低,煤锁加煤频次减少。
这种情况为汽氧比低,炉温高造成,我们应该适当增加汽氧比,降低炉温。
炉篦正反转交替将炉内结渣部分排出,严重时可将负荷处理。
在这个调整过程中,可能会出现炉内偏烧的现象,表现为:炉篦电流高,夹套耗水还未减少,出口开始出现波动,灰中细灰偏多,偶尔夹带个别较坚硬的大渣块。
此时不能盲目的认为是工况已经调好,汽氧比偏低!而是因为结渣较严重的部分还未完全排出,只是在调整过程中结渣不是很严重的部分已经有了好转,我们应该再适当降低汽氧比或者不动汽氧比,炉篦正反转交替转。
直至炉篦电流下降,耗水量减少。
2.气化炉出口温度和灰锁温度同时升高
出现这种情况的原因一般有三点:①气化炉内出现沟流,气化炉出口温度大幅度波动,煤气中CO2含量高。
严重时粗煤气中的氧含量超标,灰中有渣块和未燃烧的煤。
我们应该增加汽氧比,短时间增加炉篦转速反转破坏风洞,沟流。
严重时可稍降气化炉负荷,进行调整。
②气化剂分布不均,由于煤或者灰渣堵塞炉篦气化剂的通道或布气孔。
此时,我们应该提高汽氧比,频繁切换炉篦正反转,重新分布床层。
③床层混乱,灰中残炭多,导致双高。
此时,我们首先应该适当的降负荷,增加汽氧比,炉篦低转速调整,稳定灰锁温度,重新培养床层。
3.气化炉火层偏斜
气化炉火层偏移的现象有:气化炉出口温度高,灰锁温度时高时低,灰中有大块也有细灰和残碳。
主要是因为原料煤的粒度不均匀,炉内料层分布不均,原料煤中矸石较
多,炉篦转速过低,下灰量不均匀所形成。
处理方法是:气化炉降负荷,根据灰锁温度和出口温度正反转炉篦进行调整,现场加强听灰,看灰。
4.气化炉夹套压差高
如果发现夹套压差过高时可能造成夹套鼓包,应停车检查
出现夹套压高的原因有两点点:①汽氧比过高,入炉蒸汽量大,造成灰细,床层孔隙率小,阻力大。
我们应该适当降低汽氧比,减少入炉蒸汽量。
②气化炉结渣,会出现出口温度高,夹套耗水量大,排灰困难,灰锁温度偏低,煤锁加煤频次减少。
此时,我们应该增加汽氧比,降低负荷,增加炉篦转速,最大限度排灰,将炉内结渣部分排出。
四、刚开车运行炉子的操作
对于刚开起来的炉子我们应该以高汽氧比运行,通过各参数、灰样和气体组份来做出准确判断,设定最佳汽氧比。
另外,在运行期间主要以低转速正转以培养床层为主,不应该大转速或反转,以免破坏刚培养的床层。