超音速火焰喷涂工艺流程
超音速喷涂钴铬钨耐磨涂层的工艺研究
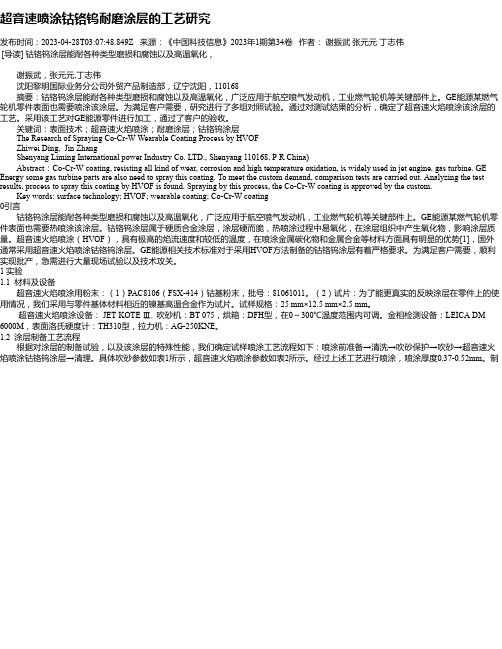
超音速喷涂钴铬钨耐磨涂层的工艺研究发布时间:2023-04-28T03:07:48.849Z 来源:《中国科技信息》2023年1期第34卷作者:谢振武张元元丁志伟[导读] 钴铬钨涂层能耐各种类型磨损和腐蚀以及高温氧化,谢振武,张元元,丁志伟沈阳黎明国际业务分公司外贸产品制造部,辽宁沈阳,110168摘要:钴铬钨涂层能耐各种类型磨损和腐蚀以及高温氧化,广泛应用于航空喷气发动机,工业燃气轮机等关键部件上。
GE能源某燃气轮机零件表面也需要喷涂该涂层。
为满足客户需要,研究进行了多组对照试验。
通过对测试结果的分析,确定了超音速火焰喷涂该涂层的工艺。
采用该工艺对GE能源零件进行加工,通过了客户的验收。
关键词:表面技术;超音速火焰喷涂;耐磨涂层;钴铬钨涂层The Research of Spraying Co-Cr-W Wearable Coating Process by HVOFZhiwei Ding, Jin ZhangShenyang Liming International power Industry Co. LTD., Shenyang 110168, P R China)Abstract:Co-Cr-W coating, resisting all kind of wear, corrosion and high temperature oxidation, is widely used in jet engine, gas turbine. GE Energy some gas turbine parts are also need to spray this coating. To meet the custom demand, comparison tests are carried out. Analyzing the test results, process to spray this coating by HVOF is found. Spraying by this process, the Co-Cr-W coating is approved by the custom.Key words: surface technology; HVOF; wearable coating; Co-Cr-W coating0引言钴铬钨涂层能耐各种类型磨损和腐蚀以及高温氧化,广泛应用于航空喷气发动机,工业燃气轮机等关键部件上。
科技成果——超音速火焰喷涂技术

科技成果——超音速火焰喷涂技术成果简介随着现代工业的高速发展,对各种机械设备的表面性能要求越来越高。
很多机械零部件往往因为表面局部的损坏而导致整个零件失效乃至报废。
摩擦会导致大量机械能的损耗,并且磨损是机械零件失效的一个很重要的原因。
据统计,工业化国家有30%的能源消耗于摩擦。
对于一个高度工业化的国家,每年因摩擦磨损造成的经济损失几乎占到国民经济年产总值的1-2%。
因此为了提高机械零件的可靠性,延长其使用寿命,国内外都在提高零件表面性能方面进行了大量的研究和探索。
表面工程是经表面预处理后,通过表面涂覆,表面改性或者多种表面技术复合处理,改变固体金属表面或者非金属表面的形态、化学成分、组织结构和应力状况,从而获得所需要表面性能的系统工程。
表面工程的最大优势在于可以用多种方法制备出优于基体材料性能的表面功能薄层。
技术原理超音速火焰喷涂是利用丙烷,丙烯等碳氢系燃气或氢气与高压氧气在燃烧室内,或者在特殊的喷嘴中燃烧产生的高温、高速燃烧焰流,燃烧焰流速度可达五马赫(1500m/s)以上,将粉末送进该火焰,可以将喷涂粒子加热至熔化或半熔化状态,并加速到高达300-500m/s 的速度,甚至更高的速度,从而获得高结合强度、致密的高质量的涂层。
(1)超音速火焰喷涂系统特点1、焰流速度达到2000m/s,火焰功率100kW;2、径向送粉和轴向送粉一体化设计;3、自动化程度高,稳定性能可靠;4、对冷却水压力实行实时监控,安全可靠;5、直接用丙烷点火,不用外加氢气;6、燃料气可为丙烷或丙烯等燃气,压力为当前国际同类设备一半。
(2)所制备WC-12Co涂层特点涂层致密、涂层的孔隙率低于1%。
由于涂层内部应力为压应力,涂层厚度可达五毫米以上。
技术水平100千瓦级TJ-9100型HVA/OF超音速火焰喷涂系统由热喷涂实验室开发研制,是拥有独立“自主知识产权”的新一代热喷涂技术。
适用于喷涂制备耐磨损高硬度WC-Co、Cr3C2-NiCr硬质合金涂层和耐腐蚀、耐高温氧化性能优越的镍基自熔合金涂层。
等离子热喷涂和超音速火焰喷涂

调研报告:等离子热喷涂与超音速火焰喷涂的区别、优缺点及成本对比一、工艺原理1. 等离子热喷涂:等离子热喷涂是一种通过将喷涂材料加热到熔融状态,然后以高速喷射到工件表面形成涂层的工艺。
等离子体作为一种高温热源,能够将涂料加热至熔融状态,使其在被喷涂时具有较高的流动性。
2. 超音速火焰喷涂:超音速火焰喷涂是一种利用高温燃气和高速喷射技术将喷涂材料喷射到工件表面的工艺。
该工艺使用燃气燃烧产生的高温高速气流将涂料加热并加速,使其以极高的速度喷射到工件表面。
二、涂料特性1. 等离子热喷涂:等离子热喷涂的涂料种类较多,包括金属、合金、陶瓷等材料。
由于等离子体的高温特性,能够保证涂料在熔融状态下的流动性,因此适用于喷涂较厚的涂层。
2. 超音速火焰喷涂:超音速火焰喷涂的涂料种类包括金属、非金属陶瓷等材料。
由于高速喷射的特性,适用于喷涂较薄的涂层。
三、涂层性能1. 等离子热喷涂:等离子热喷涂形成的涂层具有较高的结合强度、硬度和耐磨性。
同时,由于涂料在熔融状态下流动性较好,能够形成较致密的涂层结构。
2. 超音速火焰喷涂:超音速火焰喷涂形成的涂层具有较高的结合强度和硬度。
由于高速喷射的特性,形成的涂层具有较小的孔隙率,具有较好的防腐蚀性能。
四、优缺点1. 等离子热喷涂:优点:形成的涂层结合强度高、硬度较好;适用于喷涂较厚的涂层;可用于不同材料的喷涂。
缺点:设备成本较高;操作过程中需要消耗大量能源;高温下容易引起材料氧化。
2. 超音速火焰喷涂:优点:高速喷射形成的涂层结合强度高、防腐蚀性能好;设备成本相对较低;操作过程中能源消耗较少。
缺点:形成的涂层较薄,需多次喷涂才能达到预期效果;对于某些材料,易引起氧化和热损伤。
五、成本对比1. 等离子热喷涂:由于设备成本较高,操作过程中需要消耗大量能源,因此等离子热喷涂的成本相对较高。
2. 超音速火焰喷涂:设备成本相对较低,操作过程中能源消耗较少,因此超音速火焰喷涂的成本相对较低。
TC27钛合金超音速火焰喷涂WC-17Co耐磨涂层工艺研究

TC27钛合金超音速火焰喷涂WC-17Co耐磨涂层工艺研究本文将从工艺研究的角度出发,探讨TC27钛合金超音速火焰喷涂WC-17Co耐磨涂层的制备工艺、性能和应用前景,以期对该材料的研究和应用提供一定的参考和借鉴。
一、工艺研究背景传统的涂层材料往往存在着高温下易氧化、耐磨性差、热膨胀系数大等缺点,不适用于高温、高速和复杂工况下的应用。
研发一种在高温、高速环境下具有良好耐磨性和高温稳定性的涂层材料显得尤为重要。
TC27钛合金超音速火焰喷涂WC-17Co耐磨涂层是一种新型的涂层材料,其主要成分为碳化钨和钴。
碳化钨是一种硬度极高的材料,具有优异的耐磨性能和高温性能,而钴具有良好的粘接性和韧性,能够有效地固定碳化钨颗粒,使得整个涂层具有较好的性能。
由于其优异的性能,TC27钛合金超音速火焰喷涂WC-17Co耐磨涂层在航空领域得到了广泛应用。
1. 材料选择:所选用的TC27钛合金为目前应用较广泛的一种航空材料,其具有优良的高温性能和耐腐蚀性能。
2. 喷涂工艺:采用超音速火焰喷涂技术进行WC-17Co涂层的喷涂,确保涂层成分均匀、结合牢固。
3. 表面处理:在喷涂前,需对TC27钛合金进行表面处理,以提高涂层的附着力和密实性。
4. 热处理工艺:对喷涂后的涂层进行适当的热处理,以提高其结合力和耐磨性。
5. 性能测试:对制备的TC27钛合金超音速火焰喷涂WC-17Co耐磨涂层进行性能测试,包括耐磨性、高温稳定性等性能指标的测试。
三、工艺研究结果与分析1. 耐磨性能:经过磨损测试,涂层的磨损量明显减小,表现出优异的耐磨性能。
2. 高温稳定性:在高温环境下,涂层不易氧化、不易脱落,保持较好的性能。
3. 界面结合强度:涂层与基体的结合强度较高,具有良好的界面结合性能。
4. 经济性:采用超音速火焰喷涂技术,制备工艺简单,成本较低。
制备的TC27钛合金超音速火焰喷涂WC-17Co耐磨涂层具有优异的性能,可以满足在高温、高速工作环境中的使用要求。
超音速电弧喷涂技术

防磨防腐新材料超音速电弧喷涂技术一、超音速电弧喷涂的原理电弧喷涂原理是利用两根连续送进的金属丝作为自耗电极,在其端部产生电弧作为热源,用压缩空气将熔化了的丝材雾化,并以超音速喷向工作件形成一种结合强度高、孔隙率低、表面粗糙度低的涂层的热喷涂方法。
其工作原理与普通电弧喷涂(亚音速雾化)一样,超音速电弧喷涂是一个不断连续进行的熔化-雾化-沉积的过程。
但在雾化方式上,超音速电弧喷涂与普通电弧喷涂有根本的区别,即超音速电弧喷涂是采用超音速雾化。
其优点是:雾化效果好,雾化后的粒子细小均匀,速度高,有利于获得高质量的涂层。
超音速电弧喷涂采用拉伐尔喷嘴,将气流的速度从亚音速提高到超音速,加强了气流对粒子的加速效果,从而提高了粒子速度。
粒子速度对涂层的性能有很大的影响。
粒子速度高,粒子沉积时对基体的撞击作用就强,粒子变形就充分。
有利于粒子与基体、粒子与粒子之间的结合,从而提高涂层的结合强度和内聚强度;粒子速度高,粒子沉积前在空气中的飞行时间短,飞行中产生的氧化物就少,有利于粒子的结合,从而提高涂层的内聚强度,降低涂层的孔隙率。
粒子速度越高,越有利于获得高质量的涂层。
随着热喷涂设备的更新换代,粒子速度在不断提高,涂层的质量也不断得到改善。
超音速雾化减小了粒子的粒度,降低了涂层的粗糙度。
粗糙度是涂层的一项重要性能指标,它取决于雾化后粒子的粒度。
超音速雾化加强了气流对丝材端部熔化金属间的作用,雾化的粒子细小均匀,大大降低了涂层的粗糙度。
同时,粒子粒度的减小,也降低了粒子扁平化过程中的飞溅,有利于降低涂层的孔隙率。
超音速雾化是超音速电弧喷涂的出发点,是其与普通电弧喷涂的根本区别。
超音速电弧喷涂设备包括电源、喷枪、送丝机构及其附件,关键设备是超音速电弧喷枪。
我公司采用进口喷嘴,并且喷涂电流稳定,能在保证丝材雾化效果、涂层质量的前提下,一天的喷涂面积达到20m2。
电弧喷涂时,弧区的温度高达5000-6000℃,用气冷的方式对喷嘴进行冷却。
超音速火焰喷涂原理

超音速火焰喷涂原理
超音速火焰喷涂是一种利用超音速气流将液态或粉状的火焰喷涂材料喷射到被涂表面的技术。
其原理可以概括为以下几点:
1. 喷涂材料的制备:将火焰喷涂材料以液态或粉状形式储存在高压容器中。
液态材料一般需要通过加热使其变为气态,而粉状材料则直接进入喷涂设备。
2. 气流产生:在喷涂设备中,利用压缩空气或氧气等气体通过高压喷嘴加速排出,形成超音速气流。
超音速气流具有非常高的动能和冲击力。
3. 火焰生成:喷涂设备中通过点火机构将气体与可燃物质混合,并点燃产生火焰。
火焰的燃烧产生高温、高能量的气体。
4. 喷涂作用:当火焰燃烧时,超音速气流通过喷嘴将火焰喷涂材料从喷射出,形成一个喷涂射流。
火焰的高温能使液体材料蒸发或粉状材料熔化,并将其析出到射流中。
5. 沉积:喷涂射流与被涂表面相碰撞,产生冲击和磨擦作用。
火焰喷涂材料将沉积在被涂表面上,与基材粘结。
6. 火焰喷涂层形成:随着火焰喷涂材料的沉积,一层薄的火焰喷涂层逐渐形成。
这层火焰喷涂层具有很高的致密性和附着力,能够提供保护和改良被涂表面的性能。
总结:超音速火焰喷涂利用超音速气流将火焰喷涂材料喷射到
被涂表面,通过火焰的燃烧以及超声速气流的动能和冲击力,将液态或粉状材料沉积到表面形成薄的火焰喷涂层。
这种技术可以实现高效、快速和高附着力的涂层制备。
超音速喷涂
高速火焰喷涂高速火焰喷涂国内习惯上称为超音速火焰喷涂,它的英文缩写为HVOF(High Velocity Oxygen Fuel的首写字母)。
高速火焰喷涂是在爆炸喷涂的基础上发展起来的一项新的热喷涂技术,是在上世纪八十年代初期,由美国Browning公司最先研制成功,并推出名为JET-KOTE的商用喷涂设备。
高速火焰喷涂技术一经问世,就以其超高的焰流速度和相对较低的温度,在喷涂金属碳化物和金属合金等材料方面显现出了明显优势。
在世界各大热喷涂公司的积极推动下,该技术发展很快,目前高速火焰喷涂技术在喷涂金属碳化物、金属合金等方面,已逐步取代了等离子喷涂和其它喷涂工艺,成为热喷涂的一项重要工艺方法。
1.高速火焰喷涂原理高速火焰喷涂是将助燃气体与燃烧气体在燃烧室中连续燃烧,燃烧的火焰在燃烧室内产生高压并通过与燃烧室出口联接的膨胀喷嘴产生高速焰流,喷涂材料送入高速射流中被加热、加速喷射到经预处理的基体表面上形成涂层的方法。
可使用乙炔、丙烷、丙烯、氢气等作为燃气,也可使用柴油或煤油等液体燃料。
煤油、氧气通过小孔进入燃烧室后混合,在燃烧室内稳定、均一地燃烧。
有监测器用来监控燃烧室内压力,以确保稳定燃烧,喷涂粉末的速度与燃烧室内压力成正比。
燃烧室的出口设计使高速气流急剧扩展加速,形成超音速区和低压区。
粉末在低压区域沿径向多点注入,粉末均一混合,在气流中加速喷出。
高速火焰喷涂焰流速度高达1500m/s-2000m/s,一般可观察到5-8个明显的马赫锥,粒子流速度高达300-650m/s。
2.设备构成高速火焰喷涂设备一般由喷枪、送粉器、控制系统、喷枪冷却系统、气体供应系统五部分构成。
目前我国在用的高速火焰喷涂设备绝大部分是进口的,使用最多的型号为:Sulzer Metco公司的DJ-2700和Praxair 公司的JP-5000,JP-5000 是原Hobart Tafa公司研制成功的,后该公司并入了Praxair公司。
超音速电弧喷涂施工方案
循环流化床锅炉受热面采用超音速电弧喷涂施工方案一、施工条件为了作好施工准备工作,其施工需要具备以下条件:(1)电源:380V 20KW 三相交流电(2)气源:气压>5kgf 流量>5m3/min(3)平台:长4m(最少3m)宽2m(最少1.5m)(4)喷涂工件的位置离主机放置位置的距离不超过15m (5)搭设好施工部位所需的脚手架二、施工工艺流程:三、施工技术规范:1、施工准备:①根据实际需要搭好脚手架。
②清除受热面上的大块焦、杂物等。
③对管壁需实施喷涂的部位进行全面的质量检查,如发现需要修整补强的部位应及时向甲方提出。
④利用现场已有条件进行设备就位、电气接线、气源管线连接及磨料回收帆布铺设工作。
2、表面预处理:表面预处理按照GB11373-89《热喷涂金属件表面预处理通则》进行,其处理的好坏直接影响喷涂层的结合强度。
①喷砂前,对非有效表面采用遮蔽带、硬木板或橡胶等物进行遮蔽保护。
并预留过渡区域,以保证涂层边缘光滑过渡。
②磨料选择及使用:喷砂材料应选用质坚有棱角的金刚砂必须净化,使用前应经筛选,砂内粘土及细粉尘含量不应大于5%,不得含有油污。
喷砂前要晾晒干燥,含水量应不大于1%,并存放干燥,防止受潮、雨淋、砂内混入杂质。
所用砂粒必须清洁、干燥,喷砂区域设围护及其它回收措施,确保不污染周围环境,经质量工程师确认后方可进行喷砂。
③喷砂装置:采用压力式喷砂设备④压缩空气:利用现场气源或自备空压机,空气压力范围为0.5—0.6Mpa,气体流量控制在6m3/min左右。
⑤操作方法:喷砂距离100—300mm;喷砂角度:与基体60—80℃;每次喷砂5-6m2。
除锈应从下至上进行,将凹凸不平的受热面打磨光滑平整后立即喷砂。
使表面清洁度达到GB8923-88《涂装前钢材表面锈蚀等级和除锈等级》规定的Sa3.0级,即完全去除钢材表面的锈、氧化皮、油污等附着物,并露出灰白色金属光泽,其粗糙度达到GB11373-89《热喷涂金属表面预处理通则》规定的R Z50-90μm。
超音速电弧喷涂防磨防腐技术方案,施工方案(煤粉炉)
超音速电弧喷涂防磨防腐技术方案煤粉锅炉受热而管由于长期受高温含尘气流的冲刷,表而腐蚀磨损情况相当严重。
为解决冲刷磨损及腐蚀问题,目前最为有效的途径是采用超音速电弧喷涂技术在管壁外表面制作防磨防腐涂层。
并在该涂层涂上耐高温金属纳米电弧喷涂涂料,形成致密复合涂层,效果良好,使用寿命可达5年以上。
〈一〉煤粉锅炉受热面的失效分析煤粉锅炉遭受腐蚀的部位通常是水冷壁管、过热器管、再热器管和省煤气管,即所谓“四管”。
这些部位在煤粉燃烧过程中,直接与火焰及燃烧产物接触,经受高温、腐蚀、磨损和应力的共同作用而失效。
我国现役机组发电装机总容量接近3亿千瓦,但90%以上为200-300W亚临界以下的机组,其中超期服役机组2500万KW。
这些机组过热器和再热器大多由低合金钢管制造(如G102, 12CrMo,TU,T12等)。
材料的因素加之运行中恶劣条件,导致较多的早期爆管情况。
局部统计表明,锅炉爆管引起停机抢修时间约占整台机组非计划停用时间的40跖以上,占非计划用时的70跖以上。
锅炉爆管不仅严重影响发电机的正常运行,同时给电厂造成重大的经济损失。
引发锅炉爆管的机因十分复杂。
管材制造、冶金质量、安装、焊接等原始质量问题。
也有运行中内壁承受高温、高压,外壁经受高温1 / 14燃气腐蚀,颗粒冲蚀、直至运作制度、管理与维护等,这些因素不下十几项,但902/14%左右的爆管木质原因是管材经高温、腐蚀、磨损和应力的共同作用,出现材料的损伤和裂纹扩展所致。
在繁多的失效因素中,应力损伤、蒸气管内腐蚀、疲劳等属于取材、制造、加工、维修和运行管理等原因有关,而腐蚀(高温氧化, 熔盐和硫的腐蚀,应力腐蚀)和有关磨损则是表而工程技术可关注与设法解决的对象。
高温氧化是指炉管在炉内1200°C上下的火焰中,构成炉管的金属元素(主要是Fe)与氧发生反应,生成氧化物,氧化物在相组成、结构等方而与原质材料的不相容而产生应力,最终脱层而减薄炉管。
超音速喷涂
热喷涂技术之未来趋势--超音速喷涂技术摘要:本文简要叙述了热喷涂技术的概况,比如热喷涂设备组成,热喷涂的工作原理,热喷涂技术的特点;着重介绍了热喷涂技术中超音速喷涂技术的发展过程, 简述了超音速火焰喷涂、超音速等离子喷涂、超音速电弧喷涂及冷喷涂等设备的结构和技术特点, 介绍了超音速喷涂工艺及涂层特性, 展望了该技术在制备纳米涂层方面的应用及发展前景。
关键词: 表面处理技术;热喷涂技术;超音速喷涂;超音速火焰喷涂;超音速等离子喷涂;超音速电弧喷涂;冷喷涂1.1 热喷涂技术概况众所周知, 除少数贵金属外,金属材料会与周围介质发生化学反应和电化学反应而遭受腐蚀。
此外,金属表面受各种机械作用而引起的磨损也极为严重。
大量的金属构件因腐蚀和磨损而失效,造成极大的浪费和损失。
据一些工业发达国家统计,每年钢材因腐蚀和磨损而造成的损失约占钢材总产量的10 %,损失金额约占国民经济总产值的2 - 4 %。
如果将因金属腐蚀和磨损而造成的停工、停产和相应引起的工伤、失火、爆炸事故等损失统计在内的话,其数值更加惊人。
因此,发展金属表面防护和强化技术,是各国普遍关心的重大课题。
随着尖端科学和现代工业的发展,各工业部门越来越多地要求机械设备能在高参数(高温、高压、高速度和高度自动化)和恶劣的工况条件(如严重的磨损和腐蚀)下长期稳定的运行。
因此,对材料的性能也提出更高要求。
采用高性能的高级材料制造整体设备及零件以获得表面防护和强化的效果,显然是不经济的,有时甚至是不可能的。
所以,研究和发展材料的表面处理技术就具有重大的技术和经济意义。
而表面处理技术也在这种需求的推动下获得了飞速的发展和提高。
热喷涂技术是表面防护和强化的技术之一,是表面工程中一门重要的学科。
所谓热喷涂, 就是利用某种热源, 如电弧、等离子弧、燃烧火焰等将粉末状或丝状的金属和非金属涂层材料加热到熔融或半熔融状态,然后借助焰流本身的动力或外加的高速气流雾化并以一定的速度喷射到经过预处理的基体材料表面,与基体材料结合而形成具有各种功能的表面覆盖涂层的一种技术。
- 1、下载文档前请自行甄别文档内容的完整性,平台不提供额外的编辑、内容补充、找答案等附加服务。
- 2、"仅部分预览"的文档,不可在线预览部分如存在完整性等问题,可反馈申请退款(可完整预览的文档不适用该条件!)。
- 3、如文档侵犯您的权益,请联系客服反馈,我们会尽快为您处理(人工客服工作时间:9:00-18:30)。
超音速火焰喷涂工艺流程:施工前的准备工作、表面预处理、喷涂、喷涂后处理四个主要步骤:一)准备工作:在编制工艺前首先应该了解被喷涂工件的实际状况和技术要求半进行分析1、确定涂层的厚度。
一般来讲,喷涂后必须进行机械加工,因此涂层厚度就要预留加工余量,同时还要考虑到喷涂时的热胀冷缩等。
2、涂层材料的确定。
选择依据是涂层材料应该满足被喷涂工件的材料,配合要求,技术要求及工作条件等,分别选择结合层与工作层材料3、确定参数:压力,粉末粒度,喷枪与工件的相对运动速度二)工件表面的预处理表面制备,是保证涂层与基体结合强度的重要工序1、凹切处理,表面存在疲劳层和局部严重拉伤的沟痕时,在强度允许的前提下可以进行车削处理,为热喷涂提供容纳的空间。
2、表面清理,清除油污,铁锈,漆层等,使工件表面洁净,油污油漆可以用溶剂清洗剂除去。
如果油渍已经渗入基体材料,可以用火焰加热除去,对锈层可以进行酸浸,机械打磨或喷砂除去。
3、表面粗化,目的是为了增强涂层与基体的结合力,消除应力效应,常用的有喷砂、开槽、车螺纹、拉毛。
A:喷砂是最常用的,砂料可以选择石英砂、氧化铝砂、冷硬铁砂等。
砂料以锋利坚硬为好,必须清洁干燥,有尖锐棱角。
其尺寸,空气压力的大小,喷砂角度、距离和时间应该根据具体情况确定。
B:开槽、车螺纹、辊花。
对轴、套类零件表面的粗化处理,可采用开槽、车螺蚊处理,槽与螺纹表面粗糙度以RA6.3—12.5为宜,加工过程中不加冷却液与滋润剂,也可以在表面滚花纹,但避免出现尖角。
C:硬度较高的工件可以进行电火花拉毛进行粗化处理,但薄涂层工件应慎用。
电火花拉毛法是将细的镍丝或铝丝作为电极,在电弧的作用下,电极材料与基体表面局部熔合,产生粗糙的表面。
表面粗化后呈现的新鲜表面,应该防止污染,严禁用手触摸,保存在清洁,干燥的环境中,粗化后尽快喷涂,一般喷涂时间不超过二个小时。
4、非喷涂部位的保护喷涂表面附近的非喷涂需要加以保护,可以用耐热的玻璃布或石棉而屏蔽起来。
必要时按零件开关制作相应的夹具保护,但是要注意夹具材料要有一定的强度,且不能使用低熔点的合金,以免污染涂层。
对于基体表面上的键槽、油孔等不允许喷涂的部位,可以用石墨块或粉笔堵平或略高于表面。
喷后清除时,注意要要碰伤涂层,棱角要倒钝。
三)喷涂工艺及参数(1)粉末特性:目前粉末供应商提供了品种繁多的碳化物粉末,而粉末特性往往因其制粉工艺方法的不同而表现出较大的差异。
粉末特性包括:粉末粒度分布、颗粒形状、表面粗糙度等。
对ZB-2700设备来说,适宜的粉末粒度为:15μm-40μm。
(2)氧-燃气流量和比例喷涂的焰流温度及特性取决于氧-燃气流量和混合比例。
喷涂时,首先应按照设备的规定要求确定氧气和燃气的流量,以保证喷枪焰流达到设计的功率水平。
实际生产过程中有多种因素可导致氧-燃气比例的波动,而氧-燃气比例对确定最终的涂层组织十分重要.理论上,丙烷完全燃烧要求氧与丙烷的比例为5∶1(C3H8+5O2=4H2O+3CO2),这一燃烧比例产生的是中性焰(即,燃烧时氧与燃气分子全部耗尽)。
若燃气比例下降,焰流中未消耗尽的氧分子将产生“氧化”气氛,导致熔融粉末粒子的过度氧化,涂层中氧化物含量增多。
混合气中燃气过多会产生低温贫氧的火焰,所得涂层中未熔粒子和孔洞增多,而氧化物含量降低。
事实上,中性焰是不存在的,在高温,燃烧过程不是完全可逆的,反应物与反应产物以热平衡和化学平衡方式共存。
ZB-2700型超音速火焰喷涂系统,当氧-燃气比例在4.2-5.6之间时,可获得高性能的涂层。
(3)喷涂距离:ZB-2700型超音速火焰喷涂系统,当粉末粒子在距喷枪出口100mm以内即已达到了其最高温度,随着喷距的增加粒子温度逐渐降低,在100-230mm范围内,粒子温度大约降低了60℃,其降低幅度并不大,粒子仍可保持约1775℃的高温;而粒子速度在距喷枪出口大约190mm内是一个逐渐加速的过程,在距喷枪出口190-200mm左右达到580m/s以上的最高速度,在170-230mm喷距上,粒子速度基本维持在580m/s以上。
考虑到高温焰流对基体传热的不利影响,喷距在可能的情况下应尽量增大,故对ZB-2700型超音速火焰喷涂系统来说,适宜的喷距应为:190-230mm。
与其它喷涂工艺相比,喷涂喷距的可调整范围是比较大的,这得益于粒子的高速度。
较大的喷距可调范围对实际生产十分有利,因为可以根据工件的形状、大小、涂层厚度等要求选择适宜的喷距,以得到综合性能最好的涂层。
(4)送粉量:对任何热喷涂工艺来说,送粉量都是影响涂层性能的一个重要参数。
某种粉末在某一具体的喷涂工艺条件下,都对应有一适宜的送粉量范围。
若送粉量过小,可能的不利影响有:1)被喷涂粉末过熔,粉末烧损,烟雾大,易污染涂层。
2)每一遍喷涂不能完全覆盖其扫过的路径,造成涂层孔隙率增大。
3)延长了喷涂时间易造成工件过热涂层开裂和生产成本的增大。
若送粉量过大,可能的不利影响有:1)粉末熔化不充分,涂层结合强度降低,孔隙率增大。
2)涂层应力增大,导致涂层开裂。
3)粉末沉积率下降,生产成本提高。
使用ZB系统,喷涂WC-Co涂层时,当送粉量在38-60g/min之间变化时,涂层孔隙率在0.55—1.2%之间,显微硬度在HV1000-1300, 粉末沉积率为40-50%,涂层性能优。
喷涂CrC-NiCr涂层时:当送粉量在27-45g/min之间变化时,可获得令人满意的涂层质量。
四)喷涂后处理封孔,机械加工等工序。
涂层的孔隙率约占体积的百分之五,而且有的孔隙可由表及里。
零件为摩擦副时,可在喷后趁热将零件放在润滑油中,利用孔隙储油有利于润滑。
但对于随液压的零件,孔隙而容易产生泄露,对于喷涂后,应该用封孔剂进行封孔处理。
对封孔剂要求:浸透性好,耐化学作用,不溶解,不变质。
在工作温度下性能稳定,能增强涂层性能,常用的有石蜡,环氧,酚醛等。
当喷涂后的尺寸精度与表面粗糙度不能满足要求时,需要对其进行机械加工,可采用车削或磨削加工。
超音速火焰喷涂设备技术参数:ZB-2700超音速火焰喷涂设备(HVOF) - 技术性能参数表:电缆、符合安全规范的标准化气管、水管、电缆管路超音速火焰喷涂涂层评析 2006-10-3 19:00 信息来源:MTE制造网超音速火焰喷涂涂层评析黎明航空发动机(集团)有限责任公司军事代表室曾杰刘军和[摘要]超音速火焰喷涂由于具有焰流速度快、焰流长、直径收缩小、粉末动能和能量密度大等特点,使其涂层呈现致密、氧化物含量和未熔颗粒少、孔隙率低、结合强度高、加工性能好、不易剥落等特性。
本文叙述了等离子喷涂、火焰喷涂和超音速火焰喷涂3种喷涂试验,并对获得的涂层进行了对比、分析、评价,说明了超音速火焰喷涂的优越性。
关键词:超音速火焰喷涂等离子喷涂火焰喷涂涂层[ABSTRACT]High velocity oxygen flame (HVOF) sprayed coating is characterized by its densification, less content of oxides and unmelted particles, lower porosity, higher bond strength, better machinability and non easy spalling because of its features of rapid flame flow speed, longer flame flow, less diameter contraction and bigger kinetic energy of power and energy densities. This paper describes three spraying tests of plasma spraying, flame spraying and HVOF spraying, and the coatings sprayed are compared, analyzed and evaluated, so that the advantages of the HVOF spraying are proved.Keywords: HVOF spraying Plasma spraying Flame spraying Coating传统的火焰喷涂工艺以氧-乙炔火焰来熔化待喷涂的粉末,由于焰流速度慢,热量不集中,粉末在空气中飞行时间长,因而形成的涂层粗糙多孔(孔隙率多为10%~15%),氧化物和未熔颗粒多,涂层的结合硬度和结合强度(多为20~30MPa)较低而且易产生裂纹和剥落。
等离子喷涂工艺以等离子弧作为热源将粉末熔化,高速喷到零件表面形成涂层,由于等离子。
弧温度高(弧柱中心温度可达15000~33000K),能量大,粉末粒子飞行速度快,而且采用氩气作为等离子气体、氢气作为辅助气体,又具有还原气氛,因而粉末的氧化程度低,所形成的涂层致密,孔隙率(3%~8%)和氧化物含量都很低,结合强度(40~50MPa)和硬度较高,但由于残余应力的存在,涂层不能过厚,否则会产生裂纹和剥落。
此外,等离子喷涂还有一个明显的缺点,就是使用和维护费用较为昂贵。
20世纪80年代以来,随着超音速火焰(High Velocity Oxygen Flame,HVOF)喷涂工艺的研发,涂层的性能产生了质的飞跃。
超音速喷枪的结构独特,在燃烧室的末端即咽喉部位采用了拉瓦尔曲线设计,使得燃烧室的压力增加,通过该处的焰流获得数倍于音速的速度;而且采用了径向内送粉的方式,使得粉末在10~30cm的枪管内得到充分的加热和加速,虽然温度不是很高(2870℃),但由于能量集中,受热均匀,因此熔化得非常好;此外,由于粉末粒子的动能大,速度快,粒子在空气中的飞行时间极短,被氧化的机会极少,再加上喷枪系统本身的温度不高(2870℃),所以涂层中几乎没有氧化物,空隙率也极低(小于2%),涂层致密,剪切强度和结合强度都非常高(可达到60MPa以上),而且涂层内的残余应力几乎都是压应力,这样就使得涂层可以具有很大的厚度而不至于产生裂纹和剥落,例如316不锈钢涂层的厚度可以达到12mm。
尤其是WC-Co涂层,HVOF喷涂更具优越性。
本课题以等离子喷涂、火焰喷涂、HVOF喷涂3种工艺分别喷涂了WC/12Co 、WC/17Co、NiCrBSi 3种涂层,并对涂层的各项性能进行了分析和研究。
1 试验材料(粉末)热喷涂涂层的性能和微观结构与所使用的粉末有较大的关系,不同的粉末粒度、化学成分都会对涂层性能造成影响。
WC-Co涂层是一种典型的抗磨损涂层,WC-Co粉末有铸造/粉碎型、烧结/粉碎型、团聚/烧结型和钴包覆型4种形式。